Rps 3d printing
Stratasys Acquires RPS, Provider of Best-in-class Stereolithography 3D Printers :: Stratasys Ltd. (SSYS)
Addition of RPS’ Neo line of industrial stereolithography systems gives Stratasys a full suite of polymer 3D printing solutions across the product life cycle
EDEN PRAIRIE, Minn. & REHOVOT, Israel--(BUSINESS WIRE)-- Stratasys Ltd. (NASDAQ: SSYS), a leader in polymer 3D printing solutions, today announced it has acquired UK-based RP Support Ltd. (RPS), a provider of industrial stereolithography 3D printers and solutions. RPS’ complementary technology further expands Stratasys’ polymer suite of solutions across the product life cycle, from concept modeling to manufacturing. Stratasys will leverage its industry-leading go-to-market infrastructure to offer RPS’ Neo® line of systems to the global market with an expanded set of applications. Stratasys expects the acquisition to be slightly accretive to revenue and non-GAAP per-share earnings by the end of 2021.
This press release features multimedia. View the full release here: https://www.businesswire.com/news/home/20210218005493/en/
Neo 3D printers from RPS can produce large parts in a small footprint using a wide range of materials providing properties such as chemical resistance, heat tolerance, flexibility, durability, and optical clarity. (Photo: Business Wire)
RPS’ Neo line of 3D printers feature dynamic laser beam technology that enables build accuracy, feature detail, and low variability across the full extent of a large build platform. As an open resin system, the Neo products provide customers materials with a wide range of properties such as chemical resistance, heat tolerance, flexibility, durability, and optical clarity. Its products can produce large parts up to 800 x 800 x 600 mm, providing a significant build area in a small footprint.
In addition, all Neo systems are Industry 4.0-ready, with Titanium™ control software that includes a camera, network connectivity, support remote diagnostics, and mid-build parameter customization. The printers can automatically email progress reports on jobs. Stratasys plans to integrate its GrabCAD Print workflow software into future versions of the product.
“As businesses accelerate their adoption of additive manufacturing, our goal is providing our global customers with the world’s best and most complete polymer 3D printing portfolio,” said Stratasys CEO Yoav Zeif. “We believe the Neo products are superior relative to other solutions currently available in the market due to an open choice in resins, low service requirements, and reliable and accurate builds with simple day-to-day operation. With access to our strong global channels and our innovative GrabCAD software, we will bring RPS’ innovative products to many more manufacturing organizations.”
“We developed the Neo line to raise the industry standard for the next generation of large-frame industrial stereolithography 3D printers,” said RPS Director David Storey. “I’m looking forward to continuing to develop this best-in-class technology with the Stratasys team as we bring our products to a broadened global audience. ”
Williams Racing, a British Formula 1 racing team, recently acquired multiple Neo 800 3D printers. “The team’s RPS Neo 800 machines ran unmanned over the Christmas break, delivering a huge volume of high-quality parts to our aero test program, a truly astounding achievement,” said Williams Racing Operations Director James Colgate. “I wanted to let you know how impressed we have been with our new Neo 3D printers.”
Industrial stereolithography systems are well-established in the 3D printing industry for applications such as tooling, investment casting patterns, anatomical modeling, orthodontic clear aligner molds and large design parts. They provide quality surface finish, large build sizes, a fast time to print, and an affordable cost per part. The global addressable sector for industrial stereolithography systems is estimated at approximately $150 million and is expected to continue growing at a rate of approximately 10% per year.1
Stratasys is leading the global shift to additive manufacturing with innovative 3D printing solutions for industries such as aerospace, automotive, consumer products and healthcare. Through smart and connected 3D printers, polymer materials, a software ecosystem, and parts on demand, Stratasys solutions deliver competitive advantages at every stage in the product value chain. The world’s leading organizations turn to Stratasys to transform product design, bring agility to manufacturing and supply chains, and improve patient care.
