3D water printing
5 Ways 3D Printing Is Revolutionizing Water - 3DPrint.com
Today almost one-fifth of the world’s population live in areas of water scarcity. By the year 2025, that number will rise to 1.8 billion people. From drinking water to water for fish farms to treating wastewater, we need to revolutionize obtaining and using water to survive.
Technology is starting a water revolution when we need it most. 3D Printing in the water and wastewater industries has the potential in cost-effectively treat polluted water. Groundbreaking 3D printing technology opens the possibility to transform water infrastructures.
The water revolution uses 3D printing in five innovative ways.
1. Improved Water Quality in Fish FarmsFish farming, or aquaculture, makes up 47% of global fish production, accounting for over 80 million tonnes of fish in 2016. Fish farms make up most of the growth within the global market and are necessary to keep up with the demands of human consumption.
With fish farms growing in importance, the science behind commercially raised fish tanks and water enclosures needs to grow as well. Wild water systems have a natural balance, yet commercial operations do not. Water quality, such as acidity, must be controlled.
The convergence of 3D printing and fish farms has led to innovations in testing water quality. New systems can now send remote notifications so that water quality can be monitored consistently. This cost-effective method will allow fish farms to operate more cost-effectively over time.
2. Desalination Creates Potable WaterOver the next 50 years, it is estimated that the world population will increase another 40-50% resulting in increased water scarcity. Water is used for irrigation, household use and industry, yet only a small fraction of the world’s water is potable.
The U.S. Department of Energy is working on plans which use 3D printing to cost-effectively desalinize water. Desalinization is the process of removing mineral components from water, such as salts. By creating this technology with 3D printers, there may soon be a way to increase the supply of water globally effectively.
Photo by Ivan Bandura on Unsplash
3. Inexpensive, Portable Water AnalysisIt’s hard to believe, but one of the leading causes of death in developing countries is contaminated water. Poor water quality leads to illness, which can often be deadly. To solve this problem, there need to be more efficient ways to test and measure water quality. For these rural communities, this means finding a way to test water quality remotely and cost-effectively.
To this end, researchers have developed a simple 3D printed device that can test water quality remotely. The technology uses an 8-megapixel resolution digital camera to record color change necessary to perform a colorimetric assay. The device is battery powered and connected wirelessly for data processing. Technology like this will save lives by identifying contaminants in our water systems.
4.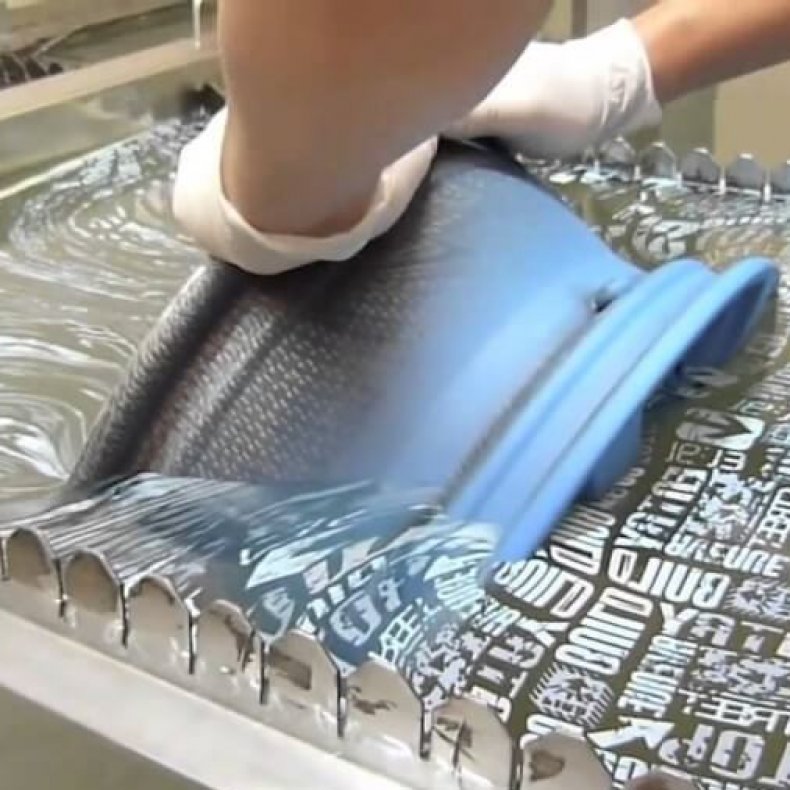
The ability to test contaminated water is incredible, but new and innovative technology which allows us to remove that contamination is revolutionary. While it has been possible to manufacture purification and filtration systems for a long time, the ability to cost-effectively do so in a short period of time through 3D printing means that filtration systems can now reach the neediest places and people.
