Two photon 3d printer
Nanoscribe introduces Quantum X, a two-photon 3D printer for microoptics
0Shares
Nanoscribe, a German manufacturer of two-photon additive manufacturing systems has introduced a new machine, the Quantum X. The latest system uses two-photon lithography for fabricating nano-sized refractive and diffractive micro-optics which can be as small as 200 microns.
Breaking the law
According to Dr. Michael Thiel, co-founder and CSO of Nanoscribe, “Beer’s law imposes strong limitations on today’s maskless lithography devices. Quantum X features two-photon grayscale lithography, which overcomes these limitations and offers unprecedented design freedom and ease-of-use. Our customers are working at the cutting edge of microfabrication.”
The two-photon Quantum X machine. Image via Nanoscribe.Nano 3D printing
Nanoscribe was founded as a spinoff of Karlsruhe Institute of Technology, and now has a subsidiary in Shanghai and an office in the U. S. The company is financially and technically supported by ZEISS, one of the oldest and largest manufacturers of optical systems in Germany.
Nanoscribe systems are based on two-photon absorption, a process in which a molecule is excited to a higher energy state. To fabricate 3D objects using the two-photon process, a gel containing monomers and two-photon active photoinitiators are used as raw material. A laser is fired onto the photosensitive material to form a nano-sized 3D printed object where the intensity of the absorbed light is the highest.
The Photonic Professional GT by Nanoscribe has found wide applications in research and is used at Harvard‘s Center for Nanoscale Systems, California Institute of Technology, Imperial College of London, ETH Zurich, and Keio University.
Recently, it was reported that Nanoscribe has also joined the MiLiQuant project, and will help bring quantum technology to an industrial level using its expertise in photon technology. In addition to two-photon machines, Nanoscribe also manufactures negative-tone resins, called IP Photoresins.
3D printing diffractive optics
Introduced at the on-going LASER World of Photonics 2019 (Booth A3.325) in Munich, the Quantum X system is specially designed for manufacturing diffractive optical elements (DOE). These micro-sized optic devices are used in the field of laser processing of materials, as DOEs can control the path and ‘shape’ of the laser with accuracy. Micro-optics are also used in LIDAR scanning and laser-based medical treatments.
One of the most common methods of manufacturing DOEs is based on the manufacturing process of integrated circuits, which can take up to twelve steps. However, with the Quantum X machine DOEs can go straight from CAD to print in a single step. According to Nanoscribe, Quantum X would be an ideal solution for rapid prototyping of micro-optics, small series production, and R&D.
An SME image of microlens array 3D printed on a Quantum X machine. Image via Nanoscribe.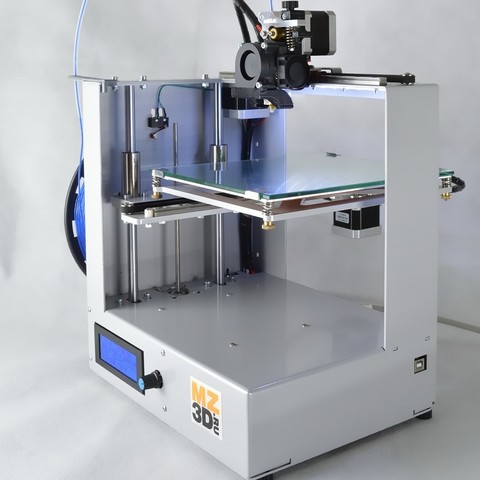
Technical Specifications
Printing technology | Two-Photon Grayscale Lithography (2GL) |
Minimum XY size | 160 – 200 nm (depending on the photoresin used) |
XY resolution | 400 – 500 nm (depending on the photoresin used) |
Finest vertical steps | 10 nm |
Scan speed | ≤ 250 mm/s |
Area printing speed | 3 mm²/h typical for diffractive optical elements |
Learn more about microfabrication by subscribing to our 3D printing newsletter and joining us on Facebook and Twitter.
