3D print material pla
Ultimate Materials Guide - Tips for 3D Printing with PLA
Overview
Polylactic Acid, commonly known as PLA, is one of the most popular materials used in desktop 3D printing. It is the default filament of choice for most extrusion-based 3D printers because it can be printed at a low temperature and does not require a heated bed. PLA is a great first material to use as you are learning about 3D printing because it is easy to print, very inexpensive, and creates parts that can be used for a wide variety of applications. It is also one of the most environmentally friendly filaments on the market today. Derived from crops such as corn and sugarcane, PLA is renewable and most importantly biodegradable. As a bonus, this also allows the plastic to give off a sweet aroma during printing.
- Low Cost
- Stiff and good strength
- Good dimensional accuracy
- Good shelf life
- Low heat resistance
- Can ooze and may need cooling fans
- Filament can get brittle and break
- Not suitable for outdoors (sunlight exposure)
Hardware Requirements
Before 3D printing with PLA make sure your 3D Printer meets the hardware requirements listed below to ensure the best print quality.
Bed
Temperature: 45-60 °C
Heated Bed Optional
Enclosure not required
Build Surface
Painter’s tape
PEI
Glass plate
Glue stick
Extruder
Temperature: 190-220 °C
No special hot-end required
Cooling
Part Cooling Fan Required
Fan Speed: 100%
Best Practices
These tips will help you reduce the chances of common 3D printing issues associated with PLA such as stringing, oozing, or under-extrusion.
Fine Tune the Retractions to Prevent Oozing
One of the most common problems with PLA is oozing. Since the filament flows relatively easily when compared to the other materials, it has a tendency to continue flowing during travel movements at the end of a segment. This creates strings or hairs on your part, and dialing in your retraction settings is the best way to combat this behavior! Different brands of PLA and different printers may need slightly different retraction settings, so you may need to experiment to find the best value for your printer. Simplify3D added a very useful feature in Version 4.0 that can help with this, by allowing you to quickly try dozens of different settings, and then look at the final part to determine which one worked the best on your specific setup. For example, you could setup two vertical pillars which are printed side-by-side to evaluate stringing when moving back-and-forth between each pillar. Then go to Tools > Variable Settings Wizard and choose how you want to adjust your settings during the print. For example, you could try a different retraction distance for each 20mm section of the print and then pick the value that works best in the end. For more tips on how to reduce stringing and oozing, be sure to check out our Print Quality Guide which contains an entire section dedicated to this issue: How to Reduce Stringing and Oozing.
Optimize Your Cooling Settings
Cooling is one of the most important aspects of printing with PLA. Having a dedicated part cooling fan makes a huge difference in the quality of the printed parts. The freshly extruded plastic needs to cool down below the glass transition temperature as quickly as possible. This will prevent the plastic from stringing and producing other artifacts. We recommend setting the fan to 100% throughout the print, except for the first 1-2 layers where you want to form a strong bond with the print bed. Simplify3D also includes a useful option on the Cooling tab of your process settings that can automatically reduce the print speed for small parts, ensuring that the layers have sufficient time to cool. This can greatly improve the print quality by allowing the layer to solidify before printing the next layer on top of it. This setting can be found on the Speeds tab of your process settings.
Choose the Correct Extruder Temperature
This is a great tip for any filament, but is especially useful for PLA which often contains different combinations of additives depending on the manufacturer. These different additives can lead to variations in printing temperature between 190-230 degrees Celsius. If you are not printing at the right temperature this can lead to several print quality issues including oozing, stringing, and under-extrusion. PLA can also be combined with different fills like metal, wood, and fiber that give it different characteristics than a standard homogeneous PLA. These may require different settings or even different hardware. Be sure to check with the manufacturer of your filament to verify the optimal temperature to use for your specific filament. If you have trouble with stringing, try reducing this temperature by 5-10 degrees, which will help prevent the excess oozing. If you’re struggling with under-extrusion, try increasing the temperature by 10 degrees so that the material flows more easily through the nozzle.
Pro-Tips
- Using a fan that cools the 3D printed part from all directions is highly recommended. Many popular 3D printers have community-designed attachments that can be printed and retrofitted onto your machine to improve the cooling airflow.
- Increasing the number of perimeter outlines for your PLA prints will create a strong bond between each layer, creating stronger parts that are less prone to breaking.
