3D print skulls
3d Printed Skull - Etsy.de
Etsy is no longer supporting older versions of your web browser in order to ensure that user data remains secure. Please update to the latest version.
Take full advantage of our site features by enabling JavaScript.
Find something memorable, join a community doing good.
(1,000+ relevant results)
BONEHEADS Skulls For 3D Printing – 3DKToys
BONEHEADS Master Set - S1
3DKToys
Regular price $69. 95
BONEHEADS Master Set - S2
3DKToys
Regular price $99.95
BONEHEADS Authentic Set - S2
3DKToys
Regular price $34.95
BONEHEADS Redux Set - S2
3DKToys
Regular price $34.95
BONEHEADS Fantasy Set - S2
3DKToys
Regular price $34. 95
Creature Skull
3DKToys
Regular price $7.95
Human Skull
3DKToys
Regular price $7.95
Killer Whale Skull
3DKToys
Regular price $7.95
Demon Skull
3DKToys
Regular price $7. 95
Ram Skull
3DKToys
Regular price $7.95
Kodiak Bear Skull
3DKToys
Regular price $7.95
Crocodile Skull
3DKToys
Regular price $7.95
Humpback Whale Skull
3DKToys
Regular price $7. 95
Lion Skull
3DKToys
Regular price $7.95
Velociraptor Skull
3DKToys
Regular price $7.95
Bull Skull
3DKToys
Regular price $7.95
Roe Deer Skull
3DKToys
Regular price $7. 95
Cat Skull
3DKToys
Regular price $7.95
Dragon Skull
3DKToys
Regular price $7.95
Owl Skull
3DKToys
Regular price $7.95
when the 3D printer is not bored (Interview with the master) / Sudo Null IT News
#Anthropology@phanerozoi
Efimov Samir: Let's start by introducing one of our team members - our bone maker, who does a lot of cool things using hands and a 3D printer. His name is Kesh Corvus. He actually produces not only skulls and complete skeletons of extinct animals from original scans, but also produces many things on the GEEK theme.
For example, "pip-boy. 3000" (in the video above) from the Fallout universe, a power brass knuckles with an imitation of a working mechanism or an exact copy of the helmet (1: 1) of the "x-01" power armor with a cooler and illuminated eyes, completely handmade.
An exact copy of the helmet (1: 1) of the power armor "x-01" from Fallout 4By the way, the power brass knuckles from the "folych" was one of the most difficult to manufacture for Cash. He did it for more than two months (about *), if I'm not mistaken. A video with power brass knuckles is shown below.
Some constantly grumbling and eternally dissatisfied old-timers of Habr with their complaints about the fact that our articles are supposedly not on the subject of Habr, today they can breathe freely for a while, because then they will again have to nervously smoke in the corner from impotence, because there will still be a lot of many, and absolutely many, and infinitely many, and extremely many biological topics on the subject of the hub - "biology" (behind the scenes my sinister laughter). But we are getting a little off topic here.
So, Cash, tell me a few words about yourself? Well, what's your name? Where are you from? And what motivated you to do it?
Kesh Corvus : Hello Samir and dear readers. My name is Nikolai. I live in Pyatigorsk, Stavropol Territory. To the question of how I came to this activity, I will answer a little in detail. As a teenager, I had many hobbies, including craft, interest in biology and paleontology. The latter manifested itself more as reading various books, watching documentaries and terrariums.
Yefimov Samir: Sorry to interrupt. By the way, Cash is still fond of terrarium and maintains an aviary for vulture and caiman turtles. A snippet can be seen in the video below
Kesh Corvus : It's okay, I think people are also interested. But let's get back to crafting. So, my first products were made of wood, a little later of metal. It was armor, swords, shields. All products were in the style of fantasy and the Middle Ages. This is due to the historical fencing and Tolkienist events that my friends and I often attended and participated in at our leisure.
By the way, the nickname Kesh also appeared in this company, which I still hear from friends more often than my own name. However, all this was just a hobby and it was 15 years ago... In those ancient times, almost no one knew the word cosplay. But I began to actively engage in crafting after an unpleasant situation with me. At the age of 25, he was hospitalized with a diagnosis of oncology.
As a result, I had an operation to remove a tumor-affected kidney. As a result of this sad event in my previous professions, I could no longer work. (auto mechanic, production and installation of outdoor advertising). I had to think hard with my head how to get out of the situation.
