Fiberglass 3d printer filament
FibreX™ Nylon+GF30 3D Filament | Glass Fiber Reinforced
ON SALE
$48.00 – $185.00
4 interest-free payments with Learn More
FibreX™ PA6+GF30 glass fiber reinforced nylon copolymer is an engineering-grade material that has excellent mechanical and thermal properties [HDT of 170°C] while offering ease of printing in a wide array of desktop printers. This material is a must-have when printing functional prototypes and production parts.
[yith_wcwl_add_to_wishlist]
SKU: Select options above Brand: FibreX™ Categories: Glass Fiber Nylon, Nylon Family, Glass Fiber Filaments
- Description
- Reviews
- Questions & Support
Our Nylon+GF30 glass fiber reinforced Nylon 6 Copolymer (PA6) is nothing less than an industrial-grade beast! Formulated to be exceptionally stiff and strong, all without being brittle. Polyamides (PA) are the work horse of the plastics industry the world over thanks to their excellent mechanical, chemical, and thermal resistance. The addition of heavy glass fiber reinforcement takes it to the next level.
Gearbox HT2™ 3D Printer:
Print industrial-grade parts using our Nylon+GF30 and more with the new Gearbox™ HT2 High-Temp 3D Printer.
Extruder Temp
260-280°C
Bed Temp
60-75°C
Heated Chamber
Not required
Nozzle Specs
0.4mm diameter minimum
Hardened Steel Nozzle
Bed Adhesion
Magigoo Bed Prep
Layer Height
0.25mm or higher
Drying Specs
90°C for 4 hours
Supports
X1 USM Water Soluble Support
Benefits of Nylon+GF30 Include:
- Printable on practically any 3D printer with a heated bed
- Ideal for structural engineering-grade applications
- Exceptionally stiff and strong, without being brittle
- Excellent chemical resistance makes it suitable for automotive and industrial applications
- Resists fuels, lubricants, heat, and mechanical loading
- High thermal properties keep it strong up to 170°C in use, depending on printing and mechanical loads applied
- Glass fiber reinforcement improves dimensional stability, reduces shrinkage, lift, and warp
- Very strong layer bonding
Filament Specifications:
1. 75mm and 2.85mm +/- 0.05mm in diameter
Recommended Print Settings:
- Extruder: 260-280°C
- Bed Temp: 60-75°C
- Nozzle: We currently recommend a hardened steel nozzle with a minimum diameter of 0.4mm
- Other: Ideal layer height is 60% of nozzle diameter. We do not recommend printing layers smaller than 0.25mm with glass fiber reinforced filaments
- Bed Prep: Magigoo Bed Prep or 3DXTECH Polyimide Tape gives us the best results
- Heated Chamber: Not required, but a 30-80°C chamber does improve layer bonding and finished part mechanical properties
- Supports: AquaTek™ water soluble X1 USM Universal Support Material works ideal for complex parts.
- Drying Instructions: 90°C for 4 hours.
What Is It?
Fibers made of glass reinforced into the polymer during manufacturing and aligned along the axis of filament.
This, along with their physical makeup, give this material enormous strength and mechanical properties.
What Does It Do?
Glass fiber reinforcement gives material a lot of desirable properties:
- High strength
- High stiffness
- High chemical resistance
- Low thermal expansion
How Does It Work?
Reinforcing plastic with glass fibers produces a 3D printing filament which exhibits the best properties of both fiberglass and the plastic of choice.
What Is It Good For?
Ideal for any applications which require strength and rigidity.
For these reasons, glass fiber reinforced filament is very popular in automotive, mechanical, civil engineering, and research industries.
What Is It?
Fibers made of glass reinforced into the polymer during manufacturing and aligned along the axis of filament.
This, along with their physical makeup, give this material enormous strength and mechanical properties.
What Does It Do?
Glass fiber reinforcement gives material a lot of desirable properties:
- High strength
- High stiffness
- High chemical resistance
- Low thermal expansion
How Does It Work?
Reinforcing plastic with glass fibers produces a 3D printing filament which exhibits the best properties of both fiberglass and the plastic of choice.
What Is It Good For?
Ideal for any applications which require strength and rigidity.
