3D printer magnets
Researchers develop new method of 3D printing magnetic cores for electrical machines
0Shares
Researchers from the Tallinn University of Technology and the Estonian University of Life Sciences are investigating the use of 3D printing technology to produce soft magnetic cores.
Magnetic cores are pieces of magnetic material with high permeability. They’re commonly used to guide and direct magnetic fields in a wide variety of electrical systems and machines, including electromagnets, transformers, electric motors, generators, inductors, and other magnetic assemblies.
Until now, the 3D printing of soft magnetic cores has been a major challenge due to difficulties in preserving core efficiency. The research team has now proposed a comprehensive laser-based additive manufacturing workflow that they claim can yield superior magnetic properties to soft magnetic composites.
A ferrite inductor comprises a magnetic core surrounded by a copper coil. Image via Jurgis Mankauskas.3D printing electromagnetic materials
The additive manufacturing of metals with electromagnetic properties is an emerging field of research. The electrical machine research community is now beginning to develop and integrate its own 3D printed components into systems, citing design freedom as a huge benefit for innovation.
For instance, 3D printing functional complex parts with magnetic and electrical properties could pave the way for custom machines with embedded motors, actuators, electrical circuits, and gearboxes. Such machines could be produced in digital manufacturing facilities with minimal assembly, post-processing, and material waste, with many of the moving components 3D printed.
Unfortunately, 3D printing large sections of complex electrical machines is still not a reality due to several factors. These devices often have challenging requirements such as small air gaps for improved power density, not to mention the need for multi-material assemblies.
As such, research so far has primarily focused on more ‘basic’ parts such as 3D printed soft magnetic rotors, copper coils, and alumina heat guides. Soft magnetic cores are also of significant interest, but minimizing core loss in the 3D printing process is a hurdle yet to be jumped.
A set of printed sample cubes showcasing the effects of laser power and print speed on the magnetic core structures. Photo via Tallinn University of Technology.An optimized 3D printing workflow
With the aim of showcasing an optimized 3D printing workflow for magnetic cores, the researchers determined the best process parameters for the application, including laser power, scanning speed, hatch spacing, and layer thickness.
The team also looked into the effects of annealing parameters to achieve minimal DC losses, quasi-static, hysteresis losses, and the highest magnetic permeability. The optimal annealing temperature was determined to be 1200°C, which resulted in the highest relative density of 99. 86%, the lowest surface roughness of 0.041mm, minimal hysteresis losses of 0.8W/kg, and ultimate yield strength of 420MPa.
Ultimately, the Estonian researchers have shown that laser-based metal additive manufacturing is a viable method of 3D printing magnetic core materials for electrical machine applications.
As far as future work goes, the team intends to characterize the parts’ microstrutures to gain insights into grain size and grain orientation, as well as their effects on magnetic permeability and strength. The researchers will also further investigate ways of optimizing the geometries of the 3D printed cores for improved performance.
Further details of the study can be found in the paper titled ‘Laser Additively Manufactured Magnetic Core Design and Process for Electrical Machine Applications’.
The effects of energy input on the surface roughness of 3D printed magnetic cores. Image via Tallinn University of Technology.The combination of 3D printing and magnetism allows for a whole host of novel applications, beyond just electrical machines. Earlier this year, an international team of scientists led by Cambridge University’s Cavendish Laboratory used 3D printing to develop a set of microscopic nanomagnets. Created using a custom 3D printing process, the nanomagnets are in the shape of a DNA-inspired double helix and show promise in domains such as particle trapping, imaging techniques, and smart materials.
Elsewhere, researchers at the IMDEA Nanoscience Institute, an interdisciplinary research center in Spain, recently developed a new method of 3D printing magnets using recycled materials. The work was conducted as an answer to the supply chain issues caused by the COVID-19 pandemic, which left the manufacturing sector short on many materials, including those required to make magnets.
Subscribe to the 3D Printing Industry newsletter for the latest news in additive manufacturing. You can also stay connected by following us on Twitter, liking us on Facebook, and tuning into the 3D Printing Industry YouTube Channel.
