3D printed brick house
10 best 3D-Printed houses around the world
© wavyThe evolution of building materials has been quite an eventful journey. Across history and civilizations, new building materials have made their mark. This transition has resulted in immense possibilities, from using hay, tree barks, stone, timber, brick, mortar, or glass and steel. Materials have a great influence on the experiential quality of a space. In this process, different materials started to use in 3d printers. Today, we can create 3D-printed houses by using these technologies. Different materials provide a different range of thermal and acoustic comfort. Materials also vary based on the region and the specific climatic conditions. The variations in building materials thus strengthen the thought that “Change is the only constant”.
© Sika Sikacrete® 3DFor instance, the brick alone has undergone multiple evolutions. It has evolved from clay and sand bricks to fly ash bricks, hollow wooden bricks, etc. Thus, the genre of materials is very deep. Moreover, technological innovations have led to unconventional techniques and materials. This not only reduces the environmental impact but also increases the life span and strength of the building. This includes using materials like Bamboo, Reclaimed Wood, Recyclable Waste, Bitumen Materials, Tempered Glass, Crumb Rubber, etc. This list also includes new-age materials like Fiber Reinforced Polymer, Glass Fiber Reinforced Plastics, Bamboo reinforced plastics, etc. But 3D printed houses are the latest and most jaw-dropping innovation of the current times.
Yes, this is not just a technological marvel in the AEC industry but also the printing technology. But what has made 3D printing a new trend in the AEC industry?
Let’s have a glance.
How is 3D Printing Technology Growing in the AEC Industry?
© news aktuell via AP ImagesA construction 3D printer employs a machine that builds houses by stacking the building material. This type of construction is termed “Construction 4.0”. In this technique, a paste material ejected through a tube. This includes materials like concrete or earth stacked in layers, thus creating a spatial volume.
This technology helps save time, effort, and material compared to traditional construction methods. But, 3D printing limited to the printing of walls and frames. Later, systems like windows, plumbing, etc., are conventionally installed. Despite these limitations, the technology is gaining traction owing to the minimal time required by the technology. This eliminates the time spent setting deep foundations, concrete settings, and other time-consuming methods involved in traditional constructions.
3D Printed Homes Across the Globe
Now that we have seen the potential of 3D printing in architecture and the advantages of 3D-printed construction, let us check out some 3D-printed homes that have pivoted the idea of housing technology worldwide.
Here’s an insightful list:
1.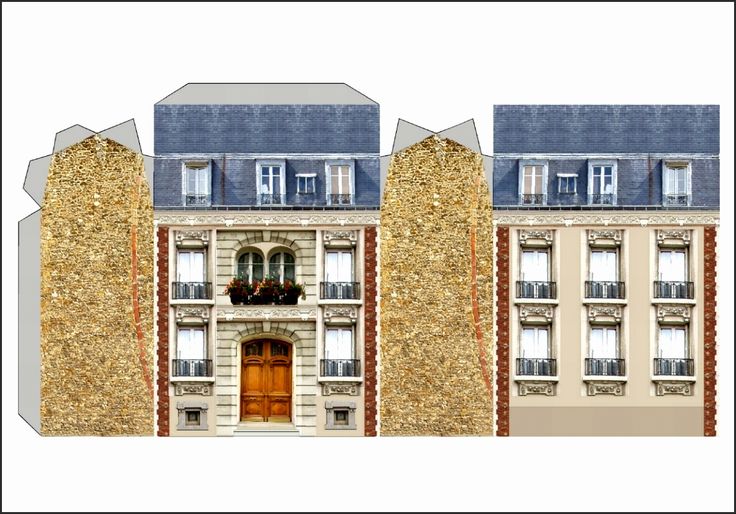
This marvelous cabin structure was designed by DUS Architects using sustainable bio-plastics and is located in the Netherlands. Bio-plastic used as a core material to print and construct this 8 sq. meter. Micro cabin, a form of additive manufacturing typically used in household 3D printers, to create its geometric walls. The Bio-plastic can be easily recycled and repeatedly reprinted. Using this method makes this project environment-friendly in the true sense. The use of black material renders this micro cabin with a customizable and ornamental facade. This cutting-edge design show how it is strategically conceptualized to induce form optimization.
