3D printer tissue
3D Bioprinting of Living Tissues
Progress in drug testing and regenerative medicine could greatly benefit from laboratory-engineered human tissues built of a variety of cell types with precise 3D architecture. But production of greater than millimeter sized human tissues has been limited by a lack of methods for building tissues with embedded life-sustaining vascular networks.
Play
In this video, the Wyss Institute and Harvard SEAS team uses a customizable 3D bioprinting method to build a thick vascularized tissue structure comprising human stem cells, collective matrix, and blood vessel endothelial cells. Their work sets the stage for advancement of tissue replacement and tissue engineering techniques.Multidisciplinary research at the Wyss Institute has led to the development of a multi-material 3D bioprinting method that generates vascularized tissues composed of living human cells that are nearly ten-fold thicker than previously engineered tissues and that can sustain their architecture and function for upwards of six weeks. The method uses a customizable, printed silicone mold to house and plumb the printed tissue on a chip. Inside this mold, a grid of larger vascular channels containing living endothelial cells in silicone ink is printed, into which a self-supporting ink containing living mesenchymal stem cells (MSCs) is layered in a separate print job. After printing, a liquid composed of fibroblasts and extracellular matrix is used to fill open regions within the construct, adding a connective tissue component that cross-links and further stabilizes the entire structure.
Confocal microscopy image showing a cross-section of a 3D-printed, 1-centimeter-thick vascularized tissue construct showing stem cell differentiation towards development of bone cells, following one month of active perfusion of fluids, nutrients, and cell growth factors.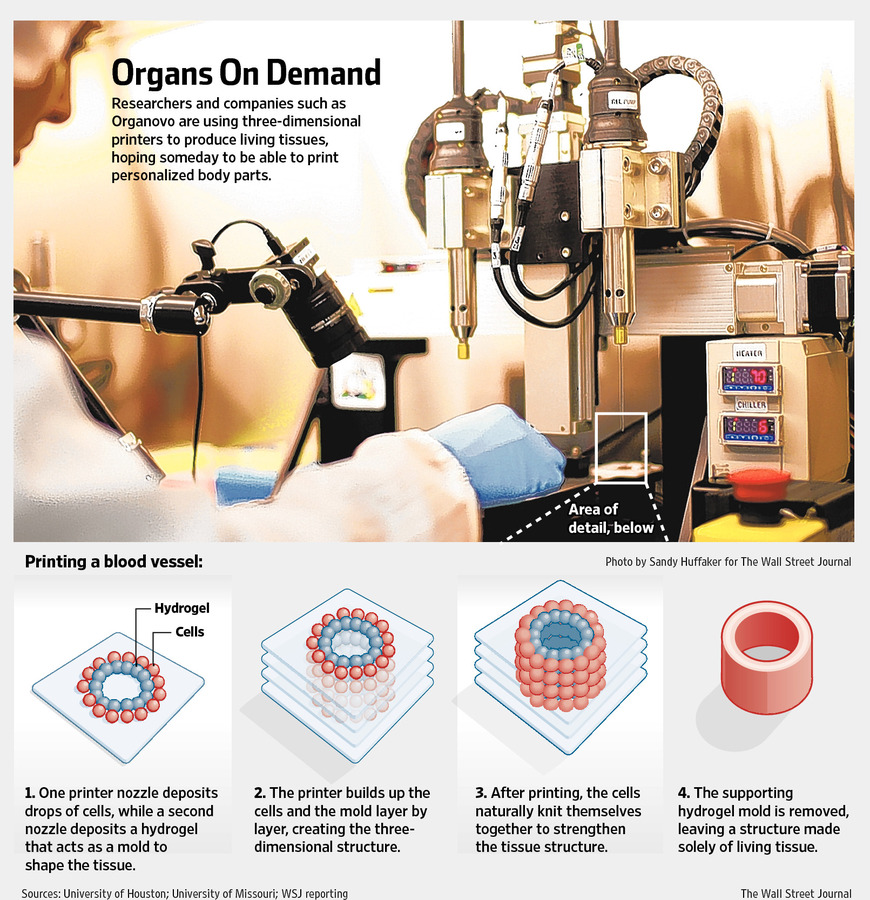
The resulting soft tissue structure can be immediately perfused with nutrients as well as growth and differentiation factors via a single inlet and outlet on opposite ends of the chip that connect to the vascular channel to ensure survival and maturation of the cells. In a proof-of-principle study, one centimeter thick bioprinted tissue constructs containing human bone marrow MSCs surrounded by connective tissue and supported by an artificial endothelium-lined vasculature, allowed the circulation of bone growth factors and, subsequently, the induction of bone development.
