Shapeways metal 3d printing
Shapeways: Metal 3D Printing Service
What is Metal 3D Printing?
Metal additive manufacturing technology like Binder Jetting, Selective Laser Melting, and Wax Casting make it possible for Shapeways customers to enjoy metal 3D printed parts that are extremely strong, complex, and lightweight.
Contact Sales
History of Metal Printing
Metal 3D printing is one of the original additive manufacturing technologies, stemming from development in the late 80’s. Beginning with the work of Carl Deckard in partnership with Dr. Joe Beaman at the University of Texas at Austin, their pioneering efforts began in Selective Laser Sintering–a technology highly associated with powder-based thermoplastics today. At that time, however, Deckard was intrigued by the concept of creating a solution for rapid prototyping and more efficient manufacturing in metal. He realized he could do so by fusing metal particles together and building upon them layer by layer–with the ultimate goal of translating this work to industrial factories.
At the same time, parallel research and development regarding 3D printing with metal was ongoing at the Fraunhofer Institute with Selective Laser Melting–also known as Direct Metal Laser Sintering (DMLS)–and connected with similar technology like Electron Beam Melting (EMB). Binder Jetting was also on the precipice of becoming patented (licensed to ExOne in 1995), offering unique technology built around metal powder particles adhering together with the strength of a liquid binding agent.
Current Trends in 3D Printing Metal
3D printing in metal continues to surge in popularity, and is expected to expand at a compound annual growth rate of almost 25% through 2030. Accelerated growth–with SLM 3D printing at the forefront– is attributed to advancement in a wide range of applications.
“Increasing adoption of metal 3D printers for the designing and prototyping of products and objects, coupled with the reduced manufacturing expenditure and accuracy in the end product, is a key market proliferating factor. The market is poised to witness high demand arising prominently from the healthcare, automotive, aerospace, and defense sectors. Growing advancements in the healthcare sector to curb physical disabilities and ensure healthy living are influencing the sector to flourish and adopt new innovative methodologies, such as 3D printing. Additionally, the automotive and aerospace sectors, where prototyping and designing play a vital role in research and development to achieve perfection in their production are leading towards greater opportunities and increasing the adoption of the 3D printing process,” states Grand View Research.
“The services segment is expected to expand at a significant CAGR of 23.5% from 2022 to 2030. With the adoption of methodology, metal 3D printing services help manufacturers to produce complicated and delicate functional parts with greater ease and accuracy.”
Purchasing 3D metal printers is extremely cost-prohibitive for most companies, so it makes sense that established metal 3D printing services like Shapeways are projected to continue expanding and contributing substantially to the global market.
Metal 3D Printing Technology and Materials
Binder Jetting Metal 3D Printing
Binder Jetting for 3D printing in metal relies on an adhesive, liquid binding agent that re-coats and saturates the build plate of the printer, layer by layer, building the solid 3D printed structure. The metal 3D printed parts are cured, and then de-powdered in post-processing. Afterward, parts are put through a thermal, sintering operation.
Variables are dependent on the material; for example, in using Steel, there is less shrinkage due to the combination with Bronze. Support materials are not required during printing with either of the metal 3D printers, because surrounding powder acts as a stabilizing force.
Shapeways offers the following metal materials with Binder Jetting:
Stainless Steel 17-4 PH
Known for hardness and toughness, as well as resistance to heat and corrosion, parts 3D printed with this single-alloy usually exhibit superior material properties and high resolution.
Shapeways customers rely on Stainless Steel 17-4 PH for industrial manufacturing of:
- Fasteners
- Jigs and fixtures
- Machine tools
- Parts for oil and gas
- Pump components
- Valving
This material is available in silver, with a granular, semi-matte finish that can be polished. Find out more about design guidelines for Stainless Steel 17-4 PH here.
Stainless Steel 316L
Shapeways customers reply on Stainless Steel 316L properties for the following industrial applications:
- Mechanical machinery
- Medical applications like surgical tooling
- Heat exchangers
- Fasteners and brackets
Stainless Steel 316L is available in a natural finish, blasted with ceramic media for a slightly rough surface and a matte finish. It is also offered in a polished finish, with 3D printed parts tumbled for a smooth surface. Find out more about design guidelines for Stainless Steel 316L here.
Composed of 60% steel and 40% bronze, Steel is affordable, strong, and mainly used for tools and accessories, home decor, and smaller industrial consumer goods.
This metal is available in the following colors:
- Bronze
- Gold
- Nickel
- Bronzed-Silver
- Black
A matte finish is available for Steel, featuring an unpolished, rough surface. A polished finish is offered for shiny, smooth parts; however, note that parts larger than 150 x 150 x 150 or those with thinner details will be finished with bead blasting instead to avoid breakage. This may also present a rougher, less consistent result. Read more about the design guidelines here.
Selective Laser Melting
During SLM 3D printing, an incredibly precise laser acts as the impetus for welding metal powder particles together within an enclosed industrial 3D printer. Layer by layer, the powder is melted until the desired structure is complete, with the part anchored to the build plate (along with support structures) and removed in post processing. At the end of the process, parts and any supports are removed, and the typically rough surface may be further machined.
