Hybrid 3d printing
What's HYBRID? - 3D HYBRID: AM FOR CNC
"Hybrid Manufacturing" is an industry recognized term for combining both Additive Manufacturing and Subtractive Manufacturing processes.
Relevant Definitions from ASTM F2792 − 12a :
- additive manufacturing (AM), n--a process of joining materials to make objects from 3D model data, usually layer upon layer, as opposed to subtractive manufacturing methodologies. Synonyms: additive fabrication, additive processes, additive techniques, additive layer manufacturing, layer manufacturing, and freeform fabrication.
- subtractive manufacturing, n--making objects by removing of material (for example, milling, drilling, grinding, carving, etc.) from a bulk solid to leave a desired shape, as opposed to additive manufacturing.
- directed energy deposition, n--an additive manufacturing process in which focused thermal energy is used to fuse materials by melting as they are being deposited.
...But why combine the two?
After review of metal 3D printing technologies, one will learn that there are two main types of metal 3d printing, powder bed fusion (PBF) and directed energy deposition (DED).
When considering printing a part using either method it becomes abundantly clear that both are plagued by poor surface finish quality and require post machining. Therefore, CNC expense is inherent. DED technologies, ignore the goal of surface finish and precision, instead focus on speed and material quality. The CNC process provides the precision required. And DED lends itself quite easily as a tool to CNC machine through 3D-Hybrid. This is consolidation is Hybrid Manufacturing.
Hybrid Manufacturing History
Hybrid Manufacturing made its first commercial appearances in the early 2000’s via Laser-Powder Deposition in a CNC Machine. Some cases used a robot in a separate cell of the CNC machine with a pallet pool change mechanism. Hybrid Manufacturing didn’t quite catch on at that time. Lasers were still large capital expenditures and were typically produced for small spot sizes (i.e. cutting and engraving applications). With the onset of the metal 3D Printing or Additive Manufacturing growth in the 2010’s hybrid manufacturing made a resurgence. At this time the cost of Lasers had dropped to around $100,000 for a couple kilowatts, making it possible to couple with a large CNC machine tool purchase. Also at this time the metal powder bed machines were being delivered for $800,000 to $1,500,000 making Hybrid manufacturing an ideal alternative, especially for larger parts.
Hybrid Manufacturing is now a common, industry recognized term for combined additive and subtractive manufacturing. Since 2013, the number of machine tool builders offering hybrid manufactring machines has gone from zero to double digits. 3D-Hybrid is the only hybrid manufacturing tool integrator offering multiple metal deposition technologies for virtually any CNC machine.
Hybrid 3D printers available on the market
Published on September 3, 2020 by Aysha M.
Hybrid machining combines additive and subtractive manufacturing methods in one single solution. The concept was around since 1990’s but it was not commercially popular until recently. Today, more and more manufacturers are developing hybrid 3D printers as the demand for such machines keeps growing. Some manufacturers are offering even more functions than 3D printing and CNC – laser engraving and cutting and paste extrusion are often added to offer a versatile solution for the customer. Therefore, such hybrid printers are also known as “All-in-one printer” or “3-in-1 printer”. We have prepared a list of 14 hybrid 3D printers available on the market, divided into desktop and industrial categories and ranked in alphabetical order.
Desktop hybrid 3D printers
5axismaker
The 5AXISMAKER solution was launched in 2015 by UK-based manufacturer 5AXISWORKS. This machine is available in two versions, the 5xm400 and 5xm600 according to the maximum manufacturing size. Both support any CAD/CAM software (provided a post processor is available) and include a one-year commercial subscription to Autodesk® Fusion 360 TM Ultimate. They include a set of tools including a 5-axis CNC router, touch probe, 3D printer, 3D scanning and measurement, and hot wire cutter, plus the potential to add more items via their adapter. As we have said they have a printing volume of 400mm3 or 600mm3 depending on the version, and are compatible with engineering thermoplastics, such as nylon, PC, etc. You can purchase one of these hybrid multifunction 3D printers for $6,500 on the manufacturer’s website.
