Ttu 3d printing
3D printing toward a new future — The Hub@TTU
By Miguel Fernandez-Junco, Special to the Hub@TTU
A student built a 3D-printed heart at the Texas Tech University Libraries’ Makerspace.
A mind may wander far and explore depths of untapped imagination. Colors that yet exist, improbable structures or fantasy worlds swirl and require an outlet to come to life.
Modern technology has progressed to a point where those ideas no longer require years of craftsmanship or skills; instead, a few programs and equipment can have anyone creating their visions. That is the foundation that puts Texas Tech’s Makerspace among the most unique and appealing services that the university offers.
A program of the library, Makerspace helps develop ideas and bring them to life using 3D printing, 3D scanning, laser cutting, virtual reality and other services. On the second floor of the library in room 210, the services are primarily free to use for students, staff and faculty.
The Makerspace, established in 2017, took roughly a year for the project to go from concept to reality, Ryan Cassidy, the Makerspace librarian, said. The goal is to provoke creativity and innovation among students.
“We did a survey on the computers that would ask if you knew about Makerspace,” Cassidy said. “‘When you hear Makerspace, what do you think about?’ The number one response was 3D printing, virtual reality was on there, and a whole list of different things.”
From there, the Makerspace brought students’ visions to life.
Libraries once stood at the forefront of providing information and allowing access to technology people could not afford. Now, the Makerspace arms its staff with the expertise to teach and adopts emerging technologies to create a place that offers that same experience in the modern age.
Promoting creativity and innovation through 3D printingThe Makerspace’s 3D printer allows students to create and invent.
Makerspace provides an area for young inventors to explore their minds, promoting creativity and innovating as 3D printing grows and evolves. One of the fastest-growing industries, some experts acclaim 3D printing as a cornerstone of our future.
In recent years, the trade has become more widespread, Cassidy explained, as it’s expanded to include market-grade technology more accessible to consumers.
And in coming years, the 3D printing industry will lead the business sector with its ability to serve all industries, ranging from manufacturing, jewelry and architecture to automotive and medical.
Texas Tech senior Abed Taha, who is a student assistant worker for Makerspace, said that 3D printing has brought in numerous clients since its inception. So much so, the growth prompted the Makerspace to relocate to the bigger space on the library’s second floor after outgrowing its original home.
Building everything from armor for cosplays to prosthetic body parts, projects are limited only by the innovator’s patience as they can take between hours to days depending on the size, with multiple-piece projects needing gluing.
“We offer ABS and PLA materials,” Taha said. “We have three Poly Printers, a five-way and two 229’s. With the PLA, we have an Ultimaker that we can make a print with two colors; you can attach two filaments on it and print it.”
He noted that the printing services come with a nominal fee to cover material costs and maintenance for the printer, adding that the technology’s cost-efficiency allows for much use overseas.
Leading a sustainable futureWhile currently problematic, moving to more eco-friendly alternatives, such as 3D printing, could lead to a more sustainable future.
“Depending on the type of materials they use, (3D printing) could be a really good answer to some of the sustainability issues,” Cassidy said. “If they are able to get out a more sustainable model of concrete, that means these lots could have a lasting presence.”
The British International Investment states that 3D printing can build homes at quicker speeds, while reducing the carbon footprint by 70%, allowing for affordable prices.
One architecture firm is already looking to build a 3D-printed neighborhood in Austin, while international builder 14Trees has already built housing and entire school districts in Africa.
Cassidy notes this as an example of how 3D printing can help solve housing problems in the United States via a lower-cost alternative.
“It has the potential to leave a great impact,” Cassidy said. “The question becomes how are people going to try to cut corners? Will we look for more profitable rather than sustainable?”
However, the feasibility of Earth-based construction — the 3D printing of earth materials — presents challenges to the market-available systems, such as the demand for more adept technologies.
Additionally, Taha noted that to make the process more mainstream and adaptable to the broader consumer market, filaments would have to withhold the same pressure and force that concrete offers while maintaining the same structural integrity.
