Prosthetic arm 3d print
Top Examples of 3D Printed Prostheses
Published on April 7, 2022 by Niru K.
When it comes to industries adopting 3D printing, one of the earliest and most fervent supporters of the technologies is of course the medical sector. Indeed, AM is becoming a crucial tool in healthcare thanks to a variety of factors. This is especially the case when it comes to prosthetics. With 3D printing, the benefits are two-fold. First, of course, the prostheses can be perfectly fit to the patient thanks to the ability to customize the part. But additionally, 3D printing enables lower-cost, local production of prostheses. As the World Health Organization estimates that 30 million people worldwide are in need of prosthetics, this can help increase availability for many especially in remote regions. We took a look at some of the top examples of 3D printed prosthetics currently available.
The E-nable association
E-nable, also known as Enabling the future , is an association created in the United States by Jen Owen. The idea behind this project is to bring together makers and enthusiasts to create a network of models of prostheses in the world that can obviously be printed in 3D. The main objective is to “give a hand” to the people who need it most, thus avoiding the high cost of a traditional prosthesis. Since its creation in 2013, the association has donated 3D printed prostheses to hundreds of people around the world.
Bionico Hand, an Open-Source 3D Printed Prosthesis
The Bionico Hand project is the brainchild of Frenchman Nicolas Huchet who has used a bionic hand since he was 18 years old. After making his own, he launched Bionicohand as a way to make more for himself and others. Essentially, what he has conceived is a myoprosthesis, his own term for a myoelectric prosthetic, that can repair itself. He aims to create something designed by and for amputees that will be available open source so anyone can make their own. The project is not yet ready, though it has been in development for a number of years now. However, the proof of concept was produced in October 2021 and the goal is to transform it into a functional prototype by the end of 2022.
Photo Credits: Bionico Hand
Make Your Own 3D Printed Robotic Arm with Youbionic
Created by Federico Ciccarese, Youbionic is a platform that is a little different from many on our list. It is not technically designed to create prosthetics for those in need, but rather a way for young people to enter into the robotics industry. Essentially, buyers will receive a kit with everything they need to create their very own robotic arms, including 3D printing part files. These files have been designed to be easy to print as well as oriented to obtain the best results. And best of all? There are not many parts that make up an Avatar Full Arm (one of the largest available projects), leaving users will less assembly than they might expect. On the company’s website, they have a variety of cool projects that you can buy, including full arms, hands, double hands and more.
Photo Credits: Youbionic
Unlimited Tomorrow – The Name Says it All
Unlimited Tomorrow was founded in Colorado in 2011 by Easton LaChapelle who had been working on robotic limb development for a few years. However, she decided to launch into this project after meeting a little girl who wore a prosthetic limb that had limited capabilities while still being expensive. Thus, the idea of Unlimited Tomorrow and improved prosthetics was born. It aims to support people with upper limb disabilities by using additive manufacturing to produce high quality, high value, low cost bionic prosthetic arms. 3D printing allows for the process to be customizable. This happens as after the user answers a few questions, they are then sent a 3D scanner to scan the residual limb. Based on this, the prosthesis, which can also be personalized, is produced with the 3D printer.
Photo Credits: Unlimited Tomorrow
A Distinct Prosthesis with UNYQ
3D printing is used at UNYQ to use mass production to create innovative, customized prostheses. In addition to being able to develop next-generation products, additive manufacturing is also used for aesthetically pleasing and practical features. Prostheses for above and below the knee amputees offer patients revolutionary personalization in terms of color and design. Currently, they are even working on manufacturing an entire leg. UNYQ provides its patients with an app to create the 3D-printed prostheses: Color, design and surface can be selected, then measurements are taken in a clinic to finally print the prosthesis using additive manufacturing.
3D Printed Foot Prostheses from Mercuris
Mecuris is a German company dedicated to the development of CAD/CAM software solutions that, together with 3D printing, make it possible to create foot prostheses. Thanks to a digital platform, called Mecuris Solution Platform, users can create and customize their individual models to their liking, saving time and money. In fact, thanks to 3D technology and its flexibility, the company is able to reduce production costs by 75%. With this, Mecuris’ goal is to convert traditional craftsmanship into digital tools and workflows that are easy to use according to the needs of each individual, and accompanying customers in every step of the process.
