Water jet 3d printer
Wematter Launches New Water-Jet Cabinet For Faster Post-Processing Of 3D-Prints
A design change in the new density is the protective hatch that opens from the front/Image Source: WematterWematter recently announced the launch of The Density 2021 Gen II, a part of Wematter’s ecosystem for additive manufacturing, which reduces the time it takes to go from a 3D-printed part to a finished end product.
After taking a holistic approach to exterior design, functionality, and reliability, the company looked inside its machine to present the next generation of the water-jet cabinet Density 2021 that makes the cleaning process in AM shorter.
Shorter cleaning after every print job avoids bottlenecks in the 3D printing production. With Density, the user post-processes printed parts with water and compressed air, helping to reduce post-print cycle times, enhancing productivity.
A quick and safe post-processing method
The new changes, at their core, still use high-pressure water to treat powder-based 3D prints after printing. This is a method that is gentle compared to other AM blasting techniques to avoid affecting the surface structure of the prints. This unique offering is enhanced by a new feature for quickly testing prints after water blasting by selecting the Density’s drying feature, utilizing a compressed air gun.
“This new model has not only taken the machine’s visual design to the next level; the changes to Density 2021 Gen II also improve the user’s workflow while significantly reducing maintenance for each unit,” explains Robert Kniola, Founder, and CEO of Wematter.
After water blasting and drying with compressed air, the 3D prints are ready to use/Image Source: Wematter“By first using water to remove excess material with Density, you can clean 3D models quickly and safely compared to using only compressed air. In comparative tests, we have in some cases measured a reduction in the finishing time by up to 83%. From one hour to ten minutes per batch of 3D prints “, continues Robert Kniola.
A versatile solution for several manufacturing techniques
Another advantage of the ecosystem is that it is easy to install, which still applies to Density Gen II. The water recirculates in a closed system. This means that you do not need access to a drain or external water connection. The compressed air is driven by an integrated compressor and Density connects to a standard wall socket, meaning that you can place it almost anywhere to really decentralize AM in organizations.
“The versatility makes Density 2021 Gen II the obvious post-processing choice for 3D printers. Regardless of whether you are cleaning powder in the Powder Bed Fusion segment or removing wax from a PolyJet-printed part. Or even removing soluble support structure such as polyvinyl acrylate from an FDM print”, concludes Robert Kniola.
Some of the new features in the Density 2021 Gen II
- Ergonomic hatch for loading 3D-prints with a dome of impact-resistant glass.
You open it from the front and a gas spring holds it up conveniently
- A larger protective window that lets in more light and provides better visibility
- A larger filter that collects more excess powder before it saturates. Placed inside the chamber which facilitates filter replacement and maintenance
- Larger chamber volume that provides increased water capacity, including visual flood protection. This enables larger and more 3D prints per job
- Integrated compressed air activated at the touch of a button. Used to dry prints faster or to blow away residual powder in cavities
- Gloves in a new position and with a new shape. Allows users of varying heights to find a comfortable working posture
- Fully cast cleaning chamber with continuous sweeping surfaces together with a dehumidification system for a hygienic environment
Density 2021 Gen II will be available as a part of the Gravity SLS ecosystem which is rented via a monthly subscription but also as a stand-alone solution for companies who want to complement their existing 3D-printing post-processing.
About Manufactur3D Magazine: Manufactur3D is an online magazine on 3D Printing. Visit our Global News page for more updates on Global 3D Printing News. To stay up-to-date about the latest happenings in the 3D printing world, like us on Facebook or follow us on LinkedIn and Twitter.
Wazer — World’s First Workbench Water Jet Cutter
Wazer is the world’s first workbench water jet cutter. It has brought the power of water within everyone’s reach.
We like to tout 3D printing as an up-and-coming replacement for traditional CNC machining. Although additive manufacturing can significantly lower costs and lead times when compared to CNC, it’s not always a perfect solution.
And that’s where the problem lies for smaller manufacturers. CNC machines are often prohibitively expensive for small operations, never mind their usually massive sizes.
This was the story for water jet cutting, as well. It’s a powerful technology for cutting parts out of extremely hard materials, but the size and price of a water jet cutter is far beyond the scope of a small business.
