How to make a lithograph 3d print
How to Make Your Own 3D Printed Lithophane
A lithophane is a three-dimensional image that changes according to the intensity and quality of the light striking it. The light areas are very thin, allowing more light to pass through, while the thicker parts appear darker.
Lithophanes date back to the 1800s, when they were traditionally carved from wax, molded in plaster, then cast and fired in porcelain. In the meantime, photography was invented as a simpler way to capture an instant, but now, 3D printing enables you to experience the best of both worlds.
Finely detailed and delicate, lithophanes are best suited for 3D printing on a high-resolution stereolithography (SLA) printer. Plastic extrusion fused deposition modeling (FDM) printers will produce thicker layers and unsightly buildup that diminish the appearance of the image.
In this tutorial, we’ll walk you through the process of creating 3D printed lithophanes on a Formlabs SLA 3D printer in three simple steps.
- Formlabs SLA 3D printer
- Formlabs White Resin
- Form Wash or Finish Kit
- Form Cure or alternative post-curing chamber
First, pick a photograph. Lithophanes rely on the difference in contrast between parts of the image. Thanks to the high resolution of SLA 3D printing, any picture with a moderate level of contrast will result in a clear image with stunning details. If the image has low contrast, try converting it to black and white, turning up the contrast, or erasing the background using a photo editing tool.
For 3D printing, convert the 2D image into a three-dimensional lithophane model. There are multiple online lithophane generator tools available, the easiest being a free online lithophane generator, like ItsLitho or the image-to-lithophane converter.
Creating 3D printable lithopanes one takes a few seconds with a drag and drop lithophane generator.
Advanced tools like Adobe Photoshop (download a free trial here) or Blender provide more room for adjustments. The steps for Photoshop are the following:
- Install the “Make Lithophane” action for Photoshop from the Adobe website. Unzip the file to reveal “Make Lithophane.atn.”
- To install the action, open Photoshop and open the Actions window by opening Window > Actions.
- Open the actions menu by clicking on the top right corner of the window, highlighted in red below:
- Click on Load Actions and navigate to the file, “Make Lithophane.atn.”
- You should now see “Make Lithophane” in your actions list.
- Open the image that you’d like to turn into a lithophane.
- Run the “Make Lithophane” action. Photoshop automatically goes through a series of steps to convert the image to grayscale, invert the colors, and make a 3D depth map. It also creates a raised border and a flat surface on the back.
- To export as an STL file to your Form 3 printer, open the print settings in the Properties window by clicking on the red box.
(You can also access this by going to 3D > 3D Print Settings). Export by clicking on the 3D print button, as indicated by the blue box.
- Set “Print To:” value to Local.
- Set “Printer” value to Export STL.
- Set “Printer Volume” to Millimeters.
- Set “Detail Level” to High.
- Set “Scene Volume” to your desired size, as long as the X is below 125, and Z below 175.
Next, 3D print the lithophane on the Form 3+. For the quickest results, print the file with the flat side directly on the build platform with no supports.
Alternatively, printing vertically will enable you to print large lithophanes, up to 185 mm by 145 mm. This will also simplify removing parts from the build platform and allow you to 3D print up to 19 lithophanes in one build, significantly increasing the efficiency of the process.
- Open the STL file in PreForm, Formlabs' slicing software. PreForm will automatically detect any integrity issues and repair your model.
- Orient the file on the Build Platform using the Select Base feature.
- Print the file in White Resin at 50 microns for the best results. If you’re rushed for time, 100 microns will still give you great results.
Post-processing 3D printed parts is essential for a perfect finish, and due to the delicacy and extreme thinness of the parts, lithophanes require extra care.
For the best results, use the Form Wash and Form Cure automated post-processing solutions from Formlabs that simplify the production of small batches customized products.
- Pull the build platform out of the Form 3+ and place it into the Form Wash, without removing the lithophanes from the build. Form Wash will agitate the IPA to clean even the most inaccessible areas.
- Once the parts are completely dry, gently remove the 3D printed lithophanes from the build platform and put them into the Form Cure. Lithophanes require less time to cure due to their thinness, so select 5 minutes at 40 °C on the device.
Your 3D printed lithophane is now ready. Thanks to the high precision and level of detail, lithophanes created on desktop SLA 3D printers will yield beautiful results.
