2023 3d printer review
Best 3D Printer for 2022
In the last few years, 3D printing has crossed a rubicon into the mainstream consciousness. Schools and libraries often have 3D printers, and the barrier to entry for hobbyists is lower than ever, with inexpensive machines offering excellent out-of-the-box results.
Because 3D printing technology has come a long way in recent years, I've doubled down on being creative and gotten into 3D scanning and laser cutting as well, which lets you sculpt real-world designs from leather and wood. Advanced printers are also using resin machines that create amazingly detailed prints.
Current 3D printers, which range from affordable (under $300) to high-end (over $4,000), are great gifts for a creative person in your life. Even better, they're great for you to craft your own personalized designs if you're looking to open an Etsy shop or something similar.
These models by Fotis Mint are extremely detailed.
James Bricknell/CNETWe've taken a deep dive into many of the best 3D printers available today. This list includes both small and large 3D printers, with attention paid to print speed, the size of the build plate, the cost of PLA filament, the kind of print head included and other important details. And once you've decided to take the plunge into additive manufacturing -- that's what 3D printing essentially is -- there's an FAQ below.
Our top picks
Dan Ackerman/CNET
Creality Ender-3 S1
Best step-up starter printer
I'd avoided Ender-3 printers for a long while, because they came in kit form and required many hours of assembly, setup and fine-tuning to use. For just a little more than the kit versions, the newer Ender-3 S1 comes nearly fully preassembled, and with high-end features like a direct drive extruder and self-leveling bed.
Print quality even out-of-the-box was excellent, although a lot of that comes down to having good models to work from. I'd love it to have a touchscreen and Wi-Fi, but apart form those missing features, this is a great way to get polished results from a $400 3D printer.
Read our Creality Ender-3 S1 review.
$399 at Amazon
Dan Ackerman/CNET
Anycubic Vyper
Best for out-of-the-box printing
The Anycubic Vyper FDM printer attempts to be both an affordable 3D printer and easy to use. It's a tricky needle to thread. Plenty of 3D printers offer automatic bed leveling and calibration to make sure prints come out even and firmly anchored to the print bed. This, however, is the first time I've seen a 3D printer run its bed leveling once, with zero manual input from me, and be totally good to go. I printed a 3D test file from the included SD card within minutes of powering on, and I've never seen a first print from a 3D printer come out so perfectly.
Read our Anycubic Vyper review.
$319 at Anycubic
$490 at Amazon
Anycubic
Anycubic Kobra Max
Best to make big projects easily
The Anycubic Kobra Max earned a 9 out of 10 in our recent review, in large part because it's one of the most enjoyable printers I've used in years. The build area is large enough to print entire helmets for cosplay, and the auto-bed-leveling system makes setting the machine up a breeze. The Kobra Max is the best choice for a large build area printer, bar none. --James Bricknell
Read our Anycubic Kobra review.
$549 at Anycubic
Entry-level 3D printers
Prusa Research
Prusa Mini Plus
Small but mighty
The Mini Plus is one of the best small-footprint printers you can buy. It has everything you would expect from a Prusa machine: Auto bed leveling, crash detection and great print quality, all for under $450. Building it with my son gave us a lot of good insights into how a 3D printer works, and potentially how to fix one.
$429 at Prusa Research
Sarah Tew/CNET
Anycubic Mono
Best inexpensive resin 3D printer
Resin printers are the next step up in rapid prototyping design technology when you want your printing to look as high quality as possible. Just be warned: The liquid resin is harder to work with, and it requires both good ventilation and a portable UV light to properly cure. This model is extremely popular with board game hobbyists who want to print pro-looking miniatures, and sometimes you'll see it fall in price. Note that you can save $20 at Amazon by activating the instant coupon on the product page.
$189 at Anycubic
$250 at Amazon
Dan Ackerman/CNET
Monoprice Mini Delta V2
Best for tiny desks
I had high hopes for this dirt-cheap 3D printer with a tiny footprint. It's usually under $200 and requires no additional assembly. And I do like it, but it's for a specific audience. This is not the great low-cost entry-level printer I was hoping for. It required some tweaking and troubleshooting to get up and running. The included microSD card was so cheap and corrupted it never worked, the built-in Wi-Fi was never able to connect to my network, and the machine's arms got caught on some poorly installed plastic wire covers (I just ripped the paper-thin covers off).
But once I had all the problems ironed out, it was a reliable little machine for quick jobs. It would make a great second 3D printer, or if you need to fit one into a small space. I especially liked the auto-leveling, which worked well, and the color touchscreen, which is a feature that often gets chopped from low-cost models. If you're willing to put a little effort into getting it set up correctly, it's a great printer for the price.
