Pakistan 3d printer
OBJEXYZ PLAY – OBJEXYZ
INTRODUCING
OBJEXYZ PLAYOBJEXYZ PLAY is your unswerving and reliable creative partner that 3d prints intricate features with attention to detail and provides smoother surface finish for the project of your dreams.
Rs. 90,000/- Only
Sturdy and Efficient
We built PLAY keeping the highest quality standards in mind. The sturdy aluminum and carbon steel parts last 100x more than plastic and produce premium quality 3d prints without breaking a bank.
Engineering Redefined
With PLAY, we redefined how 3d printers are built. Our engineering team took five separate components and introduced them into a single metal part in the X-axis. What they built now delivers a promise of lifelong durability.
Built for You and All of Them
Suitable for all environments, PLAY’s hotend that reaches a temperature of up to 250C is enclosed with a metal cover to ensure safety by all means. Users of any skill level or age can now enjoy being creative without any fear of accidental touches.
Salient Features
Plug n Play
Silent Performance
Ready to Print out of the box
0.4mm Nozzle
Request a sample
Request a sample from preselected sample 3D Prints delivered to your home, you can chose item based on your industry.
Brilliant Print Quality
Achieve extremely high details with your OBJEXYZ PLAY 3D Printers upto 0.075mm layer resolution.
Micron Layer Resolution
Previous
Next
Ample Connectivity
Use your 3D Printer in standalone mode with SD Card or USB Thumbdrive with the built in Touch Screen LCD or power your prints directly from the PC via USB cable.
1 Year Warranty
Even with the highest build quailty and reliability features OBJEXYZ PLAY comes with 1 Year of parts replacement warranty and after sales support so you can rest assured you are in safe hands.
Born and Built in Pakistan
PLAY is proudly designed and manufactured in Pakistan. We offer the most reliable, durable and, built-to-last product while keeping the stringent quality control in-check. OBJEXYZ leads the way to prove that you can produce a premium product locally.
What's included in the Box ?
USB CableToolkitPower adapterSpatulaSpannerAllen KeysSample Filamentfilament holder START 3D PRINTINGNOW
Detailed Specifications
Print Resolution:
75-300 microns (0.075mm - 0.3mm)
Extruder Temperature:
Upto 230 CConnectivity:
SD Card, USB drive, USB Cable
Power Consumption:
150 Watt Max
Software:
Cura (Open Source)
Operating System:
Windows, MAC OS
Power Input:
220V AC - 12V / 10A DC via Adaptor
Physical Dimension:
430 x 380 x 350mm (HWD)
Build Volume:
200x200x200mm* (8 x 8 x 8in)
Printing Technology:
Fused Deposition Modeling
Material Diameter:
1.
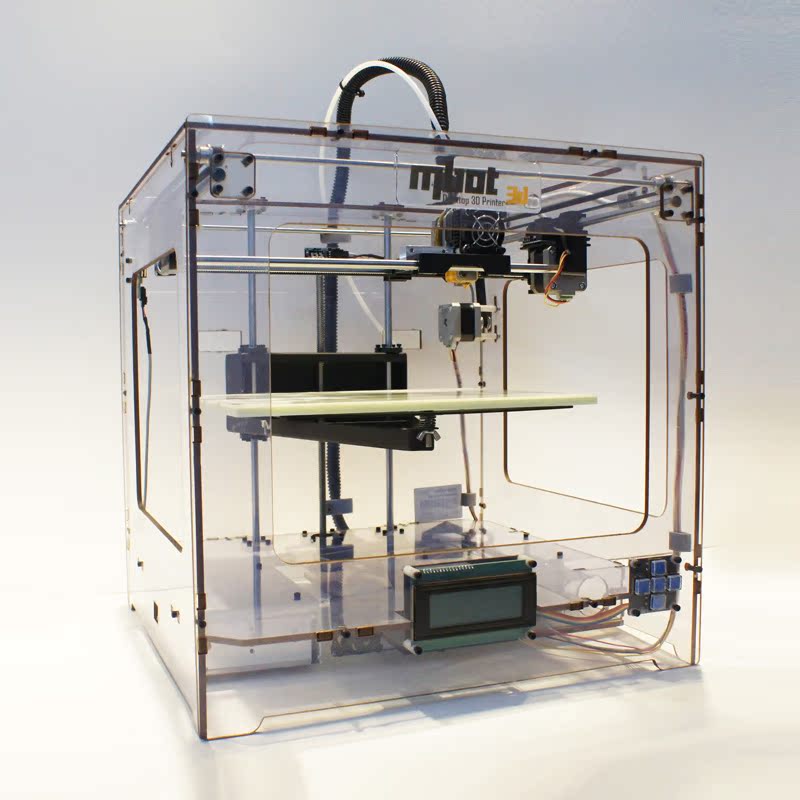
Materials:
PLA, PLA CF, PLA Composites, TPU.
