3D printed ultrasound cast
3D-printed ultrasound cast could save us costly surgeries
3D printing the cast itself is nothing new -- there are plenty of designers experimenting with different geometric patterns and last year we featured Jake Evill's beautifully designed Cortex cast that behaves like a brace and is tailored to the individual from a 3D scan. It's washable, breathable, discreet and can be made denser in the areas round the fracture that need more support.
Karasahin's version looks very similar -- albeit with a different geometric pattern -- clinging close to the subject's skin and wrapping round their thumb. But there are a few key differences. "We share a more contemporary style but this style is also mainstream in the design world," notes Karasahin. "His form/pattern inspiration is geometric-based and also the geometric/algorithmic logic is related to the place of the injury.
In my case the form/pattern inspiration is different -- I was inspired by the pattern of spongy bone geometry because of its semiotic relation with a medical cast, and the logic behind my algorithm aims for an equally distributed stronger structural integrity of the cast. "
Rather than snapping closed the Osteoid, made up of two pieces, also features a secondary, secure locking mechanism to ensure it doesn't open when in use. Of course the most obvious difference, is the proposal for an ultrasound port, where devices similar to Exogen's can be introduced. "I read the clinical studies about this tech, and some of them were almost 20 years old," says Karasahin. "After talking with an orthopaedist MD I learnt about the current application problems which prevent this tech from being widely used."
The most obvious of these, is how you reach the skin to place the ultrasound probes if it's wrapped up in a cast. Typically a hole is cut in the cast to allow a transducer to touch the skin where the fracture is. Karasahin explains that the site of the skin will also swell, causing the patient discomfort. With all the holes in the Osteoid, there's no chance of that.
Clinical studies have shown that the ultrasound waves promote bone healing by stimulating the production of growth factors and proteins that increase removal of old bone, and increase the production of new bone.
The designer has already been contacted by private and government-owned clinics in the US, looking to launch trials (the Osteoid is still at the concept stages right now). "It is the medical industry that is the most excited -- it is all positive," said Karasahin. "I also have received so many emails from people who are willing to put one on instantly."
The design has great promise, but there's a few things to remember. The Osteoid is being touted with a promise that, once hooked up to ultrasound for 20 minutes a day, it will help reduce the time it takes for the injury to heal by 38 percent. The heal rate for non-union fractures that are totally cut in two increases by 80 percent. Those figures are based on clinical trials already carried out separately.
Lightweight 3D printed cast with ultrasound therapy
Anyone who has ever worn a cast knows well how itchy, smelly, and unpleasant it can be.
April 29, 2014
Manufacturing Group
3D/Additive/Alternative Contract Manufacturing Design Devices/Implants Regulations Materials Business
Casts are heavy and have no ventilation, so skin beneath gets no air or sun while the unused muscles weaken and reduce in size. Deniz Karasahin, an industrial designer, has proposed a new approach that uses a 3D printer to create custom breathable, washable casts.
Click here to learn more on MedGadget.
Cochlear Nucleus 5 and Nucleus 6 systems are now the world's most waterproof cochlear implant systems.
April 29, 2014
Manufacturing Group
Contract Manufacturing Design Devices/Implants Regulations Business
Centennial, Colorado – Cochlear Ltd. , the global leader in implantable hearing solutions, announced that the US Food and Drug Administration (FDA) has approved the Aqua+ accessory, the only waterproof behind-the-ear solution for cochlear implant recipients on the market today. The Aqua+ is a form-fitting, easy-to-use, versatile accessory that allows Cochlear Nucleus 5 and Nucleus 6 Implant recipients(1) to swim underwater for up to two hours.
The new Aqua+ gives recipients the ability to swim while wearing their sound processor behind the ear. Its flexible, watertight sleeve simply fits over their sound processor behind the ear, so they don't have to find other places to secure their sound processor, like a swimsuit. A specially-designed waterproof coil then connects to the sound processor within the sleeve.
