3D print guinea pig
▷ guinea pig 3d models 【 STLFinder 】
Guinea Pig
thingiverse
It's a guinea pig.
Guinea Pig
thingiverse
A Guinea pig-looking critter
guinea pig
sketchfab
a low-poly guinea pig. ...free to use.
Guinea Pig
thingiverse
A guinea pig. ...These animals are actually not pigs, believe it or not.
Guinea Pig Guinea Pig Key Chain
cults3d
Key ring of a Guinea pig Easy to print in two colors
Guinea pig stencil 2
thingiverse
Guinea pig
Guinea Pig DODO
sketchfab
My Guinea Pig
Guinea Pig keyring
thingiverse
For guinea pigs lovers
Guinea Pig Cookie Cutter
thingiverse
Guinea pig cookie cutter. ...Drawn with cookiecaster.
Guinea pig cookie cutter
thingiverse
It is a guinea pig cookie cutter!
Guinea Pig Silhouettes
thingiverse
Just a couple silhouettes of guinea pigs I made for my Girlfriends guinea pig room.
Guinea Pig Cookie Cutter
thingiverse
A cookie cutter in the shape of a guinea pig
Guinea pig cutter
thingiverse
Guinea pig - cutter Approx 100 x 65 x 18 mm
Guinea Pig Charm/Keychain
thingiverse
This thing was made with Tinkercad. ...GUINEA PIGS!!!!!!!!!!!!!!!!!!!!!!!
guinea pig house
thingiverse
Silmple house for guinea pig using the cage for 2 walls
Ronin Guinea Pig
myminifactory
A fantasy samurai guinea pig armed with a sword and armour. ...Set includes the following -1 Sword armed guinea pig in samurai style armour Presupported version is provided but I recommend making your own for the best possible results
Guinea pig battle armour
cults3d
Designed on Tinkercad - fits well on our two guinea pigs and they look very sweet wearing it.
Guinea pig battle carrier
cults3d
Guinea pig battle carrier - for holding weapons / warriors while fighting the massed hordes of Mordor (especially Lego ones).
Guinea pig battle carrier
thingiverse
Guinea pig battle carrier - for holding weapons / warriors while fighting the massed hordes of Mordor (especially Lego ones). ... Instructions Print using support takes about 2 hours.
Guinea Pig Christmas baubles
thingiverse
A bunch of different guinea pig baubles for my GFs Christmas tree Customised but I aslo provide the basic one. ...
Should print with any PLA
Guinea pig battle armour
thingiverse
... Instructions Printed at 0.27 layer height, 100% infill and 2 shells on our Replicator 1 (with Frog tape). Put it on your guinea pig or other small pet. Could be scaled up to fit a dog, cat, human... ...etc.
Modular Guinea Pig Tunnels
thingiverse
I designed this modular guinea pig tunnel system in Tinkercad. The snapfit connectors should allow most orientations. I'm in the process of test-printing them but welcome to suggestions about how to improve these.
These are designed not to need. ..
Guinea pig left femur
myminifactory
This guinea pig left femur is from a specimen obtained by Bruce Manzano of the University of Kentucky from a pet store in Reading, Pennsylvania. ...It was 3-D scanned with a NextEngine Desktop 3-D scanner.
Guinea Pig Skull
myminifactory
This guinea pig (Cavia porcellus) skull was donated to the Virtual Curation Laboratory by Bruce Manzano of the University of Kentucky. ...It was 3D scanned with a NextEngine Desktop 3D scanner.
FT Guinea Pig
grabcad
FT Guinea Pig is a Cargo type RC plane designed by Flight Test. I have 3D modeled their design. ...(Only the design of the motor is downloaded from GrabCAD.)
Guinea pig radius
myminifactory
This guinea pig radius is from a specimen obtained by Bruce Manzano of the University of Kentucky from a pet store in Reading, Pennsylvania. ...It was 3-D scanned with a NextEngine Desktop 3-D scanner.