For jobs in the industry visit our 3D Printing Jobs page.
Featured image shows an SME image of microlens array 3D printed on a Quantum X machine. Image via Nanoscribe.
Tags California Institute of Technology Center for Nanoscale Systems ETH Zurich Imperial College of London IP Photoresins Karlsruhe Institute of Technology Keio University LASER World of Photonics Michael Thiel Nanoscribe Photonic Professional GT2 Quantum X two-photon absorption Two-Photon Grayscale Lithography ZEISS
Umair Iftikhar
Technology – UpNano – high-resolution 3D printing
Highest resolution meets unmatched throughput
With UpNano’s cutting-edge technology it is possible to print objects with sizes ranging from the sub-micrometer to the centimeter range and up to 40 mm in height – within times never achieved before.
Highest resolution meets unmatched throughput
With UpNano’s cutting-edge technology it is possible to print objects with sizes ranging from the sub-micrometer to the centimeter range and up to 42 mm in height – within times never achieved before.
A new era in 3D printing
The continuing trend towards miniaturization demands evermore compact and powerful products with decreasing development cycles. The requirements for microparts in the production sector as well as in academic and industrial research are constantly becoming more challenging. To keep up with these developments the industry strives to constantly search for novel, more precise, efficient and profitable production methods.
Established 3D printing technologies such as (micro)stereolithography fail to produce such highly resolved microparts, since the minimal resolution of such systems is in the range of 20 µm. The NanoOne 3D printing system developed by UpNano enables users from different sectors to fabricate high-resolution microstructured parts for their specific applications in a cost-efficient manner, beginning already with the very first batch produced. This system can be used in various fields ranging from electronics to microoptics and biocompatible applications in cell and medical research.
Taking the lead in microfabrication
With NanoOne, production times and therefore unit costs for microparts can be significantly reduced, without sacrificing resolution and tolerances. The versatile technology based on multiphoton lithography can be used to manufacture both ultrafine components with structural details in the range of 170 nm and macroscopic microparts in the centimeter range. With a writing speed of up to 1,000 mm/s and a throughput of up to >450 mm³/h, NanoOne combines high performance with a user-friendly fast process.
Adaptive
resolution
Significant throughput increase can be achieved using the patented UpNano adaptive resolution technology. The software classifies the selected geometry in high and low-resolution areas and adapts the laser voxel size accordingly.
Learn more
The laser focal point is enlarged for bulk segments or precisely focused for the outer shell and fine details. Therefore, throughput can be significantly increased, with internal areas being printed faster.
High-volume segments
The laser focal point is enlarged in order to increase throughput, while maintaining the mechanical properties of the printed component.
High-resolution segments
The laser is tightly focused to achieve the highest possible resolution.
Outline
mode
UpNano’s proprietary outline mode enables high resolution and low surface roughness. The contours of solid printed components are written with the highest possible resolution to exploit the full potential of the respective objective.
Learn more
Among other things, suitable for the production of lenses with a surface roughness down to <10 nm. With this mode even larger lenses can be produced in an economical time and with exceptional surface properties.
With few simple steps to the final product
The user is supported from the first steps of preprocessing to postprocessing by the well thought-out hardware and software solutions as well as functional accessories.
Preprocessing
Machine preparation
Objective
Vat
Material
Sample preparation
Substrate
Metal holder
Assembly tool
Job design
Import STL
Create structure
Reopen job
Postprocessing
Sample development
Washing solution
Analysis
Light microscope
Scanning electron microscope
Magnification is key
The resolution requirements as well as the overall size of the object are decisive for the choice of the objective. It is important to find the right balance between the smallest details and the total volume of the component to obtain a satisfying printing time.
Two modes for dip-in free printing
Vat mode
NanoOne features a unique vat mode which allows the fabrication of large objects with a height of up to 40 mm. During printing, a vat with a precision glass window is placed above the objective, thus preventing contact of the resin with the objective and preserving the focusing power of the objectives. During printing, the object is drawn up out of the material vat. The distance between the current print layer and the objective thus remains constant.
