Ceramic extruder 3d printing
Ceramic 3D Printing KITs - StoneFlower 3D printers for clay / porcelain / concrete. Add-ons for desktop 3d printers
Basic Ceramic KIT, 0.5L
NETTO PRICE 649 €
Lets you print objects from clay and porcelain in your desktop 3d printer. Includes:
- Print head with nozzles
- Ram extruder, 0.5l
- Control unit ( two preconfigured stepper motor drivers + "infinite printing" function), power source
- Teflon hose, cables, adapters
Ceramic 3D Printing KIT Basic
EU Plug Socket 772,31 € USA Plug Socket 772,31 €772,31 €
- 5,4 kg
- Available
- Ships within 1 week1
Standard Ceramic KIT, 0.
NETTO PRICE 679 €
Lets you print objects from clay and porcelain, experiment with many other materials. Includes:
- Print head with nozzles
- Ram extruder, 0.5l
- Control unit ( two preconfigured stepper motor drivers + "infinite printing" function), power source
- Teflon hose, cables, adapters
- Micro Printing Set
Please contact us if you have some questions.
*Upon printing, printer controls the clay extrusion. "Infinite printing" function lets you intercept this control and operate the ram extruder and dispense the clay via control unit. If the clay in the ram extruder ends, one can pause printing, refill the pump, extrude certain amount of clay using infinite printing functionality to restore a working pressure of clay, and resume printing. In that way one can print objects, which are larger than the capacity of the ram extruder.
Ceramic 3D Printing KIT Standard
EU Plug Socket 808,01 € USA Plug Socket 808,01 €808,01 €
- 5,4 kg
- Available
- Ships within 1 week1
Ceramic KIT PRO, 1.5L
NETTO PRICE 979 €
Lets you print large objects from clay and porcelain, suits for small-serial production. Includes:
- Print head with nozzles
- Ram extruder L, capacity 1.5L of clay
- Control unit (two preconfigured stepper motor drivers + "infinite printing"* function), power source
- Teflon hose, cables, adapters
- Micro Printing Set
Please contact us if you have some questions.
*Upon printing, printer controls the clay extrusion. "Infinite printing" function lets you intercept this control and operate the ram extruder and dispense the clay via control unit. If the clay in the ram extruder ends, one can pause printing, refill the pump, extrude certain amount of clay using infinite printing functionality to restore a working pressure of clay, and resume printing. In that way one can print objects, which are larger than the capacity of the ram extruder.
3d ceramic printing kit, clay printing kit
EU Plug Socket 1.165,01 € USA Plug Socket 1.165,01 €1.165,01 €