Filters which rely on nano-fiber membranes are now printed using electro-spinning 3D technology. Products like the Naked Filter use this technology to create filters 70-80% less porous than traditional filters, therefore far more effective in preventing illness from microbes such as Salmonella or e coli.
Image by 后园 卓 from Pixabay
5. Efficient Wastewater TreatmentAccording to the UN-Water’s 2014 World Water Development Report (WWDR), more than 80% of water worldwide is not collected or treated.
Countries such as China and India are growing rapidly and need their water infrastructure to keep up. Wastewater treatment can be expensive in these countries, which is why 3D printing technology that reduces cost has proven to be revolutionary.
Keeping untreated water from entering the environment is vital. Suspended solids, biodegradable organics, pathogenic bacteria and nutrients can be harmful to the environment, making technological improvements to wastewater treatment more critical as water scarcity grows.
Specific areas of innovation are in areas such as 3D printed membrane technology. Components like pumps and items like feed spacers are areas which 3D printing has been able to produce quality, low-cost alternatives to traditional technology.
A 3D Printed Water RevolutionAs water scarcity grows and population increases the demands on our water systems becomes more strained. Technological advances such as 3D printing are helping to create groundbreaking technology to improve our environment and transform communities in need.
Subscribe to Our Email Newsletter
Stay up-to-date on all the latest news from the 3D printing industry and receive information and offers from third party vendors.
Tagged with: 3d printed water • 3d printed water filters • agriculture • clean water • water • water management
Please enable JavaScript to view the comments powered by Disqus.
A Real Water 3D Printer? « Fabbaloo
By Kerry Stevenson on October 6th, 2018 in research
Tags: crystallization, solid, water
A substance can crystallize water [Source: Swanson School of Engineering/Sachin Velankar]Is it possible to 3D print water? While sounding entirely ridiculous, it may be possible to do so.
Some years ago we wrote a fanciful piece for April Fool’s day describing “Nemo”, a hypothetical “water 3D printer”, that would print “water objects”. It was, of course, a silly idea designed simply for the laughs. But now I’m reading some research that might change this completely.
A report from the University of Pittsburgh’s Swanson School of Engineering describes research from several institutions and companies that have been developing what they call a “semicrystalline oligomer hydrate material”. Basically it’s an oligomer (a collection of monomers, as opposed to polymers) which, when added to water, causes the water to crystallize – at room temperature.
This is a very curious behavior, one previously seen only in metals, where the combination of molecules effectively raises the melting point. In other words, this substance appears to make water freeze at higher temperatures. Normally combinations lower the freezing temperature of water, but not the case with this particular substance.
The researchers intend on using the unusual properties of this material for developing capacitors that surround nanotube networks used semiconductor applications. It’s a pretty specific use, but I can think there might be one more: 3D printing.
All 3D printing approaches involve a fundamental core process: solidifying a liquid or powder. Filament is softened and hardened into an object; liquid photopolymer is fused by energy; polymer powders bind together with lasers; metal powder melts together with laser power. All current 3D printers use this principle.
But is there another one? The idea of crystallizing a liquid seems like the same type of process. Could it be used for 3D printing?
Animation of water crystallization [Source: Swanson School of Engineering/Sachin Velankar]It may be that this particular substance may be unsuitable as it apparently takes some time for the crystallization to occur. There is also the matter of print strength: the resulting crystals may not be sufficiently strong to be useful for anything practical. In fact, the researchers here appear to have created more of a paste than a true solid.
However, I am wondering if these researchers have stumbled onto an entirely new avenue of research for 3D printing. They developed a “water crystalizer” material for their semiconducting purposes, but perhaps a material using the same process could be developed that might be used in a 3D printer.
The “water 3D printer” might then involve an extruder that mixes the oligomer with a supply of fresh water in just the right proportion to provide for a solidifying extrusion. The nozzle could be moved around a print volume in such a way to create an object, just as many other 3D printing processes do.
I don’t believe this research team has this in mind, but it does demonstrate that we are by no means at the end of development of 3D printing. There are likely many yet-unknown 3D printing process that could be stumbled upon any day.
But somehow water 3D printing is fascinating, as it seems a preposterous concept at first.
The melting point of the crystals would be higher than room temperature, but likely not at the high temperatures of most current 3D print materials. Thus the applications for such a material could be limited. It might be perfectly sound for basic prototypes, however, and usable in educational settings due to the absence of potentially dangerous high temperatures usually found in current technologies.
