Industrial 3d printers comparison
The Complete Industrial 3D Printer Buyer's Guide 2022
Industrial 3D printers are increasingly replacing injection molding and other processes like CNC milling as the go-to option for small production runs and rapid prototyping. 3D printers can create incredibly detailed and intricate parts as well as full-size models, making them perfect for prototypes and high-quality part production.
- Note: you may instead be looking for our ranking of the most valuable 3D printing companies.
How much does an industrial 3D printer cost?
Industrial 3D printer price really depends on the quality and type of 3D printer you’re using, and what you’re planning to produce or prototype.
There are resin 3D printers such as the Formlabs 3 that sell for $3,499 that can print industrial quality pieces in sectors such as dentistry, education, medical, and jewelry, and other printers such as the Ultimaker S3 and S5, Makerbot Method, Intamsys Funmat HT, and others that cover the prosumer 3D printer market.
Beyond this, there are machines costing between $10,000 to $100,000, such as FDM 3D printers like the BigRep Studio, and Markforged’s Metal X metal 3D printer, and premium industrial 3D printers such as those sold by EOS, Carbon 3D and Desktop Metal that can cost hundreds of thousands of dollars.
We have recommended lower-end industrial 3D printers starting from the $3,000-$6,000 range, as well as higher-priced commercial machines.
How to decide which industrial 3D printer to buy?
There are several factors to consider, most notably:
- Size: consider both the industrial 3D printer’s size in terms of build volume (maximum size of parts you can print), and the total area the printer encompasses. You may not have the space to store the printer, or need the extra build volume.
- 3D printing technology: there are a range of technologies within 3D printing, which we explain in our free 3D printing eBook. Do you prioritize cheap part printing, or extremely detailed surface quality? These will determine which technology you need, and therefore which industrial 3D printer to buy.
- Materials to print: are you looking to 3D print polymers like PLA, ABS or Nylon? If so, you have options between FDM (all 3), or SLS (Nylon). If you’re looking to 3D print metal materials such as aluminum or titanium, you’ll have to buy a DMLS, EBM, Binder Jetting or other type of metal 3D printer.
- Speed: some types of 3D printers print much faster than others, even within the same technology. DLP 3D printing is typically faster than SLA, and delta 3D printers are almost always faster than Cartesians.
- Does it require a trained operator: expensive, complex and high-quality industrial 3D printers often require a skilled operator to ensure the printing process goes smoothly and the correct temperatures are maintained. This adds to costs but may be necessary for your prototyping, and is something to keep in mind.
- Resolution: different 3D printers have different levels of accuracy, precision and resolution.
Resin 3D printers are more accurate than FDM 3D printers, and material jetting printers have some of the highest resolutions of any industrial 3D printer available on the market today.
- Ability to print full color: some 3D printing technologies are limited to a single color based on the metal / polymer powder, filament or resin, whereas some can print in full color such as Binder Jetting and Multi Jet Fusion.
The best industrial 3D printers we recommend
Based on our advice and criteria, here are some of the industrial 3D printers we recommend. Where possible we have provided options that are affordable to small and medium-sized businesses that do not run into the hundreds of thousands of dollars.
Raise3D Pro2 Plus — Great affordable yet large industrial 3D printer
- Build volume: 305 x 305 x 605 mm
- Price: $5,999 — Available on Dynamism Store here / Available at Matterhackers here
Raise3D offer both the Pro2 and the Pro2 Plus as industrial FDM 3D printers offering fantastic reliability, accuracy and versatility – with the Pro2 Plus offering a larger 605 mm Z-axis for tall parts compared with the Pro2’s 300mm.
The printer can print with 100-micron resolution, has an industrial build plate to prevent part warping, and a fully enclosed chamber to keep printing conditions consistent. The dual extruder allows for multi-material printing, such as for supports or for any rapid prototyping that requires two different colors.
The 7-inch touchscreen features a very ergonomic UI and provides useful on-screen visualizations during printing. Moreover, if you do have any problems Raise3D has US-based tech support to provide solutions.
The maximum temperature of 300C creates a lot of opportunities for filament printing; the Raise3D Pro2 Plus can print not only standard 3D printer filaments like ABS, PLA, PETG, Nylon, but also carbon fiber infused, metal-filled, and glass-infused filaments. You can connect wirelessly using IdeaMaker – Raise3D’s 3D slicer software – to control and monitor printing remotely.
Ultimaker S5 & S5 Pro Bundle
- Industrial 3D printer build volume: 330 x 240 x 300 mm
- Price: $5,499 for the S5, $9,000 for S5 Pro Bundle — Available on Dynamism Store here / Available on Matterhackers here
- Weight: 20.
6kg
Ultimaker staked their claim as kings of the prosumer 3D printer market with the Ultimaker 3, winning awards and reaching new heights of success. The S5 was a step up into a higher price bracket, featuring a number of key upgrades and even better print quality.
Costing $5,499, the Ultimaker S5 moves up into the industrial FDM 3D printer price range, but that gets you up to 20-micron layer resolution. Incredibly accurate and intricate prototypes and parts can be printed to test functionality and shape, with partners including VW, Siemens, L’Oreal and Ford clearly seeing benefits to their production by using Ultimaker 3D printers. It can even print high-strength glass and carbon fiber filaments, with the latter especially having key applications in strong prototype and part production.
The 4.7-inch touchscreen is easy to use and has won design awards, and you can print with Ultimaker filaments or any third party 2.85mm filament — the S5 features an open filament system. Some architects have used the Ultimaker combined with a Palette to create multi-color architectural model prototypes.
Ultimaker also sells the Ultimaker S5 Pro Bundle, featuring an S5 as well as an Air Manager that goes on top of the printer that captures 95% of ultra-fine particles, and a Material Station that goes underneath the printer. The Material Station can hold up to six filament spools and can automatically switch between each one dependent on what material or color you need to use.
