3D print pla stringing
Stringing or Oozing | Simplify3D Software
Stringing or Oozing
Stringing (otherwise known as oozing, whiskers, or “hairy” prints) occurs when small strings of plastic are left behind on a 3D printed model. This is typically due to plastic oozing out of the nozzle while the extruder is moving to a new location. Thankfully, there are several settings within Simplify3D that can help with this issue. The most common setting that is used to combat excessive stringing is something that is known as retraction. If retraction is enabled, when the extruder is done printing one section of your model, the filament will be pulled backwards into the nozzle to act as a countermeasure against oozing. When it is time to begin printing again, the filament will be pushed back into the nozzle so that plastic once again begins extruding from the tip. To ensure retraction is enabled, click “Edit Process Settings” and click on the Extruder tab. Ensure that the retraction option is enabled for each of your extruders. In the sections below, we will discuss the important retraction settings as well as several other settings that can be used to combat stringing, such as the extruder temperature settings.
Common Solutions
Retraction distance
The most important retraction setting is the retraction distance. This determines how much plastic is pulled out of the nozzle. In general, the more plastic that is retracted from the nozzle, the less likely the nozzle is to ooze while moving. Most direct-drive extruders only require a retraction distance of 0.5-2.0mm, while some Bowden extruders may require a retraction distance as high as 15mm due to the longer distance between the extruder drive gear and the heated nozzle. If you encounter stringing with your prints, try increasing the retraction distance by 1mm and test again to see if the performance improves.
Retraction speed
The next retraction setting that you should check is the retraction speed. This determines how fast the filament is retracted from the nozzle. If you retract too slowly, the plastic will slowly ooze down through the nozzle and may start leaking before the extruder is done moving to its new destination. If you retract too quickly, the filament may separate from the hot plastic inside the nozzle, or the quick movement of the drive gear may even grind away pieces of your filament. There is usually a sweet spot somewhere between 1200-6000 mm/min (20-100 mm/s) where retraction performs best. Thankfully, Simplify3D has already provided many pre-configured profiles that can give you a starting point for what retraction speed works best, but the ideal value can vary depending on the material that you are using, so you may want to experiment to see if different speeds decrease the amount of stringing that you see.
Temperature is too high
Once you have checked your retraction settings, the next most common cause for excessive stringing is the extruder temperature. If the temperature is too high, the plastic inside the nozzle will become less viscous and will leak out of the nozzle much more easily. However, if the temperature is too low, the plastic will still be somewhat solid and will have difficulty extruding from the nozzle. If you feel you have the correct retraction settings, but you are still encountering these issues, try decreasing your extruder temperature by 5-10 degrees. This can have a significant impact on the final print quality. You can adjust these settings by clicking “Edit Process Settings” and selecting the Temperature tab. Select your extruder from the list on the left, and then double-click on the temperature setpoint you wish to edit.
Long movements over open spaces
As we discussed above, stringing occurs when the extruder is moving between two different locations, and during that move, plastic starts to ooze out of the nozzle. The length of this movement can have a large impact on how much oozing takes place. Short moves may be quick enough that the plastic does not have time to ooze out of the nozzle. However, long movements are much more likely to create strings. Thankfully, Simplify3D includes an extremely useful feature that can help minimize the length of these movements. The software is smart enough that it can automatically adjust the travel path to make sure that nozzle has a very short distance to travel over an open space. In fact, in many cases, the software may be able to find a travel path that avoids crossing an open space all together! This means that there is no possibility to create a string, because the nozzle will always be on top of the solid plastic and will never travel outside the part. To use this feature, click on the Advanced tab and enable the “Avoid crossing outline for travel movement” option.
Movement Speed
Finally, you may also find that increasing the movement speed of your machine can also reduce the amount of time that the extruder can ooze when moving between parts. You can verify what movement speeds your machine is using by clicking on the Speeds tab of your process settings. The X/Y Axis Movement Speed represents the side-to-side travel speed, and is frequently directly related to the amount of time your extruder spends moving over open air. If your machine can handle moving at higher speeds, you may find that increasing this settings can also reduce stringing between parts.