$175 at Amazon
Midrange 3D printers
Anycubic
Anycubic Photon Mono X
Best for mass-produced gaming minis
Standard resin printers are fine if you want to print small items or miniatures. For more oversized cosplay items, practical models or collections of gaming miniatures, you're going to need a bigger build area.
Enter the Anycubic Mono X, a resin printer that solves that issue by having a build plate nearly three times bigger than the standard Anycubic models. For example, I managed to print the entire blade of a Dune Crysknife, something that would have needed to be split into three parts if it wasn't for the extra build volume.
The Mono X also prints at insane speeds. Because resin prints the entire layer in one shot, they tend to be quicker than traditional FDM printers in the first place, but the Mono X takes this to the extreme with layers printing in as little as 1 second. It's incredible to watch. --James Bricknell
It's still cheaper to shop at Anycubic directly, but you can save $110 at Amazon by activating the instant coupon on the product page.
$349 at Anycubic
$660 at Amazon
James Bricknell/CNET
Flashforge Adventurer 4
Best 3D printer for ease of use
The Flashforge Adventurer 3 has long been one of CNET's favorite midprice 3D printers. The updated Adventurer 4 brings a handful of iterative improvements that make for a winning evolution. The Adventurer 4 is a fully enclosed unit, which helps control the temperature and block drafts. The build area is 220 by 200 by 250mm, and it has a system for easily swapping out nozzles -- all good features to have in a mid-level to high-end printer.
$849 at Amazon
High-end and professional 3D printers
Creality
Creality CR-30
Best for small biz or pro cosplayers
A word of warning; the CR-30 is not for the beginners out there. It is a complicated machine, and you will need some 3D-printing knowledge to really get the hang of it. It's also a very different beast, and instead of printing on a static-sized build plate, it uses a conveyor belt to create an "endless Z-axis." That lets you print very long things or lots of things over and over again.
If you are a cosplayer looking to make weapons or large armor pieces, the CR-30 gives you a lot of room to create. I've managed to print Squall's Gunblade from Final Fantasy VIII as well as the Whisper of the Worm from Destiny 2 (both were printed in two halves and attached together). It's great for small businesses looking to mass-produce small parts, and with just two CR-30s you could create a small empire on Etsy or Shopify. --James Bricknell
$1,100 at Crealty
$1,100 at Amazon
Sarah Tew/CNET
Glowforge 3D Laser Cutter
Best for woodworkers
I can't begin to tell you how much I love the Glowforge. Laser cutters can create projects from wood, leather, lucite and other materials, making it an interesting creation alternative to filament-based 3D printers. Even better, what would take a 3D printer hours to do takes just minutes in the Glowforge.
With it, I've created laser-etched LED lights, birch wood tool caddies, and even a three-tier box for my Nespresso sleeves. There's a robust community of makers creating and sharing files, but pretty much any line drawing you can create in something like Adobe Illustrator can be turned into a project.
The software is all cloud-based, which adds a layer of complication (you need internet service to use it), but the ability to create amazing gifts and more from simple 0.125-inch or 0.25-inch cheap plywood is pretty empowering.
See some of my laser cutter projects (and download my SVG files) here.
$3,995 at Glowforge (Glowforge Basic)
$4,995 at Glowforge (Glowforge Plus)
3D Scanners
Revopoint
Revopoint Pop 2
Incredible details
While the software has a pretty steep learning curve, the end result is extremely detailed. I've really enjoyed using the handheld version to scan larger models while the included turntable makes scanning smaller objects a breeze. If you are looking for a professional-grade scanner and can spend some time on the software, the Pop 2 is a great choice.
$800 at Amazon
Sarah Tew/CNET
SOL Desktop Laser 3D Scanner
Best 3D scanner for easy replicas
Recreate pretty much anything by putting it on this 3D scanner, where a rotating base and built-in camera create a 360-degree copy, which is then editable in any 3D program and printable on your 3D printer. Simply scan the object, import the scan into your slicing software for cleanup, and print. The included software alerts you of next steps in the printing process with either sound or texts. Scan quality and print resolution are great, and setup is easy, although you might want to clean up your 3D model a bit in a 3D software app after.
$614 at Amazon
3D printing FAQs
What material should I use to print with?
Most home 3D printers use PLA or ABS plastic. Professional printers can use all sorts of materials, from metal to organic filament. Some printers use a liquid resin, which is much more difficult to handle. As a beginner, use PLA. It's nontoxic, made mostly of cornstarch and sugarcane, handles easily and is inexpensive. However, it's more sensitive to heat, so don't leave your 3D prints on the dashboard of a car on a hot day.
Which brand of PLA is best?
