Arcelormittal 3d printing
Additive Industries and ArcelorMittal 3D print large scale spare parts for steelmaking operations
0Shares
Metal PBF system manufacturer Additive Industries has teamed up with steelmaking company ArcelorMittal to push large-scale spare part printing in the steel industry. With the use of Additive Industries’ 4-laser 3D metal printing system, the MetalFAB1, ArcelorMittal has produced on-demand, end-use spare parts for its facilities with a focus on large and intricate components in recent weeks.
Harry Kleijnen, Key Account Manager at Additive Industries, stated: “We are proud to work together with ArcelorMittal, jointly driving the business case for 3D-printed parts in the steel industry. ArcelorMittal’s typical applications have enabled us to further adapt the MetalFAB1 system to print high density, high volume parts. We are looking forward to expanding the range of applications and materials in this intense and strong collaboration.”
The MetalFAB1
The two companies began working together in 2017, when the MetalFAB1 was installed in ArcelorMittal’s R&D facility in Avilés, Spain. Since then, the metal 3D printer’s 420 x 420 x 400mm build volume has been used to fabricate several spare parts for steelmaking and mining operations, some of which are still in use at the facility today. The MetalFAB1 is designed with safety and material recyclability in mind, which is in line with ArcelorMittal’s focus on operator safety and environmental responsibility.
Daan A.J. Kersten, Co-founder, and CEO of Additive Industries, explained, “Innovation and market leader ArcelorMittal have helped us to stress-test our MetalFAB1 system for critical spare-part production. This enabled us to expand our experience to the steel industry from our main application markets in aerospace and automotive. It has become clear that metal 3D printing is a serious alternative for a large variety of cast parts.”
3D printing large scale spare parts
3D printing spare parts is practical in that it renders excess unnecessary stock obsolete. Parts can be manufactured on-demand and on-site, shortening the product cycle and saving on costs. The spare parts used in steelmaking operations tend to be very large as well as having to be of very high quality. This initially limited the potential applications of 3D metal printing in the facility. However, recent collaborative efforts have yielded improved quality and reliability, as well as a 4x increase in the size of the parts being 3D printed. This means the potential applications have been extended from just small size parts to large, complex, and functional spare parts.
Jose López Fresno, Head of Additive Manufacturing, ArcelorMittal Global R&D in Avilés, said, “Additive Manufacturing is an exponential technology, moving very fast. Our collaboration with Additive Industries is a clear demonstration of our ability to remain at the cutting-edge of this technology: we started by printing small specimens and have now progressed to large size and complex parts.”
3D printed spare parts used in ArcelorMittal facilities.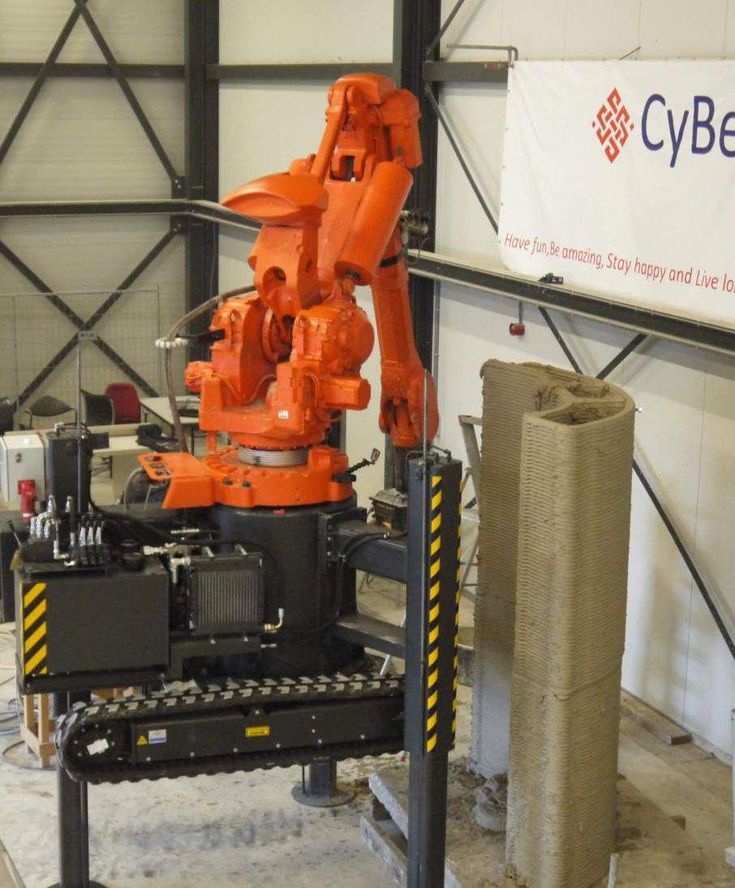
Additive Industries has developed 3D metal printing for not just production tooling, but aerospace applications too. The company has previously worked with APWORKS to qualify components at Additive Industries’ Process & Application Development Center in the UK. The two companies set out with the goal of advancing the series production of certified parts for the aerospace industry. Last year, Additive Industries also worked with an unnamed aerospace client to expand the clients’ facilities with the installation of ten MetalFAB1 3D printers.
