Scientific american 3d printer
Your Next House May Pop Out of a 3D Printer
In the Netherlands, renowned for its canals, bridges are a common sight. But four bridges in particular are construction oddities: each 26-foot structure was fashioned from concrete by a giant robotic printer.
They are part of a revolution that is seeing 3D printers, which extrude plastic and other materials to build up solid objects, move from the tabletop to the construction lot. Since 2017, several companies and groups in the U.S., Europe and Asia have ‘printed’ bus-stop shelters and convention-hall partitions, as well as entire homes.
The techniques of 3D printing are still in the early stages, but commercial-grade printers could radically change the construction business in the next decade. Experts believe they could cut construction time in half, reduce costs by as much as a third, and offer greener, sturdier designs, with more scope for customization.
As the technology takes off, the global 3D printing construction market is forecast to reach USD14. 9 billion by 2026 from just USD4.6 million in 2019, according to Polaris Market Research.
3D construction printers work a lot like home-office inkjet ones, except instead of ink they spit out concrete. Nozzles run back and forth on rails, with computers controlling the pattern of extrusion, so that an inch-thick layer of concrete (or steel or other material) is laid down precisely where needed. By the time the slow-moving nozzle reaches the end of its path, which can be up to 100 feet long, the layer has usually hardened just enough to lay down another on top of the first, building up, layer-by-layer, a home-sized wall. With precise pattern of deposit, the nozzle can leave spaces for windows, doors, utility conduits, and other design and structural elements.
One of the most obvious advantages is speed. It takes about 24 hours of printing to build a 500-square-foot single-floor home. “The printing process delivers structure, insulation, wall-sheeting, interior and exterior surface finishing, and the conduit system, all at the same time,” says Jason Ballard, co-founder and CEO of ICON, an Austin, Texas company focused on 3D-printing-based construction. “That normally takes 20 people representing five or six different trades working several days.”
3D construction printers are also less wasteful. A typical home construction site generates about four tons of waste. Because the concrete used in conventional slab construction is applied uniformly, regardless of whether it’s needed for structural support in a particular area or not, about half of the concrete is wasted. That’s especially damaging to the environment because cement, the main ingredient of concrete, accounts for about seven percent of our carbon dioxide emissions. 3D printers, by contrast, can vary the thickness of a structure with great precision, using concrete only where it is really needed — a process called topological optimization.
Another advantage of printed construction is that it’s digital, which means a design rendered on a computer gets converted directly into instructions for the printer. That eliminates the need to transfer designs to paper blueprints, which are then open to interpretation by tradespeople — an error-prone process that often leads to cost overruns and delays.
The digital-to-digital approach has the added benefit of removing barriers to design creativity. An architect can offer custom or semi-custom designs more cheaply, without having to worry about training tradespeople to execute a novel plan. “The printer doesn’t care what design you come up with,” says Theo Salet, a structural engineer at the Eindhoven University of Technology, a pioneer of printed construction who built the Amsterdam bridges. “It won’t charge you more for being original.”
So far, printed buildings have been modest, low-cost affairs. For instance, ICON printed a dwelling in Austin, Texas, intended for families, at a cost of $10,000, and has a contract to print a total of six. Then it plans to take a printer down to Latin America to build 50 low-cost homes there. Salet, meanwhile, is about to start working on a 90-foot bridge in Amsterdam, and is also in a partnership to build several homes in the Netherlands.
A blueprint for the futureTo scale up production, more work is needed in technology and regulation. For the former, practitioners haven’t yet found an efficient way of reinforcing concrete from a printer. In conventional construction, that’s done by laying down steel reinforcement bars. Some developers are experimenting with using a second robot to lay down steel bars in each newly deposited layer. In other schemes, the main printer shoots out metal or plastic wire a few millimeters thick along with the concrete. Neither approach has yet proven optimal.