Shapeways provides the following 3D printing materials for SLM 3D printing:
Aluminum
Shapeways offers the AlSi10Mg alloy for 3D printing with Selective Laser Melting (SLM). A blend of aluminum, silicon, and magnesium, AlSi10Mg is highly suited for parts requiring resistance to corrosion and parts requiring thinner walls. Aluminum is temperature- and pressure-resistant, and skin-friendly. This material is designated for end-use parts that must be strong, highly accurate, and low in weight.
Shapeways customers rely on Aluminum for the following industrial applications:
- Aerospace
- Automotive
- Energy
- Machining
- Medical
- Robotics
Shapeways offers Aluminum in Standard finish only. Find out more about the design guidelines for this metal 3D printing material here.
Lost Wax Casting
For designers and engineers eager to try a variation on metal 3D printing technology–but with a fast and more economical edge–Lost Wax Casting is a great option. Paired with high-quality 3D print Lost Wax Casting materials and precious metals this technique is preferred by many Shapeways customers.
Also referred to as Investment Casting, Precision Casting, or even cire perdue (french), this unique technology has historically been recognized as a strong suit for foundries. Created around 5,000 years ago to make metal products and ammunition, Lost Wax Casting is performed in most instances by pouring red-hot, liquid metal into molds to create structures.
Molds for Lost Wax Casting are 3D printed with metal, thermoplastics like Nylon 12 [Versatile Plastic], MJF Plastic PA12, and other materials like Sandstone and Thermoplastic Polyurethan (TPU).
Wax inserts are most often used, structuring the interior of each mold. Once liquid metal is introduced to the mold for making the desired structure, all the wax melts and is drained. With 3D printing, the cooling process is more stable, and once complete, the solidified metal part can be removed. From there, each casting is an exact replication of the previous one. If the mold requires modifications, the design can be changed accordingly, and the part can be 3D printed again easily.
- Brass – An alloy made up of 15% zinc, 5% tin, and 80% copper, Brass is available with a natural matte finish or a shiny polish, and is offered with Gold Plating or Rhodium Plating.
- Bronze – A copper-tin alloy made up of 10% tin and 90% copper, Bronze is used for jewelry with a vintage appearance, featuring a deep red color, marbling, and silver highlights.
Bronze materials are available in natural matte or polished finishes.
- Copper – Featuring a red-orange color that oxidizes over time, turning to a deeper color, Copper is desired for its corrosion-resistant properties. This material is available in a natural or polished finish.
- Gold – Both 14-carat and 18-carat gold are available in yellow, white, and rose. Intricate designs can be made for valuable parts or fine jewelry with this precious metal.
- Platinum – One of the highest quality metal materials available, Platinum is a white metal used for luxury products. This material is available in a professional finish.
- Silver – A high-quality alloy, Silver tends to be more malleable, and is popular in the jewelry industry. Silver is offered with the following finishes: natural, polished, fine-detail polished, and antique.
Luxury Sterling Silver Jewelry with Handcrafted Touches
As industrial designers and creators of luxury jewelry inspired by nature, Groen and Boothman designed a bracelet series. Shapeways manufactured the parts via Wax Casting with Sterling Silver, which Groen and Boothman then polished. Both the Water and Cosmic bracelets feature a hidden clasp mechanism and hinge in the 3D printed design–exemplifying one of the greatest benefits in 3D printing, with the ability to engineer precise parts with interlocking features.
Testimonials
Ola Shekhtman, Owner and Designer of Cityscape RingsConsumer 3D Printing
It would probably take me about 100 years to produce 1,000 of my rings by hand. It only takes Shapeways 2 to 3 weeks to create and ship the same amount.
On-demand Metal 3D Printing
Designers have vast opportunities for customization in metal 3D printing, coupled with the opportunity to take advantage of on-demand production–one of the greatest benefits built into 3D printing technology. Entire inventories can be managed on a single digital file, in comparison to traditional warehouses holding large stores of parts.
Improved efficiency via on-demand manufacturing also allows Shapeways customers to take their metal 3D printed products to market faster. Other great features include:
- Security in uploading 3D models to the digital inventory.
- Large 3D printed parts with reduced assemblies.
- Strong, lightweight parts that are highly optimized for long-term use.
- Less use of resources, materials, and energy.
Shapeways works with businesses of all types and sizes for on-demand metal 3D printing, allowing them to eliminate product backlogs and prevent supply chain issues. Lead times are eliminated, accelerating the prototyping and metal additive manufacturing process, resulting in a more agile supply chain.
3D printing with metal at Shapeways is as easy as uploading a 3D model (up to 20 a once). At that point, an instant quote is activated, along with automated printability analysis. Expedited shipping is available, whether customers need parts shipped to themselves or their own clients.
Our Most Popular Materials
Shapeways: Steel
60% Stainless Steel / 40% Bronze Matrix Material
Binder Jetting
Upload a model
Loading contents...
Show menu
60% Stainless Steel / 40% Bronze Matrix Material
Binder Jetting
Upload a model
Material info
About Steel
Steel is an affordable and strong metal that is well-suited for consumer products both small and large with an industrial look and feel. It’s printed using a binder jetting process and is later infused with bronze, creating a material that is 60% steel and 40% bronze and can range in color from a silver gray to reddish bronze. It is strong enough for metal parts like bottle openers and dice, but is not recommended for industrial load bearing applications.