For these reasons, glass fiber reinforced filament is very popular in automotive, mechanical, civil engineering, and research industries.
Abrasive Material
This material is particularly abrasive among 3D printing filaments. Users may find standard brass nozzles are chewed through very quickly compared to standard wear and tear. When worn through, the nozzle diameter will widen inconsistently and the printer will experience extrusion issues.
Because of this, it's strongly recommended this material be printed through a hardened steel nozzle rather than a softer metal. Hardened steel nozzles can often be inexpensive and easily installed depending on your printer manufacturer's instructions.
Questions?
Send us a message and we'll reach out as soon as we can!
Please enable JavaScript in your browser to complete this form.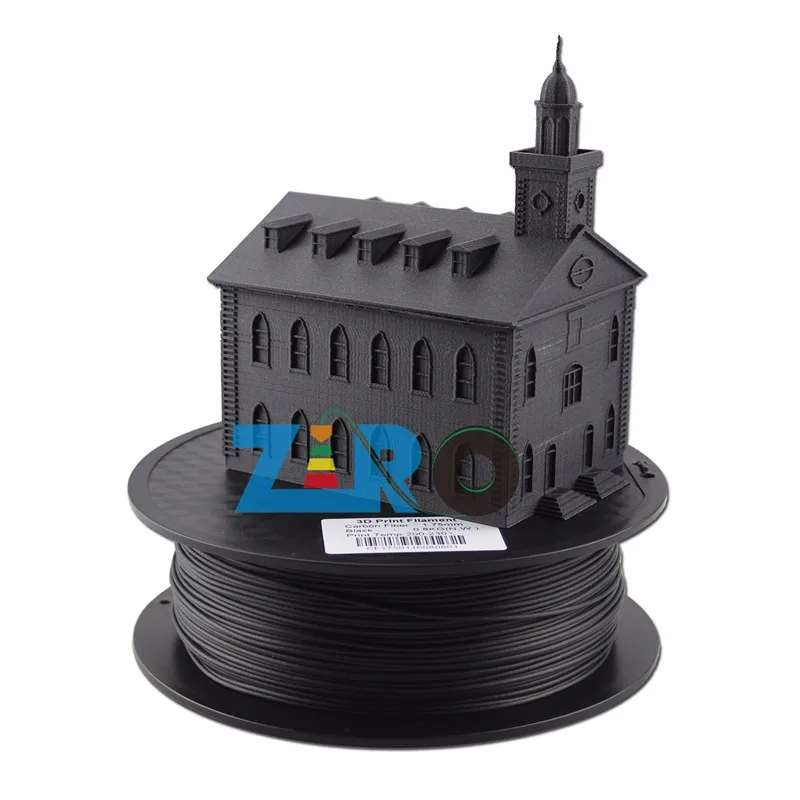
Name *
Business / Organization
Email *
Phone
What can we help you with? *
Newsletter Signup
- Sign me up for the 3DXTECH newsletter
Glass vs. carbon fiber 3D printing composites
David Durbin16 October 2019
Applications
Both glass and carbon fiber composites extend the versatility of fused filament fabrication (FFF) 3D printing by enhancing a part's mechanical properties.
For example, by using glass or carbon fiber composite materials on a compatible 3D printer (like the Ultimaker S5 Pro Bundle or Ultimaker S3), you can quickly and affordably produce high-strength parts that:
Validate geometries
Optimize designs
Reduce weight
Consolidate assemblies
Test prototypes that will be injection molded
Replace metal components
But which composite 3D printing materials should you choose in the first place?
Choosing the right fiberglass or carbon fiber composite is key to the success of your 3D printing application
After all, both glass and carbon fiber filaments can end up having similar mechanical properties in a 3D printed part.
This is especially true when leading materials companies (like those whose print settings profiles are downloadable via the Ultimaker Cura Marketplace) can boost various properties by tweaking:
Base polymer choice (e.g. ABS, nylon, polycarbonate)
Base polymer mix (e.g. ABS + polycarbonate)
Fiber length (e.g. long or chopped, short or milled)
Fiber fill percentage (e.g. 20% glass fiber)
And many more variables...
So why would you choose one fiber over the other?
