3D printed cubesat
3D printing CubeSat bodies for cheaper, faster missions
Enabling & Support22/05/2017 13560 views 52 likes
As a first test of a new printable hard, electrically conductive plastic, ESA has 3D-printed CubeSat structures incorporating their own electrical lines. In future, such miniature satellites could be ready to go once their instruments, circuit boards and solar panels were slotted in.
“We’ve been looking into 3D printing using ‘polyether ether ketone’ – or PEEK,” explains ESA’s Ugo Lafont.
“PEEK is a thermoplastic with very good intrinsic properties in terms of strength, stability and temperature resistance, with a melting point up around 350ºC. PEEK is so robust that it can do comparable jobs to some metal parts.
“We started a project with Portuguese company PIEP and, in a technical first, we made this printable PEEK electrically conductive by adding certain nano-fillers to the material.
CubeSats orbiting Earth“This kind of customising has taken place for as long as the plastic industry has existed. Plastic has been mixed with different materials to tailor their properties as desired, to make them more resistant for instance, or shinier. In this instance, this ‘doped’ PEEK filament can now be used as a standard feedstock in our 3D printing process.”
As a demonstration of this breakthrough, Ugo and intern Stefan Siarov from TU Delft in the Netherlands decided to print bodies for CubeSats.
These are cheap nanosatellites literally in a box: they are based on rugged, stackable electronic boards housed in one or more standardised 10 cm units. First developed as educational tools, CubeSats are increasingly being put to active uses in orbit.
Electrical lines in CubeSat body“The resulting PEEK CubeSat structures would be capable of flying in space,” comments Stefan. “But these bodies are also functional, because they incorporate electrically conductive lines in place of the wire harness normally connecting up the different CubeSat subsystems. ”
As a next step, the Materials’ Physics & Chemistry team is collaborating with ESA’s Directorate of Human Spaceflight and Robotic Exploration on a space-optimised PEEK printer for initial testing on ‘zero-g’ aircraft flights, then eventually at the service of astronauts on the International Space Station.
“The vision we have to enable a new maintenance strategy,” adds Ugo. “Rather than just making toys with no added value, PEEK and comparable thermoplastics are robust enough to find a lot of practical uses, plus the added option of electrical functionality.
PEEK-printed test part“Space Station crews end up needing all kinds of items, all of which currently require transport from Earth: everything from screws and water valves to hermetic containers and water valves. All of these could be 3D-printed instead – even toothbrushes – since PEEK is biocompatible.
“3D-printing such items in orbit would be cheaper, and would change the equation of recyclability. Because these plastic items can later be recycled, we reduce the scarcity of materials in space and start to make human missions to space more self-sustaining.”
Stefan meanwhile is now assessing the recyclability of other 3D-printed engineering thermoplastics at ESA’s European Astronaut Centre in Cologne, Germany.
“We have been taking a continuing interest into high-performance thermoplastic materials over the last decade,” comments Christopher Semprimoschnig, heading ESA’s Materials’ Physics and Chemistry Section. “The freedom that new processing options such as 3D printing offer are especially intriguing for ESA.”
Reflecting the relative maturity of this 3D-printed material, a small PEEK-printed structural part is due to fly on the Meteosat Third Generation series of weather satellites at the end of this decade.
3D printing in hard plastic
Thank you for liking
You have already liked this page, you can only like it once!
3D printed 3U demonstrator, space-ready CubeSat
In Short
Application
3U technological demonstrator Cubesat
Solution
Selective Laser Sintering and Windform® XT 2.
