3D printing study
Using 3D Printing to Meet Customer Demands
At Formlabs, we constantly hear about amazing 3D printing applications. Our customers are continually pushing the envelope of what’s possible with additive manufacturing, inspiring us to improve our materials and 3D printers. And while we know that for every industry, there are different applications and reasons to invest, we were curious to hear why businesses are investing in 3D printing, many for the first time in 2022.
That’s why Formlabs created our first ever state of the industry report, called “The 2022 3D Printing Applications Report”. Filled with key insights on what is driving current and future investment in additive manufacturing, this report is based on survey data from 400 businesses in a multitude of industries around the world.
In our previous blog post, we covered one of the central findings of the report: the rapid rise of end-use part creation as a use-case of 3D printing. In this post, we will look at what has been driving recent investments in 3D printing.
As businesses re-evaluate their sustainability initiatives and analyze the impact their products are having on the environment, a growing number of them are viewing in-house 3D printing as a major solution to address sustainability concerns. 70% of recent adopters (those who invested in the technology in the past two years) cite sustainability as a significant or very significant benefit of 3D printing, which is more than double that of early adopters of 3D printing.
While SLA 3D printing does produce waste, such as post-processing water mixed with IPA, it can often be used to eliminate the shipping of parts from outsourcing firms. Additionally, traditional manufacturing processes such as injection molding create waste, which is completely eliminated when using in-house 3D printing processes such as SLS. Oftentimes, in order to reduce the amortized cost of an injection molding order, firms will purchase in large quantities, with some parts going unused and later thrown out. With in-house production, supply can be created to perfectly match demand, reducing excess waste.
Finally, Formlabs strengthened its own supply chain by purchasing resin maker Spectra, making sure we had control over resin production for Formlabs prints. This further strengthens our customers' supply chains, removing the need for businesses to rely on third party suppliers and knowing exactly when and for how long different materials will be supported.
There are many reasons why businesses across a range of industries invest in 3D printing for end-use part production. When examining the top three reasons given in the 2022 3D Printing Applications Report, we see a common theme: innovate quickly, meet customer demand, and speed to market. These three are inextricably linked; innovating products quickly and getting them to market before competitors is incredibly important for every business, allowing brands to establish themselves as market leaders. But shipping a bad product quickly is counterproductive, which is why using 3D printing as a tool to meet customer demand is critical. The report highlights how 3D printing is increasingly being deployed across modern workflows, from rapid prototyping, to the creation of rapid tooling, to the use of end-use parts to create better products for customers faster than ever before.
3D printing is unleashing new possibilities and business opportunities. What used to be too complex, prohibitively expensive, or impractical to produce with traditional methods is now available in-house at a fraction of the cost, giving full control to designers and manufacturers, and opening the door for fully customizable products to become a reality. The increased adoption of end-use parts as a major application of 3D printing doesn’t replace, but supplements, other use cases such as rapid prototyping. While 3D printing will never fully replace traditional manufacturing methods, it has become an integral part of the engineering toolbox.
The 2022 3D Printing Applications Report is packed full of information on the current state of the 3D printing industry. It covers changes in perceived benefits (such as addressing supply chain shocks) of 3D printing, to adoption of new applications, and more.
The entire report is available below, free to download. Let us know what you think of the report on LinkedIn.
Download the Report
3D Printing Research at EPA
Studies have found that the 3D printing process releases gases and particulates which could pose health risks to users. These emissions include volatile organic compounds, referred to as VOCs, some of which are hazardous to human health when inhaled. In addition to VOC emissions 3D printers can release particles of ultrafine size (1–100 nm), and researchers have found that they are small enough to be deposited deeper into the respiratory system. These particles can be more difficult to clear from the body than larger solid particulates.
What material do these emissions come from?