Related Topics
How to diagnose, and fix, PLA stringing in 3D printing
3d printers - 3D Printing - additive manufacturing - digital fabrication - digital manufacturing
3D printing is revolutionizing everything from rapid prototyping to small-scale and hyper-local manufacturing. As the prices and quality of commercial and hobbyist 3D printing hardware continues to drop, its popularity grows - but 3D printing has challenges above and beyond those found in 2D printing.
It’s common for a 3D printer fresh out of the box to deliver disappointing prints. Poor bed adhesion, layer splitting, blobs of filament, oozing, and stringing will be problems familiar to any 3D printing enthusiast. But they’re problems which can usually be resolved, with a little troubleshooting.
Polylactic acid filament (PLA filament) is one of the most common materials for 3D printing, thanks to a relatively low melting point and its high strength once printed. It’s typically delivered as a reel of thin spaghetti-like filament, which is heated and extruded by the printer to create the desired object.
Recommended reading: Food-grade 3D printing: Is PLA Food-Safe?
PLA stringing, the wispy strands of melted plastic which can appear outside the printed part, is a common problem. The strings’ appearance can vary from short spikes to thicker hairs and even blobs of material, but they’re all caused by the same thing: PLA oozing from the extruder even when extrusion shouldn’t be taking place.
Image courtesy of Ultimaker.
It’s usually possible to remove the strings during post-processing and finishing. To save time and improve print quality, though, it’s better to get to the root cause of the problem and prevent the strings from forming in the first place.
The print head on a fused deposition 3D printer works by pushing the filament through a heater and then out of the nozzle. In theory, when the filament isn’t being pushed nothing should appear from the nozzle; in practice, just stopping pushing isn’t enough to prevent some material from leaking through.
The answer is retraction, commonly overlooked in the print settings: Pulling the filament back by a few millimeters after each extrusion, to “suck” material back from the nozzle and prevent it from oozing out as strings or blobs. Retraction is usually controlled in your model slicing software: In Ultimaker’s Cura, for example, retraction settings are found in the Travel menu. In some cases you’ll also need to specifically enable retraction; check your software’s documentation if you’re unsure.
Some 3D printers override retraction settings set in slicing software. If that’s the case with your printer, consult its documentation to find out how to set it on the printer itself. Also look into coasting, if your software supports it: It can help reduce stringing by stopping the extrusion of filament slightly earlier than usual.
Recommended reading: What Is FDM 3D Printing?
The retraction distance is how far the filament is pulled back. A retraction distance of 0mm means that there’s no retraction at all, and stringing is all-but guaranteed. Setting too high a retraction distance, however, can result in clogs forming - or even pop the filament right out of the hot end, derailing the whole print.
Most 3D printing software uses a default retraction distance of around 6mm. This may not be the best setting for your particular combination of printer and filament, though. If you’re seeing PLA stringing, try increasing the distance in 0.5mm or 1mm increments.
Recommended reading: Z Banding: Rooting out the Cause and Fixing the 3D Printing Defect.
Image courtesy of Osman Talha Dikyar.
The distance the filament is retracted is only part of the equation: You also have control over how quickly it’s retracted. Too high a speed, measured in millimeters per second (mm/s), and the filament can snap inside the hot-end; too low a speed and the pressure isn’t relieved quickly enough to prevent oozing.
There’s another reason to dial in the perfect retraction speed, too: Print time. The slower the retraction speed, the longer your print will take to finish. This is particularly true for models where the hot-end spends a lot of time swapping between extrusion and non-extrusion travel.
Recommended reading: People of 3D Printing: Fabien Bruning.
The minimum travel setting isn’t found in all slicers, but can help balance the risk of clogging against stringing: It controls how far the extruder should travel without extruding before it considers it worth retracting at all.
If you’re happy with the retraction distance and speed settings but are suffering clogs, try setting a slightly larger minimum travel distance. If the strings reappear, tweak the retraction distance and speed settings again until you’ve found the perfect balance.
If you’re using a common model of printer, like the Creality Ender 3 or Prusa Mini, your best resource for retraction settings is the community. Find other 3D printing enthusiasts with the same printer and compare notes; chances are more than a few people will have had the same problems and found a solution.
