Shotcrete 3d printing
Robotic 3D Printing Solution | KUKA AG
In a factory near Hamburg, a start-up is using KUKA robots to build the digital future of urban and infrastructure construction. The team is not only revolutionizing the production of concrete components using 3D printing, but also the associated planning and execution processes.
New process for 3D concrete printing with robots
In the middle of a room, an L-shaped steel mesh basket is standing on a steel pallet. A thumbs-up sign is given to the operator who presses the start button on a touch panel. Seconds later, the hum and clatter of a concrete mixer fills the hall. Slowly, a machine raises itself in the workshop like a dinosaur come to life. But the scene is taking place in Hamburg and not in Jurassic Park. The bright white KUKA robot inside the installation is anything but frightening as it applies shotcrete to the steel mesh basket through a large nozzle in uniform movements. Layer by layer, a moist, shiny, blue-gray structure grows – at this point still with a wave-like structure and rough surface. This is soon smoothed into shape by a second robot with a large spatula-like tool.
Using shotcrete from a 3D printer to create an unlimited variety of shapes
“The robot with the shotcrete nozzle is the star of our system,” says Hendrik Lindemann. Right now, it is printing the prototype of an edge beam, as needed for a concrete bridge, for example. But the robot also has walls and other elements in its repertoire. Lindemann is a qualified architect and an expert in digital manufacturing. And, together with Roman Gerbers, Niklas Nolte and Alexander Türk, he is co-founder of Aeditive – a start-up company that is working on the digital future of concrete construction here in an old factory building near Hamburg.
In the construction industry, the first robot applies the shotcrete during 3D printing, and the second robot smooths it out.
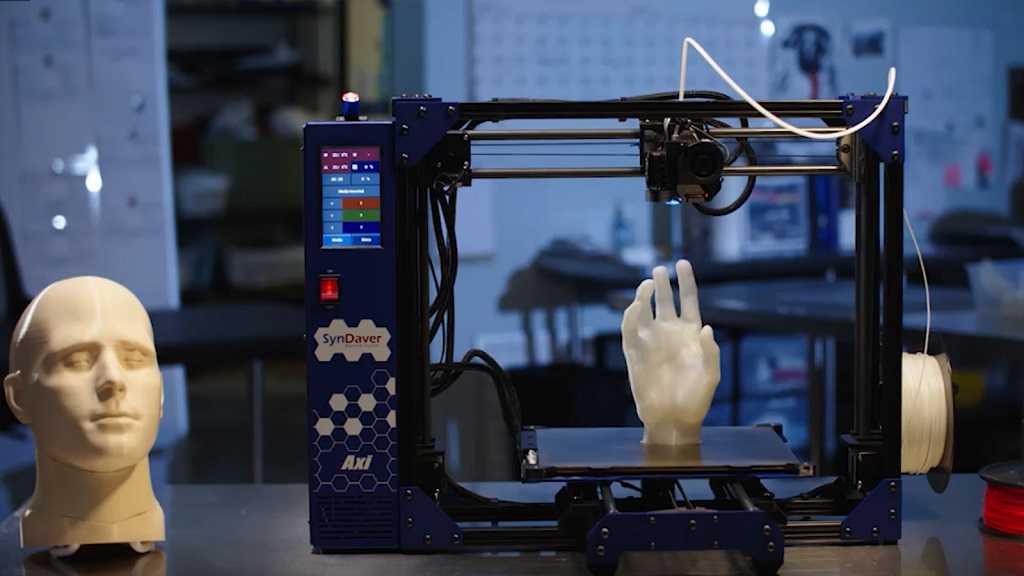
The Concrete Aeditor can be used in both stationary and mobile applications
The heartbeat of the 3D concrete printing facility for use in both stationary and mobile manufacturing applications is determined by two six-axis KUKA robots from the KR QUANTEC ultra series. With a maximum payload of 300 kilograms and a reach of up to 3,900 millimeters, they are among the most powerful and compact industrial robots. As Foundry variants, they are particularly suited for operation in environments with a high degree of fouling, high humidity and high temperatures.
