3D printer picture frame
3d Printed Frame - Etsy.de
Etsy is no longer supporting older versions of your web browser in order to ensure that user data remains secure. Please update to the latest version.
Take full advantage of our site features by enabling JavaScript.
Find something memorable, join a community doing good.
( 1,000+ relevant results, with Ads Sellers looking to grow their business and reach more interested buyers can use Etsy’s advertising platform to promote their items. You’ll see ad results based on factors like relevancy, and the amount sellers pay per click. Learn more. )
Neil Patrick Harris and 3D Printing Nerd Built Massive Picture Frames
In what’s quickly becoming our favorite YouTube collab, Neil Patrick Harris and Joel Telling – the 3D Printing Nerd – have teamed up yet again to work on a bespoke 3D printing project. Previously, NPH and Joel spent 87 days printing three 5’ x 4’ picture frames assembled from a ton of small parts for NPH’s house in the Hamptons. This time around, the duo used a Massivit 3D printer to print a couple of 6’ x 4’ frames in just a few days!
The last time around, the intricate ornamentation was quite a time-consuming process. The team needed to print tall edges, wide edges, and dozens of additional details, each of which required days or weeks to print.
While it’s obvious from the video that Joel and NPH had a blast doing the assembly, the protracted build time made the process less than ideal for projects moving forward.
Although desktop printers are awesome and people use them to create all kinds of cool projects, when you’re building something massive, it helps to have a massive printer, so Joel decided to use a Massivit 1800 printer to work on a new idea that Neil had for some interesting technological artwork.
Joel Knows Massivit Builds Bigger
Joel, the 3D Printing Nerd, is a pro at matching up machines with applications. He had previously met Massivit CEO Erez Zimerman at a 3D printing show, Formnext where he was blown away by how quickly Massivit 3D printers can build – 6 feet high in just 6 hours!
After the Formnext meeting, we gave Joel a closer look at how Massivit’s patented GDP (Gel Dispensed Printing) technology works and he made an awesome deep dive video demonstrating exactly how the 1800 Pro works in detail.
For his next project with Neil, it looked like this technology was just the ticket and they went back to making picture frames, but with a twist!
Frames in a Flash
Neil’s latest idea was to conjure up custom-made picture frames to fit his large tv screens, on which he could display unusual, Harry Potter-esque images of himself and his husband, creating a sort of optical illusion. When you first look at either one of them, they appear to be still photos, but if you watch them over time, you’ll notice they appear to move – because they actually do!
Instead of hundreds of pieces to assemble, the frames were printed in four parts each, two at a time. The taller edges of the frames (74.5”) took only 18.5 hours to print in parallel. The shorter top and bottom edges of the frames (49”) took 14 hours to print in parallel.
That’s a grand total of 32.5 hours of printing per frame, compared to nearly 700 hours per frame in the previous project – over 95% reduction in printing time, for frames that are even larger!
Printing for Pros
Daniels Woodland in Paso Robles, California, made this project possible by directly printing the intricate design on their Massivit 1800 Pro. And extremely quickly. This tech provided designers Garrett and Chelsey Kearney from the Chaos Core Tech channel nearly unlimited freedom to create custom architectural elements without requiring tons of post-processing time from artisans.
Not only that, with GDP technology, there’s virtually no wasted material in the form of elaborate support structures, so each frame was printed with about 16 kg (35 lbs) of gel.
The Chaos Core Tech team cleverly designed the frames to neatly hide the screens and at first glance, it’s nearly impossible to tell they are anything other than authentic, antique picture frames.
The printed pieces were post-processed to emulate the look and feel of brass, and the frames were distressed and finished by the artisans at Daniels Wood Land, before being delivered to Neil’s home.
The installed frames make for quite a statement in the entry to Neil’s home, and we’re so thrilled we could be a part of bringing Neil’s innovative vision to life!
What’s next for the 3D Printing Nerd and Neil Patrick Harris using Massivit 3D machines? We don’t know yet, but we’re already excited for whatever these two creators come up with. Subscribe to the Massivit 3D blog to make sure you don’t miss out!
Injection molding in 3D printed molds: a technical study from a leader in the plastics and composites industry
using 3D printed molds. This article summarizes some of the findings, particularly those related to Formlabs 3D printers.