Bottom-up mode
With the bottom-up mode it is possible to produce high-resolution structures directly within a substrate. The laser beam is focused through the high-precision glass bottom of the substrate and the structure is built from bottom to top. Possible substrates include well plates, Petri dishes and microfluidic chips.
The reason why 2-photon polymerization is more precise than 1-photon processes
UpNano’s high-resolution 3D printing system is based on 2-photon polymerization (2PP), which allows highest resolution in the sub-micrometer range. The 2PP technology takes advantage of the spatial selectivity of 2-photon absorption (2PA). The 2PA probability significantly reduces beyond the focus point, thus also the fluorescent volume is lowered, resulting in higher spatial resolution.
Direct comparison of the single and multi-photon beam path in fluorescence microscopy shows that 2PA only occurs in the focal point of the beam. Therefore, monomer crosslinking is induced only at the focal plane, as polymerization is dependent on this non-linear absorption – whereas the emitted light is absorbed along the whole beam in the case of 1-photon absorption.
This explains why parts produced with 1-photon based processes, such as stereolithography, are produced layer by layer, while 2PP parts can be produced in a pre-defined volume with a resolution of less than 1 µm.
UpNano Introduces Two-Photon Polymerization Technology for 3D Printing Centimeter-Sized Parts in Minutes
2PP (Two-Photon Polymerization) 3D printing system, developed by UpNano GmbH, a Vienna-based company in Austria, can print polymer parts from 100 to 1012 cubic micrometers. The company recently demonstrated the capabilities of its printer by printing four models of the Eiffel Tower ranging from 200 micrometers to 4 centimeters, with a perfect representation of all the miniature structures of the building, with print times ranging from 30 to 540 minutes. A team from the University of Vienna (UpNano is a spin-off institution) was one of the first in the world to master the possibilities of two-photon polymerization, an ultra-precise 3D printing technology that until now could only be optimized for a very limited range of scales. In addition, printing in the centimeter range was very time consuming and thus inefficient for any kind of mass production.
With its NanoOne system, the Austrian firm has now demonstrated what previously seemed impossible: producing centimeter- and millimeter-sized, nano- and micro-resolution precision parts in minutes. “We have developed and patented an innovative adaptive resolution technology for our 3D printing system,” explained Peter Gruber, Head of Technology and co-founder of UpNano. “Together with an optimized optical path and intelligent algorithms, we can use the full laser power up to 1 W, which is several times more than comparable systems. Such a powerful laser provides enough power for high-speed printing, especially in adaptive resolution mode. This is, in fact, a significant advantage over other systems that use weaker lasers and therefore performance is limited.”
“The benefit of this innovation,” added UpNano CEO Bernhard Künburg, “is most noticeable in the meso range. The NanoOne system provides significantly faster production times than other systems. Add to this our patented adaptive resolution technology and you'll be able to print centimeter-sized objects at micrometer resolution in short production cycles.
This algorithm allows you to expand the laser spot up to 10 times according to the specifications of the printed sample. A simple change of lenses (available from 4x to 100x magnifications) makes it possible to produce parts in the micro-range with nanometer-scale resolution. It's also significantly faster than other systems thanks to special optical paths, optimized scanning algorithms, and proprietary adaptive resolution technology. In fact, NanoOne is capable of producing objects with volumes that vary by up to 12 orders of magnitude. Sizes [of prints] are equally possible both in the micrometer range and in the centimeter, while maintaining ultra-high resolution. And all this in the shortest possible time.” An example of the use of the system in medicine and research is the production of trace elements with tight tolerances and specific functions, such as sharp tips, cannulas or reservoirs. Another interesting area of application of the technology is the creation of functional micromechanical parts. A 6mm high functional spring printed in less than 6 minutes is given as a reference example, or two-piece parts with included moving parts for medical technology.