Nozzle Diameter:
0.4mmHeatbed
: NoneInterface:
Standalone operation via Touch Screen LCD
File Type:
STL, OBJ.
Facebook Instagram Youtube Linkedin
Copyright © 2022 OBJEXYZ (Pvt) Ltd.
3D printers and national security
ISLAMABAD: While the world is fighting a pandemic and preparing for an impending recession, it seems trivial to discuss 3D printers. But this trivial example does indicate bigger issues at work in public policy.
For starters, the 3D printing process builds a three-dimensional object from a computer-aided design model, usually by successively adding material layer by layer, which is why it is also called additive manufacturing.
The world is entering the fourth industrial revolution, which is mostly based on technologies like robotics and 3D printing. Engineers and designers are now already working remotely and making products with high precision using 3D printers.
3D printing offers an excellent avenue to improve housing, food supplies, healthcare and educational facilities. Due to the intricate nature of the emerging trend of Internet of Things (IoT), no country can afford to restrict the use of 3D printers.
Unfortunately, Pakistan has rather restrictive policies for the import of 3D printers, with the procedure being cumbersome and time-consuming. In 2016, Pakistan placed a ban on the import of 3D printers, citing threats to national security as these printers could be used to manufacture illicit weapons.
While it is correct that some components of weapons can be made through this technology, 3D printing of the most important parts like the chamber or the barrel is extremely difficult, requiring high resistance to heat and explosion. It is much easier to make such parts from a milling machine than a 3D printer.
Countries like Jordan and Thailand, which had imposed restrictions, have now allowed the import to kick-start innovation in industries, healthcare and educational sectors. It is high time for Pakistan to take cue from these countries and allow the import of 3D printers with minimum restrictions.
Currently, Pakistan faces an acute shortage of ventilators amid Covid-19 pandemic. In addition, the shortage of other healthcare products such as face masks and personal protective equipment for healthcare workers is also posing serious challenges.
In this regard, the 3D printing technology can play a pivotal role in meeting the high demand for such essential commodities. It will not only benefit the health sector but also other sectors such as academic institutions, industries and housing.
However, this is possible only if the government allows for and streamlines the import of 3D printers. In Pakistan, awareness of 3D modelling and printing is gradually increasing and members of the academia, along with industries, are now approaching the laboratory.
3D printers are being used in some areas of the educational, engineering and health sectors. For example, a group of volunteers in Lahore, which includes doctors, biomedical professionals, academics and engineers, has used 3D printing technology to design a device that allows a single ventilator to support multiple patients at a time.
It seems imperative that an ease in regulation rather than strict restriction should be the government’s priority when it comes to handling the proliferation of 3D printer technology, and any such platforms which allow more choices, more competition and more innovation.
Recently, the Ministry of Commerce has issued a notification, allowing the import of 3D printers to ensure the availability of ventilators.
However, it would take some time to see its benefits due to the time needed for import and setting up the technology. In fact, given global restrictions on supply chains, this may be already too late.
What are the bigger issues, which we can discern from this episode of myopic thinking?
