Make guide to 3d printing
A Step-By-Step Guide of 3D Printing
For many people, 3D printing seems to be a manufacturing technology that exists in the future world. 3D printing technology has been popularized and widely used today. 3D printing was born in the late 1980s. The world’s first 3D printer was born in 1986. However, due to its high price and immature technology, it was not popularized in the early days. After more than 30 years of development, 3D printing technology has become more skilled, accurate, and the price has been reduced.
At present, 3D printing technology is widely used in manufacturing, medical, education, design, and other industries. For example, Surgeons at the Albany Medical Center in the United States use 3D printing to produce organ models; archaeologists of the Italian Agency for Cultural Heritage Restoration (ISCR) applied the 3D printing technology to make copies of precious cultural relics. Now, it is no longer an unattainable dream for ordinary people to own a 3D printer. Makers around the world can use 3D printing technology to create all kinds of models. It can be said that whether for a company or an individual, 3D printing technology can easily realize their desire to print independently at anytime and anywhere.
Italian Cultural Heritage Restoration Agency (ISCR) used 3D printing to make cultural relics
How does 3D Printing Work?
3D printing is a new type of manufacturing and processing technology. Visually speaking, ordinary printers print graphics and text on 2D paper with ink, while 3D printers convert raw materials (such as metals, ceramics, plastics, etc.) into thin layers by heating, light, laser, etc. Then, like building a house, the layers are added up to form an entity in the space. Mainstream 3D printing technologies are FFF, SLA, SLM, etc. The FFF is the most common technology, which will be focused on in this article.
FFF (Fused Filament Fabrication) is a 3D printing technology using PLA, ABS and other thermoplastic filaments, which will be heated and extruded by an extrusion head, and then stacked layer by layer under the control of a computer to finally construct a shaped three-dimensional model. It is the most common and widely used 3D printing technology, with higher precision and lower cost.
The printing process of Raise3D’s 3D printer
Choose a Suitable 3D PrinterAt present, there are various brands and printers on the market, you can choose the most suitable 3D printer according to your needs. It is a good choice for you to choose a Raise3D Pro2 Series printer that is easy to operate!
Raise3D Pro2 Series printer components
The easiest way to understand FFF printing technology is to learn the components of a 3D printer that applies the FFF technology. A 3D printer mainly contains components such as printing bed, extruder, moving parts, touch screen, etc.
Printing bed: The printing bed is the platform for printing models, and usually the print bed is heated to help layers adhere to each other firmly.
Extruder: The extruder is the core component of a 3D printer, which will melt and stretch the filaments to build the model.
Moving parts: The parts of the printer will move on three axes, which are X, Y, and Z-axis. The X-axis and Y-axis are responsible for forwarding and backward movements, and the Z-axis is responsible for vertical movements.
Touch screen: Users can operate the printer and complete various settings by clicking the built-in RaiseTouch on the LED touch screen.
How to 3D Print a Model?
Unlike traditional processes, 3D printing requires very few steps, allowing you to print more easily. Generally speaking, to print a model through 3D printing needs to go through the following four steps: modeling, slicing, printing, and post-processing.
ModelingIf you want to print a 3D object, you naturally need to obtain a digital model of the object. Modeling will turn the object you want to print into a digital model that can be printed on a 3D printer. You can create 3D models with 3D modeling software (such as CAD software). Of course, you can also download the model files other users create. The STL files are widely used in rapid prototyping, 3D printing, and computer-aided manufacturing (CAM). The ideaMaker Library of Raise3D will also provide you with a platform where you can share and obtain 3D modeling models and settings files.
3D Rabbit Model
SlicingWhen you have a designed model, you can use specific slicing software such as ideaMaker to slice the model. The purpose of slicing is to allow the 3D printer to calculate the route and the amount of filament required when printing the model. Just like building a house, you need to calculate the steps to build and the amount of wood needed. ideaMaker will generate a GCode file, which is essentially a long list of instructions, and then the 3D printer will read the GCode instruction to build the model. ideaMaker is a powerful slicing software, which can create personalized configurations according to different printers, filaments, and models, it can also automatically create precise support structures. Therefore, ideaMaker will provide you with more possibilities for creativity.
Sliced Rabbit Model
PrintingAfter slicing is complete, you can upload the slice file to the printer, and calibrate the printer to prepare for printing. The extruders and the printing base need to be calibrated, to improve the accuracy of printing. During the printing process, you can observe the printing process through the transparent panel of a Raise3D Pro2 Series printer, or you can also monitor the printing progress remotely through our APP RaiseCloud in real-time. You will have a more intuitive and deeper understanding of the principles of 3D printing in this way. It will be a wonderful thing to observe the process of filaments accumulate layer by layer and monitor the printing progress!
Printing the model
RaiseCloud Mobile App.
Post-processingPost-processing is the final stage of 3D printing. The post-processing of FFF 3D printing has the following steps (not all steps must be completed):
Removing support: After printing, you need to remove the support (if the model contains). Filament will remain on the surface of the model.
Sanding: You can use some sandpapers to make the model smoother.
Coloring: You can color the model according to your preference and add more details.
Polishing: You can use apply a specific coating or other processes to make the model surface smoother and brighter.
Welding / Assembling: When you print a multi-part model or a large model, you can divide it into multiple parts, and then assemble the parts to form a complete model.
Post Processing
Advantages and Development of 3D printingAlthough it is a novel manufacturing technology, with its unique additive manufacturing method, 3D printing will surpass the traditional manufacturing process and become a new choice for future production.
Shortening the production cycle: 3D printing greatly shortens the product production cycle. By using a 3D printer, the company can more quickly produce the prototypes of the product and enable customers to make detailed and rapid feedback. The application of 3D printers in prototyping and small-scale production will continue to expand.
Manufacturing complex parts: 3D printing has powerful forming capabilities and will not be restricted by complex curved surfaces and precise structures so that 3D printing can produce very complex parts.