Injection molding is an economical and highly reproducible technology
mass production of plastic parts with tight tolerances of
geometric dimensions. However, the high cost of traditional steel equipment makes it difficult to injection mold small batches of parts and can often be a barrier to new product introduction. By using 3D printed injection molds, engineers, fabricators and product designers can lower their costs, reduce lead times and bring better products to market. 3D printed injection molds are a great option for those who want to develop functional prototypes from end-use materials, produce a series of identical pre-production samples, or even custom or limited-edition end-use models.
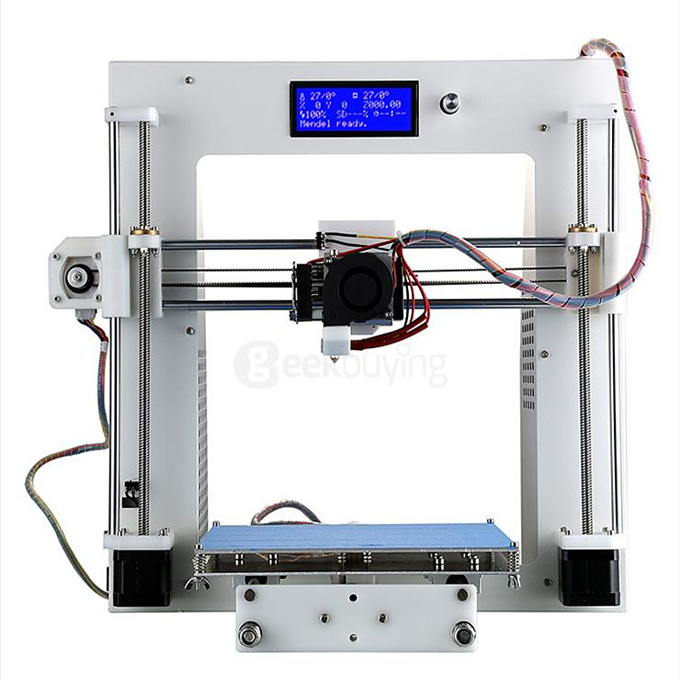
Checkpoints
The IPC study was divided into three stages:
1. Comparison of 3D printing technology: The first classification was based on the technical data of several manufacturers. The thermal and mechanical characteristics were evaluated, respectively, in terms of deformation heat resistance (HDT) and tensile modulus. To select the three most promising materials for each of the identified technologies, four types of control points were developed to highlight critical properties. Due to the high resolution and smooth surface of the 3D printable models, resin-based solutions have been recognized as the best material choice for injection molding molds.
In general, a similar range of dimensional variation is measured for all considered 3D printing technologies: from ± 0.02 mm to ± 0.05 mm for small parts and from ± 0.05 mm to ± 0.2 mm for large parts.
The standard accuracy of machined metal tools shall be ± 0.02 mm. This accuracy is desirable for a good fit along the parting line and to prevent reflow. IPC offers two methods for optimizing the parting line of a 3D printed resin tool.
2. Recommendations for material characterization, design and 3D printing.
3. Injection molding test: IPC conducted two tests with different sets of molds. The first test used an "extreme test" design. Nearly a hundred polypropylene models were cast using a mono-material mold printed in High Temp Resin. The second test used a more complex "extreme test" scheme. Thousands of polypropylene models were molded using a mold of different materials: the core and mold inserts were printed from Rigid 10K Resin, and the frame was printed from Nylon 12 (Polyamide 12) using selective laser sintering technology.
Mold design materials with inserts (Fig. 2).
IPC has developed two sets of molds for casting two different complex patterns. Both sets were designed to optimize the quality of the parting line:
both halves of the tool must be positioned with a tolerance of ± 0.

1. Monomaterial mold printed in High Temp Resin.
It has a simple geometry with no inserts or additional moving parts, includes texturing. To improve the parting line, it will be redesigned in the final stage.
Monomaterial STL file printed with High Temp Resin and loaded into PreForm software. Fixed side (left) and movable side (right).
2. Multi-material mold: The fixed side of the mold is printed with Rigid 10K Resin and includes texturing. The moving side consists of one core and four inserts printed in Rigid 10K Resin,
and a frame printed in Nylon 12 (Polyamide 12) using selective laser sintering (SLS) technology. The soft frame is equipped with an insert to compensate for dimensional deviations from the parting line. Nylon 12 (Polyamide 12) is flexible enough to accommodate size variation during mold clamping. However, selective laser sintering should only be used to print the frame and not the entire plate, because it does not provide high enough resolution for the shaping surfaces, and the plate melts at high temperatures.