If we continue to restrict the use of such technologies, the digital divide between us and the rest of the world will accentuate. We will lose many opportunities of experimentation, trial and innovation, which are preconditions for growth. The coronavirus pandemic is also a good reminder that the national security paradigm, which is cited for restrictions on this technology (and certainly not limited to Pakistan), needs radical transformation.
The security should be defined in terms of human welfare, individual freedom and freedom of technology instead of relying on archaic modes of governance that requires a top-down approach.
The writers are associated with an independent think tank, PRIME, based in Islamabad
Published in The Express Tribune, May 4th, 2020.
Like Business on Facebook, follow @TribuneBiz on Twitter to stay informed and join in the conversation.
What Does Resolution Mean in 3D Printing?
Looking for a high resolution 3D printer? “Resolution” is a term from the field of 3D printing and additive manufacturing that is often talked about, while rarely understanding its meaning. How does XY and Z resolution affect the quality of 3D printed models? What is the minimum element size and what layer thickness should I choose?
This detailed guide explains how 3D printer resolution affects model printing and how it differs between SLA, FDM and DLP printers.
For decades, technology manufacturers have been striving for higher resolution than their competitors. TVs have recently quadrupled their pixel count from HD to 4K, but manufacturers are already thinking about pushing the resolution to 8K. Mobile phones, tablets and other devices with screens show resolution as one of the main characteristics, if, of course, they have something to brag about. But this is nothing new. Resolution wars have been fought since digital became popular and the printing industry became one of the first battlegrounds.
If you lived in the 80s and 90s, you'll remember how Canon, Brother, HP, Epson, and Lexmark (among others) sought to improve print speed and resolution. 100 x 100 dpi quickly grew to 300 x 300, then to 600 x 600. Finally, now the standard resolution is 1200 x 1200 dpi. Then these values were extremely clear, and the use of units of measurement was quite logical. Unfortunately, things get much more complicated when you add another dimension to print.
The level of detail of the model depends on the resolution of the 3D printer in all three dimensions.
In 3D printing and additive manufacturing, there are three dimensions to consider: two planar 2D dimensions (X and Y) and a third dimension, Z, which is used for 3D printing. Since planar measurements and Z measurements are usually controlled by completely different mechanisms, their resolutions will differ. Therefore, they must be considered separately. As a result, there is a lot of confusion about the interpretation of the term "3D printing resolution" and false expectations for print quality.
Experience the quality of stereolithography for yourself. We will send a free sample of the Formlabs stereolithographic 3D printed model directly to your office.
Request a free print sample
Formlabs high-resolution stereolithographic 3D printers feature high Z-axis resolution and a low minimum element size on the XY plane, allowing them to capture fine details.
What affects the high resolution of a 3D printer? It is impossible to name any one isolated factor. Since 3D printers produce models in 3 dimensions, there are at least two factors to consider: the minimum size of the XY plane elements and the resolution of the Z axis (thickness or height of the layer). Z-axis resolution is easy to determine and is therefore more commonly reported, although it is less related to print and surface quality. The more important XY resolution (minimum element size) is measured with a microscope and is therefore not always found in specifications.
In practice, this means that the 3D printer must perform well in both categories (in all 3 dimensions).
White Paper
Download our White Paper to find out how SLA printing works, why thousands of professionals use it today, and how this 3D printing technology can help your work.
Download white paper
A lot has changed since the first desktop 3D printers hit the market. Now stereolithographic (SLA) 3D printers such as the Form 3 directly compete for desktop space with Fused Deposition Modeling (FDM) 3D printers. One of the main advantages of 3D printers that use polymers as consumables over their plastic-melting counterparts is print quality: SLA printers produce models with a smoother surface and a higher degree of detail. While stereolithography printers typically achieve significantly thinner layer thicknesses, the reason for the improved print quality is the much higher XY resolution.
SLA printers (right) have higher resolution and produce models with smoother surfaces and more detail than FDM printers (left).