Unlimited design and manufacturing space: 3D printers can print everything as long as you create a 3D model on the computer. Different filaments can be combined to create more possibilities.
In the future, 3D printing will have higher precision and faster speed, and more multi-materials with excellent comprehensive performance will develop. Therefore, 3D printing will be applied in more sophisticated and high-end industries such as aviation, aerospace, military, etc. to create a new industry format.
Connect with Raise3D:
Have you had a great experience with Raise3D that you would like to share? Please contact us at inquiry@raise3d. com. We look forward to hearing from you.
For more information about Raise3D printers and services, browse our website, or schedule a demo with one of our 3D printing experts.
A Beginner's Guide to 3D Printing
3D printing is an additive manufacturing process that uses thin layers of filament (in most cases, plastic) to create a physical object from a three-dimensional model. A digital file creates the model which eventually transfers to the printer. The 3D printer creates thin layers, one on top of another, until a 3D printed object is formed. 3D printing also allows the production of models of more complex shapes with less material than traditional manufacturing techniques.
Research shows that 3D printing was first introduced in the ’70s. It was not until 1980 that early additive manufacturing equipment and materials were developed. Hideo Kodama initiated a patent for this technology but, unfortunately, never commercialized it. In the ’90s 3D printing began to attract attention from technologies around the world. These years also saw the invention of fully functional human organs for transplants in young patients using 3D printed methods covered with particles and cells from their very own body. It was a major success for the medical industry.
Despite these advancements, 3D printing had limited functional productions until the 2000s, when additive manufacturing gained popularity. Additive Manufacturing is the process of adding materials together to produce an item. The procedure of additive manufacturing is in stark contrast to the concept of subtractive manufacturing. Subtractive manufacturing is the process of removing material by carving out a surface to create an object. This process also produces a great deal of material waste. In this regard, the term 3D printing still refers more to technologies that use polymer materials and, additive manufacturing refers more to metalworking. But by the early 2010s, the terms of these two processes were used in popular language across the market, media, companies, and manufacturers.
Around 2008 the first self-replicating 3d printer model was created. That means a 3D printer was able to recreate itself by printing its parts and components. This enabled users to produce more printers for others. Studies show that later the same year, a person successfully walked with a 3D printed prosthetic leg fully printed in one piece. Then in the 2010’s the additive processes matured, and 3D printing work began to create objects layer by layer. In 2012, with the addition of plastic and other various materials for 3D printing, several authors began to think that 3D printing could be important for a developing world.
During the following years, more applications for 3D printing have emerged, including the world’s first aircraft. Makers using 3D printers agree that this method is faster and cheaper compared to traditional methods and are ideal for those who need rapid prototyping (RP). Terms such as desktop manufacturing, rapid manufacturing, and rapid prototyping have since become synonymous with 3D printing.
The market offers a wide variety of 3D printers. Sophisticated machines are expensive, but there are also more affordable models available with high-quality printing and features. 3D printing also offers easy-to-use desktop printers, which are increasingly popular among schools and engineers.
How Does 3D Printing Work?In a shell, 3D printing works by blending layers of material to build an object. In this process, the 3D printer works with the direction of a computer 3D modeling software that regulates the process with high precision and exactness.
The 3D printing manufacturing includes several types of manufacturing technologies, all these work in the same way by creating models’ layer by layer essentially. Each one of these types of 3D printing manufacturing processes may utilize a different type of material, finish, and cost.
Some of the most common and utilized types of technologies are FDM, SLS, SLM, SLA, and DLP. Below read on a summary of each one of these technologies.
Let us start with the most common of these, the FDM or Fused Deposition Modelling, this is a trading name given by Stratasys. Even though this concept has been around since the ’90s, a lot of 3D printers since 2009 starting to utilize this process. This technology is also known as FFF (Fuse Filament Fabrication). In this type of process, several layers are aligned together until a shape is formed, by melting plastic that is deposited via a heated extruder. The most common materials used or filaments of this type of process are ABS and PLA.
Another SLS or Selective Laser Sintering uses a laser to sinter powdered plastic material and turn this into a solid model. Normally, this type of technology is a popular choice due to the rapid ability to create prototypes and small-batch manufacturing.
SLM or Selective Laser Melting uses a high-power density laser to melt and fuse metallic types of powder. With his type of technology, the metal material can be fully melted into a solid 3D model. This process also allows for the shape to be created layer by layer and create parts that cannot be easily cast with other conventional methods. The file is sliced into layers on a CAD computer software, normally and .STL file, and then it is loaded onto a file preparation software, then the material is melted using a high- power laser beam until a part is complete.
Continuing SLA or Stereolithography creates parts with high levels of detail, smooth surfaces, flawless finishes, and quality. This type of technology is widely used for applications on the mechanical industry and models.
Finally, DLP or Digital Light Processing is a technique similar to SLA that cures the resin materials by using light through a light projector screen. Because of the light usage, an entire layer can be built at once making this process relatively faster but recommendable for low-volume production runs of mostly plastic parts.
