Stratasys 3d printer materials
3D Printing Materials & Filaments
Breaking The Sound Barrier Webinar With Our Guest Boom Supersonic - Click Here to RegisterUSA & Canada
Select your country and region
- Americas
- English
- Español (México)
- Português (Brasil)
- EMEA
- English (United Kingdom)
- Deutsch
- Español
- Français
- italiano
- APAC
- 中文(简体)
- 日本語 (日本)
- 한국어(대한민국)
- English (India)
USA & Canada
3D printer materials and filament.
To ensure ultimate performance and quality, we provide a robust range of advanced 3D printing materials and filaments in the below three distinctive tiers:
- Stratasys Preferred: Preferred by Stratasys for its customers for the highest performance applications. These materials are engineered to provide the best combination of material and printer performance and are developed either by Stratasys or third-party material partners.
- Stratasys Validated: Materials validated by Stratasys with basic reliability testing to accelerate the expansion of material options available in the marketplace. These materials may or may not be exclusive to Stratasys.
- Open: Unvalidated materials accessed via an Open Material License (OML). These materials may offer unique attributes and the potential to address new applications but they have not received validation testing or optimization relative to performance and functionality on a Stratasys printer.
Specifically created for tooling, functional prototyping, jigs & fixtures and end-use production parts, the Stratasys materials & filaments meet the most demanding industry standards.
Make sure it's always the best.
The Stratasys Aircraft Interiors Solution gives aerospace companies a faster, more streamlined process.
Learn more
Make it as vibrant as your ideas.
With its exquisite detail and unsurpassed realism, Stratasys’s range of clear, flexible and rigid PolyJet materials can help you 3D print prototypes that look and feel like the final product.
Learn more
"Time is our greatest enemy. With the Stratasys F370, we can spare more resources for other complex designs, saving logistic and prototyping costs and time. Developing a drone used to take up to a year, now we have it down to around eight months.
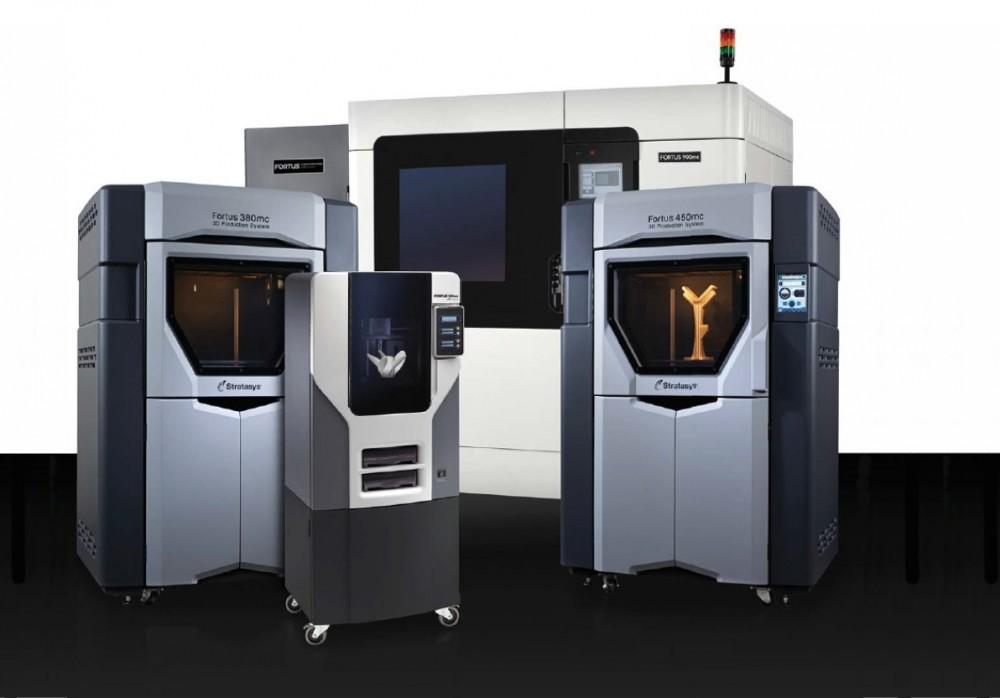
Guy Nickless, R&D director, Toy State International
Learn more
Explore all our materials
Explore all
Know the materials you need?
Shop Now
Want to consult a materials expert?