Looking for a career in additive manufacturing? Visit 3D Printing Jobs for a selection of roles in the industry.
Featured image shows a ferrite inductor comprising a magnetic core surrounded by a copper coil. Image via Jurgis Mankauskas.
Tags Estonian University of Life Sciences Tallinn University of Technology
Kubi Sertoglu
Kubi Sertoglu holds a degree in Mechanical Engineering, combining an affinity for writing with a technical background to deliver the latest news and reviews in additive manufacturing.
What is Fluxprint? | Magnetic 3D Printing
Search
Please stay in touch.
Search
Hardware
What is Fluxprint?
Imagine creating fully-optimized composite materials with the press of a button. Magnetic 3D printing, or Fluxprint, does just that. No complex fabrication, no sub-par materials. Just custom composites within hours.
Fluxprint is an additive manufacturing process that creates precisely-tailored composites such as carbon fiber. This method combines the benefits of 3D printing and composites. Composites are among the most advanced materials available. 3D printing is an incredibly fast, hands-off fabrication process that can form nearly any geometry. Fluxprint goes a step further by precisely tailoring composites voxel-by-voxel to create the ideal material for a project.
Fluxprint can
produce durable parts in detailed geometries such as this injection mold. The Purpose of FluxprintFluxprint produces fully customized composite materials. Composites such as carbon fiber have incredible mechanical properties; carbon fiber outperforms steel, aluminum, and engineering plastics in most applications. If everything could be made of composites, they would be. But composites are a less common material because of their traditional lay-up fabrication process, which is time-consuming and expensive.
With Fluxprint, composites can not only be quickly and easily formed into any geometry, but they can also be tailored precisely to meet the needs of the project. Strength, stiffness, weight, and other mechanical properties can be adjusted voxel by voxel. The result is functional printed parts for applications that could not otherwise be made with 3D printing.
The Fluxprint process uses DLP 3D printing and magnets to create a fully-optimized, high-resolution object. Scale bar: (c) 2, 500, and 50 mm from left to right. How Fluxprint WorksIn Fluxprint,
(a) Electromagnets apply a precise magnetic field to a composite SLA resin.
(b) A digital light processing (DLP) projector selectively polymerizes the composite resin.
(c) Steps (a) and (b) are repeated multiple times within each layer to achieve different alignment directions.
(d) The build plate moves upwards to repeat steps (a)-(c) in a new layer.
(e) Steps (a)-(d) are repeated until a tightly-toleranced part has been produced with a composite microstructure that is optimized for its application.
Fluxprint can produce detailed reinforcement micro-architectures such as the Golden Ratio (above) that exhibits discrete reinforcement regions of 90 μm and lower.
Applications of FluxprintFluxprint is a revolutionary fabrication method in the automotive industry, aerospace, and product design. In auto design, cars are stronger, lighter, and safer with guided stress cracking, all while saving time and money in fabrication. The same goes for aerospace, where it’s essential to optimize material properties for a safe, lightweight aircraft. Fluxprint also brings the benefits of composites to injection molding; composite injection mold tools can be made in days instead of months, and produce hundreds of accurate prototypes molded with end-use plastics. Across a range of industries, Fluxprint is replacing parts that were previously machined, cast, or molded with hands-off digital fabrication and optimized material properties.
Fluxprint is the Fluxprint process that fuels Digital Composite Manufacturing. With DCM, you can have fully-optimized composites in hand within hours. This manufacturing method opens up the benefits of 3D printing to high-performance parts. This means low cost, high speed, limitless geometries, and no machining required. DCM opens up new possibilities in materials, making fabrication faster and products better.
3D printed magnets of a given shape This limits their shape. Engineers and designers have to choose between available shapes of magnets when developing products.
On the other hand, polymer magnets (polymagnets) have recently appeared. They use a mixture of NdFeB magnetic powder (granule diameter of about 45 microns) and plastic or rubber, and are made by injection molding. These magnets have almost arbitrary shape. In fact, you can pre-program the shape of the magnetic field - and make a permanent magnet of the required shape specifically for your design. This technology is already used in industry, and magnets are used, among other things, for various tricks.
