Large format 3d printing
Large Scale 3D Printers Big Enough to Print Furniture
Home / 3D Printers / Large Scale 3D Printers Big Enough to Print Furniture
Use Cases
Just like all types of 3D printing, XL 3D printing has its own strengths and tradeoffs. Users are constantly finding more applications for these gigantic machines so the XL 3D printing space is getting bigger and bigger. Let’s have a closer look.
Quick jump to:
- Request XL 3D printer quote
- Request XL service quote
When To Consider Large Scale 3D Printing
It takes a large scale 3D printer to print furniture, vehicle parts and architectural components. Obviously, size is the driving factor in choosing to use large-format printing but there’s more to it than that. Here’s a breakdown of some of the less-obvious considerations:
- Unibody Parts – Often, producers are already able to fabricate their large objects through traditional methods of assembly but those objects would perform better if they were produced as one solid piece, something only a large 3D printer can do efficiently.
- Weight Reduction – Large objects are usually made of wood, metal, or injection molded plastics. Printing the same objects in plastic will make them much lighter, especially when factoring that users can easily adjust the density infill of 3D printed objects. Consolidating large assemblies into single components also reduces weight by eliminating the need for fasteners like nuts and bolts.
- Faster Development – The larger an object, the longer it takes to create and setup the tooling to fabricate it through traditional means. With 3D printing, there are essentially no setup steps so large prototypes are significantly faster to print than to make them any other way. A large object may take a while to print, but by cutting out the time-consuming tooling step, it may also be faster to do production runs of large objects, depending upon the specifics.
- Reduced Cost – 3D printed large parts can be cost competitive with conventionally-made parts almost entirely because of the tooling costs of the latter.
Consolidated assemblies usually cost less as well because fewer materials have to be sourced from different places.
- Design Freedom – Using conventional manufacturing methods, many geometries are just not possible, such as internal channels and complex lattice structures. Many large objects, like furniture, benefit from such features and XL printers are the only way to realize those designs.
Large Scale 3D Printing Examples
- Restoration and replication – XL 3D printing has become rather popular among paleontologists as the technology allows them to both study and preserve the delicate fossils that they regularly handle.
- Furniture – Thanks to large-scale 3D printers it is now possible to create complex functional designs within a fully digitized process chain. From full-size prototyping to production of 3D printed furniture.
- Display advertising – XL 3D printers are perfect for making high-quality, modern signage and lettering for retail stores, businesses and exhibitions.
- Props – With the introduction of large scale 3D printers, designers can now produce enormous set pieces – overnight. 3D printing can help designers quickly manifest their wildest imaginations into the physical reality, and the Film & TV industry has taken notice.
Pellet Extrusion
One of the differences between desktop-sized machines and XL printers is the possibility to utilize pellet extrusion systems on the large printers. Pellet extrusion doesn’t use spooled filament as feedstock but instead uses the same virgin plastic pellets that are used for injection molding, which are much cheaper than spooled filament. This makes it easy to mix different plastics to make custom polymer blends and colors. These systems can also take shredded plastics as feedstock, which enables users to directly recycle water bottles, milk jugs, and failed and unneeded prints into new objects. Such a degree of a circular ecosystem can not be achieved with any other form of manufacturing.
That’s all great but what compels most users to opt for pellet extrusion is its blazing speed as the technology enables output of several kilograms per hour. Printing times scale exponentially with part size so having a high extrusion rate is pretty important for large-format 3D printing. One drawback of pellet extrusion systems is that they struggle with retraction, a feature that filament extruders employ to improve surface finish by pulling back on the filament during non-extrusion travel moves; retraction reduces or eliminates blobs, dots, and stringing on prints. Some XL printers can operate with both filament and pellet extrusion systems, allowing users to choose the best toolhead for their specific application.
Get a Quote
Large Scale 3D Printers
Looking to implement large scale 3D printers in your production process? Get a quote from Modix or Industry
Modix BIG Meter
With the Modix BIG Meter, you are now able to manufacture objects as large as 1010 x 1010 x 1010 mm in one go!
$13,500Modix
Request a Quote
modix big meter
- Benefits
- Applications
- - DIY self-assembly kit
- - Print Volume: 1010 x 1010 x 1010 mm
- - Printer Dimensions: 1300 x 1470 x 1830 mm
- - Shipping Weight: 200kg
- - Included: Dual print head, E3D Aero & Volcano 1.
