3D printer sydney
Sydney 3D Printing Service - FREE SHIPPING
3D printing provides an opportunity for you to see your idea completely materialised in physical form. Traditionally, creating an item of this nature would require contracting a company in manufacturing, which would cost a lot of money because major manufacturers produce items in mass for large scale sale and distribution, as opposed to 3D printing where you can custom create an item to suit your needs in a fraction of the time and cost. The following are the most significant advantages to 3D Printing:
1. Faster Turn- Around Time
3D Printing is faster than traditional subtractive and injection-mold methods. Whether it be a test model or a prototype product, 3D Printing provides the flexibility and consistency for the benefit of clients and customers alike.
2. Quality
3D Printing eliminates the potential for poor craftsmanship and human error. Optimised design based on the specifications of the required object to be printed and based on the type of printer, helps to minimise the risk of a failed print and can help to reach a positive outcome
3. Affordability
Conventional manufacturing is predominantly large scale operations, whereby heavy machinery is operated by highly skilled technicians, this process is costly taking into consideration the cost of labor and the cost of operating the machines. 3D printing on the other hand, significantly reduces the chain of command and over-heads; and often a single operator initiating a print command will suffice.
4. Testing
Due to the luxury of fast print and turn-around time, the opportunity to do extensive testing is afforded. You are able to conduct comprehensive testing in order to locate potential flaws and if necessary, make digital modifications to the CAD design file to initiate a re-print.
5. Freedom to Customise
Conventional manufacturing is based around the idea of mass production for mass consumption, there is very little room for customisation. Whereas in the case of 3D Printing, the opportunity to create a fully customised and personalised object is afforded, the only limitation, in this case, is the creativity of the designer and the capacity of the chosen printer.
6. Risk Mitigation
Rather than producing items on a large scale, which has been the case traditionally, and running the risk of a bad production line due to minor flaws; 3D Printing gives the benefit of producing on a small scale for testing before embarking on potential major production.
7. Diversity In Choice of Raw Material
3D Printing provides a wide array of options with regards to the material that can be used to produce a physical object. Some of these include plastic, glass, metal, wood, paper, bio-material, ceramics, etc.
8. Less Waste
Conventional manufacturing processes involve the production of a lot of waste due to the subtractive approach, however 3D printing being an additive approach uses much less waste often only requiring the material needed to produce the object and in some cases minor support material.
9. Health And Safety
Less human resources mean a reduction in risk of injury. Furthermore, eliminating the need to operate heavy machinery means less potential for short term and long term health issues.
10. Education
Being a relatively new technology, 3D Printing provides the opportunity to learn, the same way that the introduction of personal computers to schools changed the way children learned in the early ’90s, introducing 3D Printers into schools and incorporating them as a learning tool in the curriculum can influence an entire generation. 3D design and printing teaches students how to create an abstract digital design and then watch it come to life reducing the need for physical craftsmanship. The trial and error process can also help students to understand optimisation methods and design techniques in dealing with complex prints; locating flaws and making necessary digital changes to understand why a print may have failed and rectify it. Moreover, 3D Printers are usually modular, this can also be a teaching mechanism, whereby changing, replacing and modifying internal printer parts can become part of the learning process.
SLS 3D Printing Service in Sydney – 3D Printing Studios
Our 3D Printing Capabilities
3D Printing
3D Printing Studios has one of the widest 3D Printing capability in Australia, Singapore and Malaysia. Whatever your project we have the right technology to bring it to life. Our highly skilled team of designers and engineers know which 3D Printing technology is right for which projects, so contact us today or head into one of our studios.
Instant 3D Printing Quote
Fused Deposition Modelling (FDM)
FDM is a great technology for producing quick turnaround prints. It is used extensively in the studios as it offers a large range of material options. The maximum print size is 900 mm x 605 mm x 900 mm (H)
Read More
HP Multi Jet Fusion (MJF)
HP Multi Jet Fusion is a new additive manufacturing method invented and developed by the company Hewlett-Packard (HP). Parts produce by this technology is strong and durable close to a machine or injected molded part. Effective build area is about 380 x 284 x 380mm.
