3D printing growth rate
Three Areas Holding Back The $10.6B 3D Printing Industry
Market research firm SmarTech Analysis recently released its data for the additive manufacturing (AM) industry. It determined that, in 2021, the 3D printing sector reached $10.6 billion in revenue, excluding the revenues associated with hardware maintenance contracts and post-processing equipment. The firm further projects that AM is expected to grow to over $50 billion by 2030.
The 3D printing industry is projected to reach over $50 billion by 2030, according to one market ... [+] research firm.
Image courtesy of SmarTech Analysis.This growth is closely pinned to the trend that large manufacturers will increasingly use the technology for mass production. However, in order for AM to reach wide-scale adoption, it will need to advance significantly in three crucial and interrelated areas: throughput, factory integration, and quality control. Fortunately for the industry, these are all also issues that are being actively addressed.
3D Printing Throughput
Due to its roots as a prototyping technology, 3D printing was never designed with mass production in mind. Instead, its ability to create complex shapes has been limited to one-off parts or small batch manufacturing. For that reason, firms across the 3D printing industry have been working to develop systems that can make many parts as rapidly as possible, a concept known as throughput.
Among the leaders in this regard is HP, which spent years researching the technology before finally unveiling technologies capable of rapid production both in plastics and metals. The 2D printing giant has ported its expertise in inkjet printheads over to 3D printing with a technology called Multi Jet Fusion (MJF). MJF is already being used to produce large batches of polymer parts for everything from eyewear to grocery bots.
Legor Group in Italy is using HP Metal Jet to 3D print functional stainless steel accessories for ... [+] the jewelry and fashion markets.
MORE FROMFORBES ADVISOR
This is just the beginning for the company, which is now rolling out its Metal Jet technology. A form of what is called “metal binder jetting,” Metal Jet deposits a liquid binder onto metal powder, creating a component that must then be sintered in a furnace. Customers as large as Volkswagen are investing in the technology with a plan to mass produce up to 100,000 metal components annually for consumer vehicles.
However, HP isn’t the only company in this quickly evolving space. A widely publicized startup called Desktop Metal is working to speed up metal binder jetting. GE, too, is working on its own version of the technology. Altogether, these companies are ushering in an era in which low-cost metal powders can be used to 3D print large numbers of parts in a single job, potentially changing the cost structure for metal 3D printing altogether.
This means that they will be taking on the established leaders in metal 3D printing, which typically rely on zapping high powered laser beams at expensive metal powders. These companies are working on increasing throughput, as well, by adding up to 12 lasers to their machines.
3D Printing Factories
While a fleet of 3D printers may be capable of manufacturing at volume, that doesn’t mean that they’ll necessarily fit into an existing factory operation. In large part, this is due to the fact that they lack mass production-level software.
Now, a handful of startups have emerged to take on the challenge of developing AM-specific software for manufacturing execution systems (MES). These tools make it possible to both manage a fleet of 3D printers and connect them to a company’s existing production software. They typically aid in the entire order-to-fabrication workflow. This means order quoting and tracking, print file preparation, print job monitoring and data collection, printer fleet queuing, quality control, and shipping.
MES software necessarily connects to a business’s existing software tools. This includes product lifecycle management (PLM), enterprise resource planning (ERP), and general IT software. While PLM might include a company’s preferred 3D modeling software, ERP will be made up of everything from payroll programs to tools for tracking overall finances.
MES platforms are now working to take all of the software that a manufacturer might already be working with and inserting 3D printing into the mix. However, they’re not just limiting themselves to AM. Many MES developers are looking to connect with other production equipment, such as CNC machines. Then, with the help of machine learning, the entire workflow can be improved automatically as data from each order and each machine job feeds back into the work cycle. Artificial intelligence is significantly adding to the capabilities of MES software.
3D Printing Quality Control
Perhaps the biggest obstacle to widespread AM adoption is quality control. This is because, with additive, each part is distinct. Every point on the build platform may be slightly different and even the slightest variation in a printing parameter may change the microstructure of the printed object.