This allows for far more scalable and continuous printing — Ultimaker sells it as a 24/7 productivity feature. The S5 Pro Bundle costs around $9,000, and is one of the most highly regarded industrial FDM 3D printers around.The Ultimaker S5 Pro Bundle with the Air Manager on top, and Material Handler underneath.
Formlabs Form 3 — best affordable industrial resin 3D printer
- Build volume: 145 x 145 x 185 mm
- Price: $3,499 — Available on Dynamism Store here
- Weight: 17.
5kg
The Form 2 was already a mainstay in dental 3D printing, medical device printing and in 3D printed jewelry, and the Form 3 expands on this further with several key upgrades.
It uses Low Force Stereolithography (LFS) to provide extremely high quality, precise (up to 25-micron XY resolution), and crisp surface finish prints that are clear and accurate. And for those looking for a resin 3D printer with a larger build volume, Formlabs also sell the Form 3L, featuring a far larger 335 x 200 x 300 mm build volume.
No FDM 3D printer will be able to match the smooth surface area of a Formlabs resin print, making the Form 3 ideal for really precise prototypes – Formlabs show an example of 3D printed glasses on their site – as well as for intricate pieces like jewelry and dental parts, or custom pieces like hearing aids.
Intamsys Funmat HT Enhanced — entry-level industrial PEEK 3D printer
- Price: $7,499 — Available on Matterhackers here
- Build volume: 260 x 260 x 260 mm
The Intamsys Funmat HT has two interchangeable hot ends depending on whether you want to print standard filaments like PLA and ABS, or industrial 3D printer filaments like PEEK and ULTEM. This makes it versatile not just as an industrial or abrasive filament 3D printer, but also as an accurate 3D printer for more standard filaments for everyday rapid prototyping.
Read more: the best PEEK 3D printers
With a 50-micron minimum layer thickness, small businesses and industrial clients will have no problem printing accurate PEEK, Nylon, or other material parts. The Intamsys Funmat HT offers a great alternative to using 3D printing services to 3D print PEEK and other industrial filaments, costing around $6,000, far less than previous industrial PEEK 3D printers.
The Funmat HT’s low price and effectiveness has seen it used to 3D print aerospace, automotive, engineering, and medical sector parts. It is also used in general R&D, and overall is considered a great 3D printer, offering industrial 3D printing on a smaller scale and the 3D printing of the toughest filaments around, at far more affordable prices.
Sinterit Lisa — Entry-level industrial 3D printer using SLS
- Build volume: 110 x 150 x 150 mm (For TPU)
- 90 x 130 x 130 mm (for Nylon/PA)
- Price: €7,999
- Weight: 41kg
The Sinterit Lisa is one of the lowest cost industrial SLS 3D printers around, bringing all the main advantages of selective laser sintering but without the price tag. Made in Poland, every machine passes a “precisely designed calibration and testing procedure” according to Sinterit.
The main advantage of SLS 3D printing is that you don’t need to print supports, saving time and money on powder. You can also print multiple parts concurrently in the build platform, and so is perfect for businesses printing multiple parts at once, or printing many similar parts that are slightly different to test which prototype is best. The Sinterit Lisa can perform all these functions with ease with its 0.05mm X and Y axis accuracy, and up to 0.075mm Z-axis precision.
Sinterit have designed their own dedicated software, and sell accessories including the Sandblaster as well as specialized SLS powder materials. You can control and print via the Sinterit Lisa’s 4-inch touchscreen, as well as by WiFi or USB.
Desktop Metal Fiber — Most affordable industrial metal 3D printing machine
- Price: Requires a Quote — Available at Dynamism here
- Build volume: 310 x 240 x 270 mm
Desktop Metal, now a public company and who recently acquired EnvisionTEC in a $300m deal, offer one of the most affordable ways to get into industrial metal 3D printing. The Desktop Metal Fiber System can print PEKK, PEEK, or Nylon with continuous carbon fibers or fiberglass to greatly improve part strength.
The Fiber System is still an industrial 3D printing machine, but is far lower priced than previous metal printers. It combines FDM-style filaments with metal, using their new Micro Automated Fiber Placement technology with continuous carbon fibers. Rather than purchasing it outright, Desktop Metal offer leasing options with a yearly subscription, saving smaller businesses upfront costs and making it easier to get started.
Read more: metal 3D printer buyer’s guide
The Fiber mixes these already tough materials like PEEK with carbon fibers, creating astonishing strong — yet lighter than aluminum — parts that can withstand up to 250C temperatures. For a metal 3D printer the build area is also not bad, especially considering the low price compared with most industrial DMLS 3D printers.
Markforged Metal X — Accessible industrial 3D printing metal
- Price: $100,00
- Build volume: 300 x 220 x 180 mm
Markforged’s Metal X 3D printer is one of the most accessible ways to 3D print metal, a very viable alternative when compared with possibly spending hundreds of thousands of dollars on a DMLS or EBM 3D printer.
Using Markforged’s bound powder filament technique, you can print with materials like copper, inconel, A2 and D2 tool steel, and 17-4 PH stainless steel. The Metal X combines FDM-style filament printing with metal, not too dissimilarly to how Desktop Metal have. This makes for a more accessible way to 3D print metal, either for in-house part production and prototyping, or as a service creating reasonable-sized metal parts.
Why use an industrial 3D printer?
Industrial 3D printers are used for rapid prototyping in tandem with 3D CAD software for product design (although occasionally CNC machines are used instead).
3D printers can quickly print small-scale versions of final products to test the design or functionality, with any mistakes able to be instantly changed by editing the 3D model and re-printing the next iteration for testing. Rapid prototyping is frequently used in the aerospace, automotive, and medical sectors.
Since 3D printing is a form of additive manufacturing, there is no waste from removed materials such as with CNC machines. This makes industrial 3D printing very valuable in industries where saving on expensive materials is important, such as metal 3D printing. 3D printers can also create parts with differing infill percentages, leading to lighter yet still very strong metal parts — extremely valuable in the automotive and aerospace sectors where cutting weight can noticeably increase profit margins.
