Binghamton 3d printing
3D Printing Service Binghamton, NY | Instant Quotes Online
Our 3D printing capabilities
We have over 90 3D printing shops in our network and are well known for manufacturing high-quality parts at competitive prices, from rapid prototyping with Fused Deposition Modeling (FDM) to functional end parts made with Selective Laser Sintering (SLS) or Multi Jet Fusion (MJF).
Gallery of 3D printed parts manufactured by Hubs
With over 65,000 customers from every industry, including aerospace, defense, robotics, medical, machinery, automotive and electronics, we have extensive experience meeting a diverse range of 3D printing requirements, from prototyping to production: Visual aids, concept models, injection-molding prototypes, form-fit & function prototypes, tooling and casting patterns, jigs, grips and fixtures, and durable end parts.
HP PA 12 - Dyed Black
Customer | True North Design |
Purpose | Structural and vacuum EOAT components |
Process | SLS / MJF |
Unit price | $69. |
Industry | Automotive |
Prototyping PLA
Customer | Allision Conner |
Purpose | End caps and cable strain relief for sheet metal enclosure |
Process | FDM |
Unit price | $7.92 / $4.72 / $2.80 |
Industry | Industrial Automation |
HP PA 12
Customer | US Hammer |
Description | A part for gasoline engine powered jackhammers |
Process | MJF |
Unit price | $22.18 |
Industry | Construction |
Markforged Onyx - Black
Customer | Autocom Manufacturing |
Purpose | A production part for 3D printed lathe gantry gripper fingers |
Process | FDM |
Unit price | $48.![]() |
Industry | Automotive |
PC Stratasys - white
Customer | Terumo medical corporation |
Purpose | Prototyping parts used for a disposable electrical device |
Process | FDM |
Unit price | $55.38 / $32.96 |
Industry | Medical |
Formlabs Clear Resin
Customer | Aversan Inc |
Purpose | A prototyping part of an injection molded component for an automated door mechanism |
Process | SLA |
Unit price | $29.83 |
Industry | Aerospace |
HP PA 12 - Dyed Black
Customer | True North Design |
Purpose | Structural and vacuum EOAT components |
Process | SLS / MJF |
Unit price | $69.![]() |
Industry | Automotive |
Prototyping PLA
Customer | Allision Conner |
Purpose | End caps and cable strain relief for sheet metal enclosure |
Process | FDM |
Unit price | $7.92 / $4.72 / $2.80 |
Industry | Industrial Automation |
HP PA 12
Customer | US Hammer |
Description | A part for gasoline engine powered jackhammers |
Process | MJF |
Unit price | $22.18 |
Industry | Construction |
Markforged Onyx - Black
Customer | Autocom Manufacturing |
Purpose | A production part for 3D printed lathe gantry gripper fingers |
Process | FDM |
Unit price | $48.![]() |
Industry | Automotive |
PC Stratasys - white
Customer | Terumo medical corporation |
Purpose | Prototyping parts used for a disposable electrical device |
Process | FDM |
Unit price | $55.38 / $32.96 |
Industry | Medical |
Formlabs Clear Resin
Customer | Aversan Inc |
Purpose | A prototyping part of an injection molded component for an automated door mechanism |
Process | SLA |
Unit price | $29.83 |
Industry | Aerospace |
HP PA 12 - Dyed Black
Customer | True North Design |
Purpose | Structural and vacuum EOAT components |
Process | SLS / MJF |
Unit price | $69.![]() |
Industry | Automotive |
Prototyping PLA
Customer | Allision Conner |
Purpose | End caps and cable strain relief for sheet metal enclosure |
Process | FDM |
Unit price | $7.92 / $4.72 / $2.80 |
Industry | Industrial Automation |
HP PA 12
Customer | US Hammer |