Unlike 3D printers based on FDM technology, the minimum size of elements in the XY plane in stereolithographic 3D printers is not limited by the dynamics of the flow of molten plastic, but is more determined by the optics and kinetics of radical polymerization. Although the calculations are complex (and beyond the scope of this article), it can be said that the details on models produced by stereolithography printers are about the same size as the diameter of the corresponding laser spots. And laser spots can be very small, especially when compared to nozzles on FDM printers.
Check out our detailed guide comparing FDM vs. SLA 3D printers to see how they differ in terms of print quality, materials, application, workflow, speed, cost, and more.
Technologies Resin-based 3D printing such as SLA, LFS and DLP provide the highest resolution of all 3D printing processes available for desktop printers. The primary units of measure for SLA and DLP processes are different forms, making it difficult to compare printers on a purely numerical basis.
DLP-based 3D printers have a fixed pixel matrix relative to the work area, while SLA- and LFS-printers that use a laser can focus the laser beam on any coordinate of the XY plane. This means that laser 3D printers with high optical quality can accurately reproduce the surface of the model, even if the laser spot size is larger than the pixel size in the DLP printer.
Whichever resin 3D printing technology you choose, professional 3D printers should capture the finest details of your creations, from photorealistic models to fine jewelry.
When printing on 3D printers based on SLA and LFS technologies (left), layer lines are almost invisible. As a result, surface roughness is reduced, resulting in a smooth surface, and when using transparent materials, models with greater transparency. DLP printers use rectangular voxels to render images, which can result in vertical lines (right).
Learn more about the differences between SLA and DLP technologies in terms of resolution, accuracy, clarity, print volume, surface quality, speed, and how they work.
In the world of 3D printing, no other factor affects the quality of models more than XY resolution. She is often mentioned, but rarely understood. The definition of XY resolution (or horizontal resolution) differs depending on the 3D printing technology:
- stereolithographic 3D printers - a combination of laser spot size and the size of the steps with which the beam can be controlled;
- DLP printers - pixel size, the smallest detail that a projector can reproduce in a single layer;
- FDM printers - the smallest distance that the extruder can move within one layer.
Generally, the lower this value, the finer the detail. But this number is not always indicated in the technical specifications, and even if indicated, it is not always correct. To get an idea of true XY resolution, it is important to understand how a printer works.
How does XY resolution affect the quality of your models? To find out, we decided to test a Form 2 stereolithographic 3D printer. The size of the laser spot in the Form 2 printer is 140 µm (FWHM), which should allow it to reproduce fine details on the XY plane. We decided to check if this ideal resolution corresponds to the truth.
To test the minimum feature size on the XY plane for the Form 2 printer, we designed a model (left) with lines ranging from 10 to 200 µm thick and printed it using Clear Resin (right).
We first designed and printed the model to check the minimum element size on the XY plane. The model is a rectangular block with lines of various widths in the horizontal, vertical and diagonal directions, which are applied to prevent displacement. The line thickness is from 10 to 200 µm, the lines are drawn at 10 µm intervals and have a height of 200 µm, which corresponds to two layers when printed at a resolution of 100 µm for the Z axis. Made from Clear Resin, the model was washed twice in isopropyl alcohol and subjected to a within 30 minutes.
The model was photographed and painted green for better visibility. The vertical yellow line with black dots on the right side of the window is for measuring the width of the photographed line.
After the final polymerization, we placed the model under the microscope and took a high resolution photograph for further analysis. Using ImageJ, a free image analysis program from the National Institutes of Health (NIH), we scaled the image pixels and measured the actual width of the printed lines. We collected over 50 data points per line width to eliminate measurement errors and variability. We analyzed three models made on two printers.
The results show that the Form 2 has the same ideal and actual XY resolution for model elements as small as 150 µm.
As the line width decreases from 200 to 150 µm, the ideal values are within the 95% confidence interval of the measured value. As the expected linewidth becomes less than 150 µm, the measured interval starts to deviate significantly from the ideal. This means that the printer can reliably reproduce elements up to 150 microns in size, as thick as a human hair, on the XY plane.
