How durable is 3d printing plastic
Custom 3D Printing Plastics | Pros And Cons
- 01908 374144
Multi-Award Winning
Innovative, workable design solutions inform and enhance the quality of our work,
ensuring value for money and total customer satisfaction
contact us
GET A QUOTE
What Is Meant by 3D Printing?
This is a fairly new manufacturing and design technology growing in popularity and scope as people wake up to its many possibilities. Just as plastic injection moulding techniques can offer highly bespoke results, so too can 3D printing, which combines sophisticated design software with a 3D printing machine to produce durable, reliable 3D printed objects used across a wide range of industries.
3D Printing On Demand
One fascinating aspect of this manufacturing technique is how many things to 3D print are out there and how easily a design can be produced and put into production on demand.
From toys and models to automotive parts and medical devices, the list of 3D printed products can be endless. There is a fast-growing market for 3D printed tools that can be produced in smaller quantities within short lead times to keep costs down while using highly bespoke specifications to enable tools and other 3D printed objects to meet a precise purpose on-demand.
Custom 3D Printing Projects
Adreco plastics can offer customer 3D printing support, which covers the whole process, as well as helping to correct any 3D printing problems you may have encountered elsewhere.
Our custom 3D printing service lets you order the specific product, tool, or component you need, delivered to the perfect specification, colour, and finish. This is ideal for demanding applications and highly customised designs, where branding, colours and shape are paramount.
Our 3D Printing Process
There are several stages involved when describing how to 3D print. At Adreco Plastic, we begin by working closely with our customers to finalise the chosen design and agree on materials, colours and finishes.
All this data is transferred to our 3D printing software programme, ready to translate our customer’s ideas into 3D printed reality. The actual printing is achieved through an additive process, where thin layers of a plastic filament product are added on top of each other to form the shape carefully.
The layers adhere firmly to each other for maximum durability and are printed with high accuracy levels to create the printed form of the agreed design.
We can help you with your 3D printing projects
Adreco Plastics has used its many decades of experience in injection moulding techniques to branch out into a professional 3D printing service that covers a wide range of industries.
We offer bespoke 3D printing support and work closely with our customers from initial design ideas to quality control and delivery of the finished products.
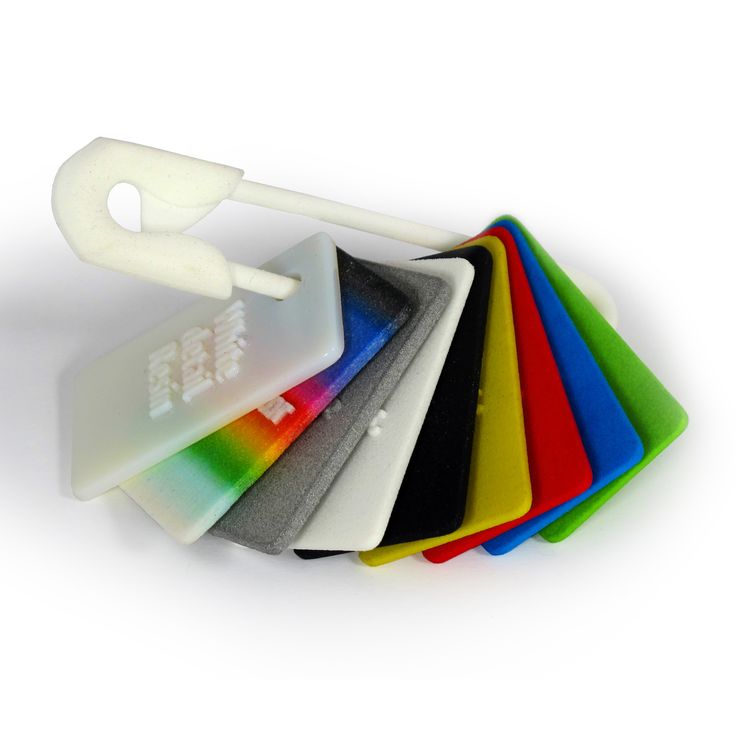
We can advise on 3D printing designs and which 3D printing materials to use, as well as offer a full logistical support service to ensure excellent customer service from start to finish.