Common 3D printer ‘ink’, called filament, is a thermoplastic that is partially melted during the printing process to form the desired 3D object, one layer at a time. There are different types of filaments to choose from, with the most popular material choices being poly-lactic acid (PLA) and acrylonitrile butadiene styrene (ABS). PLA filament is derived from renewable sources like corn and is advertised for its abilities to biodegrade and reduce greenhouse gases during use. ABS is derived from processing petroleum and is often used in industry because of its chemical resistance.
EPA researchers have conducted studies to examine the emissions of these filament types, finding that the different filaments release different amounts of respirable particles during the printing process. Learn more:
Particle emissions from fused deposition modeling 3D printers: Evaluation and meta-analysis.
Recent 3D Printer Emissions Research at EPA.
Filament Extruders
Instead of using pre-made filament, users can use filament ‘extruders’, which create feedstock for 3D printers from raw plastic pellets. EPA researchers studied these extruders to build their understanding of any additional emissions that would result from extruder use. Through their research, they found that ultrafine particle emission rates from extruders were comparable to those found in other 3D printer studies, concluding that filament extruders may present additional exposure to these particles for users. There is also an expanding market for a range of specialty filaments with additives such as metal particles, metal–containing flame retardants and others. These additives may pose additional health risks.
Learn more:
Particle and volatile organic compound emissions from a 3D printer filament extruder.
Human exposure to metals in consumer-focused fused filament fabrication (FFF)/ 3D printing processes
Children’s exposure to 3D printing emissions
The availability of published studies evaluating the effects of 3D printer emissions on respiratory health is limited, and all have focused solely on adults. However, 3D printing has become a popular educational tool, meaning children and teenagers could be regularly exposed to 3D printer emissions. This is of concern because children may be a vulnerable population, meaning that the effects of these emissions could disproportionately harm them. Children may be exposed to high concentrations of 3D printer ultrafine particles due to uncontrolled use of the printers within confined spaces, such as classrooms and libraries.
EPA researchers used an open access model called multiple path particle dosimetry model (MPPD v3.04) to predict the amount of particles that may be deposited from 3D printer emissions in different regions of the respiratory tract. Specifically, these models focused on children of various age groups from three months to eighteen years old. From this modeling, the researchers found that the greatest predicted mass deposition was highest in the range of nine to eighteen-year-olds, and that the greatest mass deposition was predicted to occur in the lungs. Learn more:
3D printer particle emissions: Translation to internal dose in adults and children.
The National Institute for Occupational Safety and Health recommends that 3D printer users protect themselves by using materials with lower emissions, using enclosures for 3D printers and ventilation to capture chemical emissions, and reducing time spent near the printer while it is running. Additional resources about 3D Printing safety:
3D Printing with Filaments: Health and Safety Questions to Ask
Characterizing 3D Printing Emissions and Controls in an Office Environment
Contact Us to ask a question, provide feedback, or report a problem.
Last updated on June 1, 2022
3D Printing Market Research: 6 Important Trends
Time is the most valuable commodity today. High competition and the emergence of new business models require accelerated development cycles to quickly and flexibly implement innovative ideas. With new, more efficient equipment, high productivity, and a wide choice of materials, 3D printing technology saves time and money in the development and production of parts.
3D printing was originally designed to completely change the principles of production. The technology has a number of strategic advantages, such as design flexibility, reduced time to market, mass customization, distributed manufacturing, and many others. Despite some difficulties, 3D printing continues to show undeniable advantages.
Over the past few years, Jabil, a global manufacturing services company, has sponsored three 3D printing trend studies to help guide additive manufacturing and assess current realities. The 2021 survey surveyed more than 300 people responsible for making 3D printing decisions in manufacturing companies. The report allows you to get acquainted with the experience and opinion of professionals working "at the forefront". Respondents work in a wide range of industries, including electronics, plastics and packaging, industrial engineering, automotive, healthcare, and many others, giving us a comprehensive understanding of the 3D printing market and how additive technologies are being used.