The key element for 3D printing with shotcrete: two KR QUANTEC ultra robots of the Foundry version.Now in the video: shotcrete 3D printing using KUKA technology
Two robots, one goal: the perfect prefabricated concrete element through 3D printing with shotcrete
And this is exactly what the Norderstedt demonstration system with the 3D printer called ‘Concrete Aeditor’ is all about. The shotcrete nozzle developed in-house and guided by the first robot works hand in hand – or rather gripper in gripper – with a second robot, which handles the set-up of the structure in parallel. “Thanks to our new automated process, we are now able to produce even load-bearing concrete elements by means of 3D printing,” says Hendrik Lindemann. And all this from a single source. The Concrete Aeditor consists of production and material containers, the concrete mixing unit including a water and power supply, and its own software-based control system. “This allows our system to always be close to its construction jobs in precast plants or on building sites,” emphasizes Türk, the market strategist.
With comprehensive data integration for maximum process and cost transparency
With the aid of its own software, Aeditive enables its users to digitally generate the elements to be printed without the need for special prior knowledge. “The data generated during the production process help us to support users in quality assurance and to predict wear,” explains Lindemann. Türk rejects the idea that the Aeditive robots take away jobs:
On the contrary. Given the continuing shortage of skilled labor, including in the construction industry, automation tends to secure existing jobs. It helps companies avoid capacity bottlenecks as the volume of orders continues to rise.
Alexander Türk, Co-Founder of Aeditive
Interlayer Reinforcement in Shotcrete-3D-Printing : The Effect of Accelerator Dosage on the Resulting Bond Behavior of Integrated Reinforcement Bars
Authors
- Niklas Freund Technische Universität Braunschweig , Institute of Building Materials image/svg+xml https://orcid.org/0000-0003-2392-5439
- Dirk Lowke Technische Universität Braunschweig , Institute of Building Materials image/svg+xml https://orcid.
org/0000-0001-8626-918X
DOI:
https://doi.org/10.52825/ocp.v1i.72Keywords:
Additive Manufacturing in Construction, 3D Concrete Printing, Shotcrete 3D Printing, Interlayer Reinforcement Bars, Pull-out Tests, Micro Level AnalysisAbstract
Additive manufacturing with cement-based materials has recently become increasingly common on construction site. The high degree of freedom in individual geometric shapes, the associated potential for resource-efficient designs, and the high degree of automation could make this technology a milestone in the history of construction industry. Many of the existing manufacturing techniques are initially based on unreinforced concrete. However, for many structural elements, the use of reinforcement is indispensable and therefore the reinforcement integration represents a prerequisite. One promising reinforcement strategy is the use of interlayer reinforcement. This method specifically uses the layered characteristic of the additive manufacturing process by integrating reinforcement between the applied layers. In combination with an adaptive path planning, it is therefore possible to manufacture force-flow-compliant reinforced elements with a minimal increase in process complexity compared to an unreinforced production. However, besides the integration process itself, material-process interactions represent an important research topic. Especially for Shotcrete-3D-Printing, the use of accelerators can significantly change the structural build-up of the applied material and thus effect the bonding ability of the sprayed concrete to the integrated reinforcement element. The present study investigates the effect of accelerator dosage on the bond properties of integrated rebars. The resulting bond is analyzed non-destructively via computed tomography and mechanically by pull-out tests according to RILEM RC6.
The results show that the material compaction caused by the sprayed application leads to excellent bond properties. However, by using high accelerator dosages, bond deteriorations can be observed.
References
Buswell, R.A.; da Silva, W.L.; Bos, F.P.; Schipper, H.R.; Lowke, D.; Hack, N.; Kloft, H.; Mechtcherine, V.; Wangler, T.; Roussel, N. A process classification framework for defining and describing Digital Fabrication with Concrete. Cement and Concrete Research 2020, 134. https://doi.org/10.1016/j.cemconres.2020.106068
Wangler, T.; Lloret, E.; Reiter, L.; Hack, N.; Gramazio, F.; Kohler, M.; Bernhard, M.; Dillenburger, B.; Buchli, J.; Roussel, N.; et al. Digital Concrete: Opportunities and Challenges. RILEM Tech Lett 2016, 1, 67. https://doi.org/10.21809/rilemtechlett.2016.16
Reiter, L.; Wangler, T.; Roussel, N.; Flatt, R.J. The role of early age structural build-up in digital fabrication with concrete. Cement and Concrete Research 2018, 112, 86–95. https://doi.org/10.1016/j.cemconres.2018.05.011
Buswell, R.; Kinnell, P.; Xu, J.; Hack, N.; Kloft, H.; Maboudi, M.; Gerke, M.; Massin, P.; Grasser, G.; Wolfs, R.; et al. Inspection Methods for 3D Concrete Printing. In Second RILEM International Conference on Concrete and Digital Fabrication; Bos, F.P., Lucas, S.S., Wolfs, R.J.M., Salet, T.A.M., Eds.: Springer International Publishing: Cham, 2020, pp. 790–803. https://doi.org/10.1007/978-3-030-49916-7_78
Kloft, H.; Empelmann, M.; Hack, N.; Herrmann, E.; Lowke, D. Reinforcement strategies for 3D‐concrete‐printing. Civil Engineering Design 2020, 2, 131–139. https://doi.org/10.1002/cend.202000022
Freund, N.; Dressler, I.; Lowke, D. Studying the Bond Properties of Vertical Integrated Short Reinforcement in the Shotcrete 3D Printing Process. In Second RILEM International Conference on Concrete and Digital Fabrication; Bos, F.P., Lucas, S.S., Wolfs, R.J.M., Salet, T.A.M., Eds.: Springer International Publishing: Cham, 2020, pp. 612–621. https://doi.org/10.1007/978-3-030-49916-7_62.