Generally speaking, Hatchbox has never let me down and runs about $25 for a full 1kg spool on Amazon. Some of the printers I tested only accommodate narrower 0.5kg spools. In those cases, I sometimes used a larger Hatchbox roll with a separate spool-holder. Other times, I had good luck with AIO Robotics 0.5kg spools, which are a little more expensive, at $14 for 0.5kg. Amazon Basics and Monoprice can also be good, but for any brand, weird colors like metallic or glow-in-the-dark filament can be hit-or-miss. Note that a 1kg roll prints a lot of stuff.
What settings should I use?
Most 3D printers include or link to recommended software, which can handle converting 3D STL or other files into formats supported by the printer. Stick with the suggested presets to start, with one exception. I've started adding a raft, or bottom layer of filament, to nearly everything I print. It has cut down dramatically on prints that don't adhere to the bed properly, which is a common issue. If you continue to have problems, rub a standard glue stick on the print bed right before printing.
What are supports?
Your 3D models probably need some help to print properly, as these printers don't do well with big overhangs -- for example, an arm sticking out from a figure. Your 3D printer software can usually automatically calculate and add supports, meaning little stands that hold up all those sticking-out parts of the model. After the print is done, clip the supports off with micro cutters and file down any nubs or rough edges with hobby files.
Where do I find things to print?
Thingiverse.com is a huge online repository of 3D files for anything and everything you can think of. Pokemon chess set? It's there. Dyson vacuum wall mount? You bet.
When you're ready to create your own designs, there are a ton of software packages to choose from, but it's easiest to start with the browser-based free TinkerCad app from Autodesk.
Crazy things I've made on a 3D printer
+15 more See all photosMore creative recommendations
- Best 3D Printer Filament
- Best Budget 3D Printer
- Best Laptops, Desktops and Tablets for Designers and Creatives in 2022
- Best Vlogging Camera for 2022
- The Best 3D Printer Resin
Best Budget 3D Printer 2022: 6 Great Printers at a Price You'll Love
It costs less than ever to get into 3D printing, with printers available for under $200. The catch is that these budget machines usually require some tweaking to get right. You'll save money, but it's a rough and tumble way to get started.
3D printing -- or additive manufacturing to give it its scientific name -- has been around a long time now. It's a fun way to create models that can be practical, or just for fun. You can print giant pieces of cosplay armor, or small statues to give as gifts. You can even buy a few printers, open your own Etsy store and make yourself a tidy profit.
These budget 3D printers all cost under $500 (though prices can drift a bit month to month), and some are better suited to beginners than others. Our list of picks for best 3D printer overall covers a much wider range of choices, but these are excellent for getting started or for buying several at once!
Dan Ackerman/CNET
Anycubic Vyper
Our top pick
The Anycubic Vyper is easily the best budget 3D printer available now. Unlike a lot of other low-cost printers, the Vyper includes high-end features that make the entire experience better. There's a filament run-out sensor and a power loss detector. The automatic bed leveling helps produce a worry-free finished product.
$430 at Amazon
Creality
Creality Ender 3
Community favorite
The Ender 3 is one of the bestselling 3D printers of all time. Its under-$200 price removes a huge barrier to entry for anyone looking to spend as little as possible for their first machine.
Its popularity means there is a huge community of people to help you get it set up and working -- it's not exactly plug-and-play -- and you may need to spend a fair amount of time tweaking the Ender 3 to get it to print as well.
$189 at Amazon
Prusa Research
Prusa Mini Plus
Small but mighty
The Mini Plus is one of the best small-footprint printers you can buy. It has everything you would expect from a Prusa machine: Auto bed leveling, crash detection and great print quality, all for under $450. Building it with my son gave us a lot of good insights into how a 3D printer works, and potentially how to fix one.
$429 at Prusa Research
James Bricknell/CNET
Elegoo Neptune 2
Keep it simple
The Elegoo is one of my favorite ultra-cheap printers. When testing it, I kept expecting it to fail and it just didn't. It produced amazing results for the price, and continues to do so every time I use it. It doesn't have auto bed leveling, but the Elegoo was easy to set up. And because it's based on the popular Ender 3, it has a lot of mods available to make it even better.
$180 at Amazon
Dan Ackerman/CNET
Creality Ender 3 S1
Direct drive with advanced features
As Dan Ackerman said in his review of the Creality Ender 3 S1 "At $399, the S1 version of the Ender-3 is about $100 more than older versions but includes so many upgrades and quality of life features that it qualifies as a great beginner-friendly, plug-and-play printer. "
It's also a great budget-friendly Direct Drive printer, making it easier to use for materials such as TPU.