Polymer magnets have a disadvantage. For technological and economic reasons, they are made from an isotropic powder, so the strength - the value of (BH) max - of such magnets is two or more times inferior to the strength of ordinary magnets. It would be possible to use a magnetic powder with better properties, but in this case the economic sense of producing such magnets is lost, because their cost increases greatly, and the increased (BH) max , that is, a strong magnet, is not needed by everyone. However, this is not about that.
Until now, there has been no technology for the piece production of polymer magnets with a complex structure. Thanks to engineers from the Technical University of Vienna, the first work in this area appeared. For the manufacture of magnets, engineers used 3D printing (and for quality comparison, they also used conventional injection molding).
Technical University of Vienna engineers next to a printer, a magnetic field computer, a 3D printer and a filament for printing a polymer magnet
Materials for 3D printing and injection molding are made by processing a commercial mixture of Neofer 25/60p. In this powder, NdFeB particles are mixed into polyamide 11, which is clearly visible in the photograph from the microscope.
Neofer 25/60p powder in SEM
Polyamide 11 is a highly elastic engineering plastic, just what you need. In the powder, NdFeB granules are mixed randomly, which leads to isotropic properties of the magnet.
Material properties are shown in the table: starting powder, 3D printing mix and casting mix.
Scanning electron microscope study showed that the NdFeB particles in the Neofer 25/60p powder granules are spherical in shape with a size of approximately 50±20 µm. For 3D printing, the material was subjected to pre-atomization and heat treatment. That is, sifted and heated. 5 mm Neofer 25/60p pellets were then spun into filaments of the desired diameter of 1.75±0.1 mm.
The engineers chose the Builder 3D printer from the Dutch company Code P. This is a commercially available model that is sold online at prices ranging from €1,675 for the smallest model to €3,750 for the largest. The scientists liked the model with a working area of 220 × 210 × 164 mm and a layer thickness of 0.05–0.3 mm. Nozzle diameter - 0.4 mm. It was loaded with threads with a diameter of 1.75 mm. Empirically, we set the optimal print parameters indicated in the table.
Using this method, engineers printed a magnet of a given shape with a pre-calculated magnetic field.
The design of the magnet is calculated by solving Maxwell's equations, as described in the scientific work of Brückner and colleagues on macroscopic simulation of isotropic permanent magnets (1, 2).
Initially, the product did not have a magnetic field, but it was magnetized - placed inside the coil in a magnetic field with an induction of 4 T.
To check the results of the experiment, the strength and direction of the magnetic field, we made and calibrated a device with a Hall sensor with a measurement range of ±130 mT. It made it possible to measure the 3D shape of the magnetic field outside the magnet. The shape almost coincided with the calculated shape of the field of an ideal magnet from a computer simulation.
Comparison of real and calculated magnetic fields along all axes
A complex-shaped product measuring 7 × 5 × 5.5 mm is printed in layers 0.1 mm high with a thickness of elements 0.8 mm. The strength of the resulting magnet indicates that 3D printing is quite suitable for making permanent magnets with complex shapes. Such magnets are not inferior in their properties to polymer magnets made of the same material by injection molding. In addition, they have less mass.
Researchers note that some devices require specially shaped permanent magnets. For example, a magnet that produces a strong field in one direction, but as weak a field as possible in an orthogonal direction.
The great thing is that using the described method, we can make magnets not only of arbitrary shape, but also use a wide variety of materials: from soft magnetic alloys to hard magnetic NdFeB or ferrite alloys.
The ability to locally print magnets of any shape in your workshop from materials with specially selected magnetic properties allows you to make magnets that are not commercially available. And which is generally impossible to produce by traditional production methods.
The scientific work of the Austrian specialists was published on October 17, 2016 in the journal Applied Physics Letters (doi: 10.1063/1.4964856).
