Gaps in walls 3d print
How to Fix Gaps Between Wall & Infill (Wall Separation) – 3D Printerly
You are on your way to finish your first 3D printed model, but something is not quite right with your model. The walls of your model are not fitting together with the model or worse it might be falling apart.
The best way to fix gaps between walls & infill is to identify one of the many possible causes and act accordingly. The solutions usually range from increasing extrusion temperature and width, slowing down print speed, decreasing fan speed, increasing infill percentage, or changing your infill pattern altogether.
The above-mentioned problem is known as wall separation. It is a commonly encountered problem when it comes to 3D printing. This is caused when the outer case of the 3D model does not hold together with the interior of the model often known as the infill.
This is something that can be a nightmare if you don’t know what is going on. But don’t worry we have the solutions for you, which can fix this issue in a jiffy. This problem can be resolved by tweaking some of the properties of your printer and its software.
I will go into detail about the possible causes and fixes for each one so rest assured, this problem can be fixed with a little more knowledge.
Before we move any further towards the solution, a better understanding about the different parts in a printed model and the problem itself will help the discussion below.
What is Infill?When it comes to 3D printing a model, one of the main advantages is that the model can be of varying degrees of hollowness. The holding structure that is inside the walls of the printed model is called infill.
Infill is a three dimensional repeating pattern that runs throughout the interior of the model. The hollowness of the finished object is determined by the density of the infill. When the density of the infill is 0%, then the model is completely hollow without any infill.
If the density 100%, it means that the object is purely solid from the inside. Apart from holding the structure, infill determines the strength of the structure too.
Before we address this issue we need to know a bit about how infill and walls are printed. 3D printing is done in layers, and each layer of the printed material is made of an outline perimeter and infill.
The outline perimeter turns out to be the wall of the printed model when it’s completed. As mention above, infill is just used to hold the object together making it rigid with the least use of material.
It will be a simple repeating pattern that speeds up the printing process. We find that the outline perimeter determines the shape and the features of the object; hence it is of a different pattern from the infill. This is the reason why wall separation or gaps between the wall and infill happen in the first place.
Being a different pattern from the infill can make the outline not stick with the infill and leave gaps in-between. This can be avoided if you carefully merge the two sections. Few things to be considered to make this happen or troubleshoot problems encountered on the way are discussed below.
There is a setting in Cura under ‘Expert Settings’ called ‘Connect Infill Lines’ and checking this box connects the ends where the infill pattern meets the inner wall. It uses a line which follows the shape of the inner wall to make your infill adhere better to the walls of your object.
Enabling this setting can also reduce the effects of infill on the quality of vertical surfaces.
It’s a good setting to try out to see if it quickly helps fix wall separation and gaps in 3D print walls.
You can also try using a Cura setting called “Fill Gaps Between Walls”, which should be set to “Everywhere” instead of “Nowhere” by default, but double check this. Simply use the Cura search box and type in “fill gaps” and the setting should show up.
Wall Separation Due to Thin WallsGaps can also be caused by printing of thin walls. When you use a printer with a fixed nozzle size, you might come across this problem. A nozzle is the part of the print head through which the melted print material comes through.
It moves around the print bed to place the extruded material on it to build the structure in layers. Thin walls are very hard to print, when its thickness is only a few time larger than the nozzle diameter, which is also called the extrusion width.
A solution to avoid this is by changing the extrusion width. If you are using a printer that can change the extrusion width using the software, then you can change the value with manual settings and play with the value until you find the best one.
If you are using a printer fixed nozzle size then you might want to change it manually. If you are planning to print a wall that is of uniform thickness, always use a large value for thickness compared to your nozzle’s extrusion width.
Outline Overlap too LowOne solution is to increase the strength between the perimeter outline and the infill. Most 3D printers come with a setting for this in its software and it is called the ‘Skin Overlap’.
This setting determines the amount of overlap between the infill and the outline. The more the infill overlaps with the innermost perimeter the better the bond between the two sections.
Printing Speed is too HighThe time for the outline to bond with the infill is an important factor that determines the bond strength. Improved bond strength will avoid wall gapping after printing.
While printing, infill is printed at a much faster pace compared to the outline. This is because the outline being the shape of the final product needs to be printed slower with precision. On the other hand, the infill being a simple repeating pattern is printed much faster.
If the printing speed is set too high, the infill will not get enough time to set and make a strong bond with the outline. If this situation arises, it is advised to adjust the default printing speed in the printer to a lower value.
The perfect print speed to avoid wall gapping can change according to the print material used. A better way to find suitable print speed will be making small test models in different speeds.
Start from a lower speed that produces no wall gapping and increase the speed on different models until you find an optimum solution.
Sometimes Things Can’t be Printed by Your Printer3D printing software acts as a powerful tool and offers the best infill patterns with good outline overlap. Even if you choose the best option doesn’t mean that you’ll get a good print.
You should also be aware of what your printer is capable of printing. One such example is your software might be set to print fine structures which your nozzle does not have the extrusion width to print.
Choosing the Right Infill PatternWhen you print a model, you have to find the best pattern for the infill to take the least volume and make more contact with the walls. Infill patterns when used according to the shape can improve its strength.
If you find wall gapping in your model, then try using patterns that make consistent and more repetitive contact with the outline like Grid, Line and Cubic rather than shape oriented patterns like concentric.
Some infill patterns are better suited to circular or rounded designs so trial and error some of the more common ones to see which one works for you.
Under Extrusion can Sometimes Cause Wall GappingUnder extrusion happens when the printer does not supply enough material to print. This can happen when less plastic is exiting the print head than the intended value. This results in weak builds with less structural strength to the walls together.
This can also cause gaps between the layers of the walls if the build has walls that are of multiple layers.
A few things to be noted to prevent under extrusion are the following.
You could be using a filament with the wrong diameter. The printer’s software specifies a diameter for the filament that is fed into the nozzle. Look for filaments with the specified diameter while purchasing.
If you have purchased the filament with the right diameter and still encounter the same issue, then it can be solved by increasing the value of the extrusion multiplier or flow rate.
Weak Infill Can Cause Wall GapsA weak infill is created when it is not printed properly. This can cause the infill to fall apart from the walls. This can be a problem with the software itself. Key reasons can be not enough material printed or it can be caused due to uneven thickness of the print.
Fast printing can also result in infill not being printed properly. One way to prevent this is by printing with a large value of infill extrusion width. In some printers, you can achieve with the inbuilt software.
