Dmls 3d print
Direct Metal Laser Sintering [DMLS] Parts On Demand
Direct Metal Laser Sintering [DMLS] Parts On Demand - Stratasys Breaking The Sound Barrier Webinar With Our Guest Boom Supersonic - Click Here to RegisterUSA & Canada
Select your country and region
- Americas
- English
- Español (México)
- Português (Brasil)
- EMEA
- English (United Kingdom)
- Deutsch
- Español
- Français
- italiano
- APAC
- 中文(简体)
- 日本語 (日本)
- 한국어(대한민국)
- English (India)
USA & Canada
Parts On Demand
What Is Direct Metal Laser Sintering?
Direct Metal Laser Sintering (DMLS) is a direct metal laser melting (DMLM) or laser powder bed fusion (LPBF) technology that accurately forms complex geometries not possible with other metal manufacturing methods.
DMLS Part Strength
DMLS parts are stronger and denser than investment casted metal parts, and they can help you get to market first with faster turnaround times.
Metal 3D printing is an ideal process for complex oil and gas components, custom medical guides, part-consolidated aerospace parts and tough functional prototypes.
Streamlined Metal Parts with DMLS
Utilize the design freedom of DMLS and produce accurate metal components in less time than other manufacturing methods.
How Does Direct Metal Laser Sintering Work?
DMLS uses a precise, high-wattage laser to micro-weld powdered metals and alloys to form fully functional metal components from your CAD model.
DMLS parts are made with powdered materials like aluminum, stainless steel and titanium, as well as niche alloys like MONEL® K500 and Nickel Alloy 718.
Finishing DMLS Parts
Raw DMLS parts have a surface finish comparable to a fine investment casting part, and expert finishing services are sometimes needed.
Stratasys Direct offers a full suite of professional finishing operations, including precision machining, media blasting, surface grinders and milling.
Direct Metal Laser Sintering Quality Controls
To maintain critical quality control standards, we use a range of tools to inspect and ensure customer specifications. With international certification standards ISO 9001 and AS9100, we have stringent systems in place to guarantee quality and consistently are met.
We utilize tools like coordinate measuring machines, probes, cutup metallography processes and flow benches, hydrostatic pressure testing machines to guarantee quality is consistently met. DMLS materials build fully dense, corrosive resistant and highly robust metal parts that can be further treated through heat, coating and sterilization.
DMLM Products
Essentials
- The fastest way to manufacture with DMLM technology
- Produce geometries with high-strength metal alloys in one fluid build
- Hand-finishing with media blast
- Manufacture in Stainless Steel 316L or 17-4, Aluminum (AlSi10Mg), Cobalt Chrome, Nickel Alloy 625, and Titanium (Ti64)
A.
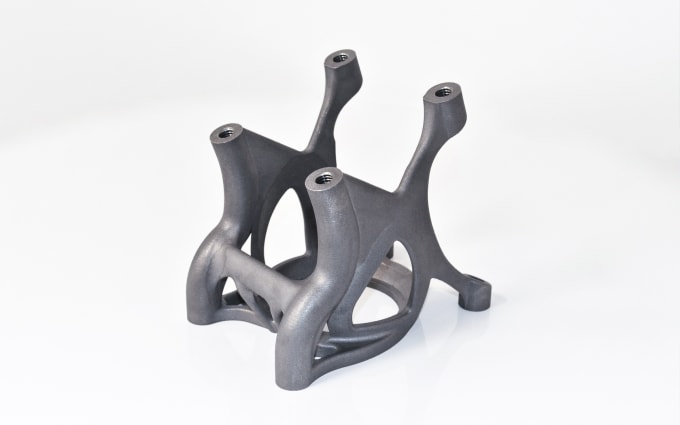
- No spec? No problem! Our Additive Metal Process Spec provides production metal parts with DMLM technology
Customer Specification
- Adhering to customer-provided statement of work and process, material, and/or machine specifications. The ultimate level of control for your project and product
DMLM Discover
We’re ready to take on any challenge and push the boundaries of what’s possible with DMLM Discover – our custom solution for new and novel additive alloys and designs.
