3D printing binder
What is Binder Jetting 3D printing?
In this introduction to Binder Jetting 3D printing, we cover the basic principles of the technology. After reading this article you will understand the fundamental mechanics of the Binder Jetting process and how these relate to its benefits and limitations.
How does Binder Jetting work?
Here is how the Binder Jetting process works:
I. First, a recoating blade spreads a thin layer of powder over the build platform.
II. Then, a carriage with inkjet nozzles (which are similar to the nozzles used in desktop 2D printers) passes over the bed, selectively depositing droplets of a binding agent (glue) that bond the powder particles together. In full-color Binder Jetting, the colored ink is also deposited during this step. The size of each drop is approximately 80 μm in diameter, so good resolution can be achieved.
III. When the layer is complete, the build platform moves downwards and the blade re-coats the surface. The process then repeats until the whole part is complete.
IV. After printing, the part is encapsulated in the powder and is left to cure and gain strength. Then the part is removed from the powder bin and the unbound, excess powder is cleaned via pressurized air.
Depending on the material, a post-processing step is usually required. For example, metal Binder Jetting parts need to be sintered (or otherwise heat treated) or infiltrated with a low-melting-temperature metal (typically bronze). Full-color prototypes are also infiltrated with acrylic and coated to improve the vibrancy of colors. Sand casting cores and molds are typically ready to use after 3D printing.
This is because the parts are in a "green" state when they leave the printer. Binder Jetting parts in the green state have poor mechanical properties (they are very brittle) and high porosity.
Schematic of a Binder Jetting 3D printerWhat are the characteristics of Binder Jetting 3D printing?
Printer Parameters
In Binder Jetting, almost all process parameters are preset by the machine manufacturer.
The typical layer height depends on the material: for full color models the typical layer height is 100 microns, for metal parts 50 microns and for sand casting mold materials 200-400 microns.
A key advantage of Binder Jetting over other 3D printing processes is that bonding occurs at room temperature. This means that dimensional distortions connected to thermal effects (such as warping in FDM, SLS, DMSL/SLM or curling in SLA/DLP) are not a problem in Binder Jetting.
As a result, the build volume of Binder Jetting machines are amongst the largest compared to all 3D printing technologies (up to 2200 x 1200 x 600 mm). These large machines are generally used to produce sand casting molds. Metal Binder Jetting systems typically have larger build volumes than DMSL/SLM systems (up to 800 x 500 x 400 mm), which allows the parallel manufacturing of multiple parts at a time. The maximum part size though is restricted to a recommended length of up to 50 mm, due to the post-processing step involved.
Moreover, Binder Jetting requires no support structures: the surrounding powder provides to the part all the necessary support (similar to SLS). This is a key difference between metal Binder Jetting and other metal 3D printing processes, which usually require extensive use of support structures, and allows for the creation of freeform metal structures with very few geometric restrictions. Geometric inaccuracies in metal Binder Jetting come mainly from the post-processing steps, as discussed in a later section.
Since the parts in Binder Jetting do not need to be attached to the build platform, the whole build volume can be utilized. Thus, Binder Jetting is suitable for low-to-medium batch production. To take advantage of the full capabilities of Binder Jetting, it is very important to consider how to fill effectively the whole build volume of the machine (bin packing).