When you change values with the software, there are a couple of things to be considered. Increasing the value of infill increase the volume of material printed. To compensate for the value of infill percentage, the software will put more space in between the lines.
To avoid this problem, you should increase the value of infill percentage along with the value of Infill Line Width.
Low Print TemperaturePlastic requires heat to soften and create a bond with the rest of the build. If the print temperature is too low this can cause many problems including wall separation.
We discussed that while printing, the outline and the infill are printed as separate sections. Hence, good temperature is required to keep both these sections intact. Printing at higher temperatures can solve this problem.
One more solution found is to increase the setting speed. This can be done by decreasing the fan speed which reduces the effect of rapid cooling by blowing cool air. You can achieve a warm environment for printing by covering up the printer to contain the heat produced while printing.
Inconsistent ExtrusionThis problem is found when your printer prints with varying extrusion width which is unintended. This will make each lines of the print bumpy in uneven intervals. This can cause the outline of the print sticking improperly with the infill.
This in turn causes a weak bond between the walls and the infill which can create wall gaps or ultimately fall apart from the structure. This problem is caused due to various reasons as follows.
If the proper amount of material is not provided at the right time, this can be troublesome. The reason can be the filament not being fed into the printer in the right speed.
If this is the problem you need to check the spool of plastic entering the printer can rotate freely. Check whether the filament is getting tangled while printing. Also check for any blockage in the tube through which the filament is drawn.
Another reason can be the clogging of the extruder. Any foreign debris or different plastic inside the nozzle can prevent proper extrusion from happening. Cleaning the nozzle can solve this problem.
Low quality filaments can also cause this problem. Poorly made filaments contain extra additives that can destroy the consistency of the plastic. This can change the rate of melting different in different parts of the filament.
As discussed above, infill density determines the percentage of the volume occupied by the infill inside the outline. Low infill density can reduce the contact of the infill with the walls. Hence, the increased value of the infill can produce more contact.
ultimaker cura - How to fix wall separation in 3D prints (gaps in between wall perimeters)?
Ask Question
Asked
Modified 3 years, 3 months ago
Viewed 40k times
$\begingroup$
The print is very solid except for the 4 walls.
From the top, I can slide a paper down to the bottom. This is ONLY between the walls, the rest of the print is solid. The filament is PLA 1. 75 mm.
But the bottom is solid, no gaps.
I have checked the usual problems on Ultimaker troubleshooting photo gallery, but I can find anything similar.
Any advice to fix this would be very welcome.
Print settings:
- print-quality
- ultimaker-cura
- 3d-design
$\endgroup$
2
$\begingroup$
To fix this, I had results with the following way:
- Change your extrusion width from being equal to your nozzle size (0.4 mm) to slightly larger (I use 0.45 mm). That way you better combat the shrinking of the filament.
- Having the
Print thin walls
setting activated to force the printer to print intermediary walls if there are areas where less than the prescribed wall thickness for a single wall fills in spaces that are as a result of the wider outer walls left.The result for a 1.2 mm wall, the central part is a 0.3 mm zigzag.
- Lower the extrusion temperature a tad as hotter filament shrinks more on cooling! For PLA about 200 °C is my sweet spot.
Additionally, there are extra steps that could be taken: * Finally, you could play around a little with the extrusion multiplier to try to get rid of the tiny bit of under extrusion you have. * Calibration could help too.
$\endgroup$
6
$\begingroup$
Now that print settings are shared we can see that this problem is not related to too fast printing (only 20 mm/s) or too low print temperature (210 °C should get PLA fluid enough). To explain this, a low temperature and too fast printing cause under-extruded lines.
There are 2 other causes that might be worth investigating:
- Under-extrusion. From the top layers one can see that there may be insufficient material printed.
Calibration of the extruder helps in this respect.
- Inaccurate positioning. This may for instance be caused by loose belts or a mechanical defect.
$\endgroup$
$\begingroup$
I've experienced this too, especially with flex modified PLA filament. For that, fixing underextrusion and increasing temperature made it go away. Sadly Cura has no option to overlap walls slightly (if printed in the right order, this could be done without affecting dimensional accuracy) except possibly the outer one, so you really have to get extrusion rate calibrated right or this will happen.
$\endgroup$
$\begingroup$
Look for the horizontal expansion setting in Cura. By default it should be zero. The description includes this:
Positive values can help compensate for too big holes.
![]()
The "holes" here includes these gaps. You can set it to something very small (ie: .01 or .03, probably no more than .05) and that will likely be enough to get it to fill in those gaps.
Unfortunately, I only have a little direct personal experience with this setting, hence the probably/likely weasel words, and I can't give much real guidance on exactly how big or small you can go with this.
$\endgroup$
3
Fixing the 20 Most Common 3D Printing Problems
3DPrintStory     3D printing process     Fixing the 20 Most Common 3D Printing Problems
3D printing allows you to create amazing models. But everyone faces unpleasant moments when even a simple model does not print well.
You checked the model, made sure that many people have already printed it and they had no problems. What are you doing wrong?
This article has collected 20 of the most common 3D printing problems. We hope that the article will help you quickly identify the problem and find a solution for it. In addition, the article details the causes of problems during 3D printing, which will help you avoid them in the future.
Model tearing off
Problem description
At the base, the model rises up relative to the table (English - warping). In addition to the quality of the manufactured part, this problem can prevent the printing of tall parts that can finally fall off the table.
What causes this problem during 3D printing?
Part breakage is a very common problem due to the nature of the printable plastic. As the ABS or PLA plastic cools, it begins to make poor contact with the surface, so the "warping" effect occurs when the plastic cools too quickly.
Solve the problem: part is torn off
- Use a heated table. The simplest solution is to use a heated table slightly below the melting point of the plastic. If the temperature is set correctly, the first layer will be in firm contact with the table. Most often, the platform temperature is set in the program to generate the g code for the model. The recommended temperature is often indicated on plastic packaging.
- Use glue. If your model still wraps around the corners, apply some glue to the print table.
- Try another table. Replace your print bed with a model that offers better adhesion. Manufacturers such as Lulzbot use PEI (Polyetherimide) surfaces. XYZPrinting add special tape to the printer box and that works great too (but they don't have heated tables). Zortrax 3D 3D printers solve the problem differently - with the help of small holes in the table.
- Level the print table.
The print bed may need to be calibrated. During calibration, make sure that the tip of the extruder is at a suitable, uniform height from the stage along its entire plane.
- Reinforce contact. Increasing the contact between the model and the print table is another easy way. Most 3D printing software has the ability to add additional layers to the base.