Perrot, A.; Jacquet, Y.; Rangeard, D.; Courteille, E.; Sonebi, M. Nailing of Layers: A Promising Way to Reinforce Concrete 3D Printing Structures. Materials (Basel, Switzerland) 2020, 13. https://doi.org/10.3390/ma13071518
Hass, L.; Bos, F. Bending and Pull-Out Tests on a Novel Screw Type Reinforcement for Extrusion-Based 3D Printed Concrete. In Second RILEM International Conference on Concrete and Digital Fabrication; Bos, F.P., Lucas, S.S., Wolfs, R.J.M., Salet, T.A.M., Eds.: Springer International Publishing: Cham, 2020, pp. 632–645. https://doi.org/10.1007/978-3-030-49916-7_64
Marchment, T.; Sanjayan, J. Mesh reinforcing method for 3D Concrete Printing. Automation in Construction 2020, 109. https://doi.org/10.1016/j.autcon.2019.102992
Bos, F.P.; Ahmed, Z.Y.; Jutinov, E.R.; Salet, T.A.M. Experimental Exploration of Metal Cable as Reinforcement in 3D Printed Concrete. Materials (Basel, Switzerland) 2017, 10. https://doi.org/10.3390/ma10111314
Bos, F.P.; Bosco, E.; Salet, T.A.M. Ductility of 3D printed concrete reinforced with short straight steel fibers. Virtual and Physical Prototyping 2019, 14, 160–174. https://doi.org/10.1080/17452759.2018.1548069
Ma, G.; Li, Z.; Wang, L.; Wang, F.; Sanjayan, J. Mechanical anisotropy of aligned fiber reinforced composite for extrusion-based 3D printing. Construction and Building Materials 2019, 202, 770–783. https://doi.org/10.1016/j.conbuildmat.2019.01.008
Hack, N.; Lauer, W.V.; Gramazio, F.; Kohler, M. Mesh Mould: Robotically Fabricated Metal Meshes as Concrete Formwork and Reinforcement. In Proceedings of the 11th International Symposium on Ferrocement and 3rd ICTRC International Conference on Textile Reinforced Concrete 2015.
Kloft, H.; Hack, N.; Mainka, J.; Brohmann, L.; Herrmann, E.; Ledderose, L.; Lowke, D. Additive Fertigung im Bauwesen: erste 3-D-gedruckte und bewehrte Betonbauteile im Shotcrete-3-D-Printing-Verfahren (SC3DP). Bautechnik (96) 2019, 929–938. https://doi.org/10.1002/bate.201900094
Kloft, H.; Empelmann, M.; Oettel, V.; Ledderose, L. 3D Concrete Printing – Production of first 3D Printed Concrete Columns and Reinforced Concrete Columns. BFT International, no. 6 2020, 28–37.