While still in the unknown, Cassidy said the future of technology, and the way it will have an impact, is in the hands of the next generation of great inventors and visionaries.
“It’s going to take a new cadre of disruptive entrepreneur,” Cassidy said. “Kids in college right now are going to be the ones to break that ground.”
And Texas Tech’s Makerspace is one of the places where they can do it.
“We’re here to help people get comfortable using them,” Cassidy said. “We offer workshops all across the semester, and we offer beginners level but do have intermediate and advanced as well.”
“Don’t let all these terms like virtual reality or 3D printing and everything else intimidate you,” he added. “Come into the Makerspace, we’re happy to show you how everything works and get you started with making something you want to see come to life.”
For more information on Makerspace, faculty support, and upcoming workshops, visit their website at https://www.depts.ttu.edu/library/make/index.php or contact them at [email protected].
Like this:
Like Loading...
Filed Under: Campus, News, Texas Tech, Texas Tech University Tagged With: 3d printing, makerspace, Texas Tech, university library
Angel Flight transports TTU’s 3D printed medical supplies to rural hospitals
LUBBOCK, Texas (KCBD) - In an effort to serve the rural hospitals across the region, Texas Tech University and Texas Tech Health Sciences Center students, faculty and staff are teaming up with pilots who are volunteering to transport their 3D printed medical supplies.
Since the outbreak of COVID-19 began, TTU and TTUHSC have collaborated to research and produce face shields, N95 masks, ventilator adapters and more. Engineering and Honors College faculty and staff jumped in to begin production with the help of other departments, colleges and local businesses that had printers and supplies. The production of face shields and ventilator splitters has been successful.
“When issues arise and something comes up, then it takes people in the community to stand up and do their part for change to happen,” Honors College staff member Douglas Guberman said.
The products are designed to help medical personnel as they fight COVID-19, whether that’s to protect them and preserve their protective equipment or serve more patients on ventilators.
Items have been donated to Lubbock hospitals. Now, they are reaching out to rural hospitals that may have an even tougher time acquiring protective equipment and other needed supplies.
To deliver the supplies, Guberman enlisted the help of a fellow Air Force veteran, Scott Gloyna, a volunteer for the Angel Flight South Central nonprofit program. Angel Flights provide transportation for patients in need of treatments at distant hospitals.
“When you have a patient on board, you are very concerned with their comfort, their safety,” Gloyna said. “I always try to find the smoothest air I can and try to land as easy as I can, as little time taxiing as I can and try to get them from home to their place they get their treatment as quickly as I can, as safely as I can. With masks and stuff, it’s a little different. I’m not so concerned about the passenger in the back but the cargo is just as vital.”
Gloyna joined Bryan Rose, owner of Rose-Text and fellow pilot, in the first trip. It was to Monahans’ Ward County Memorial Hospital. Supplies would be delivered there and to a hospital in Pecos.
“We’re so blessed in this community that we live in out here on the High Plains and the way people are here so willing to help each other,” Rose said. “This is just our opportunity to give back. So, as soon as Scott called me I was like, ‘yeah, let’s do it. ’”
Research continues into design and production of more supplies, like N95 masks. Guberman tells KCBD they are working to increase production and are also reaching out to as many hospitals as possible. But, they need your help.
“If there are people in your community that could help now, then this issue we are dealing with, COVID-19, we can’t wait,” Guberman said. “If you are able to help, you should. We could always use more people to help, anyone with 3D printers that can help, contact us and we would be happy to take their assistance. To me, it’s just everyone stepping up and doing their part, something that everyone should do if you’re able to.”
To make a donation to TTU Health Sciences Center for materials to produce face shields, ventilators, ventilator splitters, face masks and respirators, click here. Then, select “3D Printing COVID-19 Relief.”
Copyright 2020 KCBD. All rights reserved.
3D printing of mixed propellant / Sudo Null IT News
To start the video.