Get Started with PLA
Now that you are ready to start printing with PLA, here’s a bit more information to help you get started. Start thinking of project ideas by reviewing our common applications, try out one of the provided sample projects, or find a new filament to try from our list of popular material brands.
Common Applications
- Test and calibration items
- Dimensionally accurate assemblies
- Decorative Parts
- Cosplay Props
Sample Projects
- LA Spring Motor, Rolling Chassis
- G – Clamp
- Storm Trooper Helmet
Popular Brands
- Polymaker PLA, PolyMax, PolyPlus
- ColorFabb PLA/PHA
- Hatchbox PLA
- eSun PLA
- Filamentum PLA
What is PLA plastic filament and how to use it for 3D printing ?
What is PLA plastic material ? Get all information and advice to help you print your 3D model with filament fabrication, using FDM 3D printing technology. Affordable and reliable, start 3D printing using PLA filament.
Colors
Characteristics
Surface Look
Details
Strength
Flexibility
PLA Filament Material Guide
Overview
Design Guide
Technical Specifications
What is PLA material?
PLA plastic or polylactic acid is a vegetable-based plastic material, which commonly uses cornstarch or sugarcane as a raw material. The monomer is usually made from fermented plant starch. This material is a thermoplastic aliphatic polyester and it is the primary natural raw material used in 3D printing. PLA is a fully biodegradable thermoplastic polymer consisting of renewable raw materials. Among all 3D printing materials, PLA is part of the most popular materials used for additive manufacturing for filament fabrication.
PLA is a bioplastic, used in 3D printing using the FDM (Fused Deposition Modeling) technology, and along with ABS (Acrylonitrile Butadiene Styrene), this material is one of the standard materials for this technology. There is often a tendency to compare these plastic materials, as they are the two most common alternatives available for consumer printers. PLA plastic material is easy-to-use and offer some interesting mechanical properties.
PLA material is printed using BigRep 3D printers and mainly used to manufacture big parts up to 1x1x1m.
Even if this PLA material offers the opportunity to 3D print impressive big parts, please keep in mind that you will have to respect specific design guidelines to avoid any problem during the additive manufacturing process. Be sure to check the material design guidelines while creating your 3D file and before you send it for 3D printing.
If you want to know more about the general properties of PLA filament, you can check our “Technical Specifications” part.
What is PLA plastic used for ?
PLA plastic filament quickly became a popular material due to it being economically produced from renewable resources. PLA plastic material comes in the form of wire on a spool, which is fed into the extruder head where the plastic is melted and deposited in a continuous extrusion on the printing tray. This material is translucent in its natural form, but spools of coloured filament can be used to make objects in different colors.
When cooling, this material shrinks less than ABS, which gives it good geometric stability during the manufacturing process.
PLA can be useful for your product development, as this material can be used for rapid prototyping.
Large-scale 3D printing is the main advantages of the PLA we are offering at Sculpteo, which can be a great benefit for a wide range of applications. This material offers you the possibility to print professional and industrial parts of 1m x 1m x 1m thanks to a large 3D printer! BigRep PLA material, has good strength and stiffness, making this 3D printing material filament is ideal for demanding industrial production. 3Dp BigRep PLA can perfectly be used to 3D print large objects for architecture or construction fields but also for marketing displays, exhibitions or signage.
This 3D printing filament is an affordable and versatile plastic. It can easily be used for prototypes, pattern making, tooling parts, or end-use parts. However, there are still some disadvantages such as photodegradation which is caused by UV radiation if PLA is exposed to sunlight.
We inform you that this material is not suited for applications requiring suitability with high humidity (more than 98%) or high temperatures (above 60°C). Make sure you check the physical mechanical properties of the PLA plastic 3D printing material before.
Pricing for PLA 3D printing filament
To get your PLA parts 3D printed, please contact directly our sales team to place your order. It is not possible to order your parts on the website.
However, the price of the design is calculated on a series of factors, including its size, its volume, and the amount of material needed to manufacture your parts.
Our sales team will keep you updated regarding the price and the shipping time of your parts.
How does FDM 3D printing technology work?
BigRep PLA parts are 3D printed using a traditional FDM 3D printing process. Even if BigRep printers are impressive and big machines, the FDM printing process stays the same. During the FDM 3D printing process, the filament is extruded through a nozzle which melts while being gradually deposited in a structured way on the build platform of the 3D printer until the object is finished.
