Woodworking 3d printer
Woodworking best 3D printer models・Cults
#4 Tutorial Fusion 360 - Simple Box WoodWorking | Pistacchio Graphic
Free
SHOP VACUUM HOSE SWIVEL
Free
Easy 90 Corner Bracket
Free
MARKING GAUGE AND DRILL GUIDE - SET !!!
€2.50
Kreg Bench Dog For Kreg Portable Workstation
€0.50
Veritas Spokeshave Blade holder for Tormek SE-77
€0.99
Drill holder with English description
€0.50
Drill holder with French description
€0.50
Band saw throat plates
Free
Wooden Lamp with Arabic Pattern for CNC mill
Free
Digital Wood Joints for CNC
Free
MDF Glue Applicator (Aplicador de cola em MDF)
€0. 90
Woodworking Marking Gauge Tool REMIX (100% printed, no bolts)
Free
JessEm Router Lift/Table Insert Ring
Free
Vacuum Adapter 4" to 2.5"
Free
Pipe Cap For soda bottle
Free
BLUE CRAB SHELF BRACKETS
Free
Router / trimmer edge guide jig
€3
Ruler marking gauge
€2
Bench Dog Set - 20mm system
€2.32
Servo Operated Blast Gate
€1.99
Customizable Blastgate, fully 3D printable
Free
Ryobi BT3100 Table Saw Dust Port Adapter 4 Inch
Free
Oneida Air System 5 Inch Connection Adapter
Free
Shim Holder for Pegboard
Free
Passenger Boat
€1. 92
Mitre saw stop block
Free
Drill Press Vice
Free
Bench bolts 3/4" (Carpentry)
Free
WHACK-ME
Free
Corner Radius Jig Router Templates, Router Templates for Woodworking 7 Pcs Set
Free
Miter Bar
Free
Bandsaw Insert (Ridgid BS14002)
Free
Fearne’s Sickle – Critical Role
€5.82
TL Style Control Cavity Router Template
€1.25
P90 pickup router template
€1.25
Router Bit Pegboard Caddy
Free
Switch box (73mm)
Free
T-slot Track - Custom .
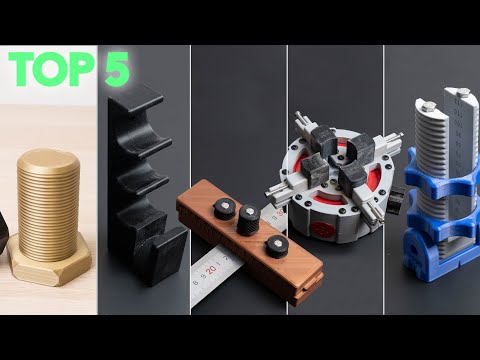
Free
Parallel / Bar Clamp Stand
Free
Easy Scribing Tool
Free
Center Finder + Edge Marker
Free
Harbor Freight Bar Clamp Pads
Free
Marking Gauge Thumb Screw
Free
Router Throat Plate
Free
Cyclone dust collector
€5
Cnc Hold Down / Clamps for Desktop Milling Machine & Sanding Tables/ Openbuilds, Mpcnc, Shapeoko, xCarve, Diy Cnc Routers T-Slot
Free
Center line finder / Gauge - Circle / Square / 45 Degree
Free
3D Printing for Digital Woodworkers
We may receive a commission when you use our affiliate links. However, this does not impact our recommendations.
Custom 3D printed sanding blocks and clamping cauls. While teaching a class building his Greene and Greene themed game table, furniture maker Darrell Peart’s student, Kevin Harris, printed out these custom profile blocks to make sanding and clamping the ogee shape easier.
Digital woodworkers who use CNCs may not be aware that there are other digital tools they can use. Maybe even some you haven’t considered before. This is because digital tools all need CAD drawings. It’s another bonus you get for learning CAD. Often, these are the same or similar to the CAD drawings you create for woodworking projects. Laser cutters, digital metal cutting tools like plasma cutters and water jet cutters, use 2D CAD or drawing files. 3D printers use 3D CAD drawings to print three-dimensional objects. These are the same 3D files CNCs use for three-dimensional carving.