Recommended reading: 8 best 3D printing tips you need to know.
If you have a less-common 3D printer, or one which has been extensively modified, you’re going to have to experiment. While you could download a test print from Thingiverse or similar and try out each adjustment in turn, there’s an alternative: The Calibration Generator.
Image courtesy of Karl Johnson.
Developed by Karl Johnson, the Calibration Generator is designed to generate the code for a retraction test print. This print walks through a range of retraction distances and speeds in order to find the perfect setting for your printer. The tool’s default settings are tailored for a Bowden tube extruder with separate heat block; for direct-drive printers the retraction distance increment should be lowered to 0.25 for best results.
When the print has finished, inspect it for stringing - and, more importantly, where the stringing stops. By comparing it to the diagram on the website you’ll find the retraction speed and distance you need for perfect prints.
Filament retraction isn’t the only thing responsible for preventing stringing issues in your prints: Getting the right temperature is equally important. If your printer’s hot-end is set to a too low temperature, pressure builds up in the extruder. As the pressure builds, clogs and jams become likely. A too high temperature, though, can result in oozing and stringing as the filament's viscosity drops.
The best way to find the optimum print temperature is by consulting your filament manufacturer. Most manufacturers will be able to provide a recommended print temperature which eliminates oozing. If your filament manufacturer can’t, or you’re not sure exactly who made that half-finished roll of filament you’re working through, there are some simple rules of thumb.
Image courtesy of Mingu Kang.
Printing in PLA allows you to get away with a lower temperature than other materials. A setting of 210°C (410°F) is typically enough to avoid clogging without overheating the filament. If your printer has a heated bed, keep it below 60°C (140°F).
Recommended reading: PLA bed temperature & print temperature settings.
These temperatures are only a guide. You’ll need to experiment to find the sweet spot for your particular printer and filament. Try setting a lower temperature in five-degree decrements, and if you see no improvement set a higher temperature instead. If you find that you’re going more than around 30 degrees outside the recommended temperatures, though, your problem likely lies elsewhere.
If you want to automate the testing process, Karl Johnson’s Calibration Generator includes the ability to increment hot-end temperature and fan speed as well as retraction distance and speed.
It’s tempting to set your 3D printer to the fastest speed possible. The printing process is slow enough, after all. Setting too high a speed, though, is a sure-fire way to see stringing - particularly if you’re printing at lower temperatures.
Recommended reading: What software to use for 3D printing?
The travel speed, which is the rate at which the print head moves while not the material is not actively under extrusion, has the opposite effect: A higher travel speed reduces the time the print head spends not extruding material. With less time traveling between extrusion jobs, there's less time for oozing to occur.
As with other settings, finding the perfect print and travel speeds for your printer and filament combination will require trial and error. If you’ve adjusted the settings above with no success, try dialing down the print speed and increasing the travel speed.
Recommended reading: Improving your 3D printing success rate with Ultimaker Cura.
Sometimes the simplest solutions are the best. Proper maintenance is vital to a 3D printer, and cleaning the nozzle is one of the most overlooked steps. With a dirty nozzle, you’re more likely to see oozing owing to increased pressure. It can also result in other printing problems, like blobs and lumps in the print or a too-thin extrusion.
Brush the exterior of the nozzle with a brass wire brush to clear external material and keep the surface clean. In some cases, that’s all that’s required. In others, particularly if there’s a clog, you’ll need to heat the nozzle and push a small pin through - making sure the diameter of the pin is not larger than the diameter of the nozzle. If you’d rather not poke around with a pin, you can buy cleaning filament: Just manually run a small quantity of this through the hot-end to clear out old filament residue.
Image courtesy of New Data Services.If your nozzle is particularly dirty, remove it from the printer and soak it in acetone. This dissolves the PLA and restores the nozzle to factory-fresh condition. It’s worth doing this if you’re switching between different types of filament, too.
Recommended reading: Essential tools for every 3D printing professional.
Finally, the filament itself can be the cause of print failures. If you’ve tried everything above and are still having stringing problems, try switching to a different brand of filament.