- Access materials in the early stages of development for DMLM
- Test custom manufacturing parameters for your project
Materials for 3D Printing Parts with DMLS
Stainless Steel 17-4 PH (As Built)
SS17-4PH is characterized by excellent weld-ability, good corrosion resistance, and mechanical properties
Learn more
Stainless Steel 316L (As Built)
SS316L is characterized by very good weld-ability, corrosion resistance, and mechanical properties including excellent ductility.
Learn more
Aluminum AlSi10Mg (As Built)
Casting grade alloy
Learn more
Nickel Alloy 625 (As Built)
Nickel based superalloy
Learn more
Nickel Alloy 718 (As Built)
High strength nickel base superalloy
Learn more
Nickel Alloy K500 (As Built)
Age-hardenable Nickel-Copper alloy
Learn more
Titanium Ti64 (As Built)
Titanium alloy
Learn more
Cobalt Chrome CoCrMo (As Built)
Metal alloy of cobalt and chromium
Learn more
Metal 3D Printing Applications of DMLS
PRODUCTION PARTS
Produce low-volume production metals parts with DMLS.
Read More
Functional Prototyping
Build tough and hardworking metal prototypes to test components in real-world applications.
Read More
Thermal Control Systems
Advance your thermal management capabilities with complex heat exchangers and heat pipes manufactured with DMLS.
DMLS Parts from 3D Printing Pioneers
Making a quality 3D printed part takes more than just a machine. It takes a responsive team behind the technology, running tests and working tirelessly to validate materials and processes.
At Stratasys Direct, our services are backed by more than the largest fleet of machines in North America; we have nearly thirty years in the industry and a team of engineers ready to assist with every step of your project.
DMLS Expertise You Can Trust
Years of experience with DMLS has led us to develop proprietary build styles, post-processing methods, and even led us into material development exploration.
Whatever your project need, we won’t rest until your requirements are met.
Frequently Asked Questions About DMLS
Are DMLS parts as strong as traditionally manufactured metal components?
Yes. The parts created with DMLS have mechanical properties equivalent to a cast metal part. Detailed information can be found on the DMLS materials page.
What is the porosity of DMLS parts?
DMLS parts can reach a 99.5% density. In fact, 3D printed metals are above industry standards for density testing.
What level of detail can be obtained with DMLS?
DMLS is available in several resolutions. At its highest resolution, the layer thickness is 0.0008” – 0.0015” Z and the X/Y resolution is 0.012” – 0.016”.
The minimum hole diameter is 0.035” – 0.045”. Read the DMLS design guidelines to learn more.
Metal 3D Printing Service for Custom Parts
Back
-
Materials
Materials by Service
Injection MoldingCNC Machining3D PrintingSheet Metal
Materials by Type
PlasticsMetalsElastomers
Related Links
Customer Supplied ResinsColors
Injection Molding Material Alternatives Guide
Struggling with thermoplastic material shortages? We created a detailed guide to resin substitutes for ABS, PC, PP, and other commonly molded thermoplastics.
Download
-
Resources
Design Tips Guides and Trend Reports Success Stories Design Aids Webinars & Trade Shows
Blog Videos FAQs Educators & Students Glossary
Industries Medical Aerospace Automotive Consumer Electronics Industrial Equipment
-
About Us
Who We Are Why Protolabs? Research and Development Cool Idea Award Partnerships Sustainability & Social Impact
Careers Investors Locations Press Procurement
Contact Us
Proto Labs, Inc.
5540 Pioneer Creek Dr.
Maple Plain, MN 55359
United StatesP: 877.479.3680
F: 763.479.2679
E: [email protected]Best-in-Class Online Quoting
After uploading your part design, you'll receive an online quote that includes manufacturing analysis to help improve part manufacturability. Within your quote, you can also adjust quantity and material and see price changes in real-time.
Learn More
Get a QuoteSign In
Get quality metal 3D-printed prototypes and production parts. Request an online quote today.
GET METAL PARTS
Certifications
ISO 9001:2015 | AS9100D | ITAR Registered
Jump to Section→ Capabilities
→ Available Alloys
→ Compare Material Properties
→ Surface Finishes
→ Post-Processing
→ Why Metal 3D Printing?
Direct metal laser sintering (DMLS) is an industrial metal 3D printing process that builds fully functional metal prototypes and production parts in 7 days or less. A range of metals produce final parts that can be used for end-use applications.
Metal 3D printing technology is commonly used for:
- Prototyping in production-grade materials
- Complex geometries
- Functional, end-use parts
- Reducing metal components in an assembly
We hope you find this guide helpful. If the file did not download, you can find it here.