LimbForge Offers Prostheses in Remote Regions
LimbForge, a US-based non-profit organization, works on creating software, design and innovative manufacturing with 3D scanning and 3D printing. With these tools they are able to develop and deliver high quality and affordable custom prosthetics. LimbForge has developed and implemented a platform that allows clinicians to spend less time customizing devices and more time treating a greater number of patients. Its platform provides more realistic designs that help patients integrate and thrive, reduces costs and also offers ultralight prosthetics. The Limbforge platform can be used to size and implement other designs beyond its existing catalog. In fact, once a prosthetic design is in the database, it can be easily configured to fit almost any human anatomy. Notably, the platform is being used to help amputees in developing countries to gain access to high quality prostheses.
Photo Credits: Limbforge
3D Printing the Prostheses of the Future
Evan Kuester is an engineer, artist and designer currently working as a Senior Advanced Applications Engineer at 3D Systems. In addition to that, Kuester is pursuing a number of interesting projects using additive manufacturing. Among them is the development of prosthetics with extremely modern and futuristic designs. For example, in the photo below we see the JD-2 prosthesis model, created with the intention of further exploring the possibilities available to designers with SLS 3D printing technology. Its inner mesh-like structure is intended to reduce the weight of the prosthesis as well as to achieve a more pleasing aesthetic.
“Hero Arm”, a Hero for Life
Open Bionics was the first company in the world to launch a 3D printed bionic arm that would not only be clinically tested but also medically certified. This 3D printed arm is called “Hero Arm” and combines functionality, comfort and design. It is customizable and includes sensors to detect muscle movements, thus providing more ease to move. It would even be able to lift up to 8 kilos, a rather high weight when we know that the prosthesis is put and removed quickly. Open Bionics offers complete customisation of the prosthesis, a real advantage for the person who wears it, who can then create it in his own image. A particularly attractive point for children who often choose a prosthesis with the image of their hero!
3D Prostheses for the Needy
In Africa, many countries have a healthcare system that is unable to treat injuries caused by traffic accidents or infections, so it continues to experience a large number of amputations. That is why there are several non-profit organizations that want to bring printing technologies to anyone in need and anywhere in the world. One example is Ayúdame 3D, a Spanish organization that promotes the social value of technology through technological-social awareness programs in order to help vulnerable groups around the world. Both it and 3D Sierra Leone create 3D printed arms, free of charge, for people with disabilities. Thanks to this, they manage to improve their quality of life and that of their environment, reduce the inequality they face and provide them with greater opportunities for schooling and employability.
Naked Prosthetics and Resin 3D Printing
Based in the United States, Naked Prosthetics (NP) is a company dedicated to the development of functional prosthetic devices for hands and fingers. To do so, they rely on resin 3D printing, specifically stereolithography, with which they create these customized models adapted to the needs of each user. Thanks to 3D printing, Naked Prosthetics is able to deliver the prosthetic devices within a few weeks. As they state on their website, NP’s mission is to help people with partial amputation of fingers and hands, to change their lives positively through functional and high quality prostheses.
Photo Credits: Naked Prosthetics
A Fully 3D Printed Ocular Prosthesis
We recently learned of the UK case of Steve Verze, a Londoner, who became the first person in the world to receive a fully 3D printed ocular prosthesis. The printed prosthesis is part of a collaboration between several players in the UK and Europe, and was led by researchers at UCL and Moorfields Eye Hospital NHS Foundation Trust. The result? A prosthetic eye is impressively realistic thanks to its clearer definition and lifelike depth which was made possible with eye socket scans to ensure a good match.
Lattice Medical, Fighting Breast Cancer with 3D Printing
Taking on breast cancer – that’s what Lattice MEdical, a company founded in Lille, aims to do. Founded in 2017, the company has produced a bioprosthesis called MATTISSE, which could offer an alternative to the silicone prostheses commonly used to help treat breast cancer patients. The silicone prostheses commonly used have to be replaced about every 10 years for safety reasons, which is why the MATTISSE bioprosthesis is made of an absorbable material that can be optimally adapted to the patient’s morphology thanks to the use of additive manufacturing. Lattice Medical uses FDM technology to be able to create the natural reconstruction as they regenerate the patient’s own fatty tissue.