Another possibility is that objects with a low melting point could be used as one-time solid-state switches. Imagine, say, a nuclear reactor where the heavy water tank can be instantly evacuated if a temperature is exceeded, as the drain would be covered with a water-print that melts away when the target temperature is met.
I would like to see more research in this area, wouldn’t you?
Via Swanson School of Engineering
A 4D Printed Microneedle Array
Researchers have used a micro-3D printing technology to produce an effective long-term drug delivery needle system.
From Fries To 3D Prints: Deep Fryer Oil Transformed Into 3D Printer Resin
Researchers have figured out how to make 3D printer resin from waste cooking oil, and it’s incredibly inexpensive.
Effective 3D Printed Magnets Open Up Many Eco-Possibilities
Researchers seem to have developed a new way to effectively 3D print magnets of similar strength to conventionally made units. What might we do with such a technology?
Kerry Stevenson, aka "General Fabb" has written over 8,000 stories on 3D printing at Fabbaloo since he launched the venture in 2007, with an intention to promote and grow the incredible technology of 3D printing across the world. So far, it seems to be working!
View all of Kerry Stevenson's posts.
Thousands of meters underwater: 3D printing in deep ocean research
URI Deep Sea Robotics Lab Principal Investigator Brennan Phillips.
Despite the international craze for space travel, the true last frontier may be closer to home. Oceans cover more than 70% of our planet's surface, but the National Oceanic and Atmospheric Administration (NOAA) estimates that less than 20% of the oceans are fully explored. Compared to the scale of space exploration, the study of the oceans is underfunded and undervalued. However, some researchers are persevering despite the challenges and are turning to 3D printing as a way to go deeper. nine0005
At the Underwater Robotics and Imaging Lab at the University of Rhode Island's Bay Campus, Professor Brennan Phillips and his students are building instruments that can probe thousands of meters below the surface of the ocean. Using the Formlabs Form 3+ and Form 3L SLA 3D printers, the lab prints waterproof camera cases and a variety of research tools for its work.
Pressurized Waterproof Parts
Ocean mapping requires tools that are not only watertight, but remain watertight even under enormous pressure far below the surface of the ocean. Phillips and lab students began designing a printed camera case that could keep the device completely dry even under pressure while still being easily disassembled for data retrieval. After dozens of iterations, the team settled on a two-piece cylindrical design printed on Form 3+ in Clear Resin. The internal structure of the case holds the circuit board and is filled with epoxy resin that holds the camera lens in the air. Everything under the lens is epoxy, poured through holes built into the body structure. nine0005
"We have been given the task of what is the smallest and cheapest deep sea camera we can make? Now we have printed dozens of these cameras in different shapes, and since this is a printable thing, we can make any shape we want. We can quickly design something then, assemble the electronics, put it in there, optimize the size, and then pour the epoxy," says Phillips.
3D printing allowed the lab to iterate rigorously without worrying about going over budget, and also allowed for more design flexibility than machining. nine0005
The DEEPi camera design uses a hybrid printed mold and an O-ring, an epoxy-filled volume for PCB components, and an external clear glass viewing window.
The laboratory uses a pressure vessel to simulate deep water conditions. Once Phillips and his students settled on a two-piece epoxy design, they placed the pieces in a pressure chamber, increasing the pressure to simulate a true deep sea environment. nine0005
Why SLA 3 D - perfect for deep sea robotics
When evaluating various 3D printers for Phillips Lab, accuracy and material properties were top priorities. The isotropic nature of SLA parts means they are not porous or water-permeable, as FDM printed parts can be. The smooth surface of the SLA parts also ensures that functional assemblies, such as two-piece cylindrical housings, can be connected to each other without a rough surface causing air gaps. Precision and high resolution also contribute to water resistance - incredibly tight tolerances and small part sizes allow screw threads to be printed directly into the material, and in Phillips Lab this is done for both the two-piece body and the screws that serve as additional protection for the mounting. nine0005
Fully printed housing capable of protecting electronics from sea water at depths of more than 1000 meters. The O-rings are printed directly on the parts and the body is sealed by a hand-screwed rim.
“You need 100% SLA detailing - with FDM you might be able to get an IP rating from them, but you won't be able to withstand more than a couple meters of pressure. Secondly, you need permission so that the o-ring between the two parts will ensure a complete seal. These parts come straight out of the printer and we sand them a little, but then orient them so that the critical surfaces are smooth and we get a perfect seal" , says Phillips. "And the third reason is that the properties of SLA materials are much better - there is no comparison at all. They are much better in terms of yield strength. All elastic moduli are better than any other material."