Moreover, bioplastic makes the micro cabin naturally insulated, eliminating the need for mechanical ventilation. This also highlights the innovation in materiality and energy consumption. The modular interiors also feature a plush 3D-printed bathtub, whereas the porch and steps in concrete open up the cabin into the park. Thus, creating an aesthetic transition between the built and the unbuilt.
In collaboration with 3D-printing specialists WASP, Italy-based studio Mario Cucinella Architects has developed this low-carbon impact housing prototype, which goes by the name Tecla. A spatial enclosure formed by two connected domes with a total area of about 60-square-meters. The large skylight at the top of each dome allows light to penetrate the space from the top, making the space well-lit naturally.
The combination of modern technology, locally-sourced clay as the building material, and the multileveled 3D printer showcases the intersection of functionality and aesthetics.
Two-Story Detached House is the first-ever 3D-printed house in Germany. It has a two-storied structure with approximately 860 sq. ft of habitable space per floor. This project is being built using the 3D printer called BOD2. It pioneered by Danish manufacturer COBOD. The key feature of this machine is that it facilitates the addition of pipes and other internal building service components while the printing is underway. Moreover, it can print up to 10 sq. ft of double-skin wall in a magical span of just 5 minutes.
Read more What is Concrete 3D Printing?
4. Project Milestone© 3dprintingmedia.networkDesigned as part of a design development that aims to be the world’s first 3D-printed rental property, this structure has become the first lived-in 3D-printed home in Europe.
This boulder-shaped home was designed by Studio Houben & Van Mierlo. It was developed as part of a research project with the Eindhoven University of Technology. The whole construction process has been a new learning experience, thereby broadening knowledge around the production of 3D-printed homes.
5. Gaia© 3dwaspPrinted using a mixture of local soil, chopped straw, and rice husks obtained from rice waste production. This 30-square-meter house is situated in Italy and was constructed by WASP.
A unique amalgamation of 3D printing technology and traditional construction method can be seen here, where the structural walls are printed from the soil. At the same time, the cavities are filled with rice waste for better insulation. Rice husks are also being used in the interior to cover the walls and ceiling of the house as a form of natural plaster.
This inspirational design proves that agricultural waste could become a major construction and 3D printing resource, making this process sustainable.
East 17th Street Residences are designed to withstand extreme weather conditions in the US.
The construction was accomplished in 7 days. This includes a configuration of two-, three- and four-bedroom residences. So far, these cement-based homes have withstood an earthquake of magnitude 7.4 and severe winter storms. This shows how 3D printing construction is reliable and can withstand environmental disasters.
Casa Covina was designed as a design experiment in the San Luis Valley. The structure is formed by the interconnection of three cylindrical volumes or vaulted structures.
The hut was conceptualized to facilitate the co-existence of two individuals considering the coronavirus-led social distancing and isolation requirements. The adobe walls of Casa Covina are built using sand, silt, clay, and water are used to build. The structure is printed using a three-axis Selective Compliance Articulated Robot Arm.
The key highlight here is an inflatable pink roof which can be erected if it rains or snows. This great example of combining modern and ancient technology to create sustainable habitable solutions.
This two-storied house in Belgium is one of the first 3D-printed houses as one piece. Located in Westerlo, this home is eight meters tall and has a floor area of 90-sq. meters. The structure showcases the enhanced potential of 3D printing technology.
Designed as a low-energy consumption home, the design integrates energy-efficient provisions like ceiling and underfloor heating, solar panels, and a heat pump.
PassivDom House is probably among the most sustainable and energy-efficient 3D-printed houses. The entire house is designed to harness solar power. Whereas, from the moisture in the air, water generation is accomplished. This acts as an add-on facility. Built using a huge 3D printer in a factory in Nevada, PassivDom House is a perfect example of futuristic housing.
