3D printed dna 200
▷ dna 200 box 3d models 【 STLFinder 】
DNA 200 Box Mod
thingiverse
This is my personal draw for a DNA 200 Box Mod, to complete you need: DNA 200 by Evolv Vapor ( http://www.modmaker.co.uk/Mod-Making...s/Evolv-DNA200 ) Turnigy Graphene 1000mAh 3S 65C ( http://www.hobbyking.com/hobbyking/s...ck_w_XT60.html ) Connector...
C frame DNA 200 vape box mod
thingiverse
It's never been successfully test printed, I can't get abs to stick to my bed to save my life. ...Needs button caps. Fits a dna 200 and a 3s 1300mah lipo.
Dna 200/250 Compact Box Mod
thingiverse
Parts list: 1x Dna 200/250 1x 510 connection 1x Renegade X push button or similarly sized button 2x Battery Contacts for bottom bridge plate - suggest some sort of bump contact similar to the one used in the top loader mod I've uploaded. 2x Spring...
DNA Box Mod 75/200/250
thingiverse
ich habe das wirklich sehr coole Design etwas verändert: - 510er ist nun mittig und eingelassen (Atties bis 32,5mm sind kein Problem) - Halter für Akkukontakte - kleine Kabelkanäle - mehr Platz für Kabel und 510er Kontermutter - Deckel für 4...
DNA 200/75 18650 Enclosure V2
thingiverse
DNA 200/75 Box for dual 18650. I used the VaporShark DNA 200 buttons (I had a dead one in my collection) Uses magnets and pegs to align and hold together. 510 is a 10mm hole. Moved 510 added some supports for the board monting. ... Print Settings...
Evolve DNA 200
grabcad
Evolve's DNA 200 model, with JST, USB, and Screen added. ... Made as accurately as possible without having a board in my hands.
DNA 200 Dual Battery Mod
thingiverse
The screws used to hold the DNA board and the mod together, are 5mm in length and 1.7mm per the DNA 200 board datasheet. The mod is designed for a Fat Daddy v4 low profile 510 connector. The buttons are 8mm and 5mm respectively. I did not...
DNA 75/200/250 Faceplate
thingiverse
This faceplate is designed for the DNA 75/200 or 250, i have used this to mount a DNA250 in a Moonshot tin, simply cutout the required rectangular hole in your mod and glue the plate in place. ...
Update: Added buttons rounded to suit.
DNA 200 board case and screen mount
thingiverse
DNA 200 board case and screen mount.https://youtu.be/hyDXC8oKOQ8
DNA box mod
thingiverse
Dna box for a limo that is approx ~130x40x30mm
Dna 200/250 Power Supply Mod Pod
thingiverse
Parts List: 1x Dna 200/250 1x Speak on quick connector 1x 510 Misc wire and wire shielding Print is incredibly straight forward here, the face place prints flat side down and the rear pod prints vertically. The 510 connection is located so close the...
DNA Storage Box
prusaprinters
Store your things in DNA -- this is an open-topped storage container with an abstract design that models DNA. Spheres represent sugars, and lines between spheres represent base-pairs. This was originally designed for holding business cards, but can...
DNA Storage Box
thingiverse
Store your things in DNA -- this is an open-topped storage container with an abstract design that models DNA. Spheres represent sugars, and lines between spheres represent base-pairs. This was originally designed for holding business cards, but can...
DNA 200 Squonk Mod
thingiverse
Hevily inspired by https://www. thingiverse.com/thing:3089608 and Vandy Vape mods.
DNA 75/200/250
thingiverse
This a a remix of the Tigerbox, i have reduced the dimensions but it will still accommodate dual 18650's or a 1300mAh lipo.
dna 200 screen holder
thingiverse
The stl looks bad but its a much needed improvement it centers the viewable area of the screen in a mod and allows for easy access to the screen and board Print Settings Printer: Geeetech i3 aluminum ...
dna 75-200 boxmod by umbra for dual 18650
thingiverse
dna 75-200 dual akku boxmod 4mm dia magnets dual 20700 can fit need test mount is in my designs 22mm Connect 510
Dna 75-200 mount and front plate by umbra
thingiverse
dna75-200 stuffby Umbra modz
dna
grabcad
dna
DNA
grabcad
DNA
DNA
pinshape
DNA
DNA
thingiverse
DNA
DNA
thingiverse
DNA
DNA
thingiverse
DNA
DNA
thingiverse
DNA
DNA
grabcad
DNA
DNA
grabcad
DNA
DNA
thingiverse
DNA chain
DNA
grabcad
DNA model
DNA
grabcad
animation DNA
New Research Could Lead to DNA 3D Printer - 3DPrint.