Creality CP-01
Creality 3D, a low-cost 3D printer manufacturer, has unveiled its Creality CP-01, a hybrid printer that can be used as a 3D printer, CNC milling machine, and laser engraving machine. The integrated FDM-based 3D printer prints with ABS, PLA, PVA, TPU and wood components at a maximum print speed of 80 mm/sec. The heating plate can be heated up to 100°C. The maximum volume is 200 x 200 x 200 mm and it must not be exceeded even for components that are milled or engraved. The integrated laser can engrave wood, plastic and paper with a laser power of 500mW. The same materials extended by printed circuit boards can also be milled with a maximum spindle speed of 4,800 rpm. The three individual modules of the hybrid printer (extruder, CNC milling and laser engraving unit) can be easily exchanged as required. By combining three units in one, the CP-01 saves not only space but also costs. However, the CNC milling and laser engraving units are entry-level models, so they do not provide above-average performance. In summary, the CP-01 is a good option for makers and hobbyists, but it is not at an industrial level.
da Vinci 1.0 Pro 3-in-1
Taiwanese manufacturer, XYZPrinting, entered the global 3D printing market with easy-to-use FDM desktop 3D printers. Today, the company is known for its da Vinci line of products for their value for money. The da Vinci 1.0 Pro 3 in 1 is a hybrid printer that integrates both a 3D printer based on FDM technology and a 3D scanner. If that’s not enough, a laser engraving unit can be added. The 3D printer prints parts from PLA, ABS, PETG, HIPS and wood PLA at a maximum print speed of 120 mm/sec. Because the da Vinci 1.0 Pro 3 in 1 has an open filament system, the materials do not necessarily have to be purchased from XYZPrinting, but can be purchased from third-party suppliers. The heating plate can be heated up to 90°C and the maximum construction volume is 200 x 200 x 190 mm. The 3D scans can have a maximum size of 15 x 15 cm with an accuracy of 0.25 mm. The optional laser engraving unit has an engraving area of 20 x 20 cm with a laser power of 350 mW. Due to its features, the da Vinci1.0 Pro 3 in 1 is suitable for professionals.
DOBOT MOOZ 2 PLUS
Shenzhen Yuejiang Technology Co. (DOBOT) is a leading global provider of intelligent robotics solutions. DOBOT’s product line includes the MOOZ 2 PLUS. The DOBOT MOOZ 2 PLUS is a hybrid printer that combines 3D printing, CNC milling and laser engraving to print parts made ofPLA, TPU, PETG and flexible materials at a maximum print speed of 80 mm/sec. The heating plate can be heated up to 80°C. The maximum construction volume is 200 x 200 x 190 mm and this volume must not be exceeded even for components that are to be milled or engraved. The integrated laser can engrave wood, bamboo, leather, paper, plastic, fabric and opaque acrylic with a laser power of 1.6 W. The CNC milling machine mills wood, bamboo, acrylic, PCB, carbon fiber boards, plastic, etc. with a maximum spindle speed of 8,000 rpm. The DOBOT MOOZ 2 Plus is a desktop printer that is ideal for makers.
H-Series by Diabase Engineering
The H-Series from Diabase Engineering is a hybrid machine that offers CNC machining and 3D printing in a single interface. The machine has been carefully engineered to solve real problems in the desktop manufacturing toolchain. It is a machine that enables the manufacture of functional products with high accuracy and a professional finish. Depending on the number of axes you decide to go for, whether 3, 4 or 5, the machine offers different build volumes. The build volume on the 3-axis machine is 416mm x 186mm x 210mm. On the 3D printing side, you can print a range of engineering-grade thermoplastics such as ABS, PLA, NYLON, PETG, TPU, water-soluble materials and more. The machine is equipped with an active nozzle cleaning system, a heated filament cabinet, a changeable heated build platform and various subtrative tool heads for milling, engraving and surfacing. As mentioned you can also go for a rotary modular axis for 4th and 5th axis printing and milling.
Snapmaker 2.0
Snapmaker 2.0, is a 3-in-1 machine that enables 3D printing, laser engraving and cutting, and CNC carving. It supports several 3D printing materials such PLS, ABS, wood, etc. For CNC carving you would be able to use carbon fiber sheet, PCB, platane wood, and more. You can also perform laser engraving and cutting on a diverse range of materials including plywood, fabric, leather, and acrylic. Snapmaker 2.0 comes with a smart touchscreen that simplifies the workflow of your projects, letting you manage the most-used tasks directly from the touchscreen. This desktop hybrid 3D printer retails for $1,039.