- Play around with the temperature. If none of the above work, try increasing the print bed temperature in 5-degree increments. Also pay attention to the operating modes of the coolers. Usually coolers start to work at full capacity when the model height is about 0.5 mm. Try increasing this height to 0.75mm so that the base layers have more time to cool naturally.
And finally, even if you have a heated table, applying a little glue is unlikely to hurt.
3D Printing Problem Checklist: Part 9 Tear Off0017
- Use a heated bed
- Add glue to the print bed
- Use a high-adhesion bed from quality manufacturers
- Calibrate the bed
- Add extra layers to the model base in your 3D printing software
- Play around with temperature and settings cooler
Elephant leg
Description of the problem
The base of the model is printed with a clear indentation to the outside. It is called - “elephant's foot”
What causes this problem during 3D printing?
This undesirable effect is caused by the mass of the model itself, which presses on the first, insufficiently cooled layers. In particular, this problem occurs if you have a heated table.
Solve the problem: "Elephant's foot"
- Correct balance. In order to avoid this problem, it is necessary to properly cool the layers at the base of the model. The base layers must be able to support the mass of the part, but not overcool, so that the part does not start to come off the table. Finding the right balance can be tricky. Start by lowering the table temperature in 5 degree increments (within +/- 20 degrees from the recommended temperature). If your bottom and top layers are set to 0.6mm, start cooling earlier.
- Level the table. Most 3D printing problems are caused by improper table alignment. Start with calibration recommendations from your printer manufacturer.
After that, print a square for calibration and evaluate how the plastic lays down. After printing, you will be able to see how evenly the plastic lays down depending on the height of the extruder relative to the table.
- Raise the extruder. A simple increase in the distance between the extruder and the table can help. But if the distance is too large, the plastic will not stick to the table.
- Chamfer the base of the model. If none of the above work, you can chamfer the base of your model. Of course, this is only possible if you developed the print model yourself or have access to the original file. Start with a 5mm 45º bevel and experiment for the best result.
3D Printing Problem Checklist: Elephant Leg
- Adjust Table Temperature and Cooler Speed
- Calibrate Table
- Check the distance between the extruder and the table
- Chamfer the base of the model
If you are interested in more detailed information on this problem, we recommend that you read our detailed material on eliminating the "elephant leg" problem.
Other first layer problems
Description of the problem
The first layer does not adhere well to the table and some parts come off. Unwanted lines appear at the base of the model.
What causes this problem during 3D printing?
Such problems are a sign that the table has not been correctly calibrated (table calibration on the example of the Anet A8 3D printer). If the extruder is too far from the table, unwanted lines appear on the base and/or the first layer does not stick. If the extruder is too close, voids may appear.
Important: The print bed must be as clean as possible. Even fingerprints can cause the model to come off.
Solve the problem: The remaining problems of the first layer
- Calibrate the table. Each printer has its own table calibration features. For example, the latest Lulzbot models have an automatic calibration system. Ultimaker 3D printers are configured manually according to the corresponding guide.
With Prusa i3 printers, you have to tinker a little longer and think for yourself.
- Adjust the distance between the extruder and the table. If the extruder is too high, the plastic will not grip the platform. If too low, you may damage the table.
- Clean the print table. It is advisable to clean the table before each new print. Especially if you are using glue. Fingerprints and adhesive residue may cause the model to come off.
- Add glue. A small layer of adhesive can significantly improve adhesion. But do not forget that if you do not clean the table, then the use of glue can lead to the opposite effect.
- Special tape for non-heated table. If you are using an unheated platform, try applying tape to improve the contact between the base of the model and the table.
Cheklist of 3D Problem: the remaining problems of the first layer
- Calibrate the table
- Check the height of the extruder relative to the table
- Clean the table
- Use the special tape without heated 9009
- Check belts. Start by checking belt tension. You should feel resistance as you bring them together with your fingers. If the top of the belt is stiffer than the bottom, this is a clear sign that they need to be tightened.
- Check table top plate. Check the top plate and screw sets in the printer. Make sure everything is taut and aligned where needed.
- Check the Z-axis screws. Most 3D printers use a screw-nut pair instead of a ball screw. In general, this does not particularly affect the print quality, but over time, the screw may deform. Do not disassemble the printer to check the screws. It is enough to use a program like ‘Printrun’ and move the extruder up and down.
If one of the screws is deformed, you will notice it. Unfortunately, it's almost impossible to fix this. But, on the other hand, this is a great chance to modify your 3D printer and replace the screws with screw-nut pairs.
- Check belt tension
- Check the reliability of fixation of the upper part of the table for printing
- Make sure that the Zears of the Z axis are not deformed 9009
Last layers
9000 9000 description of the problem 9000 the model has voids because some layers were simply skipped (partially or completely).What causes this problem during 3D printing?
The printer did not feed the required amount of plastic. This may be due to problems with the plastic (for example, it has a different diameter), the extruder, or the plastic feed mechanism.
Friction has caused the table to stop temporarily. The reason may be that the vertical screws are not calibrated.
There is a problem with one of the screws or the Z-axis nut. For example, the screw is damaged, dirty, or not well lubricated.
Troubleshooting: Missing layers
- Mechanics check. A 3D printer, like any other piece of equipment, needs maintenance. If you have this problem, this is a clear sign that you should pay attention to its service. Start by checking the screws. Make sure they are well seated in the bearings/holes, with no undue misalignment.
- Screw alignment check. Check that all screws are aligned and not bent. You can appreciate this by turning off the power and carefully moving the extruder along the coordinate axes (depending on the layout of your 3D printer). If you feel resistance, then something is wrong.
- Damaged bearings. Damage to the bearings is manifested in the characteristic vibration during the operation of the 3D printer. If you notice vibrations, turn off the power and manually move the carriage with the extruder to find exactly where the bearing failed.
- Check lubrication. Many people forget about the lubrication of joints. But this is a very important point for the correct operation of your 3D printer. Regular machine oil is inexpensive and is great for maintaining printer connections. Before lubricating, check the guides. They must not be dirty. You need to apply a little oil. If you have applied too much lubricant, simply wipe off the excess with a rag. Naturally, after lubrication, check that the carriages run smoothly.
- Plastic feed problem. The last possible problem is insufficient plastic supply. The solution to this problem may not be simple, so it is considered separately below.
3D Printing Issue Checklist: Missing Layers
- Check mechanics and make sure all screws are tight
- Check screw alignment
- Check bearings
- 0016 Problem Description
Dimples form on the sides of the model, especially on tall models.