Read More
Selective Laser Sintering (SLS)
SLS produces strong models. It uses Polymide which is a Nylon material. The maximum build size for SLS printing is about 200 x 250 x 330mm.
Read More
Stereo- lithograph (SLA) & Polyjet by Stratasys
We use SLA and Polyjet for prints that require high detail or for transparent objects. We can produce up to about 1200 x 750 x 550mm in size for a single print.
Read More
Mimaki Full Color UV Curable Inkjet (3D Printing Services available in Asia only)
Mimaki high resolution full color 3D printing creates exceptionally beautiful objects with vibrant colors.Full color of more than 10 million different colors. Effective build volume is up to 508 × 508 × 305 mm.
Read More
Technology | Application | Materials | Rapid Prototyping | Low Volume Production |
---|---|---|---|---|
Fused Deposition Modeling (FDM) – High End & Commercial Grade Plastics. ![]() | – Conceptual models – Functional prototypes -Manufacturing tooling – Production parts – Medical Devices: Prosthetics & Orthotics – High Precision Parts | ABS-M30, ABSPlus, PC-ABS, PC, PC-ISO, Nylon12, ABS-ESD7 (Static-Dissipative), ASA | ||
Fused Deposition Modeling (FDM) – Low-end Grace Plastics. Tolerance: +/- 0.3mm – 0.8mm | – Conceptual models – Functional prototypes- Medical Devices: Prosthetics & Orthotics | ABS, PLA, PETG, TPU (Flexible), TPE, Wood-filles, Metal-filled, Flame retardant, PEEK, ULTEM and more | ||
Stereolitography (SLA) – Ultra precision. Tolerance: +/- 0.2mm – 0.5mm | – Conceptual models – Functional prototypes – Manufacturing tooling – Production parts | ABS-M30, ABSPlus, PC-ABS, ABS-ESD7 and more | ||
– Conceptual models – Functional prototypes – Manufacturing tooling – Production parts | ABS-M30, ABSPlus, PC-ABS, ABS-ESD7 and more | |||
– PP/ ABS- like performance models(Strong and durable) – Electronic products – Snap-fits,assemblies – Master patterens for casting – Production-like prototypes | Accura Xtreme TM (Grey) and more | |||
Stereolithgraphy(SLA) – Low-end precision. ![]() | – Conceptual models – Functional prototypes – Snap-its, assemblies | Clear-White, Grey,Black resin, Tough resin, Flexible resin, Durable resin, High Temp resin, Castable Wax resin for Jewelry, Durable Resin Polypropylene like result. | ||
Polyjet Standard / Multijet Tolerance: +/- 0.1mm – 0.3mm | – Models that require great representation – For small parts with complex design – Medical devices – Electronic housing | Photo-polymers Vero white, grey, black or Durus white, and more | – | |
Metal 3D Printing using (Direct Metal Laser Sintering (DMLS) and Selective Laser Melting (SLM) | – Complex part designs – Spare parts – Functional parts – Biomedical implants-Engineering Mold and Conformal cooling channel inserts | Titanium (Ti64ELI), Stainless Steel (316L) and 15-5PH, Maraging Steel (MS1) and more | ||
Selective Laser Sintering (SLS) Tolerance: +/- 0. +/- 0.1mm – 0.3mm (Industrial SLS) | – Architectural models – Functional parts – Complex parts | Polyamide PA12, PA2200 Nylon powder Color: White, Dark Grey, Flexible TPU Black, Grey, | ||
HP Jet Fusion / Multi Jet Fusion 3D Printing Solution (MJF) Tolerance: +/- 0.1mm – 0.3mm | – Strong & Flexible Parts – Functional parts | Polyamide PA12 Nylon powder Colors: Grey, Black and more Certified for HP Jet Fusion 3D printers | ||
Mimaki & Stratasys Full Color UV Curable Inkjet Tolerance: +/- 0.5mm – 1mm | – Rich Full Color Application for use of display in the following industries: -Property & Interior Design Models – Prototype Models – Marketing Models – Consumer Products – Medical Display Models | Modeling ink: MH-100 (C, M, Y, K, White, Clear) Support material ink: SW-100 | – |
* As we evolve, new technology and materials will be made available.