Description | A part for gasoline engine powered jackhammers |
Process | MJF |
Unit price | $22.18 |
Industry | Construction |
Markforged Onyx - Black
Customer | Autocom Manufacturing |
Purpose | A production part for 3D printed lathe gantry gripper fingers |
Process | FDM |
Unit price | $48.![]() |
Industry | Automotive |
PC Stratasys - white
Customer | Terumo medical corporation |
Purpose | Prototyping parts used for a disposable electrical device |
Process | FDM |
Unit price | $55.38 / $32.96 |
Industry | Medical |
Formlabs Clear Resin
Customer | Aversan Inc |
Purpose | A prototyping part of an injection molded component for an automated door mechanism |
Process | SLA |
Unit price | $29.83 |
Industry | Aerospace |
HP PA 12 - Dyed Black
Customer | True North Design |
Purpose | Structural and vacuum EOAT components |
Process | SLS / MJF |
Unit price | $69.![]() |
Industry | Automotive |
Prototyping PLA
Customer | Allision Conner |
Purpose | End caps and cable strain relief for sheet metal enclosure |
Process | FDM |
Unit price | $7.92 / $4.72 / $2.80 |
Industry | Industrial Automation |
HP PA 12
Customer | US Hammer |
Description | A part for gasoline engine powered jackhammers |
Process | MJF |
Unit price | $22.18 |
Industry | Construction |
Markforged Onyx - Black
Customer | Autocom Manufacturing |
Purpose | A production part for 3D printed lathe gantry gripper fingers |
Process | FDM |
Unit price | $48.![]() |
Industry | Automotive |
PC Stratasys - white
Customer | Terumo medical corporation |
Purpose | Prototyping parts used for a disposable electrical device |
Process | FDM |
Unit price | $55.38 / $32.96 |
Industry | Medical |
Formlabs Clear Resin
Customer | Aversan Inc |
Purpose | A prototyping part of an injection molded component for an automated door mechanism |
Process | SLA |
Unit price | $29.83 |
Industry | Aerospace |
HP PA 12 - Dyed Black
Customer | True North Design |
Purpose | Structural and vacuum EOAT components |
Process | SLS / MJF |
Unit price | $69.![]() |
Industry | Automotive |
Prototyping PLA
Customer | Allision Conner |
Purpose | End caps and cable strain relief for sheet metal enclosure |
Process | FDM |
Unit price | $7.92 / $4.72 / $2.80 |
Industry | Industrial Automation |
HP PA 12
Customer | US Hammer |
Description | A part for gasoline engine powered jackhammers |
Process | MJF |
Unit price | $22.18 |
Industry | Construction |
Markforged Onyx - Black
Customer | Autocom Manufacturing |
Purpose | A production part for 3D printed lathe gantry gripper fingers |
Process | FDM |
Unit price | $48.![]() |
Industry | Automotive |
PC Stratasys - white
Customer | Terumo medical corporation |
Purpose | Prototyping parts used for a disposable electrical device |
Process | FDM |
Unit price | $55.38 / $32.96 |
Industry | Medical |
Formlabs Clear Resin
Customer | Aversan Inc |
Purpose | A prototyping part of an injection molded component for an automated door mechanism |
Process | SLA |
Unit price | $29.83 |
Industry | Aerospace |
HP PA 12 - Dyed Black
Customer | True North Design |
Purpose | Structural and vacuum EOAT components |
Process | SLS / MJF |
Unit price | $69.![]() |
Industry | Automotive |
Prototyping PLA
Customer | Allision Conner |
Purpose | End caps and cable strain relief for sheet metal enclosure |
Process | FDM |
Unit price | $7.92 / $4.72 / $2.80 |
Industry | Industrial Automation |
HP PA 12
Customer | US Hammer |
Description | A part for gasoline engine powered jackhammers |
Process | MJF |
Unit price | $22.18 |
Industry | Construction |
Markforged Onyx - Black