Injection Moulding and 3D Printing
In many ways, 3D printing is a very similar process to plastic injection moulding; however, there are some differences in how the design is created and transferred to the printer itself and techniques used by the machine to form the finished product.
Plastic injection moulding involves creating individual moulds, shaped to match the project specifications and used only to make that product. 3D printing used the same printing machine to make countless different shapes and forms. This versatility is and will continue to be a key factor in the future of 3D printing.
Advantages and Disadvantages
The versatility of being able to design pretty much anything using customised software and additive technology makes bringing 3D printing designs to life an easy and relatively rapid process.
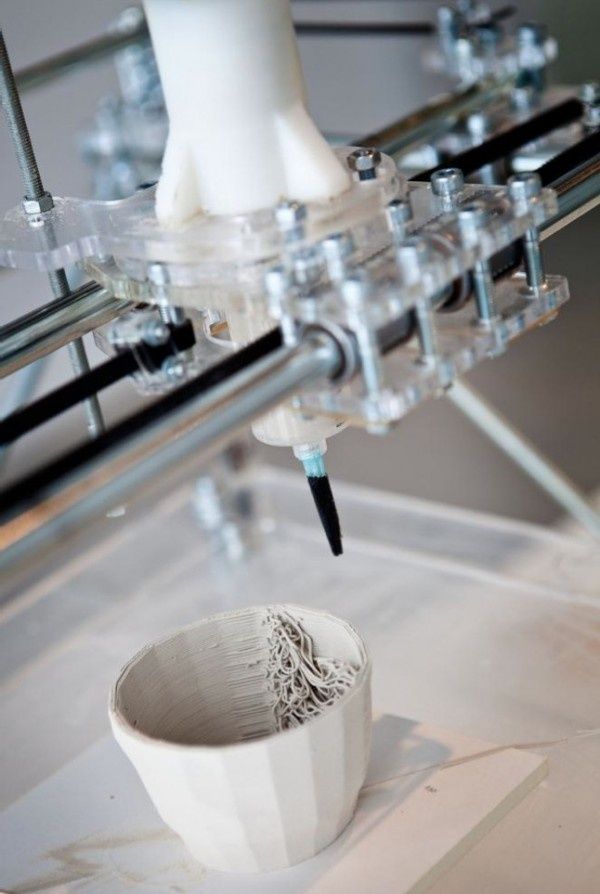
3D printers can produce smaller orders more cost-effectively when compared to plastic injection moulding, which involves creating individual moulds to create each particular design.
Buying a desktop 3D printer is relatively inexpensive, making it more accessible to people seeking to start their own production.
Disadvantages include the fact that it takes much longer to produce larger-scale orders. The finished products may not be quite as durable as injection moulded alternatives in the longer term due to the layering additive technology involved.
Ready to Speak to Our Experts?
If you have a project that you would like to see brought to life by the 3D printing industry, speak to us at Adreco Plastics to see how we can help. Our experts are standing by to discuss your ideas and requirements as part of a no-obligation, initial consultation.
What is 3D printing?
3D printing is the process by which a computer-aided design is turned into a 3D product using a 3D printer and plastic filament, which is built up, layer by layer to form the finished product.
How much does it cost?
As with any manufacturing and design process, the cost will be dependent on a wide range of factors, including complexity and scale of design, timescales and quantities needed. Speak to Adreco Plastics for a better idea of the potential costs involved.
How does it work?
It works by layering thin slices of plastic on top of each other to build up a pre-programmed design using additive technology. The plastics layers adhere to each other as they cool to form a strong and durable finished product.
What is the main use?
It is being used across several sectors with uses as diverse as medical devices, food and retail packaging, toys, construction tools and automotive parts. It is a preferred manufacturing solution for smaller-scale orders and projects involving a high level of customised design.