3D printed propellant blend - we did it. After a hundred experiments, several waves of despair and stages of acceptance of the inevitable. Made and patented.
The developed technology for the additive production of solid propellant charges (SFC) from mixed propellant propellant (SRT) for a solid propellant rocket engine (SRM) using the FDM printing method includes: a special SPT composition with the required energy and operational parameters, the layer-by-layer synthesis 3D printer itself for printing rocket fuel; and several related technologies.
What is all this for?
Yes, then, in order to “disrupt” the rocket and space industry, and in particular, “disrupt” solid rocket science, which makes up 99.9% of all rocket science, and which now suffers from many shortcomings (pains) inherent in the current technology for creating TTZ.
Firstly, 3D printing is devoid of all the shortcomings of modern TTZ manufacturing technologies. The production of mixed solid polymer propellants for solid propellant rocket engines (SSREs) today is represented by casting (vacuum and pressure) and pressing through a matrix. Casting is characterized by all defects of a rheological nature: volumetric shrinkage, lugs, bays, etc.; and pressing has a strict limitation of the geometric parameters of the TTZ and additional operations in the technological process associated with ensuring safety. After casting and pressing, TTZ is usually machined, in most cases by hand. In general, the current technologies for the manufacture of TTZ after the polymerization and cooling process have a large proportion of defects associated with product cracking. Plus, the need for a huge range of technological equipment for molding combustion channels (profiled needles, multi-piece needles, fingers, etc.). and additional equipment to ensure the tightness of the process (inserts, cuffs, sealing rings), which prevents the liquid mass of explosive fuel from entering the elements of butt joints. It is also necessary to additionally strengthen the body of the product due to the large internal loads on it during polymerization and cooling, resulting in a parasitic mass.
Another disadvantage is the time - together with control operations, polymerization can take up to one and a half months. 3D printing of CPT is devoid of such disadvantages.
Secondly, the uniformity and inflexibility of TTZ production. Each application problem solved by an aircraft with a solid propellant rocket engine has its own energy parameters: high-energy rocket boosters and meteorological rockets have different laws of change in thrust over the time of engine operation, therefore, for the manufacture of TTZ for boosters, there is its own technological process, and for meteorological rockets - its own, i.e. Specialization of production is required, with all the ensuing economic difficulties. Controlling the properties of a TTZ at each point in its volume using 3D printing makes it possible to create various TTZs with highly customizable energy characteristics and different dimensions on a relatively small production area for each specific task.
Thirdly, in the general case, the TTZ combustion surface area:
where P(x) is the combustion surface perimeter in the section perpendicular to the longitudinal axis of the charge.
That is, in order to increase the TTZ combustion surface area, on which the solid propellant rocket engine pressure and, as a result, thrust, depend, it is necessary to increase the curvilinearity of the TTZ cross-sectional profile. On fig. 1 shows a TTZ with a complex profile printed on our 3D printer.
The existing technologies for the production of solid propellant charge (SPC) are limited in the creation of complex profiled SPC, which limits the energy characteristics of solid propellant rocket engines. To complicate the curvilinearity of the TTZ cross-sectional profile, a wide range of technological equipment is required.
Even at the dawn of astronautics, engineers developed a number of complex forms of TTZ (Fig. 2), but technologically they could only implement them as experimental samples. Therefore, due to the relative ease of manufacture, the most common type of cross-sectional profile for a solid propellant rocket motor today is a hollow cylinder with a round hole in the center, a typical example of which is the Space Shuttle System solid propellant booster (Fig. 3). By the way, even with such a simple geometry of the combustion channel, the “sidewall” of the Space Shuttle is the most powerful rocket engine in the history of mankind. But what happens if you make a slightly more complex profile using 3D printing in the same form factor?
Fourthly, 3D printing itself is the most robotic technology. For 3D printing, there is no need for a large number of workers in order to assemble / disassemble numerous technological pins, needles and mandrels; wash the mixing tank; cut off excess fuel, etc. Therefore, this technology is much safer. The level of manual labor involved in pouring fuel can be seen in this excellent video.