Technology is capable of amazing things, but it doesn’t mean those things are easy. It’s incredible that scientists can produce DNA in a lab, but the process is difficult, lengthy and requires toxic chemicals. Imagine, however, if they could simply print it, the way that you would 3D print anything else. That could be the future, after scientists at UC Berkeley and Lawrence Berkeley National Laboratory developed a new way to synthesize DNA. The method could lead to DNA printers, similar to ordinary 3D printers, that could produce DNA strands that are more accurate and 10 times longer than the strands produced with today’s methods – more quickly and easily, and without the use of toxic chemicals.
“If you’re a mechanical engineer, it’s really nice to have a 3D printer in your shop that can print out a part overnight so you can test it the next morning,” said UC Berkeley graduate student Dan Arlow. “If you’re a researcher or bioengineer and you have an instrument that streamlines DNA synthesis, a ‘DNA printer,’ you can test your ideas faster and try out more new ideas.
I think it will lead to a lot of innovation.”
The research was led by Arlow and PhD student Sebastian Palluk, a doctoral student at the Technische Universität Darmstadt in Germany and a visiting student at Berkeley Lab. It is published in a paper entitled “De novo DNA synthesis using polymerase-nucleotide conjugates,” which you can access here. The research was conducted at the Department of Energy’s Joint BioEnergy Institute (JBEI).
“I personally think Dan and Sebastian’s new method could revolutionize how we make DNA,” said Jay Keasling, a UC Berkeley professor of chemical and biomolecular engineering, senior faculty scientist at Berkeley Lab and Chief Executive Officer of JBEI.
Keasling and JBEI scientists specialize specialize in adding genes to microbes, typically yeast and bacteria, to sustainably produce useful products. Palluk came from Germany specifically to work with Arlow in Keasling’s lab.
L to R: Dan Arlow, Sebastian Palluk and Jay Keasling
“We believe that increased access to DNA constructs will speed up the development of new cures for diseases and simplify the production of new medicines,” Palluk said.
![]()
The synthesis of DNA is a growing business; companies are ordering custom-made genes so that they can produce chemicals, biologic drugs or industrial enzymes. Researchers purchase synthetic genes to engineer plants and animals or try out new CRISPR-based disease therapies. Some scientists have even researched storing information in DNA, but that would require much larger quantities of DNA than are currently synthesized. All of these applications require that synthesis produce the desired sequence of nucleotides or bases, the building blocks of DNA, in each of millions or billions of copies of DNA molecules.
Current DNA synthesis is limited to producing oligonucleotides about 200 bases long, because errors in the process lead to a low yield of correct sequences as the length increases. To assemble even a small gene, scientists have to stitch together segments of about 200 bases long. The turnaround time for a small gene of 1,500 bases long can be two weeks at a cost of $300, limiting the experiments that scientists can do. Synthetic biologists like Arlow, Palluk and Keasling often insert a dozen different genes at once into a microbe to get it to produce a chemical, and each gene presents its own synthesis problems.
“As a student in Germany, I was part of an international synthetic biology competition, iGEM, where we tried to get E. coli bacteria to degrade plastic waste,” said Palluk. “But I soon realized that most of the research time was spent just getting all the DNA together, not doing the experiments to see if the engineered cells could break down the plastic. This really motivated me to look into the DNA synthesis process.”
The technology developed by Palluk, Arlow, Keasling and their team relies on a DNA-synthesizing enzyme found in cells of the immune system that has the natural ability to add nucleotides to an existing DNA molecule in water, where DNA is most stable. The technology results in increased precision, allowing synthesis of DNA strands several thousand bases long – a medium-sized gene.
“We have come up with a novel way to synthesize DNA that harnesses the machinery that nature itself uses to make DNA,” Palluk said. “This approach is promising because enzymes have evolved for millions of years to perform this exact chemistry.”
Cells create DNA by copying it with the help of several different polymerase enzymes that build on DNA already in the cell. But in the 1960s, scientists discovered a polymerase that doesn’t rely on an existing DNA template but instead randomly adds nucleotides to genes that make antibodies for the immune system. The enzyme, called terminal deoxynucleotidyl transferase (TdT), creates random variation in these genes, resulting in antibody proteins that are better able to attack new types of invaders.