How 3D Printing Works 1.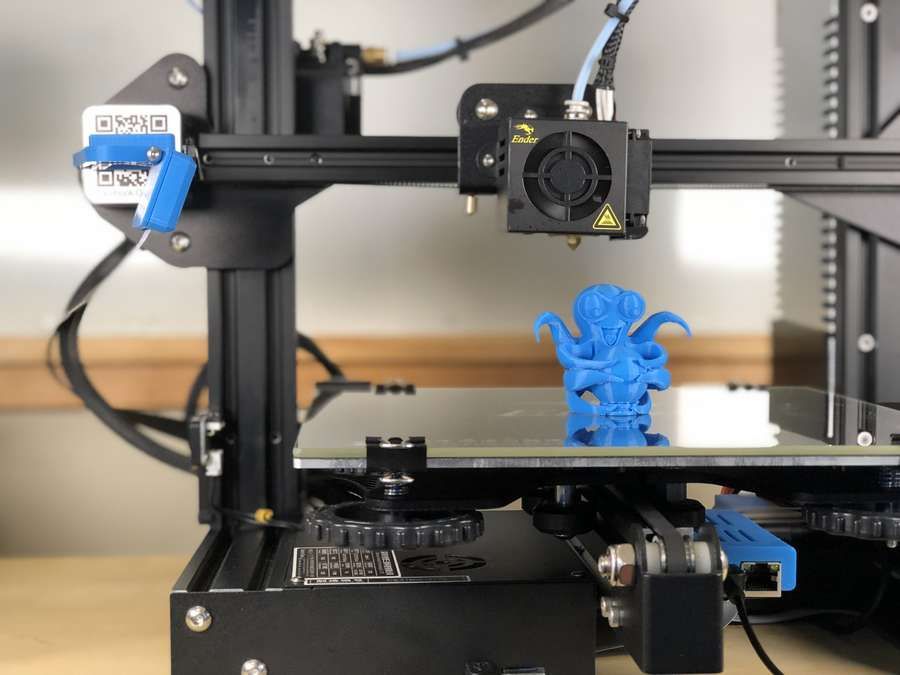
The first step to creating a 3D printed object is creating a virtual design with computer software or a 3D scanner. On this, the exact dimensions of the object to build are simulated to see how this will look like when finishing the 3D printing. When designing a 3D object utilizing CAD, fewer errors may result while printing, and fortunately, these can be corrected before the process. There is also another way of creating an object manually, like sculpting where a 3D scanner is needed to collect the data, shape, and appearance of the desired object.
2. Convert the CAD fileOnce the design is being created, the next thing is to convert the file into a format that can be read by the 3D printer. One of the most common files used is STL (standard tessellation language). STL files may sometimes create a larger file due to the number of surfaces. There is also another option of a file format used named AMF, Additive Manufacturing File format that stores information more conveniently.
Once the STL file is created, and ready to be sent to the 3D printer, the orientation and size for the object to be printed must be set. STL files also allow us to repair any inconsistencies in the original.
4. Prepare the 3D printerOnce the digital file is ready to be printed, all materials need to be ready as well to start the printing process. Once the STL file is ready, then it must be processed by a slicing software that aids in the 3D printing process by converting the object into layers and provides the instructions that later will be received by the 3D printer.
5. Build the objectOnce all the mentioned parameters are ready, the printing process can begin. Some printers may take some time to create the final product as this depends on how complex is the object to print. Many printers have high-end capabilities and print faster. When the process begins, the layers start to build the object with an incomparable resolution using a special measure of micrometers. For instance, the thickness of a typical layer is about 100 micrometers.
Once the object is ready, this must be handled very cautiously. For instance, putting gloves to handle the printed item is recommendable, finally, brush off any residual powder to clean up the piece. One of the advantages of 3D printing is that a piece can be made within hours, compared to traditional processes of manufacturing, this is very convenient and shows faster results.
How does an FFF 3D Printer Work?Fused Filament Fabrication (FFF), is also known under the trademarked term Fused Deposition Modeling (FDM). This technology was invented after SLA (Stereolithography) and SLS (Selective Laser Sintering) techniques were present. The term FFF was initially used as an unconstrained alternative given the fact that FDM is a trademarked term.
To begin with, an extrusion heated nozzle moves over a built platform, at the same time releases molten plastic, then this begins to deposit the thermoplastic material in thin layers, one on top of another onto a print bed, which is where eventually the 3D printed object is formed. The nozzle and the printed bed move while at the same time the plastic is being extruded. In this process, the slicing software is crucial due to this being the one that separates the design into different layers for 3D printing optimization.
3D printing uses a wide range of different variations of materials such as pastes, raw materials, and thermoplastics or filaments, being these the most used and come in different colors, thickness, and sizes to fit the purpose of the 3D printing model. Filament materials used for extrusion include thermoplastics, ABS, PLA, HIPS, TPU, ASA, PETG, PLA, etc.
What can be 3D Printed?3D printing has revolutionized the way models and prototypes are being created for the industry. The idea of rapid prototyping (RP) allows the creation of products usually within hours of days rather than weeks when traditional methods are used. With 3D printing, almost every object you can think of can be printed.
According to Statista, the worldwide market for 3D printing products and services is anticipated to exceed 40 billion U. S. dollars by 2024. This source states that this industry is expected to expand to an annual growth rate of 26.4 percent between 2020 and 2024.
3D printing can create a wide range of applications. Every day, new materials and applications are being discovered and therefore, more companies are relying on this method for quicker prototyping and production of items, including the fact that they already have their printers.
3D printing is actively involved across many important industrial organizations with a significant impact on product development, research, education, and more, and is promising to transform almost every industry as we currently know it.
3D Printing in the Consumer Goods IndustryMany companies and retailers are recurring to the usage of 3D printing due to its significant value on the commercial chain. They can customize and design their products in a quicker manner and keep up with the ever-changing consumer market. By producing pieces faster, they are also able to put their products rapidly in the market.
Some companies have used 3D printing to produce eyewear, footwear, lighting design, furniture, and more. Among the brands that have already produced athletic shoes are Nike and Adidas. In an article published by Nike at news.nike.com, they mention how Nike Flyprint is the first 3D printed textile upper-performance footwear. Nike Flyprint uppers are produced through SDM (solid deposit modeling).
Another application is 3D printing in jewelry. According to SmarTech the industry value of precious metals for additive manufacturing is expected to reach $1.8 billion worldwide by 2028. A famous Australian company Boltenstern, has launched a 3D printed jewelry line recently.