Photo Credits: Lattice Medical
What do you think of these 3D printed prostheses? Let us know in a comment below or on our Facebook and Twitter pages! Sign up for our free weekly Newsletter, all the latest news in 3D printing straight to your inbox!
3D Printed Prosthetics - Prosthetic Arm Design
Help Us Deliver TrueLimb to 100 Ukrainians in Need!
Take Action
The Most Convenient Fitting Experience You’ll Ever Have
All of our appointments are booked online with our clinical team and on your schedule. They’re virtual, so you never have to leave home or sit in a waiting room, and they’re usually available as soon as the next day.
Book appointments online, no referral necessary
All appointments are virtual, you never have to leave home
Book on your own schedule - days or weeks in advance
All you need is an internet connection and a half hour!
Our process was designed with you in mind every step of the way
Convenient
For the first time, you can be fitted for, receive, train, and get support for your FDA registered prosthetic device from the comfort of your own home.
Fast
With insurance hurdles, it can take over a year to receive other bionic arms. With TrueLimb, the average timeframe is just a few months.
Supportive
Unlimited support is included with your TrueLimb. A member of our Success Team is always available by chat, phone, email, or video.
User-First
We prioritize your time and your experience. No waiting rooms, no approval and appeals process, no co-pays, and no unexpected bills.
"This thing is a game-changer!"
- Jonathan S.
We've made it easier than ever to receive a completely personalized prosthetic device!
Our Process Puts You First
Step 1
Answer a few simple questions and schedule your one-on-one consultation with our clinical team.
Step 2
We ship you a 3D scanner to 3D scan your residual limb. We use these scans to create a set of check sockets for you.
Step 3
We ship you a set of check sockets and schedule a video evaluation with our clinical team to assess the comfort and fit. We repeat this step until we achieve a perfect comfortable fit.
Step 4
We 3D print, assemble, and test your personalized TrueLimb.
Step 5
Your TrueLimb is shipped to your front door, ready to train right out of the box!
FAQs
What is a prosthetic arm made of?
Prosthetic arms can be made from a wide variety of materials including acrylic resin, carbon fiber, thermoplastics, silicone, aluminum, and titanium. TrueLimb devices are made of industrial-grade PA12 nylon with acrylic and rubberized coatings. Numerous other actuators, electronics, and hardware are housed in the arm to provide proper functionality.
Can my 3D printed prosthetic be matched to my skin tone?
Yes! TrueLimb is the only device of its kind to be offered in hundreds of skin tones. There are multiple steps during the prosthetic arm design process that will ensure your TrueLimb is matched to the skin tone you select. Our goal is to make sure you are happy and confident in your choice!
Your first opportunity to select the skin tone that matches you best is during the 3D scanning process. Upon receipt of your first round of check sockets, there will be one socket that is printed in the tone you selected while conducting your 3D scan as well as another color swatch. This will allow you to compare the skin tone you selected with your residual limb and change your selection if you are not satisfied with your first choice! We continue to work with you to ensure you are completely satisfied with your personalized TrueLimb.
Why should I choose a 3D printed prosthesis over a different type?
Speed is an important factor when it comes to receiving your prosthetic. Traditional prosthetics can take weeks and even months to produce. 3D printed prosthetics can be made much quicker in comparison to other options. 3D printing prosthetics also allows for complete customization as each TrueLimb is printed specifically for each user. Advancements in 3D printing technology have also made it such that 3D printed prosthetics can offer the same or better durability over traditional prosthetics.
When wearing your prosthetic, you want to be comfortable! Comfortability is a huge bonus with 3D printed prosthetics. 3D printed prosthetics are designed to your liking, and to fit perfectly; which makes it much more comfortable for you!
How long does a bionic arm take to make?
TrueLimb takes far less time to make compared to other bionic arms. With TrueLimb, the process typically takes on average eight weeks from start to finish.