$400 at Amazon
Resin 3D printers for beginners
Most beginner printers use plastic filament to create models, but there are plenty of affordable resin 3D printers, too. Liquid resin is a little more difficult to use than standard 3D printing material, and requires safety equipment. But it also produces amazingly detailed results.
Elegoo
Elegoo Mars 3
The best starter resin printer
This small resin printer is Elegoo's latest model in its popular Mars line. Because of the 4K monochrome LCD (these printers use light from an LCD to cure liquid resin) it can print much faster than older printers. The level of detail on models is something that standard 3D printing simply can't reproduce. At this price, the Elegoo Mars 3 is the best resin printer for the money.
$255 at Amazon
James Bricknell/CNET
Anycubic Mono X
When you need it bigger
This is expensive for a budget printer, but well worth it if you want a large enough print area to make something special. I have been using this as my main resin printer and it can handle anything I throw at it, from a D&D miniature army to highly detailed sculptures.
$500 at Matterhackers
$450 at Amazon
James Bricknell/CNETFrequently asked questions
What material should I use to print with?
Most home 3D printers use PLA or ABS plastic. Professional printers can use all sorts of materials, from metal to organic filament. Some printers use a liquid resin, which is much more difficult to handle but offers sharper details. As a beginner, use PLA. It's non-toxic, made mostly of cornstarch and sugarcane, handles easily, and is inexpensive. However, it's more sensitive to heat, so don't leave your 3D prints on the dashboard of a car on a hot day.
What settings should I use?
Most 3D printers include or link to recommended software, which can handle converting 3D STL or other files into formats supported by the printer. Stick with the suggested presets to start, with one exception. I've started adding a raft, or bottom layer of filament, to nearly everything I print. It has cut down dramatically on prints that don't adhere to the bed properly, which is a common issue. If you continue to have problems, rub a standard glue stick on the print bed right before printing.
What are supports?
Your 3D models probably need some help to print properly, as these printers don't do well with big overhangs -- for example, an arm sticking out from a figure. Your 3D printer software can usually automatically calculate and add supports, meaning little stands that hold up all those sticking-out parts of the model. After the print is done, clip the supports off with micro cutters and file down any nubs or rough edges with hobby files.
How we test
Testing 3D printers is an in-depth process. Printers often don't use the same materials, or even the same process to create models. I test SLA, 3D printers that use resin and light to print, and FDM, printers that melt plastic onto a plate. Each has a unique methodology. Core qualifiers I look at include:
- Hardware quality
- Ease of setup
- Bundled software
- Appearance and accuracy of prints
- Repairability
- Company and community support
A key test print, representing the (now old) CNET logo, is used to assess how a printer bridges gaps, creates accurate shapes and deals with overhangs. It even has little towers to help measure how well the 3D printer deals with temperature ranges.
James Bricknell/CNETTesting resin requires different criteria so I use the Amerilabs standard test -- printing out a small resin model that looks like a tiny town. This helps determine how accurate the printer is, how it deals with small parts and how well the UV exposure works at different points in the model.
Many other anecdotal test prints, using different 3D models, are also run on each printer.
For the other criteria, I research the company to see how well it responds to support queries from customers and how easy it is to order replacement parts and install them yourself. Kits (printers that come only semi-assembled) are judged by how long, and how difficult, the assembly process is.
2023 Czinger 21C Prototype: 3D Printed Sports Car
"It's better than a GT3 race car," said professional Czinger racer and driver Joel Miller, "but not quite an LMP car yet." He knew. Miller has been racing sports cars and Le Mans prototypes for over a decade. Sure, the engineer Czinger hired to fine-tune the behavior of its hypercar will say nice things about his own work, but our ride in the back seat of the Czinger 21C convinced us he wasn't exaggerating.
Wait, what?
Whether you're looking at or driving the 2023 Czinger 21C, it's hard to believe the car is officially road legal, thanks in part to the Michelin Pilot Sport Cup 2R tires. Thanks to the tandem seating arrangement in the car and the huge aerodynamic elements, it looks like a toy sports car to the whole world.
Getting down to business, it's hard to believe that the Czinger gets that much grip from street asphalt. The 21C features a 1,350bhp hybrid powertrain that sends most of the 1,050bhp to the rear wheels, in a car that the LA-based company says weighs less than 1,315kg. Balancing these wild stats is a claimed downforce of 637kg at 160kph and downforce of 2,550kg at 320kph, the limit of what the tire sidewalls can take before they just burst.
The result is a car that feels like a high downforce racing sports car from the rear passenger seat. The powerful lateral acceleration it pulls is matched by downforce to keep the car stable. No other road race car we've driven handles so confidently through corners at these speeds.