The Form 2 printer has a minimum feature size on the XY plane of about 150 µm, only 10 µm larger than the spot size of the laser installed in it (140 µm). The minimum element size cannot be less than the laser spot size. There are many factors that affect this value: laser refraction, microscopic contaminants, polymer chemistry, etc. Considering the entire printer ecosystem, a difference of 10 µm is nominal. Not all 3D printers have the reported resolution as the actual resolution, so it's a good idea to do a lot of research before choosing the right resolution for your project.
If you want models with fine detail, look for a printer whose XY resolution is not just listed as a number, but supported by measured data.
When looking at the specifications of 3D printers, you will find that one parameter appears more often than any other. This is the Z-axis resolution. Also known as layer thickness or layer height, vertical resolution was the first major numerical parameter by which early 3D printers were distinguished. The first such devices struggled to overcome the barrier of 1 mm, but now the layer thickness in FDM-based 3D printers can be less than 0. 1 mm, and even less in LFS and SLA printers.
Formlabs 3D printers support layer thicknesses from 25 to 300 microns, depending on the material. This range of values allows you to find the perfect balance between speed and print quality. But the main question is what layer thickness will be ideal for your model.
The high resolution of 3D printing affects other parameters. The thinner the layer, the more layers need to be printed, resulting in increased model production time: typically, printing at a resolution of 25 µm takes four times longer than printing at a resolution of 100 µm. In addition, the more layers, the higher the probability of errors. For example, even with a layer success rate of 9A 9.99% fourfold increase in resolution reduces the chances of a successful print of the model from 90% to 67%, provided that the layer with the error leads to rejects.
The thinner the layer, the longer it takes to print and the more likely it is to cause errors and distortion.
Is it true that the higher the resolution (the thinner the layers), the higher the quality of the finished models? Not always. It depends on the model and resolution of the XY 3D printer. As a general rule, the thinner the layer, the longer it takes to print and the greater the chance of distortion and errors. In some cases, printing models at a lower resolution (i.e., with thicker layers) may even result in better quality.
Thinner layers are usually associated with smoother diagonal transitions, causing many users to push Z resolution to the limit. But what if the model consists mostly of vertical and horizontal faces, with right angles and a small amount of diagonal surfaces? In such cases, increasing the number of layers will not improve print quality.
The problem is exacerbated if the printer's XY resolution is not ideal and it "goes out of bounds" when forming the outer edges. The more layers, the more mismatched protrusions will be on the surface. In this case, the finished model will look much worse, even if the Z resolution is higher.
There are times when you need to increase the resolution. If you have a printer with good XY resolution and a model with complex features and many diagonal faces, reducing the thickness of the layers will allow you to get a physical model of much better quality. Also, if this model is small (no more than 200 layers), then increasing the resolution of the Z-axis will lead to a real improvement in quality.
Some designs benefit from higher Z resolution: organic shapes, rounded arches, fine embossing and intricate engraving.
A tiny model with lots of detail and arches needs a higher Z resolution. This cathedral was printed on a Form 2 printer at 25µm resolution.
Try to stick to this general rule: print thicker layers and increase the Z resolution only when it is really necessary. With the right combination of printer and model type, the higher Z resolution will capture the intricate details of your design.
Gray Resin allows printing at a resolution of 160 microns. Check out the difference in speed for yourself.
Formlabs PreForm software allows you to select the layer thickness. Starting with version PreForm 3.0.3 , Gray Resin can be printed in 160, 100, 50 and 25 µm layer heights. Printing at a resolution of 160 microns will speed up the iteration process and allow engineers to move from design to finished model even faster. And dentists can make more aligners per day without sacrificing quality.
We hope that once you are familiar with the concept of resolution and understand the differences in 3D printing technologies and results, it will be much easier for you to choose a 3D printer that best suits your needs and workflow.
To learn more about the next generation of stereolithographic 3D printers, check out the Form 3 and Form 3L devices based on LFS technology.
Want to see for yourself what high-resolution prints look like? Order a print sample, which will be delivered directly to your office.