This innovative bioprinting approach can be modified to create various vascularized 3D tissues for regenerative medicine and drug testing endeavors. The Wyss team is also investigating the use of 3D bioprinting to fabricate new versions of the Institute’s organs on chips devices, which makes their manufacturing process more automated and enables development of increasingly complex microphysiological devices. This effort has resulted in the first entirely 3D-printed organ on a chip – a heart on a chip – with integrated soft strain sensors.
- 1/7 Cross section of long-term perfusion of HUVEC-lined (red) vascular network supporting HNDFladen (green) matrix.
- 2/7 Top-down view of long-term perfusion of HUVEC-lined (red) vascular network supporting HNDFladen (green) matrix.
- 3/7 Photograph cross section of printed tissue construct housed within a perfusion chamber.
- 4/7 Photograph cross section of printed tissue construct housed within a perfusion chamber.
- 5/7 Photograph of a printed tissue construct housed within a perfusion chamber.
- 6/7 Photograph of vasculature network and cell inks.
- 7/7 Photograph of 3D printed vasculature network (red) within Red is the
- Next
- Prev
3D bioprinting of cells, tissues and organs
3D bioprinting of cells, tissues and organs
Download PDF
Download PDF
- Editorial
- Open Access
- Published:
- Madhuri Dey ORCID: orcid.
org/0000-0002-9523-80831,2 &
- Ibrahim T. Ozbolat2,3,4,5
Scientific Reports volume 10, Article number: 14023 (2020) Cite this article
-
32k Accesses
-
70 Citations
-
10 Altmetric
-
Metrics details
Subjects
- Experimental models of disease
- Regeneration
- Tissue engineering
3D bioprinting has emerged as a promising new approach for fabricating complex biological constructs in the field of tissue engineering and regenerative medicine. It aims to alleviate the hurdles of conventional tissue engineering methods by precise and controlled layer-by-layer assembly of biomaterials in a desired 3D pattern. The 3D bioprinting of cells, tissues, and organs Collection at Scientific Reports brings together a myriad of studies portraying the capabilities of different bioprinting modalities. This Collection amalgamates research aimed at 3D bioprinting organs for fulfilling demands of organ shortage, cell patterning for better tissue fabrication, and building better disease models.
The discovery of a 3D printer dates back to early 1980s when Charles Hull, an American engineer, built the 1st 3D printer, capable of creating solid objects by following a computer-aided design (CAD). The printer deposited successive layers of an acrylic-based photopolymer which was then simultaneously crosslinked by UV light, thus creating a solid 3D object. This simple technology, called stereolithography (SLA), revolutionized the additive manufacturing industry. Gradually, by the late 1990s, 3D printing made its appearance in healthcare where surgeons began 3D printing dental implants, custom prosthetics, and kidney bladders. Subsequently the term ‘3D bioprinting’ emerged where the material being printed, called ‘bioink’1, consisted of living cells, biomaterials, or active biomolecules. Analogous to additive manufacturing, 3D bioprinting involves layer-by-layer deposition of bioink to create 3D structures, such as tissues and organs2.