Glass vs. carbon fiber composites – which is the winner?
Roger Sijlbing, Head of Sales at BASF 3D Print Solutions Additive Extrusion Systems, told us:
There are a lot of considerations to determine which material fits the application. Even within for example automotive, both [glass and carbon fiber composite] materials could fit. It depends on the requirements of the application and the total cost of ownership.
![]()
So, to guide your material choice based on the requirements of your 3D printing applications here's an at-a-glance list to show which composite (generally) wins for different 3D printing requirements:
Requirement | Winner? |
---|---|
More affordable | Glass fiber |
Tensile strength | Carbon fiber |
Stiffness | Carbon fiber |
Durability | Glass fiber |
Flexibility | Glass fiber |
Low weight | Carbon fiber |
Heat resistant | Both |
Chemical resistant | Both |
Fatigue resistant | Carbon fiber |
UV-light resistant | Both |
ESD safe potential | Carbon fiber |
Electrical conductivity potential | Carbon fiber |
Allows radio wave passthrough | Glass fiber |
Multiple colors available | Glass fiber |
That might be useful if any of those properties are a priority for your application.
But what if there’s still no clear choice between glass and carbon fiber for your 3D printing needs? Then, there are a few more considerations to inform your choice.
To understand these, let’s dig deeper into the manufacturing processes involved...
How glass and carbon fibers are made
Glass fiber
Glass fibers began to be commercially produced in 1936. In fact, the material's invention led to the partnership known today as Owens Corning.
Glass fibers are made by melting silica to remove impurities. The liquid glass is then extruded through a heated metal plate with small holes – called a bushing. While the glass strings are cooled from around 1,200 °C with water and air, they are stretched into thin fibers as they are pulled onto a winder.
Owens Corning created two glass fiber composite filaments, XSTRAND®. Their predefined print settings are downloadable via Ultimaker Marketplace
Carbon fiber
Carbon fiber’s manufacturing process takes place at a molecular level. Despite the material's higher price tag, its rigidity and excellent strength-to-weight ratio have made carbon fiber the composite additive of choice for lightweight automotive and aerospace applications.
Starting life as a liquid polyacrylonitrile precursor, the fibrous mix of carbon atoms is then oxidized at around 300 °C to stop fibers from melting together. Then it is carbonized in an oxygen-free oven at temperatures of up to 1,000 °C. This process causes atoms to fuse and then expel any impurities, resulting in pure carbon atoms in very rigid strings.
Afterwards, carbon fiber strings pass through a surface treatment bath to etch the surface of the carbon. This makes the carbon strings more resilient and better able to stick to coating chemicals.
Coating, chopping, or milling fibers for use with 3D printing filament
Technically known as 'sizing', coating chemicals (like polyurethane, epoxy, or glycerin) allow the inert glass or carbon fibers to more easily interface with the polymer it will be mixed with. By matching the chemistry of that polymer, the coating strengthens the adhesive bond.
Fibers are usually coated when they will be cut or 'chopped' into lengths of up to 7 mm. The result is a composite 3D printing material that is reinforced by ‘long fibers’ that weave together within the polymer matrix.
But not all carbon and glass fiber used in 3D printing filament is coated.
The manufacturing process for each glass or carbon fiber composite affects the 3D printed materials' mechanical properties
While not coating or using a lower-quality coating might be a reason a composite material is less expensive, it can also be a legitimate choice.
That's especially true if the fibers will be milled into a fine powder, also known as 'short fibers'. Between 30 to 150 microns in length, these fibers have a large surface area making coating less necessary. In this case, the composite filament would more accurately be described as 'filled' (rather than 'reinforced') with carbon or glass fiber.
This approach of not coating milled fibers is not necessarily a bad thing. It just results in different material properties. Instead of being stiffer and stronger, the composite material will likely be more durable and impact-resistant.
After coating, chopping, or milling, the fibers are mixed with the base polymer(s) to create a composite material that can then be extruded into 3D printer filament.
This final filament extrusion is important because it's here that the long glass or carbon fibers become orientated within the polymer matrix. Running along the length of the filament, they create a weaving effect that provides extra strength for a 3D printed part. (This orientation is the reason why FFF 3D printers can extrude filament with up to 7 mm long fibers, through a 0.4 or 0.6 mm nozzle.)