At least that was the case until 2016 when Wazer was introduced. Here we’ll take a look at what Wazer is and how it’s revolutionising small-scale manufacturing.
What is Wazer?
As we mentioned, Wazer is the world’s first workbench-sized water jet cutting machine. It launched on Kickstarter in 2016 (where it surpassed its $100,000 funding goal by $1.2 million), and a commercial global launched followed in 2019.
The U.S.-based company behind the machine — also called Wazer — created it with a single goal: to make water jet cutting affordable and available for even small enterprises. With Wazer, they’ve definitely delivered.
There were, of course, laser-based cutters available earlier, but they were only able to cut soft materials. But for harder materials, like metal or stone, the only options available for small businesses were time-consuming and inaccurate manual tools.
Enter Wazer. This small water jet cutter, with a footprint of only 86.4 x 63.5 x 53.4 cm, fits on a regular workbench and can cut through virtually any material. With a cut width of only 1.2 mm, it creates finely detailed, high-quality cut-outs.
How Does It Work?
Wazer works with the same principle as its humongous cousins. First, the operator must prepare a cutting template. Wazer supports DXF and SVG files, which means you can draw the shape template with practically any free or commercial vector-based graphics editor.
Once you have your shape file, you’ll upload it to Wazer’s web-based preparation software that works with any popular browser. The application is user-friendly and simple, and allows the file to be properly scaled and prepared in a few minutes. When you’re ready, simply hit the start button.
Wazer blows a stream of high-pressure water through a nozzle. But despite the technology’s name, it’s not just water that does the cutting. Just as with a larger cutter, Wazer mixes an abrasive material into the water stream that slices through the material.
The abrasive that Wazer uses is garnet, a silicate mineral that’s been ground into a fine, consistent particle size. Garnet is non-toxic and easy to dispose of, thanks to Wazer’s integrated abrasive collection tank. You should note, though, that the abrasive is not recyclable at the moment.
What are the benefits?
- Availability: The single largest benefit Wazer brings to small manufacturing businesses is that it makes in-house water jet cutting available for them in the first place. Before Wazer, it simply wasn’t an option.
- Size: Wazer’s compact size allows manufacturers to have their own water jet cutting machine even in a small workshop. If you don’t have a workbench available, Wazer also offers a sturdy floor stand for the machine.
- Cost: Wazer costs only a fraction of an industrial water cutter’s price. You’ll also save on outsourcing costs, since you can now cut your parts in your own workshop.
The only running costs are water, electricity, abrasive, and the materials.
- Production flexibility: Wazer opens a new realm of opportunity for small-scale manufacturers. It can easily cut out, among other things, spare parts, decorative tiles, or flat sculptures.
- Ease of use: A large water jet cutter requires extensive maintenance and an entire crew to carry out the work. With Wazer, a single operator can both run and maintain the machine.
- Material range: Simply put, Wazer cuts through practically anything. The manufacturer highlights the mini water cutter’s ability to slice stainless steel, marble, glass, HDPE plastic, carbon fibre, and silicone, but you’ll probably be able to cut any material as long as it’s not too thick.
Are there any limitations?
Make no mistake, Wazer is a revolutionary machine for small-scale manufacturing. But in the name of honesty, the tiny form factor does somewhat limit its suitability for some applications.
The incredible cutting power of industrial-scale water jet cutters comes from their powerful pumps that squirt out a stream at pressures reaching even hundreds of thousands of PSI. Of course, you can’t physically fit such a strong pump in a machine of Wazer’s size. That puts an upper limit on how thick the material to be cut can be.
Due to the lower water pressure, Wazer also won’t cut as fast as its giant brethren. And since the machine is small, it naturally can’t produce enormous parts. Wazer’s maximum cutting area is 30.5 x 46 cm. Finally, it can’t produce layered structures, but that applies to any water jet cutter.
These aren’t real issues, though. Small-scale operators probably won’t be cutting two-inch thick steel in the first place, and we doubt anyone would expect to fit a machine capable of such feats in a regular workshop. Besides, comparing Wazer to full-sized cutters isn’t really fair in the first place.