Project label.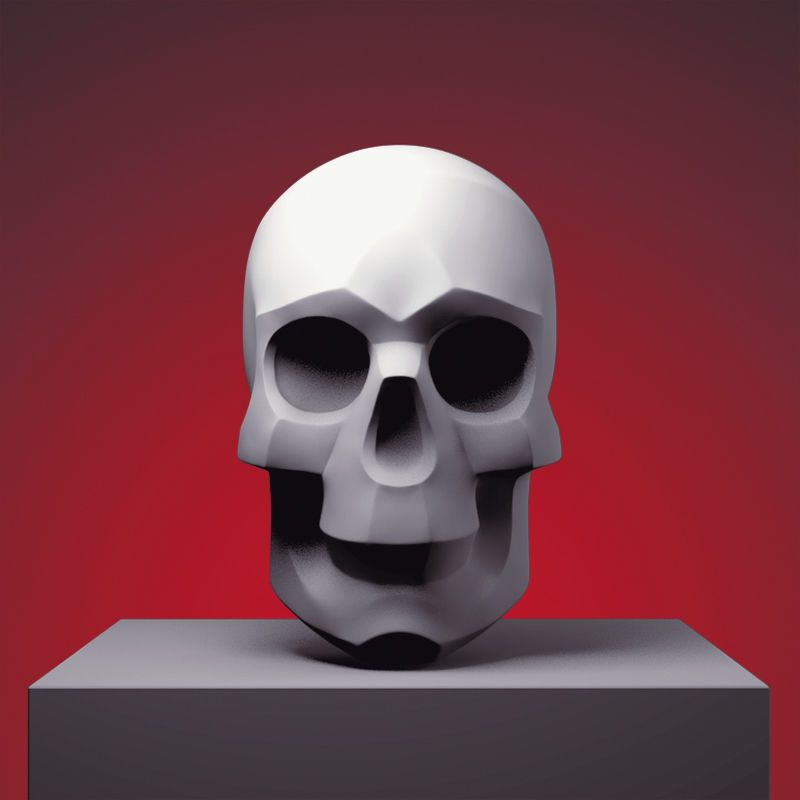
So I remembered that my arms were growing from my shoulders, and that's how the first project of D.K. craft. Initially, I did everything manually, later expanded the range of tools, assembled my first 3d printer. Not from scratch, of course, I didn’t solder the board myself, but I selected all the details myself in order to assemble it myself and understand how everything works. Later I mastered 3D printing. The D.K.Craft workshop mainly developed in the "geek" theme. Items for cosplay, miniature, key chains. Later I wanted to diversify my activities, something with an emphasis on science.
So, my second Vkontakte project appeared: Nessitera Bones Factory, where all my interests in crafting in the field of paleontology and biology are manifested. And somewhere in the interval between the creation of the second project, thanks to the Stubborn Paleontologist, I met the guys from the scientific community Phanerosa. So I joined them. At the same time, I continue to manage my two projects. Leaving them would be a crime for me.
Efimov Samir: Well, you're just cool, and that's 100% true. Huge respect for what you do and how scrupulously you approach it. And I'm actually still delighted with how high quality the output products are.
Personal photo of the author of this article from interview I have held your Neanderthal skull and it feels like bone! But in fact, this is plastic printed on a 3D printer, however, with the proviso that you killed about two and a half weeks of manual work to bring the replica to perfection. That is why it does not feel like something fake, but looks like it is a real skull. And what’s more, you did it completely free of charge as a gift for the Department of Vertebrate Zoology, Faculty of Biology, Russian State Pedagogical University named after. A. I. Herzen. The teachers of the department are very enthusiastic and say that this is an amazing preparation for classes in anthropology and anatomy courses.
They send you a huge thank you for the gift, but that's another story. In general, before moving on to the production part of the skull itself, tell us what kind of skull it is, to whom it belonged, and from whose materials did you make such a cool anatomical replica?
Kesh Corvus: So, in fact, this skull belongs to a very famous specimen, under the catalog number - La Chapelle-aux-Saints 1. In the people, his name sounds like "Old man" ("Old man"). This, in principle, reflects the essence of his body structure, which was twisted and resembled an old man.
One of the modern reconstructions of this Neanderthal. It is best known for being one of the very first, if not the very first, complete Neanderthal skeleton that was discovered in France at La Chapelle-aux-Saintes in 1908. The age of the remains dates from 56,000 to 47,000 years. It is generally accepted that at the time of death this person was 40 years old, or a little more. The remains of this species of Homo were first studied by Marcellin Boule, whose reconstruction of Neanderthal anatomy, based on material from La Chapelle-aux-Saints, shaped the popular notion of Neanderthals as prosimians for more than thirty years.
The La Chapelle-aux-Saints specimen is typical of the "classical" Western European Neanderthal anatomy of the early to mid-20th century. In this regard, in 1911-1913, Boole's reconstruction appears, where our old man is depicted as a savage, overly hairy, caveman with an elongated skull, a crooked spine, bent hips and knees, and a diverging big toe. Later, at 19In 48, this image will ennoble Gerasimov, making the appearance of the Neanderthal more humanized according to real skull samples.