In turn, an object printed at one angle will not be the same as one printed at another. And, because parts are built up layer by layer, it is difficult to validate the internal geometries of an item once printing is complete. As a result, the only true way to assure the quality of a printed object is with a CT scan, typically a cost-prohibitive method for inspecting multitudes of parts.
Fortunately, not only are newer CT scanning systems with lower price tags coming onto the market, but there are other tools that are being used to ensure the quality of printed parts. Among them is computer simulation. Companies like ANSYS have developed software that can anticipate any defects that occur during the printing process and compensate for them. Hexagon is taking this one step further by predicting issues at the microscopic level.
Meanwhile, firms like Sigma Labs and Additive Assurance have created hardware to monitor the build chambers of metal 3D printers to detect errors. Increasingly, these tools will enable active feedback so that the machines can quickly correct issues during the print process. When connected with MES software and 3D printing simulation, the equipment can learn from past errors and address them before they even happen in the future.
Altogether, these areas are advancing at incredible rates, in large part because manufacturers see the value in being able to produce objects from digital files on demand. As companies as large as Ford, GE, and Siemens look to 3D printing to produce quality end parts, they are driving the entire additive market to bend to their needs. To reach a whopping $50 billion by the end of the decade, the 3D printing industry has to be capable of making millions of parts for those customers.
3D Printing Market Size, Growth
The global 3D printing market size was valued at USD 15.10 billion in 2021. The market is projected to grow from USD 18.33 billion in 2022 to USD 83.90 billion by 2029, exhibiting a CAGR of 24. 3% during the forecast period. Based on our analysis, the global market exhibited an average growth of 20.2% in 2020 as compared to 2019.
Rapidly increasing digitization, increasing adoption of advanced technologies such as Industry 4.0, smart factories, robotics, machine learning, and others fuel the demand for online 3D printing for simulation purposes. These technologies increase the chances of broader adoption and greater utilization of this technology across industries, including aerospace, automotive, healthcare, among others. For instance,
- Aerospace companies are exploring this 3D printing for manufacturing various hardware parts of their products. For instance, Boeing leverages industrial 3D printing to manufacture the interior parts of its plane, whereas, NASA uses it to build rocket engines and parts of the satellite.
- Automotive industry is expected to show a huge adoption of this technology. Rapid tooling incorporated with additive manufacturing has become the priority of many automotive manufacturers.
Customization of the automotive interior is another major application of this technology in the automotive industry.
COVID-19 IMPACT
Supply Chain Disruption and Halts on Production Units Negatively Impact Printing Industry Amid Lockdown
Post outbreak of the COVID-19 crisis, industrial hubs, manufacturing sectors witnessed an immediate supply chain disruption and halts on production. As a result of the fast-spreading pandemic, the overall industrial production across the globe experienced a sharp decline. It was demobilized, reflecting supply chain disruption, and reviving financial market conditions. The crisis forced market players across the globe to reduce their operational expenditure. Fewer operation expenditures restricted the investments of market players in this technology in 2020, impacting the 3D printing market growth.
The temporary closures of the factories in major economies such as China, Southeast Asia, the U. K., Germany, and others have impacted the production plants of the 3D technology industry and operations of suppliers resulting in short-term supply shortages. Manufacturing capacity was observed to be restored to normalized levels by the end of July 2020. The short-term disruptions in supply shortages have resulted in logistics challenges, including delays in delivering services to end-use industries. Such a situation affected the company’s ability to meet the technology demand of the end customers. For instance,
- Stratasys, one of the well-known companies in the market, experienced dip in sales in the early months of COVID-19 pandemic. However, later, the company started rebounding as it picked up new manufacturing contracts.
However, the study conducted by the ‘Society of Manufacturing Engineers’ states that 25% of the manufacturers in the United States plan to change their supply chains in response to the pandemic. The study also found that they prioritize investing in this technology post-COVID-19 out of other technologies such as robotics, 5G, digital security, and artificial intelligence. This shows that the increasing investments of manufacturers in 3D technologies are likely to uplift the growth of the market in the forthcoming years.