Wazer’s size has its limitations, but when the other option is not having a water cutter at all, it really doesn’t matter.
Is this the right machine for me?
Whether you should consider purchasing a Wazer for your operation comes down to one question: do you regularly need small water jet-cut parts? If you answered yes, you can’t go wrong with the machine.
Granted, Wazer does cost a bit more than similarly sized 3D printers or CNC milling machines. That said, water jet cutting isn’t really a comparable technology, and the costs you save on outsourcing will quickly return the investment.
Wazer is a flexible small water jet cutting machine that helps any manufacturer expand their product catalogue and potentially break into entirely new industries. The world’s first desktop water jet cutter proves that good things really do come in small packages.
Are you interested in Wazer and the opportunities it creates? Our team at Solid Print is to tell you more. Call us on 01926 333 777 or email us at [email protected].
how we taught 3D printers to print complex parts more economically and twice as fast .
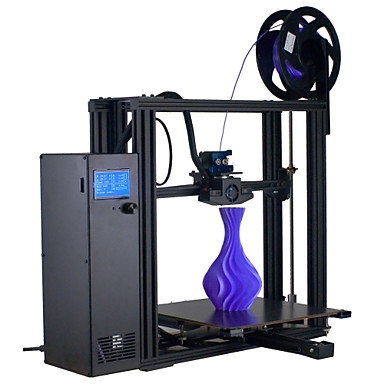
6871 views
What is the idea
The most popular FDM 3D printers print the parts layer by layer. At the same time, in 70% of cases, “hinged” elements appear during printing - fragments that do not have support under them and hang over the desktop like visors. To fix such details, it is necessary to print special supporting structures (they can take up to 50% of the material).
In addition, after printing, these supports must be removed: such processing is often time consuming and not always safe - the part may break in the hands due to insufficient strength, and then everything will have to be redone. And some designs are simply impossible to produce using this method: the supports will fill almost the entire space of the part.
I saw a solution that avoids this problem in the field of metalworking - five-axis milling machines have been used there for a long time. The idea is to equip the 3D printer with a turntable: with its help, the body of the model is always positioned during printing so that each subsequent layer is built based on the already printed elements of the model.
Five Axis 3D Printer
Why do we need a five-axis 3D printer and who are our customers
The 5-axis 3D printer allows you to print complex parts quickly without wasting material on supporting structures and saving time in post-processing. In essence, we allow you to reduce costs and increase productivity: according to our estimates, one machine can replace two previous generation 3D printers.
The 5-axis printer allows you to print parts with complex geometries, such as live piping layouts that companies need during the design phase. Printing this on a conventional 3D printer will not work, and creating it using conventional methods will take a lot of time and effort. In addition, products printed on a five-axis printer are much stronger than conventional ones. When printing, new layers of matter are not just layered on top of each other, but are printed "overlapped" at different angles - it is much more difficult to break such details.
Of course, not everyone needs to print complex and durable products: potential buyers of the Epit 5.1 5-axis 3D printer are 3D printing service companies, industrial design studios and design departments of manufacturing enterprises. That is, our machine is needed specifically for industrial use.
How we got into this topic
Seven years ago I worked in a company that produced plastic automotive components, responsible for marketing and creating new business lines.
Back then, for one of the projects, it was necessary to make a prototype of a new part: it was expensive and time consuming to do it with traditional methods (I would have to create a mold), so I decided to contact a company that was engaged in 3D printing. At that time, this direction was on the hype, and everyone talked about the fact that soon 3D printers would be in every kitchen and garage.
But the reality turned out to be completely discouraging. With our task, we turned to several companies that were engaged in 3D printing in Naberezhnye Chelny, but no one was able to make the part according to our request: it turned out to be too complicated.
Since I am a designer by education, I began to think and look for solutions to the problem myself - and did not find anything similar on the market.
Creating a team proved to be more difficult than finding funding. Initially, I focused on the "iron" component of the project and did not think about the software that is necessary for the efficient operation of a 3D printer, so I began to look for developers.
An expert I knew then told me: “You need people who, like you, do not understand what they are getting into” - because developing software for such a printer turned out to be a rather specific and long task.