Customer | Autocom Manufacturing |
Purpose | A production part for 3D printed lathe gantry gripper fingers |
Process | FDM |
Unit price | $48.![]() |
Industry | Automotive |
PC Stratasys - white
Customer | Terumo medical corporation |
Purpose | Prototyping parts used for a disposable electrical device |
Process | FDM |
Unit price | $55.38 / $32.96 |
Industry | Medical |
Formlabs Clear Resin
Customer | Aversan Inc |
Purpose | A prototyping part of an injection molded component for an automated door mechanism |
Process | SLA |
Unit price | $29.83 |
Industry | Aerospace |
HP PA 12 - Dyed Black
Customer | True North Design |
Purpose | Structural and vacuum EOAT components |
Process | SLS / MJF |
Unit price | $69.![]() |
Industry | Automotive |
Prototyping PLA
Customer | Allision Conner |
Purpose | End caps and cable strain relief for sheet metal enclosure |
Process | FDM |
Unit price | $7.92 / $4.72 / $2.80 |
Industry | Industrial Automation |
HP PA 12
Customer | US Hammer |
Description | A part for gasoline engine powered jackhammers |
Process | MJF |
Unit price | $22.18 |
Industry | Construction |
Markforged Onyx - Black
Customer | Autocom Manufacturing |
Purpose | A production part for 3D printed lathe gantry gripper fingers |
Process | FDM |
Unit price | $48.![]() |
Industry | Automotive |
PC Stratasys - white
Customer | Terumo medical corporation |
Purpose | Prototyping parts used for a disposable electrical device |
Process | FDM |
Unit price | $55.38 / $32.96 |
Industry | Medical |
Formlabs Clear Resin
Customer | Aversan Inc |
Purpose | A prototyping part of an injection molded component for an automated door mechanism |
Process | SLA |
Unit price | $29.83 |
Industry | Aerospace |
HP PA 12 - Dyed Black
Customer | True North Design |
Purpose | Structural and vacuum EOAT components |
Process | SLS / MJF |
Unit price | $69.![]() |
Industry | Automotive |
Prototyping PLA
Customer | Allision Conner |
Purpose | End caps and cable strain relief for sheet metal enclosure |
Process | FDM |
Unit price | $7.92 / $4.72 / $2.80 |
Industry | Industrial Automation |
HP PA 12
Customer | US Hammer |
Description | A part for gasoline engine powered jackhammers |
Process | MJF |
Unit price | $22.18 |
Industry | Construction |
Markforged Onyx - Black
Customer | Autocom Manufacturing |
Purpose | A production part for 3D printed lathe gantry gripper fingers |
Process | FDM |
Unit price | $48.![]() |
Industry | Automotive |
PC Stratasys - white
Customer | Terumo medical corporation |
Purpose | Prototyping parts used for a disposable electrical device |
Process | FDM |
Unit price | $55.38 / $32.96 |
Industry | Medical |
Formlabs Clear Resin
Customer | Aversan Inc |
Purpose | A prototyping part of an injection molded component for an automated door mechanism |
Process | SLA |
Unit price | $29.83 |
Industry | Aerospace |
HP PA 12 - Dyed Black
Customer | True North Design |
Purpose | Structural and vacuum EOAT components |
Process | SLS / MJF |
Unit price | $69.![]() |
Industry | Automotive |
Prototyping PLA
Customer | Allision Conner |
Purpose | End caps and cable strain relief for sheet metal enclosure |
Process | FDM |
Unit price | $7.92 / $4.72 / $2.80 |
Industry | Industrial Automation |
HP PA 12
Customer | US Hammer |
Description | A part for gasoline engine powered jackhammers |
Process | MJF |
Unit price | $22.18 |
Industry | Construction |
Markforged Onyx - Black
Customer | Autocom Manufacturing |
Purpose | A production part for 3D printed lathe gantry gripper fingers |
Process | FDM |
Unit price | $48.![]() |