Hack, N.; Bahar, M.; Hühne, C.; Lopez, W.; Gantner, S.; Khader, N.; Rothe, T. Development of a Robot-Based Multi-Directional Dynamic Fiber Winding Process for Additive Manufacturing Using Shotcrete 3D Printing. Fibers 2021, 9, 39. https://doi.org/10.3390/fib9060039
Mechtcherine, V.; Grafe, J.; Nerella, V.N.; Spaniol, E.; Hertel, M. 3D-printed steel reinforcement for digital concrete construction - Manufacture, mechanical properties and bond behaviour. Construction and Building Materials 2018, 125–137. https://doi.org/10.1016/j.conbuildmat.2018.05.202
Müller, J.; Grabowski, M.; Müller, C.; Hensel, J.; Unglaub, J.; Thiele, K.; Kloft, H.; Dilger, K. Design and Parameter Identification of Wire and Arc Additively Manufactured (WAAM) Steel Bars for Use in Construction. Metals 2019, 9, 725. https://doi.org/10.3390/met9070725
Weger, D.; Baier, D.; Straßer, A.; Prottung, S.; Kränkel, T.; Bachmann, A.; Gehlen, C.; Zäh, M. Reinforced Particle-Bed Printing by Combination of the Selective Paste Intrusion Method with Wire and Arc Additive Manufacturing – A First Feasibility Study. In Second RILEM International Conference on Concrete and Digital Fabrication; Bos, F.P., Lucas, S.S., Wolfs, R.J.M., Salet, T.A.M., Eds.: Springer International Publishing: Cham, 2020, pp. 978–987. https://doi.org/10.1007/978-3-030-49916-7_95
Classen, M.; Ungermann, J.; Sharma, R. Additive Manufacturing of Reinforced Concrete—Development of a 3D Printing Technology for Cementitious Composites with Metallic Reinforcement. Applied Sciences 2020, 10. https://doi.org/10.3390/app10113791
Kloft, H.; Hack, N.; Lindemann, H.; Mainka, J. Shotcrete 3D Printing (SC3DP) - 3D-Drucken von großformatigen Betonbauteilen. Deutsche Bauzeitschrift 2019, 54 - 57.
Baz, B.; Aouad, G. ; Leblond, P.; Al-Mansouri, O.; D’hondt, M.; Remond, S. Mechanical assessment of concrete – Steel bonding in 3D printed elements. Construction and Building Materials 2020, 256. https://doi.org/10.1016/j.conbuildmat.2020.119457
Mechtcherine, V.; Nerella, V.N. Integration der Bewehrung beim 3D-Druck mit Beton. Beton- und Stahlbetonbau 2018, 113, 496–504. https://doi.org/10.1002/best.201800003
Matthäus, C.; Kofler, N.; Kränkel, T.; Weger, D.; Gehlen, C. Interlayer Reinforcement Combined with Fiber Reinforcement for Extruded Lightweight Mortar Elements. Materials (Basel, Switzerland) 2020, 13. https://doi.org/10.3390/ma13214778
Gebhard, L.; Mata-Falcón, J.; Markić, T.; Kaufmann, W. Aligned Interlayer Fibre Reinforcement for Digital Fabrication with Concrete. In Fibre Reinforced Concrete: Improvements and Innovations; Serna, P., Llano-Torre, A., Martí-Vargas, J.R., Navarro-Gregori, J., Eds.: Springer International Publishing: Cham, 2021, pp. 87–98. https://doi.org/10.1007/978-3-030-58482-5_8
Dreßler, I. ; Freund, N.; Lowke, D. The Effect of Accelerator Dosage on Fresh Concrete Properties and on Interlayer Strength in Shotcrete 3D Printing. Materials Journal, Special Issue “Concrete 3D Printing and Digitally-Aided Fabrication” 2020. https://doi.org/10.3390/ma13020374
Neudecker, S.; Bruns, C.; Gerbers, R.; Heyn, J.; Dietrich, F.; Dröder, K.; Raatz, A.; Kloft, H. A New Robotic Spray Technology for Generative Manufacturing of Complex Concrete Structures Without Formwork. Procedia CIRP 2016, 43, 333–338. https://doi.org/10.1016/j.procir.2016.02.107
Kloft, H.; Krauss, H.-W.; Hack, N.; Herrmann, E.; Neudecker, S.; Varady, P.A.; Lowke, D. Influence of process parameters on the interlayer bond strength of concrete elements additive manufactured by Shotcrete 3D Printing (SC3DP). Cement and Concrete Research 2020, 134, 106078. https://doi.org/10.1016/j.cemconres.2020.106078
RILEM RC6. Bond test for reinforcement steel: 2. Pull-out test, 1983.
Lootens, D.; Jousset, P.; Martinie, L. ; Roussel, N.; Flatt, R.J. Yield stress during setting of cement pastes from penetration tests. Cement and Concrete Research 2009, 39, 401–408. https://doi.org/10.1016/j.cemconres.2009.01.012
Paglia, C.; Wombacher, F.; Böhni, H. Influence of alkali-free and alkaline shotcrete accelerators within cement systems: hydration, microstructure, and strength development. ACI Materials Journal 101 (5) 2004, 353–357.