Glass or carbon fibers up to 7 mm in length reinforce filament that can be extruded through Ultimaker print core CC Red's 0.6 mm nozzle
How to choose between different composite materials
With so many things in life, you get what you pay for. And composite 3D printing materials are no different
Composite materials from smaller filament companies may be more affordable. But because they don't necessarily specialize in the material science used to develop the composite, these companies might buy ready-made pellets from a larger wholesaler. They then extrude the filament themselves, on machines that may not have the torque required to properly orientate the fibers within the polymer matrix, resulting in a lower-quality filament.
By contrast, leading manufacturers have decades of expertise in developing reinforced polymers – often for the injection molding industry. By applying that expertise to additive manufacturing, using the highest-quality fibers, coatings, and processes, they fine-tune their polymer matrixes and extrude them on industrial-grade machines. This results in a filament that more readily carries the mechanical properties you need over to your 3D printed part.
For example, composite filaments from Clariant include:
BASF's composite filaments include:
PAHT CF15
PET CF15
PP GF30
And Owens Corning's:
XSTRAND® GF30-PA6
XSTRAND® GF30-PP
Download predefined composite material profiles from Ultimaker Marketplace for a plug-and-play 3D printing experience
Conclusion: Make an informed choice
All these composite filaments (and many more) are listed in the Ultimaker Cura Marketplace.
By downloading their predefined print profiles, you gain a plug-and-play 3D printing experience with the Ultimaker S5 Pro Bundle and Ultimaker S3 – without the need for trial-and-error. Plus, the materials’ descriptions and datasheet links make it easier to choose the right composite material for your application.
This means you can be more confident to achieve the mechanical properties and high-quality results you need – even with your first print.
And with a deeper understanding of how carbon or glass fibers are used to reinforce 3D printing filament, you can leverage the many benefits of composite materials for your own in-house production needs.
To access the Marketplace, download Ultimaker Cura for free here:
Download Ultimaker Cura
Large Format Raise3D RMF500 for 3D Printing with Carbon Fiber Reinforced Materials
Last autumn, the well-known Chinese manufacturer of 3D printers, Raise3D, announced the creation of a new 3D printer for small-scale production in the industrial sector - RMF500 . The unique feature of the novelty is the combination of the ability to print with carbon fiber reinforced material (colloquially carbon fiber), wide format and affordability .
We all know that high technology is becoming more accessible every day, and the RMF500 is a prime example of this. There have been systems on the 3D printing market for several years that print carbon fiber composites of similar quality, but, unfortunately, they are not available to all companies due to the very high cost and supply problems. For example, such professional 3D printers are produced by the American company Stratasys - Fortus 450mc, but they are equipped with less technological features and are much more expensive.
Let's take a closer look at what the RMF500 is and how it differs from other 3D printers.
The RMF500 is specifically designed for printing complex parts with high durability. It will enable 3D printing companies to expand their product portfolio with carbon fiber and fiberglass end parts. Both materials specially developed by Raise3D, such as PA12 CF, and materials from other manufacturers approved by Raise3D under the Open Filament Program (OFP) will work. Parts made of carbon and fiberglass are more rigid, durable, resistant to heat and shock than parts made of other plastics. For carbon and fiberglass printing, the RMF500 uses silicon carbide nozzles with a hardness of more than 60 HRC.
PA12 CF filament is the result of long-term development by Raise3D engineers. This is a carbon fiber reinforced filament with increased stiffness and reduced shrinkage and does not require a thermostatic print chamber. The parts obtained from it are light and extremely durable, sometimes they can even be used instead of metal. In addition, the company has developed the PPA GF glass-filled filament specifically for the RMF500 and plans to release PET-CF, ASA-GF, PPSU-GF and PP plastics for medical use. Raise3D promises that all fiber reinforced plastics will be competitively priced.
The RMF500 has a huge building area 500x500x500 mm. The size of the build area matters in the production of large parts and small-scale production. For comparison, the print area of the Fortus 450mc is 406x355x406mm.
In the photo: printing a large model with carbon fiber in the RMF500 3D printer from Raise3D.