The Czinger 21C is rock-solid under heavy braking, with massive 16.1" front and 15.4" rear carbon ceramic brakes to slow down any speed that the two front electric motors and 2.8 kW battery can't handle* h.
Czinger is still developing traction and stability control systems, and Miller went lapping the Thermal Club circuit in South Palm with the systems on. He said the transmission could actually rip the tires off the car if it really tried to, so he deliberately adopted a moderate understeer setup with gradual breakaway at the limit. As a result, in his opinion, amateur drivers will feel comfortable behind the wheel: "It won't scare them."
Indeed, according to Miller, stability at high speeds is the main strength of the Czinger 21C. Czinger claims that in its optional low-drag configuration, the 21C can reach 407 km/h. This version has yet to be built, but Miller said the downforce model feels great at high speed, which can't be said for the equally radical-looking McLaren Senna (whose 21C set the Laguna Seca stock car lap record).
Monster view
Impressive as the car is, the back seat is not the place to experience it. The seats are built into the bodywork, covered only in thin, durable padding, and have no props to hold passengers in place. We just put our hands on our sides. At least there is enough legroom. Getting in and out of the back seat is, as you might imagine, wildly ugly.
We weren't able to test it in the front seat for the simple reason that there is only one Czinger 21C prototype and the company is not prepared to let outside employees or developers fly it. It's not that it couldn't print multiple extra copies (more on that in a moment), but the car's modularity is what allowed the manufacturer to quickly and easily replicate the same car over and over again. It's version 10, which is crazy considering it was created as version 1.0 just two and a half years ago.
During this time, everything has changed a lot. The 21C got a stunning 8.0 inches wider when the former Williams Formula 1 aerodynamicist went overboard and made a significantly wider front splitter and rear diffuser to achieve the Czinger's desired performance. The wheels, as well as the suspension and bodywork, also got wider when the team switched to the latest, biggest Michelin tires.
3D Revolution
If this all sounds crazy, it's because no one else builds cars like Czinger. The vast majority of 21C is 3D printed on the largest and most advanced printers in the world. While regular 3D printers use four lasers, Czinger printers (built by parent company Divergent) use 12 lasers and are already building the next generation printer. They are powered by new aluminum alloys developed by Divergent scientists specifically for their end use. These massive printers can process the same complex parts that used to take days to print in a matter of hours.
As with most 3D printers, the chamber in which the part is created is only the size of the inside, so to create larger assemblies, such as, say, an engine stand, several smaller parts must be joined together. Each part has tongue and groove seams at the ends, and they are fastened together with two proprietary adhesives. The former cures in 2.0 seconds when exposed to ultraviolet light that enters through tiny windows on the side. Its job is to hold the pieces together while the base adhesive cures for an hour. However, the first adhesive is strong enough to hold everything together while the assembly is assembled without any external support.
With such freedom of production, the entire assembly process on the assembly line needed to be rethought. Parts don't move on conveyor belts at the station, where more and more pieces of stamped metal are welded to them. Instead, the robots are arranged in a circle. One robot in the center picks up the first part and holds it in place while other robots reach out and apply adhesives and additional parts. The robots use lasers and cameras to see each other and details rather than relying on pre-programmed positioning. Within minutes, the complex component comes together and is ready for final assembly after an hour of curing.
How is it done?
As wild as the manufacturing process is, the software that makes it all possible is a real breakthrough. Called the Divergent Adaptive Production System, it takes 3D modeling and automates it in part, then presses the fast forward button. The engineer tells the software the basic parameters of the part, such as the space it should fit in, the loading paths it should handle, where it should connect to other components, how much it might cost to manufacture, and more, and it does the rest. The AI-driven software runs thousands and thousands of simulations, each adding and removing material until it reaches the final part.
According to Divergent, the result is the absolute best solution for the criteria given by the software. Every piece of metal is needed, and no detail is foreign: every piece of metal is exactly where it needs to be to complete its task. No scrap metal is generated, except when machining to very tight tolerances is required.
The Big Picture
Car company Czinger is Divergent's proof of concept. The 21C has done everything that can be 3D printed, from the chassis to the steering wheel and the crazy one-piece wheel hub and brake caliper behind each partially 3D printed wheel. (At the moment, the company is using carbon fiber rims, but Czinger hopes to eventually print the entire wheel.) What's left is carbon cladding, leather interior, a hybrid system and a clean 2.9liter V-8 twin-turbocharged engine. The engine block and head are machined from billet aluminum, but Czinger is also working on 3D printing them.
21C is hand-built because hypercar manufacturers can afford it. A company seeking to scale up this technology will use a traditional assembly line after printers and circular robots have done all the parts.