- 10,4 kg
- Available
- Ships in 4 weeks1
Ceramic KIT BIG, 2.
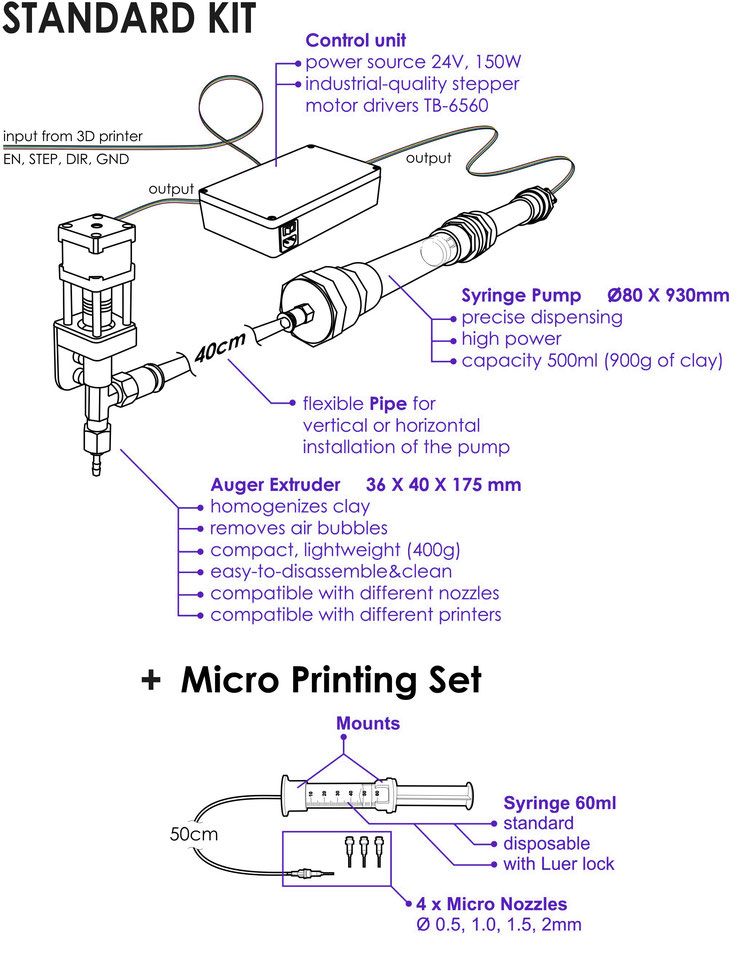
NETTO PRICE from 1800 €
Lets you print large objects from clay and porcelain, suits for industrial production. Includes:
- Print head 4.0 with nozzles
- Ram extruder L, capacity 2.5L, 3.75, or 5L
- Control unit, power source
- 1 inch (25mm) fiber-reinforced PVC hose (2m long), hose adapters
Please contact us if you have some questions.
3d ceramic printing kit, clay printing kit
2.5 EU Plug Socket 2.142,00 € 2.5 US Plug Socket 2.142,00 € 3.75 EU Plug Socket 2.499,00 € 3.75L US Plug Socket 2.499,00 € 5L EU Plug Socket 2.856,00 € 5L US Plug Socket 2.856,00 €2.142,00 €
- 10,4 kg
- Available
- Ships in 4 weeks1
Micro Printing Set
NETTO PRICE 30 €
Extension of the ram extruder for precise dispensing of small amounts of viscous liquids and pastes. Includes
- 3 disposable syringes (60ml) with luer lock
- mounts
- 6 nozzles (ID = 0.26, 0.41, 0.60, 0.84, 1.19, 1.55 mm).
- compatible high-pressure pipes
Micro Printing Set
for Basic KIT 34,51 € for PRO KIT 34,51 €34,51 €
- 0,1 kg
- Available
- Ships within 1 week1
• Light-weight print head 4.0 or precise, durable and high performance all-metal print head 5.0
• New control unit that makes the KIT compatible with mother boards of all FDM 3D printers!
• Compatible with all the software and firmware for desktop FDM 3D printers
• Layer thickness 0.3 ... 1.5 mm (clay/porcelain)
• Printing speed 20 . .. 100mm/s, recommended speed 30 ... 60mm/s (2.5mm nozzle)
• Available nozzle diameters 0.5 ... 7mm
• Capacity:
Basic/Standard pump 500ml
PRO pump 1500ml.
BIG pump 2.5L to 5.0L
• Infinite printing function: you can pause printing, upload more clay and resume. Used for large objects.
• Print head weight 630g (version 4.0, all-metal)
• Print head dimensions WxDxH = 42x72x120mm
• Dimensions of the pump (assembled) diameter 80mm, length 930mm (Basic)
• Weight of the pump 3600g (Basic)
• Extruder and pump are powered through a separate power source; 120/240W, 110/230V.
*Infinite printing
Upon printing, printer controls the clay extrusion. "Infinite printing" function lets you intercept this control and operate the ram extruder and dispense the clay via control unit. If the clay in the ram extruder ends, one can pause printing, refill the pump, extrude certain amount of clay using infinite printing functionality to restore a working pressure of clay, and resume printing. In that way one can print objects, which are larger than the capacity of the ram extruder.