3D bioprinting can be broadly categorized as either extrusion3, droplet4, or laser-based bioprinting. Extrusion based bioprinting employs mechanical, pneumatic or solenoid dispenser systems to deposit bioinks in a continuous form of filaments, while droplet based bioprinting relies on the generation of bioink droplets by thermal, acoustic or electrical stimulation. Laser based bioprinting utilizes laser power to 3D print structures such as in SLA by a photopolymerization principle. It can also be used for precise positioning of cells such as in laser direct-write and Laser Induced Forward Transfer (LIFT). The selection of “bioinks” for each of these different bioprinting modalities usually varies based on the ink’s rheology, viscosity, crosslinking chemistry, and biocompatibility. Extrusion based bioprinting primarily requires shear thinning bioinks while droplet or inkjet bioprinting needs materials with low viscosity. Over the past few years, the design and synthesis of bioinks has evolved to meet the increasing needs of new bioprintable materials. Significant advancements have also been made to integrate secondary techniques accompanying the above-mentioned modalities of bioprinting. For example, creating 3D structures with low viscosity bioinks has always been a challenge. To overcome this issue, such bioinks can now be extruded in a granular support bath containing yield stress hydrogels which solidify around the extruded structure and prevent it from collapsing5.
Apart from organ printing, bioprinting is also being used to fabricate in-vitro tissue models for drug screening, disease modelling, and several other in-vitro applications.
The 3D bioprinting of cells, tissues and organs Collection at Scientific Reports is dedicated to this field of research. This collection clearly portrays the diverse applications of different bioprinting modalities and how they could be utilized for improving various aspects of healthcare. Kim et al. 3D printed a novel two-layered polycaprolactone (PCL) -based tubular tracheal graft6. This tracheal graft, seeded with induced pluripotent stem cell (iPSC) -derived mesenchymal (MSCs) and chondrocyte stem cells supported the regeneration of tracheal mucosa and cartilage in a rabbit model of a segmental tracheal defect. Galarraga et al. used a norbornene-modified hyaluronic acid (NorHA) macromer as a representative bioink for cartilage tissue engineering7. Printed structures containing MSCs, on long term culture, not only led to an increase in compressive moduli, but also expressed biochemical content similar to native cartilage tissue. Vidal et al. used 3D printed customized calcium phosphate scaffolds with and without a vascular pedicle to treat large bone defects in sheep8. They used CT angioscan to scan the entire defect site and subsequently 3D print a personalized scaffold to anatomically fit the defect site. A bioink comprising decellularized matrix from mucosal and muscular layers of native esophageal tissues was used by Nam et al. to mimic the microenvironment of native esophagus9. Leucht et al. used gelatin based bioinks to study vasculogenesis in a bone-like microenvironment10. Kilian et al. used a calcium phosphate cement (CPC) and an alginate-methylcellulose based bioink containing primary chondrocytes to mimic the different layers of osteochondral tissue11.
This special issue also contains three notable research articles on the patterning of cells—two utilizing acoustics, and one, magnetism. Even though bioprinting enables the homogenous distribution of cells representing the macro-architectural properties, it lacks control of the tissue micro-architecture such as orientation of cells within the bioprinted constructs. Chansoria and Shirwaiker delved deep into the physics of ultrasound-assisted bioprinting (UAB) that utilizes the acoustophoresis principle to align MG63 cells within single and multi-layered extrusion-bioprinted alginate constructs12. Cells were aligned both orthogonally and in parallel to the printed filaments, thus mimicking cellular anisotropy in tissues such as ligaments, tendons, and cardiac muscle. Similarly, Sriphutkiat et al. used acoustic excitation to align skeletal myoblast cells (C2C12) and human umbilical vein endothelial cells (HUVECs) encapsulated in methacrylated gelatin (GelMA) bioink13. Goranov et al. magnetically labelled MSCs and HUVECs, and aligned them in a magnetic scaffold to mimic vascularization of bone constructs14.
It is important to note that the applications of 3D bioprinting are not limited to organ printing. It also holds great promise in less explored avenues, such as using scaffolds for drug delivery, studying disease mechanisms, or creating personalized medicines. In this Collection, Lee et al. 3D printed a rifampicin loaded PCL scaffold for possible treatment of osteomyelitis15. Xu and coworkers 3D printed paracetamol containing PVA tablets with three different geometries, each demonstrating different release profiles which could be tailored based on the patient's needs16. Further, Foresti et al. applied 5D additive manufacturing techniques to create personalized models of patients’ pathology17. Ding, Illsley and Chang 3D bioprinted GelMA-based models to investigate the trophoblast cell invasion phenomenon, enabling studies of key placental functions18.