Some other articles you may be interested in:
- The best commercial 3D printers
- The best 3D printers for small business
- Large format resin 3D printers buyer’s guide
How to Choose an Industrial 3D Printer
The 3D printing industry went through its most striking hype cycle during the early 2010s, when promoters claimed that the technology would find broad usage in consumer applications. Away from the frothy consumer 3D printing market, however, additive manufacturing technologies continued to advance rapidly.
Industrial 3D printing technologies have been rapidly maturing in many concrete ways, crossing critical thresholds in print quality, reliability, and cost structure. Recent advances in machinery, materials, and software have made 3D printing accessible to a wider range of businesses, enabling more and more companies to use tools previously limited to a few high-tech industries.
Today, industrial 3D printers accelerate innovation and support businesses in various industries including engineering, manufacturing, dentistry, healthcare, education, entertainment, jewelry, and audiology.
An industrial 3D printer can revolutionize a business, as well as lower production costs and lead times. Here’s how to pick one that best suits your company’s needs.
Industrial 3D printing is available to businesses for a variety of applications, from prototypes to production parts. These technologies include fused deposition modeling (FDM), stereolithography (SLA), selective laser sintering (SLS), material jetting, and metal 3D printing.
A common theme across many of these technologies is the recent appearance of highly capable, but more compact and accessible industrial 3D printers, which helped lower the initial investment costs from $100,000 - $200,000 to often below $10,000.
FDM, also known as fused filament fabrication (FFF), is a printing method that builds parts by melting and extruding thermoplastic filament, which a printer nozzle deposits layer by layer in the build area.
FDM is the most widely used form of 3D printing at the consumer level, fueled by the emergence of hobbyist 3D printers. Industrial FDM printers are, however, also popular with professionals.
-
Advantages of FDM
FDM works with an array of standard thermoplastics, such as ABS, PLA, and their various blends. This results in a low price of entry and materials. FDM best suits basic proof-of-concept models and the low-cost prototyping of simpler parts.
FDM has the lowest resolution and accuracy when compared to other industrial 3D printing technologies for plastics such as SLA or SLS, which means that it is not the best option for printing complex designs or parts with intricate features. Higher-quality finishes require labor-intensive and lengthy chemical and mechanical polishing processes. Some industrial FDM 3D printers use soluble supports to mitigate some of these issues and offer a wider range of engineering thermoplastics, but they also come at a steep price. With large parts, FDM printing also tends to be slower than SLA or SLS.
FDM printers (left) are ideal for simple shapes, but struggle with complex designs or parts with intricate features, compared to other processes like SLA printers (right).
SLA printers use a laser to cure liquid resin into hardened plastic in a process called photopolymerization. SLA is one of the most popular processes among professionals due to its high resolution, precision, and material versatility.
The Form 3L, a large-format SLA 3D printer from Formlabs, is capable of 3D printing large prototypes the size of a full-scale helmet.
While SLA technology used to be available only in large, complex industrial 3D printers that cost more than $200,000, the process has become much more accessible. With the Formlabs Form 3+ printer, businesses now have access to industrial-quality SLA for just $3,750. Large-format SLA with the Form 3L starts at just $11,000.
-
Advantages of SLA
SLA parts have the highest resolution and accuracy, the clearest details, and the smoothest surface finish of all plastic 3D printing technologies. The main benefit of SLA lies in its versatility; SLA resin formulations offer a wide range of optical, mechanical, and thermal properties to match those of standard, engineering, and industrial thermoplastics.
SLA is a great option for highly detailed prototypes requiring tight tolerances and smooth surfaces, as well as molds, tooling, patterns, medical models, and functional parts. It also offers the material with the highest heat deflection temperature of 238 degrees Celsius—which makes it an ideal choice for certain engineering and manufacturing applications—as well as the widest selection of biocompatible materials for dental and medical applications. With Draft Resin, the Formlabs SLA printers are also the fastest options for 3D printing large parts, up to 10X faster than FDM.
SLA’s wide versatility comes with a slightly higher price tag than FDM, but it is still more affordable than all other industrial 3D printing processes. SLA resin parts also require post-processing after printing, which includes washing the parts and post-curing.
Some examples of large 3D printed parts manufactured on the Form 3L.
Sample part
See and feel Formlabs quality firsthand. We’ll ship a free sample part to your office.
Request a Free Sample Part
SLS printers use a high-powered laser to fuse small particles of polymer powder. The unfused powder supports the part during printing and eliminates the need for dedicated support structures, making SLS a particularly effective choice for complex mechanical parts.
Its ability to produce parts with excellent mechanical capabilities makes SLS the most common polymer additive manufacturing technology for industrial applications.
Just like SLA, SLS used to be only available in large-format, complex 3D printing systems starting at about $200,000. With Formlabs’s Fuse 1 SLS printer, businesses can now access industrial SLS starting from $18,500 with a 30 x 16.5 x 16.5 cm build volume.
Parts printed on the Fuse 1 SLS 3D printer.
-
Advantages of SLS
Since SLS printing doesn’t require dedicated support structures, it’s ideal for complex geometries, including interior features, undercuts, thin walls, and negative features. Parts produced with SLS printing have excellent mechanical characteristics, with strength resembling that of injection-molded parts.
The most common material for SLS is nylon, a popular engineering thermoplastic with excellent mechanical properties. Nylon is lightweight, strong, and flexible, as well as stable against impact, chemicals, heat, UV light, water, and dirt.
The combination of low cost per part, high productivity, and established materials make SLS a popular choice among engineers for functional prototyping, and a cost-effective alternative to injection molding for limited-run or bridge manufacturing.