TdT is fast and does not have side-reactions that could affect the resulting molecule. Scientists over the years have tried to use the enzyme to synthesize DNA sequences, but it was hard to control. The key is to find a way to get the enzyme to add one nucleotide and then stop, so that the sequence can be synthesized one base at a time. Previous approaches tried to obtain that control by using modified nucleotides with a special blocking group that prevents multiple additions at once. After the DNA molecules have been extended by a blocked nucleotide, the blocking groups are removed to allow the next addition.
TdT, however, cannot accommodate a blocking group on the nucleotide being added. But Arlow came up with the idea to tether an unblocked nucleotide to TdT, so that after the nucleotide is added, the enzyme remains attached and prevents further additions. After the molecule has been extended, the tether is cut, releasing the enzyme and re-exposing the end for the next addition.
In the first trials, the researchers demonstrated that this technique is not only faster and simpler, but nearly as accurate as other techniques in each step of the synthesis.
“When we analyzed the products using NGS, we were able to determine that about 80 percent of the molecules had the desired 10-base sequence,” Arlow said.
“That means, on average, the yield of each step was around 98 percent, which is not too bad for a first go at this 50-plus-year-old problem. We want to get to 99.9 percent in order to make gene-length DNA.”
Once they can reach 99.9 percent fidelity, they can synthesize a 1,000-base-long molecule with a yield of more than 35 percent, which is currently impossible with existing techniques.
“By directly synthesizing longer DNA molecules, the need to stitch oligonucleotides together and the limitations arising from this tedious process could be reduced,” said Palluk. “Our dream is to directly synthesize gene-length sequences and get them to researchers within few days.”
“Our hope is that the technology will make it easier for bioengineers to more quickly figure out how to biomanufacture useful products, which could lead to more sustainable processes for producing the things that we all depend on in the world, including clothing, fuel and food, in a way that requires less petroleum,” said Arlow.
![]()
He added, “Our dream is to make a gene overnight. For companies trying to sustainably biomanufacture useful products, new pharmaceuticals, or tools for more environmentally friendly agriculture, and for JBEI and DOE, where we’re trying to produce fuels and chemicals from biomass, DNA synthesis is a key step. If you speed that up, it could drastically accelerate the whole process of discovery.”
Discuss this and other 3D printing topics at 3DPrintBoard.com or share your thoughts below.
[Source: UC Berkeley / Images: Marilyn Chung, Berkeley Lab]
Stay up-to-date on all the latest news from the 3D printing industry and receive information and offers from third party vendors.
Tagged with: 3d printed dna • dna • dna printing • Joint BioEnergy Institute • Lawrence Berkeley National Laboratory • synthetic dna • uc berkeley • University of California at Berkeley
Please enable JavaScript to view the comments powered by Disqus.
I did not expect this 3D printer Vector 200
Hello everyone!
Today I will tell you about my new acquisition, Vector 200 from Geralkom . I'll tell you about its characteristics, strengths and weaknesses. And I will also share my impressions of using the printer.
By its name, you can already understand that 200 is the size of the working area of the table 200 by 200 mm. And along the Z axis, the working field is 210mm. I am one of those people who find it easier to glue a model from several pieces. Than overpaying a lot of money for a printer with a large table. To print something more once a year. Over the many years of my life with a 3D printer, my experience has shown that a 200x200mm table is enough for home printing and small businesses.
But let me start from the beginning. It all started with my friend knowing how much I dislike dark and gloomy printers. Pleased me with the news that a white printer appeared on the market.
I became interested and started looking for information about him. And since the model was fresh, there was very little information. I just found out the kinematics of his H-bot extruder Direct and he is white. According to this information, not everything was clear and I wanted to fix it. Then I started asking the manufacturer to give me a printer for review. It lasted about three months, and finally the day came when I went for the printer.
First look, equipment and appearance.
I won't talk about the configuration for a long time. While I am writing an article, the manufacturer is still looking for the ideal price and kit option. This may change in the future. I had the kit as pictured. Only another spool of PLA plastic 0.75 kg.