Reconstruction of a Neanderthal Gerasimov, 1948. But still, in general, the old man was often portrayed as a savage. Of course, these first reconstructions of Neanderthals were wrong, because they were reconstructed in the image and likeness of a very sick individual of a person.
But scientists and paleo-artists are not really to blame. Nevertheless, it should be told why it happened. The thing is that the old man was in very poor health: almost toothless, with a crumbling lower jaw. He also suffered from advanced arthritis, which showed throughout his skeleton. Twisted and ugly, scary, but at the same time not abandoned by his relatives to the mercy of fate. This is indicated by the fact that a person with such serious illnesses, by the standards of primitive life, lived for a relatively long time. Now in our time you rarely come across such nobility, but in those primeval centuries it is amazing.
Old man's original skull. In fact, this skull exhibits many of the "classic" Neanderthal features, including large uninterrupted brow ridges, wide nasal opening, long ovoid foramen magnum, relatively flat skull base (compared to modern humans), small mastoid processes, long and low skull, large eye sockets. Typical huge and massive dimensions of the skull itself. There is also clear evidence of postcranial pathology. Of course, some of the pathologies in the reconstruction of the skull were eliminated.
Restored, lower jaw, eliminated, damage to the skull, a row of teeth was restored, etc.
Efimov S.T. . : Why? I believe that if a person who positions himself as a master of something, then he must be completely imbued with the business he is doing. I also said above: biology and paleontology are on the list of my interests. And I would like to add that my task, first of all, is quality. Let me spend more time on it, but then I will not be ashamed of the product. I still try not to stop learning and doing better than now.
Efimov S.T. : Completely agree. Well, since we have already reached production, can you tell us how you made this replica? How many hours of work, materials, nervous breakdowns did it take?
Kesh Corvus . : I will describe briefly. Actually, I found the reconstruction scan itself on the net. Upon request, I was provided with a 3d scan of a plaster replica from Madeleine Hazard, University of Pennsylvania.
Item was catalog number 1979rp15. To begin with, I improved the quality of the scan itself for printing in editor programs. Now this model is freely available and everyone can download it, the source without my modifications. Next, cutting into parts of the model itself so that the parts fit on the print area of the printer. Then the printing itself, everything is done with ABS plastic.
Fragment of work. Photo by Cash.It took about 1kg of material. The skull has 2 walls: external and internal, between the walls the filling is 35%. The skull itself is hollow inside, like a real one, respectively. The thickness of the wall itself is 4 perimeters, the nozzle is 0.4.
A fragment of a printer that printed a Neanderthal skull There was a lot of work to be done after printing. A lot of time was spent on the processing of the product, mainly on grinding, to remove the layering of the product. Chemical treatment of plastic with solvents was also carried out. After that, I had to work as an engraver to highlight small details and so on, including painting with a brush. At the expense of spent nerves, I have already gone through all this. For 4 years of work, there was a lot of things, but now mostly the nerves are spent on repairing printers, if something suddenly fails. It is difficult to say exactly how many hours the whole work took. The printing itself takes about 5 days of almost continuous work. Everything that I did next with him took more than 2 weeks.
I spent at least 3 hours a day on my skull. Acrylic painting by hand for about 22 hours.. Next, a varnish to protect the paint from external influences. The skull that you were holding, as you understand, is precisely a reconstruction. and it's really not just 3D printing. This is a lot of hard work.
Efimov S.T. : I just don't have the words. Truly titanic work. In general, I really look forward to when you write an article about how you made the skull of a Triceratops cub and a complete Velociraptor skeleton in detail. I think it's really worth it to be on the hub. Thank you very much for the interview. Glad to have you on our team. You are a wonderful friend and a good person. In conclusion, I want to say that if you liked this article in the interview format and you want more of this, support the article with a like and a plus sign in karma. We hope you enjoy this format. Stay with us. There will be a lot of interesting things ahead... As a bonus, you will get the skull of a Homo sapiens from Cash.
An article in the interview format was written by the inspirer of the scientific community Phaneroza, biologist Efimov Samir and bone master Kesh Corvus exclusively for Habr, in the future this article will be published in the communities by Phaneroza and Nessitera Bones Factory
3D printing of the anatomical model of the skull
Skip to main content
3D printed skull model
3D printed anatomical skull model
3D printed anatomical skull model
3D printed anatomical skull model
News
-
Photopolymer printing in various formats is in great demand in the field of high-speed production of various blanks.
3D printing with a photopolymer produces the highest detail of any object. Not only a special computer program helps in this, but also polymer resins applied in thin layers, which harden well under the action of laser beams or UV radiation.