Guinea pig right tibia
myminifactory
This guinea pig right tibia is from a specimen obtained by Bruce Manzano of the University of Kentucky from a pet store in Reading, Pennsylvania. ...It was 3-D scanned with a NextEngine Desktop 3-D scanner.
Guinea pig scapula
myminifactory
This guinea pig scapula is from a specimen obtained by Bruce Manzano of the University of Kentucky from a pet store in Reading, Pennsylvania. ...It was 3-D scanned with a NextEngine Desktop 3-D scanner.
Guinea pig keychain
thingiverse
Se trata de un llavero de una cobaya. ...Tiene un pequeño orificio para poder colgarlo. This is a keychain of a Guinea pig . It has a small hole for being able to hang it. ...Print Settings Printer: Prusa i3
Guinea pig right pelvis
myminifactory
This guinea pig right pelvis is from a specimen obtained by Bruce Manzano of the University of Kentucky from a pet store in Reading, Pennsylvania. ...It was 3-D scanned with a NextEngine Desktop 3-D scanner.
Adorable Guinea Pig and Pets 3D Print Jewelry & Accessories 天竺鼠
$690.00
Colored / Brooch LargeColored / Brooch MediumColored / Magnet Large🧲Colored / Magnet Medium🧲Colored / Ring💍Colored / Charm Necklace MediumColored / Charm Bracelet MediumCopperfill / Ring💍Copperfill / Charm Necklace MediumCopperfill / Charm Bracelet SmallCopperfill / Charm Necklace SmallCopperfill / Stud EarringsCopperfill / Hair ClipCopperfill / CufflinksPLA / Ring💍PLA / Charm Necklace MediumPLA / Charm Bracelet MediumPLA / Charm Bracelet SmallPLA / Charm Necklace SmallPLA / Stud EarringsPLA / Hair Clip
Material
Colored
Copperfill
PLA
Type
Brooch Large
Brooch Medium
Magnet Large🧲
Magnet Medium🧲
Ring💍
Charm Necklace Medium
Charm Bracelet Medium
Charm Bracelet Small
Charm Necklace Small
Stud Earrings
Hair Clip
Cufflinks
Overview
Made to order and handcrafted
Ships worldwide from Hong Kong 🇭🇰
Free Shipping on any order of over HK$500 for the region of Hong Kong and Macau, over US$83 for other regions.
Packed in a card box 📦
Production Time⏳: PLA & Copperfill item shipped within 14 to 21 calendar days. Colored item shipped within 24 to 31 calendar days.
Once in production progress, returned, exchanged or refunded are not allowed.
👆360 3D model viewer
👆Guinea Pig Color ring
👆Guinea Pig Colored medium charm necklace/bracelet
Size & Weight
Dimensions📏
Charm Size Small: |
18W 16D 20H mm / 0.7W 0.63D 0.78H inch |
Charm Size Medium: |
22W 20D 25H mm / 0.88W 0.8D 0.98H inch |
Brooch🧷 / Magnet🧲 Size Large: |
38W 22D 43H mm / 1.5W 0.88D 1.68H inch |
Brooch🧷 / Magnet🧲 Size Medium: |
23W 15D 25H mm / 0.89W 0.59D 0.![]() |
Ring💍 Size inner diameter: |
from 15 to 22 mm / 0.6 to 0.87 inch * for accurate ring size measurement, please see optional tab |
Length of cord 🧵 Necklace & Bracelet: |
Necklace 80 cm / 31 inches Bracelet adjustable from 15 to 30 cm / 6 to 12 inches Cord color option in the optional tab Custom length available on request. |
Length of chain 🔗 Necklace: |
42cm / 16.5 inches For Copperfill item only. Custom length available on request. |
Weights (gram)⚖️
Colored Charm Small: | 1.2 g |
Colored Charm Medium: | 2.1 g |
Copperfill Charm Small: | 5.5 g |
Copperfill Charm Medium: | 10 g |
Brooch / Magnet Large: | 7 g |
Colored Ring Size #7: | 3 g |
Materials
Optional
Ring Size
Photo Requirement
Collections: Others
Some of the most amazing 3D printing materials currently available
3D printing with classic materials such as plastic, metal or ceramics is widespread. In the meantime, there are many alternative materials that are not only unusual, but can make a 3D printed part even more special. In our selection, we introduce you to these unusual materials. From chocolate and salt to recycled plastic waste or ashes, now you can create the most extraordinary items. In some cases, these materials are even proving to be a great alternative to plastic, reducing overconsumption and the associated environmental impact. Today we're going to take a look at these amazing 3D printing materials.