Multi-material STL files loaded into PreForm print preparation software: fixed side (left) and movable side, core and inserts (right) printed with Rigid 10K Resin.
This geometry is slightly more complex and is designed to test the stability of thin inlays. To simplify the assembly, the angle of inclination between the core and the frame is three degrees. The frame was made with a 0.05mm allowance for a better fit.
Nylon 12 (Polyamide 12) frame CAD design for multi-material movable mold side.
Shape CAD file, textures look the same with both toolboxes. From left to right: (1) Large sphere with a radius of 1.82 mm and a height of 0.3 mm; a small sphere with a radius of 1.09 mm and a height of 0.3 mm. (2) Wood 0.25 mm high. (3) Pyramid with a side of 0.3 mm and a depth of 0.2 mm. (4) Skin height 0.14 mm.
Design Guides
After several revisions, IPC recommends using the following best practices:
- Plan an allowance for the printed form and process it to adjust the dimensions.
- Avoid small cross-section cores: parts with a smaller cross-section may not withstand pressure and temperature. IPC recommends printing multiple inserts for thin protruding parts (they can be replaced in case of failure) or making small metal parts.
- Fabrication of structures larger than 400 mm can be challenging. Since the parameters increase with size, it will be more difficult to match the shape.
- Increase pitch and overhang angles (10° to 20°) to avoid deformation.
- Do not integrate cooling channels into the mold design. Heat transfer in plastic models is slower than in metal models, so the cooling channels will not have enough effect on temperature to compensate for the time spent designing this system. When complex materials or designs are used, regulation may be useful, but this is for further study.
3D Printed Molds
3D Printable Resin
Forms were printed on a Form 3 3D Printer and post-processed on a Form Wash and Form Cure. IPC printed two different sets of molds:
°C and thermal final cured for three hours at 160°C. This material has a HDT of 238°C at 0.45 MPa, the highest among Formlabs resins and one of the highest among resins on the market. These characteristics allow it to withstand high injection molding temperatures with minimal cooling time.
2. Rigid 10K Resin core and mold inserts, printed at 50 µm layer height, rinsed twice in isopropyl alcohol for 10 minutes, finalized for 60 minutes at 70°C, and thermally finalized at 70°C. for 90 minutes at 125°C to achieve higher deformation heat resistance. This polymer is an industrial material with a high glass content - ideal for
casting in a wide variety of geometries and injection molding process conditions. Rigid 10K Resin has a deformation heat resistance of 218° C at 0.45 MPa
and a tensile modulus of 10,000 MPa. These characteristics make this polymer a strong, extremely rigid and thermally stable molding material that retains its shape under pressure and temperature for precision models. The mold frame was printed from Nylon 12 (Polyamide 12) using SLS selective laser sintering technology.
3D Printing Manual
After several revisions, IPC recommends the following best practices for 3D printing:
- Print with Rigid 10K Resin for extended plate life.
- Use a low layer height for better resolution: SLA 3D printing provides very fine texturing.
- Whenever possible, print the plate without supporting structures to achieve greater dimensional accuracy and avoid distortion.
- Orient the mold so that there are no protrusions.
Mold printed with Rigid 10K Resin, fixed side on build platform
- If possible, print both halves aligned with the assembly direction. Possible size variations can improve the compatibility and quality of the parting line.
- Machining after 3D printing the mold. In particular, adjust the parting line so that both halves of the mold match each other and do not melt.
The diameter has a risk of deformation, so drilling a hole may be required.
Mold printed textures in Rigid 10K Resin.
Scan Metrology
IPC scanned the plates to evaluate dimensional change immediately after printing and after final curing. These scanned images show less than ±0.05 mm deviation for over 75% of the details.
- 1. High Temp Resin. Scans of a 3D printed High Temp Resin mold: movable side (left) and fixed side (right).
- 2. Rigid 10K Resin. Scans of a 3D printed Rigid 10K Resin plate: movable side (left) and fixed side (right).
Injection molding
Mold assembly
As mentioned above, it is recommended that the 3D printed mold be machined before assembly to ensure critical dimensions are met. However, the multi-material mold did not need to be machined as the soft Nylon 12 (Polyamide 12) parting line is able to absorb dimensional changes. You can then add push pins or inserts. IPC recommends printing several inserts for thin models with protrusions that are at increased risk of breakage: in this case, they are easy to replace. Mold handling and assembly are operations that require care as 3D printed parts can break during processing. 3D printed molds should be placed in a metal die or master mold to withstand the pressure.