Color & Finishes
Bronze
This finish gives the material a brown antique bronze look
Gold
A thin layer of 24K gold plating that will wear with handling
Nickel
A thin layer of nickel plating providing a shiny silver gray color that will wear with handling
Bronzed-Silver
A metallic silvery color with a bronze tint
Black
The black finish gives the material a dark gray to black look
Technology
- Binder Jetting
Technical Documents
Material Properties
Ultimate Strength (ASTM E8)
496 MPa
Elongation (ASTM E8)
7. 0 %
Hardness (ASTM E18)
93 HRb
Description
Material Highlights
good strength, many available colors, supports larger parts
Handling and Care
not food safe, heatproof to 831°C/1521°F
Design Guidelines
Bounding Box
Bounding Box Max
762 × 393 × 393 mm (Bronzed-Silver, Bronze, Black)
178 × 178 × 178 mm (Gold, Nickel)
152 × 152 × 76 (Polished models)
178 × 178 × 178 (Plated models)
Bounding Box Min
6 × 6 × 3 mm
The bounding box is a 3D imaginary outline of a box that encloses the smallest area occupied by your model. Your model must be within the minimum and maximum bounding box sizes. If the size of the model is close to the maximum bounding box, then the printing orientation will be restricted.
Supported Wall Thickness Min
Model’s Longest Dimension:
3 to 75 mm = 1.0 mm
75 to 150 mm = 1. 5 mm
150 to 200 mm = 2.0 mm
200 to 300 mm = 3.0 mm
Unsupported Wall Thickness Min
Model’s Longest Dimension:
3 to 75 mm = 1.0 mm
75 to 150 mm = 1.5 mm
150 to 200 mm = 2.0 mm
200 to 300 mm = 3.0 mm
A supported wall is connected at least on two sides of the wall, while an unsupported wall is connected only on one side of the wall. Walls that do not meet the minimum requirements may not survive printing and cleaning processes. Additionally, models may still be rejected based on the wall geometry of the model. Please consider the size of your model and reinforce the walls or add support structures as needed as minimum guidelines will not always be adequate for large models.
Supported Wires Min
Model’s Longest Dimension:
3 to 75 mm = 1.0 mm
75 to 150 mm = 1.5 mm
150 to 200 mm = 2.0 mm
200 to 300 mm = 3. 0 mm
Unsupported Wires Min
Model’s Longest Dimension:
3 to 75 mm = 1.0 mm
75 to 150 mm = 1.5 mm
150 to 200 mm = 2.0 mm
200 to 300 mm = 3.0 mm
A wire is a circular, rectangular or even triangular feature that is thinner in its unconnected directions than its length. A supported wire is connected at least on two sides of the model, while an unsupported wire is connected on one side of the model. Wires that do not meet the minimum requirements may not survive printing and cleaning processes. Additionally, models may still be rejected based on the wire geometry of the model. Please consider the size of your model and reinforce the wires or add support structures as needed as minimum guidelines will not always be adequate for large models.
Details
Details Min Embossed
1.0 mm high & wide
Details Min Engraved
1. 0 mm high & wide
For text, the ratio between width and depth, should be 1:1 and sans-serif fonts are preferred for line weight consistency.
Escape Holes
Single Escape Hole Diameter (Min)
4.0 mm
Multiple Escape Hole Diameter (Min)
2.0 mm
Escape holes are necessary to empty the support material of a hollow model. Two escape holes at the opposite ends of the model is optimal for the support removal process. Please consider the size of your model and make the escape holes bigger or add more escape holes as needed as minimum guidelines will not always be adequate for large models.
A single escape hole at the end of a cavity will not allow material in the corners near the escape hole to fully escape. So we recommend multiple escape holes at both ends of the cavity.
Clearance
Min
3. 0 mm
Clearance is the space between two individual parts in a model. If the space among the individual parts do not meet the minimum clearance, then parts can fuse together or can be difficult to clean. This is important for movable pieces like hinges, gears, etc.
Sprues
We cannot print Steel parts with sprues. Any part with sprues will be rejected. Since sprues are inherently thin by design, Bronze will not be able to be infiltrated between parts that are sprued and the model will fail in production.
Sprues are wires that keep two or more parts together. Parts should be connected with a minimum of two sprues each. Please consider the size of your sprues and increase them as needed as minimum guidelines will not always be adequate for large models. If the sprues are within the guidelines and are broken, but there is no damage to your model, we will still ship them as is.
Interlocking & Enclosed Parts
Interlocking
No
Enclosed
No
Parts in File
Max
up to 250
Accuracy
Accuracy ±5% The bronze infiltration of each steel part makes this material less dimensionally accurate than other Shapeways materials. Shrinkage is more prevalent, especially on small holes and inner diameters. Accuracy and tolerance can vary greatly depending on the model, and are hard to predict because they are so geometry specific. A 5% deviation on a ring is around 1 US ring size. So if you order a size 6, the deviation could cause the actual print to be a size 5 or 7.
For example: a product with dimensions of 50 x 50 x 100 mm can be 0.05*100 mm = 5 mm bigger or smaller in any direction.