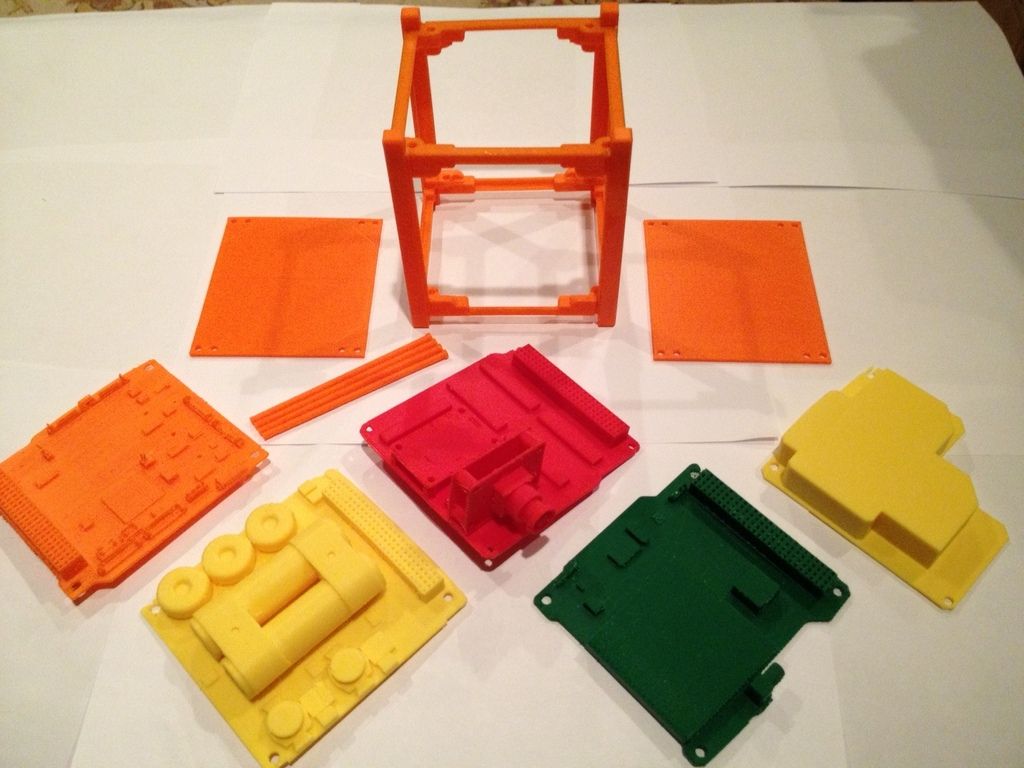
Challenge
Manufacturing a 3U CubeSat formfactor that withstands the design and launch-pad requirements in terms of dimension, flatness and roughness, mass optimization, internal parts integration, but also for outgassing, UV resistance, thermal expansion, and overall space constraint.
Features of the application
Field tested required
Fulfillment outgassing criteria
Functional component
High mechanical performances
Lightweight
Resistant to thermal vacuum test
Space/flight ready
Customer's requests
Highly customizable
Maintaining high-end user quality standards
Minimized production speed
No tooling cost
Reduced time to market
Remarkable accuracy
Services supplied
Complete engineering assistance
Suggestions for overcoming critical application consultancy
Technology and material selection
Testing
back to full version
back to full version
request a quote
request a quote
3D printed 3U CubeSat structure via laser sintering technology using Windform© XT 2.
jump to in short version
jump to in short version
Space industry has been revolutionized by the ever-increasing production and launch of small satellites.
Additive manufacturing technologies not only helped this radical change to be fulfilled, but have itself reached new heights with the manufacture of structural components for the new generation of Space parts using high performance composite materials.
Although much still must be done to reach an extensive use of additive manufacturing for Space applications, CRP Technology’s built a considerable experience supplying cutting-edge solutions for space key industry leaders. A clear and remarkable example comes from the experience with LISA.
The Italian-based company specialist for over 25 years in the use and development of advanced additive manufacturing technologies and materials, collaborated with the Laboratoire InterUniversitaire des Système Atmosphérique (LISA) of Universite Paris-est Creteil (UPEC) on the construction of a nano-satellite that is a 3U CubeSat formfactor.
The project was carried by students under CNES and Space Campus University supervision.
The goal was to develop a demonstrator that can be flight-ready in Low Earth Orbit.
The engineering team at LISA and CNES decided to rely on CRP Technology and its Windform® TOP-LINE family of high performance materials for the manufacturing of the nano-satellite.
The project manager at LISA, commented, “Using such a process and composite material from Windform’s® TOP-LINE, we knew for sure we would be able to design the structure exactly the way we needed it.”
The structure had to survive vibration tests (to endure the launch) and thermal-vacuum tests. It had also to withstand outgassing requirements.
“The design has been done taking into account all of these constraints – the project manager at LISA added – . CRP Technology’s support was crucial to achieve our aims. Their Windform® TOP-LINE materials and additive manufacturing/Powder Bed Fusion process with composite polymers fibers-reinforced allowed us to reduce mass and optimize the way to integrate parts inside the CubeSat.
CubeSat Structure is critical as it has to fulfill the launch-pad (P-Pod) requirements in terms of dimension, flatness and roughness, but also for outgassing, UV resistance, thermal expansion, and general space constraints.
Plus, if it breaks, or stays stuck in the P-pod launcher, the mission is over.
The assignment was tough, but thanks to the long-term experience gained in the field of additive manufacturing service alongside the key leaders of the most advanced industrial sectors CRP Technology accepted the challenge.
The activity of CRP Technology’s 3D Printing department has been focused from the beginning on maximizing and achieving the targets required, providing full collaboration to the team at LISA.
Work began with an accurate analysis of the 3D and 2D files: through their long-standing technological expertise, CRP Technology suggested alterations that made it possible to optimize the geometries of the parts, reaching the required target in terms of mass optimization and part integration.
3U-CubeSat OGMS-SA (OutGassing Material Study by Spectroscopy Analysis) with solar panels and antennas deployed – courtesy of LISAThrough the know-how earned in over 25 years of activity serving the most demanding and high-performance industrial sectors, CRP Technology has been able to assist LISA and CNES in choosing the best technology and material to guarantee the success of the project: PBF selective laser sintering and Windform® XT 2.0 Carbon composite material.