Aeditive Promotes Shotcrete 3D Printing of Reinforced Concrete Structures
News
to grow full-fledged reinforced concrete structures in an automated manner using multi-axis robotic manipulators.
In short, the technology is an automated version of shotcrete, a well-known and widely used method of applying mortar to surfaces using compressed air. Usually this technique is used to increase the strength of concrete, brick or stone buildings, or to repair concrete and reinforced concrete structures. Aeditive uses shotcrete in a broader additive way as a kind of 3D printing technique.
The technology is reduced to the application of building mix on pre-prepared reinforcement. As with the more familiar 3D construction printing techniques a la Contour Crafting, the advantage is that there is no need for formwork. As a rule, construction 3D printers print fixed formwork, into which, if necessary, reinforcing elements and communications are manually inserted, after which concrete is poured. Here, the opposite is true: first, reinforcement is installed, communication elements are inserted into it, and then a monolithic concrete shell is grown around the reinforcement and filling.
The process is highly automated: the installation of reinforcement and the application of the mixture are carried out using two multi-axis robotic arms mounted on rails to increase coverage. The official name of the process is Robotic Shotcrete Printing (RSP). If necessary, the same robots can perform surface post-processing. 3D printing is carried out on a steel pallet, which, together with the printed product, can be moved by crane to storage for strength while the system works on the next products.
In its current form, the plant is capable of producing arbitrary-shaped reinforced concrete blocks up to 11x4x4 meters in size both in workshop conditions and at the construction site. To do this, the entire system, complete with accessories, can be loaded into eight shipping containers. A supply of consumables and a connection to water and electricity will be required on site. Integration with BIM software tools is planned but not yet implemented. The cost of mixtures is slightly higher than the cost of conventional materials due to the use of special additives, but the developers claim that this is more than offset by the absence of the need to manufacture formwork. Obviously, the most beneficial use of this technique in the construction of non-standard structures.
This spring, the company announced the recruitment of industry partners to participate in a pilot program to demonstrate the capabilities of robotic shotcrete printing technology in practice. The company expects to demonstrate the first full-fledged construction project in the second quarter of next year. Additional information about Aeditive's offers is available on the official website.
construction Editive shotcrete
Follow author
Follow
Don't want
1
More interesting articles
12
Subscribe to the author
Subscribe
Don't want
Jetson One is an eight-engine electric aircraft designed for one person. The design uses...
Read more
ten
Follow the author
Subscribe
Don't want
In an interview with the magazine, Veronika Levenets revealed her success story, spoke about the role of inclusion, and that. ..
Read more
sarkazm
Loading
04/01/2016
39928
68
Subscribe to the author
Subscribe
Don't want
News from the world of printing in a short line
FDplast announced the release of a free...
Read more
Application of ground concrete in 3d printing
A.V. Gubanov 1,a , V.A. Kutugin 2,b , E.A. Novikova
1 Tomsk State University (Russia, Tomsk, Lenin Ave., 36, 634050), 2 Tomsk Polytechnic University (Russia, Tomsk, Lenin Ave., 30, 634050)
E-mail: a derzhiarbuz@gmail. com, b [email protected]
Introduction
3D printing of buildings and small architectural forms is one of the developing directions in additive technologies. The key differences between construction 3D printing and other types of printing are the large size of the printed object, its strength and durability in changing climatic conditions, as well as lower requirements for printing accuracy.
The main approach used in building 3D printing today is to layer-by-layer pre-mixed concrete along a predetermined path. This approach is widely known under the name Contour Crafting. In this technology, as a rule, rather liquid concrete mixtures with a long setting time are used. They are commercially available as dry mixes and are available, but they are difficult to print objects with edges that deviate greatly from the vertical. Printing arched and vaulted structures with such materials is difficult.
Free-form objects made of concrete can be obtained with D-shape technology, a variant of the binder-jetting technology for large-sized products. The object is grown in layers in a volume completely filled with dry powder, then the excess powder is removed. The disadvantage of this technology is that the product must be entirely placed inside a container filled with a dry mixture, and the bulk of the mixture is not used.