1 Estimated market size and annual growth rate based on company and third-party analyst estimates.
To learn more about Stratasys, visit www.stratasys.com, the Stratasys blog, Twitter, LinkedIn, or Facebook. Stratasys reserves the right to utilize any of the foregoing social media platforms, including the company’s websites, to share material, non-public information pursuant to the SEC’s Regulation FD. To the extent necessary and mandated by applicable law, Stratasys will also include such information in its public disclosure filings.
Stratasys is a registered trademark of Stratasys Ltd. and/or its affiliates. Neo is a trademark of RPS Ltd. All other trademarks are the property of their respective owners, and Stratasys assumes no responsibility with regard to the selection, performance, or use of these non-Stratasys products.
Cautionary Statement Regarding Forward-Looking Statements
The information contained in this press release may include “forward-looking statements” within the meaning of the Private Securities Litigation Reform Act of 1995, Section 27A of the Securities Act of 1933, and Section 21E of the Securities Exchange Act of 1934. Forward-looking statements are often characterized by the use of forward-looking terminology such as “may,” “will,” “expect,” “anticipate,” “estimate,” “continue,” “believe,” “should,” “intend,” “project” or other similar words, but may be identified in other ways as well. These forward-looking statements may include, but are not limited to, statements relating to the anticipated completion of the acquisition of RPS by Stratasys, Stratasys’ objectives, plans and strategies with respect to RPS following its acquisition, statements that contain projections of results of operations or of financial condition with respect to RPS and Stratasys after the acquisition, and all statements (other than statements of historical fact) that address activities, events or developments that Stratasys intends, expects, projects, believes or anticipates will or may occur in the future. Forward-looking statements are not guarantees of future performance and are subject to risks and uncertainties. Stratasys has based these forward-looking statements on assumptions and assessments made by its management and, in certain cases, by RPS’ management in light of their experience and their perception of historical trends, current conditions, expected future developments and other factors they believe to be appropriate. Important factors that could cause actual results, developments and business decisions to differ materially from those anticipated in these forward-looking statements include, among other things: any potential obstacles to closing the acquisition of RPS; the degree of success of Stratasys in efficiently and successfully integrating the operations of RPS into Stratasys after the acquisition; the general economic environment and the economic environment for 3D printing and Stratasys’ customers in particular; the impact of competition and new technologies; general market, political and economic conditions in the countries in which Stratasys operates, particularly in respect of the ongoing COVID-19 pandemic; government regulations and approvals; changes in customers’ budgeting priorities; litigation and regulatory proceedings; and those factors referred to under “Risk Factors”, “Information on the Company”, “Operating and Financial Review and Prospects”, and generally in Stratasys’ annual report on Form 20-F for the year ended December 31, 2019 filed with the U.
S. Securities and Exchange Commission, or SEC, on February 26, 2020, and in other reports that Stratasys furnishes to or files with the SEC from time to time, including, most recently, the report of foreign private issuer on Form 6-K reporting Stratasys’ results for the quarter and nine months ended September 30, 2020, furnished to the SEC on November 12, 2020. Readers are urged to carefully review and consider the various disclosures made in Stratasys’ SEC reports, which are designed to advise interested parties of the risks and factors that may affect its business, financial condition, results of operations and prospects. Any forward-looking statements in this press release are made as of the date hereof, and Stratasys undertakes no obligation to publicly update or revise any forward-looking statements, whether as a result of new information, future events or otherwise, except as required by law.
View source version on businesswire.com: https://www.businesswire.com/news/home/20210218005493/en/
Stratasys PR Corporate & North America
aaron. [email protected]
+1 612-716-9228
Investor Relations
Yonah Lloyd
[email protected]
+972-54-4382464
PR Europe, Middle East, and Africa
Jonathan Wake / Miguel Afonso, Incus Media
[email protected]
+44 1737 215200
PR Asia Pacific and Japan
Alice Chiu
[email protected]
+852 9189 7273
PR Brazil, Central America and South America
[email protected]
+55 (11) 2626-9229
Source: Stratasys Ltd.