75mm
- - Reprap Firmware developed and supported by Duet3D
- - 7 inch touchscreen made by Duet3D
- - E3D Titan Aero extruder with E3D Volcano hotend
- - Automatic bed tilt calibration
- - Power Requirements: 32A, single phase, 208-240V
Mold Making, Prototyping, Research and Development, Restoration
Industry MAGNUM
Hailing from Sweden, Industry is a company that has made major waves in the world of 3D printing. The new MAGNUM large scale pellet 3D printer enables you to print parts measuring 1500 x 1200 x 1200 mm.
A powerful E25 extruder manufactured to handle shredded material, granules or pellets. The MAGNUM handles nozzles between 2-8mm and has an average output between 1-8 kg / hour & a maximum output of 15 kg / hour.
MAGNUM offers powerful control features based on Bosch Rexroth MTX system control. It comes with a camera and mail/text module for external monitoring. A large touch screen display allows for easy setup and agile control.
€159,000Industry
Request a Quote
Industry MAGNUM
- Benefits
- Applications
- - Large scale pellet 3D printer
- - XL build size: 1500 x 1200 x 1200 mm
- - Granular extruder, which reduces material costs
- - Fast build rate: up to 15 kg per hour
- - Touch screen display
- - High quality linear motion modules from Bosch Rexroth MTX
Mold Making, Production, Prototyping, Research and Development, Restoration
Modix BIG-180X
The BIG-180X features a print volume of 1800 x 600 x 600 mm and comes at a competitive price of $12,000 USD. The unique extra width of the build chamber is designed per request of customers working in the automotive industry.
$15,500Modix
Request a Quote
modix 180
- Benefits
- Applications
- - DIY self-assembly kit
- - Print Volume: 1800 x 600 x 600 mm
- - Printer Dimensions: 2170 x 1060 x 1430 mm
- - Shipping Weight: ~240kg
- - Included: Dual print head, E3D Aero & E3D Volcano 1.
75mm
- - Reprap Firmware developed and supported by Duet3D
- - 7 inch touchscreen made by Duet3D
- - E3D Titan Aero extruder with E3D Volcano hotend
- - 4 X Z axis motors are controlled individually providing automatic bed tilt calibration.
- - Minimal Electricity requirements: 32A, single phase, 208-240V
Prototyping, Research and Development, Restoration
Modix BIG-120Z
The closed enclosure of the BIG-120Z is made of aluminum composite panels and polycarbonate doors. It incorporates a premium motion system including HIWIN motion rails, Gates timing belts and IGUS signal cables. This is a smart 3D printer providing several key reliability features including power-off resume, filament runout sensor, 120 probing points based automatic bed leveling, stall detection and more. The manufacturer offers an active air filter device as an add-on.
$7,500Modix
Request a Quote
BIG-120Z
- Benefits
- Applications
- - DIY self-assembly kit
- - XL print volume of 600 x 600 x 1200 mm
- - Z axis guides, HIWIN MGW Linear Rails
- - Duet 2 Wifi, 32Bit controller developed by Duet3D
- - Reprap Firmware developed and supported by Duet3D
- - 7 inch touchscreen made by Duet3D
- - Dual print head
- - E3D Titan Aero extruder with E3D Volcano hotend
Displays, Fashion, Mold Making, Prototyping
Modix BIG-120X
Modix BIG-120X Version 3 represents a major leap forward with regards to the printer reliability, print quality, ease of assembly and readiness to future advanced updates. Since Modix big60 and 120X share the same core design the new update is benefiting both models.
$7,500Modix
Request a Quote
BIG-120X
- Benefits
- Applications
- - DIY self-assembly kit
- - XL print volume of 1200 x 600 x 660 mm
- - Duet 2 Wifi, 32Bit controller developed by Duet3D
- - Reprap Firmware developed and supported by Duet3D
- - 7 inch touchscreen made by Duet3D
- - E3D Titan Aero extruder with E3D Volcano hotend
- - Closed loop motion system (optional)
Mold Making, Prototyping, Research and Development, Restoration
Get a Quote
XL 3D Print Service
3D printing is a viable option for display advertising, large scale concept models, car parts, furniture, molds & tooling. We offer both cost effective solutions with thick layers and rough surfaces for rapid prototyping as well as highly detailed & post-processed end-use objects. Please contact — [email protected] — for any questions or complete the form below and we’ll answer you as soon as possible.