Filter production is the third example of NanoOne's capabilities - such a device measuring a few square centimeters with micrometer-sized pores can be printed in a matter of hours. “Such filters have precisely defined dimensions for 100% of all pores,” explains Bernhard Künburg.
The most expensive 3D printers in the world
- home
- News AT
- World
- The most expensive 3D printers in the world
Various technologies do not stand still, they are constantly evolving. This article proposes to consider the evolution of industrial 3D printers today, which are the most expensive in the world and why.
3D printers are unique in terms of the variety of different 3D printing methods, materials used and their applications. You can spend as little as $100 to get a reliable 3D printer to make a huge variety of parts from affordable plastic material. On the other hand, you can spend over a million dollars to buy a 3D printer to 3D print parts with large and complex construction geometries. They can be used in the aerospace industry, the production of space satellites or miniature biocompatible devices for medical purposes. The most expensive 3D printers on the market today use 1 to 12 powerful lasers to fuse metal powder, sinter polymer materials, or polymerize resin, and 3D printing from a given 3D model occurs by applying the powder layer by layer, which is a process additive manufacturing.
It can be noted that the size of the 3D printer does not determine how expensive the 3D printer will be. Today, the price often depends on advanced patented technologies and features that allow a 3D printer to produce fast and high-quality 3D-printed parts without requiring special technical knowledge from the operator.
Some of the most expensive printers are not even for sale. Carbon 3D's 3D printers are available for rent only, which allows them to be used by many users. Others use their 3D printers on a project-by-project basis, such as the Vulcan construction printer from homebuilder Icon 3.
Stargate, the world's largest metal 3D printer built by Relativity Space to 3D print rockets, it's not for sale, but if it was, it would definitely be on our list. Many of the most exciting technologies in 3D printing can only be used for custom 3D printing, not for purchase. (Source: Relativity Space)
Let's look at the criteria that affect the cost of a modern industrial 3D printer.
Features 3 D -printers affecting their price:
- The uniqueness of the technology when creating
- How automated the processes in the 3D printer
- The size of the working chamber
- Functions allowing quality control
- of equal software
- Numerous controls and adjustments
- Controlled environment inside the working chamber (use of inert gas, the possibility of heating/cooling the working platform)
Breaking down these features:
Features that drive up the price of 3D printers include printer technology-specific software, real-time 3D printing control systems, and anything that automates processes that sometimes are performed manually in cheaper systems (layer leveling, subsequent post-processing or powder sieving) or processes that require knowledge of metallurgy or polymers.
Production technology requiring a vacuum chamber in a 3D printer, filling the working chamber with an inert gas, or printers that are certified for use in clean rooms and having these characteristics are significantly reflected in the final price of this equipment.
The materials used in the 3D printing process also have a significant impact on the final cost of a 3D printer. Many 3D printers only work with proprietary materials that have been developed by the manufacturer for that 3D printer. They can be metal powder, special resins filled with carbon fiber particles, and unique polymer powders. At this point in time, it is possible to 3D print anything from pure gold to advanced engineering plastics on 3D printers, even in the harsh environment of space.
There are 3D printers that can 3D print multiple materials in one job, and there are multicolor 3D printers that are also in the higher price segment.
THE MOST EXPENSIVE 3 D -PRINTERS
The 3D printer manufacturers discussed below are reluctant to publish exact prices for their products. This is due not only to competition, but also to the fact that 3D printers have a basic package, as well as a package with additional options according to customer requirements. That said, with that in mind, below is a look at some of the most expensive 3D printers available today - all costing over half a million US dollars - and what they provide.
E-Plus3D EP-M450H
3D printer EP-M450H LPBF (Source: E-Plus 3D)
Chinese company E-PLUS3D produces industrial metal 3D printers with a large construction camera for additive manufacturing for various industries in the country. These 3D printers are used in the aerospace, automotive, electronics, and engineering industries to produce not only large-sized parts such as heavy-duty molds, but also mass-produced parts.