What material can be used in 3D printing?
It uses a range of plastics and other materials that can be softened to form the desired shape and then cooled to solidify and strengthen the finished form. Materials can include plastics and polymers (such as ABS filament and PVC), resin, metal, nylon, carbon fibre and paper.
How much does printing material cost?
It uses a range of plastics and other materials that can be softened to form the desired shape and then cooled to solidify and strengthen the finished form. Materials used can include plastics and polymers (such as ABS filament and PVC), resin, metal, nylon, carbon fibre and paper.
What plastic is used in 3d printing?
The plastics material used are :
- Acrylonitrile Butadiene Styrene (ABS)
- Polylactic Acid
- Polyvinyl Alcohol Plastic (PVA)
- PETG
- Polycarbonate
- Nylon
- Rigid opaque plastics
- Polyamide for Selective Laser Sintering (SLA)
How durable is 3d printing plastic?
Plastics made from 3D printing usually are very durable, and is it also depends on the type of materials we use. Products made from ABS plastics generally have high durability. It can withstand high heat and higher durability, and hence it is widely used to create 3D products. On the other hand, PLA is hard yet can be broken or shattered by powerful impact. Products made from PEGT is more durable than ABS and PLA. It is also denser and more rigid.
Are 3D Printed Parts Strong & Durable? PLA, ABS & PETG – 3D Printerly
Companies worldwide have recently turned to 3D printing to create technical parts quickly while saving some money in the process. But, developing 3D versions of pieces involves using new materials that might not be as durable. So, are 3D printed parts strong?
3D printed parts are very strong, especially when using specialized filament like PEEK or Polycarbonate, which is used for bullet-proof glass and riot shields. Infill density, wall thickness and print orientation can be adjusted to increase strength.
There’s a lot that goes into the strength of a 3D part. So, we’re going to be reviewing the materials used during 3D printing, how strong they really are, and what you can do to increase the strength of your 3D printed parts.
Are 3D Printed Parts Weaker & Fragile?
No, 3D printed parts aren’t weaker and fragile unless you 3D print them with settings that don’t give strength. Creating a 3D print with a low level of infill, with a weaker material, with a thin wall thickness and low printing temperature is likely to lead to a 3D print that’s weak and fragile.
How Do You Make 3D Printed Parts Stronger?
Most 3D printing materials are rather durable on their own, but there are some things that can be done to increase their overall strength. This mostly comes down to the minor details in the design process.
Most important would have to be manipulating the infill, wall thickness, and the number of walls. So, let’s take a look at how each of these factors can impact the strength of a 3D printed structure.
Increase Infill Density
Infill is what’s used to fill in the walls of a 3D printed part. This is essentially the pattern within the wall that adds to the density of the piece overall. Without any infill, the walls of a 3D part would be completely hollow and rather weak to outside forces.
Infill is a great way to increase the weight of a 3D part, also improving the strength of the part at the same time.
There are plenty of different infill patterns that can be used to improve the strength of a 3D printed piece, including a grid infill or a honeycomb infill. But, just how much infill there is will determine the strength.
For regular 3D parts, up to 25% is likely more than enough. For pieces designed to support weight and impact, closer to 100% is always better.
Increase Number of Walls
Think of the walls of a 3D printed part as the support beams in a house. If a house only has four exterior walls and no support beams or interior walls, just about anything can cause the house to collapse or give under any amount of weight.
In the same way, the strength of a 3D printed piece will only exist where there are walls to support weight and impact. That’s exactly why increasing the number of walls inside a 3D printed piece can increase the strength of the structure.
This is an especially useful strategy when it comes to larger 3D printed parts with a greater surface area.
Increase Wall Thickness
The actual thickness of the walls used in a 3D printed piece will determine how much impact and weight a part can withstand. For the most part, thicker walls will mean a more durable and sturdy piece overall.
But, there does seem to be a point at which it’s difficult to print 3D printed parts when the walls are too thick.