Small metal Binder Jetting with fine holes of great dimensional accuracy.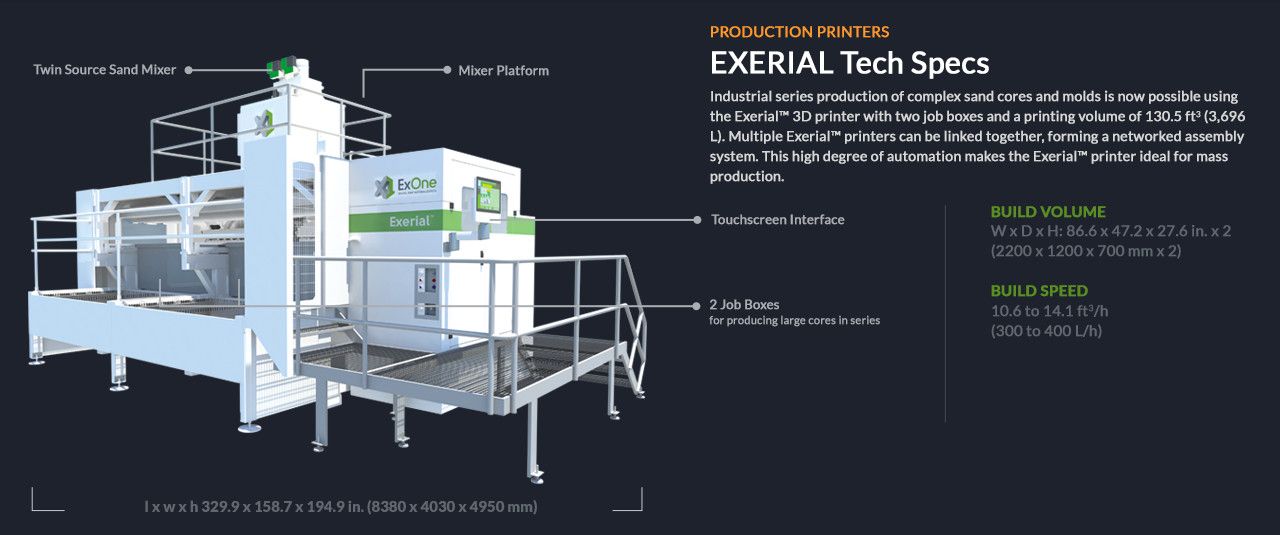
Image courtesy ofDigital Metal
Full Color Binder Jetting
Binder Jetting can produce full color 3D printed parts in a similar way to Material Jetting. It is often used to 3D print figurines and topographical maps, because of its low cost.
Full-color models are printed using sandstone powder or PMMA powder. The main printhead first jets the binding agent, while a secondary print head jets a colored ink. Inks with different colors can be combined to produce a very large array of colors, in a similar way to a 2D inkjet printer.
After printing, the parts are then coated with cyanoacrylate (super glue) or a different infiltrant to improve part strength and enhance the vibrancy of the colors. A secondary epoxy layer can then also be added to further improve strength and color appearance. Even with these extra steps, full-color Binder Jetting parts are very brittle and they are not recommended for functional applications.
To produce full-color prints, a CAD model that contains the color information must be provided. Color can be applied to CAD models via two methods: on a per face approach or as a texture map. Applying color on a per face basis is quick and easy to implement, but using a texture map allows for more controls and greater detail. Refer to your native CAD software for specific instructions.
Sand Casting Cores and Molds
The production of large sand casting patterns is one of the most common uses for Binder Jetting. The low cost and speed of the process make it an excellent solution for elaborate pattern designs that would be very difficult or impossible to produce using traditional techniques.
The cores and molds are generally printed with sand or silica. After printing, the molds are generally immediately ready for casting. The casted metal component is usually removed from them after casting by breaking the mold. Even though these molds are used only once, the time and cost savings compared to traditional manufacturing are substantial.
Image courtesy of ExOne
Metal Binder Jetting
Metal Binder Jetting is up to 10x more economical than other metal 3D printing processes (DMSL/SLM). Moreover, the build size of Binder Jetting is considerably large and the produced parts require no support structures during printing, enabling the creation of complex geometries. This makes metal Binder Jetting a very appealing technology for low-to-medium metal production.
The main drawback of metal Binder Jetting parts are their mechanical properties, which are not suitable for high-end applications. Nevertheless, the material properties of the produced parts are equivalent to metal parts produced with Metal Injection Molding, which is one of the most widely used manufacturing methods for the mass production of metal parts.
Infiltration & Sintering
Metal Binder Jetting parts require a secondary process after printing, like infiltration or sintering, to achieve their good mechanical properties, as the as-printed parts basically consist of metal particles bound together with a polymer adhesive.
Infiltration: After printing, the part is placed in a furnace, where the binder is burnt out leaving voids. At this point, the part is approximately 60% porous. Bronze is then used to infiltrate the voids via capillary action, resulting in parts with low porosity and good strength.
Sintering: After printing is complete, the parts are placed in a high temperature furnace, where the binder is burnt out and the remaining metal particles are sintered (bonded) together, resulting in parts with very low porosity.