Repeatability and print speed are very important for low volume production. The maximum print speed of the RMF500, according to the manufacturer, can reach 300 mm/s. Positioning accuracy along the XY axis - 1 micron, along the Z axis - 0.09765 microns.
Synchronous feedback control with 1 µm accuracy reduces speed fluctuations as motor load changes, further improving accuracy. Stability and repeatability of printing has long been a hallmark of Raise3D printers. The FFF technology on which this 3D printer is based allows the production of parts with a high degree of repeatability, high positioning accuracy and uniform extrusion. The RMF500 can quickly print large batches of identical parts.
Pictured: production of lots from a large number of parts on the RMF500.
The printer has a printing system with two independent IDEX extruders. It allows you to print with one or two extruders at once. The RMF500 can run two jobs at the same time, further increasing productivity and task speed. The extruders are manufactured using high temperature alloys and industrial ceramic composite materials. These characteristics provide stable and high extrusion speed up to 500 g/h.
The RMF500 has a strong design . The one-piece frame is made of hardened steel. Stainless steel linear guides have a design load of approx. 100 kg. The bearing of the linear guides has minimal backlash and does not require frequent maintenance.
An important detail - Raise3D has developed special support material for printing with reinforced plastic PA12 CF, which can be easily detached.
Pictured: Parts printed on the RMF500 with PA12 CF filament with special proprietary support.
The RMF500 is equipped with four large compartments for plastic spools. Switching between the main and auxiliary compartments occurs automatically. This feature reduces the amount of time spent threading the filament. The humidity control system keeps the relative humidity in the chamber below 5%, preventing humid air from entering from outside.
What else is there in the RMF500 from nice additional options. The front of the printer has a large 13.3-inch touch screen. Supports connection, management and printing via Wi-Fi and LAN. There is a reliable auto-calibration system from Raise3D.
Carbon fiber printed parts are strong enough to be used in the automotive and aerospace industries. Of course, they will not replace functional parts that have a special load, but their scope can be very wide. Raise3D has already presented the results of the first RMF500 printing and its application.
Pictured: Functional parts, accessory tools and fixtures, car décor printed on the RMF500.
Pictured: Functional parts, accessories and aerospace prototype printed on the RMF500.
In the photo: on the left is a prototype of the hinged window mechanism (details are printed with metal filament and carbon), on the right is a carbon fixture. Carbon parts printed on RMF500, metal parts printed on Metalfuse. Printing with fiber-filled plastics does not require a heated chamber, peak power consumption is less than 3 kW. The average power consumption per unit of print area of the RMF500 is 60% lower than the competition.

Operating temperature of the extruder | to 330 ℃ | to 300 mm/s 900 mm/s 900 mm/s 900 mm/s 900 mm/s 900 mm/s 900 mm/s 900 mm/s 900 mm/s 900 mm/s 900 mm/s -filter | yes |
Build Tak pad surface | yes |
Positioner | Rockchip ARM Cortex-M4 |
Operating systems | Linux, Windows, iOS |
Maintained file formats | STL/ Obj/ OLTP |
ETERARNETS, WIRELESS 802.1 | |
Ports | USB 2.0 × 1 |
Electrician | 30 A @ 380 volts AC |
Energy consumement | 24 V, 350 WATT; 12V, 75W |
Memory | 1 GB, built-in flash memory 8 GB |
Sizes (without packaging) | 1340 × 2370 mm |
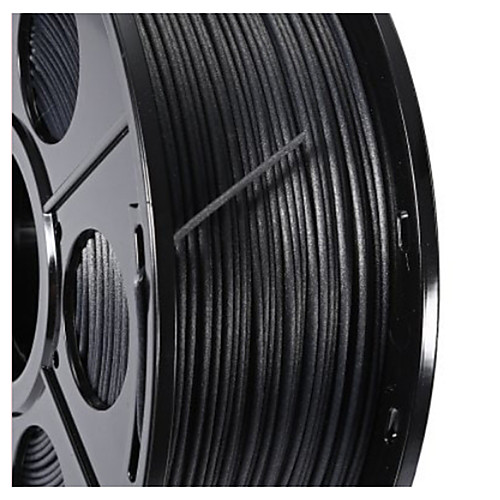
3D Printer Filament Buyer's Guide
6 - Nylon (Nylon), PA (Polyamide)
WHAT IS NYLON?