Jump start your metal 3D printing with this guide that covers material selection, design, post-processing, and quality inspections.
United States of AmericaAfghanistanÅland IslandsAlbaniaAlgeriaAmerican SamoaAndorraAngolaAnguillaAntarcticaAntigua and BarbudaArgentinaArmeniaArubaAustraliaAustriaAzerbaijanBahamasBahrainBangladeshBarbadosBelarusBelgiumBelizeBeninBermudaBhutanBolivia, Plurinational State ofBonaire, Sint Eustatius and SabaBosnia and HerzegovinaBotswanaBouvet IslandBrazilBritish Indian Ocean TerritoryBrunei DarussalamBulgariaBurkina FasoBurundiCambodiaCameroonCanadaCape VerdeCayman IslandsCentral African RepublicChadChileChinaChristmas IslandCocos (Keeling) IslandsColombiaComorosCongoCongo, the Democratic Republic of theCook IslandsCosta RicaCôte d'IvoireCroatiaCubaCuraçaoCyprusCzech RepublicDenmarkDjiboutiDominicaDominican RepublicEcuadorEgyptEl SalvadorEquatorial GuineaEritreaEstoniaEthiopiaFalkland Islands (Malvinas)Faroe IslandsFijiFinlandFranceFrench GuianaFrench PolynesiaFrench Southern TerritoriesGabonGambiaGeorgiaGermanyGhanaGibraltarGreeceGreenlandGrenadaGuadeloupeGuamGuatemalaGuernseyGuineaGuinea-BissauGuyanaHaitiHeard Island and McDonald IslandsHoly See (Vatican City State)HondurasHong KongHungaryIcelandIndiaIndonesiaIran, Islamic Republic ofIraqIrelandIsle of ManIsraelItalyJamaicaJapanJerseyJordanKazakhstanKenyaKiribatiKorea, Democratic People's Republic ofKorea, Republic ofKuwaitKyrgyzstanLao People's Democratic RepublicLatviaLebanonLesothoLiberiaLibyaLiechtensteinLithuaniaLuxembourgMacaoMacedonia, the Former Yugoslav Republic ofMadagascarMalawiMalaysiaMaldivesMaliMaltaMarshall IslandsMartiniqueMauritaniaMauritiusMayotteMexicoMicronesia, Federated States ofMoldova, Republic ofMonacoMongoliaMontenegroMontserratMoroccoMozambiqueMyanmarNamibiaNauruNepalNetherlandsNew CaledoniaNew ZealandNicaraguaNigerNigeriaNiueNorfolk IslandNorthern Mariana IslandsNorwayOmanPakistanPalauPalestine, State ofPanamaPapua New GuineaParaguayPeruPhilippinesPitcairnPolandPortugalPuerto RicoQatarRéunionRomaniaRussian FederationRwandaSaint BarthélemySaint Helena, Ascension and Tristan da CunhaSaint Kitts and NevisSaint LuciaSaint Martin (French part)Saint Pierre and MiquelonSaint Vincent and the GrenadinesSamoaSan MarinoSao Tome and PrincipeSaudi ArabiaSenegalSerbiaSeychellesSierra LeoneSingaporeSint Maarten (Dutch part)SlovakiaSloveniaSolomon IslandsSomaliaSouth AfricaSouth Georgia and the South Sandwich IslandsSouth SudanSpainSri LankaSudanSuriNameSvalbard and Jan MayenSwazilandSwedenSwitzerlandSyrian Arab RepublicTaiwan, Province of ChinaTajikistanTanzania, United Republic ofThailandTimor-LesteTogoTokelauTongaTrinidad and TobagoTunisiaTurkeyTurkmenistanTurks and Caicos IslandsTuvaluUgandaUkraineUnited Arab EmiratesUnited KingdomUnited States Minor Outlying IslandsUruguayUzbekistanVanuatuVenezuela, Bolivarian Republic ofViet NamVirgin Islands, BritishVirgin Islands, U. S.Wallis and FutunaWestern SaharaYemenZambiaZimbabwe
I agree to receive email messages containing service updates and Design Tips from Protolabs and its affiliates
Metal 3D Printing Capabilities
Our basic guidelines for metal 3D printing include important design considerations to help improve part manufacturability, enhance cosmetic appearance, and reduce overall production time.