Released February 18, 2021
Stratasys acquires RPS, inhouse SLA 3D printing system to be phased out
0Shares
Following the acquisition of DLP system manufacturer Origin back in December, leading 3D printer OEM Stratasys has now acquired UK-based RPS, a provider of industrial-grade SLA 3D printers.
Stratasys did not disclose the purchase price of RPS. The buyout gives Stratasys access to RPS’ entire line of Neo SLA systems, bolstering the company’s extensive technology offering which also includes FDM and Polyjet 3D printers. Stratasys expects the move to be accretive to both revenue and non-GAAP per-share earnings by Q1 2022.
“As businesses accelerate their embrace and adoption of additive manufacturing, our goal is providing our global customers with the world’s best and most complete polymer 3D printing portfolio,” stated Stratasys CEO Yoav Zeif. “We believe the Neo products are superior relative to other solutions currently available in the market due to an open choice in resins, low service requirements, and reliable and accurate builds with simple day-to-day operation.”
The Neo SLA 3D printer lineup. Photo via RPS.Carving into a $150M market
According to Stratasys, the global market for industrial SLA 3D printing sits at approximately $150M, and is expected to continue growing at a rate of 10% YOY. With only a few major players in the space, RPS has already made a name for itself with its Neo line.
The open resin systems are defined by their large-format build volumes, with the flagship Neo800 providing up to 800 x 800 x 600mm. All Neo 3D printers also feature the company’s Titanium control software, in-built cameras, network connectivity, and mid-build print parameter customization functionality.
With access to RPS’ well-established set of customers, including British Formula 1 racing team Williams Racing, Stratasys will strengthen its position in markets such as automotive and polymer tooling. The dental sector, in particular, is expected to provide an abundance of opportunities with resin-based applications such as orthodontic clear aligner molds and anatomical models. Zeif has even stated plans to integrate the company’s cloud-based GrabCAD Print software into future RPS 3D printers.
David Storey, Director of RPS, adds, “We developed the Neo line to raise the industry standard for the next generation of large-frame industrial stereolithography 3D printers. I’m looking forward to continuing to develop this best-in-class technology with the Stratasys team as we bring our products to a broadened global audience. ”
What does this acquisition mean for the V650 Flex?
Back in 2019, Stratasys unveiled its first commercial venture into SLA 3D printing, the large-format SLA 3D printer called the V650 Flex. Naturally, the acquisition has raised concerns over the future development of the printer, with RPS’ technology seemingly making it redundant.
When asked about the future of the V650 Flex, Stratasys told 3D Printing Industry: “We acquired RPS and the Neo product line to be our best-in-class industrial stereolithography solution that we will take to market globally. The Neo products by RPS will eventually replace the V650 as we expand our ability to address the demand we see in the market.”
Stratasys will continue to sell, service, and support the machine for at least seven more years. Stratasys will also endeavour to provide its customers with an easy and cost-effective transition to a Neo 3D printer when the time comes.
The Stratasys news is the latest in a long line of acquisition stories in the 3D printing industry. Just last month, metal 3D printer manufacturer Desktop Metal signed a $300M definitive agreement to acquire DLP system OEM EnvisionTEC. The cash-plus-stock deal, which completed yesterday, means EnvisionTEC has become a wholly-owned subsidiary of the publicly-listed Desktop Metal, and represents Desktop’s first move into the DLP market.
The acquisition has also enabled Desktop metal to absorb EnvisionTEC’s entire distributor network, taking the firm from just 80 partners to over 200 partners. EnvisionTEC’s customer base of 1,000+ orthodontic users is set to provide the company with a ready-made foothold in the ever-growing dental market.
Elsewhere, on-demand digital manufacturing bureau Protolabs also recently acquired online manufacturing platform 3D Hubs for a total of $280M. The move is set to create what the companies claim to be “the world’s most comprehensive” digital manufacturing offer for custom parts, as Protolabs will be given access to 3D Hubs’ global network of 240 manufacturing partners.
Subscribe to the 3D Printing Industry newsletter for the latest news in additive manufacturing. You can also stay connected by following us on Twitter and liking us on Facebook.