Fifthly, additive manufacturing technologies make it possible to digitalize the manufacturing process of TTZ, which, in turn, will allow, for the first time, to introduce adaptive business processes of the third wave in the rocket and space industry.
By itself, managing the pairing of each point of the TTZ volume by layer-by-layer synthesis makes it possible and economically justified to widely use digital twin technology, IoT elements and machine learning to improve the quality of the production process.
Particular attention was paid to safety in our project. The design includes many technical solutions that ensure the safety of the process: from modification of the fuel composition to an armored capsule for a few personnel who control the printing.
These are the main advantages of the technology of additive production of TTZ from mixed propellant.
Of course, we are not alone in seeing all these advantages of this technology. In addition to our modest project, this technology, judging by open sources, is being worked on in the USA, Great Britain, the Netherlands and China.
In the US, several major research institutes are doing this, such as the Institute of Combustion, Raytheon Technologies Corporation, and a number of technology start-ups of various levels, some of which are commissioned by DARPA, whose visible results are still classified.
On the other hand, a start-up that prints plastic fuel for hybrid rocket engines (HRE) is openly showing its results to everyone. Through 3D printing, they have improved the energy performance of the gas turbine engine.
In general, the Americans are developing this technology under at least two defense contracts: the first is the concept of on-demand payload delivery in the shortest possible time to a given orbit, and the second is a concept that they call “ROCKET FACTORY IN-A- BOX", and according to our project "Expansion" - Autonomous Rocket Plant (ARZ), which I will write about in a separate article - about how 3D printing technology radically transforms the current technological order that has developed in the rocket and space industry, and in particular how additive manufacturing of rocket fuel will change the battlefield (if the editors of Habr give the go-ahead on such a topic).
Fig. 4 - To compare the printing accuracy, on the left is the TTZ printed in the Dutch Research Institute, on the right - ourFurther development of the Expansion project
missiles.
The market for small spacecraft launch services is an excellent place for the first stage of expansion. The advantages of 3D-printed solid rocket fuel will make it possible to abandon liquid launch vehicles, which will radically reduce the cost of launching pico / nano satellites.
The current stage of the project is the search for ways of development and scaling.
Amazing things made with a 3D printer
3D printing has been around for much longer than you think - almost 40 years. But only recently the potential of this technology has begun to be fully realized. People began to create incredible things with the help of this powerful device: from all kinds of technically accurate figures and prosthetic limbs for people and animals to models of real houses and cars. Below are some amazing examples of amazing things you can 3D print.
. Toucan's beak restored using 3D printing
2. Transparent titanium prosthesis
hands"
5.
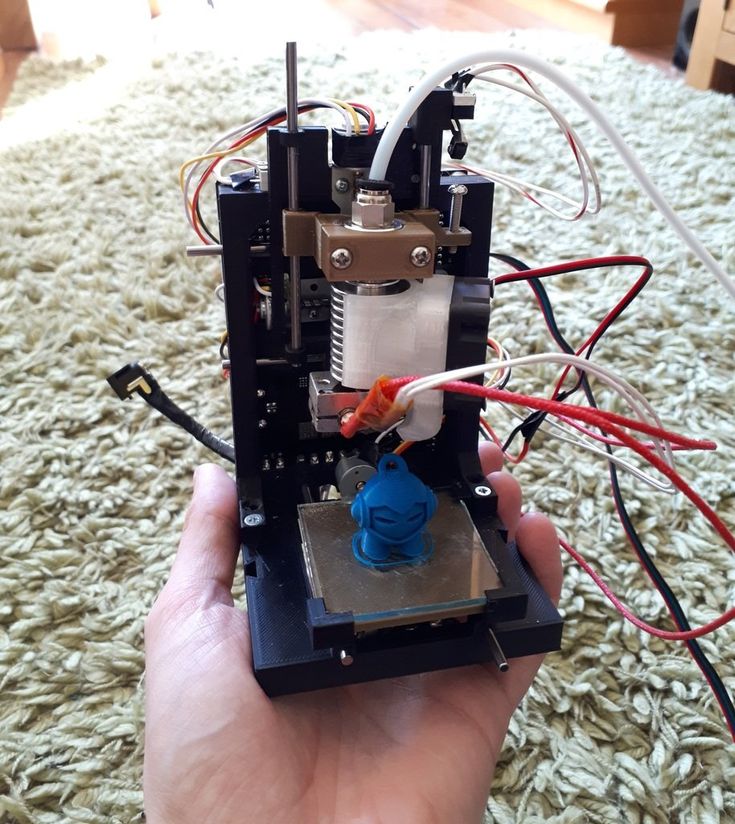
T-Rex Dinosaur Head Shower
7. A 3D printed shell for an injured turtle
9. “3D cast cast of my mom's leg. She can even take a shower in it!”