An oil and gas stator printed from stainless steel and infiltrated with bronze. Notice the surface finish, which is typical for Binder Jetted parts.Image courtesy of ExOne
Characteristics of metal Binder Jetting
Accuracy and tolerance can vary greatly depending on the model and are hard to predict as they are greatly dependant on the geometry. For example, parts with length up to 25 - 75 mm shrink between 0. 8 to 2% after infiltration, while larger parts have an estimated average shrinkage of 3%. For sintering, the part shrinkage is approximately 20%. The dimensions of the parts are compensated for shrinkage by the machine's software, but non-uniform shrinkage can be an issue and must be accounted for during the design stage in collaboration with the Binder Jetting machine operator.
The post-processing step can also be the source of inaccuracies. For example, during sintering, the part is heated to a high temperature and becomes softer. In this softer state, unsupported areas might deform under their own weight. Moreover, as the part shrinks during sintering, there here is friction between the plate of the furnace and the lower surface of the part, which may lead to warping. Again, communication with the Binder Jetting machine operator is key here to ensure optimal results.
Sintered or infiltrated Binder Jetting metal parts will have an internal porosity (sintering produces 97% dense parts, while infiltration approximately 90%). This affects the mechanical properties of metal Binder Jetting parts, as the voids can lead to crack initiation. Fatigue and fracture strength and elongation at break are the material properties that are most affected by internal porosity. Advanced metallurgical processes (like Hot isostatic pressing or HIP) can be applied to produce parts with almost no internal porosity. For applications where mechanical performance is critical though, DMLS or SLM are the recommended solutions.
An advantage of metal Binder Jetting compared to DMLS/SLM, is the surface roughness of the produced parts. Typically, metal Binder Jetted parts have a surface roughness of Ra 6 μm after post-processing, which can be reduced to Ra 3 μm if a bead-blasting step is employed. In comparison, the as-printed surface roughness of DMLS/SLM parts is approximately Ra 12-16 μm. This is particularly beneficial for parts with internal geometries, for example internal channels, where post-processing is difficult.
The table below summarizes the differences in the main mechanical properties of Stainless Steel parts, printed with Binder Jetting and DMLS/SLM:
Binder Jetting Stainless Steel 316 (sintered) | Binder Jetting Stainless Steel 316 (bronze infiltrated) | DMLS/SLM Stainless Steel 316L | |
---|---|---|---|
Yield Strength | 214 MPa | 283 MPa | 470 MPa |
Elongation at Break | 34% | 14.5% | 40% |
Modulus of Elasticity | 165 GPa | 135 GPa | 180 GPa |
What are the benefits & limitations of Binder Jetting 3D printing?
The key advantages and disadvantages of the technology are summarised below:
Binder Jetting produces metal parts and full-color prototypes at a fraction of the cost compared to DMLS/SLM and Material Jetting respectively.
Binder Jetting can manufacture very large parts and conplex metal geometries, as it is not limited by any thermal effects (e.g. warping).
The manufacturing capabilities of Binder Jetting are excellent for low to medium batch production.
Metal Binder Jetting parts have lower mechanical properties than DMSL/SLM parts, due to their higher porosity.
Only rough details can be printed with Binder Jetting, as the parts are very brittle in their green state and may fracture during post processing.
Compared to other 3D printing process, Binder Jetting offers a limited material selection.
The main characteristics of Binder Jetting are summarized in the table below:
Binder Jetting | |
---|---|
Materials | Metals, Ceramics (sand) |
Dimensional accuracy | Metal: ± 2% or 0.![]() |
Typical build size | Metal: 400 x 250 x 250 mm (up to 800 x 500 x 400 mm) Full-color: 200 x 250 x 200 mm (up to 500 x 380 x 230 mm) Sand: 800 x 500 x 400 (up to 2200 x 1200 x 600 mm) |
Common layer thickness | Metal: 35 - 50 μm Full-color: 100 μm Sand: 200 - 400 μm |
Support | Not required |
Ready to transform your CAD file into a custom part? Upload your designs for a free, instant quote.
Get an instant quoteWhat is Binder Jetting?
What is Binder Jetting?
Binder JettingBinder Jetting — also known as powder-bed and inkjet — is a cost-effective, low-energy method of 3D printing that allows for fabricating parts out of powder media. In this additive manufacturing process, a machine uses the same powder-spreading methods as selective laser sintering (SLS). However, unlike SLS, a liquid binding agent is used to adhere parts instead of a laser. These prints follow a 3D rendering from a CAD file. Once formed, these parts need to either be cured (if they are plastic) or sintered (if they are metal) to yield a useful part.