The nominations for the 2020 3D Printing Industry Awards are now open. Who do you think should make the shortlists for this year’s show? Have your say now.
Subscribe to the 3D Printing Industry newsletter for the latest news in additive manufacturing. You can also stay connected by following us on Twitter and liking us on Facebook.
Looking for a career in additive manufacturing? Visit 3D Printing Jobs for a selection of roles in the industry.
Featured image shows the MetalFAB1 3D printer. Photo via Additive Industries.
Tags Additive Industries ArcelorMittal Daan A.J. Kersten Harry Kleijnen Jose López Fresno MetalFab1
Kubi Sertoglu
Kubi Sertoglu holds a degree in Mechanical Engineering, combining an affinity for writing with a technical background to deliver the latest news and reviews in additive manufacturing.
Additive Industries & ArcelorMittal Using MetalFAB1 3D Printer to Make Spare Steel Parts - 3DPrint.com
One of the world’s leading steel and mining companies, ArcelorMittal, is partnering with Dutch company Additive Industries to investigate the use of metal 3D printing to make large spare parts for the steel industry. Additive manufacturing is used to fabricate spare parts for plenty of applications and industries, including maritime, railways, the military, consumer appliances, automotive, and many more. It makes a lot of practical business sense, as 3D printing spare parts offers companies, like ArcelorMittal, flexibility, a reduced production cycle, and on-demand manufacturing; if this happens onsite, it can even save on shipping costs.
3D printed spare parts used in ArcelorMittal facilities: (A) Example of part consolidation application with 316L original part on the left and 3D printed part on the right; (B) example of functional large parts with internal lattice structure made with 316L above 500 mm; and (C) lightweight (hollow) functional spare parts made with Maraging Steel with ArcelorMittal’s optimized parameters.
By collaborating with Additive Industries on metal 3D printing over the last few years, and using the technology to build on-demand spare parts, ArcelorMittal has improved its quality and process performance – allowing the company to print large, complex components that are ready to use.
“Additive Manufacturing is an exponential technology, moving very fast. Our collaboration with Additive Industries is a clear demonstration of our ability to remain at the cutting-edge of this technology: we started by printing small specimens and have now progressed to large size and complex parts,” said Jose López Fresno, Head of the Additive Manufacturing department, ArcelorMittal Global R&D in Avilés, Spain.
![]()
Operations in the steelmaking industry require components, and spare parts, that must hold up under difficult conditions. In the beginning of the ArcelorMittal and Additive Industries collaboration, they had to figure out how best to achieve the necessary requirements for component size and quality. But over the last two years of working together, the two have achieved an up to fourfold increase in component size, in addition to improving their reliability and quality. This means that the steel company has been able to increase the amount of applications for its 3D printed spare parts from small size part consolidation to jobs that need complex, functional, large, and strong parts.
MetalFab1 on the day of installation in ArcelorMittal R&D facilities in Avilés.
Now, the two are looking at what metal 3D printing can do for the steel industry with the MetalFAB1 by Additive Industries, which is one of the market’s largest 4-laser metal AM systems.
“Innovation and market leader ArcelorMittal have helped us to stress-test our MetalFAB1 system for critical spare-part production,” stated Daan A.
J. Kersten, Co-Founder and CEO Additive Industries. “This enabled us to expand our experience to the steel industry from our main application markets in aerospace and automotive. It has become clear that metal 3D printing is a serious alternative for a large variety of cast parts.”
First introduced back in 2015, the unique MetalFAB1 printer has a 420 x 420 x 400 mm build volume, which makes it possible to fabricate large steel spare parts for the mining and steelmaking industries. But at the same time, it also ensures high productivity because it automated the manual steps of regular powder bed fusion 3D printers; this, in turn, equals the lowest cost per 3D printed part.
The modular MetalFAB1 has multiple build chambers, up to four 500W lasers, and can be configured for up to 11 different modules for more productivity or post-processing automation. It’s also well-designed for safety, which is perfect for ArcelorMittal and its focus on operator safety. In addition, 3D printing spare parts can help reduce waste – meeting another of the company’s objectives in terms of environmental safety.
“We are proud to work together with ArcelorMittal, jointly driving the business case for 3D-printed parts in the steel industry,” said Harry Kleijnen, Key Account Manager for Additive Industries. “ArcelorMittal’s typical applications have enabled us to further adapt the MetalFAB1 system to print high density, high volume parts. We are looking forward to expanding the range of applications and materials in this intense and strong collaboration.”
Since the first MetalFAB1 3D printer was installed at ArcelorMittal’s R&D facilities, the company has already used several of the 3D printed spare parts. To see the assembly and installation of the MetalFAB1 at ArcelorMittal, check out Additive Industries’ video here.
Discuss this story and other 3D printing topics at 3DPrintBoard.com or share your thoughts in the Facebook comments below.
(Source/Images: Additive Industries)
Stay up-to-date on all the latest news from the 3D printing industry and receive information and offers from third party vendors.