3D Printing in the Medical IndustryIn the medical field, 3D printing has a lot to contribute. While donors are difficult to find, in this video published by Marketwatch, the Rochester Institute of Technology’s engineering department is researching new 3D printing techniques for health-care applications such as the capability to generate organs that can be acceptable to the recipient. Allied Market Research shows that the 3D printing market for healthcare is expected to grow at $2.3 billion by 2020.
With the rapid advancement of flexible manufacturing and innovations, 3D printing is now widely implemented for medical purposes, such as implant designs, surgical planning and training, and prosthetics. See here some articles of 3D printing for medical applications, including a most recent case study of how people are using 3D printing to produce masks to fight COVID-19.
With the rapid advancement of flexible manufacturing and innovations in Biomedical fields, 3D printing is now widely implemented for medical purposes, such as implant designs, surgical planning and training, and prosthetics. You can 3D print with thermoplastics like Polycarbonate, semi-flexible plastics, ABS, which is strong and weather resistant or PLA (Polylactic Acid), which will biodegrade over time, even inside a human body. In this case, 3D printing is used in the field of radiotherapy is used to create custom devices for beam range modulation, 3D Conformal Radiation Therapy (3D CRT), or Brachytherapy application.
In this case, spinal surgeries see Increased success rate with 3D printed guides. The Bengbu Hospital is the top-grade hospital in the Anhui Province. Since the end of 2013, Director Niu launched 3D printing application research for vertebrae in the clinical field.
Here is another case, where 3D printing has reduced costs and help the creation of prosthetic hands. Founder Mike Li worked in the IT industry up until 3 years ago when he was inspired by a video that highlighted a unique use of 3D printing for children’s prosthetics. Motivated to apply medical 3D printing for prosthetics to help others, he and other local makers volunteered their time to create and customize prosthetics for patients.
3D Printing in the Automotive Industry3D printing is also transforming the automotive industry, evolving from printing relatively simple prototypes of low production parts to 3D printing entire cars. In-car auto designs, auto parts can also be created using 3D printing. Sometimes, a scale small model is printed to gauge scale before the assembly process. This technique also helps the industry by producing rapid prototypes and reducing money and time for production. Some other automotive companies are dedicated to creating customized auto parts for special model cars. Read here more case studies about 3D printing in the automotive industry.
In the aerospace industry, 3D printing has remarkable uses as well. To name a few, Airbus is utilizing 3D printing technology to create plastic parts on commercial A310 and A350 XWB test aircraft. In this video, metal parts for wing slats, a section of the tail wing and door hinges are claimed to be produced by this company. The development and manufacturing of potential parts using 3D printing can be conceived as lighter, stronger, and with 70% less time to make it and 80% less expensive compared to others. Aside from this, Airbus also mentions how 3D printing contributes to the environment as it has reduced up to 95% of its metal waste.
Research shows that the market for 3D printing dental applications is expected to grow significantly. Dental 3D printing applications include the creation of crowns, aligners, bridge models, retainers, and even orthodontic models. Read here about Dental 3D printing in Orthodontic models.
3D Printing for ProstheticsThe impact of 3D printing on the medical field has made positive advancements such as fast processing times, low costs, and the ability to create efficient prototypes and parts that require customization, such as 3D printed implants and prosthetics. 3D printing is producing hands, feet, legs, and more.
Albert Fung, a talented biology illustrator from Canada, first designed a CAD template for the initial prosthetic. Using this as a base, he and his team were able to optimize the model for each patient’s situation.
An organization named e-NABLE is currently doing work in this area. Albert Fung and Dr. Choi created five versions of the initial prosthetic design and optimized the design to accommodate individuals in Sierra Leone within one year. Read here a 3D Printing prosthetics case study.
In this field, 3D printing allows us to quickly create an architectural model, and this is ideal because a physical model is much favored than a computer presented a model on the screen. Any architectural application can rapidly create scale models in a faster and cheaper way now. There are also other astonishing applications of 3D printing in the architectural industry, to name a few it is possible to create entire buildings and urban structures. In Madrid, Spain the first 3D pedestrian bridge was printed. This structure crosses a stream in Castilla-La Mancha Park in Alcobendas, Madrid. The structure is printed using micro-reinforced concrete and measures 12 meters in length and 1.75 wide.
3D Printing in Archeology3D printing for museums and archeology is helping with the reproduction of exact copies of artifacts that can travel the world to help researches in their developments. Archeological pieces can also be scanned and created for students to do research. This technology is widely used by museums because ancient pieces are at a high risk of being broken or damaged when transported and by the usage of scanning and 3D printing, restoration is possible. This including fossil reconstruction.
Although restoration is a field dedicated to preserving the past, some sculptors are turning to 3D printing to help facilitate their restoration work. A great example of this is the Scuola di Alta Formazione (SAF) of the Instituto Superiore per la Conservazione ed il Restauro (ISCR). This institute is the leader of the restoration of masterpieces of the Italian heritage. Teachers at the institute decided to use 3D scanning and 3D printing with excellent results for their restoration projects. Read here 3D printing in the restoration of Italian classical art.
Another example of this great use is a project called “Elastic Minds” by the MOMA, the Museum of Modern Art in New York, the artists were using 3D printing in a project to create art and furniture such as chairs at a complete scale. In this video about the exhibition, pieces of furniture were created by sketches in the air with laser technology and then a camera scans this to capture the movement and captures this as a drawing that then is sent into a 3D printer machine.
In forensics, the usage of 3D printing is creating a breakthrough in solving cold case files, by printing skulls, shoe prints instantly, and more. Daryl Ricketts is a forensic anthropologist and a professor of anthropology at Indiana University that uses 3D printing for education and research purposes. He uses the resources of 3D printing to create forensic pieces for his students. By using CT scans, fetal specimens, fetal skeletons to do virtual autopsies. He also uses facial 3D printing for facial reconstruction from different hominids.