The big hope is that new concrete formulas, or even new extrudable materials, will eventually be strong enough to do away with reinforcement. Epoxy, for example, is one potential candidate. It is a type of polymer currently used in adhesives and coatings in manufacturing and construction. Or there are other options. “From a more radical perspective, I’d like to work with a biomaterial,” says Salet. “But we just don’t have the skill set to work with it in construction yet.”
Safety rules also need to finalized, with set guidelines for the inspection of 3D-printed houses and rules on construction procedures. If inexperienced, incautious builders get access to printers, their structures could be in danger of collapse, warns Salet. “You have to make sure the bonds between the layers are strong enough, and that takes a lot of knowledge,” he says. “I fear that someone will buy a printer and decide to build a bridge, and then wait too long between layers, leaving weaker bonds. One incident will give the whole digital-concrete industry a bad name.”
There is progress, however. Ballard, for instance, is working with inspectors, insurers and federal mortgage agencies in the US, who are all part of the process needed to make printed homes a legitimate option for most potential buyers. “It’s taking them a little bit to get their heads around it,” he says. “But I think they’ll see there’s no way a conventionally built structure can be guaranteed as sound as ours can be.”
Read more about technological advances in agriculture and other fields on Mega.online. Mega seeks to energise and enrich the debate over how to create a better functioning economy and society with articles and videos featuring leading academics, scientists and entrepreneurs active in the fields of sustainability, technology, health, alternative energy and agriculture.
Forget Everything You Know about 3-D Printing—the "Replicator" Is Here
Computing
Rather than building objects layer by layer, the printer creates whole structures by projecting light into a resin that solidifies
By Davide Castelvecchi, Nature magazine on
Share on Facebook
Share on Twitter
Share on Reddit
Share on LinkedIn
Share via Email
Print
They nicknamed it ‘the replicator’—in homage to the machines in the Star Trek saga that can materialize virtually any inanimate object.
Researchers have unveiled a 3D printer that creates an entire object at once, rather than building it layer by layer as typical additive-manufacturing devices do—bringing science-fiction a step closer to reality.
“This is an exciting advancement to rapidly prototype fairly small and transparent parts,” says Joseph DeSimone, a chemist at the University of North Carolina at Chapel Hill.
The device, described on 31 January in Science, works like a computed tomography (CT) scan in reverse, explains Hayden Taylor, an electrical engineer at the University of California, Berkeley.
In CT machines, an X-ray tube rotates around the patient, taking multiple images of the body’s innards. Then, a computer uses the projections to reconstruct a 3D picture.
Stop the press
The team realized that the process could be reversed: given a computer model of a 3D object, the researchers calculated what it would look like from many different angles, and then fed the resulting 2D images into a ordinary slide projector. The projector cast the images into a cylindrical container filled with an acrylate, a type of synthetic resin.
As the projector cycled through the images, which covered all 360 degrees, the container rotated by a corresponding angle. “As the volume rotates, the amount of light received by any point can be independently controlled,” says Taylor. “Where the total amount exceeds a certain value, the liquid will become solid.”
This is because a chemical in the resin absorbs photons and, once it reaches a certain threshold, the acrylate undergoes polymerization—the resin molecules link together into chains to make a solid plastic.
The exposure process takes about two minutes for an object a few centimetres across; the team recreated a version of Auguste Rodin’s sculpture ‘The Thinker’ a few centimetres tall.
The remaining liquid is then removed, leaving behind the solid 3D object.
The process is more flexible than conventional 3D printing, Taylor says; for example, it can create objects that enclose existing ones. The resulting structures also have smoother surfaces than can be achieved with typical 3D printers, which could be helpful for manufacturing optical components.
The scientists suggest the method could be used for printing medical components.
This article is reproduced with permission and was first published on January 31, 2019.
ABOUT THE AUTHOR(S)
Davide Castelvecchi is a staff reporter at Nature who has been obsessed with quantum spin for essentially his entire life. Follow him on Twitter @dcastelvecchi
Read This Next
Newsletter
Get smart. Sign up for our email newsletter.