Specifications
Base price | 1315 kg |
Wheel base | 106.0 inches |
D x w x in | .0 x 80.7 x 43.0 inch |
0-100 km/h | 1.9 sec. |
for sale | 2023 |
5 ways, in which 3D-first changes the automotive industry / Habr
Source ALL3DP. com
Article from the FormLabs.com adapted and admitted for you shop.
You can't buy a fully 3D printed car at a car dealership yet, but additive technologies have been used in car design for many years. Every year, especially in recent years, 3D printing is taking an increasingly important place at all stages of production. This is evidenced by the rapid growth of 3D printing market share in automotive manufacturing, which is projected to reach $2.5 billion by 2023.
For example, luxury car companies including Bentley, Porsche, BMW and Ferrari are using 3D printing to create custom car interior parts. GM, Volvo, Ford are using 3D printing to produce tooling to save money, improve designs and reduce delivery times.
Source 3dprinting.com
3D printing is constantly emerging with new opportunities, it is becoming more accessible. If the first 3D printers cost about $20,000, now you can find 3D equipment for $100. Now companies can, with the help of additive technologies, produce the necessary components directly at their own enterprises and not depend on suppliers.
With new materials, 3D printers can print high-precision, functional end parts. Additive technologies facilitate the production of custom products and increase productivity.
But this is only the beginning of the journey. Here are five key ways 3D printing is driving innovation in the automotive industry, from car design to production. Plus one bonus.
1. Changing the prototyping process
It was with the manufacture of prototypes that the use of 3D printers in the automotive industry began. 3D printed prototypes took much less time than traditional methods required.
Using Raise3D 3D printers and ideaMaker software, Crazy Grandpa Garage was able to automate the process of creating custom car parts. Production costs have been reduced by 50%, design reliability has improved significantly, and lead time has been reduced by 83%. The parts now come out very well fitted to the car.
Source: facebook. com
Using 3D printing, car designers can quickly prototype individual parts or assemblies, from interior detail to dashboard, or even full-size car models. Thanks to 3D prototyping, the initial idea quickly turns into a physical embodiment of the concept - a conceptual model. The concept can then be developed into full-featured, high-fidelity prototypes, and after several validation steps, mass production begins. For the automotive industry, getting through these steps quickly is vital, and the entire downtime of an automobile production line in just an hour is very costly for the company.
For example, the assembly plant of the American car manufacturer General Motors claims to have saved more than $300,000 by purchasing a 3D printer in 2016.
Ringbrothers designers and engineers are not dependent on third parties to implement laser stereolithography (SLA) in their facility. The cost is reduced, the development time is reduced. Source: formlabs. com
Hose for Eventuri BMW M4, Source: ultimaker.com
Traditional prototyping was time consuming and costly, in part because the product went through more iterations. With 3D printing, you can create high-quality prototypes in one day and at a much lower cost. More examples.
The Ford Fiesta ST with 3D printed parts, ext. SEMA 2016, ultimaker.com
For example, General Motors has partnered with Autodesk to produce low cost, lightweight automotive parts using 3D printers. Tools, fixtures and fittings can now be produced at a fraction of the cost, according to Autodesk. For example, a 3D printed tool used to align engine and transmission ID numbers costs less than $3 at General Motors. A traditionally produced instrument will cost $3,000. In addition, downtime due to faulty tools can be significantly reduced as new tools are produced in-house.
2. Creation of non-standard and complex parts
Daihatsu, Japan's oldest car manufacturer, launched a project in 2016 to customize its Copen model.
Source: 3dprint.com
In partnership with Stratasys, Daihatsu customers can design and order custom 3D printed panels for their front and rear bumpers with a choice of over 15 basic patterns in 10 different colors.
Source: 3dprint.com
In Europe, the BMW MINI brand also uses 3D printing to create personalized car parts. Since the beginning of 2018, MINI customers have been able to personalize various trim elements such as the instrument panel, LED treadplates and illuminated bumpers, as well as choose from different colors and textures. These parts are then 3D printed using a range of technologies from DLS Carbon to SLS.
Source: formlabs.com
Volkswagen Motorsport's I.D. R Pikes Peak is designed with over 2000 3D printed test parts.
Source amfg.ai
The use of 3D printers makes it possible to experiment in the development of non-standard designs, reduces the cost of their production. Long production processes for custom-made products are becoming much shorter.
Ringbrothers uses 3D printing to create customized end pieces, such as ventilation grilles. Source: formlabs.com
Large companies are merging 3D printing technologies with traditional manufacturing methods. Volkswagen has recreated its iconic 1962 Microbus by replacing the petrol engine with a 120 hp electric one. The Type 20 concept electric minivan has received many improvements using 3D printed parts. These improvements include cast aluminum wheels. Even the wheel hubcaps, while looking like stamped steel, are actually printed on a Formlabs SLA 3D printer, then electroplated and polished.