Mount it on a window to let the light shine through it or create a LED back light to create a lithophane lamp and enjoy at night. Happy LithoForming!
We’d like to thank Italian Formlabs partner Manufat for their guidance throughout the process.
Learn More About the Form 3+
How to make one and what Filament to use! – 3D Solved
Did you know that you can print images with your 3d printer? Yes, like a regular printer but fancier and with a three-dimensional look. These images are called lithophanes and can be printed on a regular cheap 3d printer.
In this article, we will learn about 3D printed lithophanes: what they are, what the best way to print them is, which material we should use, and the steps to follow to create our own lithophane. Concisely, how can you create your own lithophane?
In order to create a custom lithophane, you need to select a high-resolution image with high contrast features. By means of free online tools, you can create an .STL file containing the lithophane, which you can then import to the slicer of your choosing. Before starting the print, it is very important to set the infill percentage at 100% in order to successfully print a lithophane.
Now that you already know the basics of a lithopane, you may be asking yourself what type of filament to use.
Due to the nature of lithophanes, white polylactic acid (PLA) stands out as the best filament type for this type of print. Nonetheless, it is important to state that PLA has a low glass transition temperature (about 60°C), so it is recommended to light the lithophane with an LED. They are more energy-efficient and waste less energy in the form of heat.
In cases where this is not an option, you should print the lithophane with PETG, which is more heat resistant but also more difficult to print.
Table Of Contents
- What is a lithophane?
- How to create a custom lithophane
- Creating your lithophane
- Slicing your lithophane
- Best materials for printing lithophanes
- Can you print a lithopane with an SLA printer?
- Best Slicer settings for printing Lithophanes
- Conclusion
What is a lithophane?
Source: LithophaneMaker.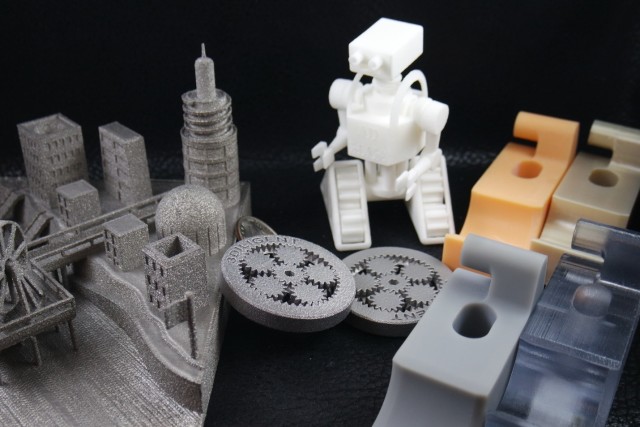
Lithophanes are images that can be seen passing light through a thin, translucent sheet. Because of the different levels of thickness in the sheet, light cannot pass through it in the same way at every point of the surface.
Thicker parts will seem dark while thinner parts will allow light to pass, making these areas seem more clear. The final result is an image, similar to a photograph.
In the past, lithophanes were carved in wax, but today we can use our 3D printers for that. If we think about it, these images are the results of different variations of thickness on a surface.
These variations can be done on a 3D printer, adding layers on the Z-Axis or increasing the quantity or thickness of lines in our design. Then, with backlighting or a lamp, we could see the image just like a normal photograph.
In other words, you can easily create an image of your family, friends, or pet for your home, using free tools. A lithophane is a great gift for special occasions. You can take a selfie and send it as a present to a friend after a special day together. Or you can make a lamp using lithophanes: when you turn it on, the images will be projected.
How to create a custom lithophane
Before we get started creating our own lithopane, lets do a quick checklist of the things we will need to get this job done!
–A 3D printer: we’ll assume you have a perfectly calibrated printer and you are an expert user (or so). In case you do not have one, you will still be introduced to a new application of 3D printing that you didn’t know. Just make sure your axis’ steps are properly calibrated, otherwise, your image will look distorted. Also, retraction settings must be set properly, or the stringing in your object will affect the print quality.
–A photograph or an image: it can be anything that comes to your mind. To get started, you can choose simple images (for example cartoon characters) or some high-contrast designs. If you do this, your first samples will be faster to print and you’ll be able to fix any mistake that shows up.