SLS has a higher entry price than FDM or SLA technologies. While nylon is a versatile material, material selection for SLS is also more limited than for FDM and SLA. Parts come out of the printer with a slightly rough surface finish and require media blasting for a smooth finish.
Material jetting 3D printers use a print head, similar to those in traditional inkjet printers, to deposit and cure droplets of photopolymer material, which harden under ultraviolet light. Some more advanced material jetting printers can also create parts from multiple materials.
Material jetting results in a finished product that is precise and has a smooth finish. The overall accuracy, combined with the fact that it is one of the only printing processes that offers multi-material and full-color printing, makes it an ideal option for realistic prototypes, such as full-color prototypes or anatomical models.
Material jetting printers can only operate with materials that have a low viscosity, which limits material options. The finished products tend to be brittle, photosensitive, and sensitive to heat. Their gradual deterioration makes them less suitable as functional prototypes. For resin 3D printing, SLA offers a wider range of functional materials, including resins that contain particles like wax and glass to imbue them with certain properties.
Beyond plastics, there are multiple industrial 3D printing processes available for metal 3D printing.
-
Metal FDM
Metal FDM printers work similarly to traditional FDM printers, but use extrude metal rods held together by polymer binders. The finished “green” parts are then sintered in a furnace to remove the binder.
SLM and DMLS printers work similarly to SLS printers, but fuse metal powder particles together layer by layer using a laser instead of polymers. SLM and DMLS 3D printers can create strong, accurate, and complex metal products, making this process ideal for aerospace, automotive, and medical applications.
While the prices of metal 3D printers have also begun to decrease, with costs ranging from $100,000 to $1 million, these systems are still not accessible to most businesses.
Alternatively, SLA 3D printing is well-suited for casting workflows that produce metal parts at a lower cost, with greater design freedom, and in less time than traditional methods.
White Paper
Get design guidelines for creating 3D printed patterns, walk through the step-by-step direct investment casting process, and explore guidelines for indirect investment casting and sand casting.
Download the White Paper
FDM, SLA, SLS, material jetting, and metal 3D printing have unique advantages and disadvantages across different applications.
Fused Deposition Modeling (FDM) | Stereolithography (SLA) | Selective Laser Sintering (SLS) | Material Jetting | Metal 3D Printing (Metal FDM, DMLS, SLM) | |
---|---|---|---|---|---|
Build volume | Up to 300 x 300 x 600 mm (desktop and benchtop 3D printers) | Up to 300 x 335 x 200 mm (desktop and benchtop 3D printers) | Up to 165 x 165 x 300 mm (benchtop industrial 3D printers) | Up to 300 x 200 x 150 mm (benchtop industrial 3D printers) | Up to 300 x 200 x 200mm (metal FDM), 400 x 400 x 400 mm (large industrial DMLS/SLM) |
Price range | Starting from $2,500 | Starting from $3,750 | Starting from $18,500 | Starting from $20,000 (multi-material starting from $100,000) | Starting from $100,000 |
Materials | Standard thermoplastics, such as ABS, PLA, and their various blends.![]() | Varieties of resin (thermosetting plastics). Standard, engineering (ABS-like, PP-like, silicone-like, flexible, heat-resistant, rigid), castable, dental, and medical (biocompatible). | Engineering thermoplastics, typically nylon and its composites (nylon 12 is biocompatible + compatible with sterilization). | Varieties of resin (thermosetting plastics). | Stainless steel, tool steel, titanium, cobalt chrome, and aluminum. |
Ideal applications | Basic proof-of-concept models, low-cost prototyping of simple parts. | Highly detailed prototypes requiring tight tolerances and smooth surfaces, molds, tooling, patterns, medical models, and functional parts. | Complex geometries, functional prototypes, short-run or bridge manufacturing. | Highly detailed prototypes, including multi-material and full-color realistic prototypes. | Strong, durable parts with complex geometries; ideal for aerospace, automotive, and medical applications.![]() |
Disadvantages | Lowest resolution and accuracy; not ideal for complex designs or parts with intricate features. | Some materials are sensitive to long exposure to UV light. | Slightly rough surface finish, limited material options. | Limited material options. Finished products tend to be brittle and photosensitive; less suitable for functional prototypes. | High costs and complexity, stringent facility requirements. |
Interactive
Try our interactive ROI tool to see how much time and cost you can save when 3D printing on Formlabs 3D printers.
Calculate Your Savings
There are several applications that capitalize on industrial 3D printers, such as prototyping, hybrid manufacturing, and production.
With rapid prototyping, designers and engineers can create prototypes directly from CAD data faster than ever before, and execute quick and frequent revisions of their designs based on real-world testing and feedback.
Because these parts or assemblies are usually constructed using additive fabrication techniques as opposed to traditional subtractive methods, the phrase has become synonymous with additive manufacturing and 3D printing.
A rapid prototype of a robot hand next to the final end-use product.
Additive manufacturing is a natural match for prototyping. It provides almost unlimited form freedom, doesn’t require tooling, and can produce parts with mechanical properties closely matching various materials made with traditional processes.
With in-house industrial 3D printers, engineers and designers can produce realistic and functional prototypes quicker and at a lower cost than any other production method to quickly iterate between digital designs and physical prototypes. It is now possible to create prototypes within a day and carry out multiple iterations of design, size, shape, or assembly based on results of real-life testing and analysis. Ultimately, the rapid prototyping process helps companies get better products to market faster than their competition.
Hybrid manufacturing combines 3D printing with traditional manufacturing processes like injection molding, thermoforming, or casting. It enhances the production process by improving its flexibility, agility, scalability, and cost-efficiency. As a result, it enables manufacturers to meet changing business needs quickly.
A 3D printed mold for vacuum forming product packaging.
Industrial 3D printers empower the rapid, cost-effective production of jigs, fixtures, and tooling in-house to save days or weeks of lead time, improve operational agility, and dramatically reduce costs versus outsourcing parts to an external vendor to machine from a solid billet of plastic or metal.