Eazao - Ceramic 3D Printing
Matirx ——This is our third generation ceramic 3D printer project.
out-of-the-box
Eazao Zero is ready to use out-of-the-box, the whole machine arrives fully assembled. That means you don’t have to waste time reading manuals and putting parts together.
No Air Compressor Needed
To make it more user-friendly for beginners, we developed electric putter instead of compressed air to guarantee outstanding printing quality and stability for prints.
Eco-friendly Printing Material
Eazao can print a variety of materials such as pottery clay and porcelain clay, which is much more Earth-friendly than traditional plastic FDM printing materials.
Print up to 28” in height, multi-materials and air chamber extruder. Matrix is the ultimate next-generation 3D printer for pottery, creative construction and education.
Buy Now
Now we present a truly next-generation ceramic printer, the Eazao Zero has arrived. Eazao Zero is easy to use, produces brilliant ceramics, and features all the upgrades that our community asked for. Get ready for an incredible ceramic 3D printing experience that turns your home into a custom pottery studio.
Buy Now
Eazao Bio is a machine for micro-fluid 3D printing in the laboratory. It is equipped with a 30ml standard material tube, and 3D printing experiments can be carried out with a minimum of 5ml material. And the direct extrusion methodhas better compatibility with materials.
Buy Now
The Eazao Mega 5 is our largest 3d Clay printer with a 32bit operating system, full-color touch screen, dust resistance module, and a massive build volume of 370 x 390 x 470mm.
Learn More
More affordable, you can upgrade your FDM printer to a ceramic 3D printer using this Air kit.
Buy Now
Using this kit, you can upgrade your FDM printer to a ceramic 3D printer.
This kit is suitable for all FDM open-source 3D printers.
Buy Now
Compare with othersThis is the most recent addition to my equipment, sent by the Chinese company for me to have a look at. Much the same size as my original JK Delta this has a screw/auger printhead and clay delivery is via compressed air or mechanical ram. I have used it for doing a bunch of tests and it works well.
Jonathan Keep
Artist potter
The Eazao is a kickstarter, so do your own research before giving money. I personally wanted to play with ceramics enough that I backed their first kickstarter and I was happy to see this one appear. The Cerambot Eazao is a new 3d printer specifically for ceramics. For more information: https://youtu.be/56Cv3HEnIvQ
Caleb Kraft
Maker
Backers ReviewLatest Release
If you encounter any problems during use, you can find answers in FAQ and BLOG.
Our blog
90,000 AIM3D offers new extruders for 3D printing compositesNews
Sign up for the author
Subscribe
I do not want
4
Aim3D announced a new generation of extruders for 3D printing with granular and fiberglass polymer compositions, as well as also composite materials with a high content of fillers for sintering into ceramic and metal products.
Startup AIM3D GmbH was founded in 2017 on the basis of the University of Rostock and develops additive systems for extrusion 3D printing with granular materials - both polymer (pure, carbon and glass-filled), and composites with a high content of metals or ceramics for subsequent annealing and sintering into all-metal or ceramic products. The process is called Composite Extrusion Modeling or Composite Extrusion Modeling, CEM for short. The idea as a whole is to move away from 3D printing with filaments towards cheaper and more diverse granulates with a particle size of up to three millimeters, including those used in injection molding.
The company's first product was the ExAM255 3D printer equipped with CEM E-1 extruders. Recently, the company announced a new generation of extruders under the designation CEM-E2, which is characterized by increased productivity. The extruders will be offered in three variants optimized for 3D printing with pure, carbon and glass-filled polymers (under the letter “P”), polymer-ceramic (under the letter “C”) and polymer-metal (under the letter “M”) materials.
93/h The new extruders include the option to upgrade to an optional liquid cooling system, added 0.4mm nozzles (maximum diameter remains at 1.5mm), and improved consumables supply and replacement.
