Nasa 3d printer wrench
3D printing hands on: Attempting to print a NASA wrench
It costs about a thousand dollars to loft a pound of anything into space. Scientists, astronauts, and project managers are therefore understandably careful about what they choose to send to the International Space Station.
Years of careful planning precede any launch and determine the contents of any launch payload. But as we all know, plans change when they encounter reality. So what happens when an astronaut on the space station needs something that didn't get packed into a shuttle payload?
They make do. The most famous example of the make-do spirit was the Apollo 13 mission, where - after an oxygen tank exploded in the command module - the astronauts had to survive in the lunar module. To do so, they had to build a carbon dioxide scrubber adapter from found parts, which consisted of the cover of the flight manual, duct tape, a pair of socks, and various other components.
While emergencies will undoubtedly still happen in space, and creativity and resourcefulness will still be necessary, NASA researchers have been working on an approach that could provide space station astronauts with a supply of objects, tools, and components using 3D printing.
This is an extremely powerful idea. Think about the general-purpose computer. Once it was possible to create one device that could run many different programs, the computer because an enormously flexible machine. It could be built and installed well before all of its uses were defined or even discovered. When a new program was needed, that program could be coded, and the same physical piece of machinery could run everything from inventory replenishment calculations to plotting missile trajectories - which have reached their cultural culmination in the computation of the flight path of small birds aimed at clusters of small, green pigs.
The general purpose computer is a single machine that can run a wide variety of programs. Likewise, a 3D printer is a single machine that can produce a wide variety of objects.
Scientists at NASA have seen the potential. This one machine can live on the space station and generate an almost infinite variety of objects, tools, and parts. Instead of, for example, waiting for the next shuttle mission to loft a special-purpose wrench to the space station, engineers can just email an .STL file to an astronaut on the station, who can print it out and put it to use.
In fact, there is a 3D printer on the space station, made by the firm Made In Space, Inc. The printer is a fused deposition modeling (FDM) printer very similar to the desktop 3D printers we've been using here in the DIY-IT 3D printing discovery series. In fact, one of the test objects printed on the station's 3D printer was just such a wrench, a small socket wrench shown below.
NASA has even made plans of the wrench, in STL format, available online. So, I decided to download the file and give it a run in my MakerBot Replicator. A special shout-out of thanks goes to MakerBot for providing the printer for our DIY-IT discovery series.
Printing the wrench
Printing the wrench turned out to be a very simple project. All I did was load the wrench into my slicing program and send it to the printer. I did, however, run into a number of problems creating an actual working unit, but those problems were limitations in my tools, not in the file or the 3D printing concept.
I have a printer that is designed to print polylactic acid-based plastic, otherwise known as PLA. PLA is biodegradable and based on corn starch. It's a reliable printing material and has the benefit of not only being good to the planet, it doesn't generate the acrid plastic smell that acrylonitrile butadiene styrene (ABS) plastic is known for.
While PLA is an ideal printing material, it is a little more brittle than ABS. There are ABS printers out there, but they often require a heated build plate and an enclosed printing area. My printer has neither. If you want a good example of something created from ABS, think of Lego bricks. There are roughly 400 billion Lego bricks in the world, and all were made from ABS.
NASA's space station 3D printer is also designed to print ABS, so the wrench design was specifically intended for an ABS printer. I tried it on my PLA printer.
I disregarded the design specs in another way as well. I decided to use the slicing defaults of MakerBot desktop, which included setting a 10 percent infill. Infill is the amount of plastic used to fill solid spaces. Rather than filling the entire space with plastic, various infill percentages generate diamond or honeycomb shapes inside the object. These often provide good strength and both reduce the amount of plastic used and the time used to generate the print.
My first print used 10 percent infill, so as soon as I tried to wrench anything with my first printed wrench, it broke.
My second attempt was unsuccessful as well, because after a little while, the print started to warp, lifting up off the print base. This is because, as layers cool, there is a difference in temperature between the lower layers (which are cool) and the upper layers which are warm. The difference tends to pull the print up off the printing base, and so my second wrench print, this time printed with 100 percent infill (or completely solid) failed due to warping.