ZMorph VX
ZMorph VX is considered by many to be one of the best desktop hybrid 3D printers currently available on the market. This versatile solution supports single and dual extrusion, CNC milling, laser engraving and cutting, and paste extrusion. ZMorph VX works with virtually all 3D printing materials on the market, so the users can take advantage of 3D printing with advanced materials like nylon, HIPS, PC/ ABS, and more. Silent X and Y steppers reduce noise by 50%. The paste extrusion function works with chocolate, dough, cream cheese, frosting, and more. To ensure a smooth workflow process for the users, the Polish company also released a designated software Voxeliser 2.
Industrial hybrid 3D printers
Aconity
MIDIThe 3D printer AconityMIDI was launched by the German manufacturer Aconity3D in 2018 with the intention of providing a flexible production system to users. AconityMIDI is equipped with an optional second camera that allows for parallel setup times while the main system is still in production. It has a maximum production volume of Ø 170 mm x H 200 mm and a layer thickness of up to 10 μm. In addition, the system integrates process monitoring or high temperature preheating (up to 1200°C). This hybrid 3D printer is also available as a DUAL-Laser system that allows for maximizing productivity. Weighing 1450kg, AconityMIDI can be equipped with the unique vacuum option and Micro-LBM configuration. This is certainly an advanced solution for professionals in the 3D industry.
AMBIT Series 7
The new multitasking system AMBIT Series 7 has been developed by the company Hybrid Manufacturing Technologies with the aim of opening up new opportunities in the production of metal parts. It provides a perfect integration of 7 production technologies in the same tool without precedents. This new multitasking system integrates DED technology heads with a robust performance to deposit metal from 0.5 to 3mm thickness. It also features a column that functions as a universal docking station to monitor and control manufacturing processes to ensure quality parts. Its main novelty is the subsequent verification of manufacturing quality thanks to the eddy current inspection head, which allows the detection of surface and subway cracks. The AMBIT Series 7 solution is undoubtedly an innovative way to integrate additives in conventional manufacturing!
INTEGREX i-400 AM by MAZAK
Manufactured by the Japanese company MAZAK, the INTEGREX i-400 AM is a hybrid multi-tasking machine that provides additive manufacturing technology and high-precision finish machining operations for large format manufacturing. The AM technology is based on Directed Energy Deposition (DED) process. The nozzle deposits the molten metal layer by layer to build the part. DED is interesting for repair applications of worn or damaged components such as aerospace turbine blades. In terms of its Multi-Tasking capabilities, the INTEGREX i-400 AM provides full 5-axis machining to process prismatic parts from solid billets or castings, round parts, highly contoured parts and AM manufactured parts.
Kraken hybrid 3D printer
The KRAKEN project is a European project that was launched to bring an all-in-one hybrid manufacturing machine to the market at an affordable price. Therefore, the KRAKEN system provides 3D printing technologies, robotics and subtractive technologies. It has been developed for the production of end-use parts and large customized functional parts, measuring up to 20 meters long with 0.1mm precision. The creators claim that the system is 40% faster than competing methods thanks to high deposition rates during the AM process and a seamless switch to milling and finishing operations (with an interchangeable manufacturing head). KRAKEN is also said to be 25% more productive and take up to 90% less floor space. On the 3D printing side, it integrates multiple technologies too: wire arc AM, resin 3D printing, and a thermal spray process to allow metal 3D printing on top of a polymer part. This is a very complete solution to say the least!
LASERTEC 65 3D Hybrid by DMG Mori
The German-Japanese manufacturer DMG Mori, the result of the merger between the German company DMG and the Japanese company Mori Seiki, offers industrial manufacturing solutions for all industries. Its product range includes hybrid manufacturing machines that can both print and machine parts. Among them is the LASERTEC 65 3D Hybrid, a machine with a spray nozzle that offers additive metal fabrication and milling capabilities. It can create parts up to a maximum size of 735 x 650 x 560 mm and is based on the DED process. Equipped with 5 axes, it can change its laser head to mill the designed part. The LASERTEC 65 3D Hybrid integrates Siemens software solutions to maximize your design and control your manufacturing process.
LENS 860 hybrid 3D printer by Optomec
The LENS 860 has been designed by Optomec to provide industrial companies with large metal parts: it combines a DED process and a milling spindle for finishing work. Its maximum printing volume is 860 x 600 x 610 mm and its laser reaches a maximum power of 3kW. Four versions are now available, with or without milling, and with or without controlled atmosphere. Depending on the configuration you choose, you will be able to print non-reactive metals such as steel or flap, or metals such as titanium.