Furthermore, at the University of South Florida, forensic artists have sculpted 3D printed skulls with clay to reconstruct the faces of more than 900 missing and unidentified homicide victims. In this video published by CNN, artists from around the world work along with the Forensic Anthropology Laboratory to reconstruct faces to identify these victims.
In the film industry, movie labs and companies now are using more widely the technology of 3D printing for makeup preps and special effects to create characters. As an example, artists Steve Yang and Eddie Wang from Alliance Studio are using 3D printing for a new era of special effects and sculpture creation. In this video, they shared their story of how they started to work with 3D printing when everything was using traditional methods and how this technology changed their way of creating things in a way that was not seen before.
Also in this article, Rick Baker the Star Wars famous makeup artist uses 3D printers for the creation of monsters and props. Rick Baker has been able to create parts and scaled copies of his movie characters by using the technology of 3D printing. This technology along with the digital design has helped to decrease the overall time spent for the creation of the movie models.
Many companies around the world are using 3D printing to create exceptional high-precision models for prototyping and industrial manufacturing. 3D offers a less expensive and a very affordable process due to most models being produced using plastic and other variety of materials. Moreover, this innovative method utilizes less material for manufacturing and prototyping compared to traditional techniques.
3D Printing in EducationIn the fields of education, there are countless applications of 3D printing technology with such interesting applications. The past decade has seen explosive growth in STEM education in progressive schools, as theoretical textbook knowledge is being replaced by experiential, project-based learning. When students shaped by this innovative learning ecosystem join the workforce, they are scaling new heights to help transform our manufacturing processes as well. Where appropriate, additive manufacturing technologies like 3D printing are now replacing traditional methods to bring more flexibility, design innovation, and cost savings to production processes.
For instance, in this case Lift 3.0 is using 3D printers in Russia to teach kids the value of additive manufacturing with remarkable results.
Traveling to California, here is the case of John Gardner is a student at Foothill High School in Tustin, CA, who has a great passion for engineering and technology. Once introduced to 3D printers he began to develop his prototypes for an electric skateboard, custom-fit prosthetic limbs, and more. If you are interested in more cases of 3D printing in education, visit here.
Many companies around the world are using 3D printing to create exceptional high-precision models for prototyping and industrial manufacturing. 3D offers a less expensive and a very affordable process due to most models being produced using plastic and other variety of materials. Moreover, this innovative method utilizes less material for manufacturing and prototyping compared to traditional techniques.
To learn more about, why companies are using 3D printing, click here
How to Print with a 3D Printer?
3D printing is changing the way that objects are being produced. To start in the process of 3D printing, you will need to take some steps and considerations. Read on a few below to have an idea of what you need to set up your creation!
The first step is to contemplate your 3D printer options and choose the one that better fits the purpose of your needs. There are a lot of alternatives and manufacturers, you can always compare models, but make sure to choose a printer that has the right features for your projects and plans.
For instance, there are 3D printers that are affordable and rightly designed for education, engineering, and small-batch manufacturing. Make sure your printer has dual extruders that can print simultaneously for a better production capability. This way you can reduce printing time for rapid prototyping. There are particularly good printers that also come with high-resolution cameras, video-assisted calibration systems, and important safety features.
Some other 3D printers are made to build larger industrial originals. These printers are more advanced and have fully enclosed capabilities. Industrial grade 3D printers permit the printing of complex parts and support a variety of filaments and improve even more printing speed. If you need to choose a printer like this, make sure it offers characteristics such as motion controllers, remote user interface, and interchangeable nozzles. If you are looking for a more comprehensive guide on how to choose a 3D printer, visit our 2020 printer buying guide.
Step 2: Choosing a 3D Slicing SoftwareTo create a 3D printed object modeling software is needed. There are a lot of websites and providers that offer free downloadable software programs to design and model, and others that offer a variety of 3D models or mockups that other people have used to create their replicas. Research and look for a slicing software that is intuitive, user-friendly, and has customized advanced features. One important point too is to make sure that the software that you prefer also supports a multi-lingual interface in case you need it.
The next step is to set the design ready for the printer. When the printer receives the data from the software it sends the signal to the printer to start building the item using a filament that is like a cord that passes to the plates of the printer. The most commonly used file format for 3D printing designs is STL, (Standard Triangle Language). The original design when being printed is translated into several triangles in a 3D printing space, which sets up for the printers and related hardware to construct the resulting object. The resolution of a file is recommended to be in an optimal size so the machines and software can work smoothly to create your final product.
In this last process, the object is created through layering. One layer by another is added until the shape and final object is formed. The process of repeatedly printing over the same area is called Fused Depositional Model (FDM). The most common material for 3D printing is plastic, but there are a lot of other materials that can be used and adopted by 3D printers such as PLA, ABS, HIPS, carbon fiber enforced, flexibles, and much more.
Where to Find 3D Printing Files?If you are looking to obtaining files for 3D printing, there are a lot of websites that offer these files, some of them for free. A variety of STL files, 3D printed models, 3D printed files and 3D printing designs in other file formats can be found if you surface the website. Shown below, here is a brief list of some sites that provide files and resources for 3D printing.
- ALL3DP visit site.
- Pinshape visit site.
- MyMiniFactory visit site.
As time progresses, there are more and more uses for 3D printing that shows light of phenomenal events thanks to the usage of 3D printers. Many people believe 3D printing will announce a revolution in the manufacturing industry and the world economy. Although 3D printing has certain limitations, this advanced technology is now universally adopted by big corporations as a crucial mainstay of the manufacturing industry.
Connect with Raise3D:
Have you had a great experience with Raise3D that you would like to share? Please contact us at [email protected]. We look forward to hearing from you.
For more information about Raise3D printers and services, browse our website, or schedule a demo with one of our 3D printing experts.
The Complete Guide to 3D Printing [Part 2]
3D printing is used in a variety of industries, both for rapid prototyping and short-term production.