- Technologies: FDM, SLA, GDP
- Materials: From PLA to CF composites & more
- Maximum print size: 1450 x 1100 x 1800 mm
- Post-processing: Spray paints, metal coatings, assembly & many more
Large Format 3D Printing Service
Back
-
Materials
Materials by Service
Injection MoldingCNC Machining3D PrintingSheet Metal
Materials by Type
PlasticsMetalsElastomers
Related Links
Customer Supplied ResinsColors
Injection Molding Material Alternatives Guide
Struggling with thermoplastic material shortages? We created a detailed guide to resin substitutes for ABS, PC, PP, and other commonly molded thermoplastics.
Download
-
Resources
Design Tips Guides and Trend Reports Case Studies Design Aids Webinars and Trade Shows
Blog Videos FAQs Educators and Students Glossary
Industries Medical Aerospace Automotive Consumer Electronics Industrial Equipment
-
About Us
Who We Are Why Protolabs? Research and Development Cool Idea Award Partnerships Sustainability and Social Impact
Careers Investors Locations Press Procurement
Contact Us
Proto Labs, Inc.
5540 Pioneer Creek Dr.
Maple Plain, MN 55359
United StatesP: 877.479.3680
F: 763.479.2679
E: [email protected]Best-in-Class Online Quoting
After uploading your part design, you'll receive an online quote that includes manufacturing analysis to help improve part manufacturability. Within your quote, you can also adjust quantity and material and see price changes in real-time.
Learn More
Get a QuoteSign In
GET LARGE 3D PRINTS
Certifications
ISO 9001:2015 | AS9100D | ITAR Registered
Jump to Section
→ Build Sizes
→ Our Large Format 3D Printers
→ Part Bonding
Large format 3D printing is used for large, complex geometries and reducing multipart assemblies into a single design. 3D print metal parts as large as 31.5 in. x 15.7 in. x 19.7 in. and plastic parts as large as 29 in. x 25 in. x 21 in.
“I haven't found a better process out there that makes executing a 3D print project any easier.”
Maximum Part Sizes for Large Format 3D Printing
Material | Build Size | ||
---|---|---|---|
Metal | Aluminum (AlSi10Mg) | 31.5 in. x 15.7 in. x 19.7 in. | 400mm x 800mm x 500mm |
Inconel 718 | |||
Plastic | ABS-Like White | 29 in.![]() | 736mm x 635mm x 533mm |
ABS-Like Gray | |||
ABS-Like Translucent/Clear | |||
PC-Like Translucent/Clear | |||
PA 12 | 19 in. x 19 in. 17 in. | 482mm x 482mm 431mm |
Large Format Metal 3D Printer
For large metal parts, we use the Concept Laser X Line 2000R 3D printer. This machine provides a build volume of 400 x 800 x 500 mm. The X Line 2000R was designed specifically for the production of large, quality parts.
Large, 3D-printed parts are often used in industrial settings, aerospace applications, automotive, and energy.
Large Format Plastic 3D Printing
Stereolithography (SLA): Large SLA parts are built on 3D System iPros, which provide large build volume, while still producing detailed parts.
Selective Laser Sintering (SLS): For large parts built in PA 12, we use sPro140 machines.
Bonding for Large Plastic Parts
Need a part that exceeds our machine's build volume? Part cutting and bonding is available for SLA, SLS, and MJF to achieve even larger part sizes.
Wall thickness needs to be sufficient for a good cut. For large geometries we need a minimum of a 0.1” (2.54mm) or 0.12” (3mm) thick wall to get a decent cut. Keep in mind, the thicker the better to achieve the best cut. If a part is too large to print in one piece then you will likely want to have thick walls regardless to overcome potential part warpage.
The cutting and bonding process will leave stark visible seams at the cut and bond interface. These can be unsightly, but may be allowable if you are using the part for function only. If the part is meant to be aesthetic, custom finishing can be performed to smooth, fill, prime, and paint the bond interface seams. Note, this is difficult to achieve with functionally clear parts.