LATEST TREND
Request a Free sample to learn more about this report.
Advancement in 3D Hardware and Software is Generating New Revenue Streams for Market Players
Techno-savvy start-ups and established market players are upgrading and developing new technologies. The advancements in hardware have led to faster and reliable 3D printers for production applications. Polymer printers are one of the most used 3D printers.
- According to a 2019 report by Ernst & Young Global Limited, 72% of the enterprises leveraged polymer additive manufacturing systems, whereas the remaining 49% used metal additive manufacturing systems. The statistics show that developments in polymer additive manufacturing would create new market opportunities for market players.
Fused Filament Fabrication (FFF) and powder bed fusion technologies such as Multi Jet Fusion offered by HP Inc. are expected to be the most preferred industrial 3D technologies by the manufacturers due to their ability of volume manufacturing and high productivity. Similarly, resin-based technologies such as digital light processing (DLP) and Stereolithography (SLA) are more likely to have a growing demand from the dental and consumer goods industry.
Similarly, software developments are gaining pace in the 3D industry driven by the demand to streamline operations. The technology has been extensively used in the manufacturing process, which has surged the need for software that can help manufacturers to increase production volumes and enhance their additive manufacturing processes efficiently.
DRIVING FACTORS
Substantial Investments of Governments and Tech Giants to Foster Market Growth
Many countries across the globe are experiencing massive digital disruptions in advanced manufacturing technologies. The United States is a potential user of 3D technology. In 2018, the United States Department of Defense included this technology as an important capability in their budget. Even tech software giants such as Autodesk, Microsoft, and HP have launched products aimed at additive and 3D printing manufacturing.
Similarly, China is making significant efforts to maintain the competitive index of the manufacturing industry in the global market. Chinese manufacturers foresee this technology as both a risk and opportunity for the Chinese manufacturing economy, and hence they tend to invest in the research and development of this technology.
Whereas India is looking forward to this technology as an opportunity to increase its share in global manufacturing competitiveness. The market in India is supported by active government initiatives such as the ‘Make in India’ Initiative.
Korea has established an independent roadmap for research and development of this technology and provides national support to execute it. The government of Korea is introducing tax incentives and accelerating industry regulatory agreements to encourage the adoption of this technology.
The U.K. government has developed an independent 3D technology strategy; however, it is witnessing some uncertainties in the U.K. manufacturing sector due to Brexit. Germany is expected to define new strategies for the technology as Germany has a well-established Industry 4.0 infrastructure.
RESTRAINING FACTORS
High Initial Investments to Restrict Market Growth
High initial investments are observed to be the most significant restraint for adoption of this technology. This investment encompasses investment in hardware, software, materials, certification, additive & manufacturing education, and training for the employees. The capital costs and resources required to set up a 3 dimensional system are quite expensive than traditional printing methods.
However, with the introduction of the industrial Desktop 3D printer, the manufacturers are helping the end-customers cut the high initial costs. Desktop printers are easy to use and handle and also are less expensive than the 3 dimensional system.
SEGMENTATION
By Component Analysis
Wider Adoption of the Software to Make Designs of Objects and Parts to Fuel its Growth Rate
On the basis of component, the market is divided into hardware, software, and services.
Adoption of hardware for manufacturing 3D printed material is maximum and is likely to maintain its dominance during the forecast period. The demand for hardware is increasing as major key players are enhancing their product portfolio and launching new technologies to serve high demand from several industry verticals. Companies are investing in research & development activities, which have a positive impact on the market growth.
The software is expected to grow at a high CAGR during the forecast period. The 3D printing software is widely used in different industry verticals to design the objects and parts to be printed. As manufacturing companies are shifting away from traditional manufacturing methods, the adoption of 3D software has grown to print iterations of different manufacturing parts.