A key application of 3D printing in various industries is the rapid prototyping of new parts during R&D. No other technology has the capability to instantly produce plastic or metal parts - even in non-factory conditions.
3D printers can be used in-house by companies, while some businesses prefer to order 3D printed prototypes through service bureaus.
Medical
3D printing can be used to make medical components such as titanium implants and surgical guides (SLM), 3D printed prostheses (SLS, FDM) and even 3D bioprinted human tissues. Components for medical equipment and technology - X-ray machines, MRI, etc. - can also be made by 3D printing.
SLA and SLS technologies are also widely used in the dental industry for model making, prostheses and restorations.
Aerospace industry
The aerospace industry has become a major consumer of 3D printing technology because it can produce very light parts with an excellent strength-to-weight ratio. Examples include things as simple as cab bulkheads (SLS) and down to revolutionary engine components (SLM) such as the 3D printed fuel injector tip designed and manufactured by GE.
Cars
Automotive companies regularly use 3D printers to make one-off parts and repairs, as well as rapid prototypes. Common 3D printed automotive parts include brackets, dashboard components and antennas (FDM).
More extreme examples include cars with large 3D printed metal structural components, like early models from automotive startup Divergent.
Jewelry and art
3D printing technologies such as SLA are widely used (as an indirect fabrication process) in the production and repair of jewelry, while almost all types of 3D printers can be used to create art and sculpture.
Construction
Advances in additive manufacturing with high quality workmanship have expanded the scope of applications in construction and architecture. Concrete 3D printing, which is a bit like FDM but with very wide nozzle extruders, plays an important role in this industry, but more common 3D printing technologies such as SLM can be used for products such as bridge structures.
3D printing file formats:
3D printing parts can be designed with standard CAD software, but 3D printers can only read certain file formats. There are four main file formats for 3D printing.
STL: The most common file format for 3D printers, STL contains part geometry information in the form of tessellated triangles. It does not contain information such as color, material, or texture. The file size is proportional to the detail, which can be a problem.
OBJ: Less common than STL, the OBJ file format encodes the geometry of a 3D model and can include curves and free-form surfaces in addition to tessellation. It can also contain color, material, and texture information, making it useful for full color processes.
3MF: Invented by Microsoft, 3MF is an XML-based format with small file sizes and a good level of error prevention. It has not yet been widely adopted, but is supported by companies such as Stratasys, 3D Systems, Siemens, HP, and GE.
AMF: The successor to the STL format, AMF is much more compact and allows you to tessellate both curved and flat triangles, making it much easier to encode parts of various shapes. Since its inception, the format has been slowly adopted.
3D printing settings and specifications:
3D printing uses specific terminology that may not be clear to beginners. These terms refer to printer settings and/or specifications that can affect how 3D printed parts turn out.
Infill
When making 3D printed parts, it may be necessary to specify an infill percentage, which refers to the internal density of the part. A low infill percentage will result in a mostly hollow part with minimal material holding the mold together; a high infill percentage will result in a stronger, denser, and heavier part.
Layer Height
Layer height, sometimes referred to as z-resolution, is the distance between one 2D part layer and the next. A smaller layer height means finer resolution (and higher possible level of detail) along the z-axis, i.e. top down. A low layer height is an indication of a high quality printer, but users can set a higher layer height for faster, more economical printing.
Print speed
The printer's print speed, measured in millimeters per second, indicates the speed at which the machine can process the source material. Like the layer height, this value can either be a measure of the printer's maximum speed or be user-defined: slower print speeds usually result in more accurate prints.
Print temperature
When applied to processes such as FDM, print temperature usually refers to the temperature of the hot end, the part of the print head that heats the thermoplastic filament. Some FDM printers are also equipped with a heated print bed, the temperature of which is specified by the manufacturer. In both cases, the temperature is usually controlled by the user.
Resolution
In 3D printing, resolution almost always refers to the smallest possible movement along the X and Y axes (width and depth) of either the laser beam (SLA, SLM, etc.) or the print head (FDM). This value is more difficult to measure than the height of the layer, and it is not always proportional to it.
Shells
Like wall thickness in injection molding, shell (or shell thickness) refers to the outer wall thickness of the 3D printed part. When 3D printing, users usually have to choose the number of shells: one shell = outer walls as thick as a 3D printer nozzle; 2 shells = twice the thickness, etc.
Color 3D printing:
Since 3D printing is primarily used as a prototyping tool, single color prints are sufficient for most applications. However, there are several options for color 3D printing, including high-end material inkjet printers, multi-extruder FDM printers, and post-processing options.
Inkjet Printing Technologies
Major 3D printing companies such as Stratasys, 3D Systems and Mimaki have developed 3D inkjet printers for printing materials and binders that can print 3D models in full color as well as 2D inkjet printers. However, these machines are expensive and the parts do not always have excellent mechanical properties.
Multiextrusion
Several FDM 3D printers are equipped with two (or more) printheads, allowing you to simultaneously print on two spools of filament - different colors or even different materials - within the same print job. It's simple and affordable, but usually limited to two colors.
Filament replacement
Single extruder FDM 3D printer can produce multi-color prints. To do this, you need to pause printing at certain points and replace the spool of thread with a thread of a different color. This is a very slow method of applying color and does not allow precise control over where each color goes.
Adding color after printing
Many 3D printed parts can be dyed, tinted or painted after printing. While this adds another step to the process, it often strikes the best balance between quality and economy.
Post-Processing 3D Printed Parts:
Many 3D printed parts require at least some level of post-processing after leaving the print bed. This may include important processes such as the removal of supports, or additional cosmetic processes such as painting. Some processes apply to all or most 3D printing technologies, and some are specific to a particular technology.
Support Removal
3D printing technologies such as FDM and SLA require the installation of support structures (vertical struts between the printed layer and the part itself) so that the printed object does not collapse during the manufacturing process.