Furthermore, to clean and recycle water, the bathroom is designed technologically powered. Designed to use as few resources as possible, the house is ‘Off-grid’ in the true sense.
10. Curve Appeal© watgCurve Appeal is a dynamic 3D-printed house built from 3D-printed plastic, carbon-fiber panels, and glazed walls. The free-flowing forms and the parametric facade inculcates this structure with incredibly bold imagery compared to the other 3D-printed homes in the world. WATG designs this 1,000-square-foot residence. This structure printed using Branch Tecnchology’s freeform process and is the first of its kind. The dynamic curved facade is aesthetic and designed with optimum structural stability. The glazed facade lets light into the interiors, making the space naturally -lit. Moreover, the use of glass as a facade also induces a sense of transparency, merging the indoors with the outdoors. The entire structure is known for its net-zero energy.
The path-breaking revolutionary construction techniques coupled with innovative technologies such as solar carving and passive mechanical systems thus make Curve Appeal futuristic in the true sense.
Learn about parametric and computational from the online courses at the PAACADEMY:
3d Printed Brick - Etsy.de
Etsy is no longer supporting older versions of your web browser in order to ensure that user data remains secure. Please update to the latest version.
Take full advantage of our site features by enabling JavaScript.
Find something memorable, join a community doing good.
( 745 relevant results, with Ads Sellers looking to grow their business and reach more interested buyers can use Etsy’s advertising platform to promote their items. You’ll see ad results based on factors like relevancy, and the amount sellers pay per click. Learn more. )
Construction 3D printing is waiting for a breakthrough The first construction projects using this technology appeared only in 2014.
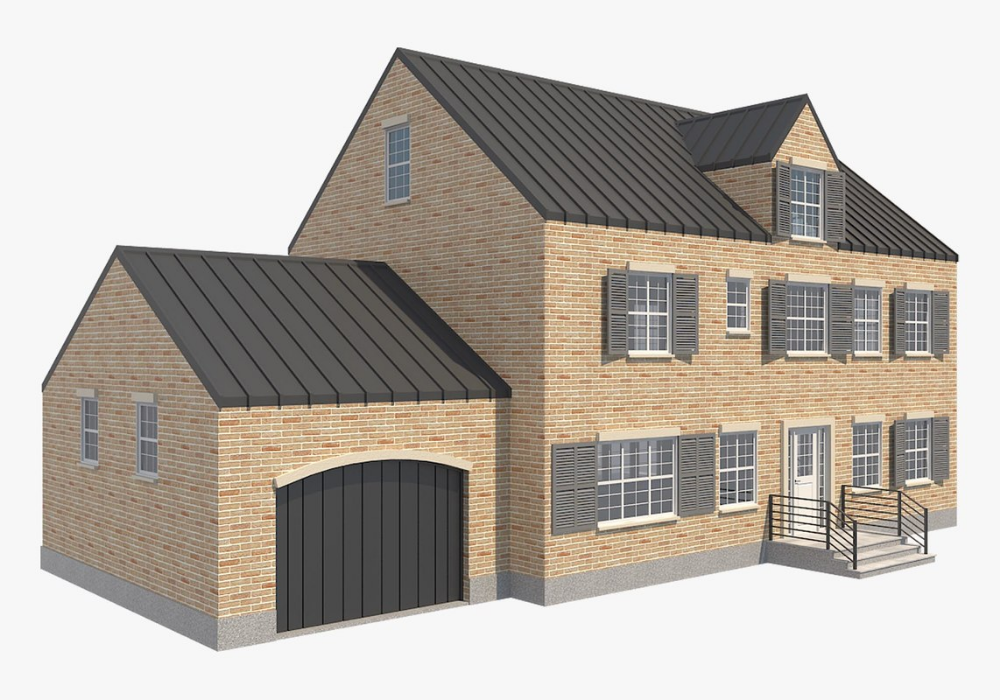
Construction is the world's number one market. And, if many technological innovations are being introduced in the field of high-rise construction, then little has changed in the field of low-rise construction over the past decades. The last 30 years have seen the availability of the Internet, mobile phones, mobile internet, robotics taken to a new level, etc., but when you get to a house construction site, you are unlikely to find many technological innovations. Automation is practically non-existent, and manual labor prevails. 2020 was a test of strength for the whole world, and also led to the highest level of inflation, which, first of all, hit the construction market, there was a dramatic change in prices for metals, cement, wood and much more.