By Technology Analysis
Fused Deposition Modeling (FDM) Technology to be at Forefront
Based on technology, the market has been divided into FDM, SLS, SLA, DMLS/SLM, Polyjet, Multi Jet Fusion, DLP, Binder Jetting, EBM, CLIP/CDLP, SDL, and LOM.
Among these, fused Deposition Modeling (FDM) technology captured the maximum share in 2021. The growth of FDM is mainly due to the ease of operation and advantages associated with the technology. FDM technology is highly used in making durable, strong, and dimensionally stable parts.
Direct Metal Laser Sintering (DMLS/SLM) technology is expected to grow at a high CAGR during the forecast period. The technology promotes the production of high-quality metal components, which makes them suitable for the manufacturing industry since they enable the creation of complex geometries of metals of extremely small sizes.
Selective Laser Sintering (SLS) is expected to show significant growth in coming years. SLS finds a wide variety of vertical applications, including aerospace, defense, automotive, and others. Polyjet, Multi Jet Fusion, DLP, Binder Jetting, EBM, CLIP/CDLP, SDL, LOM technologies are expected to witness a significant rise in adoption in the upcoming years.
By Application Analysis
To know how our report can help streamline your business, Speak to Analyst
Prototyping to Capture Maximum Market Share Due to its Widespread Acceptance Across Various Vertical Industries
This technology has application in prototyping, production, proof of concept, and others.
Due to widespread acceptance of the prototyping process across various vertical industries, the prototyping represented the largest market share in 2021. Prototyping helps businesses to achieve greater precision and produce consistent end products. This technology helps to manufacture 3 dimensional computer-aided design (CAD) models and prototypes.
The production is expected to witness strong growth during the forecast period. While manufacturers are shifting their traditional manufacturing units toward advanced manufacturing processes, the adoption of this technology to produce complex and low-volume parts is expected to grow during the forecast period.
By End User Analysis
Automotive Industry to Lead Market Owing to its Maximum Use in Producing Prototype Equipment
Automotive, aerospace and defense, healthcare, architecture and construction, consumer products, education, and others are some of the end-users of 3D printing.
The adoption of this technology in the automotive industry is expected to hold a maximum share in 2021. For decades, the automotive industry has been using this technology to produce prototype equipment and small custom products in a short time span. The technology is being widely used for the construction of lightweight components for automobiles and OEMs.
Additive manufacturing has tremendous potential for the aerospace industry, where light, solid, and geometrically complex parts are required — and normally manufactured in limited quantities. Aerospace and defense companies are heavily using this technology to produce lightweight components.
Additive processing in the healthcare industry helps create artificial tissues and muscles that mimic normal human tissues that can be used in substitution operations. These skills are anticipated to lead to vertical acceptance of 3DP in healthcare and the sector's development.
On the other hand, architecture and construction, consumer products, education verticals are anticipated to grow at a significant CAGR during the forecast period.
REGIONAL INSIGHTS
North America 3D Printing Market Size, 2021 (USD Billion)
To get more information on the regional analysis of this market, Request a Free sample
Geographically, the market is divided into five major regions such as North America, South America, Asia Pacific, Europe, and the Middle East & Africa. They are further categorized into countries.
Globally, North America accounted for the maximum share in the global market mainly due to rising expenditure on advanced manufacturing technologies by developed countries such as Canada and the U.S. Also, various government agencies, such as the National Aeronautics and Space Administration (NASA), have identified major R&D investments that can greatly contribute to space applications and create new technologies that drive business expansion.
Europe holds the second-highest market share in the global market. The demand for this technology is high among small and medium-sized industries that require high-speed, reliable, and inexpensive prototypes for manufacturing purposes. The regional market is expected to showcase strong growth in the adoption of this technology in the manufacturing and semiconductors industry.
Asia Pacific is anticipated to grow at the highest CAGR during the forecast period. An increasing interest in the development of a sustainable 3D printing environment has been backed by APAC manufacturers and the implementation of several policies and legislative proposals by governments in the region. Given the massive government funding for the industry, China is possibly the main force behind adopting this technology in Asia.