-
Tooling
Build custom tooling that stands up to the rigors of the factory floor, and can help solve the toughest manufacturing challenges. Validate manufacturing processes, solve DFM issues, and increase flexibility by direct printing of tooling for applications ranging from injection molding to CNC tube bending.
-
Jigs and fixtures
Reduce costs and increase agility by bringing jig and fixture production in-house with no minimum order quantities, no toolpath programming, wide material selection, and low capital equipment costs. Continuously improve products and respond quickly and effectively to issues on your manufacturing line with jigs and fixtures that improve assembly or QA processes.
White Paper
Download our white paper for guidelines for using 3D printed molds in the injection molding process to lower costs and lead time and see real-life case studies with Braskem, Holimaker, and Novus Applications.
Read the White Paper
White Paper
Download the white paper reducing the cost and lead time of producing jigs and fixtures.
Download the White Paper
As the economics of 3D printing are improving, and the cost-per-part threshold is moving: it’s becoming practical to use the technology in incrementally lower-value, higher-volume applications. Fueled by technology innovation and improving material properties, additive manufacturing is bound to further expand beyond rapid prototyping toward end-use parts and mass production.
Several industries have already incorporated 3D printed materials into their manufacturing processes for creating molds and casting patterns, or even printing end-use parts.
-
Mass Customization
Without the need to invest in costly tooling, use 3D printing to manufacture a variety of complex designs with no more time, energy, or material than producing simple parts. Automated 3D printing solutions can help to scale personalized products for mass-market opportunities such as patient-specific models in healthcare to consumer products like shoes, and earbuds.
Short run production with 3D printing provides flexibility to change designs without sinking high costs into tooling, and a cost-effective manufacturing alternative for producing end-use parts in the tens and hundreds.
Webinar
In this briefing, Formlabs’ Global Business Development Lead Dan Recht will show you how to identify, assess, and benefit from opportunities to use additive manufacturing as a production technology.
Watch the Webinar Now
White Paper
In this white paper, we evaluate the value proposition of bringing SLS 3D printers in-house, in comparison with outsourcing SLS parts from a service bureau.
Download the White Paper
Overview of industrial 3D printers of popular brands
Industrial 3D printers have become popular because of the possibilities they offer. The equipment allows to produce customized products at the stage of product modeling. Users can improve existing CAD models or design entirely new shapes. All this leads to a reduction in the cost of products and prototypes. The market offers a diverse range of devices. The most iconic models are described below.
Overview of industrial 3D printers
3D Systems
The American company 3D Systems is at the forefront in all areas of 3D printing. Brand technology helps to significantly reduce the time for design, prototyping, mass production. Most frequently purchased models:
• The DMP Flex 350 3D Printer can print a variety of alloys with high precision. The next generation of equipment is characterized by high performance and accurate reproduction of the digital model. The machine works on DMLS technology and is able to operate around the clock. The technique is equipped with the option of rational use of raw materials, the work is automated at each stage of printing. Unused powder is reused, reducing the cost of the final project. Embedded software controls the entire production cycle, from parameter setting to material quantification and waste disposal. Finished products are characterized by low weight, strength, it is possible to print specimens with a dense structure, identical in properties to cast ones.
Photo: 3DSystems
Features:
Country | US |
Applications | foundry industry, automotive industry, medicine, jewelry industry, automotive industry, medicine, jewelry industry |
Housing color | gray |
Construction area | 275x275x420 mm (including build platform) |
Layer thickness | 30 µm; 60 µm |
Platform | metal |
Print material | metal |
Print Technology | DMP |
Warranty | 12 months |
Minimum element size | 100 µm |
Minimum wall thickness | 150 µm |
• The DMP Factory 350 3D printer has incorporated the advantages of the previous model, supplementing the list of advantages with an automatic powder circulation module. The car is supplied with an option of cleaning of a working platform at the closed chamber. The upgraded laminar airflow system of the printable area allows you to create models of higher quality. The user interface is equipped with a touch screen that simplifies interaction. The use of DMLS-technology and modern powders of the LaserForm series ensures high speed and increased productivity. The model is optimal for commercial use.
Photo: 3DSystems
Features:
Country | US |
Applications | aviation and space, automotive industry, foundry industry, mechanical engineering, medicine, jewelry industry, automotive industry, foundry industry, mechanical engineering, medicine, jewelry industry |
Housing color | gray |
Construction area | 275x275x420 mm (including build platform) |
Layer thickness | 30 µm; 60 µm |
Print material | metal |
Print Technology | DMP |
Warranty | 12 months |
Minimum element size | 100 µm |
Minimum wall thickness | 150 µm |
• The DMP Factory 500 3D printer is a machine optimized for industrial scale. The equipment is a scalable design consisting of several special modules. An integrated metal production system provides a controlled environment for building objects, enabling continuous operation. The right combination of modules can help optimize an existing factory line or start a new product line. The 3DXpert software allows you to grow large seamless elements.
Photo: 3DSystems
Features:
Country | US |
Applications | foundry industry, jewelry industry, mechanical engineering, medicine, metal industry, mechanical engineering, medicine |
Housing color | white-grey |
Dimensions | 3010x2290x2820 mm |
Construction area | 500x500x500 mm (including build platform) |
Layer thickness | 30 µm; 60 µm; 90 µm |
Layer thickness | metal |
Platform | metal |
Print Technology | DMP |
Operating system | Windows 10 Pro, 64 bit |
Warranty | 12 months |
Minimum element size | 100 µm |
Number of lasers | 3 |
Laser Power | 500 W |
Laser wavelength | 1070 µm |
• The ProX 800 3D Printer sets the standard for performance and fine detail. The equipment operates according to SLA technology, focused on the construction of one large part or a series of small products in a full cycle. The technical ability allows the production of samples with a smooth surface that exactly matches the 3D digital model. Additional advantages of the device are the ability to select the necessary material, a clear workflow, saving on waste.