1. The scope of 3D printing is rapidly expanding
Thirty years is a very short time when it comes to traditional production methods. Additive technologies are revolutionizing a wide variety of industries.
The results of the last two surveys contrast sharply with the information that was obtained during the first survey in 2017. Even in the past two years, the adoption of 3D printing has increased significantly. The rise in popularity and expansion of the scope of additive manufacturing is clearly seen in the present study.
In 2017, the most popular answer to the question “what is 3D printing used for in your company?” was the answer "for rapid prototyping". Seven out of ten respondents confirmed the use of 3D printing for this purpose. The remaining answer options lag far behind the first: only three out of ten respondents chose the second option (tooling production). Since then, the scope of 3D printing has expanded significantly.
R&D has become the most popular area for 3D printing, ahead of prototyping. At the same time, there is a sharp increase in application scenarios in other areas. Since 2017, the proportion of companies using additive manufacturing to manufacture parts and tooling has doubled, and the use of these methods for mass production of parts has tripled.
Nearly 100% of study participants reported that they use 3D printing to produce functional or final parts. Undoubtedly, the scale of their production varies. Nearly 80% of respondents report using additive manufacturing to make at least 25-50% of functional parts.
Improvements in 3D printers allow companies to experiment with additive technologies in areas where they were previously unavailable. As the price of 3D printers declines and their productivity rises, the technology will become more accessible and will change the manufacturing industry as a whole.
2. The growth of additive manufacturing: forecasts are more optimistic than ever
The prospects for the development of 3D printing are extremely positive. Market participants are confident in a significant increase in the popularity of technology in the future. 97% of respondents believe that the adoption of 3D printing in their companies will grow in the next five years.
Most of the study participants believe that the use of 3D printers in their organizations will at least double over this period of time. Nearly half of respondents expect usage to double, and 4 out of 10 expect much more significant increases (5x or more). In addition to the growing popularity of additive technologies, a significant role in expanding their use, as already mentioned, will be played by their availability.
Companies in general plan to increase their additive capacity, but the highest expectations are in mass production of parts and goods. Slightly more than 80% of respondents expect that the use of additive technologies for mass production of products in their organizations will grow at least twice over the next five years.
H. 3D printing brings many benefits to companies
During the first study, many of the benefits were perceived as "intangible" concepts. However, over the past few years, use cases have increased, concepts have become reality, and two years later, respondents are even more inspired by the benefits of additive technologies. We have identified three main benefits of additive manufacturing according to reviews.
Perhaps the rise in popularity of 3D printing is not a coincidence, but is due to increased demand for additive manufacturing during the COVID-19 crisis. As the pandemic spread, companies with 3D printers began to produce personal protective equipment such as respirators and masks that suddenly became scarce. When developing new diagnostic equipment and analysis kits, the use of 3D printing has accelerated the process of prototyping and design.
Respondents chose faster manufacturing of parts as the main benefit of additive manufacturing. Jabil saw this first hand: indeed, the desire to eliminate the labor-intensive iterative process was the driving force behind the introduction of additive manufacturing into the Auburn Hills facility. Not only did it speed up workflows, but it also helped reduce costs by being able to immediately recreate the exact geometry (no need to cut off excess material). In fact, savings amounted to 30-40% on tooling and 80% on lead times.
“With the power of 3D printing, every aspect of manufacturing has been greatly improved,” said John Wahl VI, Tooling Engineer at Jabil's Auburn Hills facility. “The first aspect is time, the second is a more creative approach, the third is costs, the fourth is materials.”
According to the distribution by job level, senior managers are more optimistic about the benefits of 3D printing than department heads. Since it is the leaders who shape the vision (and plan the budget) for the future of the company, everything points to the further spread of 3D printing.
4. 3D printing materials become more affordable
Compared to 2019, companies are using many more types of 3D printing materials. Despite the fact that plastics/polymers are still leading the way, other materials are not losing ground and are catching up. This confirms our conclusion that the scope of 3D printing is expanding.