Given how long it takes for prints to complete (roughly five hours each), I ran out of time after two prints. You can watch my video at the beginning of the article to see the process in more depth.
Even though the project failed for me, I learned some valuable lessons. I gained a tangible lesson about the strength of the plastic and the relationship between infill percentage and strength. I got a chance to experiment with an actual tool design intended for the space station. I learned a bit about how warping takes place as you increase the infill percentage - and I learned more about build plate adhesion. Finally, I learned that even though this project didn't succeed in the time frame I had available, the discovery process is just that, all about discovery. By attempting this project, I learned a lot and had fun doing it.
If you decide to try making the wrench, especially if you do it with ABS, please let me know how it worked for you in the comment area below.
By the way, I'm doing more updates on Twitter and Facebook than ever before. Be sure to follow me on Twitter at @DavidGewirtz and on Facebook at Facebook.com/DavidGewirtz.
3D Print a Copy of NASA’s Space Wrench
0Shares
As we reported, Made In Space engineer Noah Paul-Gin recently digitally designed a ratchet wrench in Autodesk Inventor, NASA sent it up to the ISS, and Commander Butch Wilmore received and printed the first uplink tool in history. So what happens next? And, also, can I print one?
Yes, according to NASA, you can now print the same NASA space wrench among other cool STL files, such as replicas of Rosetta, Kepler, and the Mars Odyssey to name just a few. To see the full list of STL files from NASA, go to their 3D Resources (Beta) page.
What happens next is that this 4.48-inch-long by 1.29-inch-wide ratchet wrench will be returned to Earth for analysis and testing, along with a number of other parts printed in space. “We can’t wait to get these objects home and put them through structural and mechanical testing,” explained Quincy Bean, the principal investigator for the 3D printing experiment at NASA’s Marshall Space Flight Center. “We really won’t know how well this process worked in space until we inspect the parts and complete these tests.”
Before the 104 layers of plastic were deposited on the microgravity printer, NASA had to approve the object, which was unusual not because of its design qualities, but because of one simple fact: NASA would have to approve the transmission of an object that had not been physically launched from Earth. “Controllers in NASA’s Payload Operations Integration Center at Marshall have worked with investigators and students in more than 80 countries to send millions of commands from locations around the world to station experiments,” NASA reports. However, this was the first time a design file had been sent from the ground to fabricate a tool on the International Space Station.
“We wanted to work this just like we would for tools that the astronauts will 3-D print and use on the station,” explained Niki Werkheiser, the space station 3-D printer program manager at Marshall. “This wrench will not be used in space, but what if it were a tool the crew needed? We are breaking new ground not only in the way we manufacture in space but also in the way we operate and approve space hardware that is built in space, rather than launched from Earth.”
via NASA, “International Space Station astronaut Barry “Butch” Wilmore holds a science sample container that took two hours to make. The container was the first object to be printed with two parts: a lid and a container.Depending on the launch resupply schedule, it can take months or even years, to get equipment to space. For exploration missions, resupply from Earth may be impossible. This technology may drastically change how NASA completes exploration missions and conducts scientific research and experiments in the immediate and near future.
“If you can transmit a file to the station as quickly as you can send an email, it opens up endless possibilities for all the types of things that you can make from CubeSat components to experiment hardware,” Werkheiser said. “We even may be able to make objects that previously couldn’t even be launched to space.”
Exploring how the microgravity environment may benefit how objects are designed and built in space for parts that cannot be made on the ground, the ISS team printed one object that is extremely difficult to make on Earth because of sag caused by gravity.
So far, Astronauts have made objects with 13 different designs and built a total of 20 objects, making duplicates of some items. Of course, the ratchet is unique among them because the other 19 objects were preprogrammed into the printer before it left Earth. On the fourth SpaceX cargo resupply mission this past September, the same objects were printed on Earth with the same printer, before it launched to the space station, as a control group for the experiment.