I agree. 3D printers and woodworking seem like an odd combination. Starting with the obvious, woodworkers make things out of wood and 3D printers make things out of plastic but as I’ve found out, you can make useful things with a printer. For example, after only a short time, I now regularly create CNC clamps, jig and fixture parts, new router templates and design, create and/or prototype new shop, CNC and equipment upgrades using 3D printers. A surprising use for me is that I’m now prototyping many of my wood and GFRC concrete sculpture projects with 3D printers. And, recently I’ve begun to experiment with 3D printed furniture joinery components.
3D printers are different
3D printing is quite different than the processes we use in a woodworking shop. All woodworking in a subtractive process. That is, we take wood off. Woodworkers remove wood by cutting, carving, routing, bending and shaping. 3D printing is an additive process in that to make something, material is added. The most common 3D printing process is called Fusion Deposition Modeling (FDM). Polymers in the form of wire-like filament rolled onto spools is melted and deposited in layers until the 3D object is complete.
Where woodworking processes work great is for making relatively large things: furniture, cabinetry, etc. 3D printing excels in ways woodworking can’t: small-scale, detailed, highly accurate objects made out of a consistent material. This difference makes 3D printing a complementary process for making things that can’t easily be made out of wood. Small objects and components with a utility or functional use around the shop are a good example. And, because the printing process is “hands-off” rather than “hands-on” like woodworking, it comes with a special advantage. You can start a print, leave the room and come back hours later for a completed result.
Simply put, 3D printers manufacture things. Woodworkers build things by making one part at a time and assemble them into a final result. Because the processes are so different, printers’ advantages are not what woodworkers are used to. For some, a 3D printer might be a tool to produce small, detailed, useful things that help or support us in the pursuit of our chosen hands-on craft.
3D Printed corner round over templates being made on the very capable Dremel 3D45 printer.
Creating with a 3D Printer
To make anything with a 3D printer you start with a 3D drawing of the thing you want to make. You can create your own using 3D CAD software, such as Fusion360, Rhino3D (what I use) or other online or free CAD programs like TinkerCAD or FreeCAD. But, if you’re not yet comfortable using CAD software to create your own designs, you can download ready-to-go, printable files online. And, there are a lot of them. One of the biggest reasons 3D printers are so popular is the availability of literally millions of free 3D designs at websites such as thingiverse.com or myminifactory.com. On these sites, you’ll find things to print of every conceivable description from the practical (replacement parts for microwave ovens and refrigerators, T-track components, even toothpaste tube squeezers) to the impractical (toys, robots, cosplay character costume parts). Even if you expect to never even consider buying a 3D printer, I suggest you look around online to see what’s possible. It’s quite entertaining. You’ll be amazed at what you can find.
3D printers can make many useful things for woodworkers. In the photo above are several CNC hold down clamps designs made with different materials I’m testing for strength and flexibiliy. One advantage of using a 3D printer is you can quickly test things or make a tool for a specific situation. And, the cost of prints is usually very low. The clamps above cost about $.10 each in plastic and $.03 in electricity to make.
Hold down clamp 3D printing in action.
What’s it like to use a 3D printer?
At some point, I may do a more complete how-to, but for now here’s a quick version of the process of getting something 3D printed.
- Find a file online or create a 3D printable file on your computer. This usually comes in the form of a STL file.
- Open up the file in the program that comes with the printer that prepares yor files for printing. These are referred to as “slicer” programs.
- Apply the printer’s default settings for the kind of filament you’ll be using (PLA for example) for your print.
- Export the machine-ready file (this is a G-code file just like on a CNC) to a SD card or USB flash drive that the printer accepts.
- Load the filament of your choice onto the printer.
- Choose the file you wish to print and begin.
- Come back hours later to see the results.
This little 3D printer is my first printer. It’s very small. The print area is just 5″ x 5″ x 5″. This little gem is called the Snapmaker and it has some rather interesting capabilites. A key feature is that it’s modular. The 3D print head can be swapped out with a Laser Cutter/Burner head or a minature CNC head in a few minutes. Now that’s a small CNC.
Is 3D printing difficult?