At the expense of appearance. They say it's all a matter of taste. And the taste and color of all felt-tip pens are different. So it's up to you to decide whether you like it or not. I really like it. Having brought it home and on the very first day I filled the TPU coil from FDplast (who does not know this is one of the most flexible rubber-like filaments in Russia). And about a miracle! From the box. Without any settings. On the profile from the manufacturer, I got a very high quality print. Airflow was broken on my old printer. And I have decently accumulated projects that needed airflow. And then it began! For a month, almost day and night, the printer worked without stopping the nozzle.
One simple moment can probably explain such an unbridled thirst for printing. To print something, it was enough just to change the temperature for the plastic and turn the blower on or off. Instead of digging through a pile of settings with the hope that it will be better than last time.
Here are some of the things that were printed with this printer.
Well, it would probably be logical to show you closer. What pleased me the most. So this is a flat surface with a minimum number of artifacts. To be honest, this is the first time in my life that I have such print quality. If the plastic is not damp and dumb, then the details are of amazing quality. I even almost stopped using my grinder. Pay attention to the seam that forms at the beginning of the layer. With bowden, I had big problems with this seam.
And in this picture you can clearly see the difference between the printed parts on the Vector and on the Flying Bear. I used the same plastic and temperature conditions. (Not a big deviation). Last year I lived with a Bowden printer and despite the fact that the printer is good, the Bowden feed just killed me. That will loosen the tube due to which under-extrusion at the beginning of the layer. Then you have to put such retracts that the motor on the extruder goes crazy. And the advantage of a light head is negated. You try to print in flex and it's not that it doesn't print. But there are so many nuances and torments that I vowed to convert all my bowdens to direct and forget about these torments).
That's why the direct printer out of the box was like a breath of fresh air for me.
These were not all the details. Many immediately went to my friends and I did not have time to photograph them. But there was one very large project, which I took some pictures of.
A friend modeled a rider with a horse on the iPad and it was almost 40 cm long. Because of this, the whole model was cut into 13 pieces and printed with a layer height of 0.15mm. And small details in general with a layer height of 0.05mm. There were two such riders. And it took me a week and a half, almost around the clock printing. All parts of the horse were printed from ABS plastic. And on the example of the tail, it is very clearly seen that despite the ABS and the small area of \u200b\u200bcontact with the table, the tail did not fall. And all this thanks to the precise feed of the direct extruder. I couldn't print like that on a Bowden. The nozzle constantly clung to some bumps and influxes of plastic. Which led to knocking down fine details. In this photo, the infill was being printed at 80mm per second. You can judge the quality yourself.
After I printed two horses, the author of the model glued all the parts (I want to note that he had never encountered printing before and did everything for the first time). Then I applied a thin layer of epoxy and walked a little with fine sandpaper. I first applied a layer of black primer. And then covered it with paint that tries to look like bronze. The result of all these manipulations, you can enjoy in the picture below. that after the purchase I did not set up anything and did not finish it with a high-precision file. The result made me happy.
Useful printer features.
- The printer comes with an auto-off module from the box. This is an important option. Since in the event of some kind of breakdown, the printer will turn itself off and prevent fire, self-destruction or something else :). An auto-off bonus is a button on the front panel.
With it, it is very convenient to turn the printer on and off. Especially when he stands close to the wall, you need to squeeze your hand and look for the button by touch. Believe me, I know what I'm talking about.
- It has a competent backlight that does not hit the eyes and illuminates the model well. This is one of the very useful things that everyone usually completes themselves. But here everything goes factory and we can only enjoy life.
- My favorite trick that not everyone understood. So it's not a bug, but a feature. The spool holder is inside the printer and only holds a 750g spool. But what if we have a kilogram? With a slight movement of the hand, open the lid, which is held on neodymium magnets and turn it over. Voila, we can fit any kilogram coil. I was also pleased with the fastening not from the back, but from the side. ( I hate rear mounting ) But if you decide to earn money and print a lot with this printer, then there are holes on the back wall for attaching a 2.
5kg coil. In general, thought out for all occasions.
- The printer is fully enclosed and ready to print out of the box. Plastics such as ABS, Nylon and so on. And since I print ABS in 95%, I accordingly paid attention to this not least.
- Well, then there are many little things that I will write in one paragraph.
- All coolers come with bearings.
- Head wires are connected via an adapter plate. Thanks to this, you can quickly change the heater, thermistor or fans.
- The cable channel is not simple, but tricky. With the ability to snap off the segments and lay new wires with a slight movement of the hand. A trifle, but nice.
- Table for 220v and it is grounded.
- Good two-way airflow for the model. My life tests showed excellent results on PLA plastic.