To know how our report can help streamline your business, Speak to Analyst
The Middle East & Latin America is expected to showcase high growth during the forecast period. The rapid adoption of 3D technology in the region is mainly due to technological advancements and improvements in the manufacturing industry.
KEY INDUSTRY PLAYERS
Companies are Focusing on Partnership and Collaboration Activities for Safer Internet Environment
The prominent players of the market are focusing on offering advanced and innovative solutions catering to the growing needs of industries. These key players are investing in R&D to provide innovative services and materials. They are entering into strategic partnership and collaboration to provide next-generation solutions. These companies are offering consumer-centric solutions to help in boosting business growth. Similarly, the key players are keen on offering a vast range of 3-dimensional materials to grow across every industry application.
February 2022 – Imaginarium partnered with Ultimaker to introduce desktop & industrial 3D printer range in the India market. This partnership would help Ultimaker to expand its business in India, where additive manufacturing is anticipated to reach a point of breakthrough in the coming years.
November 2021 – 3D Systems is planning to enhance additive manufacturing innovation through partnerships and launch of products. The company launched new 3-dimensional printing tools and collaborated with the U.K.-based startup Additive Manufacturing Technologies (AMT) to present novel 3-dimensional printing workflows and improve AM software, which is ideal for automotive components.
List of the Key Companies Profiled:
- 3D Systems Corporation (U.S.)
- The ExOne Company (Germany)
- voxeljet AG (Germany)
- Materialise NV (Belgium)
- Made in Space, Inc.
(U.S.)
- Envisiontec, Inc. (Germany)
- Stratasys Ltd. (U.S.)
- HP, Inc. (U.S.)
- General Electric Company (GE Additive) (U.S.)
- Autodesk Inc. (U.S.)
KEY INDUSTRY DEVELOPMENTS:
- March 2022 – South Africa’s Department of Science and Innovation (DSI) launched a pilot project to build around 25 houses by utilizing 3D printing technology to combat the shortage of housing in the country.
- March 2022 – 3DGence, a European manufacturer, launched a new industrial FFF machine, INDUSTRY F421, which is well-suited with high performance materials. Additionally, the firm has also introduced AS9100, a new high-temperature filament, which is made using polyether ether ketone (PEEK) and certified for use in defense and aerospace sectors.
REPORT COVERAGE
An Infographic Representation of 3D Printing Market
View Full Infographic
To get information on various segments, share your queries with us
The global 3D printing market research report highlights leading regions across the world to offer a better understanding to the user. Furthermore, the report provides insights into the latest industry growth trends and analyzes technologies that are being deployed at a rapid pace at the global level. It further offers drivers and restraints, helping the reader gain in-depth knowledge about the market.
REPORT SCOPE & SEGMENTATION
ATTRIBUTE | DETAILS |
Study Period | 2018-2029 |
Base Year | 2021 |
Estimated Year | 2022 |
Forecast Period | 2022-2029 |
Historical Period | 2018-2020 |
Unit | Value (USD billion) |
Segmentation | By Component, Technology, Application, End-User, and Region |
By Component |
|
By Technology |
|
By Application |
|
By End-User |
|
By Region |
|
with what resolution 3D printers are printed
threaded parts of the printed parts
6 safe ways to remove 3D scribes
9000 3D-spent at home gives us the opportunity to give us the opportunity to produce given objects at a very low cost.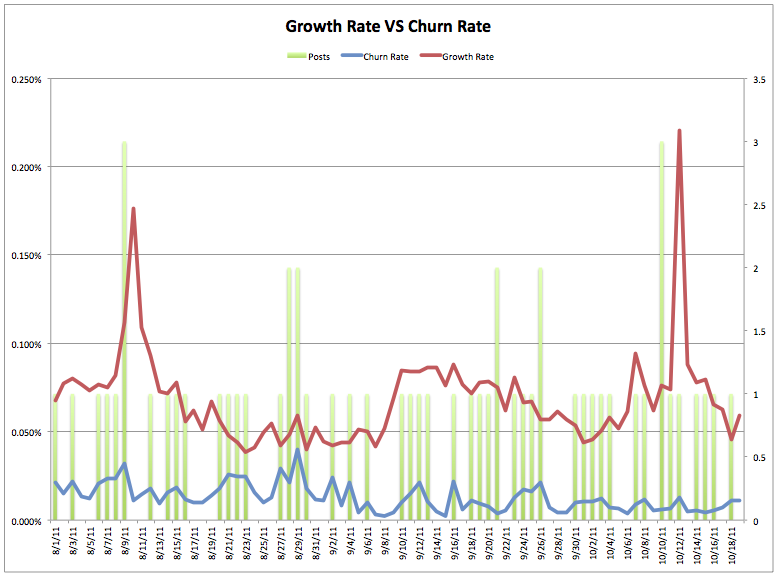
Desktop printers
3D print speed settings
In general, there are currently three blocks of speed settings supported by 3D printers. The first block includes speeds from about 40 to 50 mm / s, the second - 80-100 mm / s, the fastest printing is carried out at about 150 mm / s. Some printers can even print at speeds over 150mm/s.