Metal 3D Printing Tolerances
For well-designed parts, tolerances of +0.003 in. (0.076mm) plus 0.1% of nominal length can typically be achieved. Note that tolerances may change depending on part geometry.
Max Dimensions
Layer Thickness
Minimum Feature Size
Tolerances
*At this time, Inconel 718 and Aluminum are the only materials available on our large format, X Line machine
Metal 3D Printing Material Options
Below is our available metal alloys for 3D printing. Various heat treatments are available depending on material.
Stainless Steel (17-4 PH)
Stainless Steel 17-4 PH is a precipitation hardened stainless steel that is known for its hardness and corrosion resistance. If needing a stainless steel option, select 17-4 PH for its significantly higher tensile strength and yield strength, but recognize that it has far less elongation at break than 316L. Final parts built 17-4 PH receive vacuum solution heat treatment as well as H900 aging.
Primary Benefits
- Heat treated for full hardness and strength
- Corrosion resistance
LEARN MORE>
Stainless Steel (316L)
Stainless steel 316L is a workhorse material used for manufacturing acid and corrosion resistant parts. Select 316L when stainless steel flexibility is needed; 316L is a more malleable material compared to 17-4 PH. Final parts built in 316L receive stress relief application.
Primary Benefits
- Acid and corrosion resistance
- High ductility
LEARN MORE>
Aluminum (AlSi10Mg)
Aluminum (AlSi10Mg) is comparable to a 3000 series alloy that is used in casting and die casting processes. It has good strength -to-weight ratio, high temperature and corrosion resistance, and good fatigue, creep and rupture strength. AlSi10Mg also exhibits thermal and electrical conductivity properties. Final parts built in AlSi10Mg receive stress relief application.
Primary Benefits
- High stiffness and strength relative to weight
- Thermal and electrical conductivity
LEARN MORE>
Inconel 718
Inconel is a high strength, corrosion resistant nickel chromium superalloy ideal for parts that will experience extreme temperatures and mechanical loading. Final parts built in Inconel 718 receive stress relief application. Solution and aging per AMS 5663 is also available to increase tensile strength and hardness.
Primary Benefits
- Oxidation and corrosion resistance
- High performance tensile, fatigue, creep, and rupture strength
LEARN MORE>
Cobalt Chrome (Co28Cr6Mo)
Cobalt Chrome (Co28Cr6Mo) is a superalloy is known for its high strength-to-weight ratio.
Primary Benefits
- High performance tensile and creep
- Corrosion resistance
LEARN MORE>
Titanium (Ti6Al4V)
Titanium (Ti6Al4V) is a workhorse alloy. Versus Ti grade 23 annealed, the mechanical properties of Ti6Al4V are comparable to wrought titanium for tensile strength, elongation, and hardness. Final parts built in Ti6Al4V receive vacuum stress relief application.
Primary Benefits
- High stiffness and strength relative to weight
- High temperature and corrosion resistance
LEARN MORE>
Compare Material Properties
20 μm = high resolution (HR)
30, 40, and 60 μm = normal resolution (NR)
- US
- Metric
Materials | Resolution | Condition | Ultimate Tensile Strength (ksi) | Yield Stress (ksi) | Elongation (%) | Hardness |
---|---|---|---|---|---|---|
Stainless Steel (17-4 PH) | 20 μm | Solution & Aged (H900) | 199 | 178 | 10 | 42 HRC |
30 μm | Solution & Aged (H900) | 198 | 179 | 13 | 42 HRC | |
Stainless Steel (316L) | 20 μm | Stress Relieved | 82 | 56 | 78 | 90 HRB |
30 μm | Stress Relieved | 85 | 55 | 75 | 88 HRB | |
Aluminum (AlSi10Mg) | 20 μm | Stress Relieved | 39 | 26 | 15 | 42 HRB |
30 μm | Stress Relieved | 50 | 33 | 8 | 59 HRB | |
40 μm | Stress Relieved | 43 | 27 | 10 | 50 HRB | |
Cobalt Chrome (Co28Cr6Mo) | 20 μm | As Built | 182 | 112 | 17 | 39 HRC |