Looking for a career in additive manufacturing? Visit 3D Printing Jobs for a selection of roles in the industry.
Featured image shows a resin part being cured in a Neo UV800 post-processing station. Photo via RPS.
Tags David Storey RPS Stratasys Yoav Zeif
Kubi Sertoglu
Kubi Sertoglu holds a degree in Mechanical Engineering, combining an affinity for writing with a technical background to deliver the latest news and reviews in additive manufacturing.
3D printing in plastics, basic parameters
Plastics such as ABS and PLA have long been and will continue to be the most popular materials for 3D printing for a long time. The main reason is their affordability in conjunction with relatively high strength characteristics compared to other materials. In this article, we will not delve into the reasons for the popularity of the plastics described above, fully describe their characteristics, or delve into the features of 3D printing technology. Here we want to highlight the influence of print settings/parameters and the position of the part on the printing platform, when printing with FDM (FFF) technology, on the final strength of the product.
You can learn about how a 3D printer works here, about 3D printing technologies (including FFF, FDM) and how they differ here.
The strength characteristics of a 3D model can be affected by 3 main factors: layer thickness, filling and orientation of the model relative to the printing platform.
Layer Thickness
Layer Thickness is an adjustable parameter that determines how much vertically (Z-axis) the furnace head moves when moving to the next 3d print layer. There are 4 standard sizes: 0.1, 0.15, 0.2 and 0. 3 mm. There are smaller values, but, frankly, with a standard 0.4 mm nozzle, they make no sense (there will be no noticeable difference in quality). There are larger sizes, but they require a larger diameter nozzle. The typical value for this parameter with a typical 0.4 mm nozzle is 0.2 mm (200 microns).
First of all, it is worth mentioning that the layer thickness directly affects the surface quality (this is especially noticeable on surfaces slightly deviated from the horizontal or vertical), the lower the layer height, the higher the surface quality. This of course will depend on the type of printer, speed settings, etc., but we will not go into this. The higher the layer thickness, the correspondingly lower surface quality, while a simple transition from 0.2 to 0.3 mm will be noticeable.
Next, it is worth mentioning that the higher the layer height, the faster the printing takes place and, accordingly, it costs less. So 0.1 from 0.2 differs in speed by 2 times and in cost by 1. 5-1.7 times.
And finally - strength. Without going into technical justifications, let's just say that the greater the thickness of the layer, the greater the overall strength of the product.
Infill
Infill in 3D printing with plastic is a configurable parameter that controls the amount of material and voids inside the outline of the model.
The outline of the model (default 1.2 mm) is the wall separating the outer space from the interior of the model. Since the printable models have a closed volume, when the print is finished, the interior space is completely hidden.
By default, the parameter is set to 12.5% (12.5% - material, 87.5% - void), creating the required minimum strength. The higher the infill, the greater the weight and printing time of the model, and, accordingly, the cost.
For printing on plastics, you can choose any infill from 10 to 100%. It is better not to choose more than 90% to keep the minimum headroom for depreciation. Many tests have proven that 90% filling is stronger than 100%. The presence of free space inside adds additional strength under dynamic loads and object operation in changing conditions (for example, cooling-heating), due to the ability of the material to absorb into empty space. Moreover, 100% filling has a negative effect on the quality of the surface: small excesses appear on it plastic.
The relationship between filling and strength is simple: the higher the filling, the higher the strength. It is also worth remembering: the higher the filling, the greater the cost.
Location of the part on the printing platform
The location of the part on the working platform is controlled by the 3D printer operator and can significantly affect both the strength and the quality of the surface of certain areas. In some cases, this parameter is unregulated, since the very shape of the model dictates the only correct location. For example, a thin plane with a slight relief on one side (a plate with letters) should not lie on a plane (and not stand on an edge) so that the letters are directed upwards.
One could probably write a separate article about the location of the part, since the quality of the surface from different sides will largely depend on the shape of the model and the presence / absence of support. To do this, you need to understand the principle of operation of the FDM (FFF) technology, you can find it here.