Stay up to date on promotions, case studies, and more.
Newsletter Sign up
Stay up to date on promotions, case studies, and more.
Email Address
Metal 3D Printing - The Essential Guide
There is no hotter trend in 3D printing today than metal. We will talk about metal printing at home, how it is done on an industrial scale, about technologies, applications, printers, processes, prices and materials.
Metal 3D printing has grown in popularity over the past few years. And this is quite natural: each material offers a unique combination of practical and aesthetic qualities, can be suitable for a wide range of products, prototypes, miniatures, decorations, functional details and even kitchen utensils. nine0003
The reason metal 3D printing has become so popular is because the printed objects can be mass-produced. In fact, some of the printed parts are just as good (if not better) than those made with traditional methods.
In traditional production, working with plastic and metal can be quite wasteful - there is a lot of waste, a lot of excess material is used. When an aircraft manufacturer makes metal parts, up to 90% of the material is simply cut off. 3D printed metal parts require less energy and waste is reduced to a minimum. It is also important that the final 3D printed product is up to 60% lighter than a traditional part. Billions of dollars could be saved in the aviation industry alone—mainly through weight savings and fuel savings.
So, what do we need to know about metal 3D printing?
Metal 3D printing at home
If you want to make objects at home that will look like metal, your best bet is to look at metalized PLA filaments (Photo: colorFabb)
Where to start if you want to print metal objects at home ? Given the extreme heat required for true metal 3D printing, a conventional FDM 3D printer will not be able to do this.
It is unlikely that in this decade it will be possible to print with liquid metal at home. Until 2020, you probably will not have a printer specialized for this purpose at home. But in a few years, as nanotechnology advances, we may see significant developments in new applications. This can be 3D printed with conductive silver, which will emit in much the same way as it does in 2D home printers. It will even be possible to mix different materials like plastic and metal in one object. nine0003
Materials for metal 3D printing at home
Even though you can't print actual metal objects at home, you can turn to plastic filament that has metal powders added to it. ColorFabb, ProtoPasta and TreeD Filaments all offer interesting metal-PLA composite filaments. These filaments, containing a significant percentage of metal powders, remain pliable enough to be printed at low temperatures (200 to 300 Celsius) on virtually any 3D printer. At the same time, they contain enough metal to make the final object look, feel, and even weigh like metal. Iron-based filaments even rust under certain conditions. nine0003
But you can go further. Typically, up to 50 percent metal powder is added to 3D printing filament. Dutch company Formfutura says they have achieved 85 percent metal powder with 15 percent PLA. These filaments are called MetalFil Ancient Bronze and Metalfil Classic Copper. They can be printed even at "moderate" temperatures from 190 to 200 degrees Celsius.
Metallic 3D Printing Filament Spools, in this case from SteelFill and CopperFill colorFabb (Steel and Bronze), Ancient Bronze (Ancient Bronze) from Formfutura
Here are the key points about metal printing at home
- Gets a unique metal surface and look
- Ideal for jewelry, figurines, housewares, replicas
- Durability
- Objects are not flexible (structure dependent)
- Objects do not dissolve
- Not considered food safe
- Typical print temperature: 195 - 220°C
- Extremely low shrinkage on cooling
- No table heating required
- Printing complexity is high, requires fine tuning of nozzle temperature, feed rate, post-processing
Preparing Your Home Printer for Metal 3D Printing
Since getting metal 3D prints is more difficult than usual, you may need to upgrade your 3D printer nozzle, especially if you are an entry-level printer. The metal filament wears it out quickly. There are hard-wearing hot-ends (like the E3D V6) that are themselves made of metal. They can withstand high temperatures and fit most printers. Be prepared for the fact that the nozzles will have to be changed frequently, because the metal filament is very abrasive. nine0003
You will also need to take care of the final finishing of the surface (cleaning, grinding, oiling, waxing or priming) so that the printed metal object shines as it should.
How much does metal filament for 3D printing cost?
And what about metal filament for 3D printing? - you ask. Here are a few examples:
- ColorFabb's 750 gram Bronzefill spool is $56.36
- ColorFabb 750g Copperfill Coil $56.36
- Protopasta's Polishable Stainless Steel PLA Composite is $56 for 56 grams of
- Protopasta's Rustable Magnetic Iron PLA Composite is $34.99 for 500 grams of
Industrial metal 3D printing
But what if you want a better result or even full metal 3D printing? Should a real "metal" 3D printer be purchased for business needs? We wouldn't recommend it - unless you're going to be doing it every day. A professional metal 3D printer is expensive: EOS or Stratasys devices will cost you 100-500 thousand dollars. In addition, the costs will be even greater, since you will have to hire an operator, a worker to maintain the machine, as well as to finalize the printouts (polishing, for example). Just a note: In 2016, an affordable metal 3D printer didn't exist. nine0003
Lowering Metal 3D Printing Costs
If you are not going to start a metal 3D printing business, but still need a professionally 3D printed metal part, it is best to contact the appropriate company that provides such services. 3D printing services like Shapeways, Sculpteo and iMaterialise offer direct metal printing.