This Internet meme shows what happened to the cost of building materials in just a year. And the process is still going on. At the same time, there is a serious rise in the cost of labor, and there is an acute shortage of it. All this leads to a sharp rise in the cost of building houses. No matter how strange it may sound, statistics show that the growth of automation does not occur when everything is fine, but precisely in crisis situations, during increased competition, reduced demand and the need to urgently look for new technologies to increase production efficiency. So it happened this time, and after some stagnation, construction 3D printing received a new impetus for development.
Preparing to write an article, I turned to the founder of Arkon - Boris Kozlov y. Arkon was established in 2020 and is engaged in the production of construction 3D printers, both a workshop type for creating prefabs (prefabricated houses) and a portal one capable of printing a two-story house. I asked Boris the key, in my opinion, question:
- Construction 3D printing appeared in 2014, but no mass introduction of this technology followed in 7-8 years. Why do you think this happened, and why is there a surge of new projects right now?
- It seems to me that the reason is the snowball effect. The technology had to mature, grow from a hypothesis to a pilot implementation, and finally to commercialization and scaling (what is happening now). In addition, it should be borne in mind that construction is one of the most conservative industries, where, unlike even aviation and the automotive industry, there is still an extremely low introduction of digital solutions and automation in the field of the production process itself - the construction itself.
The issue of regulation and certification also plays an important role - this process is long and creates an additional lag.
In 2014-2016 the first samples of building 3D printers and prototypes of printed buildings appeared. The concepts of various form factors of construction 3D printers and types of printing materials were tested.
In 2017-2018 in the world, the first notable investments were made in a number of construction 3D printing start-ups. Further, by 2020, these investments "rolled" in the form of reaching a certain level of technology maturity - the first commercial products (3D printers and houses) appeared.
Finally, in 2020-2022 it became clear that the hypotheses of the effectiveness of construction 3D printing were justified (cheaper, faster, more environmentally friendly), and large investments began in the industry. A striking example is the investment of GE (the French division of General Electric) in the Danish COBOD or the achievement of a capitalization of $ 2 billion by the American company ICON.
![]()
In 2022-2023 over 1,000 buildings will be printed worldwide already, scaling from single buildings/pilot projects to entire villages and major infrastructure/reinforced concrete implementations. In addition, in a number of countries, by now, a regulatory framework has been created or is being actively created for the introduction of additive technologies in the construction industry.
Thus, I believe that the specified time period is a fairly natural cycle of technology development, which is likely to experience exponential growth in the next decade.
According to ResearchAndMarket report, the global construction 3D printing market is valued at USD 354.3 million in 2022 and is projected to reach USD 11068.1 million by 2027, growing by 99.04%.
Various market processes affect the prices and behavior of participants in the global 3D construction printing market. They create price signals that are the result of changes in the demand and supply curves for a product or service. They can be associated with both macroeconomic and microeconomic factors. Even human emotions can also drive decisions, influence the market, and create price signals.
Now let's take a quick look at what the construction 3D printer is. Without delving too deeply into the technology, we can say that construction 3D printers are very similar to classic FDM/FFF printers that print with plastic, but instead of plastic, the material here is a cement mixture, which is fed directly into the nozzle and forms an object by layer-by-layer overlay. Printers are also portal, on the basis of a flying boom, with a robotic arm.
Pictured left is a construction printer based on a boom. The figure on the right is a gantry construction 3D printer
In the figure above, a construction 3D printer in the form of a robot arm installed on a mobile platform.
Everything changed completely when, in the summer of 2021, the American company ICON, which was trying to introduce 3D printing into the construction of various auxiliary facilities, signed a contract with one of the largest American developers, Lennar, to build a village of 100 houses in Texas and immediately became a unicorn , having received 200 million dollars of investments from several investment funds.