When it comes to primary material, the difference between plastic and metal in 3D printing is not as big as you might think. More than a third of respondents answered that they use plastic and metal equally, and those who choose only plastics are only 10% more.
Certainly some problems must be overcome in order to use some materials. More than half of the respondents (twice as many as in 2019) said that it takes too long to develop the necessary materials. Slightly more survey participants said that some materials are too expensive for large-scale use, and are not available or certified.
However, as these problems are overcome, interest in different materials increases. When you look at what materials companies actually use and what they would like to use, plastic still comes out on top. At the same time, the desire to use almost all materials exceeds the current use. It is noteworthy that the interest in printing with glass exceeds the actual use by 20%, ceramics - by 14%, metal - by 10%. It will be interesting to see the changes in the use of materials in the next two years.
5.
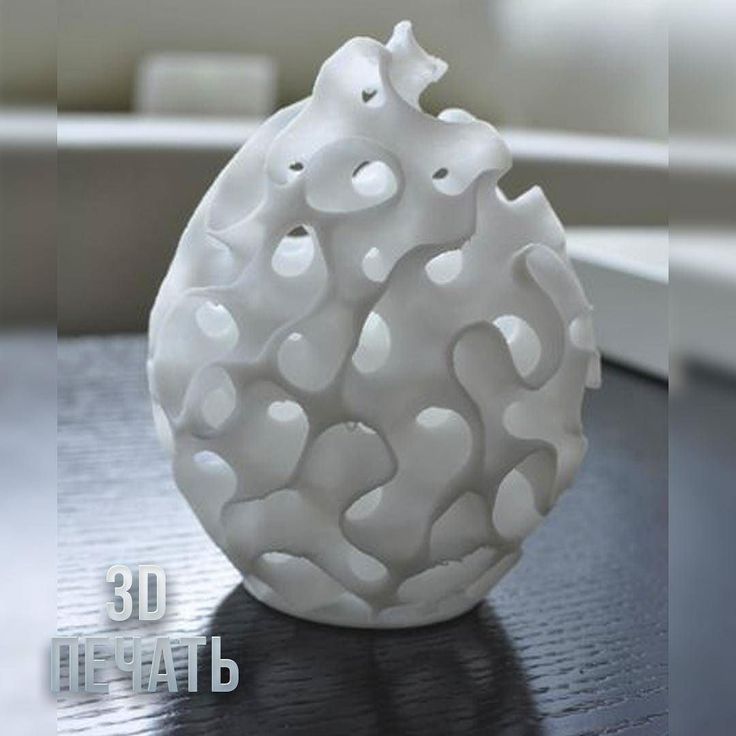
Despite the optimistic view of the development of additive manufacturing, companies still have to solve a number of problems associated with 3D printing. In 2019, half of respondents cited material costs as a problem, but this year only about two-fifths did so. All problems are located approximately on the same level: most of them fluctuate around 40%.
However, many of the current problems are related to costs, since 95% of respondents reported financial barriers to adopting additive manufacturing. Obtaining appropriate qualifications and certifications is the main challenge, followed by capital expenditures associated with equipment and the need for in-house specialists.
In 2021, pre- and post-processing costs have become a major concern. Companies are using more and more pre- and post-processing techniques. In 2019, just over half of respondents reported using mechanical finishing, now it is almost three-quarters, with no polishing being the most common option. Given that the use of all processing methods has increased significantly, it is possible that companies are experiencing growth difficulties. If these problems continue to be given priority attention, they can be overcome.
6. Training of specialists is a priority
Now about three-quarters of the respondents are engaged in additive manufacturing on their own. Given that half of the time they chose “lack of in-house talent” as their problem, it can be assumed that companies are prioritizing educating their employees about additive manufacturing or attracting professionals with experience and knowledge in the field of 3D printing.