LUMEX Avance -25 by Matsuura
Released in 2002, LUMEX Avance-25 is a hybrid 3D printer developed by a Japanese manufacturer Matsuura. It combines metal 3D printing technology with conventional milling, CNC. This hybrid solution uses a 400 W Yb fiber laser and can store up to 20 tools, as well as 3D print parts at a speed of 7 cubic cm per hour, for a maximum part weight of 90 kg. An interesting advantage of this machine is its APR System (Automatic Powder Recovery System), which means that powder supply, collection and reuse can be fully automated without the need for the operator to directly touch the powder. Excess powder that remains after sintering is automatically sieved and reused for subsequent sintering.
Did this list of hybrid 3D printers help you? Let us know what you think of these hybrid 3D printers. Leave a comment below or on our Facebook and Twitter pages! Don’t forget to sign up for our free weekly Newsletter, with all the latest news in 3D printing delivered straight to your inbox!
hybrid hydrogel and extrusion 3D printing / Sudo Null IT News For a long time, 3D printers were used exclusively for the production of functional or aesthetic prototypes, and the technology itself was called "rapid prototyping". The rapid development of computing technology has led to the emergence of various methods for implementing additive technologies: from laser stereolithography (SLA) to the more famous 3D printing (3DP). Another term that appeared as early as 1894, this is a hydrogel - a polymer capable of absorbing water (if very exaggerated). Hydrogels, like additive technologies, have many applications: medicine, pharmacology, and even energy.
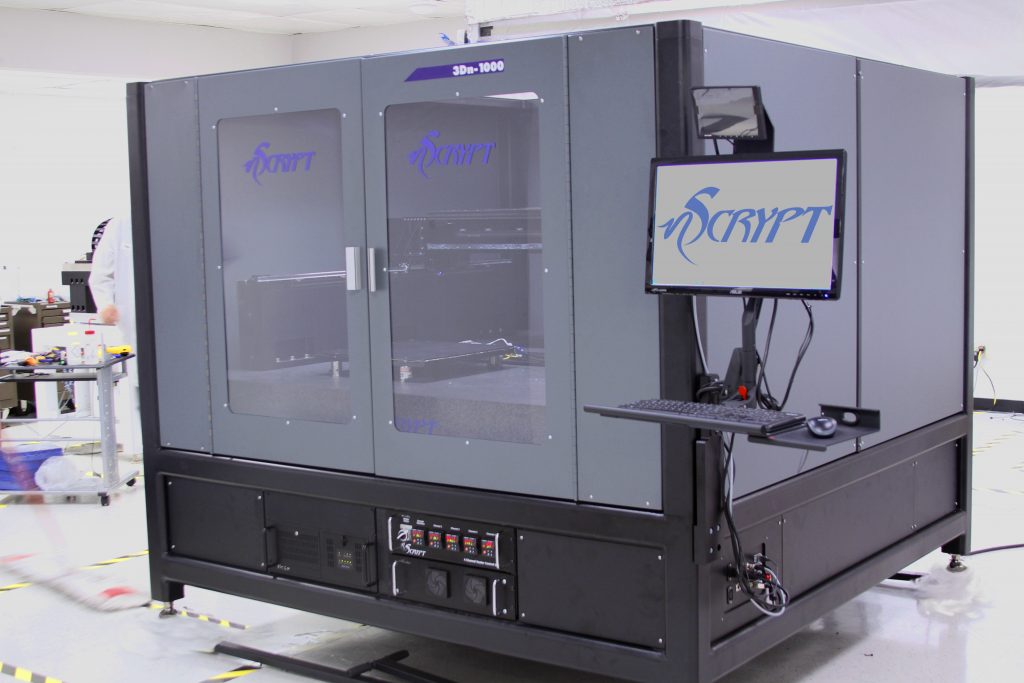
Research basis
To begin with, it is worth briefly explaining what a hydrogel is. This is a network of intersecting polymer chains capable of equilibrium and reversible swelling in water and aqueous solutions. The basis of the hydrogel are hydrophilic molecules.
The problem with classical hydrogels made from polymer networks in water is that they are soft and brittle; they lack elasticity and strength. Because of this, the use of hydrogels in various industries (robotics, tissue engineering, etc.) is severely limited.