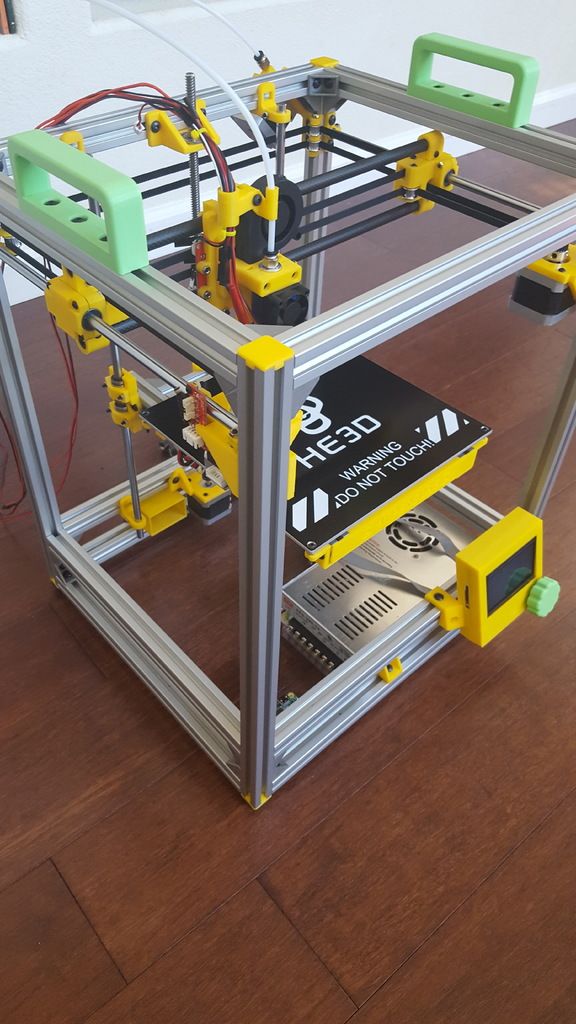
Some of our Machines
3D printers: revolutionizing medicine
Sydney Kendall lost her right arm to the elbow in a boating accident when she was only 6 years old. Now that Sydney is 13, she has to wear dentures every day.
But these products can't match the practicality ('not as cool' as Sidney herself says) of the new 3D printed pink plastic prosthesis.
This hand was custom-designed for Sidney this spring and finished in the desired color.
The prosthesis was designed by a student at Washington University in St. Louis who collaborated with doctors at Shriners Hospital. Remarkably, Sydney and her parents were even able to watch the printing process.
“It took only 7 minutes to make each finger. We were all amazed,” says Beth Kendall, Sydney's mom.
When the girl came to school with a new prosthesis, her classmates were also delighted with the design. She was told: “Everyone liked your new hand, you look so cool. You will become a celebrity!
A robotic arm with controlled fingers helps Sidney catch a baseball, use a computer mouse, grab a cup of coffee.
Question price? About 200$. A traditional robotic prosthesis in the US can cost $50,000-$70,000 and will need to be replaced as the child grows.
“Children don't usually get robotic prostheses because they're expensive,” Sydney's mom said.
Custom 3D printed robotic prostheses represent a truly new era in personalized medicine.
From dentures to heart valves, 3D printing technology opens up incredible possibilities for custom medical devices. Experts say dozens of US hospitals are now experimenting with 3D printers, and researchers are coming up with ever more incredible uses for the technology, all the way to printing human organs.
To help researchers around the world share their 3D printing experiments, the US National Institutes of Health launched a network in June 2014 that allows registered users to upload drawings of such products.
“3D printing is a potential game changer in medical research. Here at the National Institutes of Health, we are seeing an incredible return on investment: cheap plastic helps scientists solve the toughest technological problems, saving millions of dollars and precious time,” says NIH director Dr. Francis Collins.
One of the leading researchers in the field, Dr. Anthony Atala, director of the Wake Forest Institute of Regenerative Medicine, understands the promise of 3D printers best. He has already created a miniature liver that "lives" in a petri dish, tests new drugs and serves as a prototype for creating future organs.