Usually, though, faster 3D printing means lower quality. At speeds above 150 mm/s, the quality drops significantly, and problems can arise, since the filament is prone to slip at such speeds.
How to set the print speed
Typically, the 3D print speed is set in the slicer software used to prepare the 3D model for printing. In Cura, for example, you just need to enter the desired print speed in the Print speed field in the Basic tab (in previous versions, you first had to switch to the Advanced mode and open the Speed tab).
Cura calculates the duration of the print process based on print speed and quality settings.
As soon as the print speed ( Print speed ) or other setting is changed, Cura recalculates the print time and displays it (see arrow). Cura's calculations turn out to be very close to real-time printing.
How long does 3D printing take in practice?
To find out how fast 3D printers actually print, two popular desktop printers, the Ultimaker 2 and the Wanhao Duplicator 6, were tested on two more or less complex objects.
These two models were printed:
3DBenchy. This 3D model is designed to test and measure the speed of 3D printers; it is quite complex and requires attention. The boat is 6 cm long, 4.8 cm high and 3.1 cm wide. Here you can get the 3DBenchy STL file for testing for free.
3DBenchy's 3D printing speed is relatively slow, the model is quite difficult to print (Photo: 3DBenchy.com).
Universal tablet stand (up to 1.2 cm thick). The stand is 14 cm long, 4.2 cm high and 9.8 cm wide. The STL file is available for free on Thingiverse.
The stand is quite large and difficult to print (Photo: Thingiverse).
These objects were printed at two speeds, 100 mm/s and 50 mm/s, at similar settings. Here are the results:
Printer
Model
50 mm/sec
100 mm/sec
Ultimaker 2
3DBENCHY
h 09 min 9 min.0003
1 h 55 min
Wanhao Duplicator 6
3dbenchy
2 h 13 min
1 h 51 min
Ultimaker 2
Strection
9000 H 23 min4 h 36 min 9000 min
Wanhao duplicator 6
Stand
6hrs 27mins
4hrs 45mins
- For the smaller models, the difference between slow and fast printing is not particularly striking: almost 2.
25 hours versus less than 2 hours. Unless you're insanely short on time, choose a slower speed for better print quality.
- For large models, the print speed varies more significantly: 6.5 hours versus 4.75 hours.
Cunning. If you don't have your own 3D printer, download the free Cura software from the Ultimaker website. Cura has profiles for most desktop printers (FDM), so you can check how long it takes to print a specific 3D model on a particular device - just import the STL file and play with Cura settings. To try another 3D printer, select Machine > Add new machine.
Does high-speed sintering promise the fastest 3D printing?
On an industrial scale, even more impressive prospects dawn on the horizon. The University of Sheffield has announced that its scientists have built a £1m-funded 3D printer that can produce plastic parts as quickly as traditional mass-production methods such as injection molding.