This does not mean that organizations are opposed to outsourcing additive manufacturing: in fact, almost 100% of respondents said they were considering this option. When looking at potential suppliers, companies take into account a variety of criteria. Design capability is key, and scalability, pricing, and experience continue the list.
We are seeing significant growth in 3D printing in some areas. In others, this growth is still small. Four years ago, companies used 3D printers primarily for fast, low-cost prototyping: Few businesses relied on additive manufacturing for full-scale production. However, in just four years, as the problems with materials for additive manufacturing were solved and the scope of its use increased, the situation has changed. We have seen how 3D printing has literally taken over many manufacturing industries, which is reflected in the growth of market performance. Slowly but surely, the adoption of additive manufacturing continues. Digital manufacturing is the future.
Source
Tags:
business model, 3d printing, Jabil, 3d printing trends, automotive, prototyping, R&D, additive manufacturing, 3D printer, additive technologies, plastic, polymer, 3D printing materials
Strength research characteristics of the model material obtained by FDM printing
Relevance of the work and research objectives
Additive technologies are currently one of the most dynamically developing areas of digital production, which has great prospects in the production of engineering products and repair work. Additive technologies are based on the use of 3D printers. Of the seven basic principles of the 3D printing process, the most common today is the extrusion of material, which is selectively fed through a nozzle or jet. This type of 3D printing is commonly referred to in the technical literature as FDM printing (Fused Deposition Modeling).
The widespread use of FDM printing is explained by the relative cheapness of 3D printers for this technology and the possibilities in the production of various types of products. However, it cannot be argued that the strength characteristics of the material of parts obtained using FDM printing correspond to the strength properties of the material of the threads that are used in this case. The application of alternating layers by sequential deposition of filaments leads to the formation of a multilevel physical structure of the material. The formed structure may differ in the anisotropy of properties relative to the direction of laying the threads, the difference in the thicknesses of the stacked layers, the presence of various types of defects, and the peculiarity of the mechanisms of material destruction. The factors listed above affect the strength characteristics of the resulting materials.
The most common materials for FDM printing are plastics, such as the commonly used ABS plastic. Therefore, the purpose of this work is to study the strength characteristics of the material obtained by FDM printing using ABS plastic.
Description of the technique and conditions for manufacturing samples
The material obtained by FDM printing may have a different structure, but it will necessarily consist of a set of volumes with unidirectionally laid threads. This is determined by the technological features of the implementation of FDM printing. In order to assess the strength characteristics of the material and the anisotropy of the properties, tests must be carried out along and across the direction of laying the threads.
The shape and dimensions of specimens for tensile tests were taken in accordance with GOST 11262–80 “Plastics. Tensile test method. A sample of the second type was chosen for research (Fig. 1). 3D printing was carried out using ABS+ plastic monofilament manufactured by StrimPlast, supplied according to TU 2291-001-24687042-2016. In accordance with these specifications, the monofilament must have a tensile strength of at least 47 MPa and printing must be carried out in the temperature range of 220–250 ° N.
1. Sketch of a sample for tensile testing
3D printing allows you to immediately produce samples for testing tensile strength, bypassing the stages of obtaining a primary blank and then cutting samples from it. The thread laying order (G-code) was prepared in the Simplify3D program version 4.0 according to GOST 20999–83 “Numerical control devices for metalworking equipment. Coding information of control programs, taking into account the location of the threads in the working part of the sample along or across the direction of stretching. FDM printing was carried out on a Picaso Designer Pro250 3D printer with an extruder nozzle diameter of 0.3 mm.
Before printing, to improve the adhesion of the material, the table was covered with a special The3D binder. The table temperature was 110 ° C and the extruder nozzle temperature was 240°C. Printing was carried out in three modes:
- Mode 1: speed of movement of the extruder nozzle V c = 30 mm/sec, the thickness of the stacked layer of thread h sl = 100 µm;
- Mode 2: extruder nozzle speed V s = 45 mm/s, filament layer thickness h sl = 150 µm;
- Mode 3: speed of movement of the extruder nozzle V c = 60 mm/sec, the thickness of the laid layer of thread h sl = 200 µm.