JPG format is best used for images in this case because of its size and high image quality.
–A slicing software: use your favorite. You won’t need any complex tools. With the sole exception of infill percentage, we will mainly be using regular settings. If you are proficient in obtaining good prints from your machine, keep most of the settings you regularly use.
Just remember to set the infill percentage at 100%. Otherwise, you will end up with a lithophane of a translucent grid (or honeycomb, or the pattern you use for infill). I use Cura as my go-to slicer, but, again, any slicer will be fine.
–An online tool to convert images into STL files: although you can use advanced design software like Adobe Fusion 360 to create a lithophane, we can skip the learning curve and go straight to online tools that are designed for this sole purpose.
In this article, we will be using a free online tool that does not require registration, offers lots of customization options, and yields awesome results. It is developed by 3dp.rocks and you can check it out here.
Creating your lithophane
Once you’re on the website, click the “IMAGES” button and then upload the image that you choose from your computer.
To make your first try easier, choose the “FLAT” type on the bottom menu. Once you’re done with your first lithophane and happy with the results, you could try more complex shapes.
Click “Refresh” and then “Settings”. This will open a menu with multiple options.
The first one is “MODEL” and it allows us to adjust the size and resolution of the lithophane. I recommend you start with a Maximum Size of 150 mm, a thickness of 3 mm, and 0 for the border.
“Thinnest Layer” allows us to choose the smaller width of the image. Here, I advise you to set the width of your nozzle. I usually use 0,4 mm. A smaller nozzle size will improve the image quality but it will increase the printing time.
You can modify the rest of the settings once you master this awesome tutorial.
The second option in the menu is “IMAGE” Settings, and it contains different effects to apply to your lithophane. For now, we’ll let everything as default except “Negative Image”: we will change it to “Positive Image”. Click on Refresh after that.
The last option menu is “Download Settings”, and it allows us to change the format of our 3D file. Select binary and manual to continue. Now that you are ready to download your lithophane, click on download and import your 3D model into your goto slicer.
Slicing your lithophane
It’s very important that you decide in which position you’ll print the 3D model. You can either print it vertically or horizontally. If you choose the first one, the layer height can be less than the nozzle width, and that improves the resolution of the image. I recommend you to use 0,1 mm as layer height.
The disadvantage of printing a lithophane vertically is that printing time will increase drastically. This can be reduced by adjusting jerk and speed settings, but this time let’s focus on getting a nice print instead of making it fast.
If for some reason you prefer to print horizontally, you’ll have to change the “thinnest layer” setting into the chosen layer height. Because of the lower resolution, the smallest details in your lithophane may disappear, so I don’t recommend you print it this way.
Printing speed is another key parameter in this project: to maintain a high resolution in your image, you’ll have to slow down the speed to 30-40 mm/s. Small differences in your object’s perimeter will result in ugly marks, so start slowly and increase speed later when you are comfy.
The importance of movement speed when printing lithophanes can not be overstated. Take a look at the following example of the same file printed in different settings:
There are only two differences between both prints, but they greatly improved the outcome. The movement speed was reduced from 45mm/s to 30mms/s, while the layer height was taken from 0.3mm to 0.2mm. The filament used in both cases was a generic white PLA that I had laying around (properly preserved and in good condition).
The increase in printing time was noticeable, but in the broader scheme of 3d printing, lithophanes don’t require that much filament or time.
The infill percentage in your print must be at 100%. Otherwise, the slicer won’t fill the thicker spaces and the “darker areas” effect won’t come out.
Best materials for printing lithophanes
As you know, PLA is the friendliest material to use, so it is a great option to print lithophanes. When the thinnest parts are printed, it seems translucent, and it becomes darker when the thickness increases. This effect becomes even more notorious when a white PLA is used.
Although you can use any light color, white is the best option for this because it achieves the best results even with low power lamps. Dark colors don’t let the light pass through the lithophane, so these are not suited for this.
The disadvantage of 3D printing lithophanes with PLA is the limited thermal resistance of this material. At 60°, PLA starts to lose its shape and becomes soft. Many people make lithophane lamps, and if the lightbulb gets too hot, PLA could melt and ruin the object. A great solution for this is to change the lamp for one with LED lights. These are brighter and don’t heat up too much.