"With the approval of the Aqua+ accessory, recipients can have the confidence that they have the world's most waterproof cochlear implant system on the market, while benefitting from the sleek, form-fitting, behind-the-ear design that truly makes it one-of-a-kind," said Chris Smith, president of Cochlear Americas. "The Aqua+ will undeniably change the way our cochlear implant recipients interact with water going forward by allowing them to swim in and under water while wearing their sound processor."
While the Nucleus 5 and Nucleus 6 Sound Processors already have a high water resistance rating, the Aqua+ provides added confidence with its IP68 water resistance rating.(2) It is safe to use in all types of water including chlorinated pools, fresh water lakes and rivers, saltwater oceans and pools, and soapy water. Additionally, the Aqua+ is a reusable solution allowing recipients to use the form-fitting sleeve numerous times without having to replace it.(3)
The Aqua+ Kit, which consists of all the necessary parts that recipients will need, can be ordered from the Cochlear Americas store beginning May 2, 2014. All Nucleus 5 and Nucleus 6 Cochlear Implant recipients in the United States and Canada are eligible to order the Aqua+.
References
[ 1 ] The Aqua+ can be used with a Nucleus 5 or Nucleus 6 Sound Processor with rechargeable batteries only. Not compatible with the acoustic component.
[ 2 ] The Nucleus 5 and Nucleus 6 Sound Processor with the Aqua+ is water resistant to level IP68 of the International Standard IEC60529. This water protection rating means that the sound processor with the Aqua+ can be continuously submerged under water to a depth of 3 meters for up to 2 hours.
[ 3 ] Testing shows Aqua+ can be re-used up to 50 times, but this may vary depending on your particular use of it.
Source: Cochlear
Attendees will see four US premieres – 38 machines live in operation and learn about additive manufacturing in finished-part quality.
April 29, 2014
Manufacturing Group
Machining Centers Business Manufacturing
Chicago, IL. Manufacturers around the country are invited to join DMG MORI’s Headquarters for a sneak preview of innovative DMG MORI machining centers in the new common design as well as the latest in software, automation, additive manufacturing and more.
DMG MORI’s Innovation Days 2014 from May 6-9, 2014, will feature machining demonstrations, seminars, and one-on-one application consultations aimed to help manufacturers remain productive and competitive. DMG MORI will be showcasing 38 machine demos, including four innovative U.S. premieres, the new common design and the new control platform CELOS – from the idea to the finished product.
CELOS offers a uniform interface for all new high-tech machines from DMG MORI. CELOS apps provide the user with integrated and digitized management, documentation and visualization of order, process and machine data. Visitors to the event can also experience the New Design at Innovation Days: new long life surfaces provide a higher scratch resistance and better protection against damages.
Among the U.S. premieres will be the new and improved universal turning machines NLX 3000Y/1250 and NLX 4000BY/1500, as well as the 4th generation 5-axis machining center DMU 80 P duoBLOCK and the recently released compact CTX 450 ecoline.
One highlight will certainly be the hybrid machine demonstrations, combining laser metal deposition and turn-mill processes in one machine. On show will be the NT 4300SZ turn-mill center from Iga, Japan. The unique combination of laser metal deposition via powder nozzle and subtractive machining accelerates the manufacturing process. Complete workpieces can be generated up to 20-times faster as compared to powder bed technology. Additionally, unique machining operations are possible – for instance the realization of geometric features with negative angles. Additionally, presentations on the many facets of today’s advanced manufacturing will include gear-milling technology. Special software and newly developed processes have transformed the turn-mill centers of the NT and NTX series into perfect gear milling machines for small and medium-sized batches. The machines can accomplish virtually everything that special gear cutting machines can do. They are also more flexible, making cost-effective capacity planning far easier.