I began to apply to the universities of Tatarstan and neighboring regions - to look for students who are ready to take on a non-trivial task. But the students who responded could not move forward in the solution, and as a result, I found Mikhail Ivanov in Innopolis, who became a developer and my partner in a startup.
The second person who was needed in our business was someone who understands electronics, a specialist in the field of digital program management. Unlike a programmer, such a specialist cannot work remotely, so I was looking for a person in Naberezhnye Chelny.
Having spent a lot of effort and nerves, I found only two people who had the necessary level of knowledge and were able to realize my ideas, and fortunately one of them, Pavel Kozhevnikov, took up the project.
Getting funding, finding a team, and working on a printer went gradually - and in April of this year we created an MVP.
What we are doing now
In the spring of 2020, we entered the Pulsar Venture Capital accelerator and are now working on a project together with the company's experts. Acceleration made me run faster, spend even more time on the project, and constantly refine something.
On the other hand, due to quarantine, we work remotely, and for me it turned out to be even more convenient - I stayed in the familiar atmosphere with the opportunity to work on the product.
Now we have a finished product, the first pre-orders for it, and an understanding of how we will bring it to the market, how to position it. In addition, during the acceleration we have expanded the horizons of thinking and now we are looking not only at Russia, but also at the global market - this has ceased to seem like an impossible task.
We assessed the economics of the business and set the price for the printer at around $7,000, which is an adequate price for a printer with such a wide range of capabilities, because it allows you to get prototypes of products quickly and with high quality.
I see how 3D printer owners are increasingly thinking about equipment efficiency and the ability to do more. In response to these requests, in recent years, the number of developments in the field of creating a new generation of 3D printers has been growing, and this is encouraging - it means that the topic is really in demand and the market will actively develop.
For example, the scientific community is working on the creation of algorithms and principles for processing models. A new generation of 3D printers is being made by our competitors from Europe and Asia, but so far they have not announced the launch of mass production.
Therefore, it will be great if we, Russian companies, manage to become market leaders in the creation of third-generation 3D printers that can work even more efficiently and change attitudes towards additive manufacturing.
STL file 80MM WATER JET PROPULSION ・3D printing template to download・Cults
Share Add to ?Quality of creation: 4.1/5 (15 votevotes)
Ratings of participants on printability, usefulness, level of detail, etc.
- 👁 32.9k views
- ♥ 33 i like s
- 188 downloads
- 35 comments
- 0 makes
3D model description
My 80mm jet propulsion design for big rc boats, kayaks, jet surf, small boats. ..Great high angle design, low drag for maximum water flow, high or low angle of attack impellers (two options - stl for both included). Great water cooling system for motor and esque (you don't need an extra water pump). The shaft sits on 3 bearings for better stability. With brass inserts that are very easy to insert with a soldering iron. You can choose between a conventional diffuser or a steering diffuser. The wall thickness is 3 mm, which makes the construction very durable.
Easy to print (solid parts made of PLA, spacers made of flexible material). All you need to assemble:
-3x skateboard bearing (8mm ID, 22mm OD, 7mm thick),
-2x lip seal (same size as bearing),
-13x-7mm brass threaded insert M4,
-8x bolt M4,
-2x nut m4,
-2x knurled screw,
-2x brass fitting for water cooling - thread 10 mm,
2 -1x shaft length 2 -50 mm 8 mm thick,
-1x 24mm thick M8 nut that is inserted into the 6-blade impeller during the printing process.
You can watch a demo video of this inkjet here (I only used a 6s battery in this video) :
https://www.youtube.com/watch?v=PgiL3OGt4yM
A new version is out! : https://www.youtube.com/watch?v=BY_GGa0Qc6o
Tips:
3 vane impeller - when fully unsealed ream the two holes with a 4mm drill and make an M5 thread with a hand tap. Then insert an M5 concave end bolt on each side. When using this impeller you will need a 250mm shaft with two holes 2.5mm deep. The first hole is located 40 mm from the end of the shaft, and the second - 73 mm from the end. The holes are rotated by 180° (each on one side, like on an impeller). Line up the holes on the impeller and on the shaft and tighten the concave bolts to secure the impeller in place.