Another great option to print lithophanes is PETG, which is even more translucent than PLA (soda bottles are made of this material). It can withstand higher temperatures and doesn’t break so easily. As a negative part, this material is not that easy to print. It can cause more warping, low adherence between layers, and delamination. Besides, it requires a heated bed to be used.
Nylon can withstand up to 90ºC and it’s even more translucent than PLA so it can be used for this kind of print. If you are very skilled in 3d printing you can try a Nylon lithophane, but in my opinion, it’s not worth it.
This material is more expensive and really difficult to print. It must be dry or it will start clogging. Also, you will need a special hot-end: Nylon needs nearly 250ºC to be printed. If your extruder has 3d printed parts, forget about Nylon.
I don’t recommend using ABS for this. It’s true that it can resist higher temperatures, but the opacity of this material is too high. Thin ABS layers can block all of the light from the lamp, so you won’t be able to see any image in your lithophane.
In a nutshell, PLA stands as the best option. Now choose an image, turn your printer on, and get into the lithophanes’ world!
Recommended Materials: White PLA Filament and white PETG filament.
Can you print a lithopane with an SLA printer?
It is absolutely possible to print a lithophane using a resin-based SLA printer. In fact, the level of detail and precision that can be obtained by using this type of printer is going to be much higher in comparison to an FDM printer. Nonetheless, lithophanes are commonly not printed using SLA technology because of the rather small build surface that these printers usually have.
Best Slicer settings for printing Lithophanes
No matter what Slicer you use, the settings won’t be any different. In fact, some slicers may already include a specific profile for printing Lithophanes, so you could try those ones out first.
Since PLA will probably be your filament of choice, here are the ideal settings for achieving high-quality lithophanes.
Ideal Slicer settings for printing Lithophanes (PLA):
- Printing Temperature: 200 – 210 ºC
- Bed Temperature: 50 – 65 ºC
- Layer height: 0.
12 mm up to 0.2mm for greater detail
- Retraction: 6 mm
- Infill: 100%
- Speed: 50 mm/s
- Initial Layer Speed: 20 mm/s
- Initial Layer Height: 0.2 mm
- Initial Fan speed: 0%
- Fan speed (after the initial layers): 100%
If you decide to give it a try using PETG, then simply adjust the print and bed temperatures accordingly: Print temperature 230ºC and Bed temperature 80ºC.
Conclusion
Printing lithophanes is much easier than most people think, since you only need to upload the image to the software which will convert it into a file that can be sliced by the slicer, set the infill to 100% and that’s about it.
So, I hope that you give it a shot and print your first lithophane soon!
We created a recommended products section that will allow you to remove the guesswork and reduce the time spent researching what printer, filament, or upgrades to get, since we know that this can be a very daunting task and which generally leads to a lot of confusion.
We have selected just a handful of 3D printers that we consider to be good for beginners as well as intermediates, and even experts, making the decision easier, and the filaments, as well as the upgrades listed, were all tested by us and carefully selected, so you know that whichever one you choose will work as intended.
print your photos in 3D! - qbed
Detailed instructions for 3D printing of lithophanes |
---|
3D printed lithophane from kraftly.com
Modern 3D printers allow you to create many original and unique things, and one of them is 3D photo-lithophanes, which are gaining more and more popularity as a customized gift for loved ones or just an original product for sale. Let's take a look at what linophane is and how to print it.
Article content:
What is lithophane?
Designing a lithophane
Selecting a photo
Converting a photo into a 3D model
Creating and printing a 3D model of a lithophane in Photoshop
How to slice a lithophane?
Seal of lithophane
What is lithophane?
Classic lithophane is a three-dimensional image on thin translucent porcelain that can only be seen when illuminated from behind by a bright light source (such as the sun or an ordinary light bulb). The image will appear in gray tones. Traditionally, lithophanes were created in several stages: first, the image was cut out of wax, then, based on the wax model, a mold was created from plaster, into which porcelain was cast, after which the image was fired.