3D printing material from the sea
Today, filaments are still the most commonly used 3D printing materials, mainly because FDM machines are readily available. But did you know that some threads are made from shellfish and crustaceans? The French company Francofil offers materials from PLA and shells of mussels, scallops and oysters. Their shells come from recycled food service waste and are shredded to become threads. The materials are made in France and can be printed like normal PLA.
Photo: Francofil
Local Salt
Emerging Objects is an American company that uses new technologies with innovative materials to create impressive projects. Among the most prominent initiatives is Saltygloo, a salt 3D printed structure. The salt used was collected from San Francisco Bay. Due to climatic conditions, about 500,000 tons of sea salt are produced here annually. Salt has been used to additively manufacture lightweight structures on a large scale. In addition to Saltygloo, the company is known for other salt projects such as the GEOtube tower and building houses.
Photo: Matthew Millman
Chocolate is the sweetest 3D printable material
This 3D printable material may not be as exceptional as some of the others on the list, but it is certainly one of the most used. The chocolate 3D printing process is similar to FDM technology, but it has different cooling properties than plastic, so the process takes longer. The popularity of this technology has grown over the years, prompting many companies to develop various designs and even chocolate 3D printers. Among the best known is the collaboration between 3D Systems and Hershey's, one of the world's largest chocolate makers. We also featured some 3D printers that can make delicious sweets like mycusini or Print2Taste. If you want to know more about this technology, don't miss the video below.
3D printed material from the ashes to remember your loved ones
The Spanish company Narbón is introducing new technologies and innovations in the funeral industry. 3DMemories uses 3D printing to create original, unique and exclusive ceramic jewelry from the ashes, hair, DNA or skeletal remains of a loved one. To do this, the pattern must be processed and then combined with porcelain before the decorations can be 3D printed. Then the enamel is applied and the product is fixed. The service offers a wide range of products for men and women. Undoubtedly, 3DMemories with its range of jewelry is an exceptional way to remember a loved one.
Photo: Narbón
Wood-Based Threads
Wood or vegetable threads have also been available on the market for some time. For example, the Dutch company ColorFabb offers several alternative threads in this category. What started in 2014 with BambooFill has expanded in subsequent years with CorkFill and WoodFill. Wood fibers, usually blended with a PLA/PHA base, give parts a natural, high-quality finish. Whether used to make figurines, pieces of furniture, or wall decorations, the threads can be used anywhere the look of wood is desired. Since ColorFabb discontinued BambooFill, a similar product can be purchased in Wood Bamboo form from AzureFilm. According to the company, 40% of recycled wood is mixed with 60% of polymers for this purpose. However, to avoid problems when printing with this filament, it is recommended to reduce the print speed.
Left: ColorFabb, Right: Azure Film
Other Uses for Linen
Another alternative to traditional filaments is a composite of PLA and linen from French manufacturer Nanovia. The company says the composite is not only a sustainable alternative to traditional filaments, but also offers the ability to achieve different shades of brown by applying different print settings. This can be achieved simply by changing the print temperature during production. As for the finish, the manufacturer recommends sealing the printed parts with UV protection to keep them intact for as long as possible.
Photo: Nanovia
Sugar 3D Printing
Sugar Lab was acquired by 3D Systems almost ten years ago and, as the name suggests, has focused on sugar 3D printing. Using the 3D Systems ChefJet Pro printer, the company creates intricately shaped candies and decorations. The Los Angeles-based company claims to be able to produce candy in all flavors and colors. Whether it's birthdays, weddings or Christmas parties, The Sugar Lab offers all sorts of 3D printed candies. As for quantity, the 3D printer seems to be capable of producing up to 100 candies a day. While The Sugar Lab is the most famous company using sugar as a printing material, other companies like The Modernist Cuisine are also trying their hand at 3D printing with sugar.