They currently work with the following metal materials in 3D printing:
- aluminum
- steel
- brass
- copper
- bronze
- sterling silver
- gold
- platinum
- titanium
If you are a jeweler, you can also order wax models for casting in precious metals.
If we talk about wax models, then in most cases they (with subsequent melting) are used when printing with metals (including gold and silver). Not all orders are carried out directly by these firms. They usually turn to other metal 3D printing companies to complete the order. However, the number of such services around the world is growing rapidly. In addition, metal 3D printing techniques are becoming more and more common in companies that offer such services. nine0003
The reason big companies love 3D printing so much is that it can be used to build fully automated lines that produce "topologically optimized" parts. This means that it is possible to fine-tune the raw materials and make the components thicker only if they must withstand heavy loads. In general, the mass of parts is significantly reduced, while their structural integrity is preserved. And this is not the only advantage of this technology. In some cases, the product turns out to be significantly cheaper and affordable for almost everyone. nine0003
Please note that metal 3D printing requires special CAD programs for modeling. It is worth paying attention to the recommendations of Shapeways - 3D printing metal guidelines. To delve further into the topic, check out Statasys’ information on related 3D printers and the nuances of metal 3D printing.
Here are some examples of Benchy test model prices for metal 3D printing:
- Metal plastic: $22.44 (former alumide, PLA with aluminium)
- Stainless steel: $83.75 (plated, polished)
- Bronze: $299.91 (solid, polished)
- Silver: $713.47 (solid, mirror polished)
- Gold: $87.75 (gold plated, polished)
- Gold: $12,540 (solid, 18K gold)
- Platinum: $27,314 (solid, polished)
As you might expect, solid metal 3D printing prices are quite high.
Metal 3D printing. Applications
GE LEAP aircraft engine parts 3D printed at Avio Aero (Photo: GE)
There are several industries already using 3D printers to make everyday objects - you may not even know that these objects are printed. nine0003
- The most common case is surgical and dental implants, which are considered the best option for patients today. Reason: they can be tailored to individual needs.
- Another industry is jewelry. Here, most manufacturers have abandoned resin 3D printing and wax casting, switching directly to metal 3D printing.
- In addition, the aerospace industry is becoming more and more dependent on 3D printed metal objects. The Italian company Ge-AvioAero was the first to do all-metal 3D printing. It manufactures components for LEAP aircraft engines. nine0051
- Another industry targeting metal 3D printing is the automotive industry. BMW, Audi, FCA are seriously considering this technology, not only for prototyping (3D printing has been used for this for quite some time), but also for making real parts.
Before metal 3D printing really takes off, however, there are some hurdles to overcome. And first of all, this is a high price, which cannot be made lower than during molding. Another problem is the low production speed. nine0003
Metal 3D printing.
Technologies
Most metal 3D printing processes start with an “atomized” powder
You can talk a lot about “metal” 3D printers, but their main problems remain the same as any other 3D – printers: software and hardware limitations, material optimization and multimateriality. We won't talk too much about the software, we'll just say that most of the major specialized software companies, such as Autodesk, SolidWorks and solidThinking, try to emphasize as much as possible the fact that as a result of the 3D metal printing process, you can get any shape you want. nine0003
In general, printed metal parts can be as strong as parts made by traditional processes. Parts made using DMLS technology have mechanical properties equivalent to casting. In addition, the porosity of objects made on a good "metal" 3D printer can reach 99.5%. In fact, manufacturer Stratasys claims that 3D printed metal parts perform above industry standards when tested for density. nine0003
3D printed metal can have different resolutions. At the highest resolution, layer thickness is 0.0008 - 0.0012" and X/Y resolution is 0.012 - 0.016". The minimum hole diameter is 0.035 - 0.045". formed layer)
The metal 3D printing process used by most relevant large companies today is called Powder Bed Fusion. This name indicates that some source of energy (a laser or other energy beam) melts an "atomized" powder (i.e., a metal powder that is carefully ground into spherical particles), resulting in layers of a printed object.
There are eight major manufacturers of metal 3D printers in the world that already use this technology; while we are talking here, there are more and more such companies. Most of them are in Germany. Their technologies are called SLM (Selective Laser Melting - selective laser fusion) or DMLS (Direct Metal Laser Sintering - direct metal laser sintering). nine0003
Metal 3D-printing process No. 2:
Binder Jetting (spraying the binder)
under 3DP technology EXONE Metal objects are printed due : ExOne)
Another professional approach that also uses a powder base is called Binder Jetting. In this case, the layers are formed by gluing metal particles together and then sintering (or fusing) them in a high-temperature furnace, just like it is done with ceramics. nine0003
Another option, which is similar to working with ceramics, is mixing metal powder into metal paste. A pneumatically extruded 3D printer (similar to a syringe bioprinter or an inexpensive food printer) forms 3D objects. When the required shape is reached, the object is sent to the furnace, i.e. in the mountains
This approach is used in the Mini Metal Maker, apparently the only inexpensive "metal" 3D printer.
Metal 3D printing process #3: 9Metal Deposition This is not entirely true. Of course, on some desktop device, simply fusing metal threads onto the base will not work. However, very large steel companies can do it. And they do. There are two options for working with "metal surfacing". nine0003
One is called DED (Directed Energy Deposition) or Laser Cladding. Here, a laser beam is used to melt the metal powder, which is slowly released and solidifies as a layer, and the powder is fed using a robotic arm.