Source: formlabs.com
Formlabs Form 2 3D printer SLA specifications
Bentley has used cutting-edge metal 3D printer technology to produce a grille, side vents, door handles and exhaust pipes much more complex than those used on current production models.
Bentley used metal 3D printing to create intricate micron precision parts. Source: formlabs.com
Source: youtube.com
3D printing has also made it possible to create parts that could not be made in any other way.
Bugatti's monobloc brake caliper is a prime example. For some components, Bugatti would have preferred titanium due to its high performance, but processing this metal with traditional methods is expensive and difficult. 3D printing has allowed Bugatti to produce a titanium alloy brake caliper. Due to the thin walls, the caliper turned out to be very light - almost two times lighter than forged aluminum. At the same time, the strength of the 3D-printed monoblock is superior to that of aluminum. The 3D printed titanium monoblock has a tensile strength of 1250 N/mm2. This means that a force of just over 125 kg will be applied per square millimeter of this titanium alloy without tearing the material. The new titanium caliper is 41 cm long, 21 cm wide and 13.6 cm high and weighs only 2.9kg compared to currently used aluminum, which weighs 4.9 kg.
Source: youtube.com. Source: formlabs.com
3. Tool making
Various devices help to facilitate and speed up the production and assembly processes, improve the safety of workers. Automotive factories and component suppliers use a large number of non-standard tooling that is specifically designed and optimized for end use. As a result, a lot of non-standard equipment and tools are made, which increases production costs.
This 3D protective wheel disc was purchased for 800 euros but can now be printed for just 21 euros. Tool development time has been reduced from 56 to 10 days.
Source: ultimaker.com
Outsourcing custom tooling and fixtures to service providers who machine parts from solid metal or plastic stock can delay production by weeks.
For example, the development and prototype of a commutator motor using traditional manufacturing methods can take up to four months and cost about half a million dollars. Thanks to 3D printing, Ford was able to develop several variants in just 4 days and 99.4% cheaper - only $3,000.
Source: youtube.com
Additive technologies allow you to complete the task in a few hours and significantly reduce costs compared to ordering from a third-party enterprise. Since increasing the complexity of a 3D printed model does not incur additional costs, products can be better optimized for their application. New elastic materials for 3D printing in many cases allow you to print plastic parts instead of metal or create prototypes on a 3D printer to test the tool before using it in production
Gradually, the production of 3D printed accessories and tools is becoming one of the largest applications of additive technologies.
Pankl Racing Systems uses 3D printed fixtures to fasten workpieces to a conveyor belt. Source: formlabs.com
For example, Pankl Racing Systems uses multiple Formlabs SLA 3D printers to make critical manufacturing tools. The multi-stage production of parts for transmissions on automatic lathes requires a series of fixtures and tools designed for each specific part.
With the help of 3D printing, Pankl's engineers have reduced the production time for the aids by 90%, from 2-3 weeks to around 20 hours. Costs were also reduced by 80-90%, saving $150,000.
The transition to 3D printing has enabled Volkswagen Autoeuropa to cut tooling development costs by 91% and tooling time by 95%.
4. Troubleshooting Parts
Spare parts have always been a problem for the automotive industry. The demand for them is either there or not, so the production of spare parts is not economically viable, and the storage of pre-fabricated replacement components is also costly. But if there are no repair parts available, difficulties arise and the main product becomes less valuable.
3D printing could solve the problem of parts in the automotive industry in many ways. The main factors are printed materials, which can match the characteristics of traditional materials used in parts and be cost-effective. There are prerequisites for this.
Using computer-aided design, drawings of all parts can be stored digitally, so there is no need to store the parts themselves. The parts needed by the client can be printed on a 3D printer right in the workshop.
Even obsolete parts whose drawings have not survived can in principle be recreated by making a 3D scan of existing parts of this type and applying reverse engineering (reverse engineering). You can read more about this on our blog. Old projects can take on new life. There are many lovers of vintage cars, with the help of 3D printing it would be possible to create parts for them.
Ringbrother 3D printed the Cadillac emblem for a custom built old car. Source: formlabs.com
5.