U.S. manufacturing at its best
Guests to DMG MORI Innovation Days can also inform themselves about the company’s Digital Technology Laboratory (DTL) and Manufacturing Factory, which make up the company’s Davis, CA campus. DTL provides much of DMG MORI’s engineering analysis capability and R&D to support machine tool design and manufacturing operations around the world. The building also houses a showroom of machine tools and related products. The Manufacturing Factory, opened in July 2012, covers 200,000ft2 of manufacturing space and an expansive showroom. Here, DMG MORI manufactures and assembles the NHX series, as well as the DuraVertical 5100. In 2014, production of the DMU 50 and CTX 450 ecoline will start. Since U.S. manufacturing started to rebound in 2013, DMG MORI USA has seen increased interest in its high-end equipment, which can now be backed up by the viable resources available at the Davis, CA facilities.
Source: DMG MORI
Alliqua to launches Biovance human amniotic membrane allograft product licensed from Celgene.
April 29, 2014
Manufacturing Group
Contract Manufacturing Devices/Implants Materials Business
Langhorne, Pa., - Alliqua Inc. launched its Biovance human amniotic membrane allograft product, during the Spring 2014 Symposium on Advanced Wound Care held at the Gaylord Palms Hotel and Convention Center in Orlando, Fla.
Biovance was originally developed by, and is currently being manufactured through a supply agreement with, Celgene Cellular Therapeutics (CCT), a subsidiary of Celgene Corp. , to assist wound care specialists, physicians and nurses, as well as vascular, plastic and general surgeons, in the treatment of a wide variety of complex, acute, chronic, recalcitrant, full, and partial thickness wound types.
With the right to develop and market Biovance, Alliqua has entered into one of the fastest-growing areas of wound care, which involves regenerative medicine. Alliqua will commence sales of Biovance immediately following the Symposium via its team of direct sales representatives.
Perry Karsen, CEO of Celgene Cellular Therapeutics, remarked, "We have great confidence in Alliqua and its management team in bringing Biovance to patients throughout the United States."
On April 14, 2014, Celgene invested $5,000,000 in Alliqua as part of the company's previously announced private placement that resulted in gross proceeds to the company of $15 million.
David Johnson, CEO of Alliqua, said, "The SAWC meeting is the ideal venue at which to launch our Biovance product and to convey its natural benefits to the wound care community. The launch of Biovance marks a major milestone for Alliqua, representing a key application of regenerative medicine for advanced wound care and an important addition to Alliqua's wound care portfolio. We are confident that wound care specialists and their patients will be impressed with the value this human amniotic membrane allograft brings to their wound care arsenal."
Source: Alliqua Inc.
Becton Dickinson, C.R. Bard, Covidien lead US vascular access market to more than $5 billion by 2020.
April 28, 2014
Manufacturing Group
Design Devices/Implants Regulations Business
Vancouver, BC – According to a new report by iData Research, the leading global authority in medical device market research, the U. S. vascular access market was valued at $3.7 billion in 2013 and is expected to grow to more than $5 billion by 2020. This growth is fueled by government safety and reimbursement policies created to reduce infection and injury rates. As a result, hospitals are taking steps to reduce injuries by increasing the use of safety products such as pivoting needles, shield safety products retractable syringes, and catheter securement technologies.
The rise in demand for vascular access devices is proportional to the addressable patient population including oncology, ICU, and diabetic patients. In 2013, approximately 90% of patients who were hospitalized in the U.S. received some sort of vascular access treatment during their stay, including the use of IV catheters and syringes.
One of the strongest segments driving the vascular access market is the catheter securement market, which is expected to experience double digit growth by 2020. This segment includes Ultrasound and Tip-Location technologies, Peripheral Intravenous Catheters, Dialysis Catheters and Central Venous Catheters (CVCs).
"There has been an intensive effort by the U.S. government organizations, hospitals, medical companies and device manufacturers to reduce infections from CVCs" states Dr. Kamran Zamanian, CEO of iData Research. "New product developments such as the ultrasound and tip-location technology will reduce incidences of catheter movement or malposition, reducing the risk of thrombosis and infection."