At the same time, the Danish company COBOD, created by the world's largest construction formwork company PERRI, began selling its gantry 3D construction printers and participating in construction projects around the world. In the photo below, a modern two-story house built in Germany and a school building in Malawi, built in record time with a minimal budget.
Few things unite developed, developing and poor countries, everywhere their problems and tasks, but Affordable housing shortage is a global agenda . If in poor countries there is an acute problem with the increase in the number of homeless people due to a lack of housing, as such, then in developing countries it is necessary to dramatically accelerate the number of new housing being built to meet the needs of a growing population. In developed countries, the problem is primarily in the cost of housing, which has risen in price to such an extent that it has become practically inaccessible to young people. And with the simultaneous increase in life expectancy in these countries, this problem is only getting worse.
At the same time, the trend towards "green agenda " is developing, reducing CO2 emissions, building with more environmentally friendly materials, etc. But, unfortunately, so far the construction industry is the absolute leader in CO2 emissions, as well as in the amount of garbage that each construction site leaves behind. This is not to say that construction 3D printing solves all these problems, but at least it is moving in the right direction. Let's look at this with a few illustrative examples.
3D printed walls. Today, when we talk about 3D printing houses, we are talking about printing walls. Everything else (foundation, windows, doors, ceilings and roof) is done in the traditional way. 3D printed walls are built as fixed formwork, which significantly saves the amount of cement used , and this, in turn, reduces the cost of construction and reduces the environmental impact of cement production. In addition, with this method of construction, no additional waste is produced, the strength of the structure does not suffer. It can be reinforced, as shown in the photo on the left, and engineering communications can be immediately laid, as shown in the photo on the right, which also affects the final speed of the construction of the object. At the same time, the total weight of the structure is reduced, the remaining cavities can be filled with lightweight foam concrete, insulation, straw or any other available material. Such a lightweight design can use a lighter foundation. The construction method itself is more economical in terms of material, and therefore environmentally friendly.
Eco-concrete with the addition of polymers is being actively developed, the production of which reduces CO2 emissions from 30% to 100%. The Apis Cor company mentioned at the beginning of the article, which built a house in the suburbs in 2015, is now based in hot Florida, plans to start using this material in its projects.
Another startup from Russia, Mighty Buildings, headquartered in California, initially relied on a polymer with the addition of mineral chips. And while the company doesn't build entire homes, it only makes wall panels, it has won numerous design awards, as well as a $400 million valuation in several investment rounds.
As a result, with a rough calculation, we can say that the total savings on the construction of walls can reach 30%, and the total cost of the house can be reduced by 10%. This is true for houses designed for conventional construction. And if you initially design with 3D printing, you can improve this ratio by optimizing the laying of communications, the ability to immediately print interior walls, bookmark niches for bathrooms, fireplaces, built-in wardrobes and kitchens, as was done in the house built by COBOD in Germany.
"There are spots on the sun." Despite all the advantages of construction 3D printing, has several significant disadvantages of . The main one is layering, which cannot be avoided at the current level of technology development.
The photo above shows the layering of the 3D printed walls.
This task can be worked in several directions:
-
Ribbed walls can be plastered, painted and played with as a design element. That's how ICON does it in the US, for example their latest project House Zero is done that way and has won a number of design awards.
-
Use special "shutters" on the print head that allow smooth layers, as COBOD and other manufacturers do. The photo below shows that this does not ensure the complete absence of layering.
-
Fully sand the surface to get the usual smooth wall for plastering, painting, wallpapering or other finishing. It is possible, but it will require huge labor costs, which can reduce the overall efficiency of using 3D printing.
Pictured above is a 3D printed wall sanded smooth.
The second problem is the required temperature. Ideally, printing should take place at temperatures between +5C° and +30C°. Humidity is also important. Using additives, you can push these boundaries, but not indefinitely. At strong sub-zero temperatures, printing will be possible in the field only if the construction site is covered with a dome and the required temperature is reached inside with the help of heat guns. In conditions of intense heat, it is preferable to print at night. Another solution could be to print the wall panels in the shop and assemble them on site. Of course, each of these decisions will have a negative impact on the economic efficiency of the project.