These supports must be removed when the part is finished. Some printers, such as dual-extrusion FDM machines, can print support structures from dissolvable material, allowing the supports to be easily detached from the part using liquid chemicals. Insoluble supports must be manually cut from the part, leaving a mark that may need to be sanded down.
Washing and removing the powder
Some 3D printing technologies (such as SLA) leave sticky marks on parts, while others (SLM, SLS) may leave powder marks. In these cases, the parts must be washed - manually or with a special machine - or the powder removed with compressed air.
Heat treatment
Many of the key 3D printing technologies print parts from materials that are not yet in their final chemical state after leaving the printing mold. Such details are sometimes called "green".
Many 3D printed metal parts require heat treatment after printing to increase layer fusing and remove contaminants. And bonded inkjet 3D printers, for example, produce parts that need to be stripped and sintered after printing to remove resin bond layers from inside metal parts.
Some 3D printed resin parts require post-curing after printing to increase their hardness and make them usable.
Surface Treatment
3D printed parts can be subjected to a wide range of surface treatments, from textural treatments such as sanding and smoothing, to visual treatments such as painting and toning. Some technologies, such as FDM, can create a rather rough surface that requires sanding, while others, such as SLA, produce a much smoother surface.
Combination of 3D printing with other technologies:
3D printing does not have to be used as a separate process. Rather than being seen as a competitor to CNC machining and injection molding, it can actually complement these and other manufacturing processes.
Combination examples include:
- 3D print the main body of the part and then CNC mill the thin parts to tighter tolerances;
- 3D printable master pattern for investment casting or vacuum casting;
- 3D print the part and then injection mold it using injection molding.
There are hybrid manufacturing systems that combine 3D printing with other technologies. For example, Mazak's INTEGREX i-400 AM and DMG MORI's Lasertec DED can perform both 3D printing and CNC milling.
Will 3D printing replace other manufacturing processes?
Analysts have long speculated about whether 3D printing could replace other manufacturing processes, including:
- Processing;
- Molding;
- Casting.
However, despite the desire of AM equipment manufacturers to position 3D printing as an end-to-end manufacturing technology, in practice, 3D printing is still limited to some specific manufacturing operations, especially low-volume production of specific materials.
In some areas, 3D printing has certainly overtaken other processes. For example, rapid prototyping with inexpensive plastics like ABS now dominates 3D printing, as ABS is cheaper to print than machined. 3D printing also seems to have established itself as the ideal tool for making objects such as patient-specific titanium medical implants: the speed and geometric flexibility of 3D printing is hard to beat in these specific situations.
In addition, 3D printing is an ideal tool for making objects such as patient-specific titanium medical implants.
Despite this, processes such as CNC machining currently remain the best for producing high quality parts and prototypes from engineering materials such as POM, PEI, PPS and PEEK, with surface finishes far superior to 3D printing. . In addition, processes such as injection molding are still infinitely faster for mass production of simple plastic parts.
In addition, although additive manufacturing is one of the most significant technological advances in manufacturing, which allows it to take a stronger position in manufacturing in general, more established processes such as CNC and injection molding are also being improved to produce higher quality parts. .
3D printing will continue to take an increasing share of manufacturing jobs, but it will not completely replace other technologies.
What did 3D printing look like 10 years ago?
A decade ago, the nascent 3D printing industry was gearing up for what it believed would be a 3D printing revolution: a 3D printer in every home, allowing families to print new items they might need, such as a spare part for a refrigerator, a new toy for kids, or even components to build a second 3D printer.
In 2012-2014, FDM 3D printer manufacturers such as MakerBot actively promoted their 3D printers in the consumer market, trying to convince ordinary people that a 3D printer can improve their home life and work. However, it was clear that these companies were trying to exploit the novelty factor of 3D printing and that their products had no practical application; a 2012 MakerBot press release seems to prove it: Make an entire chess set at the touch of a button. Friends, classmates, colleagues and family members will see what you are doing and say "Wow!".
Just a few years later, this so-called 3D printing revolution clearly failed, and many 3D printer manufacturers began to rethink their goals, moving from consumer to professional and industrial markets, where there were more concrete (and profitable) applications of additive technology.
In addition, those who were already working in the professional and industrial fields - companies such as 3D Systems and Stratasys - began to try to destroy the idea of 3D printing as a prototyping technology, positioning it as a viable mass production tool (which, obviously, , could be more profitable for the 3D printing industry, as manufacturers would have to fill entire factories with 3D printers, buy 3D printer management software, and hire 3D printing consultants).
What will 3D printing look like in 10 years?
3D printing companies have abandoned the prospect of putting a 3D printer in every home. However, in 10 years, they can expect some form of additive manufacturing to appear in more factories.
Although there is less talk about 3D printing today than in 2012, the technology continues to gain momentum in the professional and industrial world.
According to a recent report, market research firm 3DPBM Research expects the value of additive metal manufacturing to rise from $1.6 billion in 2020 to $30 billion by 2030, and this is largely due to the repositioning of AM as a manufacturing tool and the development of more high-performance engineering materials. (That said, 3D printing will remain a valuable prototyping tool in many industries, and prototyping applications will benefit just as much from technological advances.)
However, not only metal AM is being developed. Technologies such as HP's Multi Jet Fusion have opened up new possibilities for plastic printing, and innovators such as Carbon have developed new high-speed processes in the photopolymerization category. Niche areas such as 3D bioprinting and micro 3D printing are also regularly opening up new opportunities, and composite 3D printing (such as continuous carbon fiber 3D printing) is also on the rise: IDTechEX predicts that by 2030, the market size of composite 3D printing will be $1.7 billion
In short, 3D printing will gradually become a serious competitor to other manufacturing processes in many disciplines.
How to outsource 3D printing services?
Investments in 3D printing hardware and software are not suitable for all businesses, so many successful companies outsource their 3D printing needs to third parties, such as online 3D printing service bureaus (for one-time projects) or prototyping partners and production, such as 3ERP (for one-time projects or repeat orders).