Contact Us
Resins Parts On Demand - Stratasys
Breaking The Sound Barrier Webinar With Our Guest Boom Supersonic - Click Here to RegisterUSA & Canada
Select your country and region
- Americas
- English
- Español (México)
- Português (Brasil)
- EMEA
- English (United Kingdom)
- Deutsch
- Español
- Français
- italiano
- APAC
- 中文(简体)
- 日本語 (日本)
- 한국어(대한민국)
- English (India)
USA & Canada
Cured Cosmetics with 3D Printed Photopolymers
Create highly detailed, finished-product realism right off the machine with photopolymers. Activated by ultraviolet light, photopolymer materials are ideal for prototypes and models that closely resemble finished products.
At Stratasys Direct, we offer a wide range of photopolymers for two 3D printing technologies: PolyJet and Stereolithography.
PolyJet photopolymers have properties that range from rubber to rigid, transparent to opaque, neutral to full color. Stereolithography photopolymers create soft and hard plastics, in both transparent and opaque formulations.
Urethane Casting with Advanced Formula Polymers
Our cast urethane materials provide unique combinations of physical properties for production cast parts.
We call these rigid urethane materials Advanced Formula Polymers (AFP’s) due to their specialized formulizations for a range of applications.
AFP’s are utilized for clinical trials, product testing, alpha/beta builds, prototype and end-use parts. These materials can service multiple applications like UL94V-0 flame rating, MRI transparency and high heat deflection.
Resin Materials for 3D Printing
Rigid Photopolymers
Learn more
Photopolymer Overmold
Learn more
Flexible Photopolymers
Learn more
Resin Materials for Urethane Casting
Rigid Urethanes
Learn more
Elastomeric Urethanes
Learn more
Silicone Rubber
Learn more
Resin Materials for CNC Machining
G10 Fiberglass
Learn more
Resin Manufacturing Technologies
PolyJet
Create parts in unparalleled resolution and detail with PolyJet. Incorporate multiple photopolymer materials, from flexible to rigid, and full color directly into your part.
View PJ Materials Table
Stereolithography
Stereolithography builds with photopolymers to create highly-accurate parts ideal for prototypes, master patterns, large concept models and investment casting patterns.
View SL Materials Table
Urethane Casting
Produce low to mid volumes of quality, precise and consistent cast parts quickly with our proprietary urethane casting methods. Our approach to master pattern production is guaranteed to delivery consistent parts.
View UC Materials Table
Resin 3D Printing Applications
Concept Modeling
Print with multiple materials and multiple colors with PolyJet’s photopolymers for true-to-product aesthetics.
Read More
Rapid Prototyping
Quickly bring ideas to life with PolyJet and Stereolithography without sacrificing detail and finish afforded by photopolymers.
Read More
Investment Casting Patterns
Build consistent patterns with great burnout from our specially formulated SL photopolymer.
Read More
3D printing services on Stratasys Connex3 Objet260
Intrasoft JSC offers 3D printing services on Stratasys F270 and Stratasys Connex3 Objet260
3D printer Stratasys Connex3 Objet260 prototype. For parts that require a wide range of mechanical, optical or thermal properties (for example, multi-layer casting, the production of transparent covers, flexible joints or heat-resistant surfaces).
The Objet260 Connex3 professional resin 3D printer can use a wide range of materials in a single job to create realistic prototypes without the need for unnecessary assembly and post-processing.
Applications Objet260 Connex3
- Instrumentation - for making molds using inserts with complex internal cooling channels;
- Architecture and design - to quickly create accurate and visual models, layouts and compositions;
- Industry (aerospace, defense, automotive industry) - modeling and high-precision prototyping of various samples, parts, improvement of drawings, innovative developments;
- Advertising, marketing - creation of mockups, three-dimensional models, samples of commercial products;
- Education - the creation of test, educational and training products that most accurately repeat the physical and geometric properties of real objects.
Objet260 Connex3 3D Printer Features
Print technology:
PolyJet Matrix Layer-by-layer deposition of photopolymer materials, with the possibility of simultaneous use of two modeling materials with different properties.
Supported materials
3D base materials:
Vero family color opaque materials:
- VeroGray (RGD850) 90)
- VeroBlue (RGD840) (blue)
- VeroBlackPlus (RGD875) (black)
- VeroCyan (blue)
- VeroMagenta (Purple)
- VeroYellow (yellow)
- VeroBlack (black)
- VeroWhitePlus (white)
- Vero PureWhite, a brilliant white 20% brighter than VeroWhitePlus and half as transparent
Digital Materials:
- Hundreds of composite materials can be made on the fly, including:
- Bright mixed colors of rigid and opaque material
- Translucent color shades
- Elastic materials in various Shore hardnesses
- Digital ABS materials for durability, including blends with rubber
- High temperature resistant polypropylene materials
Construction area size (maximum model size): 255 × 252 × 200 mm
T layer thickness: 16. 30 µm
Axis resolution: X-axis: 600 dpi (42 µm) ; Y-axis: 600 dpi (42 µm) ; Z-axis: 1600 dpi (16 µm).