Nylon or polyamide, a popular family of synthetic resins used in many industrial applications, is the champion in the world of professional 3D printing. Compared to most other types of 3D printer filament, it takes first place in the competition for strength, flexibility and durability.
USER NOTE
Another unique feature of this 3D printing filament is that it can be dyed both before and after the printing process. Nylon also has a drawback - it, like PETG, is hygroscopic, strongly absorbs moisture. Remember to store both materials in a cool, dry place, keep these filaments in perfect condition, and this will ensure the best quality prints. Better yet, dry it before printing.
in general, there are many varieties of nylon, but among the most common for use as a thread for a 3D printer-618 and 645.
Thread properties for 3D printer: nylon (polyamide)
-
Difficulty: Medium
-
Print Temperature: 240 ° C - 260 ° C
-
Table temperature: 70 ° C - 100 ° C
-
SAMPARY: Significant
-
disadvantages: Typically, sensitive to moisture, requires a high temperature of the subpolar and table
-
Pros of : Can be used as both support material and strong 3D printer warp filament
-
Cons : Requires dilution with relatively expensive D-limonene to remove supports, only compatible with ABS
-
The "cleaning" temperature depends on what types of 3D printer filament you have used before, and what kind of filament you plan to use next (cleaning filament operating temperature: from 150 to 300°C).
-
It is generally not necessary to use more than 10 cm of cleaning thread at a time.
-
There are other methods of cleaning, such as cold removal of the remaining used filament with a solvent, followed by mechanical cleaning.
-
Pros: is an easy way to achieve a smooth surface for your print on a less complex 3d printer.
-
Cons: higher price compared to ABS or PLA, inability to process items with fine surface details.
-
The main condition is that your printer must be able to print at an extruder temperature of 130 o C.
-
The extruder must be built according to the "Direct" scheme (not Bowden!).
-
Preferably Teflon tube up to nozzle for good filament glide.
-
Adjustable push wheel pressure in a wide range of settings.
-
It is also desirable that the feed gear should not be on the motor shaft, but through the gearbox. The motor heats up and can additionally soften the thread on the broach.
-
Other measures may require modifying the extruder and applying print adhesive to your printer table.
-
Plus: Creation of melted forms using a 3D printer
-
disadvantages: requires a certain type of extruder design and printed platform, limited use
00 Strength: very high | Flexibility: high | Durability: High
Soluble: NO
safety: refer to manufacturer's instructionsWHEN SHOULD NYLON (POLYAMIDE) FILAMENT BE USED?
Taking advantage of nylon's flexibility and durability, this filament can be used to create tools, functional prototypes or mechanical parts (such as hinges, buckles or durable gears), pattern rigging.
Resume
Plus: High flexibility, high flexibility, durability, self -smoked material
PA-GF (glass filled nylon)
Glass fiber reinforced nylon. Compared with pure nylon filaments, the mechanical strength, stiffness, heat resistance and fatigue strength of glass-filled nylon are greatly improved, and shrinkage during 3D printing is reduced. Moreover, the hygroscopicity is reduced.
The "trouble" of pure nylon is the relatively low temperature of the onset of softening and thermal deformation under load - total 50 °С. Filling the thread with carbon fiber helps to defeat this effect.
PA-CF (carbon filled nylon)
Environmentally friendly material based on nylon and 20% carbon fiber . Lightweight, odorless print with a matte finish. High hardness, high rigidity, good toughness, wear resistant material, suitable for printing industrial parts. Deformation temperature 120°C, therefore suitable for high temperature use. Compared to nylon, it has lower shrinkage and distortion. Fire rating: UL94-V2.
The positive experience gained with carbon-filled nylon led major filament manufacturers to make the logical decision to launch other grades of thermoplastic filaments enhanced with carbon fiber content. An overview of the various proposed options for such composite threads is the subject of the next paragraph of this Guide.
7 - Carbon-filled filaments
When 3D printer filaments such as PLA, ABS, PETG and nylon are reinforced with carbon fiber, the result is an extremely strong and stiff material with relatively low weight. Such compounds are particularly advantageous in structural applications that must withstand a wide variety of end uses.