German lithophane of the 19th century, on the left - without illumination, on the right - with illumination. Photo — Diego Verger
The first lithophanes appeared almost simultaneously in several cities of Europe — France, Germany, Prussia and England — at the end of 1820s and their three-dimensionality was strikingly different from the two-dimensional engravings popular at that time and daguerreotypes . The fact is that the quality and quantity of light interacting with lithophane significantly changes the characteristics of the image itself - such dynamism arouses great interest in the viewer. For example, lithophane inserts in windows change their appearance throughout the day depending on the quality and intensity of the sun's rays.
Modern 3D printers allow you to print lithophane from any high contrast photo. How? Varying the thickness of different sections of the 3D model to render different shades of gray when the lithophane is backlit: thin sections let in more light and look brighter, while dense parts of the print let in little light and create dark details in the image. Don't panic, you don't have to manually calculate the thickness of various sections of the digital model - there are many programs that create 3D models for lithophanes automatically and for free! Let's get down to business!
Back to Contents
Designing the Litophane
First we need to create a digital model of the lithophane.
Choosing a photo
The first step to a great printout is choosing a suitable photo , because not all images will look good in the form of a lithophane.
-
Firstly, the finished lithophane will be displayed in grayscale, so images where color plays an important role or where there is a lot of color detail will not work. You can try to convert the photo to b / w in Photoshop or any other program to make sure that you like the picture even if there are no colors.
-
Secondly, it is better to give preference to contrasting photos - so the printed linofan will look more interesting (unlike the image, where adjacent details will merge due to lack of contrast). Again, you can add contrast to the selected photo in Photoshop or any other program.
An example of a low-contrast image, not quite suitable for lithophane printing. Photo — Christina Ryumina
-
Thirdly, avoid photos consisting only of small details , it can be difficult for the printer to print them.
For lithophanes, images with large contrasting details, such as portraits, are more suitable. Images with a single-color background without details are also good, for example, portraits against a backdrop or against a clear sky. You can clean up the background or create a color fill instead of an existing background in Photoshop or any other program.
Contrast photo on a plain background is ideal for printing lithophane. You can further clean up the background and add photo contrast in any post-processing program. Photo — Christina Ryumina
An example photo with lots of detail is not the best choice for creating a lithophane. Photo — Christina Ryumina
Of course, you don't have to follow these tips. If you print on a high-quality printer with high resolution, then you can handle any details! For example, SLA printers allow you to print smaller details than their FDM counterparts (read more about 3D printing methods here), so a photo for printing on an SLA printer may contain small elements.
Convert photo to 3D model
0011
-
You can convert photo with free online Image to Litophane converter.
-
Models for lithophanes can be created in Photoshop CC by downloading a special Operation (Action) from the official website (read detailed instructions below), or in Blender: these programs have more options to edit the model. It is worth considering that a subscription to Photoshop CC is paid.
-
Cura software (version 13.11 and higher) from Ultimaker will also work. The program is easy to use and allows you to smooth the model, but it does not have the ability to edit the image and create a frame around it.
-
You can use the Customizable Lithopane from printer manufacturer MakerBot on Thingeverse. Here you can add a hole in the frame of the lithophane so you can hang your masterpiece, but in this application your photo resolution will be compressed to 100x100 pixels.
Another disadvantage: the application can be quite slow, because the Thingeverse website Customizer creates a model and STL file instead of your computer.
-
There is also a free 2D to STL converter for Windows. There are options for smoothing the model, but no way to edit the image.
-
You can create a model for lithophane in a paid Photo to Stereolithographic file converter. This program allows you to create lithophanes on spheres, cubes and other shapes, but the interface here is not the most understandable.
-
There is a nice free Portuguese converter where the language can be changed to English after installation by going to the Iniciar menu, then Idioma and finally selecting English. Here is a link to download the program. In this converter, you can create a frame for the image, edit it before creating a 3D model, and also enlarge / reduce the image. The converter generates models quite quickly, so you can experiment with 3D model settings until you are completely satisfied with the result.
The list of programs, of course, is not exhaustive. You can use any converters of 2D files to 3D models that support export to STL. In this article, we will be using Photoshop CC to create a 3D model from a photo.
Create and print a 3D model of Lithophan in Photoshop
Attention! The operation only works if the interface language in your Photoshop CC is English. You can change the language by going to menu Photoshop CC → Preferences → Interface.
To add an action in Photoshop, go to the program, go to the top menu in Window → Actions or click the icon Play in the side menu (see screenshot below).