Tagged with: 3d printing spare parts • 3d printing steels • Additive Industries • Arcelor Mittal • ArcelorMittal • Metalfab1 • MetalFAB1 3D printer • partnership • spare parts • spare parts 3d printing • steel • steel 3d printing
Please enable JavaScript to view the comments powered by Disqus.
What the first 3D printed steel bridge looks like
Trends
TV channel
Newspaper
Pro
Investments
RBC+
New economy
Trends
Real estate
Sport
Style
National projects
City
Crypto
Debating club
Research
Credit ratings
Franchises
Conferences
Special projects St. Petersburg
Conferences St. Petersburg
Special projects
Checking counterparties
RBC Library
Podcasts
ESG index
Politics
Economy
Business
Technology and media
Finance
RBC CompanyRBC Life
RBC Trends
Photo: Mashable / YouTube
The world's first 3D printed steel bridge has been installed in Amsterdam. The project was ready three years ago, but the installation of the bridge was constantly delayed
What's happening
- On July 15, the world's first 3D printed steel bridge was opened in Amsterdam.
It connects the embankments of the Oudesijds Achterburgwal canal. The grand opening was attended by Queen Maxima of the Netherlands.
- The structure weighs 6 tons and is 12 meters long.
- The bridge was printed by four robots by welding layers of stainless steel wire, it took them 4.5 tons of steel and six months to make a span of 12 meters. Then coastal supports and decorative elements were made.
- This project was developed by the laboratory of Joris Laarmann and ABB, Air Liquide, ArcelorMittal, Autodesk, AMS Institute and Lenovo, while the Amsterdam-based company MX3D was fabricating and installing the structure.
- More than ten sensors are built into the bridge, with the help of which it will be possible to monitor its condition and deformation. Thus, he will himself indicate the need for repair. The sensors will also count the number of pedestrians crossing the bridge each day.
- The structure was installed for two years as a replacement for the conventional bridge, which will be under reconstruction at that time.
- This bridge was first presented at Dutch Design Week Eindhoven 2018, where the project won the Dutch Design Award and the Audience Award. After that, the finished bridge lay in storage for another three years: first, in anticipation of the reconstruction of the canal, then due to the coronavirus pandemic and lockdown.
What does it mean
In recent years, there has been an active development of 3D printing technology in construction. The Netherlands seems to be on the mend, with the first fully 3D-printed residential building in the EU populated in a suburb of Eindhoven in early May, followed by the opening of the world's first 3D-printed steel bridge.
We have already said that 3D printing is the future of construction and design. Compared to classical buildings, 3D printing has a number of undeniable advantages, such as short construction times, reduced economic and environmental costs, and ease of execution of complex shapes.
“This is not just about reducing and optimizing construction costs, but about giving architects and designers a new tool, a very cool new tool, with which they can rethink the design of their architecture and their projects,” notes Tim Görtjens, co-founder of MX3D, a bridge builder.
Mika Mos, member of the council of the municipality of Amsterdam, expressed the hope that this construction will also help the city attract quality new tourists:
“This could attract a new type of visitor, those more interested in architecture and design, which will change the perception of the area (famous for nightclubs and noisy parties. — RBC Trends ).”
Updated on 07/30/2021
Text
Ksenia Yanushkevich
Top of the trend
Related materials
MX3D showcases the world's first 3D printed steel bridge
News
Dutch company MX3D showcases the world's first 3D printed steel footbridge. An industrial robot equipped with a welding machine acted as a 3D printer.
The MX3D team has been working on the world's first 3D printed steel bridge for three years, refining new design and manufacturing methods. The design was made in Autodesk Dreamcatcher CAD using topological optimization, due to which the mass of the twelve-meter bridge was reduced to approximately four tons.
The entire bridge is 3D printed using arc welding technology: a six-axis robotic arm with a welding machine has grown the steel wire structure. The productivity of the additive system exceeds 2 kg/h, and a kilogram of consumables costs about five euros, which is an order of magnitude cheaper than steel powder.
The list of project participants is impressive: the team led by the designer and one of the founders of MX3D Joris Laarman was directly involved in the design, experts in the field of structural engineering were shared by specialists from the transnational engineering, architectural and consulting company Arup and construction company Heijmans, the Luxembourg metallurgical company ArcelorMittal helped with materials, Autodesk provided the software, Lenovo supplied the computers, ABB supplied the robotics expertise and equipment, Air Liquide and Oerlikon helped with the welding, and the municipality of Amsterdam acted as the customer.
The bridge is ready, but work on the reconstruction of the allocated canal in Amsterdam has been delayed, so for now the MX3D is showing its offspring at the Dutch Design Week in Eindhoven. Since the project is experimental in nature, the structure is equipped with a set of sensors with which engineers will monitor structural integrity, vibrations, deformations, loading and weather conditions.
The data we collect will help ensure security and improve future projects. The bridge is expected to be thrown across the canal early next year.
Do you have interesting news? Share your developments with us, and we will tell the whole world about them! We are waiting for your ideas at [email protected].
Follow the author
Follow
Don't want
7
Even more interesting articles
5
Subscribe to the author
Subscribe
Don't want
Researchers from Peter the Great St.