NOTE TO THE USER
The downside of this material's outstanding properties is increased wear on your printer's extruder nozzle, especially if it is made of a soft metal such as brass. Just 500 grams of this exotic 3D printer filament will noticeably increase the diameter of a brass nozzle, so if you don't like frequent nozzle changes, consider using nozzles made of a more durable material - steel or even ruby.
WHEN SHOULD CARBON FILAMENT BE USED?
Due to its structural strength and low density, carbon fiber is the best choice for mechanical components. Do you want to replace a part in your car or aircraft model? Try this filament.
SUMMARY
8 - HIPS (high impact polystyrene)
In commercial production high impact polystyrene (HIPS) is a copolymer that combines the hardness of polystyrene and the elasticity of packaging such as containers, and rubber - commonly found for CDs.
In the world of 3D printing, HIPS usually plays a different role. 3D printers can't print "over the air" - that's where support structures come in. The protruding elements require some support structure, and this is where HIPS really excels. Together with ABS in a dual extruder printer, HIPS acts as an excellent support material.
USER NOTE
Using HIPS as a support material is quite simple. Print support structures on these materials where they are needed, and then carefully break them out with tweezers or other suitable tool. If it is difficult or impossible to get to the support printed with HIPS thread, it can be dissolved with D-limonene. It is also useful to squirt D-limonene at the contact points of the main model and the HIPS support before breaking it out.
Unfortunately, using HIPS as a backing material limits you to printing the main part in ABS only. Other 3D printing materials may be damaged by D-limonene. But HIPS and ABS print well together because they have the same strength, rigidity and close printing temperature.
In fact, despite the fact that HIPS was originally used as a support material, it is a worthy filament for basic printing as well. It is stronger than PLA and ABS, warps less than ABS, and is easy to glue, sand, and paint.
WHEN SHOULD HIPS BE USED?
With many characteristics similar to ABS, HIPS 3D Printing Filament is a good all-round solution for parts that must endure wear or for projects that require post-processing material to achieve the final look.
SUMMARY
9 - PVA (polyvinyl alcohol) advantage is fully used for commercial purposes. Common uses include packing dishwasher tablets or fishing lure bags (throw one into the water and watch it dissolve, releasing the bait).
USER NOTE
The same principle is applied in 3D printing, making PVA an excellent support material when combined with another filament in a dual extruder 3D printer. The advantage of using PVA over HIPS is that it can be used to support more materials than just ABS.
The downside of this filament is that it is a bit more difficult to handle. Care should also be taken during storage - moisture in the atmosphere can damage the filament before printing. Silica gel dry boxes and pouches are a must if you plan to store your PVA coil for a long time.
WHEN SHOULD PVA BE USED?
PVA filament is an excellent choice as a backing material for complex prints with raised features.
SUMMARY
10 — Cleaning
This filament is unique in its kind because it is the only one designed not to print objects. It is intended solely for cleaning the nozzle of a 3D printer from the remnants of any working material after printing. Please note that cleaning the extruder is required not only when it is already clogged. It is especially useful to clean the nozzle when changing to a build with a different color or from one material to another, especially if they are incompatible due to very different extrusion operating temperatures. How can you continue to work with a filament with a relatively low melting point after printing is refractory without completely removing its residue from the nozzle? It is also helpful to keep the extruder clean to prolong its life. Make regular use of the cleaning floss a healthy habit.
NOTE TO THE USER
The usual procedure for using a cleaning filament is as follows: heat the extruder tip to a temperature slightly above the operating temperature for the filament used before. To determine it, before starting the procedure, carefully read the information from the manufacturer of the filament used for printing. First, push the cleaning filament by hand (if your printer is designed to allow this) through the extruder to be cleaned. This is necessary to remove the "burned" material residues. Then lower the temperature to operating temperature and feed approximately 10cm of cleaning floss as normal.
A few additional points of note:
You should definitely clean your 3D printer's extruder between using two materials with completely different temperatures or colors. Generally speaking, it is very useful to regularly run a little cleaning filament through the heating tip of your 3D printer, for example, after a long (more than a day) printing even without a planned filament type change.