The EP-M450H Metal 3D Printer is the company's largest 3D printer with a build chamber of 456 x 456 x 1080 mm, producing 99.9% density metal parts from a wide range of materials at a speed of 55 cm³ per hour.
XJet Carmel 1400C
Israeli company XJet has developed a unique ceramic 3D printing technology. NanoParticle Jetting (NPJ) technology allows the production of metal and ceramic parts with a high level of detail, smooth surface roughness and geometric accuracy. The high cost of this 3D printer is not only due to the technology itself, patented materials that make this printer a serious investment, but also to the advanced automation of the 3D printer itself, which makes it easy to use.
Carmel 1400C, equipped with one of the largest 1,400 cm² work platform in the industry, which allows the production of several ceramic parts at the same time.
SLM Solutions NXG Xll 600
NXG XII 600 Large Metal 3D Printer (Source: SLM Solutions) range of printers, but its NXG Xll 600 is what the company says is a revolution in industrial additive manufacturing. The NXG XII 600 was designed for high-volume additive manufacturing and features the industry's first 12 1,000W lasers with a 600x600x600 build chamber. Lasers provide high build speed up to 1000 cm 3 /h and capacity not available for other machines.
In addition to lasers, the NXG Xll 600 has all the benefits that SLM Solutions customers have been asking for over the years, including automatic start-up, laser focusing, closed powder feed and material screening, and other latest developments.
UpNano NanoOne Bio
The Austrian company UpNano has developed a two-photon 3D printer using hydrogel-based bio-ink, which allows direct printing of 3D structures containing living cells, both at the meso- and microscale. The NanoOne Bio printer is based on the NanoOne line of laser printers capable of creating structures of 12 orders. The new hydrogel is the only commercially available resin that allows live cells to be embedded directly from culture plates into 3D printed structures for biological applications.
UpNano claims that the combination of X Hydrobio INX U200 and NanoOne Bio opens up new possibilities in biomedical research and development, both in industry and academia, allowing pharmaceutical companies and research institutes to create cell models that mimic natural growth conditions in the body person.
Black Buffalo 3D
Black Buffalo's new 1G construction printer (Source: Black Buffalo)
Black Buffalo 3D, an American company based in South Korea, officially unveiled its Nexcon 1G earlier this year, which is a 3D printer for building houses and other large concrete objects. The printer can create a 92.9 square meter structure in less than 20 hours. It uses Black Buffalo's patented cementitious material, the company calls it ink, that can be dyed to a chosen color and is also customizable to 3D print locally according to the temperature, humidity and altitude conditions of the area.
The Nexcon 1G is a modular 3D construction printer that can be extended along the X, Y and Z axes to scale up (or down) a project up to three stories high. The 1G printer is unique in that users can reposition the base rails and move the printer to a new printable area without having to remove the X or Z axis.
Optomec LENS 860
Energy Deposition (DED), which allows the recovery of large titanium components, such as those used in aircraft engines. Optomec offers several models of 3D printers that have large build chambers like 860x600x610 and laser power of 3 kW.
The LENS 860 machining systems are ideal for the fabrication, repair or coating of medium to large metal parts.
ExOne S-Max Pro
Although many ExOne printers (now owned by Desktop Metal), they are still very affordable given that high volume 3D printers can cost quite a lot of zeros.
3D printers are used to 3D print complex and detailed sand molds and cores for foundries producing large metal parts for industrial use. The S-Max Pro features a 1,260 liter build chamber for fast 3D printing of sand molds and cores. A new automated print head enables fast 3D printing, while improved sand compaction ensures the density and strength of complex sand mold designs. As the most advanced system in the ExOne family of sand 3D printers, the S-Max Pro is focused on continuous 24/7 production and offers Industry 4.0 integration with cloud connectivity and real-time machine monitoring.