See More
Connect With Us
Youtube
Tiktok
Join Our Newsletter
Please enable JavaScript in your browser to complete this form.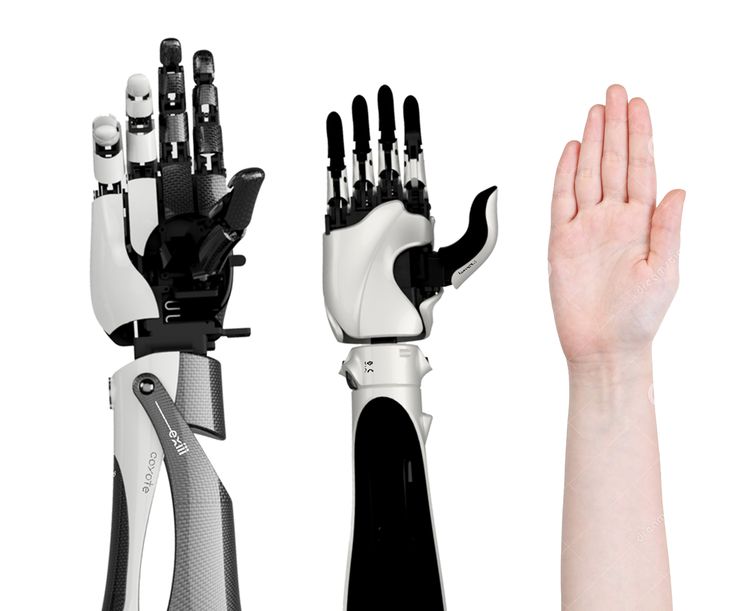
Email *
First Name *
Last Name *
Notice: JavaScript is required for this content.
Manage consent
3D printed bionic prostheses from Unlimited Tomorrow
News
Artificial hands with six grips are created from individual 3D scans of patients and are offered for eight thousand dollars.
Unlimited Tomorrow is the brainchild of a young entrepreneur named Easton LaChapelle, who built his first remote-controlled robotic arm at the age of fourteen. Three years later, the now high school student was invited to the traditional school science fair at the White House after winning a competition at the Intel International Science and Technology Fair, and a year later, Easton joined forces with British designer and almost namesake Christopher Chappelle and launched his own startup, collecting the initial funding on the Kickstarter crowdfunding platform.
Easton is now twenty-four years old and leads a company that offers a ready-made commercial product - functional 3D printed prostheses. The idea of a startup was born back in his school years, when during one of the fairs, his attention was attracted by a girl who was carefully studying his booth with a robot. The girl was missing her right arm, and a rather simple electromechanical prosthesis with one grip replaced the limb. As it turned out, this miracle of technology cost parents eighty thousand dollars.
TrueLimb prostheses can hardly be called cheap either, but they are much more affordable in terms of affordability: Unlimited Tomorrow offers its products for $7,995 or in installments with monthly payments of $259, working directly with patients, without intermediaries, while the closest analogues cost about twenty thousand even with good health insurance. In addition, these hands are much more functional, being able to perform six different grips with individual finger control, and much more attractive to look at than many of the analogues.
The size of the hand, color and detailing is chosen by the future user, who only needs to go through the 3D scanning procedure. Scanning can be performed at home: the company sends the necessary equipment and instructions to selected candidates. Then the company's engineers refine the 3D scans and use the resulting digital models to print components on a Hewlett Packard color 3D printer using Multi Jet Fusion technology. The minimum age of a candidate for prosthetics is seven years.
For now, the company is focusing on prosthetic arms, but is considering making artificial lower limbs and even exoskeletons. The most well-known Russian manufacturer of custom prostheses using 3D printing technologies is the Moscow company Motorika, which offers low-cost mechanical traction prostheses "Kibi", myoelectric prostheses "Indy" with one grip, and also working on bionic artificial hands "Manifesto" with fourteen grips. . Customers can count on compensation through the Social Security Fund. This summer, Motorika received the CE marking for all its products and announced its intention to enter the European market.