Sign Up
Support Science Journalism
Discover world-changing science. Explore our digital archive back to 1845, including articles by more than 150 Nobel Prize winners.
Subscribe Now!American space biomedical 3D printer ready to be sent to the ISS
News
In a few hours, a biomedical 3D printer developed with the support of NASA by the American companies Techshot and nScrypt will go into space.
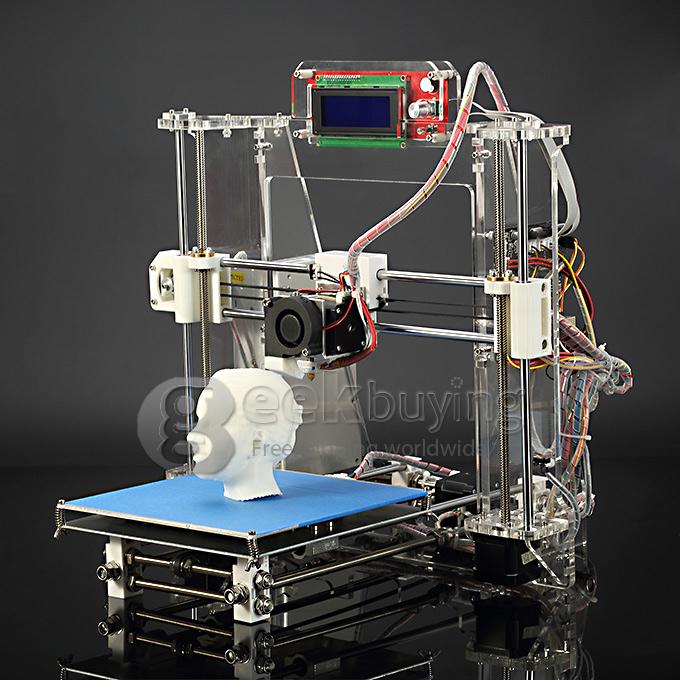
SpaceX prepares to launch the Falcon 9 launch vehicle and the Dragon cargo spacecraft as part of the CRS-18 resupply mission. In addition to the usual supplies, the ship is supposed to deliver the American biomedical additive complex BioFabrication Facility (BFF) to the International Space Station. American scientists lost the race for the title of the first space bioprinters to the Russian laboratory 3D Bioprinting Solutions, which has already completed the first cycle of experiments on 3D printing with living cells in microgravity using the Organ.Avt magnetic bioprinter ( in the illustration below ).
On the other hand, the American team has clearer plans: while the Russian scientific program is not yet showing concrete signs of purposefulness, the project of the research company Techshot and the engineering company nScrypt is aimed at studying the possibility of 3D bioprinting of functional heart tissues and organs that are indistinguishable from natural and suitable for implantation.
In the long term, scientists hope to get full-fledged replicas of hearts, but this level is still very far away. So far, the researchers will be engaged in experiments on 3D printing of prototypes of heart tissue, but functional, that is, contracting under the influence of electrical impulses. An intermediate step could be the cultivation of implantable heart patches to treat birth defects and the consequences of injuries and illnesses, such as heart attacks. One interesting point is that the printed fabrics will mature directly in orbit, in a special incubator, and to a certain extent this is due to the limited capabilities of existing space technology.
“We know that SpaceX has excellent means of delivery and return from orbit, but, unfortunately, they do not differ in a smooth return [ in the context, we mean g-forces during braking in the atmosphere and directly during landing - approx. ed. ]. This means that we will have to bring samples of biomaterials to mechanical, chemical and electrical standards even on board the station. What we get directly from the output of a 3D printer is not a fabric and cannot be a fabric. It's just a design: we assemble it from individual blocks, and then we have to sit and watch how biological processes do everything else, ”explains Eugene Boland, lead scientist at Techshot.