6-blade impeller - first calculate the time to print an unfinished impeller. This is the time when you press the pause button and stop printing the finished impeller. During this time, you should insert the M8 nut inside (it should fit snugly. If it is too tight, heat the nut with a soldering iron to make it easier to insert). When the nut is in, just keep printing. For this impeller you will need a 250mm shaft with a 70mm thread on one end. you just screw the impeller onto the shaft.
If possible, use reinforced PLA for the impeller.
Bearings and lip seal - simply press them in (bearing first, then lip seal).
Shaft - should be as straight as possible. Any vibration will heat up the bearings. It is best if it is made of inox.
If anyone needs a carbon fiber impeller with a stainless steel shaft or an impeller for this unit, please send a message to: [email protected].
3D print settings
Filling of all hard parts: 100%
Filling for seals: 15%
Supports: not needed: for impellers and gaskets picture printed 0.3 mm)
Temperature: PLA 205C, Flex 230C
3D Printer File Information
- 3D Design Format : STL Folder details close
- 3 BLADE IMPELLER.
stl
- 6 BLADE IMPELLER-FULL.stl
- 6 BLADE IMPELLER- TIME CALCULATION.stl
- DIFUSOR.stl
- GASKET.stl
- MAIN HOUSING.stl
- MAIN STEERING DIFUSOR.stl
- STEERING DIFUSOR.stl
- STEERING LEVER.stl
- motor mount 56114.stl
Find out more about
formats - 3 BLADE IMPELLER.
- Last update : 2021-01-17 19:35
- Publication date : 2020-08-16 10:46
Copyright
©
Tags
Author
designs 16
Downloads 407
Liked designs four Subscribers 49
Contact
Water Jet Propulsion Pump Unit Hamilton Water Jet Thruster 50mm
8,70 €
WATER JET PROPULSION UNIT SMALLER MAIN HOUSING 80MM- FOR ENDER 3
€4. 70
APPLE PEELER
9,99 €
3 BLADE IMPELLER FOR JET PUMP UNIT- 90MM
9,99 €
3 BLADE IMPELLER FOR JET PUMP UNIT- 100mm
9,99 €
3 BLADE IMPELLER FOR JET PUMP UNIT- 80MM
9,99 €
3 BLADE IMPELLER FOR JET PUMP UNIT- 70MM
9,99 €
IMPELLER FOR PROPULSION UNIT 80MM
9 €
Best 3D Printer Files in the Gadget Category
Jedi flashlight-lightsaber
Free
Iron Man Mark 5 Helmet
Free
Gear key
5 €
Camera suiveuse pliable parapente
Free
De Havilland Canada Dash 8 Q400 - 1:100
6.25 €
Four Swords
Free
UNU R10'5 26X31 - electric guitar pick
Free
Halloween Can Holder
2,80 €
Bestsellers in the Gadget category
Case for iPhone 14 PRO MAX
0. 73 €
Zhiromat
3.05 €
Working steam engine, printed on site, fully assembled, no supports
3.36 €
Brush conditioner
2.24 €
CYLINDER WALL/PISTON 2-STROKE
0,92 €
Karambit keychain spinner tiktok keyrambit NO BEARING
€1.72 -fifteen% 1.46 €
Owl - wall key holder
1.83 €
Missiles Launcher Pen & Pencil holder
2.19 €
Mount for GoPro DJI AVATA
2,25 €
Dice box with mechanical rotating top
4.02 €
Servo gripper for robotic arm - Servo gripper SG90
0,94 €
Keyfob application
3. 70 €
wall key holder (dragon ball)
1.25 €
Case for IPHONE 14 pro (TPU)
0,73 €
Survival pistol with arrows
6.21 €
G26 Frame DD26.2 Rail
6,50 €
Do you want to support Cults?
Do you like Cults and want to help us continue our journey on our own ? Please note that we are a small team of 3 people, so supporting us in maintaining activities and creating future developments is very easy. Here are 4 solutions available to everyone:
-
AD: Disable your AdBlock banner blocker and click on our banner ads.
-
AFFILIATION: Shop online with our affiliate links here Amazon.
-
DONATIONS: If you want, you can donate via PayPal here.
Learn more