Application of photopolymer printing
For projects that have a 3d model, or are just planned, design engineers will develop the necessary programs and select the right photopolymer. In practice, SLA or DLP printing is most often used, a feature of which is high accuracy. The presence of layouts, in the form of samples, greatly facilitates the work with objects that have complex geometry.
This includes factory-made industrial parts, jewelry and medical products. The order received for work is processed by special programs and editors, carefully checked, and only then they go to work.
Photopolymers are smooth plastic objects. Most often, acrylic is used for their manufacture. Printing with photopolymers occurs using a 3d printer.
Each printing device has its own settings in microns (from 16), which create an accurate image. Simultaneously with the application of the thinnest layers of polymers, a support material in the form of a gel is applied.
More
-
3D printers print layers of 3D blanks. 3D printing is made from one or more liquid or solid materials in accordance with specified sizes and shapes (CAD). During printing, physical or chemical processes of hardening or melting occur. Typical materials used in 3D printers are plastics, resins, ceramics, and metals.
Read more
-
The 3D printing process must go through a series of specific steps, each with a different purpose. Each needs special attention.
Read more
-
The popularity of 3D printers does not fade from the moment this production is launched. Widespread use is explained very simply: you can get exclusive things in a matter of minutes, the most important thing is to create a 3d project.
On the printer, you can print goods for children, clothes, interior items, tools and other things from different materials. 3D printing is a manufacturing process in which a 3D printer manages to print a three-dimensional part by applying several layers of a selected material. For production, a developed 3d model is required. The scope of use is multifaceted: toys for children, home accessories, dishes, door handles, mobile phone cases, shelves and coasters for kitchens are printed on a 3D printer. Anything can be printed on a 3d printer.
Read more
-
Printing on 3D printers is used for most areas, with its help it is possible to create individual items for play, education, design. This is a popular service: today printers are used not only in large-scale production, there are also home models.
Read more
-
Processing of 3d products is used to give an attractive appearance to the product, to create a glossy sheen.
Different solutions can be used depending on the material from which the product is made. For details, you can not carry out finishing processing, since the appearance of the goods does not play a big role.
The appearance of products printed on a 3D printer directly depends on the technique and processing methods used. The surface of the products can be smooth or ribbed. And if the appearance is practically not important for details, when creating decorative elements, it is necessary that they be perfectly smooth and even. In order to make products attractive, post-processing is used. Below we describe several types of equipment that are used to process materials, depending on the type of product, textures and their sizes.
Chemical post-processing of 3D models
This is the most popular method for processing plastic products. Due to timely work performed, the product acquires a glossy sheen, and its edges look natural. The most important thing is to choose the right time for processing so as not to spoil the appearance.For cleaning, the following textures are most often used:
Read more
-
Laser material processing is a production that is used in various fields. Thanks to the automated operation of the equipment, it is possible to quickly and accurately perform many works with materials of any thermal conductivity.
Thanks to scientific and technological progress, it is possible to improve the processing of various materials. Today, a laser is used for this, after the touch of which the textures change beyond recognition. There are many reasons why laser processing of various materials is in demand. We will talk about them below.
Why laser processing is so popular
Different methods are used to process materials, but the laser deserves special attention. Below we describe why this production has not lost its relevance for several decades.
Fully automated process
In today's 21st century, many people want to move away from manual labor and work on special equipment.
And laser processing completely falls under these parameters: the whole process is fully automated, you only need to set the necessary parameters.
Read more
-
Artistic processing of materials is a science that studies the effect of various methods on products in order to improve their appearance or reconstruction. Using different methods, it will be possible to apply beautiful ornaments, memorable dates, more important than inscriptions, to protect them from negative influences.
Read more
-
The company MG3D, whose main specialization is 3D printing, was contacted by a customer who wanted to create a model of the Moscow school No. 1520 named after the Kaptsovs. This is an old educational institution, built at the end of the century before last. The masters of the company took upon themselves the execution of the order for the manufacture of a detailed model of the school.
A separate difficulty of this order was that it was required to complete it in just three days.
However, the MG3D masters did an excellent job with the task.
A school with an amazing history deserves professional treatment
Read more
-
MG3D was contacted by a customer whose task surprised even experienced craftsmen who have been busy with their business for more than a year. Namely, we ordered 200 fountain cutters, this is a small-scale production, and 3D printing as a method fit perfectly: cheaper, easier and faster than casting in industrial molds. The conditions set by the customer required the MG3D team to use all their experience. After all, it was not only about an environmentally friendly, high-quality and durable product.
What other requirements did the customer have for the product?
Checkout.
Contacts
To place an order, use the form on the left.
Leave your details and, if available, attach a file to explain your order.
Our specialist will contact you as soon as possible.