Colors and Finishings available for PLA plastic material
Your PLA plastic parts can take on a variety of colors with many color options available according to your project specifications. We are also offering Chemical Smoothing and painting options, please contact us to discuss your color and finishing options to your 3D printed PLA parts.
Maximum size
Maximum size | 1 x 1 x 1 m |
The maximum size of your models are limited by the physical size of our 3D printers – nothing can be printed larger than the printer bed. |
Mechanical Properties
Documentation
Filament Sizes: | 2.3, 4.5, and 8.0 kg |
Diameter: | 2.85 mm |
Density: | 1.24 g/cm³ |
Flexural Modulus (ISO 178): | 3800 MPa |
Tensile Strength (ISO 527): | 60 MPa |
Impact Strength Notched: | 7.![]() |
Heat Resistance HDT / B (ISO 75): | 40 °C |
Hardness (Shore): | D 60 |
What does PLA material stand for?
PLA stands for Polylactic acid. It is a thermoplastic monomer derived from renewable, organic sources such as corn starch or sugar cane.
Is PLA plastic biodegradable?
PLA is biodegradable under certain composting conditions. PLA is still a plastic material and requires a laundry list of conditions to effectively break down.
Is PLA actually plastic?
PLA is a plastic material. PLA is made from a biomass resource, it is a vegetable-based plastic material, which commonly uses cornstarch as a raw material.
Is ABS or PLA better for 3D printing?
PLA is a perfect material if you need to 3D print parts where aesthetics is important. ABS is a good material for applications where strength, ductility, machinability and thermal stability are required.
Related blog posts:
Ready to 3D print with PLA plastic material?
With Sculpteo’s online 3D printing service you’re just a few clicks away from professional PLA 3D printing. Your 3D model is printed with the highest quality and delivered straight to your door.
Get started now to get your PLA prints!
Discover our other plastic materials...
PLA plastic for 3D printing
- 1 Plastic composition
- 2 PLA safety
- 3 PLA Specifications
- 4 Advantages of PLA in 3D printing
- 5 Navigation
PLA-plastic (polylactide, PLA) - is a biodegradable, biocompatible, thermoplastic aliphatic polyester, the structural unit of which is lactic acid. nine0018
PLA is made from corn or sugar cane.
Potato and corn starch, soy protein, cassava tubers, cellulose are also used as raw materials.
Today, polylactide is actively used as a consumable for printing on 3D printers.
Natural raw materials in the composition of PLA-plastic allows using it for various purposes without a threat to human health. nine0018
The production of PLA plastic significantly reduces carbon dioxide emissions into the atmosphere compared to the production of "petroleum" polymers. The use of fossil resources is reduced by a third, the use of solvents is not required at all.
PLA is usually supplied as a thin filament that is wound on a spool.
Melting point | 173-178°C |
Softening point | 50°C |
Hardness (Rockwell) | R70-R90 |
Elongation at break | 3.![]() |
Flexural strength | 55.3 MPa |
Tensile strength | 57.8 MPa |
Tensile modulus | 3.3 GPa |
Flexural modulus | 2.3 GPa |
Glass transition temperature | 60-65°C |
Density | 1.23-1.25 g/cm³ |
Minimum wall thickness | 1 mm |
Print Precision | ± 0.1% |
Micron size | 0.3 mm |
Manufacturing shrinkage | no |
Moisture absorption | 0.5-50% |
- non-toxic;
- wide color palette;
- when printing, no need for a heated platform;
- dimensions are stable;
- is ideal for moving parts and mechanical models; nine0004
- excellent sliding of details;
- savings in energy costs due to the low softening temperature of the yarn;
- no need to use Kapton to lubricate the surface for building up the prototype;
- smoothness of the surface of the printed product;
- obtaining more detailed and completely ready-to-use objects.
PLA plastic is ideal for 3D printing objects with great detail
Work with PLA plastic on a 3D printer is carried out using FDM-Fused Deposition Modeling technology. The thread is melted, after which it is delivered through a special nozzle to the surface for work and is deposited. As a result of building a model with molten plastic, an object completely ready for use is created. Products made of PLA plastic are subjected to grinding and drilling, painted with acrylic. However, it is worth remembering that the item made of PLA must be handled with care due to its fragility. Another disadvantage of PLA plastic is its fragility: the material lasts from several months to several years. nine0018
PLA is an ideal material for 3D printing prototypes and products that are not expected to be used for a long time. These can be decorative objects, presentation items, and items that require meticulous detailing.