Industry | Automotive |
PC Stratasys - white
Customer | Terumo medical corporation |
Purpose | Prototyping parts used for a disposable electrical device |
Process | FDM |
Unit price | $55.38 / $32.96 |
Industry | Medical |
Formlabs Clear Resin
Customer | Aversan Inc |
Purpose | A prototyping part of an injection molded component for an automated door mechanism |
Process | SLA |
Unit price | $29.83 |
Industry | Aerospace |
HP PA 12 - Dyed Black
Customer | True North Design |
Purpose | Structural and vacuum EOAT components |
Process | SLS / MJF |
Unit price | $69.![]() |
Industry | Automotive |
Prototyping PLA
Customer | Allision Conner |
Purpose | End caps and cable strain relief for sheet metal enclosure |
Process | FDM |
Unit price | $7.92 / $4.72 / $2.80 |
Industry | Industrial Automation |
HP PA 12
Customer | US Hammer |
Description | A part for gasoline engine powered jackhammers |
Process | MJF |
Unit price | $22.18 |
Industry | Construction |
Markforged Onyx - Black
Customer | Autocom Manufacturing |
Purpose | A production part for 3D printed lathe gantry gripper fingers |
Process | FDM |
Unit price | $48.![]() |
Industry | Automotive |
PC Stratasys - white
Customer | Terumo medical corporation |
Purpose | Prototyping parts used for a disposable electrical device |
Process | FDM |
Unit price | $55.38 / $32.96 |
Industry | Medical |
Formlabs Clear Resin
Customer | Aversan Inc |
Purpose | A prototyping part of an injection molded component for an automated door mechanism |
Process | SLA |
Unit price | $29.83 |
Industry | Aerospace |
Instant, online 3D printing quotes
-
Upload a CAD to start (STEP, STP, IGES, IGS, SLDPRT, 3DM, SAT, STL, OBJ or X_T)
-
Price updates in real-time as you change materials, lead time, etc.
.
-
No hidden costs. Our instant quotes are not just indications, but the actual price, and include shipping and customs up front.
Learn about how our quoting algorithm works
Our ordering process
Receive instant quote
Upload your CAD to our online quoting platform
Confirm specs
Configure your part specifications and select a lead time that suits your schedule
Production
We select the best manufacturer for your order, and production begins immediately
Quality control
We take full responsibility for making sure your parts are manufactured according to our standards
Delivery
Our 3D printing service has been rated 4.9/5
Over 322 customers are satisfied with our 3D printing service.
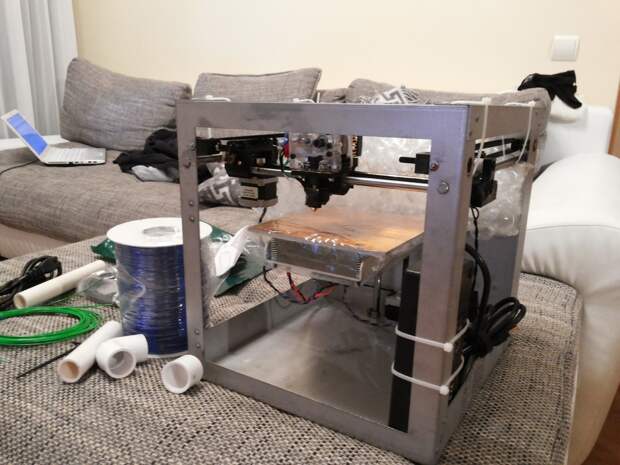
“Arrived quickly with updates throughout the process, exactly as requested.”
“I was pleasantly surprised that whole process was so good! Definitely use it again!”
“Just as expected. Fast delivery. No issues.”
“Excellent print quality and fast service.”
“Parts look great and are 100% functional.”
“I didn't know TPU was so flexible :) The parts were too loose on my Win 2. I'm now going to order parts with different material :)”
“I had an excellent experience with this provider. He was extremely responsive and did a great job on the parts.”
“Great part, works and fits exactly as i needed”
“Fast service, Excellent Print. What more could you want?”
“Great prints, great communication. Will use this seller again.”
“Very helpful and patient, quality focused”
“Always a wonderful experience and perfect print. Thank you!”
“I ordered a print at the cheapest level and the quality is much better than I anticipated. These guys examined my drawings in no time, got the print started, snapped images post-print, and got it out the door in the same day. A+ service.”