One of the most unexpected problems, the solution to which is usually not where you are looking for it.
What causes this problem during 3D printing?
In higher layers, the material cools faster because the heating from the table does not reach this height. Because of this, adhesion on higher layers is lower.
Solve the problem: Dimples on high models
- Extruder temperature. Start by raising the extruder temperature in 10ºC increments. The specifications for your plastic should list operating temperatures. Try to keep the temperature within the specified range.
- Cooler direction and speed. Check the coolers, make sure they work and point to the model. If so, try reducing their speed.
3D Printing Problem Checklist: Dimples on Tall Models
- Check extruder temperature and raise it in 10 degree increments
- Check the location and speed of the coolers aimed at the 3D model
Dimples, holes on the top of the model
Description of the problem
Dimples or even holes form on the top of the model.
What causes this problem during 3D printing?
The two most common causes are improper cooling of the top layer or insufficient thickness.
Solve the problem:
hollows, holes on the top of model- Printable plastic diameter. Most common when printing with 1.75 plastic. Similar problems can appear in any 3D printer, but most often they appear when using plastic with a diameter of 1.75 mm, not 2.85.
- Check cooler location. Any cooling problems are naturally related to coolers. At the start of printing, the coolers run slowly or turn off altogether, but after the first coat they should work much harder. Be sure to rate the performance of the coolers at the end of the print. If everything works, just in case, check the direction of their rotation. Cold air should flow to the model, and not vice versa.
- Set the fan speed in G-code. As the last layers of the model are formed, the cooling must be very intense so that the plastic does not fall into the holes of your mesh in the model.
Cooler speed can be configured in G-code. The standard code for an on cooler is M106 and M107 for off. That is, adjust the maximum speed for the upper layers. An example would be a 1 cm by 1 cm cube with a layer thickness of 0.1 mm. In this case, the G-code obtained from CURA for the Prusa i3 3D printer will be 97 layers. Knowing that we have the 'Bottom / Top Thickness' settings set to 0.6mm, we can look at ;LAYER:91 and add M106 S255 at the end of the line. The M106 kicks off the cooler, while the S255 makes it run at full capacity.
- Increase the thickness of the top layer. The simplest solution is to increase the thickness of the top layer. In most applications, this can be done in the advanced settings under ‘Bottom / Top Thickness’. It is desirable to form a minimum of 6 layers and 8 for extruders with a smaller nozzle diameter and, accordingly, a smaller plastic diameter. So if the layer height is 0.1mm, set ‘Bottom / Top Thickness’ to 0.6mm. If this does not help, increase the thickness to 0.
8 mm.
3D printing problem checklist:
hollows, holes on the top of the model- Increase the diameter of the printing plastic
- Make sure the coolers are correctly installed and working
- Specify the speed of the cooler in manual mode - in G-code 9027 Increase the thickness of the top layer
Plastic residue
Problem description
Unwanted plastic residue forms between parts of the model.
What causes this problem during 3D printing?
When the extruder is moving and not printing (in idle mode), plastic residue is still coming in.
Solving the problem:
plastic residue (more detailed article on troubleshooting plastic residue between parts of the 3D model)- Activate the Retraction option. Retraction is a very useful option, especially when it comes to finishing. It works very simply - before the print head begins to move, the plastic flows back into the extruder, and is not fed.
Thus, the problem can be nipped in the bud.
- One-click backfeed activation. Most apps like Cura offer a one-click option to activate this option. The default settings are used, which is sufficient for most cases. However, if you want more flexibility, there should be other options. For example, you can set the minimum printhead path before activating plastic backfeed.
- Minimum travel (mm). Reducing the minimum path is usually the quickest fix if the standard retraction settings didn't help. Decrease this value by 0.5 mm until the problem goes away. By the way, activating reverse feed will increase the speed of 3D printing.
- Just cut off the rest of the plastic. This is not the most elegant solution, but by far the easiest and fastest.
Cheklist of 3D Problem:
Residual plastic- Turn on the return submission of plastic (Retraction option)
- Set up the minimum path before starting feedback
- Just delete the remaining plastic with a knife
Regularly
The 3D printer cannot feed the required amount of plastic (or at the required speed).
As a result, thin layers are formed, layers with unwanted depressions or layers are completely absent.
What causes this problem during 3D printing?
There may be several reasons. The first is that the diameter of the plastic for printing does not match the diameter specified in the software for forming layers. The second - the amount of plastic supplied is insufficient, due to incorrect settings in the software. Well, perhaps your extruder is very dirty.
Solving the problem: Insufficient supply of plastic
- Check the diameter of the plastic. Start with the simplest case - check the plastic diameter settings in your software. If you are not sure about the correct diameter, it and the temperature are usually indicated on the packaging of the plastic.
- Measure the plastic diameter. If the problem still persists, measure the plastic diameter manually and enter more precise settings in your G-code generation software.
- Check the print head. In most printers, the print head is retracted from the print table. Check extruder. There should be no obvious contamination on it.
- Set the extrusion ratio. If there is no difference between the actual plastic diameter and the settings in the software, check the extrusion coefficient (extrusion multiplier or flow rate or flow compensation). Perhaps these settings are too small. Each program handles these settings differently, but the principle is the same - increase the value in the settings by 5% and restart 3D printing.
In Simplify3D open Edit Process Settings and go to Extruder tab - extrusion ratio set to 1.0 corresponds to 100%; If you are using Cura, open the Material tab and increase the Flow setting (you may need to activate the Flow settings in the Preferences panel).
3D Printing Problem Checklist: Plastic Insufficiency
- Check Print Plastic Diameter
- Manually Check Plastic Diameter
- Check Extruder Cleanliness
- Increase extrusion ratio by 5%
Too much plastic feeding
Problem description
Your 3D printer is feeding too much plastic.
Because of this, the material peels off at the edges of the model.
What causes this problem during 3D printing?
This is usually caused by the Extrusion multiplier or Flow in your G-code generation software being set too high (see section above).
Solve the problem: Too much plastic feed
- Extrusion ratio. Open your layering software and make sure the extrusion factor is set to the correct value.
- Feed settings. If the previous point did not help, reduce the flow value (Flow).
3D Printing Problem Checklist: Too Much Plastic Feed
- Check extrusion ratio settings
- Decrease plastic feed value
Layer misalignment
Problem description
Bottom and top layers are shifting relative to each other during 3D printing. Usually the offset is not as large as in the figure, but the above case can also occur.