Leading the market for vascular access market is Becton Dickinson (BD), despite participating in only two market segments, the PIVC and syringe & needle markets. Other major competitors in the U.S. market include C.R. Bard, Covidien, Teleflex Medical, Johnson & Johnson, and Smith & Nephew.
iData's comprehensive report series entitled: Market for Vascular Access Devices and Accessories 2014 includes the latest data, market analyses, and competitor profiles. This market segment includes the implantable port, port needle, central venous catheter, peripherally inserted central catheter, peripheral intravenous catheter, dialysis catheter, ultrasound vascular access device and accessories, catheter securement device, syringe, and needle market.
Source: iData Research
3D laboratory
- home
- 3D laboratory
Modern hearing aids are able to compensate for any hearing loss and meet the needs of the most demanding users. But there is one caveat - all devices have a standard shape and do not take into account the individual features of the structure of the ear canal, which will house the body of the hearing aid or its sound guide (liner). The sound pressure on the eardrum and its frequency response will directly depend on the quality of the individual otoplasty. Even the best hearing aid will not do the job if it is not properly positioned in the ear canal. nine0009
The standard manual technology for the manufacture of otoplasty products (inserts, shells, earplugs) in the modern world has long given way to digital 3D printing.
Our company has been using digital printing since 2018 and already has enough experience in this field. We are constantly improving our technology for the manufacture of individual otoplasty and can provide high quality to our customers.
- Impression taking . The impression procedure is performed by a hearing care professional. An otoblock is installed in the ear canal, which prevents contact of the impression mass with the eardrum. Then a two-component silicone mass is introduced into the canal, which hardens after mixing for 5-10 minutes. The mass fills the cavity of the canal and the entire auricle to create a complete imprint of the outer ear. nine0004
- Impression scan . A special optical scanner creates a 3D impression model for further processing. We use a high-precision scanner that allows you to simultaneously scan both impressions of one patient.
- Create 3D model .
Special software allows you to process the scanned model of the ear impression and give it the desired shape. Thanks to the digital method of calculating the acoustic characteristics and the position of the components of the hearing aids, the most optimal cosmetic effect is achieved for in-canal and deep-canal hearing aids. nine0004
- 3D printing . Finished 3D models of future otoplasty products are sent to a 3D printer for printing. The printer's laser beam cures the biocompatible photopolymer resin in layers. Depending on the technical characteristics of the product, the layer thickness can be from 25 microns (40 layers in 1 millimeter!). Printing time directly depends on the resolution of the product and averages 1.5-2 hours.
- Workpiece wash . The printed blank is sent to an ultrasonic cleaner to remove residual liquid resin.
- Preform Curing .
After washing, the preform must be placed in a photopolymerizer to eliminate the “stickiness” of the outer layer that has been in contact with oxygen and give the material final hardness.
- Finishing . At this stage, the final processing of otoplasty products made of hard materials is carried out - grinding, polishing, varnishing. To make silicone products, a printed hollow mold is filled with silicone, then demolded, sanded and varnished. nine0004
- Mounting . In-the-ear or behind-the-ear receivers are mounted in a printed housing. In individual liners, a sound-conducting tube is installed, in earplugs - acoustic filters. The finished product is sent to the customer.
3D-printed gypsum substitute with ultrasound to speed up fracture healing and save costly operations low intensity for non-invasive treatment of complex fractures and bone defects.