“Fast, easy to work with and great final product!”
“Great job and shipped quickly. Item was received before quoted delivery date. ”
“Everything was great, but i should have had some of the pieces printed solid.”
“Great prints and excellent quality. No issues with leftover powder stuck inside the prints. Well worth the money spent!”
“This was my first 3D printing order ever. I am 100% happy with the quality, price, and I liked the way I was notified at every step. Posting photos of the printed parts took customer service to the next level!”
“Fast service good prints will do business with again”
“looks like the photos, was a tough print and will serve its purpose well”
“Prompt response, very good quality, delivery as promised - highly recommended! ”
“Print quality was great. Ordered 36 pieces of the same part and they all look identical and flawless. ”
“Extremely fast turnaround. Print turned out great. Always a pleasure.”
“Print as expected. Communication and flexibility was excellent.”
“Great work, very clean sidewalls on these parts!”
Show more reviews
Show less reviews
Teams build better parts
Create your Hubs team and start collaborating
Read more
The Hubs Standard - consistent quality, every time
Hubs takes the stress out of manufacturing by guaranteeing the quality and consistency of every part. Each order is dimensionally and visually inspected to make sure it meets the Hubs Standard.
3D printing materials
We can generate instant 3D printing quotes for 25+ plastics. For metal 3D-printed parts, you can request a quote from our parent company, Protolabs.
Available materials
SLS
PA 12 Glass filled PA 12
Desktop FDM
Prototyping PETG Prototyping ASA Prototyping TPU Prototyping ABS Prototyping PLA
Desktop SLA
Formlabs Standard Resin Formlabs Clear Resin Formlabs Tough Resin 2000 Formlabs Rigid Resin 4000 Formlabs Grey Pro Resin Formlabs Flexible Resin 80A Formlabs High Temp Resin Formlabs Durable Resin
MJF
HP PA 12 Glass filled HP PA 12
Industrial FDM
Markforged Onyx ABSplus Stratasys ULTEM 9085 Stratasys Stratasys ASA ABS M30 Stratasys ULTEM 1010 Stratasys
Industrial SLA
Accura 25 (PP-like) Accura ClearVue Accura Xtreme White 200 (ABS-like)
3D printing locations near Binghamton, NY
Union, NY Binghamton, NY Ithaca, NY
Scranton, PA Elmira, NY Hazleton, PA
Syracuse, NY Bloomsburg, PA Clay, NY
Williamsport, PA
The 3D Printing Handbook
No one understands 3D printing like us - our founders literally wrote the book. Click here to download the sample chapters.
Buy the book from Amazon
FAQ's
How much does your 3D printing service cost?
The cost of your 3D printed parts depends on factors such as part volume, part complexity, choice of material, which 3D printing technology is used, and if any post processing is required. For more details on these cost factors, see our article on the cost of 3d printing. To check the cost of your 3D printed part, simply upload a CAD (.STL) file and select your material and 3D printing technology to receive a quote within seconds.
How do you guarantee the quality of my prints?
Your parts are made by experienced 3D printing shops within our network. All facilities are regularly audited to ensure they consistently meet the Hubs quality standard. We include a standardized inspection report with every order and offer a First Article Inspection service on orders of 100+ units.
We have partners in our network with the following certifications, available on request: ISO9001, ISO13485 and AS9100.
Follow this link to read more about our quality assurance measures.
How do I select the right 3D printing process for my prints?
You can select the right 3D printing process by examining which materials suit your need and what your use case is.
By material: if you already know which material you would like to use, selecting a 3D printing process is relatively easy, as many materials are technology specific.
By use case: once you know whether you need a functional or visual part, choosing a process is easy.
For more help, read our guide to selecting the right 3D printing process. Find out more about Fused Deposition Modeling (FDM), Selective Laser Sintering (SLS), Multi Jet Fusion (MJF) and Stereolithography (SLA).
How can I reduce the cost of my 3D prints?
In order to reduce the cost of your 3D prints you need to understand the impact certain factors have on cost. The main cost influencing factors are the material type, individual part volume, printing technology and post-processing requirements.