Binder Jetting is usually cost effective because it’s both low energy and uses affordable materials. It uses less energy as a laser is not required, and produces parts quickly, resulting in a lower operating cost per part. The technology is precise and its production is scalable, making it ideal for high-volume production of small, accurate parts and objects.
Binder Jetting is used in a variety of applications -- including the manufacturing of full-color prototypes, large sand-casting cores and molds on the plastic/ceramic side and small, functional parts on the metal side. Binder Jetting plastics is a well-developed, mature technology; the same process used for metal parts is in an earlier stage of development.
Binder Jetting or binder jet 3D printing technology was developed at the Massachusetts Institute of Technology (MIT) to print complex parts in industrial-grade materials.
As mentioned above, Binder Jetting is faster and more cost-effective than many 3D printing technologies. Binder Jetting machines can print quickly by using multiple heads to jet binding material in several places simultaneously, turning out tens or even hundreds of parts in a single build. However, metal parts produced by Binder Jetting have inferior mechanical properties than DMLS/SLM parts; delicate parts may be brittle and may be damaged during post processing. For now, the choice of materials used in Binder Jetting is narrow.
Does Binder Jetting use heat or lasers in the build process? Binder Jetting is unique in that it does not use heat to cure parts, so avoids the warping and residual stresses that can be caused by heat. Build chambers are often heated, but not to the level that a conventional 3D printer would see.
Does Binder Jetting require a build plate or scaffold? No, because parts are sustained by the loose powder in a job box, which eliminates the need for additional structures and supports.
What materials can be used in Binder Jetting? Metals, sand (for ceramics), silica, and polymers.
Is Binder Jetting suitable for creating metal parts with tight tolerances? Yes, depending on materials used and method of binding.
Is Binder Jetting faster than other 3D printing techniques? Yes and no. Binder Jetting a single part may be slow due to post processing times, but for batch production it is very fast. Post-process steps like sintering or those taken to improve the surface, add color, or coat parts will take additional time.
Binder Jetting 3d printing technology
In this article we will talk about the additive Binder Jetting technology - layer-by-layer bonding of powder materials with a binder. We will look at what this technology is and how printing is carried out in devices based on Binder Jetting. We will also highlight the advantages of this method of manufacturing 3D products and tell you what opportunities it provides and in what areas it is used.
Contents:
Binder Jetting - the essence of the technology and the principle of operation
Binder Jetting (BJ) is a 3D printing method where powder materials are used as consumables, connected with a special binder. Various types of powders can be used for printing, such as ceramic, polymer or metal.
Binder Jetting was developed by the MIT Institute of Technology. She appeared at 1993, after which it was acquired by Z Corporation, and then the rights to it were transferred to 3D Systems. This printing method has become widespread in industrial areas - in design and production.
Binder can be translated as "binder", and jetting - "injection". The name of the technology reflects the essence of this printing method - applying an adhesive, similar to how ink is transferred to paper in an inkjet printer.
Printing is carried out in several stages - first, a part of the powder material enters the working chamber, it is leveled with a roller until a homogeneous thin layer is obtained, after which a printing unit passes over it, applying a binder by the jet method. After that, a new portion of the powder material is applied over the finished layer, and all steps are repeated until the finished part is obtained. nine0003
This technology works with different types of consumables - gypsum and metal powders, sand, as well as ceramic and polymer raw materials.
One of the distinguishing features of the technology is the possibility of obtaining full-color models, for which you only need to add a dye to the binder. In this case, the pigment can be applied not only on top of the product, but also to any required depth, which allows you to get a well-dyed model with a color that is resistant to external influences. nine0003
Binder Jetting products require additional processing, which varies depending on the type of raw material.
Working with metal powders
Metal additive printing in the Binder Jetting method uses raw materials in the form of metal powders of various types and compositions, as well as a binder polymer component. This method makes it possible to obtain metal models that cannot be made using traditional methods. Through 3D printing, complex internal elements of a part of any shape and configuration are produced. When printing, different types of metals and non-metals are used, for example, stainless steel, copper, composite, titanium powders, inconel, tungsten carbide, ceramics. nine0003
After manufacturing, the part is sent for post-processing, where it is given the required strength characteristics. The model is placed in an oven and kept at a certain temperature. Thus, by burning out the binding component and/or sintering the model, a product is obtained whose properties are not inferior to conventional all-metal parts.