Go to the main page of Encyclopedia of 3D printing
types, applications and properties
3D printing enables fast and cost-effective prototyping and production of models for a wide range of applications. But choosing the right 3D printing technology is only one side of the coin. Ultimately, the ability to create models with the required mechanical properties, functional characteristics or appearance will depend on the materials. nine0018
This comprehensive guide provides information on the most popular plastic and metal 3D printing materials available, compares their properties and applications, and provides guidance on how to select the most suitable material for your project.
Interactive Material
Need help choosing your 3D printing material? Our new interactive materials wizard will help you select the right material from our growing range of polymers, based on your intended application and the properties that matter most to you. nine0018
Get material recommendations
Dozens of plastic materials are available for 3D printing. Each of them has unique properties suitable for specific applications. To make it easier to find the best material for a particular model or product, let's first look at the main types of plastics and the various 3D printing processes.
There are two main types of plastics:
-
thermoplastics are the most common type of plastics. The main feature that distinguishes them from thermosetting plastics is their ability to withstand multiple melting and solidification cycles. Thermoplastics can be heated and shaped into desired shapes. This process is reversible because no chemical bond is formed. As a result, they can be recycled or melted down and reused. Thermoplastics can be compared to butter: it melts and hardens many times. With each melting cycle, the properties of thermoplastics change slightly. nine0018
-
thermoset plastics (also called thermosets) remain permanently solid after polymerization. The polymers in thermosetting plastics are crosslinked during the polymerization process, which is induced by heat, light, or appropriate radiation.
Thermoset plastics decompose when heated, rather than melt. In addition, they do not change their shape when cooled. It is not possible to recycle thermosetting plastics or restore the material to its original state. Thermosetting is like pie dough: once baked, the pie cannot be melted back into dough. nine0018
The three most common plastic 3D printing processes today are:
-
Fused Deposition Modeling (FDM) 3D printers melt and extrude thermoplastic filaments, which the printer nozzle deposits layer by layer on the work area.
-
The Stereolithography (SLA) 3D Printer uses a laser to photopolymerize thermoset liquid polymers into a hardened plastic. nine0018
-
The Selective Laser Sintering (SLS) 3D Printer is equipped with a high power laser to sinter fine particles of thermoplastic powder.
How-to video
Can't find the 3D printing technology that best suits your needs? In this video tutorial, we compare Fused Deposition Modeling (FDM), Stereolithography (SLA), and Selective Laser Sintering (SLS) technologies in terms of the top factors to consider when purchasing. nine0018
Watch video
Fused fusion modeling (FDM), also known as fused filament manufacturing (FFF), is the most common form of consumer grade 3D printing, fueled by the proliferation of hobbyist 3D printers.
This method is well suited for making basic experimental models, as well as for quickly and inexpensively prototyping simple products, such as parts that are usually machined. nine0018
Consumer-grade FDM has the lowest resolution and accuracy of any plastic 3D printing process, making it unsuitable for printing complex designs or models with intricate features. It is possible to improve the surface quality of models printed using this technology using chemical and mechanical polishing processes. FDM-based industrial 3D printers, which offer a wider range of engineering thermoplastics, can solve these problems, but are also much more expensive. nine0018
Each layer is formed with a thermoplastic thread. Sometimes, if the layers are not completely adjacent to each other, there may be voids between them. As a result, anisotropic models are obtained, which is important to consider when designing products that must withstand load and be resistant to tension.
FDM 3D printing materials are available in a variety of colors. There are also various experimental mixtures of thermoplastic threads designed to create models with a surface that mimics wood or metal. nine0018
The most common FDM 3D printing materials are ABS (acrylonitrile butadiene styrene), PLA (polylactic acid) and various blends of these polymers. More advanced FDM printers can also print on other materials with different properties, such as increased temperature and chemical resistance, impact resistance, and rigidity.
Material | Features | Conceptual models Realistic prototypes |
---|---|---|
PETG (polyethylenertalatlatglycol) | is compatible with low production temperatures 9008.![]() | Waterproof application Clip-on components |
nylon | hard, durable and light strong and partially flexible heat -resistant and shockproof Complex for printing using FDM | Functional Prototypes Bastens -resistant models |
TPU (thermal poliuretan) | 902 902 902 902 902 902 9003 Excellent vibration dampingFlexible Prototypes | |
PVA (polyvinyl alcohol) | Soluble support structure material The material for supporting structures | |
impact -resistant polystyrene | The material for creating soluble supporting structures, most frequently used with ABS | material for supporting structures |
compositions is dissolved in water. Kevlar, fiber optic) | Strong, tough and incredibly hard Only compatible with some expensive industrial 3D printers based on FDM technology | Functional prototypes Clamping fixtures, fixtures, tooling |
Invented in the 1980s, stereolithography is the world's first 3D printing technology and is still one of the most popular among professionals today.