SUMMARY
11 - Smooth
Many 3D printed objects require a glossy finish. These are molds for casting in silicone, finishing elements of furniture prototypes or other details that are sensitive to a smooth look. In such cases, the main disadvantage of filament printing (layer-by-layer deposition) plays a very unpleasant role. How to get rid of the characteristic layered structure without applying laborious and expensive mechanical post-processing? Printed ABS objects can be processed in an acetone bath, but this operation is not the most pleasant for the printer user. How to be? The answer is: use an easily smoothed plastic, for example, eSmooth from the Chinese manufacturer eSUN.
USER NOTE
Smooth filament printing is no more difficult than PLA, temperature characteristics are close, no closed 3D printer chamber is required. It is enough to treat the constructed object with ordinary ethyl or isopropyl alcohol and leave it for some time, preferably for 8-9 hours. Alcohol, as it were, melts the outer layer, making the surface glossy. However, during processing, small external parts can “float” or dissolve completely. Therefore, not any geometric shape of a product or tooling can withstand such a smoothing method. This should be taken into account when choosing an object for printing with the Smooth filament.
WHEN SHOULD I USE Smooth?
This interesting filament is recommended for applications where a very smooth printed surface is required and mechanical post-processing is difficult or impossible. It is desirable that there are no small significant elements of construction or design on the surface - they can be melted with alcohol. But details with a rounded surface and smooth transitions will turn out very well!
SUMMARY
12 - Wax3D (Wax thread)
Do you want to get a product made of real brass, pewter or other metal? It's possible! First, you will print your investment casting pattern using 3D printer wax filament, and after a few extra steps, your idea will be embodied in metal.
NOTE TO THE USER
This process is called "lost wax casting" and it works like this:
Create a direct wax mold, i.e. a wax copy of the intended final metal product.
Dip the mold in plaster or other special compound and allow it to dry and harden.
Place an item with a lost shape into the furnace. At a sufficiently high temperature, the wax will melt, leaving a "negative" space inside the shell into which the metal work is to be cast.
The 3D printer wax filament made the first step much easier. According to traditional technology, first it was necessary to prepare a metal mold on a CNC machine, and then pour wax into it to obtain an investment mold for metal casting.
When using this or similar waxy materials, be aware that they are much softer than most types of 3D printer filament. Basic conditions for printing with wax filament:
WHEN SHOULD WAX BE USED?
If you are casting metal parts, wax-like filaments such as Filamentarno WAX3D can give you more options, allowing you to print complex 3D objects directly, integrating into your investment casting workflow.
SUMMARY
13-ASA (acrylonitril-stool)
Of course, ABS is good, but it has its drawbacks: ABS prints tend to denature and yellow if left outdoors in direct sunlight. That's why plastics manufacturers have found an alternative - acrylonitrile styrene acrylate (ASA), a weather-resistant analogue of ABS plastic that was originally developed for outdoor "street" use. Hence its main application is in the automotive industry.
ASA has high rigidity, resistance to dilute acids, mineral lubricating oils, diesel fuel. Unlike ABS, ASA plastic is resistant to UV radiation. The material does not turn yellow in the open air, it is easy to process. The ASA range includes high and low gloss grades. The main application of ASA-plastic is the production of lampshades, car exterior parts (rear-view mirrors), lighting products.
USER NOTE
In addition to being strong and relatively easy to print, this 3D printer filament is also extremely resistant to reheating and, most importantly, shape and color changes.
Another small benefit of using ASA over ABS is that it warps less during printing. But be careful how you set up your cooling fan - the ASA can easily burst if the fan is set too high during printing.
WHEN SHOULD ASA THREADS BE USED?
For a variety of outdoor applications, from replacement electrical outlet covers and architectural trim to custom garden gnomes and birdhouses.
SUMMARY
14 - PP (Polypropylene)
Polypropylene (PP) is strong, flexible, lightweight, chemical resistant and food safe, which may explain its wide range of applications including engineering plastics, food packaging , textiles and banknotes.
USER NOTE
Unfortunately, as a type of 3D printer filament, PP is difficult to print, often exhibiting severe deformation and poor adhesion to the table.