Additionally, there are other notable articles in this Collection enumerating different aspects of bioprinting. Afghah et al. used a Pluronic-nanoclay based composite support bath to bioprint representative structures, for complex and hollow tissues, using cell laden alginate hydrogel19. Zhao et al. developed a 3D printed hanging drop dripper system for analyzing tumor spheroids in-situ20. Yumoto et al. performed RNA-seq analysis on inkjet-printed cells to analyze the effect of bioprinting on gene expression21. We would like to extend our utmost gratitude and thank all the authors and reviewers who devoted their time and effort towards this 3D bioprinting collection.
Even though 3D bioprinting is advancing at a commendable rate with researchers trying to develop new printing modalities as well as improve existing modalities, there still remains a multitude of challenges that need to be overcome. Currently, a limited number of bioinks exist which are both bioprintable and which accurately represent the tissue architecture needed to restore organ function post-printing. While bioinks made from naturally derived hydrogels are conducive to cell growth, synthetic hydrogels are mechanically robust. Thus, hybrid bioinks should be designed to amalgamate all these aspects. Moreover, the bioprinting process itself needs to be more cell-friendly. Shear stress applied to the cells during the printing process are detrimental to cell growth and might even alter the gene expression profiles. Stem cells, such as iPSCs, are sensitive to such physical forces and usually do not survive the printing process. As stem cell studies have mostly been performed on 2D environments, there exists a lot of unknowns for a 3D stem cell culture. Effective techniques need to be developed for high throughput generation and bioprinting of organoids22 for personalized drug testing and predictive disease models. Additionally, vascularization of bioprinted constructs for proper nutrient exchange, as well as integration of printed vasculature with host vasculature post organ implantation, is another major obstacle. Overall, 3D bioprinting is a rapidly evolving field of research with immense challenges, but tremendous potential to revolutionize modern medicine and healthcare.
References
Hospodiuk, M., Dey, M., Sosnoski, D. & Ozbolat, I. T. The bioink: a comprehensive review on bioprintable materials. Biotechnol.
Adv. 35, 217–239 (2017).
PubMed CAS Google Scholar
Ozbolat, I. T. 3D Bioprinting: Fundamentals, Principles and Applications (Elsevier Inc., Amsterdam, 2016).
Google Scholar
Ozbolat, I. T. & Hospodiuk, M. Current advances and future perspectives in extrusion-based bioprinting. Biomaterials 76, 321–343 (2016).
PubMed CAS Google Scholar
Gudapati, H., Dey, M. & Ozbolat, I. A comprehensive review on droplet-based bioprinting: past, present and future. Biomaterials 102, 20–42 (2016).
PubMed CAS Google Scholar
Heo, D. N. et al. 3D bioprinting of carbohydrazide-modified gelatin into microparticle-suspended oxidized alginate for the fabrication of complex-shaped tissue constructs.
ACS Appl. Mater. Interfaces 12, 20295–20306 (2020).
PubMed CAS Google Scholar
Kim, I. G. et al. Transplantation of a 3D-printed tracheal graft combined with iPS cell-derived MSCs and chondrocytes. Sci. Rep. 10, 1–14 (2020).
Google Scholar
Galarraga, J. H., Kwon, M. Y. & Burdick, J. A. 3D bioprinting via an in situ crosslinking technique towards engineering cartilage tissue. Sci. Rep. 9, 1–12 (2019).
Google Scholar
Vidal, L. et al. Regeneration of segmental defects in metatarsus of sheep with vascularized and customized 3D-printed calcium phosphate scaffolds. Sci. Rep. 10, 1–11 (2020).
ADS Google Scholar
Nam, H. et al. Multi-layered free-form 3D cell-printed tubular construct with decellularized inner and outer esophageal tissue-derived bioinks. Sci. Rep. 10, 1–14 (2020).