What is 3D printing?
Imagine an inkjet printer that, instead of spraying ink and printing letters, emits a jet of fast-curing plastic or metal gel that takes the shape of a tooth, finger, or knuckle. Such a device needs a command from a 3D MR or CT scanner, which transmits the exact parameters of the body part to be copied. A 3D printer prints an object gradually, applying material layer by layer.
Although 3D printers have existed since 19In the 1980s, the medical use of this unique device only began to be seriously considered in the last few years. A 3D printer can create much more complex geometries than the traditional industry, which would require numerous special blanks and molds for each such piece. Therefore, it is now possible to print an exact copy of a bone or joint, and it will cost pennies.
The process saves time and money by moving the production of medical devices to the patient's bed. Nobody has exact data, but Scott Hollister, a professor of biomedical engineering, believes that hospitals in the United States already use several dozen 3D printers in one form or another.
Teeth, limbs and hearing aids
3D printing is already widely used to produce various body parts (usually made of plastic and metal) that come into contact with tissues but do not enter the bloodstream. This includes teeth, hearing aids, and prosthetic limbs.
“In the past, a dental crown was made in a dental lab, which could take days, and patients needed 2-3 dental visits,” says Dr. Chuck Zhang, Lecturer in Industrial and Systems Engineering at Georgia Institute of Technology (Georgia Tech). Today, a dentist can simply take a 3D image of your tooth and print the crown on the spot.
This technology gives amputees like Sidney an alternative to the usual scary-looking and impractical prostheses. 3D printing studios often develop prostheses together with clients, which allows you to create a work of art that will not only make life easier, but also evoke positive emotions in others.
Dr. Tsang and his colleagues at Georgia Tech are actively working on new prostheses for military veterans. His team is using 3D printed materials to create prosthetic pockets that adapt to changes in body fluid levels. If necessary, these pockets become softer or harder so as not to cause discomfort when wearing the prosthesis.
Implantable devices
Plastic and metal for 3D printers are already being used inside the human body. Doctors at the University of Michigan's Mott Children's Hospital have saved the lives of two children since 2012 by implanting printed airways in them.
These babies had a rare congenital anomaly - tracheobronchomalacia. Without treatment, their weak airways would collapse and the children would die. The only treatment is a tracheostomy and connection to a ventilator in the hope that in a few years their airways will be sufficiently strong.
New technology saved the children from this nightmare. At 17-month-old Garrett Peterson, there was no sign that the ventilated airway would get stronger and allow the baby to shut down. The doctors in Utah, where he was treated, did everything they could.
“Everything in the world should have been beautiful. Garrett couldn't cry because he was turning blue. We had to keep him in a happy mood all the time, but it was unrealistic to keep him on the machine forever,” says the father of the child.
The Petersons read an article about how university doctors implanted a 3D-printed trachea in a child with a similar problem in 2012. They decided not to hesitate, and turned to them for help.
Based on CT scans of Garrett's airways, surgeon Dr. Green and Professor of Biomedical Engineering Hollister designed and printed a personalized breathing tube that would allow the child to breathe on his own. Over time, his body would have to "absorb" this prosthesis, and the airways would remain open on their own.
Mott Children's Hospital subsequently performed this fantastic procedure for the first time.
"I think it was a great example of a 3D printer in a life-or-death situation," said Hollister.
The cost of tracheostomy and subsequent ventilator support for these children is in the order of $1 million per patient. The development, printing and operation to install the breathing tube, according to Hollister, will cost $ 200,000-300,000.
Surgeons have also implanted other 3D devices into patients. Skull patches to fill cavities after brain surgery, for example. Skull plates to replace large pieces of cranial bone that patients lose as a result of injury or cancer. The Mayo Clinic and several other hospitals are already offering 3D-printed joint replacements. These personalized joints minimize intervention and shorten hospital stays.
The FDA currently owns two labs that are exploring the potential of 3D printers for medical device manufacturing.