Recommended reading: What is the strongest 3D printing material?
Another common cause of print failures is improperly stored filament. PLA, and many other 3D printing materials, readily absorbs moisture - and as it does it swells. Swollen PLA increases the pressure at the printer nozzle, making oozing more likely. As the material is heated, the water is turned to steam - which can cause sputtering, increasing the risk of oozing still further.
Image courtesy of Osman Talha Dikyar.You can buy specialist filament drying cabinets, but there are cheaper methods. Store unused filament in a sealed plastic box with a sachet of silica gel. This will dry the air in the box and pull moisture out of the filament, improving your chances of a good print.
Recommended reading: Dealing with Over Extrusion in 3D printing.
It’s easy to get discouraged when your first prints don’t come out perfect. PLA stringing is a common problem but easily solved, and following the above should improve things dramatically.
Recommended reading: Researchers establish first-of-its-kind framework to diagnose 3D-printing errors.
Remember to approach the problem scientifically. Use test print solutions like Karl Johnson’s calibrator to reduce the time you spend experimenting. Keep your nozzle clean and your filament dry, and check your slicer software’s settings with other 3D printer owners to find a good starting point for your tweaks. Keep an eye on your printing right at the start: Often oozing problems can be seen even in the first layer.
Ultimaker Support, How to fix stringing: https://support.ultimaker.com/hc/en-us/articles/360012016280-How-to-fix-stringing
Ultimaker Support, Travel settings: https://support.ultimaker.com/hc/en-us/articles/360012611299-Travel-settings
Wikipedia, Polylactic Acid: https://en.wikipedia.org/wiki/Polylactic_acid
Karl Johnson, The Calibration Generator: http://retractioncalibration.com/
How to properly print with PLA filament
Let's take a closer look at the process of 3D printing with PLA filament. We will discuss what PLA is and how to make friends with your printer, how to choose the right temperature and what surfaces to print on.
PLA is an amazing material for 3D modeling. But it is non-toxic and smells pleasant during operation. PLA comes in a wide variety of colors, and because of its temperature characteristics, it's exceptionally easy to make great objects. nine0003
If you've worked with ABS, you'll find that PLA is harder, applies more slowly, and produces remarkably smooth details more easily. PLA is less distorted by temperature, and it is easier for them to print large objects. It should be taken into account that since this material is more rigid, it is therefore more brittle. If you are going to use your printed object in an environment where it will experience a lot of impact and violent collisions, PLA may not be the best choice. nine0003
Another important consideration when printing PLA is the temperatures that the print will be exposed to. PLA becomes soft at 70-80°C, and objects made from this plastic will deform if exposed to temperatures above these for extended periods of time. That's why ABS or some other material should be used near the extruder. We usually print all other parts of the printer from PLA - except for those that are next to the extruder, they are from ABS. nine0003
Check the quality of the filament
Problem The plastic filament is brittle and breaks in the hand. When printing, the layers lay unevenly, rough, frequent gaps and smudges, clicks and pops are heard. (Happens with ABS and PLA)
PLA and ABS are hygroscopic, meaning they absorb moisture from the environment. Wet rod becomes more brittle and brittle. Can break by hand when bent. Such a filament, if not broken in the extruder feed mechanism, entering the hot end in a split second is heated to the boiling point of water, as a result of which even a small moisture content instantly boils and breaks out, creating a characteristic explosion. Outwardly, such plastic will not differ from healthy one, but it will be more fragile and brittle. Quality PLA and ABS should not break by hand without effort. nine0003
Solution dry the plastic spool
- Place the filament in an electric oven for 2-3 hours at 70°C. You can use the closed chamber of the printer with a heated table for these purposes.
- Store unused plastic in sealed box or desiccant bags. The correct factory packaging for PLA and ABS is a sealed vacuum bag with a silica gel bag.
- The desiccant will not dry out the plastic, but will provide excellent protection against excess moisture. nine0026
- Use non-hygroscopic grades of SBS and HIPS plastic - they do not absorb moisture, can be stored as long as you like without the risk of deterioration
Problem Plastic leaks from extruder nozzle.