NASA and Made In Space will use data from these tests to prepare for the second phase of printer operations scheduled to begin early next year. “For our next phase of operations, we are working with the astronaut office to identify existing tools that we can make with the printer.” Werkheiser said. “We can’t wait until it is routine to see station astronauts use tools that they built in space.”
Andrew Wheeler
Andrew Wheeler is a 3D printing and technology journalist. He studied Creative Writing at NYU and received his Bachelor's Degree in Information Technology. He is currently working on a multi-media science fiction project. His favorite journalist of all time is George Orwell.
NASA builds training simulator of a Martian colony using a 3D printer
News
own design.
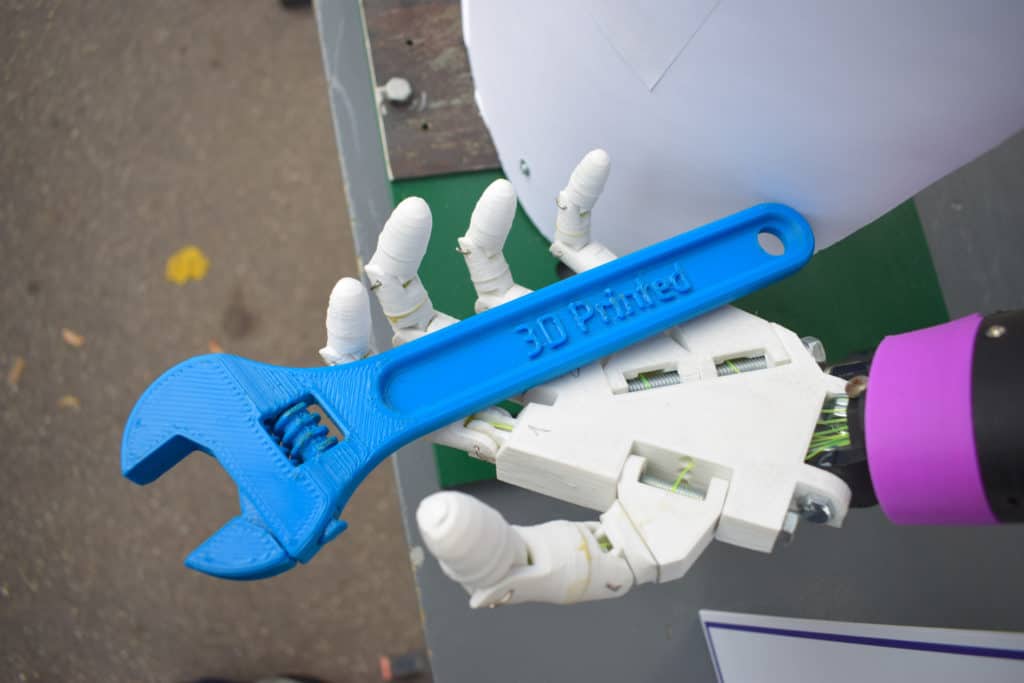
The first task is to build a building with an area of about 160 square meters. The building will then be used in the Crew Health and Performance Exploration Analog (CHAPEA) experiment, during which a team of imaginary colonists will live and work in conditions as close to Martian as possible. The experiment will last for twelve months, starting next autumn. In total, NASA plans to conduct three such experiments to study the impact of long-term expeditions on the physical, mental health and performance of astronauts. Not only people will be tested, but also equipment, such as systems for storing and preparing food.
We use the construction 3D printer Vulcan II developed by the Texas company ICON. This enterprise has already appeared in our news more than once with various projects - from the construction of affordable housing in Mexico and native Austin ( in the illustration above ) to the training of US Marines and experimental 3D printing of caponiers. Designed by BIG-Bjarke Ingels Group, the Martian House is being built in one of the hangars at the Lyndon Johnson Space Center in Houston, Texas.