What causes this problem during 3D printing?
Layer misalignment can occur for a variety of reasons, including a blow to the printer during printing! This problem may manifest itself due to incorrect belt tension or misalignment of screws.
Or due to the fact that the extruder hooked the model and it shifted a little right during printing.
Solving the problem: Layer misalignment
- Check the stability of the printer. The 3D printer must be placed on a stable surface. Even slight shocks can cause the layers to shift.
- Check table stability. Most 3D printers have removable tables. Although this is convenient in terms of replacing it, over time the mounting screws can loosen. So it's worth checking them periodically.
- Check the bottom layers. If you print at high quality, the underlying layers may break off due to cooling. If a break occurs, the plastic rises and the extruder can hit it. In most cases, the model will come off the table, but if there is no lift, the powerful motors can push the model and the table. So if you have problems with the first layers, try reducing the rotation speed of the coolers.
- The print speed is too fast.
Raising the temperature and increasing the feed can speed up 3D printing. However, even though the plastic will feed properly, your printer may not be able to handle the selected mode. If you hear clicks while printing, this is a sure sign that the printer is running at too fast speeds. In this case, check if the plastic breaks in the extruder itself, and then go to the settings for the actual speed of the 3D printer. The speed can be adjusted in your software to generate the g-code. If you are using Simply 3D go to ‘Other > Default Printing Speed (mm/min)’, if Cura go to ‘Basic > Print Speed (mm/s)’.
- Check belts. If the layers are still shifting, it's time to check the belts. The tension of all belts must be the same. Timing belts tend to stretch over time (this is clearly manifested when the belts begin to slip on the pulleys). If the tension is very weak, you should consider replacing them. Strong belt tension can also be a problem. But usually this is a problem with DIY 3D printers.
On some 3D printers (like the Prusa i3), special screws are provided to adjust the tension.
- Guide shafts must be clean and lubricated. Over time, the guides become covered with dirt in places with maximum friction. This, in turn, can cause problems when moving and shifting layers. A quick cleaning and lubrication usually solves the problem.
- Curved or misaligned rails. If you notice that the print head position error occurs in a certain place, this may be a sign that one of the guides is deformed. You can check this by turning off the 3D printer and moving the print head along the coordinate axes. Check axle alignment. If everything is in order, remove the guides and lay them on a flat surface. If there is a bend, you will immediately see it.
3D Printing Problem Checklist: Layer Misalignment
- Check the stability of the 3D printer base.
- Check table stability.
- The first layers of the model should not form cliffs.
- The print speed is too fast.
- Check belts.
- Guide shafts must be clean and lubricated.
- Curved or misaligned rails.
Blocked plastic feed mechanism
Problem description
You start 3D printing, but no plastic comes out of the extruder. You took the rod out of the extruder, put it back in, but it didn't work.
What causes this problem during 3D printing?
After replacing the plastic, a small piece of bar remained in the feed mechanism. Most often, the break occurs at the very end. When you insert a new rod, the remnants of the old one block the flow of plastic.
The second option - the remnants of the old plastic dried up at the end of the extruder. In this case, the remnants of the frozen plastic must be removed manually.
Solving the problem: blocked plastic feed mechanism
- Unlock with a needle. If you're lucky, unlocking the feed mechanism is quick and easy.
Start by removing the plastic. After that, on the control panel, select the option “heat up nozzle” (heat up the extruder) and increase the temperature to the level of plastic melting. If you have an Ultimaker 2 3D printer, go to Maintenance > Heat Up nozzle. For PLA plastic, set the temperature to 220 C. When the extruder is hot, use a needle or something with a small diameter and clean the hole (be careful not to burn your hands!). By the way, it is useful to clean the outside of the extruder.
- Push through the old plastic. If the extruder is still blocked, you may be able to push the stuck plastic through with a new rod. Remove the plastic supply tube from the print head. Preheat the extruder to 220 C for PLA plastic and then, using a new rod, try to push the stuck plastic through the extruder. It may take some effort, but be careful not to bend the printer's horizontal guides. After that, you can clean the nozzle with a needle in accordance with the instructions from point 1.
- Remove and reassemble the extruder. In extreme cases, you will have to disassemble and reassemble the plastic feed mechanism. If you've never done this before, consider taking photos or recording your every step as you take apart the feed mechanism, as you'll need to put it back together afterwards. First remove the plastic bar. After that, read the instructions for dismantling the print head in the instructions for your 3D printer. Wear gloves while doing this, as the nozzle will be hot. Let's take a closer look at the Ultimaker 2 3D printer as an example. Move the print head to the center of the printer. Loosen the four screws on the print head. Preheat the nozzle to 220 C (for PLA). When the extruder reaches the desired temperature, turn off the power. Holding the cooler's plastic case, remove the rest of the interfering plastic. Clean the nozzle with a needle. You can also clean its outer surface. When the nozzle is cool, assemble the extruder, turn on the 3D printer and load new plastic.
3D printing problem checklist: blocked plastic feed mechanism
- Warm up the nozzle and clean it inside and out with a needle.
- Remove the plastic feed tube and try pushing through the remaining plastic with a new rod.
- Disassemble the feed mechanism and try to remove any remaining plastic.
Faulty plastic
Problem description
Plastic appears to be fine, correctly seated in the feed mechanism, and exits the nozzle when printing. This happens most often in Bowden-feed 3D printers rather than straight-feed 3D printers, as the plastic isn't visible or noticeable when it's broken.
What causes this problem during 3D printing?
Printing plastic breakage can occur for various reasons, but mostly because the plastic is old or cheap. Most plastics like PLA and ABS last a long time, but if stored in poor conditions (such as direct sunlight), they can become brittle. If you use such plastic, no settings will help.
The second possible reason is the bar diameter, which may vary slightly depending on the manufacturer. And if the pressure in the feed mechanism is too high, it can break.
Troubleshooting: broken plastic
- Remove the plastic. The first thing to do is to remove the plastic from the 3D printer. If you are using Ultimaker, you can use the Maintenance and Change Material option. Heat up the extruder and remove the plastic.
- Try another plastic. If the problem persists after reinstalling the plastic, try a different one to make sure the media quality is not the problem.
- Reduce feeder pressure. If the new plastic also breaks, loosen the pressure on the feed mechanism. Start 3D printing and increase the pressure until the slip is complete.
- Check nozzle. Check nozzle for cleanliness.
- Check flow and temperature. If problem persists, check nozzle heating.
Also make sure the pitch is 100% and no more.