Related Resources
PODCAST: Large-scale 3D printing with GE Additive’s X Line
Explore the history of large-format 3D printing and how to design your parts for best results on these machines with GE Additive.
Read Blog
Combining Part Assemblies with Additive Manufacturing to Reduce Cost and Increase Performance
How to find the right opportunities to consolidate multi-part assemblies into single components with industrial 3D printing
Read White Paper
Large Format 3D Printing for Aluminum and Inconel Parts
When you’re printing really large parts in metal, it’s great to have a choice of materials. Aluminum and Inconel 718 both make a lot of sense, but which one is the best for your application?
Read Blog
3D Printing Materials: Select the Right Plastic or Metal for Your 3D-Printed Part
Explore material properties available for plastic and metal 3D printing processes
Read Guide
Large Format Raise3D RMF500 for 3D Printing with Carbon Fiber Reinforced Materials
Last autumn, the well-known Chinese manufacturer of 3D printers, Raise3D, announced the creation of a new 3D printer for small-scale production in the industrial sector - RMF500 . The unique feature of the novelty is the combination of the ability to print with carbon fiber reinforced material (colloquially carbon fiber), wide format and affordability .
We all know that high technology is becoming more accessible every day, and the RMF500 is a prime example of this. There have been systems on the 3D printing market for several years that print carbon fiber composites of similar quality, but, unfortunately, they are not available to all companies due to the very high cost and supply problems. For example, such professional 3D printers are produced by the American company Stratasys - Fortus 450mc, but they are equipped with less technological features and are much more expensive. nine0003
Let's take a closer look at what the RMF500 is and how it differs from other 3D printers.
The RMF500 is specifically designed for printing complex parts with high durability. It will enable 3D printing companies to expand their product portfolio with carbon fiber and fiberglass end parts. Both materials specially developed by Raise3D, such as PA12 CF, and materials from other manufacturers approved by Raise3D under the Open Filament Program (OFP) will work. Parts made of carbon and fiberglass are more rigid, durable, resistant to heat and shock than parts made of other plastics. For carbon and fiberglass printing, the RMF500 uses silicon carbide nozzles with a hardness of more than 60 HRC. nine0003
PA12 CF filament is the result of long-term development by Raise3D engineers. This is a carbon fiber reinforced filament with increased stiffness and reduced shrinkage and does not require a thermostatic print chamber. The parts obtained from it are light and extremely durable, sometimes they can even be used instead of metal. In addition, the company has developed the PPA GF glass-filled filament specifically for the RMF500 and plans to release PET-CF, ASA-GF, PPSU-GF and PP plastics for medical use. Raise3D promises that all fiber reinforced plastics will be competitively priced. nine0003
The RMF500 has a huge building area 500x500x500 mm. The size of the build area matters in the production of large parts and small-scale production. For comparison, the print area of the Fortus 450mc is 406x355x406mm.
In the photo: printing a large model with carbon fiber in the RMF500 3D printer from Raise3D.
Repeatability and print speed are very important for low volume production. The maximum print speed of the RMF500, according to the manufacturer, can reach 300 mm/s. Positioning accuracy along the XY axis - 1 micron, along the Z axis - 0.09765 microns.
Synchronous feedback control with 1 µm accuracy reduces speed fluctuations as motor load changes, further improving accuracy. Stability and repeatability of printing has long been a hallmark of Raise3D printers. The FFF technology on which this 3D printer is based allows the production of parts with a high degree of repeatability, high positioning accuracy and uniform extrusion. The RMF500 can quickly print large batches of identical parts. nine0003
Pictured: production of lots from a large number of parts on the RMF500.
The printer has a printing system with two independent IDEX extruders. It allows you to print with one or two extruders at once. The RMF500 can run two jobs at the same time, further increasing productivity and task speed. The extruders are manufactured using high temperature alloys and industrial ceramic composite materials. These characteristics provide stable and high extrusion speed up to 500 g/h. nine0003
The RMF500 has a strong design . The one-piece frame is made of hardened steel. Stainless steel linear guides have a design load of approx. 100 kg. The bearing of the linear guides has minimal backlash and does not require frequent maintenance.
An important detail - Raise3D has developed special support material for printing with reinforced plastic PA12 CF, which can be easily detached.