The elasticity of hydrogel materials can be improved by combining interpenetrating covalent and ionic polymer networks to form highly extensible and strong structures. Another method for improving the mechanical properties of hydrogels is based on the use of fillers with a high aspect ratio (high ratio of the length of the filler to the diameter of its cross section). This allows the gel matrix to be mechanically strengthened. However, the use of a filler material other than the matrix material results in stresses on the interface surfaces that cause cracking when deformed or heated.
The opposite method is based on the use of single-polymer composites or so-called homocomposites. The mesoscale amplifying network of homocomposites is made from a material that is chemically identical to the primary matrix material. Networks of homocomposite reinforcement make it possible to modulate the mechanical properties of the primary (main) matrix without stress, delamination points, etc. It sounds very promising, but there is also a problem - the manufacture of HHG (from homocomposite hydrogel , i.e. homocomposite hydrogel) is an extremely difficult process due to the lack of methods for creating reinforcing networks with the same chemical composition as the hydrogel matrix.
In the work we are considering today, scientists describe a new type of HHG, in which both the primary gel matrix and the reinforcing network consist of sodium alginate (SA from sodium alginate ; C 6 H 9 NaO 7 ). These HHGs are reinforced with a fibrillar network of alginate soft dendritic colloids (SDC from soft dendritic colloid ). SDC is a hierarchically structured class of soft matter synthesized through a shear-induced deposition process in a turbulent medium.
The high degree of branching around the cores of SDC particles makes them morphologically similar to polymeric molecular dendrimers. However, SDCs are much larger than these dendrimers. Scientists believe that hierarchically branched SDCs could be an excellent option for effective reinforcement of composite materials. Significantly, the SDC branches cover a larger surface area, which can increase the stability of the composite by distributing the load more evenly.
Study results
The first step was to prepare soft alginate dendritic colloids (i.e. SDC) to serve as reinforcing meshes. For this, turbulent settling was used. To obtain an SDC hydrogel, an alginate solution (120–190 kDa) was introduced into an aqueous solution of Ca 2+ ions, which effectively bind two -COO- side groups on the alginate backbone ( 1а ).
Image #1
The precipitation process leads to the formation of SDC with a characteristic hierarchical morphology ( 1b ) with branching of different scale and generations (secondary branches) of fibers. In fact, SDCs are made up of micron-sized fibers that fork repeatedly into ever finer fibers. The outermost layer ("crown") surrounding each SDC is made up of flexible nanofibers that can be up to 10 nm thick ( 1b ). The nanofibers in the crowns endow them with physical adhesion, which is a major factor in the ability of dendricolloids to create the structural strength of the colloidal network. The final size of conventional SDCs, including their corona, is in the range of 100–500 µm.
Next, the viscoelastic properties of aqueous SDC suspensions had to be evaluated. First, the scientists tested whether alginate SDC hydrogels form a colloidal network at low volume fractions in water. In theory, in aqueous suspensions, contacting SDCs will adhere strongly due to van der Waals forces to form a percolation* network of branched fiber subcontacts ( 2a ).
Percolation* — in chemistry, the phenomenon of liquids flowing or not flowing through porous materials.
Image #2
Evaluation of the storage moduli (G') and loss (G″) of SDC suspensions in the linear viscoelastic region showed that SDCs have a strong tendency to form colloidal networks.
Dynamic modulus* : the dynamic modulus G set can be used to represent the relationship between vibrational voltage and load: G' is the accumulation module; G″ is the loss modulus.
Yield strength was observed in aqueous suspensions of 0.25 wt% SDC, i.e. at a lower concentration than most types of conventional colloidal gels.
A suspension of 1.0 wt.% SDC showed a G' value of 200 Pa, while the reported value for 1.0 wt.% alginate microgels should be 10–100 Pa. Those. SDC slurries have more pronounced solid-like characteristics than conventional alginate particle slurries.
Continuous phase HHG consists of molecular alginate gel combined with Ca 9 ions0033 2+ . First of all, the scientists analyzed the properties of molecular hydrogels containing 1.0 wt.% bound alginate, but without SDC. The hydrogel was prepared by adding CaCO 3 nanoparticles and D-gluconic acid δ-lactone (GDL) to the SA solution. As GDL undergoes hydrolysis and lowers pH, CaCO 3 slowly releases Ca 2+ ions. After 2 hours of equilibration, data were obtained regarding the viscoelastic properties of the hydrogel ( 2c ). At a concentration of CaCO 3 above 0.05 wt.% the hydrogel behaved like a solid. With further introduction of Ca 2+ into the hydrogel, its rigidity continued to increase. But at CaCO 3 above 0.2 wt.%, syneresis (structure aging) of the hydrogel was observed, followed by water release. As a result, it was found that to maintain the stability of the hydrogel, its composition should contain 1.0 wt.% SA and 0.1 wt.% CaCO 3 .