3D Printing Problem Checklist: Plastic Breakage
- Check the shelf life of plastic
- Check the diameter of the plastic
- Set up the pressure in the supply mechanism
- Check the cleanliness of the nozzle and its temperature
- set the supply of 100%
Glorment of the rod
Description of the problem
Prrukta can start slipping for love. 3D printing stage. And it does not depend on the type of plastic. As a result, no plastic is fed.
What causes this problem during 3D printing?
Clogged nozzle, insufficient feed force, incorrect nozzle temperature. As the motor rotor rotates, the small wheel that normally grips and feeds the plastic will pinch the bar and prevent it from being printed.
Solving the problem: bar slippage
- Help the feed system. If the plastic has just begun to slip, this will show up as a characteristic noise.
Try applying some pressure to the bar to get this section through. This often helps and the 3D printer continues to print well.
- Adjust the feed force. Start by depressurizing. After that, start increasing the force until the bar stops slipping. Heads vary in diameter, so some require fine tuning.
- Remove the plastic. More one solution is to remove and reload the plastic into the feed mechanism. After removing the bar, cut off the plastic over the place where the slip marks are visible and reload it into the feeder. If slippage remains, try this operation again. If that doesn't help, replace the plastic as this one is most likely no longer printable.
- Check nozzle temperature. If you installed a new plastic and the problem persists, or vice versa, check the temperature of the nozzle.
Cheklist of 3D Problem: slippage of the rod
- Help the supply mechanism with an additional force
- Set up the force in the supply mechanism
- Eliminate the plastic and load a re -
- Check the temperature of the nozzle
Bad Semit 9d Seal Seal 9D SEMS0016 Description of the problem
The printed product is missing an internal mesh or it is obviously incorrect
What causes this problem during 3D printing?
There can be several reasons why the internal structure of the 3D model does not print well.
The most common is incorrect settings in your software for generating a G-code. It may turn out that the problem is a clogged nozzle.
Solving the problem: Poor 3D printing of the inner mesh
- Check the fill factor. This is checked in your software. A value of about 20% is quite acceptable. If less, problems may arise. This parameter should be increased for large models.
- Speed for printing inner layers. The speed at which printing takes place can have a direct effect on the quality of the inner grid. If you see problems, try reducing the print speed of the inner mesh.
- Change the mesh configuration. Most programs allow you to change the grid configuration. Squares, triangles, hexagons, etc. Experiment with these settings.
- Check nozzle. It may be that the cause is a clogged nozzle. At the same time, the outer parts of the model will be printed well, since plastic is fed more intensively on them.
3D Printing Problem Checklist: Poor 3D Printing of Inner Mesh
- Check and Adjust Inflation Ratio of Model
- Reduce Inner Mesh Print Speed
- Change Mesh Configuration
- Check Inner Nozzle
- 0013
Description of the problem
The printed model generally looks normal, but the internal mesh is visible through the outer walls of the model.
What causes this problem during 3D printing?
See-through problem occurs when your model has thin walls and the internal structure intersects with the outer wall line.
Normally the outer wall thickness should be proportional to the nozzle diameter. That is, if your nozzle diameter is 0.4 mm, the wall thickness of the model should be 0.5, 0.8, 0.12 mm, etc. If the proportion is not maintained, the effects of the clearance of the internal structure may occur.
Problem Solved: Inner mesh showing through
- Check the outer wall thickness of your 3D model.
Check that the wall thickness value is proportional to the nozzle diameter.
- Increase the outer wall thickness. The simplest solution is to increase the wall thickness. Doubling the thickness will most likely help solve the clearance problem.
- Use the filling option after the walls have been formed. Most g-code programs have the ability to generate the internal structure after printing the outer walls.
- In Cura open 'Expert Settings' and in the Infill section activate the option 'Infill prints after perimeters'
- In Simply3D click on 'Edit Process Settings', then select 'Layer' and in 'Layer Settings' select 'Outside-in' next to 'Outline Direction'.
- Check the print table. Examine the printed model. If the effect is more on one of the sides, the cause may be in the calibration. If so, calibrate.
- Use this effect to your advantage. Depending on the task, you can use the print sequence to your advantage.
If you need a model of high quality, with a good outer surface and at the same time the rigidity of the model is not critical, choose Outside-in printing (first the outer layer, then the inner filling). If the rigidity of the model is important, print inside-out, doubling the wall thickness.
3D printing problem checklist: inner mesh shows through
- Check the outer wall thickness of the model.
- Thicken the outer wall.
- Use the filling option after wall formation.
- Check print bed and calibrate if necessary.
- Use this effect to your advantage.
Gaps between inner mesh and outer walls
Problem Description
If you look at the bottom or top surfaces of the model, you will see gaps between the inner mesh and outer walls.
What causes this problem during 3D printing?
Gaps between outer wall and inner mesh used to be a common problem, but with the increasing accuracy of 3D printers, this is now a rare bug.
However, there are new materials for 3D printing that can cause this problem again.
The most common cause of these gaps is that your software does not have an overlap of the mesh and outer walls set, or this value is set to "0". Your 3D printer considers this so that the wall and mesh should not intersect, and gaps may occur.
Another possible reason is the sequence in which you set the printing of the inner mesh and the outer wall. If you print the outer wall first, there may be no or minimal overlap. Accordingly, there is a chance of occurrence of these gaps.
Solving the problem:
gaps between the inner mesh and the outer walls of the 3D model- Check the parameter of the intersection of the walls and the inner mesh of the model. This is the most common problem and is very easy to fix. Find the "Infill Overlap" option in your gcode generation software and increase this value.
- Cura defaults to 15%.
Increase it to 30%.
- In Simplify3D these settings are in the 'Edit Process Settings > Infill > Outline Overlap' tab. Again, increase this value. This setting is directly related to the thickness of your head. So the % value will be % of the bar thickness to be printed. When tuning, do not set this value above 50%, as you will go beyond the walls.
- Cura defaults to 15%.
- Form the inner mesh before printing the walls. If at the same time the inner mesh begins to show through, increase the thickness of the outer wall of the model as indicated in the section above.
- Increase extruder temperature. Some newer 3D printing materials (such as XT-CF20) may require finer temperature settings. Try increasing the extruder temperature by 5-10º. It might work.
- Reduce speed. You probably want to print your model faster, but faster speeds can cause a lot of problems. Especially if the 3D printer is not perfectly calibrated.
If print speed is still important to you, try lowering it for the top layer only.