The obtained specimens were tested for tension at the rate of extension of the clamps of the testing machine corresponding to 1±0.5 mm/sec (the minimum rate of extension of the clamps of the testing machine, provided by GOST 11262–80).
Discussion of the obtained experimental data
Experimental data on the results of testing the material obtained by FDM printing using ABS along and across the filament laying are shown in fig. 2. It can be seen from them that the tensile strength of the material obtained by all three 3D printing modes in the direction of filament laying is close in its values and is at the level of 31–33.5 MPa. If we use the manufacturer's data on the strength of the monofilament used in FDM printing (47 MPa), then these values are approximately 31% lower. However, in order to conduct a more correct comparison of the strength levels of these two materials, it is necessary to clarify to what extent the conditions for testing monofilaments coincide with the conditions for their loading in the model material.
Fig. Fig. 2. Dependence of the tensile strength σr of the model material with longitudinal and transverse filaments, obtained in different modes of 3D printing (Mode 1: V s = 30 mm/sec, h sl = 100 µm; Mode 2: V s = 45 mm/s, h sl = 150 µm Mode 3: V s = 60 mm/s, h sl = 200 µm)
depends on FDM printing modes (Fig. 2). The speed of movement of the extruder nozzle in combination with the thickness of the laid layer affect the adhesion strength of the threads. This is due to the spread of heat from the nozzle into the material. At high print speeds, less heat is transferred to the plastic at any given point in time than at low speeds. If you print a small layer at a low speed, then too much heat may be given off. This will increase adhesion, but there will be a possibility of defects in the form of plastic sagging. Conversely, if you are 3D printing with a thicker layer at high speed, there may not be enough heat to form good adhesion between the filaments.
This assumption is confirmed by the obtained experimental data (Fig. 2). In mode 1 (minimum printing speed and thickness of the stacked layer), the strength of the model material across the laying of the threads is maximum and amounts to 20.2 MPa (67% of the strength of the material along the laying of the threads), in mode 2–14 MPa (41% of the strength of the material along the laying threads) and in the mode of 3-15. 9 MPa (51% of the strength of the material along the laying of the threads). That is, when switching from mode 1 to mode 2 of 3D printing, there is a decrease in tensile strength of samples with cross-laid filaments as a result of a stronger effect of the increased thickness of the stacked layer of filaments than an increase in printing speed. And when switching from mode 2 to mode 3, the increase in printing speed has a predominant effect, which leads to a slight increase in material strength (Fig. 2).
Samples of model material with longitudinal and transverse laying of threads have a different type of tensile diagram and fracture surface. If the tensile diagram of samples with transverse filament laying has a characteristic form for brittle fracture, then on the tensile diagram of samples with longitudinal fiber laying, after a slight decrease in the tensile force, after reaching a maximum, its gradual decrease is observed until the moment of sample failure.
Fig. Fig. 3. The nature of the destruction of samples with transverse (a) and longitudinal (b) laying of threads
Samples with transverse fiber laying (Fig. 3a) have an absolutely flat fracture surface, while specimens with longitudinal fiber laying (Fig. 3b) have a developed fracture surface. When examining these fractures with an optical microscope, it can be seen that the destruction of the material with transversely laid fibers occurs in one plane (Fig. 4a) along the surface of the laid filaments. The fracture of the model material with the longitudinal laying of fibers (Fig. 4b) has a developed character. Fracture proceeds in different planes, and both areas of damage accumulation and flat zones characteristic of the main crack propagation are observed at the fracture.
Fig. Fig. 4 Fracture view of specimens with transverse (a) and longitudinal (b) filaments
Conclusion tensile from 3D printing modes. The strength in all printing modes was 31-33.5 MPa, which is approximately 31% lower than the strength of monofilaments declared by the manufacturer.
Learn more