CNET publication on the Unlimited Tomorrow project:
More interesting articles
eleven
Subscribe to the author
Subscribe
Don't want
The results of the first experiments on 3D printing with polymer materials in microgravity, pro...
Read more
eight
Follow author
Follow
Don't want to
Skat 3D prototyping and 3D printing center specialists launched additive manufacturing of orthopedic...
Read more
53
Subscribe to author
Subscribe
Don't want to
As we all know, a true 3D printer must have a solid acrylic body, high quality. ..
Read more
our journey from idea to implementation
Share on Facebook Share on Twitter Share on Vkontakte
A few months ago, our idea for an affordable prosthetic hand was just an idea, an intention. Today we are happy to share our results with you!
How did it all start? The first prosthesis printed with the 3D printer was created in South Africa by Richard Van As. His video went around the world and inspired many people, including us. Having studied the issue of limb prosthetics, we were surprised how difficult it is in our country. Those prostheses that are available perform only a cosmetic function. And those that are functional cost fabulous money and require compliance with certain conditions, in particular, a person reaching a certain age.
Building a team and finding a patient
It was decided by the general council that we would take on a project to create an affordable mechanical hand prosthesis for people of almost any age. First of all, we needed to find colleagues from different professions - 3D designers , designers, doctors and, of course, find a patient who will try out the first prosthesis created using 3D printing . It cannot be said that it was quick and easy, but the necessary specialists were found. Young engineers from the company 9 joined the project0086 W.E.A.S. Robotics , who work in the field of robotics and are known for their desire to develop this area in Russia, as well as their passion for engineering, which is expressed in their projects . As well as an orthopedic surgeon from the St. Petersburg Institute of Prosthetics, who liked the idea. It was up to the patient. We were approached by several people who could become testers of the prosthesis, but either they were too far away, or their age was too young. We continued to search and found Alexander from Yaroslavl, where we were also advised by an excellent doctor, who later agreed to install a prosthesis.
Thus, we have a fully formed team and a patient.
Work has begun
Alexander lost his fingers on both hands in an accident, but his wrist joints have retained full functionality. The first step was to take the necessary measurements in order for the prosthesis to fit.
Then came the collaborative effort of 3D designers . As a result, we very soon had a ready-made 3D model for printing:
The next step was perhaps one of the simplest - the individual parts of the prosthesis went to print. Unfortunately, we did not have time to take disassembled photos, as we were eager to put all the parts together as soon as possible and see the almost completely completed prosthesis.
It is worth noting that the final assembly of the prosthesis takes place already on the patient’s arm, and, in addition to the parts printed on a 3D printer, cables or rope, screws and a turbocast are also needed. If everything is clear with cables and cogs, then it is worth mentioning the turbocast separately. This is a special thermoplastic that, when heated, for example, in hot water, becomes flexible and it is easy to give it the desired shape, after a few minutes it hardens again, and the rest of the prosthesis structure is attached to it. It was sold to us at a discount at company Horse , which manufactures retainers from similar plastics.
Installation of the prosthesis and the first test
We had the most exciting action - the installation and the first test of the prosthesis. Choosing in advance a convenient time for everyone, we went to Yaroslavl and for the first time personally met with the doctor and Alexander. Alexander turned out to be a very cheerful and cheerful person, and the process of installing the prosthesis went under his playful comments.
This short video shows the mechanics of the prosthesis in action:
Practical tests of the prosthesis not only proved its functionality, but also importantly, helped to find some flaws in the design developed by Richard, which will be solved in the following design prosthesis iterations. We decided to completely redo the prosthetic hand model and it is almost ready, and by the way, now it looks like this:
What conclusion can be drawn after going from the idea of creating a prosthesis to its implementation? We made sure that an affordable mechanical prosthesis created using 3D printing is more than just an idea, it is a real and tangible help to many people - both children and adults. We are very grateful to everyone who, by deed or word, has contributed and continues to contribute to this good deed. It's nice to know that there are caring people who are willing to spend their time and money to create something really useful.
You can also contribute to the common cause of helping those in need of a prosthesis by sharing a link to our article, and perhaps this will allow a person in need to solve their problem with the help of our project.