Models printed with stereolithography printers have the highest resolution and accuracy, the finest detail, and the smoothest surface of any other plastic 3D printing technology. Resin 3D printing is a great option for producing highly detailed prototypes that require tight tolerances and smooth surfaces such as molds, templates, and functional models. Models printed using SLA technology can be easily polished and/or painted after printing, resulting in highly detailed finished products. nine0018
3D printed SLA models are generally isotropic: their strength is more or less constant and independent of orientation, since chemical bonds are created between each layer. This results in models with predictable mechanical characteristics critical for applications such as fasteners, fixtures, finished products, and functional prototypes.
Stereolithography supports a wide range of plastic 3D printing materials. nine0018
SLA 3D printing is versatile and provides a wide range of optical, mechanical and thermal properties that match those of standard, engineering and industrial thermoplastics.
Materials of Formlabs | Characteristics | Methods of use |
---|---|---|
Standard polymers | High resolution Glavoe, matte surface | Concredity.0014 Realistic prototypes |
Clear Resin | The only truly transparent material for 3D printing from plastics can be polished to almost full optical transparency | Models | One of the fastest 3D printing materials Prints 4x faster than standard resins and 10x faster than FDM | Initial prototypes Rapid iterations |
Tough Resin and Durable Resin | Materials that are tough, strong, functional and dynamic Can withstand compression, tension, bending and impact without breaking Various materials with properties similar to ABS | Enclosures and Enclosures Clamps and Fixings Connectors Wear Prototypes |
Rigid Resins | Highly filled, rigid and strong material, resistant to bending Resistant to temperature and chemicals Holds size under load | Clamping and clamping fixtures, tooling Turbines and fan blades Fluid/air components Electrical enclosures and enclosures used in the automotive industry |
High Temp Resin | High temperature resistant High Precision | Hot Air, Gas, and Liquid Components Heat Resistant Fasteners, Enclosures, and Fixtures Molds and Inserts |
Flexible Resin and Elastic Resin | Flexibility of Rubber, TPU, or Silicone compression Withstands many successive cycles without wear | Consumer Prototypes Foldable Structures for Robotics Medical Devices and Anatomy Models Props and models for special effects |
Medical and dental resins | A wide range of biocompatible resins for the manufacture of medical and dental products | Dental and medical products, including surgical templates, dentures and prosthetic limbs | Lost wax and vulcanized rubber casting materials Easy to cast with intricate features and good shape retention | Products for trying on Models for reusable press forms Jewelry to order |
Ceramic Resin | Surgery, similar to a fire of firing for creating a real ceramic product | Technical search 9001 9001 9001 9 |
Sample
Experience Formlabs print quality for yourself. We will send a free print sample directly to your office. nine0018
Request a free sample
Selective laser sintering (SLS) 3D printing is a technology trusted by engineers and manufacturers across industries to create durable and functional models. With its low model cost, high performance, and use of common materials, this technology is well suited for a wide range of applications, from rapid prototyping to low-volume production, limited trial runs, or custom-made products. nine0018
The green powder supports the model during printing and eliminates the need for special support structures. As a result, SLS is ideal for complex geometries, including internal features, undercuts, thin walls, and negative draft features.
Like stereolithography, SLS produces more isotropic models than FDM models. Models created with SLS technology have a slightly rough surface due to powder particles, but have almost no visible layer lines. nine0018
SLS 3D printing materials are ideal for a range of functional applications, from consumer product design to manufacturing and healthcare applications.
Compared to FDM and SLA technologies, SLS technology allows the use of a limited number of materials. However, the available materials have excellent mechanical properties. They have strength comparable to die-cast models. The most common selective laser sintering material is nylon, a popular engineering thermoplastic with excellent mechanical properties. Nylon is light, strong and flexible, resistant to impact, heat, chemicals, UV radiation, water and dirt. nine0038
Products for the final use of
Medical devices
resistant to deformation
High resistance to ultraviolet
Excellent damping capacity
Medical devices
End-Use Structural Products
Sample
Experience Formlabs SLS print quality for yourself. We will send a free print sample directly to your office.