Another radically different construction printing method is printing with polymer concretes, in which the inorganic aggregate is in a matrix of thermoplastic or photopolymer. This approach makes it possible to print geometry of any complexity available for 3D printing with plastics (including arches and ceilings), however, the use of plastics as a building material has certain disadvantages (high cost of plastic compared to inorganic materials, lower fire resistance, shorter service life). In addition, there are technologies for printing with sulfur concrete, foaming compositions, shotcrete, etc.
This work is devoted to the use of such material as ground concrete in 3D printing. Some features of working with this material, its distinctive properties and their influence on the 3D printing process, as well as the results obtained are considered.
Purpose
The main purpose of this work was to elucidate the fundamental possibility of 3D printing of objects with a geometry that strongly deviates from the vertical (vaults, arches) using a material made from available mineral raw materials (ground concrete).
Tasks
3D printing mix properties study:
- determination of the minimum shear stress of the freshly mixed mixture;
- determination of the ability of the mixture to plastic deformation without rupture;
- determination of the strength characteristics of hardened composites (resistance to compression, rupture) depending on humidity;
3D printing:
- development of a CNC router of sufficient size and bearing capacity;
- development of a prototype of a print head for printing with a model mixture and printing of test samples;
- development of a prototype printhead for printing with a target mixture and printing test samples.
Soiled concrete
Soiled concrete is a building material obtained from cohesive soils (clays, loams, sandy loams), mineral binders, water and various additives. As a rule, soil-concrete is obtained in a semi-dry way and is used for molding building blocks, building foundations [2], walls of buildings as a whole.
The use of soil as a building material has a long history [1]. In regions with a dry climate, buildings are erected from non-cohesive soils reinforced with organic fibers (adobe, adobe). The Italian company WASP proposed using adobe 3D printing as a way to solve the problem of affordable housing in arid regions and created the Big Delta printer [7].
In regions with a humid climate, soil modification with mineral binders allows the construction of adobe structures that are resistant to moisture.
Despite the availability of raw materials for the production of soil concrete, it is not widely used. Soil concrete is plastic and molded by pressure, it cannot be poured into molds or effectively compacted by vibration, and the strength of soil concrete [2] is inferior to the strength of concrete based on sand-cement mixtures and does not allow the construction of high-rise buildings. As a result, it is not economically feasible to use soil concrete in mass construction.
However, the plasticity property becomes extremely useful when it comes to the use of the material in 3D printing.
Rheological properties of soil concrete
The main component of soil concrete is clay or loam, so its rheological properties are close to those of clays and loams. The introduction of cement, which is an electrolyte, slightly worsens plasticity, but in general, the behavior of a fresh soil-concrete mixture is similar to the behavior of clay or loam, on the basis of which it is made.
In a certain humidity range, the rheology of clays and loams is well described by the Bingham fluid model [8]. The Bingham fluid behaves like a solid body until the shear stress between the layers reaches a certain value min , called the minimum shear stress. When this voltage is exceeded, the Bingham fluid flows like a Newtonian fluid. Thus, the Bingham fluid is plastic - it changes shape when force is applied and retains it after the force is removed.
3D printing technology that uses the plasticity property of ink to form spatial objects is called DIW (direct ink writing) and its use for printing ceramic products is widespread. This technology allows you to print quite complex geometry with large angles of deviation from the vertical (45 degrees and above).
The experimentally obtained value min , suitable for 3D printing of large-sized products, lies in the range from 0.2 to 0.25 MPa. The value was obtained using a modified Lotov viscometer [9] for soil concrete based on clay from the Kornilov deposit in the Tomsk region.
This value allows you to design an extruder that must create a pressure at the outlet that is not less than min .
Unlike soil, soil concrete, being mixed with water, rather quickly changes its plastic properties. Clay-based soil concrete containing 20% cement becomes unprintable 20 minutes after mixing with water, and soil concrete containing 50% cement loses plasticity after 5 minutes.
Ground concrete as a structural material
In order for ground concrete to be strong, it is necessary to provide moist curing conditions for a rather long period of time. According to the authors of [2], soil concrete should be in a humid environment for the first 2 weeks. Under normal hardening conditions, after a week, it will gain 2/3 of its design strength. Most likely, the long curing time is due to the fact that the main component of soil concrete, soil, shrinks when moisture is lost.
The compressive strength grade for ground concrete used for 3D printing lies within M50 - M100, which is sufficient for the construction of low-rise buildings, provided that the ground concrete will only experience compressive loads. The tensile strength of soil concrete is extremely low compared to reinforced concrete.