It is very difficult to find the right extruder temperature for some brands. Capricious printing, the layers do not lie evenly, the print quality leaves much to be desired. This is not an ideal plastic, all that remains to be done is to select the temperature of the extruder with each loading of plastic. nine0003
Solution Purchase quality materials from trusted manufacturers.
How to print the first layer correctly
The first layer is the most important part of any printout. There are a few things that need to be done to get the first coat to stick well.
- The mounting plate (or print substrate) must be installed at the correct level.
- The extruder must be at the correct height above it.
- The base material must be good enough for the PLA to stick to. nine0026
Printing on a substrate
Use adhesive materials: substrates are one of the easiest and fastest ways to get great prints from PLA, just like ABS, SBS or HIPS.
Used to be 3M blue tape everywhere - not the height of perfection, but it was very easy to use until it was discontinued. But sometimes during printing, your part could tear off the tape from the table, and in such cases the object will have distortions.
Heated bed printing
If you have a temperature controlled table, you can print directly on the glass quite successfully. The recommended table temperature for PLA printing is 70°C.
When printing on glass, it is extremely important to set the table and extruder to the correct height. If the extruder is too far away from the table, the PLA won't stick AT ALL; if too close, the glass will completely block the extrusion of the material, and again it will not stick AT ALL.
If your first coat doesn't stick
- Check table level.
- Make sure the printhead is close enough to properly extrude the first layer. The gap between the nozzle and the table surface is checked with an ordinary sheet of paper. The sheet should be able to crawl through this distance, but not get stuck.
- Make sure you run the extruder enough before you start printing so that the filament is on the table during the entire printing process of the first layer. In slic3r you can set the number of passes up to 4 or 5 depending on the part. nine0026
- Clean glass with denatured alcohol.
When everything is set up correctly, glass is the best option for working with PLA. It produces a wonderful shiny bottom layer, and the table heating ensures that everything comes out smoothly and evenly.
Other printable surfaces
Printing on a transparent self-adhesive film for a 3D printer table
Transparent self-adhesive polyester film with a permanent heat-resistant adhesive layer. Stick the film on the printtable. This film is much denser and stronger than Kapton tape, so you can print much longer, withstand high temperatures. Brim (Brim) is not needed - gears without Brim are great. Lasts longer than kapton. nine0003
Printing on Kapton ribbon
Many people have had good results printing on Kapton ribbon. To print on it with PLA, a heated pasteboard is required. We used to print exactly like this, but when we learned how to do everything right on glass, we stopped considering this option the best. The process of printing on kapton tape is almost identical to printing on glass, but requires more preparatory work and cleaning. If you know of any other benefits of kapton tape, please share. We are constantly working to improve the process. nine0003
Printing on polycarbonate
We experimented a bit with polycarbonate, lightly oiling it with vegetable oil. Polycarbonate works, everything prints well. That's just the part is difficult to remove, so the benefits are somehow not obvious. It seems to us that this method deserves a deeper study, and we will report our research as soon as they are carried out. In the meantime, we recommend working with blue tape.
What to watch out for
If the temperature is too high
Between different parts of the print you will notice a lot of a kind of string (snot) and the extruder will "leak", releasing a lot of plastic when moving between different printable areas. If this happens, you should try to lower the temperature in 5 degree increments until there is no more material coming out of the extruder.
Sometimes you have to work with a material that is simply less viscous than PLA usually is and therefore flows more easily even at lower temperatures. We recommend increasing the return feed by a few millimeters (retract)
If the temperature is too low
You will notice that the filament either does not adhere to the previous layer and you get an uneven surface, or the part is not strong enough and is easy to separate. One way or another, you should increase the temperature by 5 degrees and continue to increase it until you get good cuts on each layer, and after printing the part is strong enough.
Filament change
PLA color change:
- Set the cold extruder to 80 °C and wait for it to heat up.
- When the temperature reaches 80 °C, remove the filament from the extruder. You can pull it out by hand, or reverse feed may be required.
- If you have trouble removing the filament, increase the temperature to 100°C and try again.
- Increase the temperature further and insert new filament in the usual way. nine0025 Run it through the extruder until it comes out clean, i.