Accuracy: 20-85 µm for parts up to 50 mm; up to 200 µm for full-size models (only for solid materials, depending on geometric parameters, axes parameters and model orientation).
Print modes:
High Speed - speed up to 20 mm/h, layer thickness 30 µm, work with one material,
High Quality (high quality) - layer thickness 16 µm, speed up to 12 mm/h, work with one material,
Digital Material (DM) (composite material) - production of models from a mixture of 2 materials, layer thickness 30 microns.
Software
Supported file formats: STL, SLC and objDF File
Learn more and calculate the cost: +7 812 363-14-09, [email protected]
we wanted to trace the history of the development of 3d printing from its inception to the present day, as well as give a forecast regarding the future development of technology.
The first 3d printer was invented by the American Charles Hull, he worked on the technology of stereolithography (SLA), the patent for the technology was filed in 1986. The printer was a fairly large industrial installation. The installation "grew" a three-dimensional model by applying a photopolymerizable material to a moving platform. The basis was a digital model pre-modeled on a computer (3D model). This 3d printer created three-dimensional objects, rising by 0.1-0.2 mm - the height of the layer. Despite the fact that the first device had many disadvantages, the technology has received its application. Charles Hull is also the co-founder of 3dsystems, one of the world's leading manufacturers of industrial 3D printers.
Charles Hull was not the only one to experiment with 3D printing technology, as in 1986 Carl Deckard invented Selective Laser Sintering (SLS). You can learn more about the method in another article, briefly: a laser beam sinters a powder (plastic, metal, etc. ), while the mass of the powder is heated in the working chamber to a temperature close to the melting point. The basis is also a digital model pre-modeled on a computer (3D model). After the laser passes through the horizontal layer, the chamber is lowered to the layer height (usually 0.1-0.2 mm), the powder mass is leveled with a special device and a new layer is applied.
However, the most famous and widespread 3D printing method today is layer-by-layer direction (FDM). The idea of technology belongs to Scott Crump (Scott Crump), the patent dates back to 1988. You can learn more about the method in another article, in short: material (usually plastic) is fed from the heated nozzle of the print head using a stepper motor, the print head moves on linear guides along 1 or two axes, and the platform moves along 1 or 2 axes . The basis of the movement is also a 3D model. The molten plastic is laid on the platform along the established contour, after which the head or platform is moved and a new layer is applied on top of the old one. Scott Crump is one of the founders of Stratasys, which is also one of the leaders in the production of industrial 3D printers.
All the devices described above belonged to the class of industrial devices and were quite expensive, so one of the first 3d Dimension printers from Stratasys in 1991 cost from 50 to 220 thousand US dollars (depending on the model and configuration). Printers based on the technologies described above cost even more and until very recently, only a narrow circle of interested specialists knew about these devices.
Everything began to change since 2006, when the RepRap project (from the English Replicating Rapid Prototyper - a self-replicating mechanism for rapid prototyping) was founded, with the goal of creating a self-copying device, which was a 3D printer working on technology FDM (layer by layer deposition). Only, unlike expensive industrial devices, it looked like a clumsy invention made from improvised means. Metal shafts serve as a frame, they also serve as guides for the print head. driven by simple stepper motors. The software is open source. Almost all connecting parts are printed from plastic on the 3D printer itself. This idea originated among English scientists and aimed at spreading available additive technologies so that users can download 3D models on the Internet and create the necessary products, thus minimizing the production chain.
Leaving aside the ideological component, the community (which exists and develops to this day) managed to create a 3d printer accessible to the "ordinary person". So a set of unprinted parts can cost around a couple of hundred US dollars and a finished device from $500. And even though these devices looked unsightly and were significantly inferior in quality to their industrial counterparts, all this was an incredible impetus for the development of 3D printing technology.
As the RepRap project developed, 3D printers began to appear, taking as a basis the base laid down by the movement in technical and, sometimes, ideological terms (for example, commitment to the concept of open source - OpenSource). The companies that made printers tried to make them better both in terms of performance, design and user experience. The first RepRap printers cannot be called a commercial product, since it is not so easy to manage (and even more so to assemble) and it is not always possible to achieve stable work results. Nevertheless, companies tried to close the more than significant gap in quality, leaving a significant gap in cost whenever possible.