Building 3D printing can be useful not only for the construction of houses . With its help, you can solve many other problems, and there its disadvantages will not matter. For example, the American concern GE uses COBOD printers to build towers for wind turbines in the shop. Ribbed surface and temperature restrictions in this case do not play any role. Construction takes place in the shop, after which the object is transported to the installation site.
Construction 3D printing, or, as it is also called, additive construction, has just appeared, and I want to believe in its bright future. There are many prerequisites for this, but a lot still needs to be done for success. First of all, it is necessary to develop principles for designing houses for building 3D printing. Then it is necessary to attract top architects to create landmark projects, which can be followed by the mass introduction of a new and very promising technology. Construction 3D printing could help solve the global housing shortage and bring more automation to other areas of construction.
Alexander Kornveits
Expert in the field of additive technologies and 3D printing, head of the Tsvetnoy Mir company
The United States created the first machine for rapid (24 hours) pouring of concrete houses, which was designed by engineering genius Robert Gilmore LeTorneau.
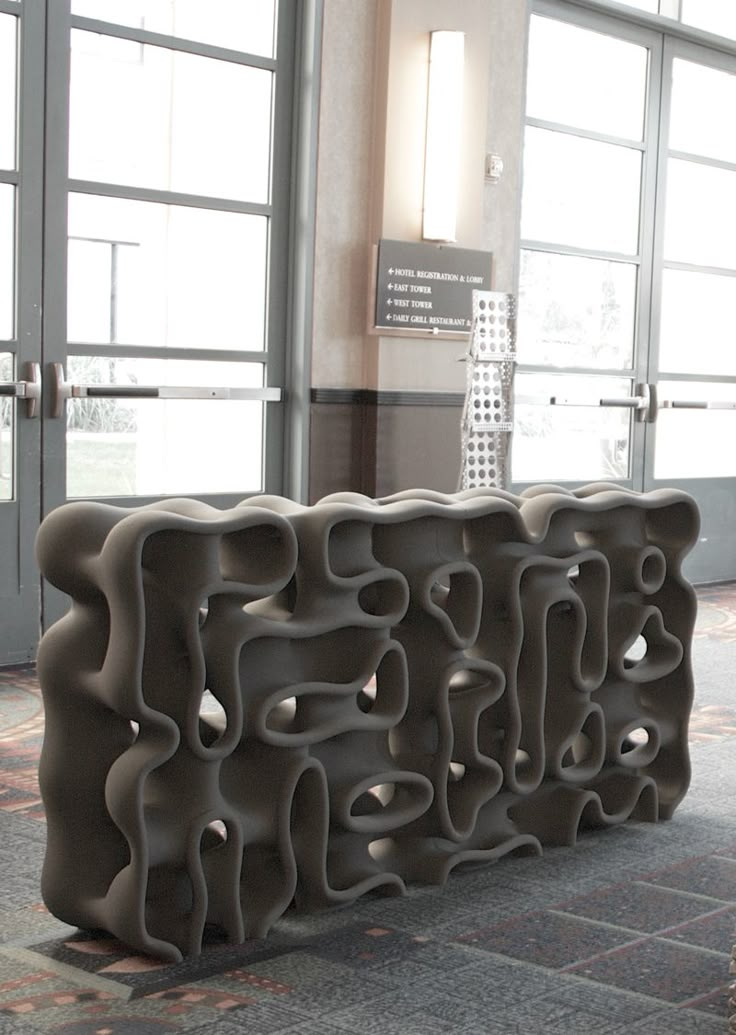
Building area 38 m². The total cost of turnkey construction, including the foundation, walls, ceilings, roofing, electrical wiring, doors and windows, exterior and interior decoration, amounted to 593,568.19 rubles (detailed estimate), but this is without the cost of the work of some specialists.
The printer is completely mobile. The loader brings it in the back and installs it on the prepared foundation at the construction site.