Normally the whole process takes place in a closed chamber, but the MX3D project used conventional 3D printing techniques to build a full-size bridge. Another option for metal fusion is called EBAM (Electron Beam Additive Manufacturing - additive electron beam technology), which is essentially soldering, in which a very powerful electron beam is used to melt 3 mm titanium wire, and the molten metal forms very large finished structures. As for this technology, its details are known so far only to the military. nine0003
Metallic 3D printing. Metals
3D Printing Metal #1: Titanium
Pure titanium (Ti64 or TiAl4V) is one of the most commonly used metals for 3D printing and is definitely one of the most versatile, strong and lightweight. Titanium is used both in the melting process in a preformed layer and in the process of spraying a binder and is used mainly in the medical industry (for the manufacture of personal prostheses), as well as in the aerospace industry, automotive and machine tools (for the manufacture of parts and prototypes). But there is one problem. Titanium is very reactive and explodes easily in powder form. Therefore, it is necessary that titanium 3D printing takes place in a vacuum or in an argon environment. nine0003
3D printing metal #2: Stainless steel
Stainless steel is one of the cheapest 3D printing metals. At the same time, it is very durable and can be used in a wide range of manufacturing and even artistic and design applications. The type of steel alloy used also contains cobalt and nickel, is very difficult to break, and has a very high elasticity. Stainless steel is used almost exclusively in industry. nine0003
3D Printing Metal #3: Inconel
Inconel is a superalloy manufactured by Special Metals Corporation and is a registered trademark. The alloy consists mainly of nickel and chromium and is very heat resistant. Therefore, it is used in the oil, chemical and aerospace (for black boxes) industries.
3D Printing Metal #4: Aluminum
Due to its lightness and versatility, aluminum is very popular in 3D printing. Aluminum alloys are commonly used. nine0003
3D Printing Metal #5: Cobalt Chrome
gap). It is most commonly used in the manufacture of turbines, dental and orthopedic implants, where 3D printing has become the dominant technology.
3D printing metal #5. Copper and bronze
With some exceptions, copper and bronze are used in wax melting processes, rarely in layer melting. The fact is that these metals are not very suitable for industry, they are more often used in the manufacture of works of art and crafts. ColorFabb offers both metals as the basis for a special metal filament.
3D printing metal #6. Iron
Iron, incl. magnetic, also mainly used as an additive to PLA-based filaments, which are produced, for example, by ProtoPasta and TreeD. nine0003
3D printing metal #7. Gold, Silver, and Other Precious Metals
Most preformed layer companies can 3D print precious metals such as gold, silver, and platinum. Here, along with the preservation of the aesthetic properties of materials, it is important to achieve optimization of work with expensive starting powder. Precious metal 3D printing is required for jewelry, medical applications and electronics. nine0003
Metallic 3D printing. Printers
Do not hesitate - the purchase of a metal 3D printer will not pass without a trace on your budget. It will cost at least 100-250 thousand dollars. Here is a list of a variety of "metal" printers, some of which can be found in firms providing 3D printing services.
Metal 3D Printer #1:
Sciaky EBAM 300 - Metal Filament Printing
If you need to print really large metal structures, Sciaky's EBAM technology is your best bet. By order, the device can be built in almost any size. This technique is used mainly in the aerospace industry and the military.
Sciaky's largest production printer is the EBAM 300. It prints objects in a volume of 5791 x 1219 x 1219 mm.
The company claims the EBAM 300 is also one of the fastest industrial 3D printers on the market. A three-meter-sized titanium part for an aircraft is printed on it in 48 hours, while the material consumption is about 7 kg per hour. In general, forged parts that usually take 6-12 months to complete can be made in 2 days with this 3D printer. nine0003
The metal layers are first cut and then ultrasonically welded. The largest Fabrisonic 7200 printer operates in a volume of 2 x 2 x 1.5 m. The metal powder 3D printer is the Concept Laser XLine 1000. It has a modeling volume of 630 x 400 x 500 mm and is the size of a house. nine0003
Its German company, one of the main suppliers of 3D printers for aerospace giants like Airbus, recently introduced a new machine, the Xline 2000.
This machine uses two lasers and has a working volume of 800 x 400 x 500 mm. Uses LaserCUSING laser technology (a variant of selective laser fusion) from Concept Laser, which allows you to print alloys of steel, aluminum, nickel, titanium, precious metals and even some pure substances (titanium and stainless steel). nine0003
Metallic 3D printing. Services
There are more than 100 companies worldwide offering metal 3D printing services. We list the most popular services for consumer needs.
Metal 3D Printing Service #1: Shapeways
The world's most popular 3D printing service, Shapeways offers two types of services. As a consumer, you can choose from a wide range of professionally designed objects, customize them, and then have them printed to your specifications. Like other 3D printing services, Shapeways offers a platform for designers to sell and print their work. Shapeways is also a good place for rapid prototyping: customers benefit from industrial-grade printers (EOS, 3D Systems) and personal technical support. nine0003
3D printing metals: aluminium, brass, bronze, gold, platinum, precious metal plating, silver, steel. There are also wax molds for jewelry purposes.