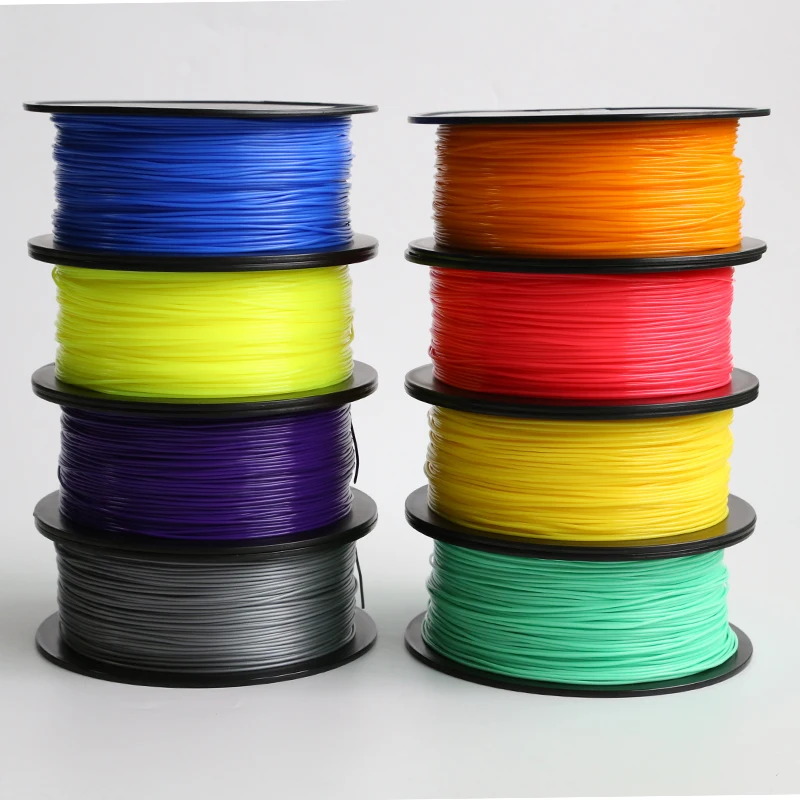
- Clean the extruder gear and blow out any particles from the inlet.
- Print something you don't mind if it has some previous color, or run the extruder for a few minutes. This process can take 10 to 15 minutes before you can confidently note that the dark material is no longer mixed with the light material. nine0026
We recommend removing the filament when it is in a soft, rather than fully melted state - then there is less chance of melted material depositing on the inside of the extruder or even before the melt chamber. In both cases, this kind of residue can lead to hard-to-remove clogging of the printing mechanism. You can also shove a flexible piece of filament through to make sure all contaminants are removed from the end of the extruder.
What to do if something is wrong
There are a few key things to check if printouts are not coming through. But before we consider the solutions, we must briefly characterize the symptoms.
"First coat does not stick at all".
- Make sure the extruder is at the correct height. Set the limiter or the extruder itself to a height of 0.
- Make sure the table is level. The gaps at all calibration points between the nozzle and the table should be approximately the thickness of a sheet of paper. nine0026
"Part has poor inner layers and top surface."
- Check extrusion temperature (you may need to increase it in 5 degree increments)
- Check filament tension.
- Clean the filament feed gear
“There are a lot of small bumps on the edges of my part.”
- Make sure the printer is getting enough data. When printing from a computer, make sure that it is not overloaded and sends commands to the printer normally. If the printer slows down, it usually means that it is overloaded.
nine0026
- Print from an SD card. On some printers, you can try printing from an SD card. This often helps the printer get enough data and run more smoothly.
- Buy better quality PLA. We have found that the quality of the source material can have a significant impact on print quality. Buying higher quality PLA can help you achieve better results. However, do not rush to blame everything on PLA. With the right settings and a lot of patience, 3D printers have been able to successfully print a wide variety of materials, many of which have very low viscosities and very large inhomogeneities. You have to be able to get at least functionality out of a part - even if with slightly lower quality filament. nine0026
"The vertical elements of my printout look melted or stuck together."
- Turn on "cooling". If your printer has a cooler, you must enable "cooling" in the print settings.