- This is my first experience with H-Bot kinematics and I had some concerns about the long strap. Like, it can stretch and affect the print. Fears were not confirmed.
It turned out that Hiwin rails are a very good solution. And you do not need to change bearings every half a year. As it happens on roller printers.
- I don't even know if it makes sense to say that HIWIN's accurate MGN-9 rails are not cheap. Which directly affects the quality and life of the printer. I am very glad that the manufacturer stopped on them.
- There are very few printed parts in the printer, but enough milled aluminum parts. Which adds another plus sign to karma.
- Optical end switches that do not click.
- Complete USB stick. And what a flash drive! Which does not stick out of the body.
- Proven power supply from the Taiwanese company MEAN WELL for 24 volts.
- By default there is a thermistor, which works up to 300 degrees. Optionally, you can install another one that works up to 350 degrees. As a matter of fact, I have one. Therefore, there will be more interesting videos with tests of high-temperature plastics.
Don't forget to subscribe to .
- Branded motors Stepperonline.
- Motherboard Robin nano v3 with quiet drivers on all TMC2209 motors.
It may seem that my sugary review is paid. And everything that I wrote here is presented through the prism of that mountain of money that was brought to me. But let's immediately dot the "I"! (Although I still don’t understand where her dots are, I’ll still clarify the situation).
I took this printer for review on my own initiative. After a week spent alone with the printer, I realized that I would not return it. Therefore, I added the manufacturer to the black list and use the printer with pleasure! :D It's a joke, I just bought the printer from Geralcom and my fee for the review was a discount on the purchase.
Therefore, everything that I wrote above and will write below is my personal experience and my impressions. I really liked the printer and for two months of everyday work with it. I have not had a single skipped step or aborted prints due to the printer. (Well, I can't really blame the printer for the overlap on the spool)
So my conclusion is this. The printer is very hardworking, stable and problem-free. Who does not want to deal with finishing and alterations, but buys for work from the box. It's his choice.
I was pleased with many thoughtful things and his appearance.
Shortcomings:
With all my laudatory reviews. The printer has a number of things that I didn't like.
- For all its specifications, the printer is quite noisy. Especially the hot end blower cooler. With the door closed, there is less noise, but probably you won’t be able to sleep in the same room with him. And I have something to compare with and I have slept with the printer in the same room more than once. At what printed ABS. (Here I am such a kamikaze).
- The aluminum plate of the table is only 2mm, which, according to my subjective feelings, is not enough.
Sometimes you have to tighten the table at the beginning of printing, as the calibration is a little off. Not often but still. Although, in general, my table is flat and details in the entire area are printed without problems.
- The wires to the fans on the hot end are a bit inconvenient. Because of what, when you remove the cover with fans, you need to get used to putting it back. If you do not do this carefully, you can damage the wires.
- I've heard complaints from people who opened the lid for the first time, which is only held on by magnets. They managed to drive this cover over the metal case. But this is only the first acquaintance. If I were the manufacturer, I would stick some kind of warning on the lid and when unpacking, a new person would not step on this rake. Because I really like this mount and it greatly expands the degree of freedom and access to the printer components.
- Someone complained about the weight of the printer. But here it is more a virtue than a disadvantage.
You don't carry the printer from room to room. Install it in its place and print. I personally like its armor-piercing hull.
Well, I will end on this note. You can buy a printer HERE, and subscribe to my channel HERE.
Thanks to everyone who read to the end! I appreciate it and for this I am going to do the next project! Fortunately, there is something to print it on! ;)
Have a good mood and no problem printing!
3D drug printing
September 11, 2018
Popular science competition "Bio/mol/text"-2018
Overview
Tablet formed by printing layers of polymer mixed with drug
Alvaro Goyanes
-
Author
- Alexey Korolev
-
Editor
- Andrey Panov
Topics
- "Bio/mol/text"-2018
- Biology
- Biotechnology
- The medicine
- Personalized medicine
- Pharmacology
Bio/mol/text contest entry: Recently, 3D printing has become one of the most revolutionary and powerful tools in many areas. The pharmaceutical industry is no exception. This article will tell readers about the history of 3D printing in the pharmaceutical industry, the latest developments and achievements in this field, and the prospects for the development of 3D printing in the industry.
This work was published in the nomination "Biopharmaceutics" of the competition "bio/mol/text"-2018.