30 μm | As Built | 176 | 119 | 14 | 38 HRC | |
Inconel 718 | 20 μm | Stress Relieved | 143 | 98 | 36 | 33 HRC |
30 μm | Stress Relieved | 144 | 91 | 39 | 30 HRC | |
30 μm | Solution & Aged per AMS 5663 | 208 | 175 | 18 | 46 HRC | |
60 μm | Stress Relieved | 139 | 83 | 40 | 27 HRC | |
60 μm | Solution & Aged per AMS 5663 | 201 | 174 | 19 | 45 HRC | |
Titanium (Ti6Al4V) | 20 μm | Stress Relieved | 153 | 138 | 15 | 35 HRC |
30 μm | Stress Relieved | 144 | 124 | 18 | 33 HRC |
Materials | Resolution | Condition | Ultimate Tensile Strength (MPa) | Yield Stress (MPa) | Elongation (%) | Hardness |
---|---|---|---|---|---|---|
Stainless Steel (17-4 PH) | 20 μm | Solution & Aged (H900) | 1,372 | 1,227 | 10 | 42 HRC |
30 μm | Solution & Aged (H900) | 1,365 | 1,234 | 13 | 42 HRC | |
Stainless Steel (316L) | 20 μm | Stress Relieved | 565 | 386 | 78 | 90 HRB |
30 μm | Stress Relieved | 586 | 379 | 75 | 88 HRB | |
Aluminum (AlSi10Mg) | 20 μm | Stress Relieved | 268 | 180 | 15 | 46 HRB |
30 μm | Stress Relieved | 345 | 228 | 8 | 59 HRB | |
40 μm | Stress Relieved | 296 | 186 | 10 | 50 HRB | |
Cobalt Chrome (Co28Cr6Mo) | 20 μm | As Built | 1255 | 772 | 17 | 39 HRC |
30 μm | As Built | 1213 | 820 | 14 | 38 HRC | |
Copper (CuNi2SiCr) | 20 μm | Precipitation Hardened | 496 | 434 | 23 | 87 HRB |
Inconel 718 | 20 μm | Stress Relieved | 986 | 676 | 36 | 33 HRC |
30 μm | Stress Relieved | 993 | 627 | 39 | 30 HRC | |
30 μm | Solution & Aged per AMS 5663 | 1434 | 1207 | 18 | 46 HRC | |
60 μm | Stress Relieved | 958 | 572 | 40 | 27 HRC | |
60 μm | Solution & Aged per AMS 5663 | 1386 | 1200 | 19 | 45 HRC | |
Titanium (Ti6Al4V) | 20 μm | Stress Relieved | 1055 | 951 | 15 | 35 HRC |
30 μm | Stress Relieved | 993 | 855 | 18 | 33 HRC |
These figures are approximate and dependent on a number of factors, including but not limited to, machine and process parameters. The information provided is therefore not binding and not deemed to be certified. When performance is critical, also consider independent lab testing of additive materials or final parts.
Surface Finish Options
Standard Finish
Expect roughness values of 200 to 400 µin Ra (0.005 to 0.010mm Ra), depending on material and resolution. Support structures are removed and layer lines are visible.
Custom Finish
We offer brushed surfaces in a range of grits and polished mirror finishes. Be sure to indicate if the custom surface finish is for functional or aesthetic purposes so we can best consult you on our custom options.
Post-Processing Capabilities for Metal 3D-Printed Parts
Improve strength, dimensional accuracy, and cosmetic appearance of final metal components with DMLS for production.
Surface Finishing
- 3- and 5-axis milling
- Turning
- Polish (Mirror or Brushed)
- Passivation
- Wire EDM
- Tapping and reaming
Heat Treatments
- Stress relief
- NADCAP heat treatment
- Hot isostatic pressing (HIP)
- Solution annealing
- Aging
Mechanical Testing
- Tensile
- Rockwell Hardness
Powder Analysis & Material
- Traceability
- Chemistry
- Particle size and distribution analysis
Why Use Metal 3D Printing?
See how metal additive manufacturing technology can be used to reduce components within an assembly, fabricate complex geometries, and ultimately save you time and costs.
Click to enlarge
How Does Metal 3D Printing Work?
The DMLS machine begins sintering each layer—first the support structures to the base plate, then the part itself—with a laser aimed onto a bed of metallic powder. After a cross-section layer of powder is micro-welded, the build platform shifts down and a recoater blade moves across the platform to deposit the next layer of powder into an inert build chamber. The process is repeated layer by layer until the build is complete.