The illustration above is an example demonstrating the benefits of 3D printing with granular composites. This is a part of the coolant manifold, custom-made by Schaeffler. The consumable material was polyphenylene sulfide with a 40% glass fiber content. This highly durable and non-flammable material is not available in the form of a fine powder or filament, so the closest alternative when using FDM or SLS 3D printers would most likely be a polyamide composite, which means that high temperature resistance, strength and low hygroscopicity would have to be sacrificed.
New extruders as well as developments in larger format additive systems will be showcased November 16-19 at Formnext in Frankfurt am Main. Detailed information about AIM3D offers is available on the official website.
composite granulate AIM3D
Follow author
Subscribe
Don't want
4
More interesting articles
fourteen
Subscribe to the author
Subscribe
Don't want
At the end of November, the Almaz-Almaz concern announced the launch of serial production of Dobryn quadrocopters...
Read more
ten
Subscribe to the author
Subscribe
Don't want to
Igor Kostusev, an employee of the Arktika shipbuilding enterprise, received the Lomo Regional Prize. ..
Read more
sarkazm
Loading
04/01/2016
39889
68
Subscribe to the author
Subscribe
Don't want
News from the world of printing in a short line
FDplast announced the release of a free...
Read more
3D Printer Extruder - Complete Manual Heatle
Learn the basics of direct drive and Bowden extruders, hot and cold ends, nozzle sizes and materials, and find the best 3D printer cartridge for your needs.
The 3D printing process of can be briefly described as follows: a filament of plastic material is fed into a heated metal block with a nozzle, where it is melted and extruded in a given form. This path is repeated, gradually building up until a solid three-dimensional object is formed.
The entire business task of handling the material, melting it and exiting for printing takes place in a block called 3D printer extruder .
In this article, we will look at the main sections of the 3D printer extruder, the options and advantages of different styles of extruders, popular models on the market, as well as cartridge heaters for 3D printers and other items.
What is an extruder
3D printer extruder is a set of parts that together process and move the plastic filament.
Some consider the extruder to be just the motor and associated parts that push and pull the filament, others the entire assembly including the heated part that melts and deposits the filament.
For simplicity, this article treats the entire assembly as an extruder. To begin with, while explaining the key components of a 3D printer extruder, we will divide it into two elements: a cold zone and a hot zone.
Cold zone
As the name implies, the cold zone is exactly that - cold. This is the top of the 3D printer extruder system, where the filament is fed into and then passed into the hot zone to be melted and extruded onto the print bed.
The appearance and location of the cold zone on your 3D printer depends on whether it is a direct drive or Bowden drive extruder (both of which are detailed below).
There is no filament heating here. The cold zone consists of the extruder motor and gear train, which are usually mounted either on the printer frame or on the print head itself, depending on the type of extruder, and a PTFE tube to smoothly guide the filament into the hot end.
What happens in the cold zone?
With the heatsink removed on this e3D Titan Aero, we can see the inner workings of the 3D printer's extruder.
Essentially, the cold zone consists of a stepper motor, some form of gear, a toothed bolt or gear, a spring-loaded idler (usually a bearing of some kind) to hold the filament, and then a PTFE tube to guide the filament.
A humble stepper motor with a metal gear required for a 3D printer's extruder drives the filament extrusion in most if not all modern desktop 3D printers.
However, one stepper motor is not enough to feed the filament to the hot end. The parts attached to and operating the stepper motor drive shaft must physically grab the filament and push it on its way to the hot end.
In this cutaway view of a 3D printer extruder, we see a metal gear and a plastic gear with a toothed shaft.
This usually uses a combination of toothed gears and toothed bolts or shafts (in the image above we see a metal gear and a plastic gear with a toothed shaft) serving as a pressure wheel along with a bearing or other rigid frictionless material.
Here we see a plastic lever with an integrated bearing, an extension spring and a plastic gear with a toothed shaft. Together they apply pressure to the filament and force it through the extruder.