The precision of Formlabs printers and the availability of Formlabs materials have allowed the lab's core work, watertight deep-sea hulls, both onshore and offshore, to flourish. In January 2020, Phillips and his students published their 3D printing process using a stabilization rig on the Form 2. They were able to print the same cases without perceptible differences from their land-based counterparts, which means these devices can be printed and deployed. locally, on ships around the world. Continuing the laboratory's mission to democratize deep sea science, this work provides evidence that these important tools can be made inexpensively and locally. nine0005
Working with Form 3L
When Formlabs announced the Form 3L large format 3D printer, Phillips and the lab were among the first to get to work right away. "We were among the first to purchase Form 3 L " , says Phillips. The Form 3L's large format allowed them to experiment with larger underwater structures and improve other lab functions with innovative research tools. nine0005
To deploy these housings and other monitoring devices underwater, the laboratory must use and maintain thousands of feet of thin fiber optic cable. To avoid tangles or knots, they first used repurposed bicycle wheels to guide the fiber over the side of the boat. However, with a large-format SLA printer on hand, they were able to prototype the design to reduce the size and increase productivity of the process.
A 3D printed "slide" helps guide fiber optic cables smoothly along the side of the boat without tangling or breaking them.
“We didn't want to use a swivel pulley or wheel for line. We needed a slide. So we've printed about three or four iterations of this slide. It's big and nice and smooth, and that smoothness helps with finer lines," says Phillips. The slide printed on Form 3L in Clear Resin reduces the time it takes to store line carefully for reuse and reduces the number of times they need to replace their equipment. nine0005
Innovations in fiber optics
Line, despite the complexity of rewinding, is not the thinnest material. However, fiber optic cables cannot be treated in the same way, as they are much more expensive in the event of a breakdown. Phillips Laboratories partnered with Nautilus Defense LL, based in Pawtucket, Rhode Island, to pioneer the invention of a new type of fiber optic line, or FOFL. “Fiber optics gives us Ethernet, live video and the like. This is very difficult to do with copper cables over long distances”, says Phillips.
But the fiber optic line was not quite usable on its own - it needed a mechanical connection point so that it could be pulled without breaking the fiber optic strand. Since fiber optic cables cannot be knotted or manipulated in the same way as other, stronger fishing lines, the laboratory had to invent a device for the end of the cable.
Printed to the tight tolerances achievable with Formlabs high resolution SLA printers, the load-bearing outer braids of the line can be separated from the fragile strand of fiber. Using injected epoxy, the braided line is glued to a 3D printed fixture, and the fiber optic is routed into a metal branching tube that can connect to a computer to receive the information carried by the fiber optic cable. nine0005
SLA printed parts are used as mechanical terminations for "fiber line" or FOFL), separating the load-bearing outer braid from the fragile fiber optic core.
"This type of mount is very strong, it can hold at least 100 kilos. We have filed for a patent and also published it in the public domain. Without 3D printing, in a normal manufacturing process, they could cost $3,000 or $4,000" , - says Phillips . "It's the combination of rapid prototyping techniques like Formlabs printers and the new fiber optic line that makes it possible to realize new ideas like this" .
3D printed lower cost seals
Prior to 3D printing, these tools were expensive to develop, deterring researchers from making the necessary design changes and preventing underfunded programs from developing them at all. The Underwater Robotics and Imaging Lab is part of the global "deep and cheap" movement, an effort to democratize science and open access to these technologies to better understand the oceans around us. nine0005
"I started 3D printing end caps that had O-rings built into them, and it worked. If you print on a machine, it costs hundreds or even thousands of dollars, and the drawings must be accurate. With these With printers, I can print three or four and get a perfect fit for about $50 per material," says Phillips.
The lab team didn't just print the final parts; using Clear Resin, they have developed a successful workflow for printing forms. The end result is an optimized way to quickly splice submarine cables using printed forms. nine0005
Versatile Uses
At Phillips, Formlabs printers are used for prototyping, end products, quick tooling, workpieces and fixtures, and even medical devices. Even in a small research lab, the innovative spirit of Phillips and his students is constantly expanding the possibilities of using printers.