Generally, the answer is no. Most 3D printers have simple one-button controllers and an LCD screen. It’s on your computer where you set up your files to print. Compared to programming and setting up a CNC, 3D printers are far easier to use. Though, there’s quite a bit of magic going on under the hood, for the user 3D printing is not a particularly technical thing to engage in. You make a few setting choices and let the machine do its thing.
Essentially your key choices are to select the kind of filament you’re using and the quality level of your print. However, some people struggle a bit learning how to solve basic printer issues. Though 3D printers have far fewer variables than CNCs, users still need to understand causes and solutions to printing problems as they crop up. Most have to do with finding the right temperature settings for the extrusion nozzle and the bed and getting the first print layer to stick. I’ve found that most of the time, the default print settings for different kinds of filaments work fine. The good news is once you get things dialed in you just can print almost anything. To make the entire process simpler yet, 3D printer companies like Dremel are working hard to make printing even easier by automating many of the choices.
Yes, that really is an adjustable Crescent Wrench made out of ABS plastic. No, you can’t use it to over tighten or loosen snug bolts, but it does work and it was printed in one piece. The other items shown are CNC clamp designs I’m testing.
Knife Hinges out of plastic? These are tests made for a friend, furniture maker Bob Spangler to check the fit before he machined the final hinges out of brass for his beautiful custom Tansu cabinets.
What can a woodworker make with a 3D printer?
- Jig parts
- Fixtures
- Patterns
- Custom clamping cauls
- Shop upgrades
- Model projects
- Joinery components
- Lots more…
Testing designs on 3D printers
One thing I use a regularly use a 3D printer for is to preview and test sculpture designs and work out details before committing the time and materials to build a full-scale sculpture. Much better to solve design and construction issues before running into a problem halfway through the building and carving a 4′ tall version out of wood. The printer shown is one of my favorites: the superb Prusa I3 MK3
This is a 3D printed test of a 12″ model for a planned 7′ sculpture to be made with stack wood lamination. The model is printed on the excellent Ultimaker 3 Plus. It took 23 hours to print.
A sample of the many 3D printed sculpture tests I make before committing to making full-size pieces out of wood.
Despite the fact that 3D printers work in plastic, they can make things we can use in the pursuit of our craft. As with CNCs and other digital tools, the secret in getting the best out of 3D printing is to learning how to use CAD software. Digital tools use CAD. That’s pretty much a given. No matter what kind of woodworking you choose to do, I can’t encourage readers enough to invest your time and $ in learning how to use quality CAD software. Don’t be cheap with either. We all have limited amounts of each. So, invest wisely.
Even if you’ll never use a CNC, 3D printer or any digital woodworking tool for that matter, at the very least becoming fluent in CAD will help make you a better designer. Skill and craftsmanship are critical components for better woodworking. They also drive the very passion behind everything we all strive for in woodworking. But, learning to be a better designer is all too often an after thought. Yet, getting better at design is the best long term investment you can make in woodworking. Instinct and personal taste will get you 10% of the way there. The other 90% are about design skills. In the end, it’s design that separates the merely good from the great. CAD just happens to be a great tool for exploring new directions and exploring design possiblities. It’s not that hard to learn CAD basics if you’re willing to try. And, if you regularly use it, you’ll progressively get better at design just by trying variations and testing out ideas. Nice bonus!
With printers starting at $200, 3D printers have become very affordable. At the other end of the equation, serious printers close to the capabilities of expensive industrial/engineering prototyping machines that use tougher, bendable and flexible materials are also becoming more reasonably priced. This class of machines is well suited for useful tasks in a woodworking shop. I’ll have a review of one and a new video in my next post. I’ll review the Dremel 3D45 Digilab 3D printer.
— Tim Celeski
Related Posts
- Digital Tools Have a Lot in Common
Additional Resources
- Digital Woodworking on Instagram
- Personal Work on Instagram
- Digital Woodworking YouTube Channel
Product Recommendations
Here are some supplies and tools we find essential in our everyday work around the shop. We may receive a commission from sales referred by our links; however, we have carefully selected these products for their usefulness and quality.