The best part about adjusting the wall thickness is that the thickness can vary based on the area of the part. That means the outside world probably won’t know that you’ve thickened the walls unless they cut your piece in half to dissect it.
Generally speaking, extremely thin walls will be quite flimsy and won’t be able to support any exterior weight without collapsing.
Generally, walls that are at least 1.2mm thick are durable and strong for most materials, but I’d recommend going up to 2mm+ for a higher level of strength.
The Strength of Materials Used to Create 3D Parts
3D printed parts can only be as strong as the material that they’re made of. With that said, some materials are a lot stronger and more durable than others. That’s exactly why the strength of 3D printed parts varies so greatly.
Three of the more common materials used to create 3D parts include PLA, ABS, and PETG. So, let’s discuss what each of these materials is, how they can be used, and how strong they really are.
PLA (Polylactic Acid)
PLA, also known as Polylactic Acid, is perhaps the most popular material used in 3D printing. Not only is it quite cost-effective, but it’s also very easy to use to print parts.
That’s why it’s often used to print plastic containers, medical implants, and packaging materials. In most circumstances, PLA is the strongest material used in 3D printing.
Even though PLA has an impressive tensile strength of about 7,250 psi, the material does tend to be a little brittle in special circumstances. That means it’s a little more likely to break or shatter when placed under a powerful impact.
It’s also important to note that PLA has a relatively low melting point. When exposed to high temperatures, the durability and strength of PLA will severely weaken.
ABS (Acrylonitrile Butadiene Styrene)
ABS, also known as Acrylonitrile Butadiene Styrene, isn’t quite as strong as PLA, but that doesn’t at all mean that it’s a weak 3D printing material. In fact, this material is much more capable of withstanding heavy impact, often flexing and bending rather than shattering completely.
That’s all thanks to the tensile strength of about 4,700 PSI. Given the lightweight construction yet impressive durability, ABS is one of the best 3D printing materials out there.
That’s why ABS is used to make just about any type of product in the world. It’s quite a popular material when it comes to printing children’s toys like Legos, computer parts, and even piping segments.
The incredibly high melting point of ABS also makes it able to withstand just about any amount of heat.
PETG (Polyethylene Terephthalate Glycol-Modified)
PETG, also known as Polyethylene Terephthalate, is usually used to develop more complex designs and objects when it comes to 3D printing. That’s because PETG tends to be much denser, more durable, and more rigid than some of the other 3D printing materials.
For that exact reason, PETG is used to make plenty of products like food containers and signage.
Why Use 3D Printing at All?
If 3D printed parts weren’t at all strong, then they wouldn’t be used as an alternative production method for many supplies and materials.
But, are they as strong as metals like steel and aluminum? Definitely not!
However, they are quite useful when it comes to designing new pieces, printing them at a lower cost, and getting a good amount of durable use out of them. They’re also great for small parts and have a generally decent tensile strength given their size and thickness.
What’s even better is that these 3D printed parts can be manipulated to increase their strength and overall durability.
Conclusion
3D printed parts are definitely strong enough to be used to make common plastic items that can withstand great amounts of impact and even heat. For the most part, ABS tends to be much more durable, though it does have a much lower tensile strength than PLA.
But, you also need to take into consideration what’s being done to make these printed parts even stronger. When you bump up the infill density, increase the number of walls, and improve the wall thickness, you’re adding to the strength and durability of a 3D printed piece.
What is the most durable material for 3D printing?
3DPrintStory     3D printing process     What is the most durable material for 3D printing?
While the 3D printing process seems like a great alternative to traditional manufacturing methods, the parts produced can be fragile and unusable. As a rule, this is the result of using standard materials that are not designed for strength and durability. But there is a solution: use durable materials! Durable 3D printing materials can greatly enhance your options, as you can print parts and assemblies for small projects without fear of breakage.
In this article, we'll take a look at the three most durable types of 3D printing materials. However, before that, we will take a closer look at what strength means in terms of filament materials.
What is strength and how do we evaluate it?