First of all, it is worth mentioning the company MakerBot, which started as a startup, based on the ideas of RepRap and little by little turned them into a product of a new quality.
Their flagship product (and in our opinion the best to this day) remains the MakerBot Replicator 2 3D printer. The model was released in 2012 and later discontinued, but remains one of the most popular 3D printer models to this day " personal" segment (according to 3dhubs). The word "personal" is in brackets because this printer, which cost $2,200 at the time of release, was (and is) primarily used for business purposes, but falls into the personal segment due to its cost. This model differs from its progenitors (RepRap), being, in fact, a finished commercial product. Manufacturers abandoned the concept of OpenSource, closing all sources and software codes.
In parallel with the release of equipment, the company actively developed the Thingiverse resource, which contains many models for 3d printing, available for download for free. During the development of the first printer and beyond, the community has helped the company a lot, testing the product and offering various upgrades. After the release of the Replicator 2 (and the closure of development), the situation has changed. You can learn more about the history of MakerBot and other companies and people associated with 3d printing by watching the film Print the legend.
This film also highlights the history of Formlabs, one of the first companies to launch an affordable 3D printer using SLA (Strereolithography) technology. The company raised funds for the first FORM 1 model through crowdfunding, encountered production difficulties, but eventually released an affordable and productive 3D printer, closing the quality gap described above.
Although the 3D printers described above were far from perfect, they set the stage for the development of affordable 3D printing technology that continues to this day. At the moment, the quality of FDM and SLA printers is increasing, but there is no significant price reduction, rather, on the contrary, it is growing slightly. Along with FDM and SLA, many companies are developing in the field of powder sintering (SLS), as well as metal printing. Despite the fact that such printers cannot be called affordable, their price is much lower in comparison with analogues from the professional segment. It is also worth noting the development of the line of materials, in addition to the standard ABS and PLA plastics, today many different materials are used, including nylon, carbon fiber and other durable and refractory materials.
Personal 3D printers of today are very close to professional devices, the development of which is also not stopping. In addition to the "founders" of the technology (Stratasys, 3dsystems), many small companies specializing in industrial 3D printing technologies (metal in particular) have emerged. 3D printing is also attracting the attention of large corporations, which, with varying degrees of success, are striving to take their place in a growing market. Here it is worth highlighting HP, which recently released the HP Jet Fusion 3D 4200 model, which has gained popularity among 3d printing professionals (as of 2018, it is at the top of the ranking of professional 3D printers in the quarterly reports of the 3dhubs portal).
However, 3D printing technologies are developing not only in breadth, but also in depth. One of the main disadvantages of 3D printing, compared to other production methods, is the low speed of creating models. A significant advance in terms of accelerating 3D printing was the invention of CLIP technology by CARBON, printers operating on this technology can produce models 100 times faster than classic SLA technology.
There is also a constant expansion of the range, properties and quality of materials and post-processing of products. All this accelerates the transition to the use of 3d printers in production, and not just as prototyping devices. Today, many large and not only companies and organizations are closely using a 3D printer in their production chain: from consumer goods manufacturers NIKE and PUMA to BOEING and SPACE X (the latter prints engine parts for its rockets that could not be made in any other way) .
In addition to the "classic" scope of 3D printing, today you can increasingly see news about how a house or some organ (or rather, a small part of it) was printed on a 3D printer from bio-material. And this is true, several companies around the world are testing or already partially using 3D printing in the construction of buildings and structures. This mainly concerns the contour pouring of walls (similar to the FDM method) with a special composite concrete mixture. And in Amsterdam there is a 3D printed bridge project and this list will only expand over time, since the use of 3D printing in construction can significantly reduce costs and increase the speed of work at certain stages.
With regards to medicine, here 3D printing also finds application, but at the moment it is not printing organs, but rather the use of technology in prosthetics (of various kinds) and bone replacement. Also, 3D printing technology is widely used in dentistry (SLA technology). Regarding the printing of organs, this is still far in the future, at the moment bio-3D printers are experimental facilities in the early stages, the success of which is limited to printing a few limited-viable cells.
Looking to the future, it is safe to say that 3D printing technology will expand both in breadth and depth, improving technology, speeding up processes, improving quality and improving material properties. 3D printers will increasingly replace old methods in production chains of various scales, and world production, due to this, will move towards the “on demand” scheme of work, increasing the degree of product customization. Perhaps someday, 3D printers will be widely used at the household level for the production of necessary things (the dream and goal of the RepRap movement), but this requires not only the development of technology, but also a paradigm shift in social thinking, as well as the development of a powerful design ecosystem ( 3d modeling) products (which is often forgotten).