Google Scholar
Leucht, A., Volz, A. C., Rogal, J., Borchers, K. & Kluger, P. J. Advanced gelatin-based vascularization bioinks for extrusion-based bioprinting of vascularized bone equivalents. Sci. Rep. 10, 1–15 (2020).
Google Scholar
Kilian, D. et al. 3D Bioprinting of osteochondral tissue substitutes-in vitro-chondrogenesis in multi-layered mineralized constructs. Sci. Rep. https://doi.org/10.1038/s41598-020-65050-9 (2020).
Article PubMed PubMed Central Google Scholar
Chansoria, P. & Shirwaiker, R. Characterizing the process physics of ultrasound-assisted bioprinting.
Sci. Rep https://doi.org/10.1038/s41598-019-50449-w (2019).
Article PubMed PubMed Central Google Scholar
Sriphutkiat, Y., Kasetsirikul, S., Ketpun, D. & Zhou, Y. Cell alignment and accumulation using acoustic nozzle for bioprinting. Sci. Rep. 9, 1–12 (2019).
ADS CAS Google Scholar
Goranov, V. et al. 3D patterning of cells+in magnetic scaffolds for tissue engineering. Sci. Rep. https://doi.org/10.1038/s41598-020-58738-5 (2020).
Article PubMed PubMed Central Google Scholar
Lee, J. H. et al. Development of a heat labile antibiotic eluting 3D printed scaffold for the treatment of osteomyelitis. Sci. Rep. 10, 1–8 (2020).
ADS CAS Google Scholar
Xu, X., Zhao, J., Wang, M., Wang, L. & Yang, J. 3D printed polyvinyl alcohol tablets with multiple release profiles. Sci. Rep. https://doi.org/10.1038/s41598-019-48921-8 (2019).
Article PubMed PubMed Central Google Scholar
Foresti, R. et al. In-vivo vascular application via ultra-fast bioprinting for future 5D personalised nanomedicine. Sci. Rep. 10, 3205 (2020).
ADS PubMed PubMed Central CAS Google Scholar
Ding, H., Illsley, N. P. & Chang, R. C. 3D bioprinted GelMA based models for the study of trophoblast cell invasion. Sci. Rep. 9, 1–13 (2019).
Google Scholar
Afghah, F., Altunbek, M., Dikyol, C. & Koc, B. Preparation and characterization of nanoclay-hydrogel composite support-bath for bioprinting of complex structures.
Sci. Rep. 10, 1–13 (2020).
Google Scholar
Zhao, L. et al. A 3D printed hanging drop dripper for tumor spheroids analysis without recovery. Sci. Rep. 9, 1–14 (2019).
Google Scholar
Yumoto, M. et al. Evaluation of the effects of cell-dispensing using an inkjet-based bioprinter on cell integrity by RNA-seq analysis. Sci. Rep. 10, 1–10 (2020).
Google Scholar
Ayan, B. et al. Aspiration-assisted bioprinting for precise positioning of biologics. Sci. Adv. 6, eaaw5111 (2020).
ADS PubMed PubMed Central Google Scholar
Download references
Author information
Authors and Affiliations
Department of Chemistry, Penn State University, University Park, PA, 16802, USA
Madhuri Dey
The Huck Institutes of the Life Sciences, Penn State University, University Park, PA, 16802, USA
Madhuri Dey & Ibrahim T.
Ozbolat
Engineering Science and Mechanics Department, Penn State University, University Park, PA, 16802, USA
Ibrahim T. Ozbolat
Biomedical Engineering Department, Penn State University, University Park, PA, 16802, USA
Ibrahim T. Ozbolat
Materials Research Institute, Penn State University, University Park, PA, 16802, USA
Ibrahim T. Ozbolat
Authors
- Madhuri Dey
View author publications
You can also search for this author in PubMed Google Scholar
- Ibrahim T. Ozbolat
View author publications
You can also search for this author in PubMed Google Scholar
Contributions
M.D. wrote the manuscript. I.T.O. reviewed and edited the manuscript.
Corresponding author
Correspondence to Ibrahim T. Ozbolat.
Ethics declarations
Competing interests
The authors declare no competing interests.