The strength of a material can be measured and evaluated in different ways. In this article, we will mainly use tensile strength (stress before something breaks). We will list the tensile strength of each 3D printing material in pounds or pounds per square inch (PSI).
Despite the obvious number of pounds the material can support, there is still a margin of error depending on how the part was printed. We've compiled research from a variety of sources to make sure these three materials are the strongest.
You must also understand that the material itself is not the only factor that affects the strength of the finished product. The design itself, post-processing and the 3D printing process also affect the strength of the part.
Polycarbonate
Polycarbonate (PC) is considered by many manufacturers and reviewers to be the strongest 3D printing filament available. In particular, it is possible to achieve high strength of polycarbonate products by 3D printing with an all-metal hot end and a 3D printer in a case that is isolated from the influence of the external environment.
Some Numbers
Airwolf 3D has come to the conclusion after many filament tests that polycarbonate is the best choice of durable filaments for desktop 3D printers. They were able to hang up to 685 pounds on a polycarbonate printed hook and found that this material had a tensile strength of 9800 psi. In contrast, the same part printed in PLA could only support 285 pounds.
Using a similar test, MatterHackers studied the tear strength of this type of thread, as well as a number of other materials. They were able to hang an average of 409 pounds on the polycarbonate hook, while the PLA parts had a significantly lighter average weight of just 154 pounds.
Finally, renowned 3D printing YouTuber Thomas Sunladerer reviewed several polycarbonate materials and gave very positive feedback on the strength of the material.
3D printing with polycarbonate
It is worth noting that the quality of 3D printing with polycarbonate is not very good. Compared to other materials, protrusions and small details may not turn out as well as using the same PLA.
According to Rigid.Ink, polycarbonate is mostly sold in clear. This 3D printing material has excellent heat resistance as well as impact resistance. But note that you will have to print at high temperatures. As mentioned above, it is better to use an enclosed 3D printer and a solid metal hotend.
Pros of polycarbonate : extra strong, excellent thermal and impact resistance.
Cons of polycarbonate : does not cope well with protrusions and small details of a 3D model, requires a body and an all-metal hot end, a limited number of colors.
Nylon
Next on our list of durable 3D printing materials is nylon. This material is considered by many to be the most reliable for desktop 3D printers. Nylon is inferior in strength to polycarbonate, but still clearly stronger than other competitors such as PLA and ABS.
Some numbers
A hook printed with nylon (910) thread had a breaking strength of 7,000 psi, while the same ABS hook only had a strength of 4,700 psi, according to Airwolf 3D. Airwolf 3D also noted that the nylon filament-printed clip holds 485 pounds.
MatterHackers posted similar results and noticed that a hook printed with their NylonX material can hold an average of 364 pounds before it breaks. Rigid.Ink also reviewed some nylon threads and gave them a four out of five rating for strength and a five for durability. For comparison: the strength and durability of PLA is three conventional units.
Nylon 3D printing
Nylon is slightly easier to print than polycarbonate, but it's still not PLA. Nylon filament is quite hygroscopic, so it must be kept dry and requires a high printing temperature of 220-270°C. This material is prone to slight warpage, but is also resistant to impact, fatigue, and high temperature.
Nylon pros: impact resistance, fatigue resistance, heat resistance, easier to print than polycarbonate.
Nylon 9 cons0042 : hygroscopic, warping, very high hot end temperature required.
Composites
Finally, composite threads, although not essentially a single material, can be extremely strong. Composites are threads with certain additives that affect the properties of the material, including to increase strength. The names of these threads usually have the words "pro", "reinforced" (reinforced) or "infused" (infused), since they are usually a mixture of different materials.
For this reason, it is impossible to assess where the composite fibers are compared to the two previous materials. Some composites, such as Carbonyte, can compete with nylon threads for strength, while some composites are less durable.
It all depends on what the composite thread consists of. Durable is usually a high strength material such as nylon impregnated with another high strength material such as carbon fiber or glass.