Sintered at 97% of the melting point of the material used to make the part. In this case, the products undergo shrinkage, but this is taken into account in advance when designing the model. nine0003
Sometimes post-processing is limited to only burning out the binder, without sintering. In this case, the product retains its original dimensions, but its density decreases. The resulting voids are subsequently filled with bronze. Binder Jetting Technology the possibility of manufacturing full-color models using the BJ method. nine0003
When producing color products, the printer uses two printheads: one applies the binder, and the other is used to add ink.
Post-sintering in the same way as described above helps to improve the mechanical strength of the part.
3D Binder Jetting can be made using a variety of raw materials, including natural sand and artificial silica.
Sand casting molds produced by BJ technology are highly accurate, in addition, this method can significantly save time for their manufacture and reduce the cost of parts. nine0003
BJ Media Types
Different types of powders can be used in printing, while the variety of raw materials gradually increases, new types of consumables are developed over time. However, the following types of powder raw materials are most commonly used in BJ 3D printing.
Stainless steel
It has already been mentioned above that metal products shrink during baking, their original dimensions change. However, if these model changes are taken into account at the design stage, stainless steel products obtained by this method can be used in any area, in no way inferior to those made by conventional casting or using other traditional manufacturing technologies. Finished parts have high strength and excellent mechanical characteristics, while being resistant to corrosion. nine0003
Non-sintered products, in which the binder is burned out and the cavities filled with bronze, also have high strength. But this figure is slightly less than that of sintered ones, due to partially preserved porosity, which can reach 10%. These products can also be used in a variety of areas, including in solving production problems. The advantage of the burn-in method is to obtain parts with more predictable and accurate dimensions.
Silica
Silicon dioxide, or silica, is used in the manufacture of 3D models that have increased resistance to high temperatures. This type of powder raw material is excellent for printing sand molds, where silica 3D printing can produce particularly effective results.
Making full-color plaster and sandstone models
Although products made from these materials do not withstand strong mechanical stress and are rather fragile, they are widely used for demonstration purposes, as well as in the manufacture of decorative elements. Using such models as an example, you can clearly demonstrate the possibilities of full-color 3D printing, as well as use them as visual material in training. Gypsum and sandstone make interesting decorative items, decorative elements, as well as copies of works of art or museum exhibits. nine0003
Inconel
3D printing with Inconel, which belongs to the family of heat-resistant alloys, with the subsequent baking of products, allows to obtain high-strength parts with excellent mechanical characteristics, resistant to high temperatures and aggressive (chemical) environments.
Tungsten Carbide
Tungsten carbide products obtained by the Binder Jetting process, after baking, have a high hardness, which makes it possible to produce cutting tool bits with this method. nine0003
Like any other 3D printing technology, the Binder Jetting method also has its advantages and disadvantages. Consider the main pros and cons of this method in order to get a more objective idea of the capabilities of the technology.
BJ Benefits:
- Cheaper than other metal additive printing methods such as SLM, DMLS or Material Jetting.
- Allows you to get full color products.
- Works great on parts with complex shapes and inner sides. nine0098
- Products do not deform when printed.
- Differs in high productivity in the manufacture of small and medium batches of products.
BJ Disadvantages:
- Models have higher porosity than DMLS or SLM parts, resulting in lower strength.
- Prior to the heat treatment stage, parts are more brittle.
- If the part is to be baked, the difference in size due to shrinkage must be taken into account during the design phase. nine0098
- Limited range of available materials - compared to other 3D printing methods, there are still not many.
3D printers based on Binder Jetting
Let's look at some 3D printers based on Binder Jetting technology.
Robotech R-2000
This is a large industrial grade 3D printer designed for the needs of large manufacturing plants in the steel industry. Development of the Russian company "Robotech". Produces products at a speed of 6 to 20 mm/hour with a minimum layer thickness of 200 microns. A distinctive feature of the device is a large working area of 2000 x 1000 x 1000 mm, which allows the production of large molds for casting large products. Allows you to print 3D products of complex configurations. It is possible to customize for a specific order, including limiting the print area and reconfiguring the software. nine0003
Advantages:
- the production process is environmentally friendly and safe;
- reliability of the 3D printing machine;
- automated model making process;
- the ability to remotely control the device;
- sand without binder remaining after model making can be reused;
- the ability to partially use the work area;
- support for integration with ERP systems.