-
1/8" Roundover Bit
-
Jig & Fixture Bar
-
Dado Blade Set
3D Printers, CAD, CAM, CNC, Digital Woodworking
Recommended Posts
Digital Woodworking
In-depth with Shaper Origin
Does adding a CNC to your shop make you less of a woodworker?
When should I process 3D printed parts with CNC machines?
In the beginning there were CNC machines, soon after that came 3D printers, and since then machining has changed.
This may be a slight oversimplification, but it is not far from the truth. Both CNC machining and 3D printing are mechanical processes to shape a workpiece or part into the desired shape, but both work in different ways. CNC machining is a subtraction process; it removes material bit by bit, cutting or shaping the workpiece.
On the other hand, 3D printing is an additive manufacturing process. 3D printers create a blank slowly, layer by layer, from scratch. It may seem that using both processes on the same part works against you. Did you print a part just to be machined? Why did it have to be done? Why couldn't the finished part be printed right away?
It turns out that although CNC machining and 3D printing seem to be opposite processes and should not be involved in the manufacture of a part at the same time, there are times when using these two methods together really makes sense. We have outlined a few circumstances when you should use both of these methods together.
When to use CNC machining and 3D printing together:
Use a CNC machine to process 3D parts to:
1) Save time:
One of the traditional production methods is machining press - molds for injection molding, but this is a labor-intensive process. While 3D printing isn't exactly fast, it is faster than the alternative, so when time is pressing it makes sense to 3D print a part and then finish it on a CNC machine.
2) Ensure Accuracy:
The technology behind 3D printing has evolved by leaps and bounds over the last decade, but it is still unable to achieve low tolerances simply by printing. To achieve a high level of precision, 3D printed parts need to be processed. CNC machines are able to withstand such low tolerances. If 3D printing is the most efficient way to produce a given part - say, a prototype - but CNC machines provide more accurate results, then 3D printing approximate dimensions and CNC precision machining may make sense.
3) Finish the part well:
As mentioned, CNC machines are capable of very precise and smooth finishing, which 3D printers do not currently have. Machining 3D printed parts on a CNC machine makes sense when high tolerances or finishing are required, as lathes and milling machines can make multiple passes and use multiple tools to achieve a smooth finish.
This also makes sense for certain materials. Cutting an entire part out of a particularly hard material can cause additional wear on the CNC machine, but 3D printing the same part followed by simple CNC machining results in a better finish and less wear on both machines.
How to Use 3D Printing and CNC Machining:
If you think your situation deserves to use both methods to produce the same part, here are some considerations to keep in mind.
1) Increase some dimensions:
CNC machines remove material, so don't 3D print parts too close to the desired dimensions. Otherwise, you will remove too much material with your CNC machine and the finished product will be too small.
2) Be careful with positioning:
3D printers can create parts with geometry inaccessible to CNC machines - at least without removing any material in its path and thus destroying the part. If you plan to use a CNC machine to finish a part, be sure to use the geometry available for your CNC machine.
3) Remove all supports for 3D printing:
3D printers make the product in layers. If necessary, to keep these layers from collapsing on top of each other, your 3D printing project can include structural supports. These supports will need to be removed after the 3D printing step, but do not remove them until you are sure that you will not need these supports when machining the part on the CNC machine.
4) Be careful with fixing the part:
Curved, flowing parts are ideal for 3D printing. However, they can be extremely difficult to process on CNC machines. Built-in additional material or even additional architecture to make it easier to fix parts on a CNC mill or lathe.
New potential for combined processing:
Traditional methods are often the best, and the most effective is the use of 3D printing and CNC processing separately, not together. However, when flexibility and creativity are required and circumstances are favorable, experienced machinists may use both methods in combination. Both methods are amazingly flexible. This makes the combination of CNC machining and 3D printing ideal also for one-off scenarios such as prototyping.
3D printing and CNC machining are not polar opposites; It's not even two sides of the same coin. Instead, the two methods form the yin and yang of modern production. The combination of both processing methods opens up a whole new world of possibilities for machinists. As 3D printers get bigger, more precise and faster, more and more manufacturers are combining both additive and subtractive processing. Increased flexibility, reduced production times and more precise parts are just some of the results.