Learn how stereolithography 3D printing technology works
3D printer: what is it and how does it work? | GeekBrains
https://gbcdn.mrgcdn.ru/uploads/post/1999/og_image/501bb6c82a53bb3bc2a0fee73b0c9e9e.png
In 2011, a printer filled with a human kidney TED printed directly during a TED conference. Two years ago, Adidas announced a new sneaker that can be 3D printed in 20 minutes. And recently, Elon Musk's SpaceX successfully tested the spacecraft's engines, which were also printed on a 3D printer.
In today's world, 3D printing is not an amazing technology of the future, but a well-studied reality. It is used in architecture, construction, medicine, design, production of clothing and footwear and other areas. At the request of "3D printer", search engines give out hundreds of drawings and prototypes of varying complexity - from a soap dish and a table lamp to a car engine and even a residential building.
Anyone can buy a printer and print a case for a smartphone, but not everyone goes beyond 3D printing from a drawing. In this article, we will tell you when 3D printing appeared, how the technology can be applied and what its prospects are.
How the 3D printer came to be
Let's not bore you too much with the dates and briefly retell the history of 3D printing.
A precursor to 3D printing. In the early 1980s, Dr. Hideo Kodama developed a rapid prototyping system using photopolymer, an acrylic-based liquid substance. The printing technology was similar to the modern one: the printer printed the object according to the model, layer by layer.
First 3D printing. The production of physical objects using digital data was demonstrated by Charles Hull. At 19In 84, when computers were not much different from calculators, and ten years before the release of Windows-95, he invented stereolithography, the forerunner of 3D printing. The technology worked like this: under the influence of an ultraviolet laser, the material solidified and turned into a plastic product. The form was printed on digital objects, and this became a boom among developers - now it was possible to create prototypes at a lower cost.
The first 3D printer. Source: habr
The first manufacturer of 3D printers. Two years later, Charles Hull patented the technology and opened the 3D Systems printer company. It released the first machine for industrial 3D printing and is still leading the market. True, then the printer was called differently - an apparatus for stereolithography.
The popularity of 3D printing and new technologies. In the late 80s, 3D Systems launched mass production of stereolithographic printers. But by that time, other printing technologies had also appeared: laser sintering and deposition modeling. In the first case, the powder was processed by the laser, not the liquid. And the majority of modern 3D printers work according to the fusing method. The term "3D printing" came into use, the first home printers appeared.
A revolution in 3D printing. At the beginning of the 2000s, the market split into two directions: expensive complex systems and those that are available to everyone for printing at home. The technology began to be used in specific areas: for the first time, a bladder was printed on a 3D printer, which was successfully implanted.
Kidney Test Print. Source: BBC
In 2005, the first high-quality color 3D printer appeared, creating kits for itself and "colleagues".
How a 3D printer works
Basically, 3D printers consist of the same parts and are similar in design to conventional printers. The main difference is obvious: a 3D printer prints in three planes, and in addition to width and height, depth appears.
Here are the parts of the 3D printer, not counting the body:
- extruder or print head - heats up the surface, measures the exact amount of material using a gripping system and squeezes out semi-liquid plastic, which is fed in the form of threads;
- desktop (it is also called a working platform or printing surface) - on it the printer forms parts and grows products;
- linear and stepper motors - set the parts in motion, are responsible for the accuracy and speed of printing;
- clamps - sensors that determine the print coordinates and limit moving parts.
They are needed so that the printer does not go beyond the desktop, and make printing more accurate;
- frame - connects all elements of the printer.
Schematic of a 3D printer. Source: Lostprinters
All of this is computer controlled.
How products are created
An additive 3D printing process is responsible for creating a three-dimensional product - this is when layers of material are superimposed on each other, from bottom to top, until a copy of the form in the drawing is obtained. This is how plastics are printed. And photopolymer printing works on stereolithography (SLA) technology: under the influence of a laser emitter, photopolymers harden. In addition to plastic and photopolymer resins, modern 3D printers work with metal clay and metal powder.