3D printing with glass
Glass has been popular in many industries for many years and is also used in additive manufacturing. Several researchers, such as those at MIT or Lawrence Livermore National Laboratory (LLNL), have developed 3D printing solutions to print on glass. For example, an MIT team has developed the G3DP2 machine, which can process 5 kg of glass per hour. With this machine, the researchers were able to create three-meter-high glass columns at Milan Design Week. Recently, the Glassomer startup has also unveiled its glass 3D printing technology. The company is developing a material made from fine glass powder and a plastic binder that can be processed on SLA printers.
Photo: Glassomer
Recycled plastic filament
Sustainability is gaining more and more attention in additive manufacturing, and many companies are looking for alternatives. In recent years, several exciting products have been developed to make 3D printing more sustainable by making filaments from recycled plastic. One such project is Print The City by The New Raw, in which plastic from the waste of the people of Amsterdam and Thessaloniki is turned into 3D printed filament and used to print benches and other outdoor furniture. Another initiative is the Million Wave Project, which aims to produce recycled PET filaments for 3D printed prosthetic limbs for those in need. Another example is the ZUV tricycle, which was printed in Austria by EOOS using filaments made from 70kg of plastic waste from supermarkets in Vienna.
Photo: New Raw
Ivory Inspired 3D Printing Material
Among the many materials used for 3D printing, there are some that have been specifically designed to meet specific requirements and solve old problems in an innovative way. One such material is Digory, which was developed by the University of Vienna in collaboration with Cubicure GmbH to meet the need for the restoration of ancient ivory monuments and objects. It is a synthetic resin containing calcium phosphate particles and silica powder. Researchers have developed this new material with ivory-like characteristics and properties to restore objects using 3D printing or SLA technology. The similarity between these two materials is striking - there is almost no difference!
The Digory material on the right is very similar to the real ivory on the left (photo courtesy of Vienna University of Technology).
Clay as a greener material for 3D printing
One of the unusual 3D printing materials that has certainly attracted attention in recent years is clay. Technically, this is a subset of ceramic 3D printing that, although difficult to print, is known for its incredible properties, in particular the use of clay was especially popularized by the work of the Italian company WASP. For example, we recently saw WASP and Honda use 3D clay printing to create greener vehicles. There are many other uses, although many of them focus on sustainability due to the clay's properties. This can be seen in projects such as archiREEF terracotta tiles for coral restoration in Hong Kong, or 3D printed clay containers designed to reduce food waste.
Photo: Jonathan Keep
Diamond - 3D Printing of the Hardest Material on Earth
It may surprise many that one of the hardest materials on Earth, diamond, can actually be printed. Back in 2019, Sandvik Additive Manufacturing announced the first ever 3D printed diamond composite. It is not shiny, but will allow manufacturers to 3D print super-hard material, which will help revolutionize, especially in the tool industry. Diamond is often used in industries such as mining and drilling, machining, and medical implants, especially for its wear-resistant properties, but it is difficult to process. Sandvik claims that this breakthrough in composites will now allow very complex shapes to be 3D printed, and the company has high hopes for its use in the near future.
Human cell printing
When it comes to 3D printing in the medical sector, people often think of bioprinting. In bioprinting, cellular structures, including human structures, are made from bioink loaded with stem cells. As with conventional 3D printing, the biomaterial can be applied layer by layer to create things like skin, tissues, bones, and even organs. Although it is still in its infancy as a technology when it comes to creating viable long-term solutions, we have already seen a number of interesting projects using this technology. Notably, the researchers have been experimenting with 3D printing of organs, including the heart, kidneys, pancreas, and liver. Others have also developed a way to bioprint using ceramics and bioink to recreate bones in the human body.