- Purchase a small fan. If your printer does not have a built-in cooler, you should consider looking for a small desktop fan.
This will greatly improve the situation with the vertical elements of your printouts and will help with "bridging" (where the top layer bridges the gaps on the bottom). nine0026
"My printer is not outputting any media."
- Make sure the hotend gets hot at all. If not, the printer needs to be serviced. Most likely, your connection is broken or the electronics are “fried” (this is if the printer is connected at all and responds to program commands :)
- Clean feed gear and adjust tension. The very first thing to do is to clean the feed gear that touches the filament and make sure the thread tension is correct. Incorrect tension or a clogged feed gear usually results in much the same pattern as a low filament temperature, but sometimes it will block extrusion altogether. Clean the pinch roller with a wire brush and make sure the filament tension is good and tight (too much can also interfere with extrusion, usually with direct feed printers - when the motor directly turns the feed gear; this happens less often with intermediate gears).
nine0026
- Remove the loaded filament. Perhaps small particles of plastic are stuck in the very tip of the extruder and clog it. Use the filament change technique described above to remove all particles from the end of the extruder.
- Check for blockage between extruder and hot end and correct. This problem is the most extreme because it can only be fixed by disassembling the extruder. Sometimes the filament from the hot end can flow back into the extruder, resulting in bubbles that then freeze and block further work. This usually happens at the junction of the extruder and the hot end. Remove the extruder and remove all the PLA you can (you may need to preheat the hot end to 80-100°C for this). If you can't remove all of the filament by pulling it out, you can try pushing it through the hotend. To do this, we usually use a small hex (inbus) key. If it still doesn't work, you can try drilling out the extruder or hot end, but then they may need to be replaced. Be sure to take precautions against electric shock and burns.
If you don't have enough experience, find someone who does - it's better than risking injury. nine0026
PLA print settings | How to choose modes for PLA filament
PLA plastic filament is used in FDM 3D printers. This is a truly amazing material that is environmentally friendly and non-toxic. During printing, it does not "stink", but emits a light aroma of popcorn. The thing is that it is made on the basis of natural plant materials - corn, potatoes, cane, etc.
If you compare PLA with ABS, it turns out that the former is harder, and therefore the process of applying the next layer will be slower. But this has a positive effect on the result of printing, because the products are smoother. However, this imposes its own characteristics on the print settings, the choice of which should be guided by the characteristics of the material. nine0003
PLA plastic specification
PLA plastic for 3D printer has a number of key characteristics. Depending on the brand, the properties may vary slightly. However, this material is characterized by:
- strength and rigidity;
- translucency and even transparency;
- wide range of colors;
- smoothness, detail of the finished models and a shiny surface.
PLA turns out to be easier to work with, ideal for those new to 3D printing as it doesn't warp or shrink like ABS. But it is less heat-resistant and already at 70 degrees it can begin to deform. nine0106
The most important layer in FDM 3D printing will always be the first layer. It must be fixed on the desktop to avoid further deformation. In this regard, PLA plastic is less demanding in comparison with ABS. But many use special substrates, blue tape or glue stick. You can print simply on glass, especially if the 3D printer is equipped with a heated table. The optimum temperature in this case will be 70 degrees, although in some cases, it has been experimentally established that the best results are achieved on a cold table. nine0003
The second point - it is important to correctly set the height of the extruder. The nozzle should be at such a height that a standard sheet can easily pass between it and the work table.
Next, you need to decide on the standard set of settings:
- temperature;
- layer thickness;
- table temperature (if heated).
Another important point to get the best print result from PLA is to use the blower at full power. So the plastic will be cooled in time and not deformed. nine0003
As with ABS, print performance will be derived empirically. For example, the temperature will be set to 200 degrees and then raised or lowered by 5 degrees until the best option is found, in which the layers will perfectly hold together, have time to freeze and not swim.
And the average print settings for PLA are as follows:
0002 Satisfactory + + normally + + Good + + + excellent + + + +
Simplify3D PLA print settings Below are the recommended settings for PLA plastic printing and job preparation in the Simplify3D slicer. |