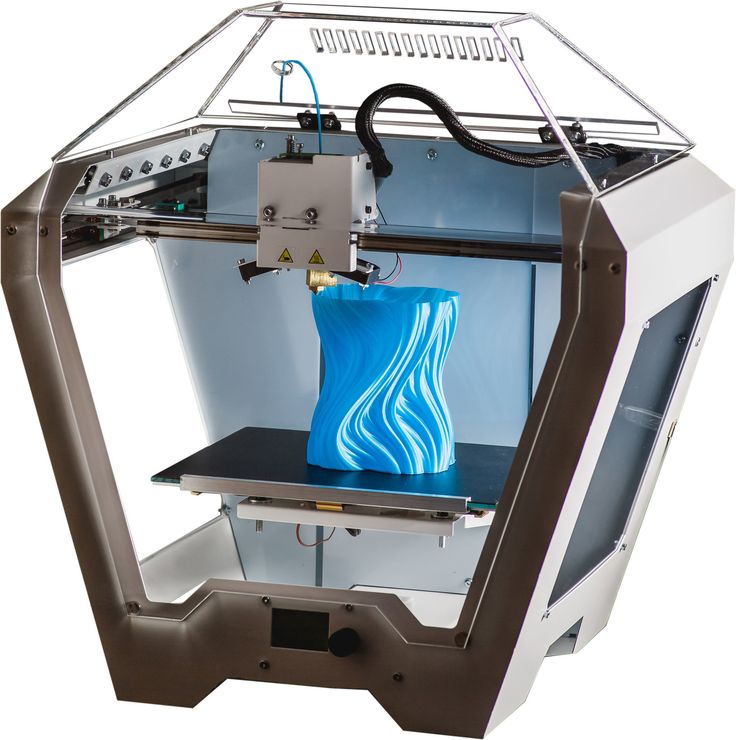
As 3D printers and materials for 3D printing become more affordable, a gradual transition to the production of mass-produced automotive parts using additive technologies is possible.
3D printing makes it possible to combine components into a single whole. Let's say there is a mechanism assembled from six or seven car parts that can be combined into one printed part. It will save time and assembly costs. With 3D printing, it is also possible to reduce the weight of the combined assembly, as a result, the car will use fuel more efficiently.
3D Systems has developed an advanced exhaust pipe for a sport bike. In the image below, you will see 20 sheet metal and hydroformed parts needed to assemble the original exhaust pipe. On the right is a monolithic exhaust pipe that does not require assembly, made using metal 3D printing.
Source designnews.com
The 3D printed tube was produced using Grade23 titanium in just 23 hours, compared to three weeks for traditional production. Design development time reduced from 6 weeks to 6 days. Additive manufacturing also eliminates the need for tooling, fixtures, multiple welding and multiple inspections.
Geometry optimization has reduced the amount of material required for maximum productivity. All elements of the original exhaust pipe are incorporated into the new design and, when printed with a typical wall thickness of 0.5mm, the 3D printed exhaust pipe is about 25% lighter than the original one.
A wide range of 3D printing materials is beginning to meet the requirements of various vehicle components. Since additive methods reduce costs compared to traditional methods (such as molding and injection molding), it makes a lot of sense from a production and financial point of view to further introduce 3D printing into the production of basic parts.
Volkswagen, one of the world's largest and most innovative car manufacturers, is using an HP Metal Jet 3D printer to produce high-performance functional parts with special design requirements, such as shift knobs and mirror mounts. Volkswagen's long-term plans to work with HP include accelerating the production of mass-customized parts such as key rings and exterior nameplates.
Source: youtube.com
+1. 3D printed cars
While 3D-printed cars have yet to hit the market, there are some interesting designs and concepts that can suggest a possible direction for the automotive industry.
Light Cocoon . German engineering firm EDAG was clearly inspired by nature to create the 3D printed supporting structure of the Light Cocoon concept car. The frame resembles the veins of a tree leaf or its branch. Despite the fact that the design of the EDAG took less material than a conventional frame, all the strength requirements for structurally significant components are met. Outside, the case is covered with a lightweight and durable waterproof fabric.
The cover protects the EDAG Light Cocoon from bad weather and gives the car a unique personality. Source: formlabs.com
Blade . Blade ("Blade") announced as "the world's first 3D-printed supercar." It meets supercar standards but is made from inexpensive materials: carbon fiber tubes and aluminum rods, combined with 3D printed metal parts. Blade turned out to be very light and does not take long to assemble.
The world's first 3D printed Blade supercar. Source: formlabs.com
Strati . The American company Local Motors 3D printed and assembled the Strati electric car right at the exhibition stand, in just 44 hours. Most of the components were printed - the body, seats, interior parts. A car is made up of less than 50 assemblies, far fewer than the thousands of parts that go into a traditional car. The company intends to reduce the print time to 10 hours.
Local Motors Strati is made up of less than 50 individual parts*. Source: formlabs.com
LSEV. Developed by the Italian company XEV, the LSEV could be the first in the 3D printed electric vehicle market when it goes on sale.