As a result, the researchers had two components on hand that required combining - SA SDC (alginate soft dendritic colloids) and SA CMH molecular matrix (alginate gel bound by Ca 9 ions0033 2+ ).
Many hybrid HHGs were synthesized where the total SA concentration was kept constant at 1 wt% and the ratio of SDC to CMH was varied.
Image #3
All samples obtained in this way exhibited solids characteristics ( 3a ). The characteristic stress-strain curves ( 3b ) obtained from the mechanical tensile test also demonstrate that hybrid HHGs are more stiff than SDC or CMH gels alone. On chart 3c shows tensile-strain and rheometry measurements for all specimens. Analysis of these data shows that homocomposite systems containing mixed SDC and CMH exhibit a strong synergistic effect. The complex modulus (G) and Young's modulus (E) values for the homocomposite gels showed a threefold increase with maxima at low SDC to CMH ratios.
However, this cannot be attributed solely to the increase in the concentration of Ca 2+ in the homocomposite system. So the maximum shear modulus in HHG (G = 950 Pa at 0.125 wt. % SDC / 0.875 wt.
Therefore, a strong synergistic effect leading to an increase in the mechanical strength of HHG can be directly related to the physical interweaving of molecular SA and colloidal networks of SDC ( 3d ). The resulting structure is stable in most environments, but can be easily destroyed by placing it in solutions of strong chelating agents such as EDTA (ethylenediaminetetraacetic acid; C 10 H 16 N 2 O 8 ).
Scientists note that another important feature of the developed hybrid hydrogel is the ability to change the kinetics of its gelation depending on.
First, the dependence of gelation on time was tested for three variants of samples: SDC, CMH and composite HHG (the SA concentration was the same for all - 1 wt.%).
Picture #4
On the graph 4a presents the results of the analysis of a pure suspension of SDC. It can be seen that SDC immediately exhibits a solid behavior without the addition of CaCO 3 or GDL. This is explained by the fact that the formation of this network occurs due to contact splitting and interweaving of fibrillar dendricolloids.
On the other hand, pure CMH exhibits liquid behavior at first and gradually solidifies as the bonding agent Ca 2+ is released by hydrolysis. The CMH becomes a fully connected structure after 120 minutes ( 4b ).
It is important to note that the time dependent evolution of HHG is directly dependent on the kinetics with which SDC and CMH (the main building blocks of HHG) are assembled in the network. HHG initially solidifies due to gelation of the mechanically rigid SDC network. A stronger hydrogel then forms as the interpenetrating CMH molecular network becomes bound by Ca 2+ ions ( 4c and 4d ).
These material properties show controlled initial yield stresses and a slow increase in hydrogel elasticity over time. Therefore, such a material can be used in 3D printing, which the scientists decided to test at the next stage of the study.
The fact that the created hydrogel is a homocomposite system allows precise control of its properties. Due to this, such a hydrogel can be used in 3D printing using extrusion, which was previously an extremely difficult task. For example, both SDC and CMH are not extrudable in their pure form, unlike hybrid HHG.
The ability to control the properties of the hydrogel allows the creation of an extrusion "ink" in which the time-independent yield strength and setting time can be adjusted to suit the individual.
Synergistic effect in mixed SA-SDC composites.
Because the 3D printer applies a pressure drop that exceeds the HHG yield strength, the extruded shape is maintained by the rapid gelation of the SDC network ( 4c , video above).
Image No. 5
It is also important that the developed hydrogel could be used for printing under normal conditions without additional processing or preparation of the material ( 5а ). It is noteworthy that the G' of a pure SDC suspension (1500 Pa) is almost four orders of magnitude greater than that of the CMH mixture before the addition of GDL (0.5 Pa; 5b ).
Despite maximum HHG gel stiffness occurring at lower SDC/CMH ratios ( 4c ), HHG with higher SDC ratios produced more filaments with improved layering (video below).