Disadvantages:
- if the part is planned to be baked in the future, it is necessary to include the percentage of shrinkage in the dimensions of the model at the design stage.
Robotech R-600
Another development of Robotech, a small industrial printer, well suited for small steel companies, universities, research centers, design bureaus. The printing area dimensions are 600 x 480 x 250 mm and allow the production of molds of small and medium sizes. The minimum height of the printed layer is 200 microns. The printing speed is from 6 to 20 mm/h, the production of the form takes, on average, no more than a day. nine0003
Advantages:
- Possibility of making complex 3D models;
- high precision fast printing;
- the ability to reconfigure equipment and software for a specific order;
- allows you to partially use the construction area;
- the possibility of reusing the sand left after the manufacture of the model;
- integration with ERP systems.
Disadvantages:
- Porosity and less strength of the model compared to other 3D printing methods.
nine0098
ExOne X1 160Pro
Binder Jetting 3D printer with large volume print chamber. The patented ExOne Triple ACT system controls dosing, distribution and compaction of powder materials, which provides the best density and repeatability of products in similar devices. The device allows you to make models with dimensions up to 800 x 500 x 400 mm thanks to a working chamber of 160 liters.
Advantages:
- high precision and repeatability of products;
- large working chamber;
- high speed;
- the ability to remotely manage the printer.
Disadvantages:
- lower product density than other printing methods.
Summary
Binder Jetting is one of the most accurate and cost-effective 3D printing technologies on the market today. Its use is especially effective in the metallurgical industry and in the printing of sand casting molds. The use of devices based on this technology will allow enterprises to significantly improve the efficiency of production processes and increase their competitiveness. nine0003
- November 04, 2022
- 205
Get expert advice
Copper 3D printing - complete guide
Copper is one of the newest and most promising areas of metal 3D printing for everything from electric motors to heat sinks.
Previously, copper 3D printing was a challenge due to the metal's reflectivity and high thermal conductivity, but advances in printers and materials have largely resolved these early problems. Today, 3D printed copper propulsion systems send rockets into space, 3D printed copper heatsinks cool processors, and 3D printed copper coils boost the performance of electric motors. nine0003
3D printed copper parts (Source: Trumpf)
Why 3D print copper?
Copper has always been a very useful metal due to its ability to conduct heat and electricity, resist corrosion and even kill bacteria and viruses. Demand for complex copper parts is on the rise as 3D printing opens up even more uses and possibilities for this metal.
3D printing (also known as additive manufacturing) allows the creation of exceptionally complex shapes, fine details, internal structures and lattice inserts that are not possible with any other form of metal fabrication. These capabilities reduce weight, increase efficiency, and reduce fabrication and assembly times, as multi-component assemblies can be 3D printed as a single unit. nine0003
Additive metallurgy
3D printing also allows this relatively expensive metal to be produced more efficiently, reducing waste by using only the amount of material needed to make each part. For companies interested in copper 3D printing, reducing raw material costs is critical.
If you already produce custom copper parts, 3D printing can significantly reduce your production costs while optimizing part performance. nine0003
Markforged 3D printed copper heatsink (Source: Markforged)
Although there aren't many 3D printers that can print copper, there is still a wide variety of printing technologies and prices.
FDM printers using copper-filled plastic filament can produce copper jewelry, decorative items, and other parts that are almost 100% copper. While for more advanced production, 3D printers using copper powder, rods or copper polymer slurry produce industrial parts with excellent mechanical and conductive properties, which can meet international standards such as IACS (International Annealed Copper Standard). nine0003
Let's look at what types of printers can work with copper today.
Trumpf's TruPrint 1000 Green Edition 3D printer
several equipment manufacturers have recently included copper in their material list. Since copper is highly reflective, laser processing of the powder has been a hurdle for manufacturers. However, this technology and materials have evolved to solve this problem. nine0003
3D printer manufacturer Trumpf, for example, has developed an industrial green laser that can 3D print materials such as copper, copper alloys, and precious metals that are difficult to process with infrared waves.