Photo: 3DSystems
Features:
Country | US |
Application area | architecture, foundry industry, interior design, foundry industry, education, dentistry, foundry industry, interior design, foundry industry, education, dentistry |
Housing color | gray |
Communication interface | LANs, IEEE 802.3 using TCP/IP and NFS, USB |
Dimensions | 1370x1600x2260 mm |
Construction area | 650x750x550 mm (including build platform) |
Layer thickness | 125 µm |
Platform | mesh |
Print media | photopolymer |
Print Technology | SLA |
Operating system | Windows 10 |
Warranty | 12 months |
Minimum element size | 125 µm |
Maximum weight of model | 75 kg |
Maximum resolution | 4000 DPI |
3DCeram
The French brand 3DCeram offers services and equipment for 3D printing of original ceramic products. For development work, serial production of samples of complex geometry, the following machines are used:
• 3D printer CERAMAKER 100 is a brand development aimed at additive manufacturing of ceramic products. This modification is actively used in the chemical and aviation industries, the medical field, jewelry, watchmaking. The equipment operates on the principle of layer-by-layer curing by a laser installation of a special composition of ceramic powder and photopolymer. The latter is a binder and is burned out after the alignment of the object is completed.
Photo: 3DCeram
Features:
Country | France |
Applications | aviation and space, automotive, nuclear industry, interior design, railway, mechanical engineering, medicine, dentistry, shipbuilding |
Dimensions | 1000x1500x1900 mm |
Construction area | 100x100x100 mm |
Layer thickness | 50 µm |
Material | ceramics |
Print Technology | SLA |
Warranty | 12 months |
• The CERAMAKER 900 3D printer reproduces objects with a surface roughness of less than 2 µm. Mechanical post-processing of the product is available at every stage of production. The open architecture of the device allows you to customize the work with the necessary materials, and the adjustable size of the platform makes it possible to line up parts of various sizes. Production is carried out without preliminary creation of a form. Evenly distributed UV power over the entire area of the working platform ensures shrinkage is predictable.
Photo: 3DCeram
Features:
Country | France |
Applications | foundry industry, jewelry industry, medicine, mechanical engineering, dentistry |
Dimensions | 1060x2250x2040 mm |
Construction area | 300x300x100 mm |
Layer thickness | 35 µm |
Print material | ceramics |
Print Technology | SLA |
Warranty | 12 months |
• The CERAMAKER C3600 ULTIMATE 3D printer is a large scale production equipment. The device is aimed at the production of massive products or large batches of products. The device is compatible with materials that are distinguished by chemical, corrosion resistance, as well as formulations used in dentistry. The industrial unit operates according to the stereolithography method, adopting unassisted printing technology.
Photo: 3DCeram
Features:
Country | France |
Industries of application | foundry industry, jewelry industry, medicine, mechanical engineering |
Dimensions | 2100x1800x2500 mm |
Construction area | 600x600x300 mm |
Layer thickness | 25 to 125 µm |
Print material | ceramics |
Print Technology | SLA |
Warranty | 12 months |
Number of lasers | 4 UV lasers |
Laser wavelength | 405 nm |
VoxeiJet
The German company VoxeiJet produces 3D machines for the production of sand molds and cores. The company has developed its own line of polymeric materials, and also produces a diverse range - from small-format research devices to large-sized industrial units. Most famous models:
• The VoxelJet VX 200 HSS 3D printer is a compact system based on polymer powder sintering technology. The equipment is used for research purposes and to create new resources for the HSS process. An open system makes it possible to control the settings of print modes and parameters of temperature, layer thickness.
Photo: VoxelJet
Features:
Country | Germany |
Application area | interior design, aviation and space, automotive, prototyping |
Construction area | 290x140x180 mm |
Layer thickness | > 80 micron |
Print material | polyamide |
Print Technology | BJ |
• The VoxelJet VX 1000 HSS 3D printer works with polymers. The high-performance system stands out with a capacious build chamber and high print speeds. The machine is useful for large-scale production of plastic parts that are comparable in quality to samples created by injection molding. The equipment is easily integrated into the existing factory line and adapted to the existing production. Material recycling technology reduces the cost of finished products.
Photo: VoxelJet
Features:
Country | Germany |
Applications | prototyping, mechanical engineering, interior design |
Construction area | 1000x540 mm |
Print material | polyamide, nylon |
Print technology | BJ |
• The VoxelJet VX 4000 3D printer is a 3D sand mold printing system. The printer is capable of producing large items or a series of small items in a single cycle. The device operates in automatic mode, which guarantees the continuity of the manufacturing process. The car provides fast release of products of the set quality. The capacious space of the construction area allows you to print custom objects with exact compliance with the configuration and plus sizes at high resolution. The technique is in demand in mechanical engineering and the aerospace sector. Finished molds and cores can be immediately used for metal casting.
Photo: VoxelJet
Features:
Country | Germany |
Dimensions | 20000x7800x4000 mm |
Construction area | 4000x2000x1000 mm |
Layer thickness | 300 micron |
Print material | sand |
Print Technology | BJ |
Maximum resolution | 600 dpi |
Inss Tek
The Korean company Inss Tek has focused on working with alloys. DMT 3D printing technology has found its way into various industries. The most popular models working with metals:
• The MX-Lab 3D printer is designed for the manufacture of functional devices, remodeling, reconstruction and restoration work, special coatings. The device uses DMT technology, which provides the necessary mechanical characteristics of the finished product, a unique density, the finest microstructure. Entry-level DMT machine with 3-axis laser system is suitable for material properties study, prototyping, alloy development. 9Feature:
Country | South Korea |
Applications | aviation and space, metallurgical industry, mechanical engineering, foundry industry |
Dimensions | 700x700x860mm; 200 kg |
Construction area | 150x150x150 mm |
Layer thickness | 150 micron |
Print material | metal |
Print Technology | DMP |
Operating system | Windows 7 |
• InssTek MX-600 3D Printer - The machine is configured to produce small objects with specified mechanical characteristics. Using this technique, you can repair various devices, modernize mechanisms, and create industrial alloys. The technique is able to quickly convert a complex CAD model into a finished part, which is in demand in medicine, electronics, defense and manufacturing industries. The advanced CVM powder feeding system operates at a stable, adjustable speed.