Once these have been decided, an easy way to further cut costs is to reduce the amount of material used. This can be done by decreasing the size of your model, hollowing it out, and eliminating the need for support structures.
To learn more, read our full guide on how to reduce the cost of 3D printing.
Where can I learn more about 3D printing?
Our knowledge base is full of in-depth design guidelines, explanations on process and surface finishes, and information on how to create and use CAD files. Our 3D printing content has been written by an expert team of engineers and technicians over the years.
See our complete engineering guide to 3D printing for a full breakdown of the different 3D printing technologies and materials. If you want even more 3D printing, then check out our acclaimed 3D printing handbook here.
We have an extensive range of online resources developed to help engineers improve their capabilities.
Introductory guides
Design guides
Material guides
Applications
CAD & file preparation
Post processing & finishing
Our other manufacturing capabilities
CNC machining
CNC machining
Milling (3-, 4- & full 5-axis), turning and post-processing
-
50+ metals and plastics & 10 surface finishes
-
Tolerances down to ±.0008” (0.020 mm)
-
Lead times from 5 business days
See our CNC machining services
Put your 3D printed parts into production today
Get an instant 3D printing quote
Binghamton - NoE - 3D Printing
By Todd R. McAdam
Kaiming Ye has a term for the process he uses to build a team out of a bunch of multi-disciplined researchers with different goals, resources and from different New York campuses.
He calls it “lunch.”
The appetizer is a $150,000 grant from the SUNY Health Network of Excellence, enough to buy supplies for a couple months at the eight laboratories from five universities involved in the work.
The main course is a hoped for $24 million grant from the National Science Foundation to develop a process to use 3-D printing technology to build on-demand implantable tissues and organs for treating otherwise incurable diseases – such as diabetes.
And for dessert, there's the promise in 10 years of developing the technology far enough to build the most complex of human organs – such as the eye.
“Those grants are incredibly competitive,” said Bahgat Sammakia, vice president for research at Binghamton University. “The win rate is typically 1 to 2 percent. The best thing you can do is to form a team that is the best in the world.”
The team in this case came from Binghamton University, Neural Stem Cell Institute, SUNY-Albany, Cornell University, Rennselaer Polytechnic Institute, SUNY's College of Nanoscale Science and Engineering, and the University of Texas, Arlington.
“I don't have special skills” in building teams, Ye said. “Bring them together, talk together. Share the vision.”
Ye’s vision, shared over a lunch or two, is pretty compelling.
Islet cells, produced in the pancreas, don’t survive beyond three months if cultures in a petri dish because they don’t mature properly. That’s because cells don’t grow effectively in isolation. They grow, develop and maintain their function in biochemical context with the cells around them.
Ye’s plan uses a patient’s own cells. It would strip them down to a framework, like a stem cell. Then the 3-D process would add new material, piece by piece, until it produces a functioning specialized cell. They’re crafted from a patient’s own cells, so there’s no chance of rejection.
Islet cells, among the simplest organs in the human body, are the first project. More complex organs – the liver, kidneys, lungs, heart, the eyes and even the brain – can eventually be built using a similar matrix.
While Ye, a bio-engineer and former National Science Foundation program director, has a technology to re-program cells, he need the skills of leading-edge biomaterials experts, stem cell biologists, other biomedical engineers and biomechanical specialists.
“You have to open your mind first. We've all collaborated in the past,” Ye said. “If the team members lose the faith, then the collaboration goes nowhere. Our team members are very collegial and collaborative. They are first-class scientists and leaders in the field.”
Ye wasn't surprised when the initial funding requests were twice the $150,000 pot he had to work with. Negotiating effectively is part of the team process – and keeping the goal in mind is essential. In this case, better lives, saved lives, and a $24 million grant to make that happen.
“We're very clear what the end product is,” Ye said.
The willingness to hang together in those early days when funding is relatively light is critical to future success, Sammakia said. “They would have won a grant together and published some data together.”