3D printing of a multilayer structure by extrusion.
for 5a and 5c show the process of 3D printing a homocomposite hydrogel by direct extrusion. HHG is extruded through a nozzle (25 G, inner diameter 0.26 mm) at 140 kPa and the gel retains its shape due to its yield strength (≈80 Pa). Additional structuring in the z-direction can be achieved by stacking successive layers that have been found to adhere well to the underlying ones. The scientists were able to additively print more than 10 layers of hydrogel in the vertical direction without reducing the extrusion speed. After curing (60 minutes), the finished printed structure could be easily removed from the substrate ( 5d ). If there is a need for a structure of large dimensions, then staged extrusion is necessary, giving additional time for the gel to solidify, it is also necessary to increase the yield strength of the material by changing the composition of HHG.
For a more detailed acquaintance with the nuances of the study, I recommend looking at the report of scientists and additional materials to it.
Epilogue
In this work, scientists have demonstrated their amazing creation - a composite hydrogel, the properties of which can be manipulated depending on the needs of the end user. The hydrogel they created is excellent for 3D printing via extrusion, something that previous hydrogels could not boast of.
Scientists say that water-based materials are not very strong, they are brittle and soft, which is quite expected. However, if alginate soft dendritic colloids and alginate gel bound by Ca 2+ ions are combined, a hydrogel with increased strength can be obtained. In other words, they have combined two different hydrogels into one with properties that are superior to those of its constituents.
Applications for the new hydrogel include medicine, the food industry, and soft robotics. But full use is still far away, since the hydrogel needs to be improved. In particular, the scientists want to modify the hydrogel so that it can be used in 3D printing of biomedical injection materials.
Thank you for your attention, stay curious and have a great week everyone. :)
A bit of advertising
Thank you for staying with us. Do you like our articles? Want to see more interesting content? Support us by placing an order or recommending to your friends, cloud VPS for developers from $4.99, a unique analogue of entry-level servers, which was invented by us for you: The whole truth about VPS (KVM) E5-2697 v3 (6 Cores) 10GB DDR4 480GB SSD 1Gbps from $19or how to properly divide the server? (available with RAID1 and RAID10, up to 24 cores and up to 40GB DDR4).
Dell R730xd 2 times cheaper in the Maincubes Tier IV data center in Amsterdam? Only here 2 x Intel TetraDeca-Core Xeon 2x E5-2697v3 2.6GHz 14C 64GB DDR4 4x960GB SSD 1Gbps 100 TV from $199 in the Netherlands! Dell R420 - 2x E5-2430 2. 2Ghz 6C 128GB DDR3 2x960GB SSD 1Gbps 100TB - from $99! Read about How to Build Infrastructure Corp. class using Dell R730xd E5-2650 v4 servers costing 9000 euros for pennies?
Hybrid printing: what is it and how to do it?
Although additive and subtractive manufacturing processes seem to be completely opposite, in fact, as these technologies develop, the advantages of hybrid manufacturing become more and more obvious. Hybrid manufacturing systems, equipped with both additive and subtractive technologies, could be a major technological breakthrough for the industry. Thus, these two technologies can be considered as complementary and allow to use the advantages of each of them.
1. Hybrid production
The joint use of additive and subtractive technologies is not a new concept. For example, post-processing of 3D printed metal parts often includes CNC machining to give them mechanical precision and a better surface finish. However, there is another way to combine these two processes, resulting in what we call hybrid manufacturing (Figure 1).
Hybrid manufacturing consists of combining additive and subtractive technologies in one machine in order to take advantage of the advantages of each of these technologies: the geometric complexity of additive processes with the high precision of subtractive processes. Thus, it is possible to obtain an additive and a machined part in one step, which speeds up the entire production process. Naturally, when designing a hybrid part, the requirements of each of these technologies must be taken into account.
Applications for hybrid systems can range from the production of small batches of metal parts to the repair of damaged or worn parts.
Fig.1. Hybrid fabric (Source: DMG Mori).
2. P Direct energy and material supply
Direct energy and material supply (DED) is one of the additive processes that can be used in hybrid technologies. This process consists of fusing the material with a laser or electron beam as it is applied through a choke onto a building platform. The deposited material can then be machined for a better surface finish and greater mechanical precision. Alternatively, you can also add material on top of a machined part to increase the geometric complexity of the part.
Another advantage of the additive DED process is that it is possible to use a 5-axis system in the print head, which allows geometrically complex areas to be printed without the need to place support structures.
DED is suitable for the production of large parts and the repair of mechanical components, and these two characteristics are quite useful if we compare this process with metal powder laser melting. On the other hand, melting metal powder allows parts to be obtained with better finishes and dimensional accuracy.