Metal 3D Printing Service #2: Sculpteo
Like Shapeways and i.materialise, Sculpteo is an online 3D printing service that allows anyone to upload 3D models and send them to fabrication in a wide range of materials . Like its competitors, Sculpteo provides a platform for hobbyists and professionals to showcase and sell their designs. The stable of Sculpteo printers includes highly professional machines from 3D Systems, EOS, Stratasys and ZCorp. Extensive technical documentation will help identify design flaws and select the right material for the project. nine0003
Metals for 3D printing: alumide (plastic with aluminum particles), brass, silver.
Metal 3D Printing Service #3: iMaterialise
Materialise is a company that works with industrial customers to prototyp 3D printed products. For casual users and designers, Materialize offers an online 3D printing service called i.materialise. As with Shapeways, this service allows anyone to upload their 3D designs and print them out. Once an object has been uploaded and successfully printed, a designer can list it for sale either in the gallery of the i.materalise online store or by embedding some code into their website. nine0003
3D printing metals: alumide (plastic with aluminum powder), brass, bronze, copper, gold, silver, steel, titanium.
Metal 3D Printing Service #4: 3D Hubs
Through 3D Hubs, you can search for individuals and companies that offer 3D printing services in your area, upload STL files (which are immediately evaluated for defects ) and contact service providers directly to get the job done. The online 3D printing service also allows you to sort offers by materials, customer rating, distance and many other parameters. Whatever object you wish to print, there is likely to be someone nearby who can print it. A significant number of materials can be printed in industrial quality, such materials have an HD mark in the search field. nine0003
3D printing metals: aluminium, bronze, cobalt-chromium, stainless steel, titanium.
How metal 3D printers work. Overview of SLM and DMLS technologies. additive manufacturing. 3D metal printing.
Metal 3D printing. Additive technologies.
SLM or DMLS: what's the difference?
Hello everyone, Friends! 3DTool is with you!
BLT metal 3D printer catalog nine0003
Selective laser melting ( SLM ) and direct metal laser sintering ( DMLS ) are two additive manufacturing processes that belong to the family of 3D printing , using the powder layer method. The two technologies have much in common: they both use a laser to selectively melt (or melt) metal powder particles, bonding them together and creating a pattern layer by layer. In addition, the materials used in both processes are metals in granular form. nine0003
The differences between SLM and DMLS come down to the basics of the particle bonding process: SLM uses metal powders with a single melting point and completely melts the particles, while in DMLS the powder consists of materials with variable melting points.
In particular:
SLM produces single metal parts while DMLS produces metal alloy parts.
Both SLM and DMLS technologies are used in industry to create final engineering products. In this article, we will use the term "metal 3D printing" to summarize the 2 technologies. We will also describe the main mechanisms of the manufacturing process that are necessary for engineers to understand the advantages and disadvantages of these technologies. nine0006 There are other manufacturing processes for producing dense metal parts, such as electron beam melting (EBM) and ultrasonic additive manufacturing (UAM). Their availability and distribution is rather limited, so they will not be presented in this article.
How 3D printing with SLM or DMLS metal works.
How does metal 3D printing work? The basic manufacturing process for SLM and DMLS is very similar.
1. The printing chamber is first filled with an inert gas (such as argon) to minimize the oxidation of the metal powder. It then heats up to the optimum operating temperature. nine0006 2. A layer of powder is spread over the platform, a powerful laser makes passes along a predetermined trajectory in the program, fusing the metal particles together and creating the next layer.
3. When the sintering process is completed, the platform moves down 1 layer. Next, another thin layer of metal powder is applied. The process is repeated until the entire model is printed.
When the printing process is completed, the metal powder already has strong bonds in the structure. Unlike the SLS process, parts are attached to the platform via support structures. The support in metal 3D printing is created from the same material as the base part. This condition is necessary to reduce deformations that may occur due to high processing temperatures. nine0006 When the 3D printer's chamber cools down to room temperature, excess powder is removed manually, such as with a brush. The parts are then typically heat treated while they are still attached to the platform. This is done to relieve any residual stresses. They can then be further processed. The removal of the part from the platform occurs by means of sawing.
The scheme of the 3D printer for metal.
In SLM and DMLS, almost all process parameters are set by the manufacturer. The layer height used in metal 3D printing varies from 20 to 50 microns and depends on the properties of the metal powder (fluidity, particle size distribution, shape, etc.). nine0006 The basic size of the print area on metal 3D printers is 200 x 150 x 150 mm, but there are also larger sizes of the working area. Printing accuracy is from 50 - 100 microns. As of 2020, metal 3D printers start at $150,000. For example, our company offers 3D metal printers from BLT.
Metal 3D printers can be used for small batch production, but the 3D printing capabilities of such systems are more like those of mass production on FDM or SLA machines. nine0006 The metal powder in SLM and DMLS is recyclable: typically less than 5% is consumed. After each impression, the unused powder is collected and sieved, and then topped up with fresh material to the level required for the next production.
Waste in metal printing, are supports (support structures, without which it will not be possible to achieve a successful result). With too much support on the manufactured parts, the cost of the entire production will increase accordingly. nine0006
Adhesion between coats.