The general sponsor of the competition is the Diaem company: the largest supplier of equipment, reagents and consumables for biological research and production.
The partner of the nomination is the medical company Invitro.
The audience award was sponsored by the Genotek Medical Genetics Center.
"Book" sponsor of the competition - "Alpina non-fiction"
Introduction
Now 3D printers can create almost everything. From car parts and fashion accessories to transplant organs and pharmaceuticals. For example, 3D printers can print medical devices with intricate designs, geometries, and features that fit a particular patient's anatomy.
3D bioprinting of organs and tissues is described in the articles " Organs from the laboratory " [1] and " Artificial organs and tissue engineering " [2]. — Ed.
Medical 3D printing is rapidly revolutionizing healthcare. The use of 3D printing in medicine brings wide-ranging benefits: personalization of medical devices, medicines, cost-effectiveness, increased productivity, and democratization of design and production.
Before we start delving into the topic of 3D printing in the pharmaceutical industry, let's figure out what 3D printing actually is.
Three-dimensional (3D) printing is an additive (additive) manufacturing method in which objects are made in layers by melting and sintering solid or solidifying liquid materials (ceramics, plastics, metals, powders, liquids, or even living cells).
There are about two dozen 3D printing methods that use different printing technologies, resolutions and speeds. There are hundreds of materials from which you can recreate a 3D object of almost any shape.
In order for a three-dimensional object to come into being, you must first create a digital model in a 3D editor, or CAD program, and export it to STL format. Using a special slicer program, translate the STL file into a control G-code for a 3D printer, prepare the 3D printer for work, and start printing. The most important elements of the printer are working platform (on which the formation of the object takes place) and printhead (it forms the object layer by layer). Some time passes (if the object is small - a few minutes or hours, and if it is large, then printing can take more than a day), and voila, the object is ready!
What is 3D printing we learned, move on.
A bit of history
Figure 1. The most important advances in 3D printing in the pharmaceutical industry
- Early 70s. Pierre Ciraud ( Pierre Ciraud ) described the method of applying a powder material and then solidifying each layer under the influence of a high energy beam.
- 1984 Stereolithography (SLA) invented by Chuck Hull ( Chuck Hull ) became the first commercially available 3D printing technology. This method is based on the photopolymerization of liquid resin with ultraviolet light.
- Mid 1980s. Carl Deckard ( Carl Deckard ) developed a method for solidifying powder layers using a laser beam, which he called the Selective Laser Sintering (SLS) method.
- 1989 Scott Crump ( Skott Crump ) patented Rapid Prototyping (FDM) technology is a method that uses a thermoplastic material to form a 3D object. Otherwise this technology is called Fused Deposition Modeling .
- 1990s. Invented the DOS method — similar in principle to that used in inkjet printers.
- 2008 Invented the RepRap printer, a self-copying mechanism for rapid prototyping.
- 2015 The American company Aprecia Pharmaceuticals has developed ZipDose technology, which makes it possible to form tablets that are convenient because they dissolve quickly in a small amount of water. This technology was used to produce the first FDA-approved printed drug Spritam® ( Food and drug administration , US Food and Drug Administration) [3].
Dictionary
- DOD
- ( Drop On Drop ) liquid layering.
- DOS
- ( Drop On Solid ) hard overlay.
- FDM
- fused deposition method, additive manufacturing technology.
- SLA
- stereolithography, additive manufacturing technology for models from liquid photopolymer resins.
- SLS
- selective laser sintering, additive manufacturing technology.
- STL
- file format widely used for storing 3D object models for use in additive technologies.
How drug printing works
Many different methods of 3D printing have been invented and developed over its 40 year history.
Basic 3D printing methods (fig. 2) are based on:
- solidification of powder material
- curing fluid
- extrusion [3]
Figure 2. 3D printing methods used to create medicines
Despite the variety of 3D printing methods, each of them includes the following steps, which we talked about at the beginning (Fig. 3) [3] :
- designing a 3D object using software and optimizing the geometry of the object according to the printer specification;
- export of a 3D model to a file format recognized by the printer, for example, STL;
- Importing a file into the software and creating layers in it to be printed. The height of the printed layer significantly affects the quality of the object, as well as the print time;
- fabrication of an object by subsequent application (or curing) of layers of material.
Figure 3. Stages of 3D printing, development
Application of 3D printing in pharmaceuticals (examples) see where these technologies are already being successfully used to create pharmaceutical products.