Pictured: Parts printed on the RMF500 with PA12 CF filament with special proprietary support. nine0032
The RMF500 is equipped with four large compartments for plastic spools. Switching between the main and auxiliary compartments occurs automatically. This feature reduces the amount of time spent threading the filament. The humidity control system keeps the relative humidity in the chamber below 5%, preventing humid air from entering from outside.
What else is there in the RMF500 from nice additional options. The front of the printer has a large 13.3-inch touch screen. Supports connection, management and printing via Wi-Fi and LAN. There is a reliable auto-calibration system from Raise3D. nine0003
Carbon fiber printed parts are strong enough to be used in the automotive and aerospace industries. Of course, they will not replace functional parts that have a special load, but their scope can be very wide. Raise3D has already presented the results of the first RMF500 printing and its application.
Pictured: Functional parts, accessory tools and fixtures, car décor printed on the RMF500. nine0032
Pictured: Functional parts, accessories and aerospace prototype printed on the RMF500.
In the photo: on the left is a prototype of the hinged window mechanism (details are printed with metal filament and carbon), on the right is a carbon fixture. Carbon parts printed on RMF500, metal parts printed on Metalfuse. Printing with fiber-filled plastics does not require a heated chamber, peak power consumption is less than 3 kW. The average power consumption per unit of print area of the RMF500 is 60% lower than the competition. nine0089
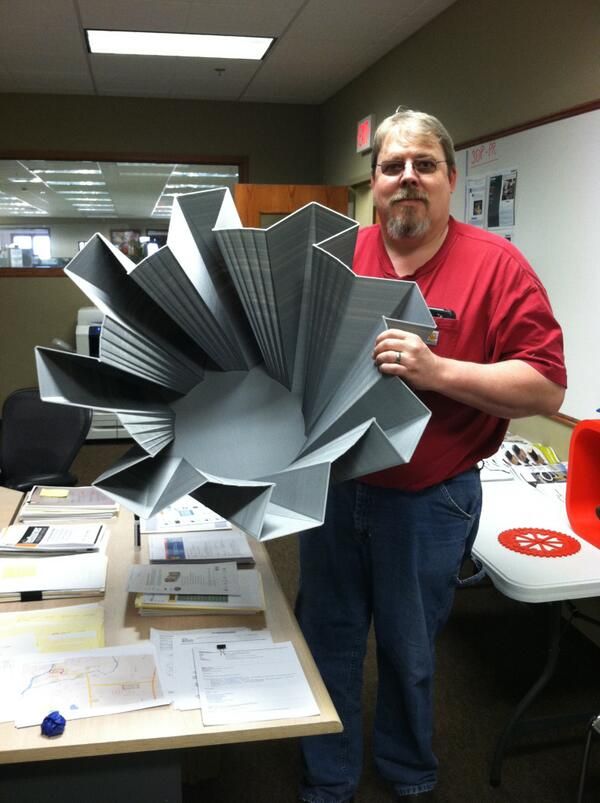
Operating temperature of the extruder | to 330 ℃ | to 300 mm/s 900 mm/s 900 mm/s 900 mm/s 900 mm/s 900 mm/s 900 mm/s 900 mm/s 900 mm/s 900 mm/s 900 mm/s -filter | yes |
Build Tak pad surface | yes |
Positioner | Rockchip ARM Cortex-M4 |
Operating systems | Linux, Windows, iOS |
Maintained file formats | STL/ Obj/ OLTP |
ETERARNETS, WIRELESS 802.1 | |
Ports | USB 2.0 × 1 |
Electrician | 30 A @ 380 volts AC |
Energy consumement | 24 V, 350 WATT; 12V, 75W |
Memory | 1 GB, built-in flash memory 8 GB |
Sizes (without packaging) | 1340 × 2370 mm |
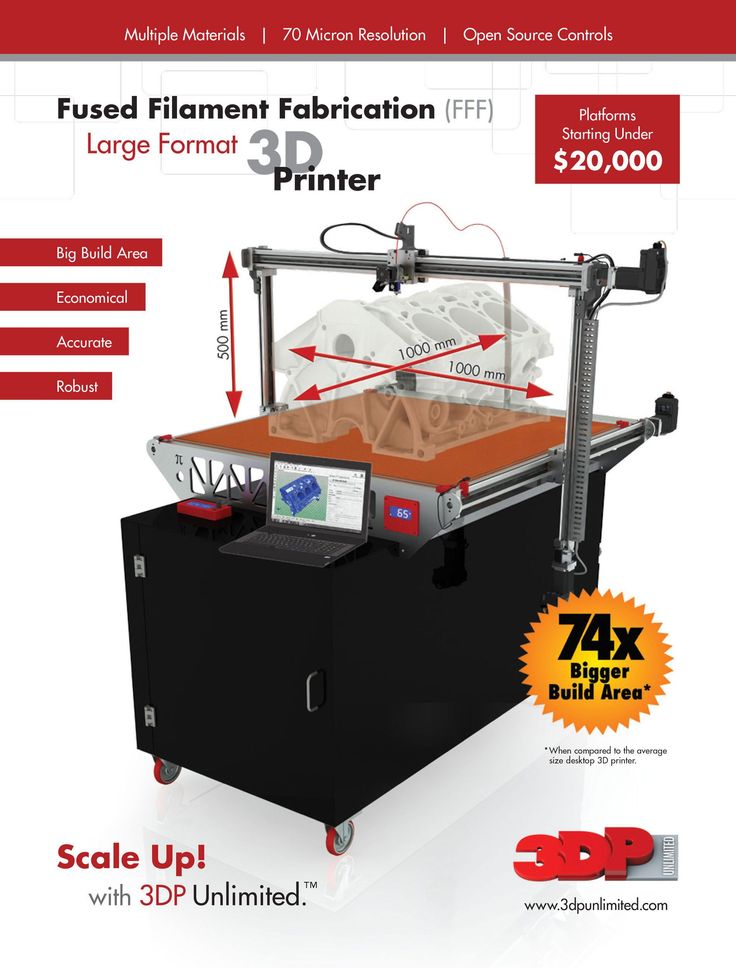
$250 room-sized 3D printer / Sudo Null IT News0001
Why not make a 3D printer out of a garage or an empty room? An open source project from Sweden makes this possible for $250. Who is less?
Article by Glenn McDonald from Seeker.com translated for you by Top 3D Shop .