Additional information
Publisher's note
Springer Nature remains neutral with regard to jurisdictional claims in published maps and institutional affiliations.
Rights and permissions
Open Access This article is licensed under a Creative Commons Attribution 4.0 International License, which permits use, sharing, adaptation, distribution and reproduction in any medium or format, as long as you give appropriate credit to the original author(s) and the source, provide a link to the Creative Commons license, and indicate if changes were made. The images or other third party material in this article are included in the article’s Creative Commons license, unless indicated otherwise in a credit line to the material. If material is not included in the article’s Creative Commons license and your intended use is not permitted by statutory regulation or exceeds the permitted use, you will need to obtain permission directly from the copyright holder. To view a copy of this license, visit http://creativecommons. org/licenses/by/4.0/.
Reprints and Permissions
About this article
This article is cited by
-
Hydrogel based tissue engineering and its future applications in personalized disease modeling and regenerative therapy
- Shikha Chaudhary
- Eliza Chakraborty
Beni-Suef University Journal of Basic and Applied Sciences (2022)
-
Emerging trends and prospects of electroconductive bioinks for cell-laden and functional 3D bioprinting
- Harish K.
Handral
- Vaishali P. Natu
- Wen F. Lu
Bio-Design and Manufacturing (2022)
- Harish K.
-
Application of 3D bioprinting in the prevention and the therapy for human diseases
- Hee-Gyeong Yi
- Hyeonji Kim
- Dong-Woo Cho
Signal Transduction and Targeted Therapy (2021)
3D printed mesh fabric
Prologue
Hello everyone! I am developing "smart sequins" - electromechanical color-reproducing devices for designer clothes. Our team is passionate about the idea of creating clothes and accessories that can change their color at the request of the owner or depending on environmental conditions.
In this article I want to talk about how we used 3D printing in our project, share our experience and tools.
3D printing on fabric
One of the tasks that I had to solve was to figure out how to make an elastic fabric out of plastic sequins, which in its properties would resemble textile materials. At the same time, it is necessary to provide for the possibility of easily creating electrical connections between the sequins.
There are quite a few articles and materials on making clothes on a 3D printer. Many different methods have already been invented, from creating hinges right in the printing process to printing with elastic plastics.
While looking for a solution, I came across this video. From it, I first learned about the method of printing on mesh fabric using a conventional FDM 3D printer.
The author himself claims that he spied the idea here: Shorey Designs.
The essence of the method is very simple. We create a 3D model of a fragment of the future canvas, then arrange a lot of fragments so that we get a whole canvas. We start the slicer and prepare the G-code. Before sending it to the printer, you need to insert a pause and raise the extruder before printing a certain layer. The printer will stop during operation. At this point, we cover the printed layers with a mesh cloth. We continue to print. Due to the presence of large holes in the fabric, the layers of plastic will interlock with each other, as in conventional printing, and the mesh fabric will be firmly integrated into the parts.
Modifying G-code
I use Cura version 3.2.1 as a slicer. 3D printer - homemade H-bot controlled by a board based on ATmega2560 (RAMPS 1.4) with Marlin firmware.
To pause the printer, there is an M25 command. Command for lifting in Z by 20mm: G0 Z20. It is noteworthy that the M25 must go before the ascent, otherwise the next command is processed first. Why this happens is a mystery to me, apparently somehow connected with the processing of commands by the printer.
Add commands to G-code:
Operation automation
Manually searching for the required line in the G-code file and inserting commands is not the most modern solution, I thought and wrote a simple program that allows you to open and view toolpaths.
For the convenience of viewing the layers, the “explode” command is provided, which allows you to visually increase the distance between the layers of the model. After pressing the "insert pause" button, the distance between the marked layer (red) and the previous one increases. This means that the print will be interrupted precisely between these layers.
To understand where one layer ends and the next begins, I used the comments that Cura kindly provides in its output files. The keyword ";LAYER:X" allows you to accurately find the boundaries of layers in a text file.
Pressing the "write file" button allows you to save the modified G-code in the specified location.
Save the file to the SD card and bring it to the printer.