The process is called high-speed sintering (HSS), which melts the polymer layer by layer (similar to the additive printing process), but instead of using lasers, HSS prints on a powder substrate with infrared-absorbing inks. After the layer is printed, it is exposed to infrared radiation, the ink-coated powder is heated, resulting in melting, while the non-irradiated powder remains cold.
A team led by Prof. Neil Hopkinson claims that their machine is capable of producing parts up to 1 m³, i.e. with a washing machine, which is three times more than existing printers can. The print speed is dependent on the size of the object, however, Hopkinson estimates that small components will be created at speeds of less than one second per part.
What use is this to us? The good news is that HSS technology has been licensed to industrial 3D printer manufacturers on a non-exclusive basis, and new machines are expected to hit the market in 2017. This means that in the near future we can expect the transition of this industrial technology to the "home" level.
What do the characteristics of a 3D printer mean?
As I wrote the other day, I am currently writing a book on choosing a 3D printer. The working title is 'How to choose a 3D printer' In it I will tell you what to pay attention to first of all for a beginner. And what does this or that parameter mean. What are the schemes of 3D printers. And a lot of what is scattered over various discussions. Here the information will be compiled in one place. The book will be FREE, with free distribution.
Below is a draft of one chapter, in which I will look at what the individual characteristics of 3D printers, which are published by equipment manufacturers and sellers, mean.
Using the Zenit 3D printer as an example, let's take a look at the specs and I'll explain what they mean.
· Printable area: 240 x 215 x 230 mm
One of the main parameters. Tells us what is the maximum size we can print a part. In fact, the printable area is usually slightly smaller. And in reality, details of this size are not printed. Typically, a part can be larger than one of the sizes. But here we must understand that we can place the part diagonally on the desktop. Therefore, the maximum length of a part is usually limited by the length of the table diagonal. Although in some cases it is possible to connect a third dimension. But here we must already take into account the direction of the layers.
· X, Y axis positioning accuracy: 0.04mm
An important parameter that affects print quality. This is how accurately the printer can position the extruder over the printable area. Achieved with good mechanics. Tensioned belts. And greased guides.
· Positioning accuracy of the Z axis: 0.01mm
Also an important parameter that affects the quality. It depends entirely on the implementation of movement along the Z axis. There are different implementation options. We will consider them later.
Filament diameter: 1.75 mm
A parameter that tells us about the consumables used by the 3D printer. Now, in fact, there are two sizes of filament: 1.75 mm and 2.85 (3.00) mm.
1.75mm is now the most common. Such plastic is used by most 3D printers. All new materials first appear in this diameter.
2.85mm or 3.00mm older size. It is now used in 3D printers, Ultimaker clones and various homemade products. The original Ultimaker uses a diameter of 2.85mm. 3.00mm plastic is usually produced by "non-mainstream" manufacturers. And it is used in clones and DIYs.
There is no significant difference in usage between these standards. The only thing is that for 1.75mm there are more types of media offered for printing. Basic ABS, PLA plastics for both standard sizes are in stock.
There are also technical differences in the used extruder circuit. The so-called Bowden extruder is more adapted to the "thick" plastic 2. 85 (3.00) mm. This is one of the reasons why 2.5mm filament is used in Ultimaker 3D printers equipped with similar extruders.
Nozzle diameter, mm: 0.3
Everything is simple here. The thinner the nozzle, the more accurately we can print the part. In theory. In fact, a thinner nozzle is prone to clogging. And starting with a diameter of 0.2 mm, this can be a serious problem.
The second reason is that as the nozzle diameter decreases, the print time increases. Here the dependence is linear - the smaller the diameter of the nozzle - it is necessary to go through more layers and passages in order for the walls to have sufficient strength.
As a result, the most common nozzles are 0.3-0.4 mm in diameter. They achieve decent accuracy. And the print time is quite adequate.
Larger diameter nozzles 0.5-1.0mm are commonly used in printers with a large printable area. With them, a speed is achieved that is more important when printing large parts than the quality of printing small parts of a model.