Request a Free Sample
Different 3D printing materials and processes have their own advantages and disadvantages that make them suitable for different scenarios. The following table provides a brief overview of some of the main features and factors to consider. nine0038
Poor detail
Limited fit to design
High cost of industrial devices if precision and high performance materials are required
Basic experimental models
Production of special end-use products using professional industrial devices and materials
Templates, molds and tooling
Dental products
Prototypes and molds for casting jewelry
Props and models
Small-scale production, production of limited trial runs, creation of products to order
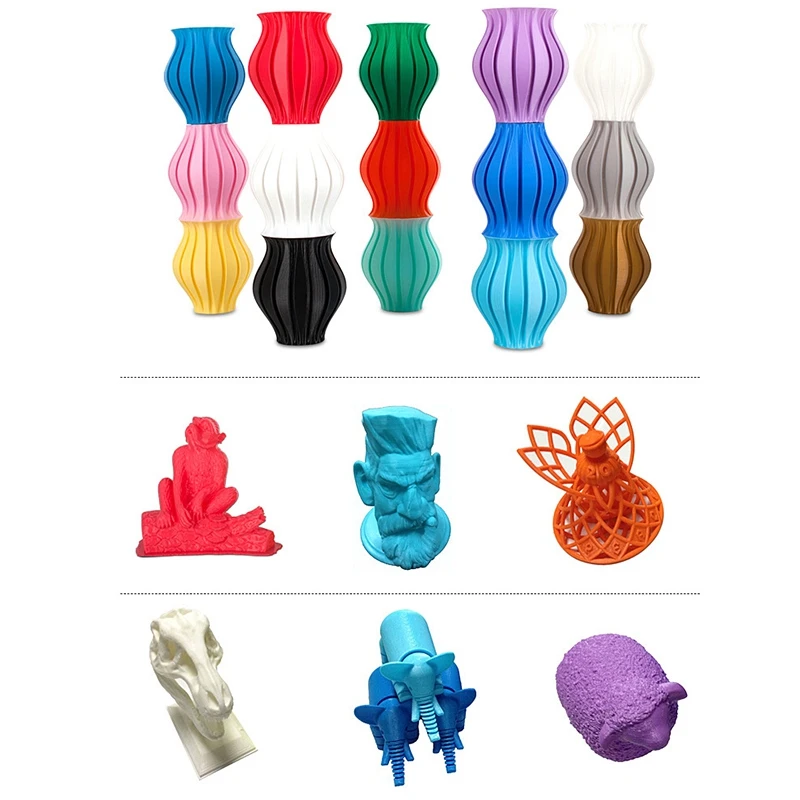
There are several 3D printing processes not only from plastics, but also from metals.
Metal FDM printers are similar in design to traditional FDM printers, but use extruded metal rods held together by a resin binder. The finished models are in an intermediate state and then sintered in an oven to remove the binder.
SLM and DMLS printers are similar to SLS printers, but instead of polymer powders, they fuse metal powder particles layer by layer using a laser. 3D printers based on SLM and DMLS technologies can create strong, precise and complex metal products, making this process ideal for the aerospace, automotive and medical industries.
-
Titanium is a light metal with excellent mechanical properties. It is strong, hard and highly resistant to heat, oxidation and acids. nine0018
-
stainless steel has high strength, ductility and corrosion resistance.
-
Aluminum is a lightweight, durable, strong metal with good thermal properties.
-
Tool Steel is a hard, scratch-resistant material that can be used to print end-use tools and other high-strength products. nine0018
- nickel alloys have high tensile, creep and tensile strength, as well as heat and corrosion resistance.
Compared to plastic 3D printing technologies, metal 3D printing is much more expensive and difficult, and therefore beyond the reach of most companies.
As an alternative to casting workflows that produce metal models cheaper and faster than traditional methods and provide greater design freedom, SLA 3D printing is well suited. nine0018
Another alternative is galvanization of SLA printed models. It involves applying a layer of metal to plastic using electrolysis. This combines some of the best qualities of metal (strength, electrical conductivity, corrosion and abrasion resistance) with the special properties of the base (usually plastic) material.
Plastic 3D printing is well suited for creating templates that can be cast to produce metal models. nine0018
There are so many materials and 3D printing options available, making the right choice can be difficult.