Swedish inventor Thorbjorn Ludwigsen has spent the last three years developing a new kind of large-format 3D printer that can create large objects. His invention can print furniture right in the room - it's very easy and relatively cheap. Ludwigsen's invention, the "Hangprinter", uses a system of wall, floor, and ceiling-mounted cables and computer-controlled drives on a print head unit. The device uses the room itself as a 3D printer case. nine0003
Hangprinter is not the first large format 3D printing system, but it is unique. First, it's cheap. All hardware and firmware components can be purchased for approximately $250. In addition, it is an open project, which means that any user can improve the system and use third-party updates. Finally, Hangprinter is self-sufficient - most of the components necessary for its creation can be printed by it.
It all adds up to a system that Ludwigsen hopes will unlock the potential of 3D printing for more people. The developer believes that 3D printing should not be an expensive perk. In his opinion, Hangprinter is not only a technical, but also a social experiment. nine0003
“In particular, I want 3D printing to avoid the fate of 2D printing, where machines are programmed to self-destruct after a certain number of objects are made. The best chance to do this is not only to use open source, but also to create self-replicating hardware. Hangprinter manufactures most of the necessary elements for itself”
- he said.
The Hangprinter project is part of a larger initiative in the 3D printing community known as RepRap. All developers try to optimize prototyping processes as much as possible. The idea is to spread 3D printing technology to low- and middle-income people through open design solutions and self-replicating mechanisms. nine0003
“Open technology can empower middle- and low-income families, and I grew up in one of those families,” said Ludwigsen.
The innovator is taking this project very seriously. As a physics student at Umeå University in Sweden, he recently completed his master's thesis on the subject.
In the Hangprinter video, Ludwigsen showed how a 3D printer creates a relatively simple and functional object - a lampshade. nine0003
The Hangmaker has also been involved in more artistic projects - Ludwigsen recently used this system to assemble a five-foot sculpture of the Tower of Babel.
Hangmaker prints the Tower of Babel sculpture. Author: Thorbjorn Ludwigsen.
As the device is optimized, Ludwigsen hopes the Hangprinter will become versatile enough to print furniture, tools and possibly fully functional machines with moving parts. He also hopes to raise money through crowdfunding to continue research and development in this direction.