3D printers (Additive machinery), conformity assessment.
3D printers (Additive machinery), the equipment manufacturer or its authorized representative must ensure that a risk assessment is carried out to determine the health and safety requirements that apply to the equipment. The equipment must be designed and built taking into account the results of such a risk assessment.
The Machinery Directive 2006/42/EC sets out the basic health, safety and performance requirements for the products they cover.
The EU legal framework is technologically neutral and does not prescribe any specific binding technical solutions for product design. Therefore, manufacturers can use a number of technical solutions to meet these basic requirements.
The Machinery Directive enables manufacturers to rely on specific technical solutions, which are detailed in harmonized European standards or parts thereof, references to which are published in the Official Journal of the European Union. If the manufacturer chooses to make such a technical decision, it is assumed that the product complies with the applicable essential health, safety and performance requirements that the harmonized standard seeks to cover.
If the manufacturer decides to adopt any other technical solution, he must provide a detailed explanation of the compliance of such technical solution with the requirements of EU legislation in the technical file. The following are some of the most important harmonized standards for 3D laser printers:
EN ISO 12100 Safety of machine tools. General principles for design. Risk assessment and risk reduction
EN 60204-1 Safety of machinery - Electrical equipment of machinery
EN 13849-1 Safety of machines - Safety related parts of control systems
EN 13850 Machine safety - Emergency stop function - Design principles
EN ISO 11553-1 Safety of machinery — Laser processing machines — Part 1: Laser safety requirements
EN 1127-1 Explosive atmospheres - explosion prevention and protection
EN ISO 19353 Safety of machinery - fire prevention and fire protection
Fire and explosion safety standards are also relevant for plastic printers.
There are some non-harmonized standards for
laser products EN 60825-1 (Safety of laser products - Part 1: Equipment classification and requirements)
EN 60825-4 (Safety of laser products - Part 4: Protective equipment against laser radiation)
CE marked
the order indicates the use - household, industrial, medical, age limit from years, as they can be used in schools. Specifies the user's skill level and certain restrictions, including suggested or excluded age groups. Specifies whether the 3D printer has any features that could lead it to be considered primarily as a machine, such as equipment with significant available mechanical (moving parts) or thermal energy sources (hot surfaces) as primary potential hazards, compared to others, enclosed units with shrouds or guards to protect the operator. Any raw material used in the 3D printer may have certain characteristics such as flammability or powder form, which may cause the installation or workplace rules to become a more important factor due to by-products from the printer, such as combustible dust or other emissions to the atmosphere.
As a general rule, products intended primarily for use by children are often subject to more stringent regulations than products intended for use by adults. For example, in the US, baby products are subject to a number of federal safety regulations. rules called baby product safety rules. US law defines a "children's product" as a consumer product designed or intended primarily for people 12 years of age or younger. Most 3D printers intended for use in schools will be used by children over the age of 12 with adult supervision.
In the European Union, products intended for use by children are subject to Directive 2009/48/EC on the safety of toys (Toys Directive), 3D printers intended for schools are not currently mentioned anywhere in the Directive, nor in the relevant Guidance Documents, such as Guidance Document No. 16 on electronic equipment (GUIDANCE DOCUMENT No. 16 ON THE APPLICATION OF THE DIRECTIVE ON THE SAFETY OF TOYS Electronic equipment) is intended for use by children, so it is unlikely that this Directive and related standards referred to in it, will apply to 3D printers used in schools. In this case, the entire responsibility lies with the school staff.
When equipment compliance is considered in the context of product safety standards and regulations, there are usually several key aspects to consider.
These include:
safety of the product itself and safe use, handling of the product by operators and maintenance personnel, generally in accordance with harmonized safety standards
safe operation of the product in the environment in which it is intended to be used in accordance with any installation regulations related to the safe use and protection of consumers and workers in the workplace.
In Europe, the potential application of ATEX Directive (2014/34/EU) remains subject to consideration for equipment installed and used in a potentially explosive atmosphere. Like the Machinery Directive, the ATEX Directive contains a number of criteria that must be met in order to determine the Directive's applicability.