When the build finishes, an initial brushing is manually administered to parts to remove a majority of loose powder, followed by the appropriate heat-treat cycle while still fixtured in the support systems to relieve any stresses. Parts are removed from the platform and support structures are removed from the parts, then finished with any needed bead blasting and deburring. Final DMLS parts are near 100 percent dense.
Large Format Metal 3D Printing
We recently added the GE Additive X Line to our fleet of metal 3D printers to build large Inconel 718 and Aluminum (AlSi10Mg) parts. Have a project that might be a good fit? Contact us and we can discuss your requirements.
Learn More >
Metal 3D Printing for Production
Improve strength, dimensional accuracy, and cosmetic appearance for end-use metal components with post-processing options like CNC machining and heat treatments.
Learn More >
Resources
Design Tip
Post-Processing for Metal 3D Printing
Learn how to improve dimensional accuracy, surface roughness, and mechanical properties on metal parts with high-requirement applications.
Read Design Tip
White Paper
Combining Part Assemblies with Additive Manufacturing to Reduce Cost and Increase Performance
How to find the right opportunities to consolidate multi-part assemblies into single components with industrial 3D printing
Read White Paper
Blog
Inconel 718: A Workhorse Material for Additive Manufacturing
Inconel 718 is a go-to material for additive manufacturing of metal parts.
Read Blog
Blog
Large Format 3D Printing for Aluminum and Inconel Parts
When you’re printing really large parts in metal, it’s great to have a choice of materials. Aluminum and Inconel 718 both make a lot of sense, but which one is the best for your application?
Read Blog
Instant quotes on 3D-printed parts
Get A QuoteDirect Metal Laser Sintering (DMLS)
- 1 DMLS Technology
- 2 Advantages and disadvantages
- 3 Application
- 4 Materials
- 5 3D Printing Technologies
DMLS Technology
Direct Metal Laser Sintering (DMLS) is a metal additive manufacturing technology developed by EOS in Munich. DMLS is often confused with the similar technologies of selective laser sintering ("Selective Laser Sintering" or SLS) and selective laser melting ("Selective Laser Melting" or SLM).
The process involves using 3D STL models as blueprints to build physical models. The three-dimensional model is subject to digital processing for virtual separation into thin layers with a thickness corresponding to the thickness of the layers applied by the printing device. The finished "construction" file is used as a set of drawings during printing. As a heating element for sintering metal powder, fiber-optic lasers of relatively high power, about 200 W, are used. Some devices use more powerful lasers with faster scanning (i.e. moving the laser beam) for higher performance. Alternatively, it is possible to increase productivity by using multiple lasers.
DMLS allows you to create one-piece metal parts of complex geometric shapes
Powder material is fed into the working chamber in the quantities required to apply one layer. A special roller levels the fed material into an even layer and removes excess material from the chamber, after which the laser head sinters fresh powder particles between themselves and with the previous layer according to the contours defined by the digital model. After the completion of the layer drawing, the process is repeated: the roller feeds fresh material and the laser starts to sinter the next layer. An attractive feature of this technology is the very high print resolution - about 20 microns on average. For comparison, the typical layer thickness in hobby and consumer printers using FDM/FFF technology is on the order of 100 microns.
Another interesting feature of the process is that there is no need to build supports for overhanging structural elements. The green powder is not removed during printing, but remains in the working chamber. Thus, each subsequent layer has a supporting surface. In addition, unused material can be collected from the build chamber after printing is completed and reused. DMLS production can be considered virtually waste-free, which is important when using expensive materials such as precious metals.
The technology has practically no restrictions on the geometric complexity of construction, and the high accuracy of execution minimizes the need for mechanical processing of printed products.
Advantages and disadvantages
DMLS technology has several advantages over traditional manufacturing methods. The most obvious is the possibility of rapid production of geometrically complex parts without the need for machining (the so-called "subtractive" methods - milling, drilling, etc.). Production is practically waste-free, which distinguishes DMLS from subtractive technologies. The technology allows you to create several models at the same time with a limitation only on the size of the working chamber. Building models takes about several hours, which is incommensurably more profitable than the casting process, which can take up to several months, taking into account the full production cycle. On the other hand, parts produced by laser sintering do not have solidity, and therefore do not achieve the same strength values as cast samples or parts produced by subtractive methods.