During COVID-19, Phillips and his students realized they had an opportunity to make a real difference in the fight against the pandemic in Rhode Island. Through extensive testing and exhaustive research, the lab was able to publish the results of the chemical degassing of Formlabs Surgical Guide Resin for use in 3D printed ventilator parts. They accomplished the feat of not only scientific publication, but also applied for FDA approval and emergency use authorization. nine0005
“There has been a huge effort during the pandemic and we wanted to really get involved and help where we could make the most difference. Thanks to the quality of the Formlabs printers and the availability of Surgical Guide Resin, we were able to contribute at a higher level.” says Phillips.
Y-splitter ventilator parts developed in collaboration with researchers at Brown University and Rhode Island Hospital are 3D printed using Surgical Guide resin in the early stages of the COVID-19 pandemic.
Depth democratization
The lower cost of manufacturing these parts not only benefits the lab budget, but also means that learning (and the inevitable stage of failure when trying new ideas) does not deprive students of access to these machines. Senior students designing parts for the first time can access the technology and learn how to 3D print without fear of making any mistakes that cost precious resources.
URI second year students have the opportunity to design and 3D print molding cases each year, contributing to research while gaining valuable new CAD and 3D printing skills. nine0003 "Before the advent of 3D printers, students didn't design or build their own underwater enclosures until they were graduate students or worked in industry and couldn't get trained because cost and access were just limited. But Formlabs printers are opening doors - I had a high school student who made a pressurized case," , says Phillips.
These opportunities are not limited to college students in America - Phillips is part of an international community committed to improving access to deep sea instruments in underdeveloped coastal countries around the world . "We're working to build the capacity of countries that want to do their own research in the deep ocean. Money is a constraint, training is also a constraint, but these methods have the potential to really unlock that opportunity and democratize deep ocean research," says Phillips.
Scientists came up with a way to 3D print objects "from water and air"
November 2, 2017 15:42
A source: Newspaper.ru nine0005
Russian chemists are ahead of global competitors in the development of carbon-neutral 3D printing technologies that do not pollute the environment and use cheap natural materials based on cellulose. Based on the new technology, finished products can actually be printed from water and air. The work was carried out with the support of the Russian Science Foundation (RSF). Her results were presented in the journal Angewandte Chemie .
Scientists come up with a way to 3D print objects "out of water and air"
Valentin Ananikov. Photo: RNF press service
Photo: Valentin Ananikov
Three-dimensional (3D) printing allows you to create finished products of any complexity from computer digital models in a short time. Despite the general backlog of Russia in this area, researchers from the Institute of Organic Chemistry. N.D. Zelinsky RAS managed to get ahead of world competitors in the high-tech field of 3D printing. The authors of the work synthesized a unique PEF material, which makes it possible to carry out three-dimensional printing in an extremely cheap and environmentally friendly way. Its full name is poly(ethylene-2,5-furandicarboxylate). The peculiarity of this material is that it is obtained from a natural substance - cellulose, which belongs to the category of the most promising renewable resources. In nature, cellulose is synthesized from carbon dioxide and water, which are available in the atmosphere in almost unlimited quantities. The energy source for this reaction is sunlight. nine0005
The "recipe" of the new substance is very simple: in the first step, plant biomass (cellulose or fructose) is transformed into 5-(hydroxymethyl)furfural (5-HMF). Chemists know many methods for such a transformation. Further, 5-HMF is oxidized to 2,5-furandicarboxylic acid, which, after reaction with methanol, is converted into the corresponding ester. These reactions do not require complex and time-consuming conditions: all three stages from a practical point of view are not difficult and have already been scaled up to industrial production. Despite its simplicity, 3D printing with PEF has been done for the first time. nine0005
“You can easily go through the full cycle: from carbon dioxide and water, the photosynthetic system of plants produces cellulose, from which a polymer is synthesized in several chemical steps, and then 3D printed. If we consider this full cycle, 3D printing objects are created from carbon dioxide and water, that is, from the cheapest components available in almost unlimited quantities,” said Valentin Ananikov, head of the work.
![]()
The resulting polymer showed high chemical stability, durability, it does not oxidize, is resistant to chemical solvents and does not decompose when exposed to natural environment. Moreover, it can be used repeatedly. Products made from such a polymer will be quite durable, and additive technologies, such as 3D printing, allow you to create an object of almost any complexity. The possible scope of application is very wide and includes all areas where accessible and recyclable materials are in demand. nine0005
“It is important that the resulting material can be repeatedly recovered and reused. At the end of its life cycle, a 3D printed product can be converted into carbon dioxide and water by incineration, and then re-produced into cellulose through the photosynthetic system of plants. The closed carbon-neutral cycle does not pollute the environment, it is based on cheap natural resources and can be carried out an unlimited number of times,” concluded Valentin Ananikov.
![]()
Learn more