Photo: InssTek
Features:
Country | South Korea |
Applications | foundry industry, metallurgical industry |
Dimensions | 2000x2900x2550mm; 6.5 t |
Construction area | 450x600x380 mm |
Layer thickness | 250 micron |
Print material | metal |
Print Technology | DMT |
Operating system | Windows 7 |
• The InssTek MX-Grande 3D Printer is an industrial system designed for producing large objects. The equipment adopts gravity feeding method or direct powder delivery method with gas. The capabilities of the device are used in the nuclear and oil industries, metallurgy, and shipbuilding.
Photo: InssTek
Features:
Country | South Korea |
Applications | automotive industry, nuclear industry, foundry industry, mechanical engineering, metallurgical industry, oil and gas industry, shipbuilding |
Construction area | 4000x1000x1000 mm |
Layer thickness | 750 micron |
Print material | metal |
Print Technology | DMT |
Operating system | Windows 7 |
Conclusion
Large-scale manufacturing giants actively use additive technologies, while developed countries open large research centers and develop state programs. Industrial printers become more affordable every year, pay off faster. All this significantly affects the production process, making it efficient, environmentally friendly and profitable.
Source
Tags:
Industrial 3D printers, 3D Systems company, DMP Flex 350 3D printer, DMP Factory 350 3D printer, DMLS technology, 3DCeram brand, CERAMAKER 100 3D printer, CERAMATE3AKER3AKER60 3D printer VoxeiJet, 3D printer VoxelJet VX 200 HSS, Inss Tek
Other materials:
- Zortrax 3D Printed Sports Helmet for Cats
- QIDI TECH S-Box 3D Printer - Reliable Heavyweight!
- 3D Scanner Review: RangeVision PRO5M, Shining 3D PRO HD, Calibry, KSCAN20, Shining 3D HX
- Go!SCAN SPARK vs HandySCAN SILVER/BLACK: which scanner is right for you?
- Printing with nylon (Nylon) on a 3D printer technology features
Attention!
We accept news, articles or press releases
with links and images. [email protected]
Comparison of 3D printing technologies: FDM, SLA and SLS
Additive manufacturing or 3D printing reduces costs, saves time and expands the technological possibilities in product development. 3D printing technologies offer versatile solutions for applications ranging from rapid concept and functional prototypes in the field of prototyping to fixtures and clamps or even final parts in manufacturing.
Over the past few years, high resolution 3D printers have become more affordable, more reliable and easier to use. As a result, more companies have been able to use 3D printing technology, but choosing between different competing 3D printing solutions can be difficult.
Which technology is right for your needs? What materials are available for her? What equipment and training is needed to get started? What are the costs and payback?
In this article, we take a closer look at three of today's most well-known plastic 3D printing technologies: Fused Deposition Modeling (FDM), Stereolithography (SLA), and Selective Laser Sintering (SLS).
Choosing between FDM and SLA 3D printer? Check out our detailed comparison of FDM and SLA technologies.
You can download this high resolution infographic here.
VIDEO MANUAL
Can't find the 3D printing technology that best suits your needs? In this video tutorial, we compare Fused Deposition Modeling (FDM), Stereolithography (SLA), and Selective Laser Sintering (SLS) technologies in terms of the top factors to consider when purchasing.
Watch Video
Fused Deposition Modeling (FDM), also known as Fused Filament Manufacturing (FFF), is the most widely used form of 3D printing at the consumer level, fueled by the rise of consumer 3D printers. On FDM printers, models are made by melting and extruding a thermoplastic filament, which the printer's nozzle applies layer by layer to the model being built.
The FDM method uses a range of standard plastics such as ABS, PLA and their various blends. It is well suited for making basic experimental models, as well as for quickly and inexpensively prototyping simple parts, such as parts that are usually machined.
FDM models often show layer lines and may have inaccuracies around complex features. This sample was printed on a Stratasys uPrint FDM industrial 3D printer with soluble support structures (printer price starting at $15,900).
FDM printers have the lowest resolution and accuracy of SLA or SLS and are not the best option for printing complex designs or parts with complex features. Surface quality can be improved by chemical and mechanical polishing processes. To address these issues, industrial FDM 3D printers use soluble support structures and offer a wider range of engineering thermoplastics, but they are also expensive.
FDM printers do not handle complex designs or parts with complex features (left) compared to SLA printers (right).
Invented in the 1980s, stereolithography is the world's first 3D printing technology and is still one of the most popular technologies among professionals today. SLA printers use a process called photopolymerization, which is the conversion of liquid polymers into hardened plastic using a laser.
See stereolithography in action.
Models printed on SLA printers have the highest resolution and accuracy, the sharpest detail and the smoothest surface of all plastic 3D printing technologies, but the main advantage of the SLA method is its versatility. Materials manufacturers have developed innovative formulas for SLA polymers with a wide range of optical, mechanical and thermal properties that match those of standard, engineering and industrial thermoplastics.
Models created using SLA technology have sharp edges, a smooth surface and almost invisible layer lines. This sample was printed on a Formlabs Form 3 Desktop Stereolithographic 3D Printer (price starting at $3499).
SLA is an excellent option for making highly detailed prototypes that require tight tolerances and smooth surfaces such as molds, templates and functional parts. SLA technology is widely used in industries ranging from engineering and design to manufacturing, dentistry, jewelry, modeling, and education.
White Paper
Download our in-depth white paper to learn how SLA printing works, why thousands of professionals use it today, and how this 3D printing technology can be useful in your work.