Source
ANIMAL MOTHERS for 3D printing, 3D printing, 3D printing, ceramic 3D packets, thread for 3D printing, 3D printing sugar, 3D - glass printing, ash material 3D printing, chocolate 3D printing, salt 3D printing
We found out the dangers of 3D printing.
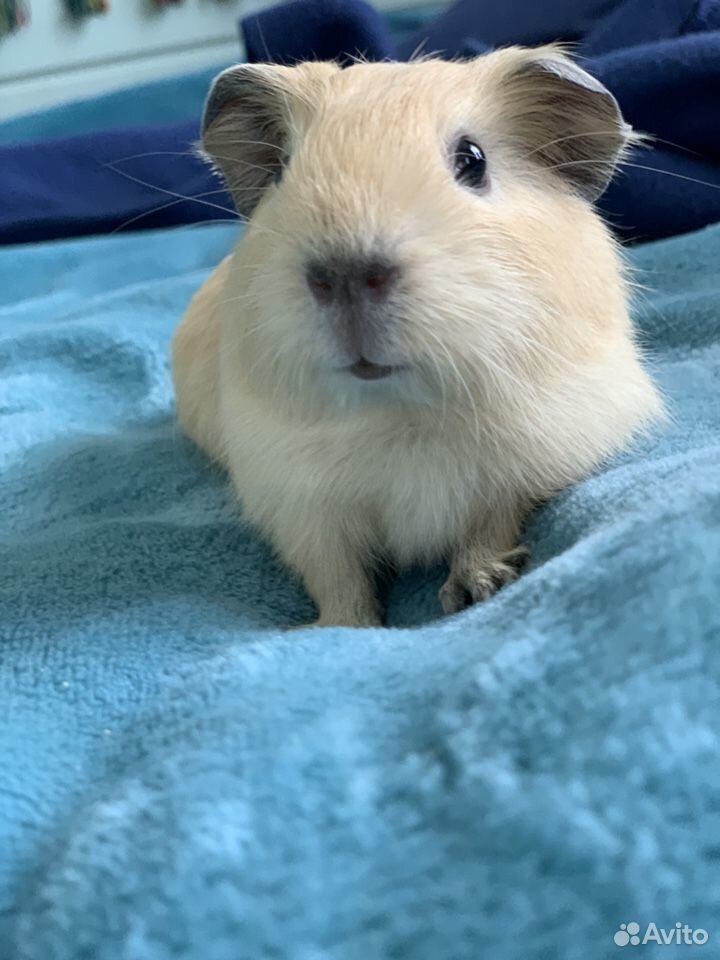
Vladislav Kochkurov General Director of the Center for Additive Technologies
The first product was 3D printed in 1983 - it was a small container in the form of a bowl. Now researchers are creating aircraft engines and rockets, jewelry, food, and even houses. Despite the fact that there is a lot of information about this area, many people still do not understand exactly how 3D printing works. Vladislav Kochkurov, General Director of the Center for Additive Technologies, talks about the misconceptions we face when talking about layer-by-layer creation of three-dimensional objects.
Read Hi-Tech at
Myth No. 1. 3D printing takes place almost without human intervention
When many people hear about 3D printing, they think of a 3D printer as the central part, which distributes consumables in layers - this is how a new product is born. One gets the false impression that the entire cycle of additive manufacturing consists only of the operation of equipment, and a person hardly participates in this - he only turns on a 3D printer and loads a polymer, metal powder or other material into it.
But the key role in building an object is played by its 3D model. It is a map on which the finished product will be built. The quality and characteristics of the future subject depend on its detailed study. Here, the participation of specialists with high competencies in the fields of design, technology and materials is needed.
In industrial production, the construction of a 3D model is carried out in AutoCAD computer-aided design systems. The design engineer, in accordance with the terms of reference and using various calculation methods, creates the geometry of the future product. Even if the 3D model already exists and does not need to be built from scratch, AutoCAD programs carry out its topological optimization - redesign for additive manufacturing.
This process aims to eliminate stress raisers and thin-walled features that can cause cracks or other damage during the printing process. Together with the 3D model, the location of technological supports is also designed - support structures needed for optimal positioning of the part on the platform, heat removal and reduction of the risk of deformation during the printing of the product. Printing is also preceded by the process of developing technological modes of construction, which is being worked on by a process engineer.