Form printed in Rigid 10K Resin and mounted in a metal matrix. Moving side with ejector pins (left) and fixed side (right).
Form printed in Rigid 10K Resin and mounted in a metal matrix. Movable side with ejector pins, inserts, SLS bezel (left) and fixed side (right).
Injection molding process conditions
The team has cast thousands of models under the following injection molding conditions:
- Injection molding machine: industrial, ENGEL 150T
- Injection molding material: polypropylene (PP)
- Injection molding temperature: 200° C
- Casting pressure: 180 bar
- Mold clamping force: 125 kN
- Release Agent: None
- Cooling system: none.
The temperature was controlled by a thermal imaging camera and the cycle only started when the plate temperature was below 36°C
- Ejection: automatic with ejection pins and robotic arm designed to move the part
- Cycle time: 150 sec.
Results
IPC cast 90 polypropylene models in a monomaterial mold printed in High Temp Resin.
The cast models were characterized by high surface quality and detail. However, after 31 iterations, the mold began to crack, which affected the surface quality of the remaining cast models.
Model #31 (left) and model #90 (right) molded from High Temp Resin.
High Temp Resin mold after 90 castings.
IPC molded 1000 polypropylene models using a multi-material mold printed with Rigid 10K Resin.
The cast models were characterized by high surface quality and detail. There were light fusions after the first castings and small cracks around the core clamps after 900 castings. Lightening appeared at the place where the sprue was supplied.
Light reflow on last model (left) and small cracks after 900 castings on Rigid 10K Resin core.
Textures on finished models molded in multiple materials.
IPC recommends choosing Rigid 10K Resin to maintain shape durability.
This polymer is less brittle and exhibits better load strength than
High Temp Resin. The 3D printed mold should be processed to improve parting line accuracy and reduce flashover. Using a multi-material soft-framed mold is a great alternative solution for compensating for dimensional variations. IPC anticipates that the injection molding process will be more challenging when dealing with viscous materials such as polycarbonate (PC),
and molding temperatures above 240°C.
small volumes. With a mold core printed in Formlabs Rigid 10K Resin and a soft border printed in PA-12, thousands of polypropylene parts were molded, reducing printing costs by 80-90% compared to using a metal mold.
Desktop 3D printing is a powerful solution for making injection molds quickly and inexpensively. It requires a limited amount of equipment, which reduces the time of the CNC and skilled operators and frees them up for other important tasks. Desktop 3D printing is easy to integrate into any injection molding workflow as it is easy to install, operate and maintain. Manufacturers will benefit from the speed and flexibility of in-house 3D printing to create a mold and combine it with the power of industrial injection molding.
As a result, it will be possible to manufacture a series of product items from conventional thermoplastics in a matter of days.
Design measurement: 14 3D printed items
- Forbes Life
- Alisa Kornilova-Rivkind Author
3D printed designer items available for purchase now
In April 2014, the architect and designer Philippe Starck launched an online store where anyone can choose a template and modify the appearance of interior items, and then print the thing on a 3D printer. Stark expressed his confidence that the 3D printer will completely change the way we look at design: stores will turn into open creative platforms where customers can produce unique products.
The market for 3D printed items and self-printing instructions is growing daily. Online retailers have emerged that specialize in 3D printing for everything from furniture and musical instruments to shoes and desserts.
Forbes has selected 14 3D printed designer items available for purchase right now.
Jewelry pendants collection Chestahedron
Californian architect Frank Chester promotes "freedom from freedom of creativity" - the rejection of both a superficially objective and purely subjective approach to art in favor of discovering the original "spiritual" forms in nature. For a long time studying biomorphic structures and Platonic solids (regular polyhedra with spatial symmetry), he discovered a new geometric figure - heptahedron chestaghedron. Subsequently, it turned out that his heptahedron exactly corresponds to the configuration and internal structure of the human heart. A series of pendants with chestahedrons made of metal alloys, bronze and silver was released in June 2014 using 3D printing as a progressive version of the usual heart pendants, introducing new knowledge and technologies.
Price: $69 to $299
Soda sunglasses
Multi-coloured bioplastic Soda sunglasses demonstrate a new way of interacting with the consumer, offering a choice of ready-made glasses and separate frames with temples - 4 shapes and 22 colors in any combination (plus universal dark lenses). With glasses, the buyer receives instructions for self-3D printing of the frame and its subsequent assembly. The store takes on the feel of a workshop—the site includes a video of a printer being printed and a link to an updated moodboard of things and looks that inspire Soda designers, from gummy bears and car concepts to sneaker ads and silent movie frames.