3D metal printing on BLT 3D printers
SLM and DMLS metal parts have almost isotropic mechanical and thermal properties. They are hard and have very little internal porosity (less than 0.2% in 3D printed condition and virtually non-existent after processing).
Metal printed parts have higher strength and hardness and are often more flexible than traditionally made parts. However, such metal becomes “tired” faster. nine0003
3D model support structure and part orientation on the work platform.
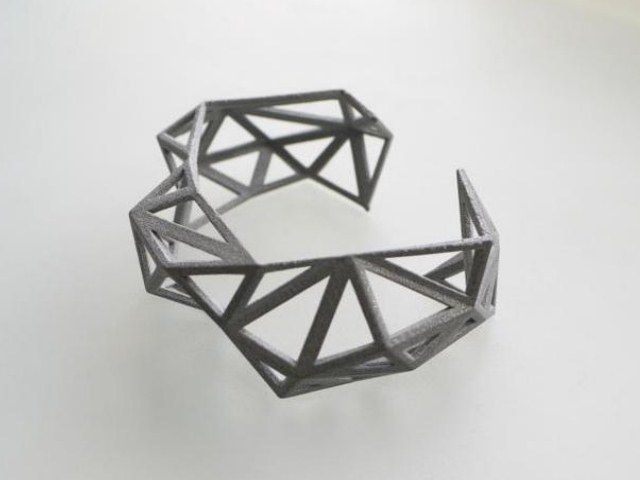
Support structures are always required when printing with metal, due to the very high processing temperatures. They are usually built using a lattice pattern.
Supports in metal 3D printing perform 3 functions:
• They form the basis for creating the first layer of the part.
• They secure the part to the platform and prevent it from deforming.
• They act as a heat sink, removing heat from the model. nine0003
Parts are often oriented at an angle. However, this will increase the amount of support required, the printing time, and ultimately the overall cost.
Deformation can also be minimized with laser sintering templates. This strategy prevents the accumulation of residual stresses in any particular direction and adds a characteristic surface texture to the part.
Since the cost of metal printing is very high, software simulations are often used to predict how a part will behave during processing. These topology optimization algorithms are otherwise used not only to increase mechanical performance and create lightweight parts, but also to minimize the need for supports and the likelihood of part distortion. nine0003
Hollow sections and lightweight structures.
An example of printing on a BLT 3D printer
Unlike polymer powder melt processes such as SLS, large hollow sections are not typically used in metal printing as the support would be very difficult to remove, if at all possible.
For internal channels larger than Ø 8 mm, it is recommended to use diamond or teardrop cross-sections instead of round ones, as they do not require the construction of supports. More detailed recommendations on the design of SLM and DMLS can be found in other articles on this topic. nine0003
As an alternative to hollow sections, parts can be made with sheath and cores, which in turn are machined using different laser power and pass speeds, resulting in different material properties. The use of sheath and cores is very useful when making parts with a large solid section, as it greatly reduces printing time and reduces the chance of warping.
The use of a lattice structure is a common strategy in metal 3D printing to reduce part weight. Topology optimization algorithms can also help design organic lightweight shapes. nine0003
Consumables for 3D metal printing.
SLM and DMLS technologies can produce parts from a wide range of metals and metal alloys, including aluminum, stainless steel, titanium, cobalt, chromium and inconel. These materials meet the needs of most industrial applications, from aerospace to medical applications. Precious metals such as gold, platinum, palladium and silver can also be processed, but their use is of a minor nature and is mainly limited to jewelry making. nine0003
The cost of metal powder is very high. For example, a kilogram of 316 stainless steel powder costs approximately $350-$450. For this reason, minimizing part volume and the need for supports is key to maintaining optimal manufacturing cost.
The main advantage of metal 3D printing is its compatibility with high-strength materials such as nickel or cobalt-chromium superalloys, which are very difficult to process with traditional methods. Significant cost and time savings can be achieved by using metal 3D printing to create a near-clean shape part. Subsequently, such a part can be processed to a very high surface quality. nine0006
Metal post-processing.
Various post methods. treatments are used to improve the mechanical properties, accuracy and appearance of metal printed products.
Mandatory post-processing steps include the removal of loose powder and support structures, while heat treatment (heat annealing) is typically used to relieve residual stresses and improve the mechanical properties of the part.
CNC machining can be used for critical features (such as holes or threads). Sandblasting, plating, polishing, and micro-machining can improve the surface quality and fatigue strength of a metal printed part. nine0003
Advantages and disadvantages of metal 3D printing.
Pros:
1. Metal 3D printing can be used to make complex custom parts, with geometries that traditional manufacturing methods cannot provide.
2. Metal 3D printed parts can be optimized to increase their performance with minimal weight.
3. Metal 3D printed parts have excellent physical properties, metal 3D printers can print a wide range of metals and alloys. Includes difficult-to-machine materials and metal superalloys. nine0003
Cons:
1. Manufacturing costs associated with metal 3D printing are high. The cost of consumables is from $ 500 per 1 kg.
2. The size of the working area in metal 3D printers is limited.
Conclusions.
• Metal 3D printing is most suitable for complex, one-piece parts that are difficult or very expensive to manufacture using traditional methods, such as CNC.