Further, based on the prepared 3D model, the printer prints on its own, sometimes working for several days in a row. But before that, the equipment needs to be prepared - make sure that the build platform is level and all the mechanisms move as they should. Even the powder in the 3D printer is not just poured, but goes through the stages of incoming control and preparation.
Another mandatory stage in the production cycle of a product, where human participation is needed, is post-processing.
Myth #2: A finished product comes out of a 3D printer
Many people think of 3D printing as it is shown in films. Robotic installations in a matter of minutes create superhero costumes and print elements of spaceships. Technology, of course, is striving for this, but today all products removed from the printer need post-processing.
To relieve internal stress that occurs during the printing process, the product undergoes alternating heating and cooling procedures. This way it achieves full mechanical properties. Then technological supports are cut off - they have already fulfilled their function. Removal of excess powder and surface treatment of the product are carried out using a sandblasting chamber. If it is necessary to achieve absolute smoothness of surfaces, then milling, turning, electrochemical and grinding machines are used. For plastic products, chemical post-treatment with acetone or other solvents is sometimes used.
Myth #3: You can 3D print anything
Innovations in the field of additive technologies appear every year and already surpass our imagination. Synthetic meat steaks, a human heart, and a whole house are already being printed. It seems that the possibilities of additive manufacturing are endless and a 3D printer can do anything. But now there are several limitations related to the size and material of the product - it is impossible to create very large and very small objects.
For example, the Center for Additive Technologies has an installation with a build chamber up to half a meter, the largest printer in Russia based on selective laser melting technology. Elements of Russian aircraft engines are already being “grown” there.
The capabilities of polymer printers are much wider - one of them, listed in the Guinness Book of Records, can create objects up to 30 m long. In 2017, a monolithic boat was printed on it, weighing 2 tons and 7 m long. The smallest object printed on a 3D printer is a ship. Its length is 2-3 times less than the thickness of a human hair - only 30 micrometers (0.03 mm).
3D printers are already used to create even at home. A construction printer works by analogy with an FDMD printer that prints plastic products, but instead of polymeric materials, cement mixtures are used as “inks”. In size, such a mechanism is much larger. The world's largest 3D printed building has an area of 641 square meters. m. and is located in the UAE.
Other limitations in additive manufacturing are not related to the size of the 3D printer's build chamber, but to the material used. During the printing process, it is in a liquid or molten state, therefore, it should melt normally. Wood, fabric, or paper objects cannot yet be printed, as they will burn before the material can be melted. Although here you can find a loophole: if you mix crushed cellulose fibers with a water-based gel, and then freeze the object, gradually removing water from it, you will get products made of a material similar to wood.
Myth No. 4. Products printed on a 3D printer are of poorer quality
Visually, the 3D printing process looks like a layer-by-layer application of material. This may raise the question: how firmly are the layers interconnected?
3D printing can introduce several defects, so it is important to follow the workflow. A lot depends on the quality of the materials. In industrial production, all metal powders undergo input control, this process is regulated by standards. Even if the material is certified, it is very important to observe the conditions for proper storage: avoid moisture and dampness, place in a special package. If you do not check the condition of the nozzle, set the temperature or print speed incorrectly, misalignment of layers, overheating, or other defects may occur.
If all the conditions are met, then the product will not be inferior in properties, and often even surpass the analog made by traditional methods. If you compare two aluminum objects under a microscope, the printed product will have a denser structure.
“If all conditions are met, then the product will not be inferior in properties, and often even surpass the analog made by traditional methods”Myth #5. 3D printing is environmentally friendly
3D printing is considered to be environmentally friendly, as this type of production leaves little waste. In fact, this is a complex issue, in which there is no consensus yet.
3D printers use a lot of electricity and leave a large carbon footprint: the ATKINS project found that the production of a product using additive technologies emits approximately 7 times more CO2 emissions 2 than the production of casting.