Printing consists of continuous cycles that repeat one after another - one layer of material is applied to the next, and the print head moves until the finished object is on the working surface. The printer itself removes print waste from the desktop.
How a 3D drawing works
The printer prints a product according to a 3D drawing: it is created on a computer in a special program, then saved in STL format. This file is output to the cutting program for the printer - it helps to set the model of the physical properties of the product, such as density. Next, the program converts the model into instructions for the extruder and uploads it to the printer, which starts printing the product.
3D drawing is easy to make at home - read the instructions on habr.
How to program a 3D printer
Brief instructions for setting up the printer:
- Select a 3D model. You can draw the product yourself in a special CAD editor or find a ready-made drawing - the Internet is full of models of varying complexity.
- Prepare 3D model for printing. This is done by the slicing method (slice - part). For example, in order to print a toy, its model must be “split” into layers using slicer programs and transferred to the printer.
Simply put, the slicer shows the printer how to print the object: which contour to move the print head, at what speed, what thickness of the layers to make.
- Transfer model to printer. From the slicer, the 3D drawing is saved to a file called G-code. The computer downloads the file to the printer and starts 3D printing.
- Monitor printing.
Whether printed products can be used
Depends on the quality of the media, printer and end product. Often home printers do not accurately convey the shape and color of an object. Plastic products need additional processing: sometimes they are printed with burrs and defects, and almost always with a ribbed surface.
Product after and before processing. Source: 3D-Today
There are several ways to finish the surface - not all are suitable for home use:
- mechanical processing - hand sanding, deburring;
- chemical - immersion in acetone, sandblasting, applying a special solution with a brush.
What can be printed with a 3D printer
The Internet is full of collections with instructions for printing 3D products. 3D-Today publishes photos of the work of printer owners, from small parts to sculptures. Three years ago, Habré posted a list of "50 cool things to print on a 3D printer." Make3D wrote about larger projects like printing cars, weapons, solar panels, and prosthetics.
There are a number of promising areas where 3D printing is already being applied.
Making models according to your own sketches. Konstantin Ivanov, the creator of the 3DPrintus service, in an interview with Afisha said that 3D printing will lead to the flourishing of customizable things: anyone can assemble and print the desired product online. For example, make a model of a robot and order its printing on an industrial printer, create and print your own design of wedding rings or shoes. Examples of such projects are Thinker Thing and Jweel.
Rapid prototyping. The most popular area in which 3D printing is used. Test models of prostheses, prototypes of medical corsets, bas-reliefs, Olympic equipment are made on 3D printers.
Prototypes of children's prostheses, 3D printing. Source: 3D-Pulse
Complex geometry. The 3D printer can easily handle the production of models of any shape. A few examples:
- an Australian university explored the possibilities of a 3D printer and printed a stool in the shape of a fingerprint;
- a Danish chef won a haute cuisine competition: he 3D printed miniature dishes of complex shapes from seafood and beetroot puree;
One of the chef's winning dishes. Source: 3D-Pulse
- A German institute has developed a system for accelerated 3D printing - in 18 minutes, the printer produces a complex geometric product 30 cm high. It usually takes printers an hour to print pocket figures.
3D printing technology
Briefly about the main methods of 3D printing.
Stereolithography (SLA). In a stereolithographic printer, a laser irradiates photopolymers and forms each layer according to a 3D drawing. After irradiation, the material hardens. The strength of the product depends on the type of polymer - thermoplastic, resins, rubber.
Stereolithography does not support color printing. Other drawbacks include slow operation, huge size of stereolithographic setups, and you can't combine multiple materials in one run.
This technology is one of the most expensive, but guarantees accurate printing. The printer applies layers with a thickness of 15 microns - this is several times thinner than a human hair. Therefore, with the help of stereolithography, dental prostheses and jewelry are made.
Industrial stereolithography machines can print huge products, several meters long. Therefore, they are successfully used in the production of aircraft, ships, defense industry, medicine and mechanical engineering.