3D printing problem checklist: gaps between inner mesh and outer walls of the 3D model
- Check the intersection parameter between the walls and the inner mesh of the model.
- Print the inner mesh first and then move on to the outer walls.
- Increase extruder temperature.
- Reduce the print speed.
Intersection of objects
Problem description
Parts of the model are missing or the final model is not rigid enough. The finished product and the 3D model are different and there are incomprehensible errors in the geometry of the printed product.
What causes this problem during 3D printing?
Virtual walls are one of the most common causes. Vertical walls only exist in 3D space, not in the real world.
For example, if you have two cubes in the real world and you try to match them, it won't work because the outer walls won't let the two objects intersect.
In the 3D world you can combine two objects and still exist as two separate objects and your slicing program will also allow them to intersect in the virtual world.
For correct printing, these two objects must be combined into one so that the inner walls disappear and one object remains.
Another possible problem - for example, you have a cube object and you have deleted one of its surfaces. In fact, you have an object with a hole. It may look like a 3D correct object, but it only exists as such in 3D space. Such an object cannot exist in the real world.
Deleting one of the surfaces leaves only two coordinates. The wall thickness, the third coordinate, has no dimension in the real world. We only see it in 3D modeling software. And when we start to form the layers of the model, the program will try to fix this bug and add the third coordinate. However, in more complex models, this can lead to unpredictable effects.
Solving the problem: object intersection
- Use the latest slicing software.
Most recent versions of slicing programs support automatic correction of intersecting objects, but it's still better to make sure that your 3D model is formed correctly.
- Set the Fix Horrible settings in Cura. In Cura, open the Expert Settings tab with the 'Fix Horrible' option set to match all (Type-A).
- Set Silmplify3D's Non-manifold settings. In the 'Process settings' select the 'Advanced' menu and then 'Heal' next to Non-manifold.
- Use layered representation. Use the layer view in your slicing software to check for problem areas in your model. A superficial view of the layers can help you quickly identify problem areas and fix the problem.
- Use your software to fix object intersections. One of the easiest solutions is to use additional software to solve the problem. Blender and Meshmixer have built-in mechanisms for identifying problems and fixing the 3D model before slicing.
- Merge objects. It's better to fix your 3D model before importing it into the slicing software. When doing this, make sure that if your two objects intersect or overlap, you use the appropriate intersect, merge, or subtract function.
3D Printing Problem Checklist: Object Intersection
- Please use the latest version of your slicing software.
- Use the "Fix Horrible" option (in Cura).
- Use the “Fix Non-manifold” option (in Simplify3D).
- Use layered view to identify the problem.
- To correct errors, use additional software like Blender or Meshmixer.
- Merge objects.
No base for next layers
Description of the problem
You have loaded your 3D model into the slicing software and everything looks good. We started printing and as a result part of the model was printed well, and some parts - badly. This is a fairly common problem in 3D printing.
What causes this problem during 3D printing?
During 3D printing, each layer is built on top of the previous one.
Naturally, if your model has a part that does not have plastic underneath (for example, as shown in the figure above - horizontally outstretched arms), printing problems will arise.
Ideally, the slicing software should somehow detect and point out this problem. However, in most cases, the programs will let us print without indicating that additional supports are needed for the model.
Problem solved: no base for next layers
- Add supports. The quickest and easiest solution is to add calipers. In most programs, this is done quite simply. For example, in Simplify3D go to Edit Process Settings > Support > Generate support material; you can customize the quantity, shape and specify other caliper settings. If you are using Cura, just select Support type in the Basic settings.
- Make your own calipers. Software generated calipers may not suit you, so you can create your own in the base 3D model. This will require a little more skill, but can give fantastic results.
- Add an additional object to your 3D model. Most often, problems occur when printing hands and similar details. In this case, adding supports from the base of the model to the arm can also result in a problem, since the distance can be quite large. Considering that the calipers should be easy to remove, the high height may prevent them from being printed correctly. You can get around this by adding an additional object to your model (a piece of wall, a bench, a box, a flower, etc.) and printing an additional rack already from this object.
- Change the angle. For example, models of people whose arms are raised at 45º will print well and it is absolutely impossible to print arms stretched horizontally at 90º relative to the body.
- Divide the model into separate parts. Another option is to divide the model into separate parts and print two pieces instead of one. The only problem that will need to be solved is how to combine the resulting parts into one model after printing.
3D printing problem checklist: no base for next layers
- Add Software for Slosing
- Add calipers in the original model
- Add an object that can be replaced by a caliper
- Change the angle of the problem node
- Separate the
Slove
description problems
As the model builds, the layers begin to shift. As a result, instead of a straight vertical model, displacements appear. In this case, the offsets are not the same over the entire height of the model. The offset can increase/decrease at different heights.
What causes this problem during 3D printing?
The reason is quite simple. One of the belts connected to the stepper motor has lost tension. To eliminate model drift, it is enough to check the tension of the belts and the pulleys that keep the belts in tension.
At first glance, the solution to the problem is simple. However, before you fix it, you should find out which belt is causing it, as getting to the belt can be a difficult task.
Solving the problem: layer shift
- Check the X and Y axes. If the model moves to the left or right, the problem is in the X axis. Forward or backward, the problem is in the Y axis. When you have decided on the coordinate, check the belts and pulleys. If you have a Prusa i3 3D printer, this shouldn't be a problem since the pulleys are mounted on the stepper motors themselves. In printers like Ultimaker, you will have to tinker.
- Tighten the pulleys on the stepper motors. Check all belts and pulleys. More complex arrangements such as the Ultimaker 2 have multiple belts and pulleys. On the main axes X, Y, eight pulleys are installed on top of the printer. Review and pull up each of them.
3D Printing Problem Checklist: Layer Offset
- Check the X and Y axes.
- Tighten all pulleys along the problem axis.
In Russia, the first concrete house was printed for 594,000 rubles / Sudo Null IT News Here is a video from 1946.
In general, this idea of Thomas Edison is more than 100 years old (patent). Over the decades, concrete printing technology has changed, full-fledged 3D printing for individual projects has begun to be used. Now these houses look much nicer. For example, in February 2017, a residential building was printed in Stupino, near Moscow, on an Apis Cor construction printer. This is the first house in the Russian Federation, printed as a whole, and not assembled from printed panels.
Building area 38 m². The total cost of turnkey construction, including the foundation, walls, ceilings, roofing, electrical wiring, doors and windows, exterior and interior decoration, amounted to 593,568.19 rubles (detailed estimate), but this is without the cost of the work of some specialists.