Download white paper
free sample
Experience Formlabs print quality firsthand. We will send a free 3D printing sample directly to your office.
Request a free sample
Selective laser sintering is the most common additive manufacturing technology used in industry.
Selective Laser Sintering (SLS) 3D printers use a high power laser to sinter fine polymer powder particles. The unsprayed powder supports the model during printing and eliminates the need for special support structures. This makes SLS ideal for complex geometries, including internal features, grooves, thin walls, and negative taper. Models produced using SLS printing have excellent mechanical characteristics: their strength can be compared with the strength of injection molded parts.
Models created with SLS technology have a slightly rough surface, but almost no visible layer lines. This sample was printed on the Formlabs Fuse 1 SLS workshop 3D printer (price starting at $18,500).
The most common selective laser sintering material is nylon, a popular engineering thermoplastic with excellent mechanical properties. Nylon is light, strong and flexible, resistant to impact, heat, chemicals, UV radiation, water and dirt.
The combination of low part cost, high productivity, and widely used materials makes SLS a popular method for engineering functional prototyping and a cost-effective alternative to injection molding in cases where production runs are limited.
White Paper
Looking for a 3D printer to create durable, functional models? Download our white paper to learn how selective laser sintering (SLS) technology works and why it is popular in 3D printing for functional prototypes and end-use products.
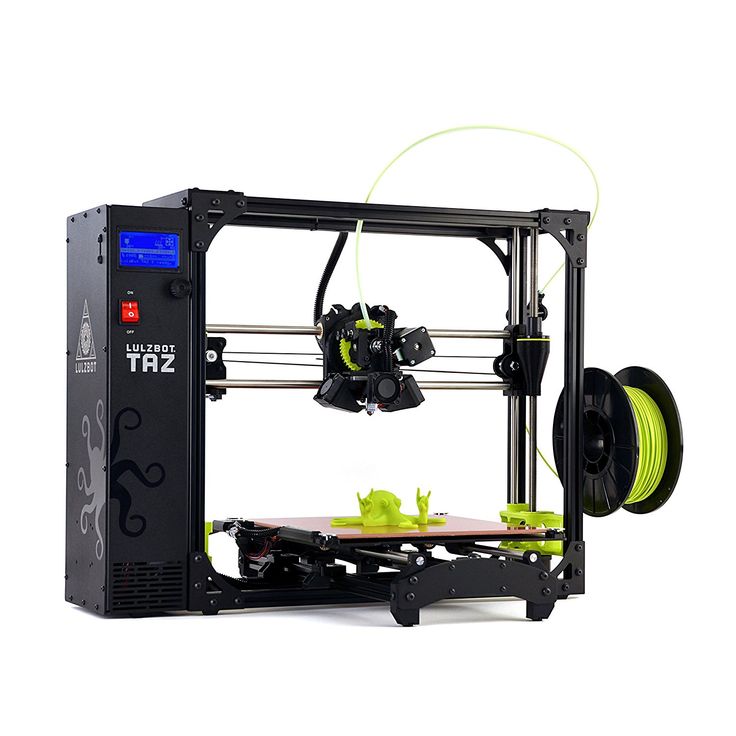
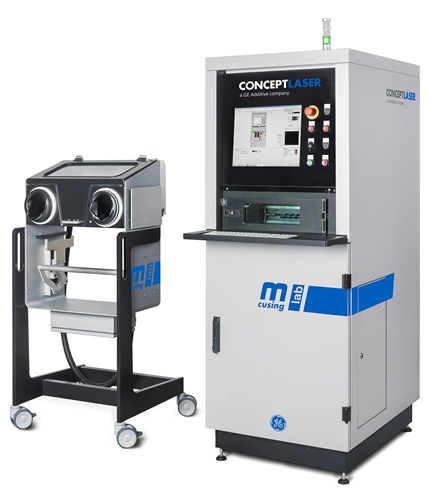
Either way, you should choose the technology that best suits your business. Prices have dropped significantly in recent years, and today all three technologies are offered in compact and affordable systems.
3D printing costing doesn't end with initial equipment costs. Material and labor costs have a significant impact on the cost of each part, depending on the application and production needs.
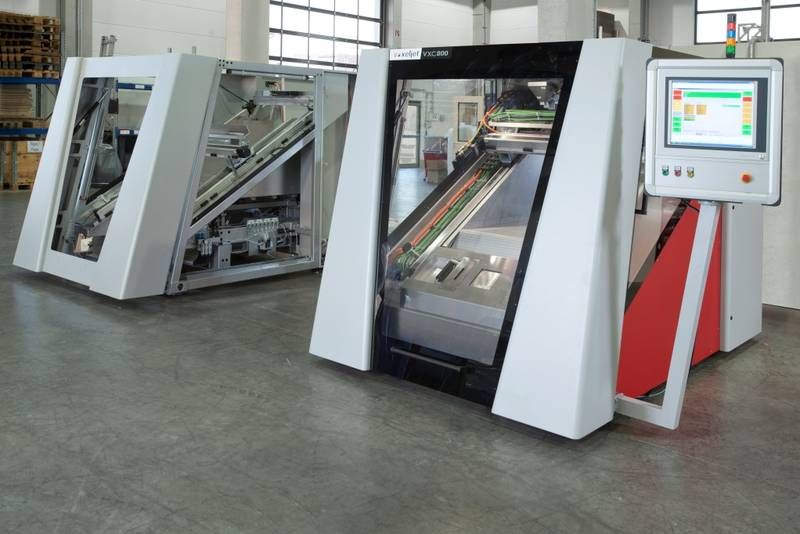
INTERACTIVE MATERIAL
Try our interactive ROI tool to see how much time and money you can save by printing with Formlabs 3D printers.
Calculate savings
FDM, SLA and SLS prototype ski goggle frames (left to right).
We hope this article has helped you narrow down your search for the 3D printing technology best suited to your needs.