Grants like the $150,000 SUNY Networks of Excellence grant. “Without that, the chances of winning (larger grants) are greatly diminished,” Sammakia said. “Faculty members that are interested in research want to be with the best possible team. They will sacrifice a lot to be a part of a team like that.”
“The money is the path; science is the goal,” Ye said. “If you put the money on the table, they'll work together.”
Tags Tags: Networks of Excellence , Binghamton University , Health and Medicine
Please enable JavaScript to view the comments powered by Disqus. comments powered by Disqus
Cool the CPU in the data center - laser 3D printing will help / Sudo Null IT News The thermally conductive material is applied directly to the surface of the chip using 3D printing. According to experts, their solution can lower the operating temperature of processors in data centers by 10°C.
Let's talk about the technology and talk about other experimental methods of CPU cooling.
/ photo artistic bokeh CC BY-SA
How to print "metal thermal paste"
The developers of the technology applied a thin layer of a metal alloy with high thermal conductivity to the processor chip and, using a laser, "printed" channels for the coolant in it. For this, the method of selective laser sintering was used.
A layer of metal powder is evenly distributed on the silicon surface. Then the laser is turned on and the beam directed by the moving mirrors fuses the particles together according to the generated 3D model. The procedure is repeated many times - at each iteration, different sections of the final product are formed. The laser sintering itself takes place in less than a second.
The alloy that is applied to the chip consists of titanium, tin and silver. The last two are needed to reduce the melting point of the material. Thus, the metal remains in the liquid state longer, which helps to avoid deformation of the layer due to sudden solidification.
Selective laser sintering made it possible to form a metal layer a thousand times thinner than the diameter of a human hair. This allows the coolant to draw excess heat directly from the chip and eliminates the need for thermal paste.
What this technology can do
The specialists managed to obtain an alloy with a thermal conductivity of 39 W/(m•K), which is seven times better than other materials for thermal interfaces - thermal pastes or polymer compounds. This made it possible to reduce the temperature of the chip by 10°C compared to other cooling systems.
The new technology is designed to solve two problems: reduce energy costs in data centers and extend the life of processors (because they will overheat less). According to the developers, the invention will reduce the energy consumption of the world's data centers by 5% and will allow the IT industry to save up to $438 million annually.
So far, the technology has been tested only in laboratory conditions and it is not known how it will work in real data centers. However, in the near future, the researchers plan to patent their technology and conduct the necessary tests.
Who else is experimenting with chip cooling
Not only Binghamton University is working on chip cooling technologies. Their colleagues from the University of California for the first time synthesized ultrapure boron arsenide crystals with high thermal conductivity. The value obtained is close to 1300 W/(m•K), while diamond (which is considered one of the champions in thermal conductivity) has a value of 1000 W/(m•K).
The new technology will make it possible to create efficient heat removal systems in electronics and photonics. However, this requires solving a number of problems. Boron arsenide is difficult to obtain on an industrial scale - defects often occur during the synthesis of crystals, and toxic arsenic compounds are used in the production of the material.
Researchers at the University of California are also working on a solution to the problem of heat dissipation from processors. They suggested changing the structure of the chip itself. The idea is to create a silicon crystal structure in which phonons (quasiparticles that carry out heat transfer) will transfer heat at maximum speed.
Their technology is called "hole silicon". Tiny holes with a diameter of 20 nm are drilled into the board, which accelerate heat dissipation. In the case of an optimal arrangement of holes, the thermal conductivity of the silicon wafer increases by 30%.
This method is still far from being implemented - only the model is ready. The next step is to explore the potential of the technology and the possibility of application in real systems.
/ stock photo PD
What's next
The practical implementation of new heat removal technologies is still far away. All of them are either at the concept stage or at the prototyping stage. Although they have good potential, there is no need to talk about their widespread implementation in the data center market yet.
For this reason, data centers are now experimenting with other cooling methods. One of the latest trends is liquid cooling . According to a survey by the Uptime Institute, 14% of data centers around the world have already adopted the technology. Experts expect that this figure will increase in the future due to the increase in the density of equipment in the data center. Since with a large number of nearby servers, air cooling is difficult.