Two powder layer technologies for metal 3D printing, DMLS (Direct Metal Laser Sintering) and EBM (Electron Beam Melting), work by depositing a thin layer of copper powder onto a platform inside the printer. The powder heats up while lasers or electron beams draw the first layer of the part. When the particles in the layer fuse, the platform is lowered slightly into the assembly chamber, and fresh powder is poured on top, and the process is repeated. Some of the copper powder left over from the process can be recycled for use in the next print. nine0003
Copper additive manufacturing powder from GNK Powder Metallurgy (Source: GNK)
Copper-bonded 3D inkjet printers
Copper powder bonded with a liquid binder and sintered in a furnace is a 3D printing technique known as binder inkjet printing that allows parts to be obtained without the use of an auxiliary material. Bond jetting is a no-heat process in which a bonding layer is sprayed between each layer of metal; the binder is then removed during the sintering process. nine0003
Binder blasting is a popular additive manufacturing method for high volume metal parts.
Featured image of
Copper Parts Printed by Markforged0 Metal X Printed Copper Parts
The most economical approach to 3D printing copper parts is to use machines that extrude the filament. Metal filament for printing metal parts consists of a plastic base with metal particles evenly interspersed in it. Copper interspersed filament for copper parts is a unique type of composite filament that, when used correctly, produces strong, chemically resistant, and near-solid metal parts. nine0003
Virtually any Fused Deposition Modeling (FDM) printer can print near-solid metal parts using a polymer filament filled with copper powder. Currently, there is only one option on the market - from the manufacturer of threads The Virtual Foundry. The company claims that its copper filament is suitable for printing on any filament 3D printer with a hardened nozzle and a hot end that can reach temperatures of up to 225ºC. However, the parts do not become metal immediately after printing and require additional post-printing steps to melt the resin binder and leave only the metal. nine0003
Other types of copper thread contain enough real copper particles to be polished and given a metal-like weight, but are for decorative purposes.
A company in Chile called Copper3D produces a copper-filled filament that produces parts that do not have metal parts, but parts that have the antibacterial and antimicrobial properties of copper. NASA is even testing the filament for use in "interplanetary microbial contamination," according to the company. nine0003
In addition to the mainstream FDM printers, two other filament-extruding printers also offer copper, but they use their own proprietary materials. Desktop Metal uses a bonded metal filament, while Markforged uses a similar metal powder bonded into a plastic matrix. The printers from these manufacturers produce all-metal parts designed for industrial use, such as machine tools, induction coils, heat sinks, and functional prototypes. nine0003
Copper Cold Spray and DED 3D Printers
WarpSpee3D Cold Spray 3D Printer (Source: Spee3D)
Although these two methods of metal 3D printing are not usually combined together here due to their general application for coating metal parts with another metal and for layering metal parts with metal powder.
Directed Energy Deposition (DED) is a system developed by Optomec of New Mexico to create, improve and repair metal parts. Like SLS, in DED, high-power lasers build up 3D structures in layers, creating parts with high density and strength, ideal for mechanical applications. In 2019Optomec developed a new copper DED process to produce heat exchangers for use in the aerospace, chemical and other industries.
Spee3D's WarpSpee3D process is unique in its use of supersonic 3D deposition to produce parts from a range of metal powder materials, including copper and aluminum.
Cold spray is an additive manufacturing technique in which metal powder is injected into a supersonic pressurized gas stream. Instead of melting the metal, cold spraying holds it together in a process called plastic deformation. Companies such as Spee3D are using cold spray technology to apply an antimicrobial copper coating to doors, handrails and touch panels intended for use in hospitals, schools and other public places. nine0003
Cold spray is also the fastest metal 3D printing method. Spee3D printed a 17.9kg (17.9kg) pure copper aerospace rocket nozzle lining (pictured below) on WarpSpee3D in about three hours at a cost of just $716, according to the company. Parts like this are usually made from solid forged copper, which takes weeks and costs tens of thousands of dollars.
One of the disadvantages of DED and cold spray is that they are limited in the production of complex geometries. nine0003
Rocket nozzle copper plating, engineer spark-free copper hammer and copper cable clamp, 3D printed by Spee3D (Source: Spee3D)
Photopolymerization Holo)
Metal DLP 3D printing is similar to resin 3D printing in that it uses UV light projected onto a photosensitive slurry to cure layer by layer.