It's funny that only while preparing this article, I came across a video that tells how you can do the same using standard Cura tools ... But the process is already running, it's too late to slow down! Here, starting at 7:30, it is described in detail how to do it. Well ... hurry up - learn how to parse G-code!
Trying to print
Formation of the first layers. We print on glass. Heated table. Table temperature 60⁰С, printing temperature 220⁰С. The print material is PLA plastic. Layer height 0.2mm.
During the pause, place a piece of fabric and fix with magnets. Since the table is aluminum (paramagnetic), we put the magnets on the top and bottom sides of the table. Fixation is made in 4 places, in the corners of the part. This is quite enough. The main thing is not to place them too close to the print area, otherwise the magnets will stick to the print head.
After 40 minutes, this is the structure. The thickness of each 6 carbon element is 1mm. The gap between the elements is 2mm.
In this experiment, tulle was used as the backing fabric. It is a lightweight mesh fabric of medium stiffness, woven from polyester threads.
Experiments have also been made with mosquito net printing. In the hardware store, there were two types of them: fabric and fiberglass. Fabric mesh is softer than tulle, but has greater mechanical tensile strength, as well as less elasticity. The fiberglass mesh is harder than tulle, its mechanical strength is the highest of all participants in the experiment.
Hexagonal sequin printing on fiberglass mosquito net. The gap between the elements is 1mm. The matrix is very hard.Clearance is clearly not enough.
Round sequin printing on fiberglass mosquito net. The gap between the circles is 2mm. It has a lot of flexibility, but there is too much unfilled space between the sequins.
After several test prints, the fabric mesh was chosen. She formed the basis of the matrix of smart sequins. The resulting matrix can bend in all directions.
The video demonstrates the operation of the program, the printing process and the final result.
Conclusion
The method of printing on mesh fabric proved to be very good. This is an ideal solution for our task, because the fabric substrate allows us to weave conductive threads into it, which are used to provide electrical connection between the individual sequins of the matrix. Moreover, the formation of a “pattern” of conductors can be carried out at the preparatory stage. And the 3D printing itself is later.
The strength of the resulting structure depends mainly on the strength of the substrate material. But the flexibility will also depend on the distance between the sequins, as well as their shape.
The developed program still needs to be improved. For example, you can finish the retract before lifting, allow the user to adjust the height of the extruder.
Link to the source code for the processing environment.
And also a link to the release with the .exe file of the program.
By the way, we recently launched our "smart sequins" on the crowdfunding platform. For those who want to get to know our work better, I will leave a link.
The irregularity of 3D printing made it possible to create a plastic analogue of fabric
American engineers have learned how to print mesh structures on a 3D printer, which are similar in structure and properties to fabric. They are obtained when the material exits the printer extruder unevenly. The method allows you to create a “fabric” structured on different scales, designed for different applications, say the authors of an article presented at the UIST 2020 conference. on the other hand, it can be stretched, bent or wrinkled without damage. Engineers not only improve the properties of fabrics and weaving methods, but also try to create materials with similar properties, but with a different composition and structure. Some of them propose to create an array of randomly oriented fibers, others create hybrids with a woven base and inserts printed on it, others directly repeat the woven fabric structure using only 3D printing.
MIT engineers led by Hiroshi Ishii have developed a simpler method. It is based on the classic and most popular type of 3D printing - FDM or Fused Deposition Modeling. In this method, the printer's print head melts the filament and extrudes the melt through a nozzle, applying it to the substrate or previous layer. One of the features of the method is that the quality of application and retention of the material depends on its viscosity and extrusion volume. With some combinations of parameters, the application becomes uneven. In particular, with a low extrusion volume, a series of bumps can form, connected by a thread that does not touch the previous (lower) layer.
The authors decided to use this application mode to create a network structure, somewhat reminiscent of fabric. As a material, engineers used various substances, mainly PLA plastic. They conditionally compare the line passing through the tubercles with the warp, and the line formed by thin threads with the weft by analogy with the same structural elements in weaving. Depending on the order in which the layers are applied, the structure is different. If the direction of each next layer is the same as that of the previous one, then the base in each next layer shifts to the side.