Another trend is AI systems for controlling the air conditioning units of the data center. According to research organizations, about 15-25% of data centers already use such machine learning algorithms. And it is expected that in the future, the popularity of intelligent technologies in the data center will only increase.
P.S. From our corporate blog:
- Unboxing: Cisco UCS B480 M5 Blade Server
- Servers for SAP: main platforms
- Unboxing all-flash NetApp AFF A300 Storage Specifications
P.S. We have a Telegram channel where we write about virtualization and IaaS technologies:
- What's in VMware: three new items
- NetApp A to Z: Vendor Technology Overview
- NetApp: we continue to talk about technologies
Cool down the CPU in the data center - laser 3D printing will help
Binghamton University (New York) has developed a new technology for cooling processors, which will eliminate thermal paste. The thermally conductive material is applied directly to the surface of the chip using 3D printing. According to experts, their solution can lower the operating temperature of processors in data centers by 10°C.
How to print "metal thermal paste"
The developers of the technology applied a thin layer of a metal alloy with high thermal conductivity to the processor chip and, using a laser, "printed" channels for the coolant in it. For this, the method of selective laser sintering was used.
A layer of metal powder is evenly distributed on the silicon surface. Then the laser is turned on and the beam directed by the moving mirrors fuses the particles together according to the generated 3D model. The procedure is repeated many times - at each iteration, different sections of the final product are formed. The laser sintering itself takes place in less than a second.
The alloy that is applied to the chip consists of titanium, tin and silver. The last two are needed to reduce the melting point of the material. Thus, the metal remains in the liquid state longer, which helps to avoid deformation of the layer due to sudden solidification.
Selective laser sintering made it possible to form a metal layer a thousand times thinner than the diameter of a human hair. This allows the coolant to draw excess heat directly from the chip and eliminates the need for thermal paste.
What this technology can do
Specialists have been able to obtain an alloy with a thermal conductivity of 39 W/(m•K), which is seven times better than other thermal interface materials such as thermal pastes or polymer compounds. This made it possible to reduce the temperature of the chip by 10°C compared to other cooling systems.
The new technology is designed to solve two problems: reduce energy costs in data centers and extend the life of processors (because they will overheat less). According to the developers, the invention will reduce the energy consumption of the world's data centers by 5% and allow the IT industry to save up to $438 million annually.
So far, the technology has been tested only in laboratory conditions and it is not known how it will work in real data centers. However, in the near future, the researchers plan to patent their technology and conduct the necessary tests.
Who else is experimenting with chip cooling
Not only Binghamton University is working on chip cooling technologies. Their colleagues from the University of California for the first time synthesized ultrapure boron arsenide crystals with high thermal conductivity. The resulting value approached 1300 W/(m•K), while diamond (which is considered one of the champions in thermal conductivity) has a value of 1000 W/(m•K).
New technology will allow creating efficient heat removal systems in electronics and photonics. However, this requires solving a number of problems. Boron arsenide is difficult to obtain on an industrial scale - defects often occur during the synthesis of crystals, and toxic arsenic compounds are used in the production of the material.
Researchers at the University of California are also working on a solution to the problem of heat dissipation from processors. They suggested changing the structure of the chip itself. The idea is to create a silicon crystal structure in which phonons (quasiparticles that carry out heat transfer) will transfer heat at maximum speed.
Their technology is called "hole silicon". Tiny holes with a diameter of 20 nm are drilled into the board, which accelerate heat dissipation. In the case of an optimal arrangement of holes, the thermal conductivity of the silicon wafer increases by 30%.
This method is still far from being implemented - only the model is ready. The next step is to explore the potential of the technology and the possibility of application in real systems.
What's next
The practical implementation of new heat removal technologies is still far away. All of them are either at the concept stage or at the prototyping stage. Although they have good potential, there is no need to talk about their widespread implementation in the data center market yet.