Going into the Actions panel in Photoshop
Opening the operations panel, click on the menu icon (see screenshot below) and select the command "Load Actions. .." . We go to the location where your downloaded Lithophane folder and the operation "Make Lithophane.atn" are located and select it. The operation is now available in your Photoshop.
Loading the operation "Make Lithophane.atn"
Operation "Make Lithophane.atn" is ready to go
Open the image you are about to print. You can convert it to black and white, add contrast and make any changes, then print the visible layers into one by pressing Ctrl + Shift + Alt + E (English), or simply merge the layers through the menu Layers (in any case , you will be prompted to merge layers when starting the operation). In the layers panel (marked in blue in the screenshot below), select the layer with the final version of your image and name it Background (or select the Background itself directly if you haven't changed anything). Then open the "Make Lithophane" operation folder, select "Make 100mm x 6.25mm Lithophane" (marked in red in the screenshot), press Play (marked in green in the screenshot). The operation automatically converts the 2D image into a 3D printable object: Photoshop converts the image to Grayscale, inverts the tones, creates a 3D depth map, as well as a frame and a flat surface on the back of the image.
Starting the operation of creating a digital model of lithophane
Litophane in Photoshop CC
To print a 3D object, click on the top menu 3D → 3D Print (marked in red in the screenshot below) or click on the print icon (marked in pink). Next, you will see the 3D printing settings panel (see screenshot below). Select a printer (or specify Printer: STL File if you want to export the model as STL), set Printer Units , Detail Level . Determine the size of the model by setting the X / Y / Z values. Option Scale to Print Volume will create the largest printout that will fit in your printer's camera.
Click on the icon marked in green in the screenshot below to have Photoshop prepare your model for printing. Photoshop will analyze the object and show you a print preview with supports in a new window (supports are turned on and off by ticking Scaffolding ). From the same window, we can print or export the model.
Preparing the model for printing/exporting
Model
print/export window
Do not forget that the size and thickness of the lithophane, as well as the amount of detail in the photo and model, affect the printing time. Depending on these settings, it may take 30 minutes or 5 hours to print.
How to slice lithophane?
The slicer will help convert our model into a printer-friendly G-code (read more here). To open a 3D model in a slicer, you need to export it as a STL file. To do this, in the Photoshop 3D printing settings panel, select Printer: STL File , export the model as described above, and open it in your slicer to set up the location of the model on the platform and set other parameters. You can also export photos to STL from any of the other converters mentioned above and then open the file in a slicer.
To achieve optimal printing results, it is recommended to slice the lithophanes as follows:
-
Set straight infill to 100% at an angle of 30-35°. 100% infill will provide the best quality lithophane, as there will be no honeycomb inside the layers, which will spoil the tones in the printout.
-
Set the minimum layer height that your printer supports.
This way you will ensure high resolution details and the maximum number of shades of gray in your lithophane.
-
Print as slowly as possible. Speaking of FDM, slow printing will help you avoid retraction problems, because most of the print is created with little extrusion, which can provoke a huge amount of retraction. To prevent your printer from smearing your printouts with unwanted material smudges and your extruder from clogging due to fast retractions, it is best to print as slowly as possible.
-
Select the optimal lithophane slicing parameters available in your slicer. Different slicers provide different options. Choose the slicer you like, however, be aware that some slicers take longer to layer the model than others, for example, Cura usually slices faster than Slic3r. Experiment!
-
Do not scale the model in the slicer. The model should be scaled in Photoshop or other converters mentioned so as not to lose resolution when printing.
Litophane Printing
Now it's to load our STL file into the printer via USB or SD card (or whatever methods are available on your printer). The faster the connection, the better, since lithophanes can contain a lot of detail, and some types of connection may not be fast enough to send the entire G-code to the printer, and the printer will begin to slow down and smear material on the printout.
Make sure your printer platform is in good condition to avoid warping your printout. Be sure to check the printer calibration and set the correct print temperature to match the melting temperature of the selected material.
It is best to use white material for printing, as colored materials will not give the same strong lithophane effect. Printing lithophane is best with ABS or HIPS, avoiding PLA : If you are going to put lithophane on a window, then PLA can melt in the sun.
Soft light is ideal for illuminating lithophane. Lithophanes make excellent lamps and even lanterns.