When outsourcing 3D printing services, it is important to consider whether your business needs design and manufacturing services or just manufacturing services. (Keep in mind that a poorly executed 3D model may fail for 3D printing).
In general, though, ordering 3D printed parts from a third party is easier than ever. Many manufacturers can start 3D printing with just a digital 3D model, although more important projects may require a technical drawing to communicate additional information such as materials, colors, and tolerances. Some 3D printing service providers (including 3ERP) will offer advice on suitable 3D printing technologies and materials for your project.
Explore our full range of 3D printing services, including available technologies and materials, or request a quote for your 3D printing project.
Transparent 3D Printing Guide
Stereolithography (SLA) 3D printing can produce transparent objects that, after some post-processing, become optically transparent.
Formlabs' latest stereolithographic 3D printer, the Form 3, improves model transparency by using an elastic resin reservoir that reduces forces on the model, resulting in smoother, more transparent parts. 3D printing on a Form 3 in Clear Resin is a great way to produce parts that require light transmission and, with the right post-processing techniques, transparency.
The following processing methods can be used to 3D print transparent parts for a variety of purposes, from optical devices to light guides and liquid elements. Techniques range from quick solutions to obtain sufficient transparency to specialized techniques for creating optically transparent parts.
Clear and transparent 3D models are ideal for creating transparent prototyping elements, showing internal cavities and details, making LED housings or windows. Formlabs and our customers have used Clear Resin to create an optically clear 100% 3D printed camera lens, Times Square Fresnel lens tiles, light guides, prisms, millifluidic devices, and more.
Formlabs application engineer Amos Dudley designed and 3D printed a lens for a fully 3D printed camera.
Curious to see for yourself what a transparent SLA 3D printed part looks like? We will send a free transparent 3D printing sample directly to your office.
Request a Free Sample
We have tested several post-processing methods for 3D printed Clear Resin parts. In this article, we will cover hand sanding, spray clear coating and resin impregnation. Each treatment option requires a different amount of effort, depending on the required degree of transparency and surface quality.
Application of : Hand sanding and polishing can be effective on simple models with few fine details, but not very suitable for complex models. With this method, it is very difficult to achieve complete optical transparency.
Hand sanding will require you to sand with very fine grit sandpaper, but with some effort you can sand and polish the parts to the transparency level of a magnifying glass. However, it is very difficult to completely remove all the layer lines with manual processing - if you turn the part at a slight angle to the light, you can notice micro-scratches.
Instruction : Use sandpaper to smooth the surface, then polish the part with acrylic cleaner and a microfiber cloth.
With approximately 3000 grit sandpaper, transparent SLA 3D printed parts become glossy and very smooth to the touch. After sanding with 12.000 grit, they reflect light. Try different sandpapers and abrasive sheets from 400 to 12,000 grit in 200 increments. Before moving on to the next grit step, slowly and carefully clean the lens and remove scratches from the previous level of sanding.
Our support site offers a simple step-by-step manual sanding guide that includes an acrylic spray finish.
If all you need is translucency, mineral oil will suffice to create a smooth surface and hide light spots.
We have tested various polishing methods for transparent 3D models, from hand sanding and spray coating to resin impregnation.
Application of : Spray coating is a quick and easy way to improve the transparency of details without significantly reducing detail. The method is effective for all types of models, since it is possible to spray the coating on complex-shaped parts, which can be difficult to grind and polish.
Clearcoat application helps to hide layer lines and protect parts from UV exposure which can cause yellowing and unintended final cure. If you require a smooth, glass-like surface, hand sand and polish before coating; the more thorough the sanding before applying the clear coat, the better the clearness. This extra step is great for post-processed prototypes that look like completely transparent plastic, such as packaging, bottles, and microfluidic devices.
Instruction : A variety of aerosols can be used to apply a clear coat, from inexpensive sprays to products that require a separate room and tools.
- General purpose clear aerosols: : The selection ranges from good, very inexpensive options like Rustoleum Painter's Touch 2X to affordable high quality aerosols like Spray Max 2k Clear Glamor.
- Automotive sprays : Products such as Lesonal Universal Clear, a high solids acrylic urethane clear coat, give a very good glossy effect.
They are designed for air drying and stoving and require a spray gun and free space to spray. A base coat must be applied before applying Lesonal Universal Clear and similar aerosols.
Coat a clean, dry model already rinsed in isopropyl alcohol (IPA). Do not finalize the model before spraying as this may cause yellowing. Air dry the model. Once it is completely dry, apply two to three coats of spray in a dust-free environment.
For a fee, a finish such as Lesonal Universal Clear can be applied at a workshop. In most cases, bodyshops use a volatile solvent such as naphtha to clean and prepare the surface of the model prior to spraying.
For the Times Square installation, Window to the Heart, Formlabs and Aranda/Lasch spray-coated the tiles with Lesonal Universal Clear in an auto body shop.
Application of : This method is best suited for applications where very high transparency of parts is required and can only be applied to flat or nearly flat surfaces such as lenses or "windows" into the interior of the part.
Resin immersion produces very smooth details with crisp and sharp surface reflections.
The method can be used to increase the smoothness of parts printed with other SLA materials, although it may reduce detail.
Instruction : Apply Clear Resin to the part using a syringe or by dipping the part into the resin, as desired. The viscous polymer will fill in the delaminations and scratches present on the part, forming a completely smooth surface.
The resin layer should be as thin as possible while still eliminating layer lines. Remove all bubbles with a syringe. Completely cure the part using the appropriate parameters, then repeat the process on the other side, both dipping and final curing.
Lens subjected to a 3-step polymer immersion procedure, final result on the left.
The polymer immersion process slightly changes the focal length of the lenses. Formlabs Applications Engineer Amos Dudley designed and 3D printed a lens tester to create a fully 3D printed camera.