In the long term, NASA is considering 3D printing already real Martian buildings, as it would be easier and cheaper in terms of logistics: it is easier to deliver relatively compact additive construction equipment and use Martian soil than to transport huge volumes of building materials from Earth. This side of the matter is also being investigated: as we reported yesterday, additional equipment and consumables have already been sent to the ISS for experiments on 3D printing of artificial regolith in microgravity conditions.
The design of the supposedly Martian house includes four bedrooms at one end of the building. At the other end there will be office space, including an infirmary. The central part will be occupied by common areas and a hydroponic garden.
ICON also received funding from NASA and launched Project Olympus, a research and development effort aimed at building additive space building equipment to support the Moon and later Mars exploration program.
construction NASA icon Mars Dune Alpha Mars
Subscribe author
Subscribe
Don't want
2
Article comments
More interesting articles
7
Subscribe to the author
Subscribe
Don't want
Monochrome liquid crystal matrices with increased sharpness, light transmission, durability. ..
Read more
6
Subscribe to the author
Subscribe
Don't want
A new method called iCLIP created with the participation of Professor DeSimon - co-founder and CEO ...
Read more
53
Subscribe author
Subscribe
Don't want
As we all know, a real 3D printer should have a solid acrylic body, high quality...
Read more
Made in space. How to "print" a satellite in orbit
Everyone who is even a little interested in astronomy has probably heard about the epic space telescope James Webb (James Webb Space Telescope). The super-expensive observatory was supposed to go into space eight years ago, but it was thoroughly delayed on Earth. The reason for this is the extremely complex design of the telescope. Due to its large dimensions, its mirror and heat shield simply “do not fit” under the head fairing of the Ariane 5 rocket. As a result, the designers had to make them collapsible. The spacecraft was “enriched” with thousands of new details. Failure of any of them could lead to the collapse of the mission, which would cause enormous damage to the reputation of NASA (not to mention the billions of dollars spent in vain). It is not surprising that the engineers sought to repeatedly check and recheck each structural element. And this, in turn, led to more and more launch delays.
In the near future, this approach should have a very promising alternative. Instead of launching a bulky structure with a complex deployment mechanism with a large rocket, or assembling some kind of structure from separate parts launched into orbit over several launches, it will be made right in space. So far it sounds like science fiction, but in recent years humanity has taken a number of important steps that have brought us very close to organizing real space production.
Made In Space
Any conversation about manufacturing in space should start with Made In Space. Unlike, for example, SpaceX, its name is practically unknown to the general public, which is somewhat unfair. After all, this company is a real pioneer, having tested a number of innovative technologies that, in the future, can significantly change our understanding of the space industry.
Made In Space was founded in August 2010. The name conveys the main goal of the company quite well - the development of technologies for creating various parts and devices in microgravity using 3D printing. Such technologies would greatly accelerate the process of exploration of near-Earth orbit and the entire solar system.
Testing a 3D printer in a "vomit comet" - an aircraft in which flights are carried out along a parabolic trajectory with imitation of weightlessness. The walls, floor and ceiling are finished with soft material. Source: nature.com In the spring of 2011, Made In Space acquired a laboratory at the Research Center. Ames (Ames Research Center - ARC). Then a contract was awarded to participate in the NASA-funded Flight Opportunities Program. Within its framework, the company got the opportunity to test an experimental 3D printer on a specially equipped aircraft designed to simulate being in zero gravity (NASA astronauts jokingly called this aircraft a “vomit comet”). During the flight, pilots direct the aircraft into a parabolic "free fall" trajectory, which allows for about 20-30 seconds to create the effect of the absence of gravity.
In total, Made In Space engineers have completed over 400 parabolic flights. Their hopes were fully justified. Experiments clearly demonstrated the possibility of 3D printing in zero gravity. As a result, the company was awarded a new grant - already under the SBIR (Small Business Innovation Research) program. He gave her the opportunity to test her 3D printer in real weightlessness in Earth orbit.