We offer a 3-step process for selecting the right material for 3D printing.
Plastics used for 3D printing have different chemical, optical, mechanical and thermal characteristics that affect the properties of 3D printed models. As you move from the intended use case to the actual operating environment, the performance requirements increase accordingly. nine0018
Requirement | Description | Recommendations |
---|---|---|
Low Efficiency | Example: Prototype mold for a ladle for ergonomic testing. | FDM PLA SLA: Standard Resins, Clear Resin (transparency), Draft Resin (fast) |
Medium Efficiency | For validation or pre-production use, printed models should have properties as close as possible to those of final production models , for functional testing, but do not meet stringent requirements regarding service life. Example: housing for electronic components to protect against sudden impacts. Functional characteristics include the ability to absorb impact energy. In addition, the body must snap into place and retain its shape. nine0018 | FDM ABS SLA: Engineering Resins SLS: Nylon 11 Powder, Nylon 12 Powder, TPU |
High Efficiency | Final 3D printed models must be highly stable in order to produce products for end use to wear and tear over a certain period of time, whether it be a day, a week or several years.![]() Example: shoe soles. Functional features include rigorous cycling and unloading life testing, color fastness over many years, and tear resistance, among other things. nine0018 | FDM Composites SLA: Engineering, Medical, Dental or Jewelry Resins SLS: Nylon 11 Powder, Nylon 12 Powder, TPU, Nylon Composites |
material requirements: material properties that will satisfy these requirements. These indicators are usually given in the technical specifications of the material. nine0018
Requirement | Description | Recommendation | |
---|---|---|---|
Tensile strength | Material resistance to fracture under tension. High tensile strength is important for structural, load-bearing, mechanical or static models. | FDM PLA SLA: Clear Resin, Rigid Resin SLS: Nylon 12 Powder, Nylon Composites | |
Flex Module | Material resistance to bending under load.![]() | FDM PLA (High), ABS (Medium) SLA: Rigid Resin (High), Tough Resin and Durable Resin (Medium), Flexible Resin and Elastic Resin (Low) SLS: Nylon composite materials (high value), Nylon 12 Powder (medium value) | |
Elongation | Material resistance to tensile failure. Allows you to compare the degree of stretching of flexible materials. It also indicates whether the material is stretched or immediately destroyed. nine0038 | FDM ABS (medium), TPU (high) SLA: Tough Resin and Durable Resin (medium), Flexible Resin and Elastic Resin (high) SLS: Nylon 12 Powder (medium), Nylon 11 Powder (Medium), TPU (High) | |
Impact Strength | The ability of a material to absorb impact and its energy without breaking. Shows toughness and durability. Allows you to determine how easily the material breaks when it falls to the ground or collides with another object.![]() | FDM ABS, Nylon SLA: Tough 2000 Resin, Tough 1500 Resin, Gray Pro Resin, Durable Resin SLS: Nylon 12 Powder, Nylon 11 Powder a certain load. Indicates whether the material is suitable for high temperature applications. | SLA: High Temp Resin, Rigid Resin SLS: Nylon 12 Powder, Nylon composites |
Hardness (durometer) | Material resistance to surface deformation. Allows you to determine the right degree of plasticity for soft plastics such as rubber and elastomers for a particular application. | FDM TPU SLA: Flexible Resin, Elastic Resin SLS: TPU | |
Tear resistance | Material resistance to notching under tension. This indicator is important for evaluating the durability and wear resistance of soft plastics and flexible materials such as rubber. nine0038 | FDM TPU SLA: Flexible Resin, Elastic Resin, Durable Resin SLS: Nylon 11 Powder, TPU | |
Creep | Creep is the tendency of a material to permanently deform under the influence of constant stress: tension or bending, compression, shear .![]() | FDM ABS SLA: Rigid Resin SLS: Nylon 12 Powder, Nylon 9 composites0038 | |
Compression set | Irreversible deformation after material compression. An important indicator for soft plastics and applications where elasticity is needed. Indicates whether the material will restore its original shape after the load is removed. | FDM TPU SLA: Flexible Resin, Elastic Resin SLS: TPU |
For more information on material properties, see our guide to the most common mechanical and thermal properties. nine0018
By converting performance characteristics into material requirements, you can most likely find out which material, or small group of materials, is right for your application.
If several materials meet your basic requirements, a broader range of desired characteristics, as well as the advantages and disadvantages of these materials and processes, can be considered for the final selection.