The printer is completely mobile. The loader brings it in the back and installs it on the prepared foundation at the construction site.The printer is connected by a hose to a large concrete mixer, that is, an automatic system for mixing and supplying the mixture.
It looks like this.
Then the work begins. All work on the construction of the house took about two months in Stupino. The project started in December 2016 and ended in February 2017. The advertised 24 hours is just the pure machine time of the Apis Cor printer. It was included at different stages to print self-supporting walls, partitions and building envelopes.
The device has an interesting design. It is located on a movable arm in the center and prints around itself, gradually rising. After the printing of wall structures is completed, it is removed with a crane - and it continues to work outside.
The appliance itself consumes 8 kW during the process, so you need to provide it with electricity during construction work.
The cost of printing a concrete house is much cheaper than building a conventional "box" of blocks.
In addition, such houses have a lot of additional advantages, which makes them truly unique.
1. Practically arbitrary shape of the walls. Rounded walls with any corners. Here, the accuracy of construction is perfect, a drunken bricklayer will definitely not screw up your project. The printer has a built-in automatic leveling and stabilization system.
2. The walls are ready for painting with decorative plaster immediately after processing. You can roll yourself in one day and paint the house in arbitrary colors, and then repaint to suit your mood at any time. Plastering with a level and beacons is not required. There is an additional reduction in the cost of finishing work. This applies to both interior and exterior finishes.
3. You can perfectly plan the shape of the walls, the size and position of the windows, taking into account the surrounding landscape and lighting. By the way, there is an assumption that the walls on one side can be made slightly inclined to further increase the illumination. However, the design fantasy is limited by the available forms of double-glazed windows, because here you can’t get by with ordinary glasses, you need to install double-glazed windows so as not to freeze in winter.
Among the disadvantages that come to mind is the flat roof.
It is clear that the developer guarantees that the roof effectively withstands high snow and operational loads. But it seems that stagnant water can accumulate on such a roof with all the ensuing (or rather, not ensuing) consequences. To prevent this from happening, a special wedge-shaped thermal insulation PIR Slope is used on the roof - a ready-made constructor for creating the necessary slopes and counter-slopes. They say that precipitation will be effectively removed from the roof surface, but still somehow unusual.
How the thermal insulation between the inner and outer walls will work is also interesting to check. Now the developer is experimenting with two methods of insulation: from Logicpir filling crumbs on one part of the house (thermal conductivity 0.022 W / m * K) and polyurethane filler composition on the other (0.023-0.025 W / m * K). Insulation was carried out simultaneously with the printing of structures, which significantly increased the construction time.
Well, not everyone will like the small size of the house - after all, not everyone is ready to live in a one-room apartment, a small studio. Although such an option for 38 m² is quite suitable for a single person to live. In addition, as mentioned, the technology allows you to build larger houses.
Yes, and for a round house, you will have to buy a concave TV if you want to play computer games on a big screen.
This technology can also be used to print three-story houses, but they will cost much more than $10,000.
Other disadvantages are restrictions on construction dates. The use of a concrete mixture used as "ink" is possible only at a temperature of 5 ° C above zero. So if you do not want to put up an awning with a heater, then construction in winter is impossible. In the future, they promise that the printer will learn how to work with geopolymer concrete from natural components - such material can be printed at lower temperatures.
In addition, it is superior to ordinary concrete in other parameters.
After all, there is definitely no place in the house to install a boiler or other heating system. Probably the only option for living in winter is an electric heater.
The estimate for the first house was around $10,000, although the estimate does not include the work of all specialists. The estimate includes the installation of window and door blocks, wall decoration, facade painting, drainage, waterproofing, thermal insulation, but the rest of the work is not taken into account. Probably, with these works, a turnkey house will come out twice as expensive, that is, approximately $20,000.0005
Foundation RUB 14,819 Walls RUB 95,629.64 Ceilings, roofing RUB 144,267.55 Wiring RUB 12,650 Doors and windows 211 052 RUB Exterior finish RUB 46,250 Interior trim RUB 68,900 But the contractor notes that expensive materials were used in this demonstration project.
Learn more
- Check the outer wall thickness of your 3D model.
Slid of the layer 9000.
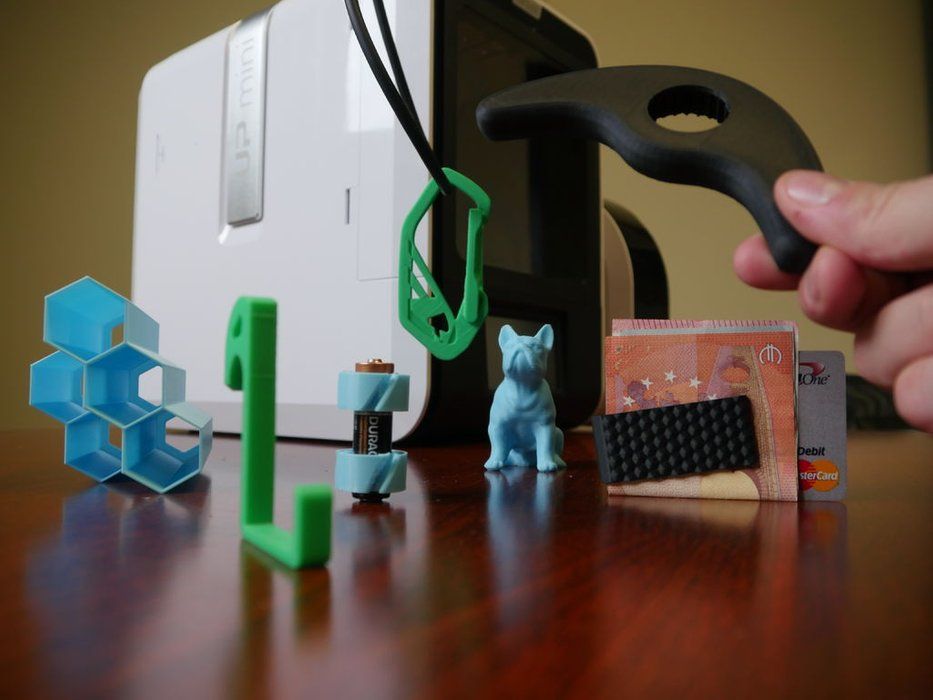
Some layers in the model are misaligned.
What causes this problem during 3D printing?
Your 3D printer belts are not tight enough. The top of the print table is not stable. One of the Z guides is not a straight line.