However, the problem lies not only in delivery, but also directly in gravity. The fact is that nutritional hydrogels saturated with living cells serve as consumables. Printing multilayer structures with a jelly-like material under normal conditions seems impossible, since the printouts will spread under their own weight. It is for this reason that almost all existing examples of 3D bioprinting, with the possible exception of the results of scientists from Tel Aviv University ( in the illustration above ), are reduced to rather primitive samples in terms of geometry and dimensions, and it is for this reason that Techshot decided to scale experiments in space. The primary goal of the scientific team is to obtain samples of 3D printed heart tissue at least one centimeter thick, which is about ten times thicker than the record-breaking samples obtained on Earth.
“We intend to use the BFF in orbit to 3D print living cells, grow and mature cell structures to the point where samples can be returned to Earth, so that incoming samples are already as functional as possible. Samples of planned sizes have never been printed here on Earth, and even more so in microgravity. What will come out of this we will tell you in forty-five days, when we meet again, ”commented Kenneth Church, CEO of nScrypt, at the pre-flight press conference of the scientific team at the Kennedy Space Center.
The launch from Cape Canaveral is scheduled for July 24 at 18:24 local time (July 25, 01:24 Moscow time). The live broadcast will be available on the NASA Youtube channel at this link.
Do you have interesting news? Share your developments with us, and we will tell the whole world about them! We are waiting for your ideas at news@3Dtoday. ru.
Follow the author
Follow
Don't want
3
Even more interesting articles
13
Subscribe to the author
Subscribe
Don't want
Last Saturday, September 24, the third 3Dtoday Fest took place in St. Petersburg...
Read more
7
Subscribe to the author
Subscribe
Don't want
In July, the international isolation experiment SIRIUS-21 ended in Moscow, which lasted 240 days...
Read more
82
Subscribe to the author
Subscribe
Don't want
Collaboration 3D
We are pleased to present you our joint development with Speci. ..
Read more
American scientists 3D printed a prototype of a bionic eye
News
0003
7
Scientists from the University of Minnesota have demonstrated a prototype of a bionic eye with electronics printed on a 3D printer.
The new work is a continuation of research on 3D printing of electronics with an eye on biological integration by a research team led by University of Minnesota Associate Professor of Mechanical Engineering Michael McAlpine. The previous experiment involved 3D printing electronics over skin ( in illustration below ) using a modified Anycubic Kossel 3D printer, with the experimental system proving to be able to compensate for involuntary movements of the subject during printing through a combination of 3D scanning and machine vision. The inspiration for the new experiment was the supervisor's mother, who lost sight in one of her eyes. The team decided to find out if a functional prosthesis could be printed.
“Bionic eyes are usually seen as something out of science fiction, but now, thanks to multi-material 3D printing, we are closer than ever to turning the idea into reality. We have a long way to go before additive manufacturing of active electronics becomes commonplace, but our 3D printed semiconductors show great potential and the ability to achieve efficiency on par with conventional semiconductor electronics. In addition, we can easily print semiconductor devices on curved surfaces, which mass electronics manufacturers can't do,” says McAlpine.
The device shown consists of a transparent hemisphere, internally lined with polyethylene terephthalate (PET) film. On top of the film, the researchers printed an array of photodetectors, each consisting of five layers—a silver-based conductive ink, then a transparent and flexible conductive PEDOT:PSS anode, a P3HT:PCBM photoactive polymer blend, an insulating silicone layer, and a liquid gallium cathode. indium alloy. The effectiveness of the prototype surprised the developers themselves: the ratio of the photocurrent at the external leads to the number of incident photons reaches 25.3%. Of course, the prototype is very primitive, but the team intends to continue experimenting with flexible and biocompatible substrates towards increasing the number of elements in the array and, if successful, creating the first true functional prosthetic eye. The report of the scientific team is published at this link.
Do you have any interesting news? Share your developments with us, and we will tell the whole world about them! We are waiting for your ideas at [email protected].
Follow author
Follow
Don't want
7
Article comments
More interesting articles
13
Follow author
Subscribe
Don't want
Last Saturday, September 24, the third 3D-printing festival 3Dtoday Fest took place in St.