10. "A friend printed his face for Halloween"
11. "3D helper for Chloe the cat"
12. “3D prosthesis that can be connected to ultrasound to quickly heal broken bones”
13. “My Cyber Corgi”
14. “Our attempt at 3D printing failed halfway. And here's how we used what we got."
15. "3D Printed Violin"
16. as an engineer's thesis. She also programmed an application with which you can control the robot.0009
17. “3D printed chess”
18. “I 3D printed my cat”
the door has become the most useful in life!”
20.
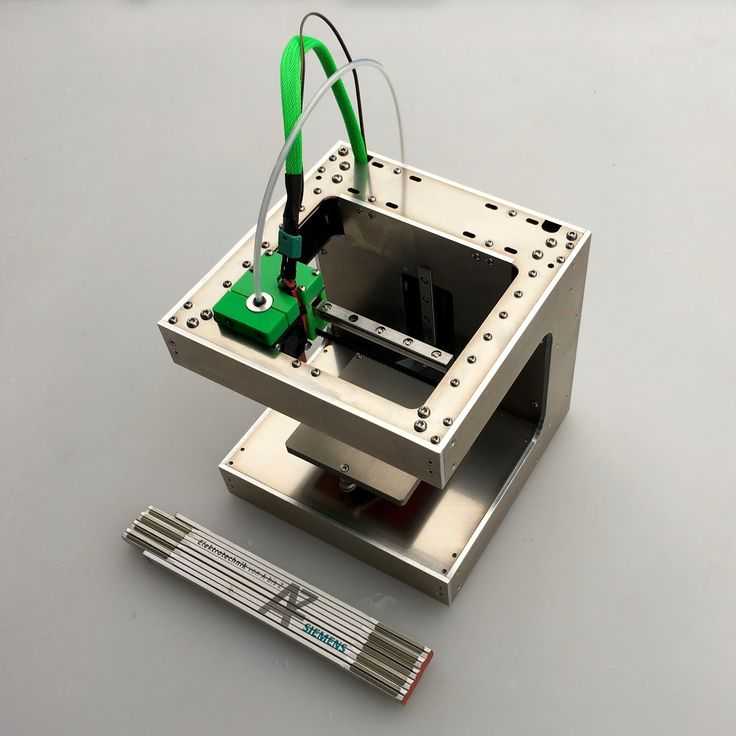
21. “3D printed vases that give plastic bottles a second life”
22. My friend made this costume for a festival using a 3D printer"
23. “Game of Thrones 3D lamp”
24. “I 3D printed my son’s brain using his MRI data”
25. Vader holder
26. “I made a guitar and it even sounds good!”
27. “Car wheels can also be printed on a 3D printer”
28. “Allosaurus skull”
29. “3D copy of my son”
30. “This house was 3D printed in just 24 hours and cost less than $11,000.”
titanium for a 29-year-old woman who, due to illness, could lose her leg. It turns out that the university cooperates with hospitals on an ongoing basis, and interest in 3D printing from medical institutions is growing. TTU doctoral student Yaroslav Golovenko tells.
Learn more