The printer is connected by a hose to a large concrete mixer, that is, an automatic system for mixing and supplying the mixture. It looks like this.
Then the work begins. All work on the construction of the house took about two months in Stupino. The project started in December 2016 and ended in February 2017. The advertised 24 hours is just the pure machine time of the Apis Cor printer. It was included at different stages to print self-supporting walls, partitions and building envelopes.
The device has an interesting design. It is located on a movable arm in the center and prints around itself, gradually rising. After the printing of wall structures is completed, it is removed with a crane - and it continues to work outside.
The appliance itself consumes 8 kW during the process, so you need to provide it with electricity during construction work.
The cost of printing a concrete house is much cheaper than building a conventional "box" of blocks.
In addition, such houses have a lot of additional advantages, which makes them truly unique.
1. Virtually arbitrary shape of the walls. Rounded walls with any corners. Here, the accuracy of construction is perfect, a drunken bricklayer will definitely not screw up your project. The printer has a built-in automatic leveling and stabilization system.
2. The walls are ready for painting with decorative plaster immediately after processing. You can roll yourself in one day and paint the house in arbitrary colors, and then repaint to suit your mood at any time. Plastering with a level and beacons is not required. There is an additional reduction in the cost of finishing work. This applies to both interior and exterior finishes.
3. You can perfectly plan the shape of the walls, the size and position of the windows, taking into account the surrounding landscape and lighting. By the way, there is an assumption that the walls on one side can be made slightly inclined to further increase the illumination. However, the design fantasy is limited by the available forms of double-glazed windows, because here you can’t get by with ordinary glasses, you need to install double-glazed windows so as not to freeze in winter.
Among the disadvantages that come to mind is the flat roof.
It is clear that the developer guarantees that the roof effectively withstands high snow and operational loads. But it seems that stagnant water can accumulate on such a roof with all the ensuing (or rather, not ensuing) consequences. To prevent this from happening, a special wedge-shaped thermal insulation PIR Slope is used on the roof - a ready-made constructor for creating the necessary slopes and counter-slopes. They say that precipitation will be effectively removed from the roof surface, but still somehow unusual.
How the thermal insulation between the inner and outer walls will work is also interesting to check. Now the developer is experimenting with two methods of insulation: from Logicpir filling crumbs on one part of the house (thermal conductivity 0.022 W / m * K) and polyurethane filler composition on the other (0.023-0.025 W / m * K). Insulation was carried out simultaneously with the printing of structures, which significantly increased the construction time.
Well, not everyone will like the small size of the house - after all, not everyone is ready to live in a one-room apartment, a small studio. Although such an option for 38 m² is quite suitable for a single person to live. In addition, as mentioned, the technology allows you to build larger houses.
Yes, and for a round house, you have to buy a concave TV if you want to play computer games on a big screen.
This technology can also be used to print three-story houses, but they will cost much more than $10,000.
Other disadvantages are restrictions on construction dates. The use of a concrete mixture used as "ink" is possible only at a temperature of 5 ° C above zero. So if you do not want to put up an awning with a heater, then construction in winter is impossible. In the future, they promise that the printer will learn how to work with geopolymer concrete from natural components - such material can be printed at lower temperatures. In addition, it is superior to ordinary concrete in other parameters.
After all, there is definitely no place in the house to install a boiler or other heating system. Probably the only option for living in winter is an electric heater.
The estimate for the first house was around $10,000, although the estimate does not include the work of all specialists. The estimate includes the installation of window and door blocks, wall decoration, facade painting, drainage, waterproofing, thermal insulation, but the rest of the work is not taken into account. Probably, with these works, a turnkey house will come out twice as expensive, that is, approximately $20,000.0003
Foundation | RUB 14,819 |
Walls | RUB 95,629.64 |
Ceilings, roofing | RUB 144,267.55 |
Wiring | RUB 12,650 |
Doors and windows | 211 052 RUB |
Exterior finish | RUB 46,250 |
Interior trim | RUB 68,900 |
But the contractor notes that expensive materials were used in this demonstration project.