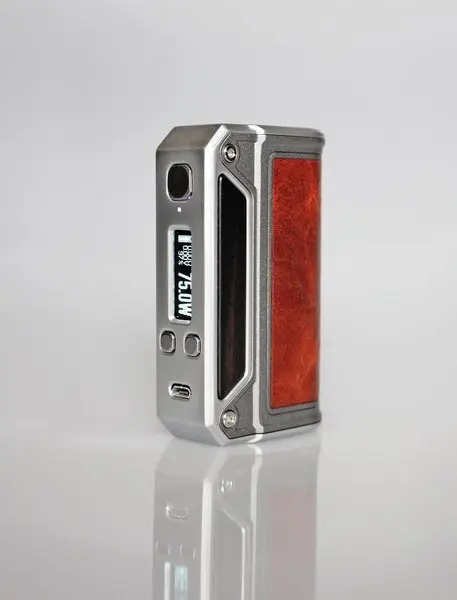
Example 1
As reported above, the first 3D printed drug was Spritam® (Fig. 4), developed by the American pharmaceutical company Aprecia Pharmaceuticals and approved by the Food and Drug Administration (FDA) . The active substance of the drug - Levetiracetam is an antiepileptic drug. Levetiracetam is able to quickly dissolve in the mouth, the time of disintegration (dissolution) of the drug is from 2 to 27 seconds (average - 11 seconds). A small sip of water is required to disintegrate the drug. The liquid formula, which binds levetiracetam and excipients for the manufacture of the drug, contains flavor-masking additives that improve the patient's condition [4].
Figure 4: Spritam® (levetiracetam), the first 3D printed drug
Aprecia Pharmaceuticals
Example 2
FabRx is a British biotechnology company specializing in the development of 3D printing technology for pharmaceuticals and medical devices. The company was founded by a group of scientists from University College London who saw the potential of 3D printing technology to create drugs [5].
Figures 5-7 show FabRx designs.
Figure 5. Gummy-like drugs in a variety of shapes, sizes, colors, textures and flavors. FabRx makes them attractive to different patient groups, especially young and old people.
fabrx.co.uk
Figure 6. FabRx researchers experimented with sizes and shapes of preparations and conducted a study that showed that a pyramidal tablet dissolves faster in water than a cylindrical tablet
fabrx.co.uk
Figure 7. University College London scientists also experimented with different drug forms (octopus, dinosaur, cat, monkey, and others) on a pediatric patient population
The future of 3D printing drugs in pharmacies is closer than you think
There are few examples, as 3D printing is just being introduced into the pharmaceutical industry, and today only a few companies are engaged in 3D printing of drugs.
Benefits and prospects of 3D printing in pharmaceuticals
Benefits
- Customization and personalization.
3D printing technologies allow dosage forms, release profiles and dosage to be customized for each patient. For example, for small patients, a tablet can be printed in the form of some cute animal of any color (Fig. 7).
- Improving cost efficiency. 3D printing will reduce production costs by reducing the use of unnecessary resources. Some drugs can be printed in forms that can be easily and conveniently delivered to the patient (Fig. 8).
- Democratization. Another feature of 3D printing is the democratization of product design and manufacturing. As the cost efficiency of 3D printing increases, the products become orders of magnitude cheaper. [6]
Figure 8. FabRx products
fabrx.co.uk
Looking ahead
In the distant future, perhaps if 3D printing develops, everyone will be able to print a drug at home. So far, this can only be a dream. But in the near future, as the researchers suggest, drugs can be printed in pharmacies and hospitals.
Can 3D drug printing replace traditional drug manufacturing technologies? No - it will require huge investments, trained employees and a number of other things. Yes, and large pharmaceutical companies can prevent the penetration of 3D printing into pharmacies and hospitals. 3D printing is unlikely to catch on in large enterprises, as 3D printers print much more slowly than pharmaceutical production machines. Another significant barrier that may prevent the widespread use of 3D printing in pharmaceuticals is the long and costly obtaining approvals from the quality control services of medicines. In addition, manufacturing regulations and government legal requirements also hinder the spread of 3D drug printing [6].
Pharmaceutical 3D printing is young and still evolving. I think that 3D printing will not be able to capture the pharmaceutical market, since Big Pharma is not going to give up. And as already mentioned, in the world there are only two companies aimed at the development of three-dimensional printing of drugs - this is the American company Aprecia Pharmaceuticals and the British company FabRx.