In November 2014, NASA astronaut Butch Wilmore installed a Made In Space 3D printer in the Columbus laboratory module on the US segment of the ISS.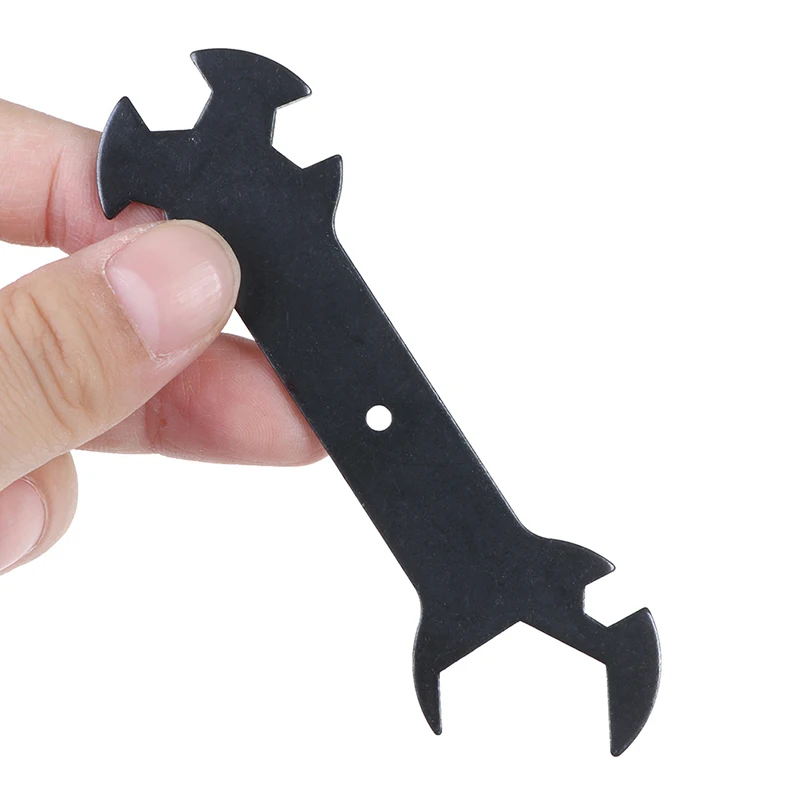
On September 21, 2014, another unmanned Dragon supply ship departed for the International Space Station. Among the many cargoes on board was a 3D printer built by Made In Space engineers. Two months later, a historic event occurred - the unit successfully printed a part on board the orbital complex. A month later, he "participated" in another historic achievement: the astronauts printed a ratchet mechanism on it. Its production differed from similar operations in that this time the file with the necessary information was not sent to the station on a hard drive (SD card), but transmitted via the Internet.
Butch Wilmore holds the first part printed aboard the ISS using the3D printer on November 25, 2014. Source: NASA
Successful tests of a 3D printer on the ISS have seriously changed the long-established "rules of the game". Space explorers got the opportunity to create the necessary items and tools on their own, without waiting for them to be "brought" on the next ship from Earth. This allowed the crew members to save time and perform their tasks more efficiently. In 2016, a real printing shop was launched on the ISS, called the Additive Manufacturing Facility (AMF). With its help, the station crew has already made several hundred tools, devices and components. For example, while studying the effects of radiation on the sensors of the inflatable BEAM module, astronauts 3D printed a series of shields of different thicknesses, and then used them as radiation shields.
Not surprisingly, NASA has decided to expand its collaboration with companies developing similar technologies. A few years ago, the agency initiated the Archinaut program. Its goal is to create a production center in orbit capable of printing large structures not in residential modules, but directly in outer space. In addition to Made In Space, Northrop Grumman and Oceaneering Space Systems are also members.
In 2017, Made In Space passed another major milestone by building and successfully testing the first ever 3D printer capable of operating in airless space. As part of a month-long test carried out inside the ARC vacuum chamber, the company's specialists managed to print polymer rods.