Windform® XT 2.0 replaces the previous formula of Windform® XT in the Windform® TOP-LINE family of composite materials.
Windform® XT 2.0 features improvements in mechanical properties including +8% increase in tensile strength, +22% in tensile modulus, and a +46% increase in elongation at break. These mechanical properties have guaranteed the achievement of the required characteristics, i.e. stiffness, low mass as well as very smooth surface finish.
Once received the .STP file with optimized geometries from LISA, CRP Technology created in a short time the functional 3D printed component (the nano-satellite structure) via selective laser sintering using Windform® XT 2.0.
PBF Professional 3D printing, combined with Windform® XT 2.0 Carbon-composite material, proved to be the best choice: the 3D printed part has successfully passed the control and testing criteria, and has fully complied with the requests and LISA’s standards.
LISA and CNES performed many tests on the 3d printed nano-satellite structure such as vibration tests and thermal-vacuum tests. They were very satisfied with the results obtained.
Thanks to CRP’s laser sintering technology and Windform® XT 2.0 Carbon-reinforced composite material, we obtained very important key advantages such as mass reduction, component integration, outgassing control, thermal expansion, and low surface roughness. We are more than satisfied with selective laser sintering technique Powder Bed Fusion process and consider Windform® XT 2.0 one of the disruptive revolutions in the small satellites arena. We do hope to use additive manufacturing intensively in space application
LISA team
Payload inside the structure – courtesy of LISAPayload inside the structure – courtesy of LISAAntenna frame integrated in the 3D printed structure – courtesy of LISA3U CubeSat internal view – courtesy of LISAThermo-vacuum chamber for the CubeSat TVAC - courtesy of LISAPrevious
Next
European Space Agency starts testing printed CubeSat satellites / 3d printing / 3Dmag.org
The European Space Agency has launched a new initiative to 3D print CubeSat enclosures in rigid electrically conductive plastic. With the start of the first test run, ESA's goal is to get these miniature satellites (1 liter volume and weight no more than 1. 33 kg), ready for future use, complete with internal electrical lines, while tools, printed circuit boards and solar panels should simply insert inside.
With a focus on polyester ketone (or PEEK), ESA hopes for a brighter future. “PEEK is a thermoplastic with very good properties in terms of strength, stability and heat resistance, with a melting point of around 370º C. PEEK is so strong that it can perform jobs comparable to some metal parts,” explains space materials and technology specialist Ugo Lafont.
Together with the Portuguese engineers of the company PIEP, the guys from the agency created PEEK, which is electrically conductive. For the initial demonstration, Lafont and Stefan Siarov of Delphi University of Technology printed cases for CubeSats, cheap satellites based on industrial template electronic circuit boards housed in standard 10cm boxes. These specialized CubeSats include electrical wires instead of wire harnesses commonly used to connect various subsystems, saving not only time but space.
As Lafont was quick to point out, CubeSats are just the beginning. The next steps involve a new collaboration between ESA and the Materials Physics & Chemistry team to develop a space-based PEEK-based 3D printer whose initial zero-gravity testing will take place on aircraft. Ultimately, the device will serve astronauts on the ISS.
Related entries:
-
hedin
3d printers → Space 3D metal printer 0 -
hedin
3d printing → Building housing on Mars 0 -
hedin
3d printing → Tardigrade - moon bike 0 -
hedin
3d printers → Portable bioprinter for space 0 -
hedin
3d printers → 3D printer on the ISS got the ability to print from PEI / PC 0
Only registered and authorized users can leave comments.
The first 3D-printed nanosatellite will broadcast from the ISS in 11 languages
← Back Home → News→ May 10, 2016
The first 3D-printed nanosatellite will start broadcasting from the ISS in 11 languages0006 May 10, AEX. "It will work today at 9:00 GMT (12:00 Moscow time). Anyone on Earth who is in the ISS visibility zone will be able to receive a signal in the amateur radio frequency range," Yakovlev explained. The device will broadcast on the frequencies of 145.8 MHz and 437.025 MHz congratulations for the inhabitants of the Earth in 11 languages - Russian, English, German, French, Portuguese, Chinese, Arabic, Tatar, Hindi, Kazakh and Spanish. A message in honor of the 12th anniversary of the university was written by students of Tomsk Polytechnic University. The interlocutor said that the satellite was turned on on board the station and tested on May 5th. The "Tomsk-TPU-120" satellite, created by scientists from TPU, the Institute of Strength Physics and Materials Science of the Siberian Branch of the Russian Academy of Sciences and RSC Energia, is the first Russian spacecraft manufactured using 3D technologies. The term of his work in space is about six months. It was sent to the ISS on March 31 on the Progress MS-02 cargo spacecraft. TPU reported that after launching into space, various sensors of the satellite will record the temperature on board, on boards and batteries, and the parameters of electronic components. Based on this data, scientists will be able to analyze the state of materials and decide whether they will be used in the construction of spacecraft in the future. |