At the moment, DMLS machines are used only in a professional environment due to the high cost.
DMLS is actively used in industry due to the possibility of building internal structures of one-piece parts, inaccessible in terms of complexity to traditional production methods. Details with complex geometry can be made as a whole, and not from component parts, which favorably affects the quality and cost of products. Since DMLS does not require special tools (such as molds) and does not generate large amounts of waste (as is the case with subtractive methods), the production of small batches with this technology is much more profitable than with traditional methods.
Application
DMLS technology is applied to the production of small and medium-sized finished products in various industries, including aerospace, dental, medical, etc. The typical size of the construction area of existing plants is 250x250x250mm, although there are no technological restrictions on size - it is only a matter of cost devices. DMLS is used for rapid prototyping, reducing the development time of new products, as well as in production, reducing the cost of small batches and simplifying the assembly of complex geometric shapes.
Photos of Super Draco rocket engine parts released by Space X founder Elon Musk
Northwest Polytechnic University of China uses DMLS systems to produce aircraft structural components. Research conducted by EADS also indicates cost and waste reductions when using DMLS technology to produce complex designs in single or small batches.
On September 5, 2013, Elon Musk posted photos of a Super Draco rocket motor part made from Inconel nickel-chromium superalloy using an EOS printer.
Materials
Almost all metals and alloys in powder form can be used as consumables. To date, stainless steel, cobalt-chromium alloys, titanium and other materials have been successfully used.
3D Printing Technologies
- Mask Stereolithography (SGC)
- Multi-Jet Simulation (MJM) Technology
- Color Inkjet (CJP)
- Digital LED Projection (DLP)
- 3D Inkjet Printing (3DP)
- Selective Laser Sintering (SLS)
- Selective laser melting (SLM)
- Stereolithography (SLA)
- Selective heat sintering (SHS)
- Lamination of objects (LOM)
- Electron Beam Melting (EBM)
- Electron Beam Fusion Manufacturing (EBFȝ)
- Fused Deposition Modeling (FDM)
Go to the main page of the Encyclopedia of 3D printing
Talking about DMLS printing, 3D printing of metal objects
A few years ago, the ability to create metal objects of an impossible shape from scratch seemed like science fiction, but 3D printing of metal objects has become a reality, and in recent months it has become very popular.
We explain how DMLS technology, laser direct metal synthesis, works.
Index
- 1 DMLS, Metal 3D Printing
- 2 Design Limitations
DMLS, Metal 3D Printing
It uses high power laser to glue you selectively particles metallic. Finished layer by layer , with the machine spreading a new layer of metal powder after sintering one layer. It is important to pay attention to support structures may be required. However, these structures are generated automatically and subsequently will be removed manually . After printing is completed, the final heat treatment is carried out.
One of the most suitable metals to use with this technology is aluminum . Models printed in aluminum have the characteristics of very strong, accurate and they can handle 0. 25mm parts of . Aluminum 3D printing is often used to make fully functional parts as well as spare parts, but aluminum is also very suitable for jewelry printing.
Design Limitations
As with other technologies, some technical limitations must be considered. In the minimum wall thickness must be 0.5 mm for small surfaces (up to 15 mm x 15 mm) and not less than 1 mm for large sections .
technology DMLS allows The level of detail of is very good, even as small as 0.25mm . However, for a fine finish such as embossed or engraved text you must respect Minimum line thickness 0.4 mm, minimum height 0.4 mm and minimum depth 0.15 mm .
When creating models for 3D printing on aluminum, you need to think about the geometry of your design. Angled shapes, right angles, and straight lines can look a little less attractive compared to freestanding or organic shapes. However, this is better to have corners sheer over 35° because they are likely to have a better and smoother surface. Angles less than 35° and suspended structures tend to have lower surface quality.
Support structures are required to keep your model rigid during printing and to prevent internal stress and deformation. If we do not use support structures, walls or ledges with angles below 40° would be in danger of collapsing during the printing process.
If you are interested in how metal objects are printed, but you do not have access to a group with these characteristics, you can always choose send your parts to online printing services Such as to materialize.
More and more websites specialize in printing using materials and methods that we do not have direct access to as individuals. This one is a good choice so that the development community can access new production methods but maybe it's something King use it constantly .