Miniature permanent magnets can be printed on a 3D printer. This will allow launching small-scale production of magnets, giving them any shape during the manufacturing process, and creating complex configurations of magnets. Such magnets are suitable for miniature electric motors and electric generators that operate pacemakers.
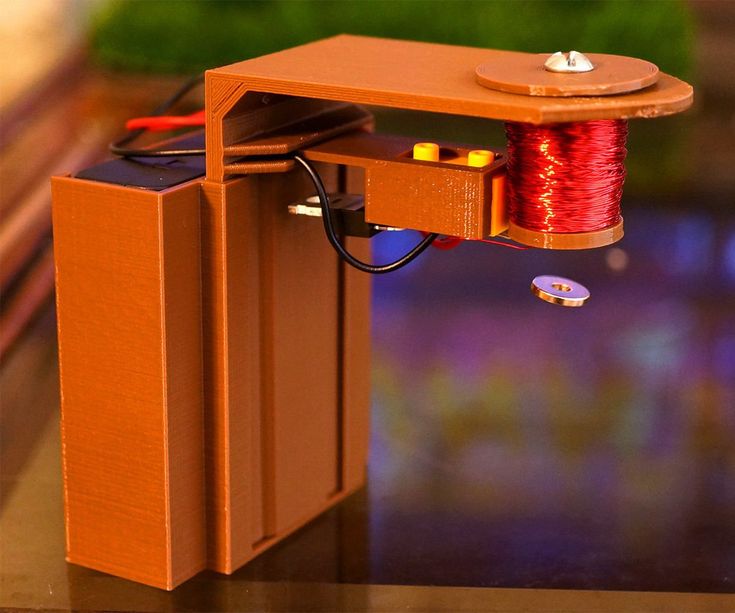
The creation of complex and small magnets is a difficult scientific and technical task, but they are in demand in various specialized applications, primarily medical ones. One of the most promising ways to create complex-shaped parts from hard magnetic materials is 3D printing. Ural scientists managed to determine the optimal parameters for 3D printing of permanent magnets using selective laser sintering. This is an additive manufacturing method in which a magnetic material in the form of a powder is sintered in layers into a three-dimensional product of a given shape according to a pre-created 3D model. This technology allows you to change the internal properties of the magnet at almost all stages of production. For example, to change the chemical composition of the compound, the degree of spatial orientation of crystallites and crystallographic texture, to influence the coercive force (resistance to demagnetization).
“Producing small magnets is a difficult task. Now they are created only by cutting a large magnet into pieces, due to machining, about half of the material used turns into garbage. Also, when cutting, a large number of defects are introduced into the near-surface layer, due to which the properties of the magnet deteriorate extremely. Additive technologies make it possible to avoid this and make complex magnets, for example, with one north pole and two spatially spaced south poles, or a magnet with five south and five north poles at once. Such configurations are necessary for pacemakers, in which it is possible to assemble a rotor for an electric motor from individual magnets only under a microscope, ”explains Dmitry Neznakhin, Associate Professor of the Department of Magnetism and Magnetic Nanomaterials, Researcher at the Department of Magnetism of Solids of UrFU.
Now scientists have managed to make thin, about one millimeter, permanent magnets, the properties of which were similar to commercially produced magnets. The basis was a powder containing samarium, zirconium, iron and titanium. The connection has suitable characteristics for permanent magnets, however, traditional manufacturing methods deprive the connection of most of the properties. Therefore, scientists decided to check whether it would be possible to preserve the properties using the new technology.
“When creating permanent magnets based on these compounds by traditional methods, the properties of finished products are far from theoretically predicted. We have found that during sample sintering, the addition of low-melting powder from an alloy of samarium, copper, and cobalt makes it possible to preserve the magnetic characteristics of the main magnetic powder. This alloy melts at temperatures lower than the properties of the base alloy change, so the final material retains its coercive force and density,” Dmitry Neznakhin adds.
At the moment, scientists are establishing the main patterns of formation of the microstructure and magnetic properties of hard magnetic materials, determine which of the magnetic materials can be used to manufacture permanent magnets using the laser sintering method.