Selective laser sintering (SLS). The most common method for sintering powder materials. Other technologies are direct laser sintering and selective laser melting.
The method was invented by Carl Descartes in the late eighties: his printer printed by layer-by-layer drawing (sintering). A powerful laser heats up small particles of material and moves along the contours of the 3D drawing until the product is finished. The technology is used to manufacture not whole products, but parts. After sintering, the parts are placed in an oven where the material burns out. SLS uses plastics, ceramics, metals, polymers, fiberglass in powder form.
The athlete is wearing New Balance shoes, which were made using laser sintering. Source: 3D-Today
SLS technology is used for prototypes and complex geometric parts. For printing at home, SLS is not suitable due to the huge size of the printer.
FDM or Fused Deposition Modeling. This 3D printing method was invented by American Scott Crump. FDM works like this: the material is fed into the extruder in the form of a thread, where it heats up and is fed to the worktable in microdroplets. The extruder moves along the working surface in accordance with the 3D model, the material cools down and solidifies into the product.
Advantages - high product flexibility and temperature resistance. For such printing, different types of thermoplastics are used. FDM is the most inexpensive among 3D printing technologies, which is why printers are popular for home use: for making toys, souvenirs, and jewelry. But mostly fusing modeling is used in prototyping and industrial production - printers quickly print small-scale batches of products. Refractory plastic items are made for the space industry.
3D inkjet printing. One of the first methods of three-dimensional printing - in 1993, it was invented by American students when they improved a conventional paper printer, and soon the technology was acquired by the same company 3D Systems.
Inkjet printing works like this: a binder is applied to a thin layer of material along the contours of the drawing. The print head applies the material along the boundaries of the model, and the particles of each new layer stick together. This cycle is repeated until the product is ready. This is one of the types of powder printing: earlier inkjet 3D printers printed on plaster, now they use plastics, sand mixtures and metal powders. To make the product stronger, after printing it can be impregnated with wax or fired.
Items printed using this technology are usually durable, but not very durable. Therefore, with the help of inkjet printing, souvenirs, jewelry or prototypes are made. This printer can be used at home.
These candies were made on a ChefJet 3D confectionery inkjet printer that uses water, sugar, chocolate and food coloring instead of plastic. Source: 3Dcream.ru
Inkjet technology is also used in bioprinting, where living cells are layered on top of each other and thus organic tissues are built.
Where 3D printing is used
Mainly in professional fields.
Construction. 3D printers print walls from a special cement mixture and even houses with several floors. For example, back in 2014 Andrey Rudenko printed a 3 × 5 meter castle on a construction printer. Such 3D printers can build a two-story house in 20 hours.
Medicine. We have already mentioned the printing of organs, and 3D printers are also actively used in prosthetics and dentistry. Impressive examples - with the help of 3D printing, doctors managed to separate Siamese twins, and a cat without four legs was given prostheses that were printed on a printer.
Read more about 3D printing in medicine in the article published by 3D-Pulse.
Space. 3D printing is used to make equipment for rockets and space stations. Another technology is used in space bioprinting and even in the work of lunar rovers. For example, the Russian company 3D Bioprinting Solutions will send live bacteria and cells into space, which will be grown on a 3D printer. Amazon founder Jeff Bezos unveiled a prototype lunar module with a printed engine, and space startup Relativity Space is building a rocket 3D printing factory.
Aviation. 3D parts are printed not only for spacecraft, but also for aircraft. Engineers at the US Air Force Lab can 3D print aircraft components, such as a fuselage skin element, in about five hours.
Architecture and industrial design. 3D printers print models of houses, neighborhoods and villages, including infrastructure: roads, trees, shops, lighting, transport. As a material, an inexpensive gypsum composite is usually used.
One of the unusual solutions is the design of concrete barricades by American designer Joe Ducet. After the terrorist attacks with trucks that crashed into a crowd of people, he proposed a model of durable and functional barriers in the form of a designer, which can be printed on a 3D printer.
UrbaStyle, a company that prints concrete molds on 3D construction printers, helped make the prototype.