3. Hybrid printing
It was with the intention of creating a hybrid part that we started this project using a CNC machined part to which we added a lock using a laser metal powder deposition process. We can't call it hybrid production, but hybrid printing, since we used two different machines, a CNC milling machine and a 3D printer, to make this part.
Another aspect we wanted to explore with this experiment was the bonding ability between two steels with different chemical compositions. We used 1.1730 steel structure for the CNC machined part and the hybrid lock was powder printed from 1.4404 (316L) stainless steel.
Below we describe the steps that led to the manufacture of the part shown in Figure 2.
Figure 2 - A hybrid part consisting of a CNC machined base and an additive lock.
The project began with 3D modeling of the part and the study of its attachment to the construction plate of the 3D printer. We chose a simple cuboid geometry with an inner box to which an additive lock was added, i.e. a part that would need to be 3D printed. On the inside, this lock consists of a series of 1 mm thick thin blades (Fig. 3) which, despite their simple geometry, would be very difficult to make in any other way.
Figure 3 - Internal section of the hybrid lock.
Another important aspect of this research was how to attach the hybrid parts to the building plate. On the one hand, the printer does not have a part straightening system, as is the case with CNC machines, and on the other hand, it would be difficult to add a tension system that does not interfere with the dynamics of the printer. In addition, the construction plate is attached to the printer with four screws, which does not guarantee its operation.
It was decided to make several holes in the plate, thinking about different fixation possibilities in future hybrid prints (Fig. 4).
Figure 4 - Preparing the impression plate.
The construction plate (and all its holes) are symmetrical about their central axis. To avoid positioning errors during puffing on the printer, an arrow has been added to indicate its position in relation to the recoater, which indicates the mobile mechanism that transports the metal powder from the feed cylinder to the construction plate, as shown in the figure. in figure 5.
Figure 5 - Study of the location and orientation of parts on the construction plate.
Figure 6 shows one of the stages in the preparation of a structural wafer, namely the opening of the thread with the help of taps (cutting an internal thread).
Figure 6 - Construction plate preparation.
In figure 7, we see the construction plate in the 3D printer, coated with metal powder and ready to print a hybrid lock.
Figure 7 - Printer preparation (printed on Eplus 3D EP-M150)
After printing is completed, it is necessary to remove the metal powder that has not been cast, as shown in Figure 8. Only after removing this powder can we remove the construction plate from the printer. The unmelted powder is screened and reused for future printing.
Figure 8 - Removal of molten metal powder (Printed by Eplus 3D EP-M150)
After removing all the metal powder, the construction plate is removed from the machine, and the printing result is shown in Figure 9.
Figure 9 - Final result after printing (Printed by Eplus3D EP-M150)
Figure 10 shows the three parts that are the results of this experiment. On the left we see the base part without the addition of the hybrid lock. In the middle part we see the hybrid hood and in the right part we see the result after CNC milling the hybrid hood. This finishing removes the surface roughness left on the outer walls of the hybrid castle as a result of printing.
Figure 10 - Machined part, machined part with hybrid cap, machined part with hybrid cap, CNC milled.
4. Conclusion
Our first hybrid printing project was successful. We can say that the project had about 70% preparation and 30% completion, since this is the research stage of fixing parts on the print plate, which required more work from us.
Although the metal powder laser melting process is not as versatile as the DED process, we can prove that CNC milling and metal powder laser melting can be successfully combined.
However, it is important to note that there are some limitations that need to be taken into account. Hybrid covers must grow out of a perfectly horizontal straightened plane so that the covers are welded to their base (Figure 11). It would be impossible to carry out this experiment if the printed plane were a surface with a certain three-dimensional profile.
Figure 11 - Indication of the print plan.
It is also important to ensure that there are no parts above the print plane that will interfere with the movement of the recoater. In other words, if we want to hybrid print a part with more complex geometry, we need to think about how to ensure the connection between the parts without interfering with the dynamics of the printer.
It could also be demonstrated that a hybrid cast can be made using similar metals but with different chemical compositions.
Nuno Boavida - Training Specialist at CENFIM Marinha Grande
About Eplus3D Metal 3D Printer EP-M150
geometric data in high-performance metal 3D parts, which is suitable for batch production of dental parts, medical implants and material research centers to develop various metal powders with its open parameter platform.