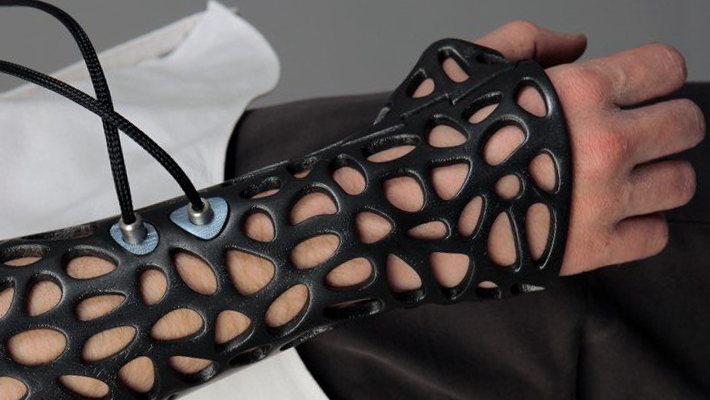
To do this, he developed the concept of a plastic replacement for plaster, which can be produced using a modern 3D printer called Osteoid Medical Cast. At the same time, the development of the Turkish designer not only looks more elegant, but also surpasses ordinary medical gypsum in terms of functionality and allows you to recover faster after fractures using ultrasound.
Rate
FINANCIAL ANALYSIS
Score P&L-, BS-, CF-stars in total for 1.5 months. nine0009
REGISTER!
“Somehow it all started by accident,” Mr. Karasakhin commented on the development of Osteoid in an interview with Wired. – “I was asked to create a short presentation on the development of 3D printing technology at Izmir University of Economics. At that time, I closely followed the development of the industry and wanted to make my small contribution.
The idea with an analogue of medical plaster was the most promising, as it offered several times more advantages compared to modern solutions in this area.” nine0009
3D printing technologies for internal organs for implantation purposes are still in their early stages of development, while the production of medical devices and their components using modern 3D printers has been a common practice over the past years. In 2013, iLab Haiti began using MakerBot 3D printers to produce umbilical clamps. Given the many disadvantages of traditional gypsum, including the massiveness of the structure itself, as well as poor ventilation, which provokes the appearance of extraneous odors and unpleasant itching, and the growing pace of mass use of 3D printers in all areas of modern medicine, such an invention should have seen the light of day even earlier. nine0009
Creating a technological plastic replacement for plaster using 3D printers is not something extraordinary - in the recent past, many designers have experimented with various geometric patterns when creating plastic plaster. Notable among these is Jake Eville's concept called the Cortex Cast, which has much in common with Karasakhin's version, a body-contact design that also grips the thumb. At the same time, there are many key differences. nine0009
“We prefer more modern style, which is the mainstream in the design world,” notes Karasakhin. “Its shape and pattern are inspired by geometric figures, and the use of certain algorithms and figures completely determines the location of the injury. In my case, the shape and pattern are different, as the source of inspiration was the spongy structure of bone tissue and its semiotic connection with medical plaster.
In the case of Osteoid Medical Cast, it was decided to move away from the one-piece design. It consists of two parts and provides for a special protective mechanism that ensures that the structure does not fall apart during operation. Of course, the most notable difference is the ability to combine the Osteoid Medical Cast with a low-intensity pulsed ultrasound stimulator like Exogen, which, through direct contact with the patient's skin through holes in the plastic "cast" construction, will speed up the process of bone healing. nine0009
Clinical studies have shown that low-intensity ultrasound accelerates the healing process of damaged bone tissue by stimulating the production of the necessary proteins.
Resource ArsTechnica reports that the designer has already sent out official requests for cooperation to several private and public clinics in the US, with the help of which Osteoid can be embodied in a commercial product.
Osteoid is touted with the promise of reducing the time it takes to heal an injury by 38% when ultrasound is applied daily. The duration of the session is 20 minutes. The healing rate in case of non-union fractures using a 3D-printed "gypsum" and a low-intensity ultrasound stimulator is increased by 80% compared to the conventional method. nine0009
The Exogen System is indicated for the treatment of nonunion fractures. The long-winded NICE report contains very precise conclusions. NICE does not believe the device is suitable for treating any fractures that fail to heal within a nine-month period.