Lithophane lamp. Original photo here
Lantern-lithophane. Original photo here
Back to Contents
Back to Contents
GalleryWhat 3D Printing Can Do
WATCH
Glossary3D Modeling and Additive Manufacturing Terms
WATCH
DIYK. 10 Comments
0 LikesLithophany: what is it and how to make it with 3D printing
This strange name hides a very beautiful way of depicting art. In , lithophany is gaining more and more followers of in the world of fabricators and 3D printing. With it, you can print all sorts of scenes, personal photos, drawings, shapes, and whatever comes to mind.
If you are interested in learning more about this method of creating art with lithography, in this article you will learn what it is, how it differs from other techniques such as lithography, and how you can start creating your own designs with Print 3D.
Index
- 1 What is lithophany?
- 1.1 Lithophany vs. lithography: the differences
- 2 How to make lithophany with a 3D printer
What is lithophany?
La lithophany is a type of projection of images and forms using light. Previously, the light of fire, sunlight or candles was used. Light bulbs are currently being used. In either case, the light source will pass through the sheet with a series of translucent silkscreens to form the image.
The idea is to have different thicknesses of foil so that the light varies in opacity, making some areas darker and others more original. The result is really beautiful, especially when used as four to decorate a room, or as a lamp for a bedroom, children's room, etc.
Originally this engraving is it was modeled in wax . Then other materials began to be used, for example, porcelain. Many other materials can now be used, such as polyamide resins or 3D printer plastics.
In the nineteenth century This method became popular in countries such as Germany and France, and later spread throughout Europe. Many point to Baron Burging as its creator, and if you want to know more about his history, you should know that there is an entire museum dedicated to this art in Toledo, Ohio (USA), the Blair Lithophany Museum.
Lithophany vs. lithography: differences
Some people confuse lithophany with lithography , but they are not the same. Lithography is an old form of printing (still in use today) that allows shapes or images to be printed on stones or other types of materials in a flat form. Actually, its name came from there, starting with lithos (stone) and graphe (drawing).
With this technique, you could duplicate art pieces and also had a wide range of applications in the world of printing, where lithographs are still used for printing.
Instead, lithography uses lithography or 3D printing of to be able to create the thickest and most opaque areas, as well as the thinnest and most translucent. But to achieve the result, this technique needs light.
How to make a lithophany with a 3D printer
To be able to create your own lithophany, you do not need to have any skills in art or drawing, you only need one 3D printer, filament, PC with appropriate software and image. you want to represent. Not much more...
As for the software for to generate lithophany , you can use several of them to convert the image into a lithophany-friendly design and into a 3D printing stratifier. For example, you can use a web application that can be used on any operating system with a compatible web browser.
This application is called 3Dp and you can access this link. Once you have accessed this web application, you must follow these steps:
- Click on Photos and select the image you want to convert to lithophany.
- Once the image is uploaded, now in Model select the model you like best and click "Update" to update it.
- Now go to tab Settings . You will see several options:
- Model Settings : Set the model to your liking.
- Maximum size (mm) : will be the size of the lithophany.
- Thickness (mm): with this parameter you play with the sheet thickness. Don't make it too thin or it will be too brittle.
- Border (MM): the ability to create a border on a sheet or in a frame. If you do not want, set the value to 0.
- Thinnest layer (mm): you play with the pixel thickness of the photo so that more or less light passes through the thinnest areas.
- Vector per pixel: The higher it is, the better the resolution, but there is a risk that if it is too high, the detail will fail. You can leave this after about 5.
- Base/Stand Depth: It creates a base in sheet for support, although if you are making a different shape, such as a round sheet, you don't need that base to stand.
- Curve: this will create more curvature in the sheet. You can even set it to 360º to make it cylindrical. Ideal choice for lamps.
- Image settings : Adjust the image according to the model.
- Positive Image/Negative Image: It is used to make the photo stand out or face inward as you wish. That is the direction of the relief.
- Mirror off / Mirror on: Creates a mirror effect.
- Flip image off / Flip image on: you can flip the image.
- Manual update / image click update: If you check it when you go to the model tab, it will update automatically.
- Repeat X count: makes horizontal copies.
Learn more
- Model Settings : Set the model to your liking.