Most printers can change the nozzles and use the correct diameter for their job. But in fact, by setting 0.3-0.4mm you will close 95% of all possible tasks.
· Layer height : 50 to 150 microns
Many manufacturers declare layer heights even less than 50 microns. This is 0.05mm. For most, the lower limit is 50-100 microns. Here you need to understand - the thinner the layer, the more the printing time increases. That is, a part with a layer of 0.05 mm will be printed at least twice as long as a part with a layer of 0.1 mm.
Therefore, for most applications, a lower limit of 0.1mm or 100 microns is more than adequate.
As for the upper limit of the thickness, there is also a dependence here. For high-quality printing, it is necessary that the layer thickness be no more than 0.5-0.6 of the nozzle diameter. That is, for a nozzle diameter of 0.3 mm, the optimal upper limit of the thickness, as indicated here, is 150 microns or 0.15 mm.
· Print speed: 40-150 mm/s
Print speed is a relative term and is usually achieved on large straight parts. The print speed is uneven and depends on many parameters. And the more complex the model, the slower the print speed. The average speed of most printers lies in the region of 50-100mm/sec. If a printer can't print simple parts well at 50mm/sec with standard PLA or ABS, there's something wrong with it.
As I said, super quality is usually achieved at 30-40mm/sec. This speed is selected either manually in the settings or the slicer itself (print preparation program) itself reduces the speed to adequate values.
· Maximum print head speed: 300mm/s
Parameter that affects print speed. It is indirectly related to the overall print speed.
Demonstrates the maximum speed at which the extruder can move "idle". In theory.
· Heated table: Yes
Another important option that caused a lot of copies to be broken. The presence of a heated table allows you to use almost all available materials for printing. First of all, with a large shrinkage. For example, one of the two most common materials is ABS. But here is a nuance ... Now there are quite a lot of materials that replace ABS in many tasks. If you do not plan to use such plastic, then you can get by with a table without heating. Conclusion - a table with heating is certainly better than without heating. But if you do not plan to use ABS in your tasks, then you can safely do without it.
Number of printheads: 1
Most 3D printers have one extruder and this is also usually enough for the vast majority of applications. The second extruder makes it possible to use the dissolved material to create supports. For example, HIPS or PVA.
You can also print in two colors. But it almost didn't work out. And apart from demonstrating the possibilities, it is usually not seriously used.
In general, two-material printing got its momentum after the launch of the PRO250 printer from PICASO. It uses an extruder with JetSwitch rotary nozzles. It allows you to achieve high-quality printing with two materials. And most importantly, he dramatically reduced the printing time with two materials. The fact is that when printing with two materials, when the extruders are located next to each other, you have to build an additional technological “tower” next to the part. This leads to a significant increase in print time. Switching between extruders can take several minutes.
So if you don't need to print complex models, then you probably won't need a second extruder.
· Software : RepetierHost, Slic3r, Cura
With the exception of some 3D printers with their own software, most can work with universal programs. Both paid and free. These are Cura, RepetierHost, Slic3r, Simplify3D and many others.
Computer connection: USB
Most 3D printers connect to a computer using USB. Although more and more new models are appearing that also support connecting to the network using WiFi or Ethenet.
· SD card printing: Yes
This is the more important setting. Almost all printers have it. But there are still printers that cannot print from Flash or SD cards.
Why is this necessary? If possible, start printing using such memory cards. Printing via USB can lead to marriage. The fact is that the USB interface is quite dependent on the speed of the computer. And if you load your computer with a “heavy” program at the time of printing, it is possible to “hang” it, which will lead to marriage.
· Dimensions: 460x360x370 mm
The parameter is only important for understanding where you can place the equipment.
· Weight : 20 kg
The same - it will help you choose a place for the printer. Although it’s probably clear that it’s not worth putting 20kg on a flimsy stool.
Warranty: 3 years
Everything is clear here too. The bigger the guarantee, the better. Most printers now have a warranty of around a year. This, of course, is about printers bought in Russia, and not purchases from Ali.