Living tissue
In addition to metal and plastic, doctors and scientists around the country are working to fuel 3D printers with living human cells. This gave rise to living tissue printing, or bioprinting. The main goal of such work is to learn how to print full-fledged living organs for transplantation, using patients' own cells for complete compatibility.
Some experts believe that this will revolutionize transplantation within a few decades. Patients will not die by the thousands without waiting for a donor organ. Gone in the past is such a terrible phenomenon as transplant rejection.
Dr. Atala of the Wake Forest Institute says researchers can now use the miniature liver he created to test drugs for hepatotoxicity. The scientists expect this method to be much more accurate and humane than current animal and patient testing.
Biomedical engineers use several methods to print organs. The printer creates a plastic frame that can then be coated with human cells. Or the printer can inject living cells into the collagen gel that holds the organ's structures together. Once printed, the cells must grow on their scaffold for several weeks in the lab before the organ can function properly.
After the organ is in place, the scaffold is removed and only living human tissue remains, ideally compatible with the recipient's body. If the organ is transplanted to a child, then it will be able to grow with him, eliminating the need for repeated transplants.
Bioengineers at Cornell University and the University of Michigan are working hard on this concept. Many laboratories have been printing organs for drug testing for a long time, and the production of patches for damaged organs is a matter of the near future.
According to Professor Holister, in the near future medical 3D printers will appear in absolutely every medical institution, changing the face of healthcare beyond recognition.
Konstantin Mokanov: Master of Pharmacy and Professional Medical Translator
3D printers: revolutionizing medicine
Sydney Kendall lost her right arm to the elbow in a boating accident when she was only 6 years old. Now that Sydney is 13, she has to wear dentures every day.
But these products can't match the practicality ('not as cool' as Sidney herself says) of the new 3D printed pink plastic prosthesis.
This hand was custom-designed for Sidney this spring and finished in the desired color.
The prosthesis was designed by a student at Washington University in St. Louis who collaborated with doctors at Shriners Hospital. Remarkably, Sydney and her parents were even able to watch the printing process.
“It took only 7 minutes to make each finger. We were all amazed,” says Beth Kendall, Sydney's mom.
When the girl came to school with a new prosthesis, her classmates were also delighted with the design. She was told: “Everyone liked your new hand, you look so cool. You will become a celebrity!
A robotic arm with controlled fingers helps Sidney catch a baseball, control a computer mouse, grab a cup of coffee.
Question price? About 200$. A traditional robotic prosthesis in the US can cost $50,000-$70,000 and will need to be replaced as the child grows.
“Children don't usually get robotic prostheses because they're expensive,” Sydney's mom said.
Custom 3D printed robotic prostheses represent a truly new era in personalized medicine.
From dentures to heart valves, 3D printing technology opens up incredible possibilities for custom medical devices. Experts say dozens of US hospitals are now experimenting with 3D printers, and researchers are coming up with ever more incredible uses for the technology, all the way to printing human organs.
To help researchers around the world share their 3D printing experiments, the US National Institutes of Health launched a network in June 2014 that allows registered users to upload drawings of such products.
“3D printing is a potential game changer in medical research. Here at the National Institutes of Health, we are seeing an incredible return on investment: cheap plastic helps scientists solve the toughest technological problems, saving millions of dollars and precious time,” says NIH director Dr. Francis Collins.
One of the leading researchers in the field, Dr. Anthony Atala, director of the Wake Forest Institute of Regenerative Medicine, understands the promise of 3D printers best. He has already created a miniature liver that "lives" in a petri dish, tests new drugs and serves as a prototype for creating future organs.
What is 3D printing?
Imagine an inkjet printer that, instead of spraying ink and printing letters, emits a jet of fast-curing plastic or metal gel that takes the shape of a tooth, finger, or knuckle. Such a device needs a command from a 3D MR or CT scanner, which transmits the exact parameters of the body part to be copied. A 3D printer prints an object gradually, applying material layer by layer.
Although 3D printers have existed since 19In the 1980s, the medical use of this unique device only began to be seriously considered in the last few years. A 3D printer can create much more complex geometries than the traditional industry, which would require numerous special blanks and molds for each such piece. Therefore, it is now possible to print an exact copy of a bone or joint, and it will cost pennies.