Speaking of carbon fiber, this is also a very strong filament that is sometimes used for 3D printed bicycles. However, some composite fibers are stronger than many pure carbon fibers, so they are not in the top three, but deserve special mention as composite fibers.
Some numbers
We will use carbon fiber nylon and glass fiber nylon threads as examples. MatterHackers has determined that hooks printed on these materials can hold an average of 349and 268 pounds respectively.
Rigid.Ink gave the fiberglass nylon filament four out of five ratings for strength and five for durability. They also gave the carbon fiber nylon a five out of five rating for both strength and durability. In comparison, PLA and ABS were in the top three for strength.
3D printing with composites
Composites vary in the way they are 3D printed, but they are generally relatively similar to their base material. Durable composite fibers are usually made from nylon, so you'll have to print at fairly high temperatures. These threads are also quite expensive.
Advantages of composites : This is a combination of several materials to achieve the best possible properties, durable.
Cons of composites: Expensive, requires high 3D printing temperatures.
WHICH IS BETTER ABS OR PLA? WE DESTROY THE MYTHS. / Articles
Which plastic is better?
PLA-PLASTIC (POLYLACTIDE)
This is a completely biodegradable, safe, environmentally friendly product derived from corn or sugar beets. It does not use fossil fuels in its production. During operation, when heated, PLA emits a semi-sweet smell. These characteristics make PLA plastic the most suitable material for use in indoor areas, schools and offices. PLA is the best material to get started with a 3D printer. The lower deformation of this plastic promotes the correct printing of the model, and also provides a high print resolution, allowing you to create models of greater geometric complexity than with ABS. When printing with PLA, it is recommended to use a fan to cure the products faster and achieve better print quality. The main drawback of PLA plastic is the peeling of corners (delamination). Does not absorb moisture.
ABS PLASTIC (ACRYLONITRILE BUTADIEN STYRENE)
This is a tough and tough fossil fuel derived polymer used to make Lego bricks and plastic phone cases. When printing large objects, be careful as warping is possible due to thermal distortion as the parts cool down. Due to the high melting point of ABS, the use of a heated print bed is recommended to ensure proper layer adhesion and avoid issues such as warping. Kapton tape can also be used to improve adhesion. The use of ABS plastic is recommended for the manufacture of parts exposed to high temperatures. To process the finished products made of ABS plastic and soften the surface, acetone is used (in the form of steam in a closed container or using a special brush), it is also possible to cover the surface of the model with acrylic paint. Typical disadvantages of ABS plastic are cracking, curling corners, and layer separation.
General
Both plastics can be drilled, sanded, polished and painted with acrylic paint. They are sold in the form of spools weighing 1 kg, with a thread diameter of 1.75 or 3 mm.
PLA Myths
- Dissolves in water and deforms when wet. Water soluble plastic is PVA (polyvinyl acetate), not PLA.
- Being biodegradable, it decomposes in a few months. The product will only degrade if it is exposed to atmospheric agents for a long time. In addition, the use of materials with similar characteristics is one of the ways to care for the environment.
- ABS is much stronger than PLA . In injection molded plastic items, ABS parts are more durable. The technology of three-dimensional printing is based on the method of layer-by-layer deposition. Thus, if the adhesion of PLA plastic layers is higher than that of ABS, objects made with it will be much stronger.
Specifications | PLA | ABS |
Density (g/cm3) | 1.25 | 1.05 |
Tensile strength (MPa, 23 ºC) | 28 MPa | 30 MPa |
Softening point | ~ 60 °C | ~ 110 °C |
Melting point | ~ 180°C | ~ 220 °C |
Extrusion temperature | ~190-200°C | ~220°C |
ABS | PLA |
Heated platform required (increased energy costs) | The use of a heated platform is not strictly necessary |
Good results without using a fan during printing | Use of a fan is highly recommended when printing |
Better adhesion with Kapton Tape | Good adhesion to various surfaces |
Limited strength plastic | Better print clarity, better layer adhesion |
Prone to cracking, layer separation and corner curling | Prone to corner peeling and bulging |
More flexible.![]() |