Alternatively, there are versions of the cold end of the 3D printer extruder that use a slightly different arrangement of parts to feed the filament. Such deviations are often claimed to provide increased traction and yarn delivery.
Here we see both sides of the Prusa i3 Mk3 cold end, including the Bondtech extruder gear train.
As mentioned, there are varieties of 3D printer extruder that use these parts in slightly different layouts. Each has its pros and cons. Next, we will look at what is the difference between a direct drive 3D printer extruder and a Bowden 3D printer.
Direct drive extruders
The Direct Drive 3D Printer Extruder is different in that it places the extruder motor directly above the heating unit. This arrangement minimizes the travel distance of the filament to the hot end and can enable more reliable 3D printing of flexible filaments.
The advantage of using direct drive is more precise retraction control. Due to the location directly above the hot end, there is less distance between the clamp and the thread passing through the thermal barrier into the heating block. Consequently, the filament has less room to bend and deform under pressure.
Bowden extruders
Bowden Style 3D Printer Extruder The does not mount directly on the top of the hot end like a direct drive 3D printer extruder, but the motor and gear assembly mounts on the frame of the printer. This gives this type of extruder an advantage over its head-mounted direct drive brother: speed.
By placing the mass of the 3D printer's extruder on the frame instead, the printhead is freed up to print at higher speeds without sacrificing print quality.
A side effect of placing the 3D printer's extruder this way is that the filament now has to travel a long way in a tube that's a fraction wider than it is. There should be enough room along the entire length of the tube for a slight bend in the thread. When pulling in the thread between strokes, this slack in the thread shortens the pull-in distance. Without correction (i.e., an increase in retraction), this results in a delay in relieving the pressure exerted on the hot end. In short, you can get confused if you don't change your retract settings.
Heating block (Hotend)
Inside the knot, known as the hot end, the filament passes into a heated chamber where it changes from solid to liquid. Sounds simple, and mostly it is. Although there is a lot more to make the filament silky extrude onto the build plate.
What happens in the heating zone?
The E3D Titan Aero combines a heating block and an extruder in one compact unit. The hot end usually only has the central parts of this image: the heatsink (and fan), the heating element (micro cartridge heater), the heater block, the thermistor, and the nozzle.
A typical 3D printer hotend consists of a specific sequence of parts. There is a slight difference depending on whether you are using PTFE/PEEK or a full metal hot end. Here we explain the all-metal hot block.
First, it is a filament supply tube. In both a Bowden 3D printer extruder and a direct drive extruder, it will just be a PTFE tube coming from your cold filament feeder.
You can sometimes find direct drive 3D printer extruders where the filament runs straight into the print head.
On a Bowden 3D printer's extruder, this feed tube inserts the filament directly into the thermal barrier via a heatsink. The thermal barrier that is screwed into the heatsink is often a threaded stainless steel (or other non-conductive metal such as titanium) tube.
Split in two (note the two separate threads in the image below - longer for the heatsink, shorter for the heater block) and machined on the inside, the thermal break allows the filament to pass freely into the extrusion nozzle.
Clockwise from bottom left: steel thermal barrier, aluminum heating block and brass nozzle.
But since we're dealing with precision and a material that liquefies for rapid recooling, the 's temperature management is critical. The thermal barrier, in combination with the heat sink, maintains a certain limit at which the filament is exposed to high temperatures.
The top, which is actively cooled by a heatsink and dedicated fan, prevents heat from escaping from the hot end and weakening the filament before it is where it needs to be for extrusion. This unwanted phenomenon is known as thermal creep.
The lower part of the thermal barrier is located inside the heater block together with the cartridge heater, the temperature switch thermistor and the nozzle.
The heater block, usually made of aluminum, ensures a smooth transition of the filament from the open end of the thermal break tube to the nozzle.
The temperature to melt the filament has to come from somewhere, and this is where the cartridge heater comes into play.