Price: €39.99
Slow food bowl for cat food
Dutch Monique de Wilt designed a slow feeding device for one of her cats, who always tries to swallow a portion of wet food as quickly as possible and suffers from nausea afterwards. A ceramic lid with holes in the shape of a cat's paw makes you extract and eat each piece individually.
Price: €31.37
Nooka watch with PU bracelets
A limited edition of 12 unisex sports watches by the American brand Nooka with lightweight polyurethane bracelets created by laser cutting and 3D printing. For each of the dials, you can pick up three types of bracelets - "Trillion", "Honeycomb" or "Waves".
Price: $99-139
Elvis Pompilio & MGX fedora hat
A sophisticated version of the classic fedora hat in white polyamide by famed Belgian hat maker Elvis Pompilio, who has worked with Christian Dior and Valentino. The 3D fedora is distinguished from straw prototypes by its refined weaving pattern and noticeably less weight.
Price: €496
Case for iPhone 5\5S
Cases for digital gadgets are the simplest and most popular things created using household 3D printing. Among the countless shell options for the latest iPhone, you'll find a durable, polished polyamide case with a retro spinning dial that mimics the mechanics of older phones.
Price: €13. 95
Wine bottle decoration Inter Culture
Openwork "shoulder" made of white polyamide for bottles on the festive table from Tokyo-based brand Inter Culture. There are four shapes and sizes to choose from: Moët & Chandon, Dom Pérignon, traditional Bordeaux and Burgundy.
Price: €49.01
Vertigo Polka bag
Vertigo Polka is a brand of designer accessories from Illinois. Its founder, Robert Drummond, has specialized exclusively in 3D printing for the past four years. Small interior ceramics, bags and a large selection of jewelry made from a variety of materials, from nylon thread to silver and gilded brass, made the brand famous. One of the novelties is a miniature women's satchel bag, an actual model in the spirit of glam-sport and futurism, made of flexible polyamide mesh with a grainy matte surface that is pleasant to the touch and an optional chain length over the shoulder.
Price: €117
Eragatory Gold Plated Cutlery
Founder of the Belgian-British brand Eragatory Isai Bloch believes that 3D printing has a special potential, allowing you to find a balance between pure art and applied tasks. For example, to make gilded cutlery ergonomic, respectable and link together traditional etiquette, the decline of baroque luxury and associations with instruments of torture. The creators emphasize that all Eragatory items must be produced only on a 3D printer.
Price: from €140 to €250 per item
Table and floor lamps
Lamp shades are one of the popular options for experimenting with 3D printing. The simplest are varieties of openwork and mesh designs. The Dazzle Lamp series, designed by Belgian architect and programmer Cornel Cannaerts, takes a far more sophisticated approach, using Z Corp's most advanced color printer capable of transmitting 390,000 unique colors and hundreds of thousands of possible combinations. The desired range of shades can be borrowed from any image and transferred in the form of a mosaic pattern to the inside of the lampshade. When the light is on, the gray-white lampshades on the outside become colored.
Price: on request, individually for each luminaire
Leather and bioplastic ankle boots Bryan Oknyansky
British designer Brian Oknyansky plans to change the fashion shoe market with a development that allows custom-made pairs to be stamped. Trial model - open ankle boots with a lace-up top made of genuine leather and a massive bioplastic base.
The colors of the three printed parts - sole, 15 cm heel and platform - can be freely combined from a ten-color palette. Bulky-looking shoes are light and comfortable: the height of the heel is compensated by the height of the platform, and an ergonomic soft insole is built between the bioplastic and the foot. An architect by training, Oknyansky also custom-designs futuristic footwear made from leather and titanium alloys, using 3D technologies from the fields of space aviation and automotive. In the 2013/2014 season, the designer was nominated for several UK professional fashion and technology awards.
Price: £400
Set of five stools
Janne Kyttanen's five stackable Monarh stools provide an alternative to wicker furniture. The advantages are low weight, mobility and a beautiful lattice structure, complemented by silhouettes of butterflies.
Price: $9466
Electric guitar
The first and so far unique series of electric guitars Scarab (Scarab), created by music lover and 3D printing enthusiast Olaf Diegel. The designer invites buyers to become co-authors and create their own kind of guitar body using his designs.