Stereolithographic 3D printer (SLA). Source: 3dPrint.com In the same year, Made In Space sent a new printer to the ISS for the production of optical fiber. It was developed in collaboration with Allevi. The peculiarity of the project is that the products of this printer are not intended for space, but for use on Earth. According to company representatives, the optical fiber produced in zero gravity has better bandwidth than that produced in the earth's gravity. July 2019the next step was taken. NASA has signed a new $73.7 million contract with Made In Space. Within its framework, the company will build the Archinaut One spacecraft equipped with a 3D printer. After reaching low Earth orbit, it should print two ten-meter solar arrays, similar to those installed on ESPA satellites. An Electron rocket will be used to launch the device, scheduled for 2022.
The success of Archinaut One could have a very serious impact on the entire space industry. The fact is that the dimensions of solar panels remain one of the factors limiting the size of launched vehicles. The transfer of their production to space will remove this limitation, which will positively affect many of the technical characteristics of satellites. In addition, it will be possible to create large structures in orbit that cannot be delivered into space using a rocket.
The future of space printing
The construction of large-sized structures and the production of satellite parts is, of course, very promising, but still far from the only area for the efforts of space printers. This technology can find its application in many other areas. Among them are manned missions into deep space. NASA is currently implementing the Artemis program. Its main goal is the construction of a lunar manned orbital station with the subsequent landing of a man near the south pole of the moon and the further prospect of creating a permanent settlement there. One of the main problems hindering the implementation of this and other similar large-scale programs is the truly astronomical cost of delivering any cargo from the Earth to the Moon.
The most obvious solution to the problem is to produce the required components on site. So, for the construction of the lunar base, it would be possible to use not imported modules, but blocks “printed” from regolith using specialized 3D printers. Relevant projects are already being developed in the US, Europe and China. Moreover, in the future, such technology would be useful in the construction of a Martian settlement.
This is how the dome of the lunar base, built using 3D printing technology, looks like in the artist's mind.
The possibilities of 3D printing are not limited solely to the use of "simple" materials. Made In Space is developing a next-generation SMM (Satellite Manufacturing Machine) printer prototype. He will create complex structures, consisting of several materials and containing electronic components. The company has already conducted the first SMM tests on a "vomit comet". Such a multi-printer would certainly be a very significant help for deep space missions. With its help, the crew could repair their interplanetary ship, produce complex devices, structural parts, and even build their own research vehicles - for example, small landing probes.
3D printing can also be used for weightless casting. Made In Space has already patented an innovative "forced deposition" method, which allows molten metal to be poured into special molds to produce complex parts. Although this method resembles traditional technology, it should not be forgotten that in the absence of gravity, the melt behaves completely differently than on Earth. It is assumed that the method will make it possible to create fundamentally new metal alloys that cannot be manufactured under the conditions of Earth's gravity. Another interesting possibility is the use of 3D printers for the manufacture of optical elements and ceramic parts. The latter can be used, in particular, in the thermal protection of a spacecraft.
Another extremely important area is the processing of materials in zero gravity. It is associated with processes in which the original substance (for example, asteroid regolith) is crushed for further use or compact storage. The development of this technology will allow the creation of space factories involved in the processing of asteroid matter or, say, lunar soil. It could be used to extract rare earth metals, fuel for spacecraft and oxygen for crews.
In conclusion, it is necessary to mention bioprinters - devices designed to create living tissues. They can be used to conduct various medical experiments aimed at studying the influence of the space environment on the cells of the human body. In addition, it is believed that low gravity provides favorable conditions for the production of artificial organs.
At the end of 2018, the Russian company 3D Bioprinting Solutions sent the first bioprinter "Organ.Avt" to the ISS. Cosmonaut Oleg Kononenko successfully used it to print six human cartilage and six mouse thyroid glands.
The result of a three-dimensional bioprinter. Source: newatlas.com In 2019, the second bioprinter appeared on the ISS, developed by the American companies Techshot and nScrypt with the support of NASA. It will be used in experiments to 3D print heart tissue. As an intermediate result, the companies plan to create "patches" that could be used to treat congenital heart defects or the consequences of injuries and illnesses (such as heart attacks). In the long term, Techshot is going to print a full-fledged artificial heart suitable for human transplantation on the ISS.