Given these properties, as well as the fact that soil concrete allows printing relatively complex geometry, it is supposed to use this material not for printing load-bearing structures, but for printing fixed formwork, into which micro-reinforced concrete based on sand-cement mixture could then be poured. Printing thin-walled structures, the strength and rigidity of which is enough to support themselves and the aggregate will allow using the strengths of soil concrete and negate its shortcomings, as well as reduce the time of 3D printing and the construction of the object as a whole.
Mixing in small volumes
Due to the fact that soil concrete quickly loses its plastic properties after mixing with water, it is not possible to use the technical solutions common in DIW technology for delivering material to the printing point.
It is necessary to have a print head of a special device, into which the dry mixture and the mixing liquid are transported separately and mixed in a continuous mode just before extrusion.
A feature of 3D printing using DIW technology is that the amount of material in a state suitable for extrusion per unit of time is very small. This is the hallmark of any path-based 3D printing method compared to traditional manufacturing methods. Due to this, the mechanisms that carry out a certain technological process with the printing material can be significantly smaller and structurally simpler than the mechanisms for carrying out the same processes in industrial volumes.
When mixing a dry mixture with a liquid continuously in a small volume, capillary suction becomes a significant factor influencing the speed of mixing. Thus, a dry, loosely poured soil-concrete powder that comes into contact with a liquid is impregnated with it to a depth of 15 mm, and the liquid penetrates to a depth of 10 mm in a few seconds. If the cross section of the channel in which the mixing takes place does not exceed 10 mm in its largest dimension, the need for intensive mechanical movement of the particles of the mixture relative to each other is actually eliminated.
It has been experimentally found that in order to obtain a homogeneous rope with a diameter of 10 mm extruded under a pressure of 0.25 MPa from a dry mixture and a mixing liquid, the length of the mixing and extrusion area can be no more than 250 mm. In this case, the time from the moment the mixture is mixed with liquid to the moment of extrusion in the developed device does not exceed 30 s.
Results
To make sure that the specified properties of soil concrete allow printing objects with faces that deviate strongly from the vertical, a CNC router with a working area of 1500x1500x1300 mm was developed, a print head that performs mixing and extrusion of soil concrete in continuous mode and software management.
The result of the work done was the printing of a soil-concrete dome 350 mm high, with a maximum angle of deviation of the wall from the vertical of 45 degrees and a wall thickness of 20 mm (Fig. 1). Soil concrete composition: 50% clay, 50% cement without any additional additives (except water). Thus, the fundamental possibility of using a simple in composition, accessible inorganic material for printing vaulted thin-walled structures using DIW technology has been demonstrated.
USING SOIL CONCRETE IN 3D PRINTING Gubanov 1,a V. A. Kutugin 2,b , E.A. Novikova
1 Tomsk state university, Tomsk, Russia, 2 Tomsk polytechnic university, Tomsk, Russia
a [email protected] , b [email protected]
Construction 3D printing (3DCP) is one of the developing branches of additive technology. Main differences from other 3D printing technologies are a large size of printed object, it’s solidity, durability in different climate conditions, relatively low accuracy requirements.
Cement based soil concrete is known, but rarely used construction material for buildings. It has serious disadvantages that make it impracticable for classical building technologies, but also it has some useful properties that make it suitable for 3D printing process. The objective of the research is to show a possibility to print arches and domes with at least 45 degrees overhang (which is hardly achievable for Contour Crafting) using cement based soil concrete as material. To reach this goal several concrete composition was tested, then suitable 3D printer and printhead was made and printing process implemented.
The main useful property of a soil concrete is it’s plasticity (rheological model of Bingham fluid can be used) during the first several minutes it was mixed with a water. Fortunately the plasticity allows to implement DIW (direct ink writing) printing method and reach the whole specter of a geometry could be printed with clay. Unfortunately it is impossible to use common DIW extruder types because of short lifetime of a fresh mixed printing media, so the special hardware have to be designed.
To implement a soil concrete 3D printing process there should be an extruder, that is a mixer also, so we could mix a dry component powder with a water (or another fluid) continuously, following right proportions, and extrude it as soon as possible before rheological properties of mixture gone unsatisfactory. The possibility to make relatively small and lightweight suitable hardware caused by the fact that a mixing of fluid and powder in small volume is significantly affected by capillary suction, so there is no lengthy and intensive mechanical mixing needed.