Effect of location on strength. For example, let's take a 10/10/1 cm parallelepiped. When printing "lying down" (the 10/10 cm plane is placed on the platform), the layers are located along the main plane. When printing "on edge" (plane 10/1 cm), the layers are arranged across the main plane. The strength of the model across the main plane will differ up to 6 times. (layers along the plane, the model is stronger).
Accordingly, when 3D printing, it is necessary to take into account which parts of the product should have greater strength and place the model accordingly. It must also be remembered that when printing one model with the same settings, the time and weight of the print may differ (due to supporting structures), and sometimes, all significantly.
--
In conclusion, I would like to note that changing all three parameters can have a very strong influence on the strength of the model and on the quality of its surface (and of course on the cost / prime cost). If, for example, you do not need the entire model of special accuracy and strength, you can divide it into parts, saving a lot and getting exactly the characteristics that you need in specific parts.
Don't want to understand? Leave it to the professionals: we will be happy to help you find the best solution for your task.
High Temperature 3D Printing - To the Masses But, despite this, most often users turn to polylactide (PLA) threads. This is not only the cheapest of materials, but also the easiest to work with. Its extrusion can already be carried out at a temperature of 180 °C, and good results can be obtained even without preheating the table. The disadvantage of PLA-printed objects is that they are relatively brittle and do not tolerate high temperatures well.
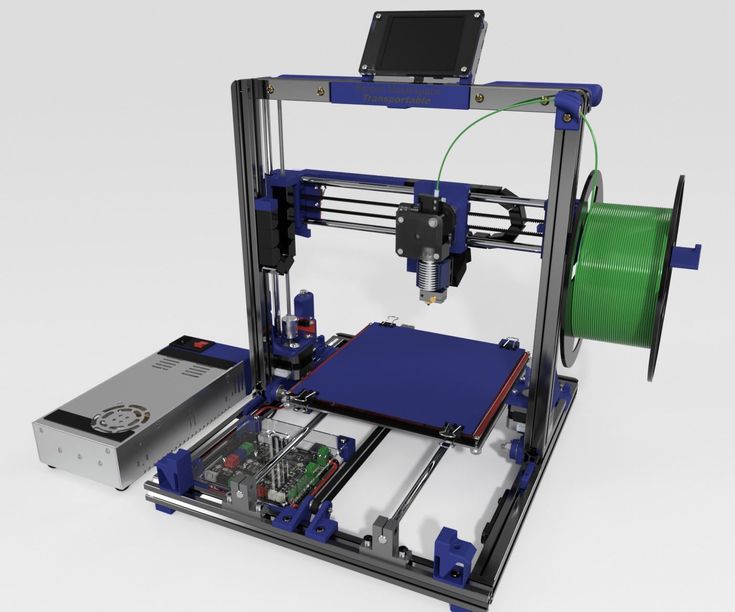
Polyethylene terephthalate (PETG) is usually the next step. It is not much harder to work with compared to PLA, while it is more reliable and can withstand higher temperatures. In general, it is better suited for creating mechanically loaded parts. But if you need to make even stronger and more heat resistant parts, you can switch to acrylonitrile butadiene styrene (ABS), polycarbonate (PC) or nylon. And this is where the problems begin. These materials are extruded at temperatures over 250°C and closed chambers are recommended for best results. These printers are at the top of the budget range that hobbyists are willing to work with.
Industrial 3D printers like this one, the Apium P220, start at around $30,000. (PAEK, PEEK, PEKK). Components made from these plastics are suitable for aerospace applications as they can replace metal while remaining much lighter.
Such plastics need to be extruded at temperatures of around 400°C, and a sealed chamber is required for operation, the temperature in which constantly exceeds 100°C. The cheapest printers of this kind cost tens of thousands of dollars, and some models even cost six figures.
Naturally, not so long ago, the same could be said about all 3D printers. Once used only by well-equipped research labs, these machines now sit on the workbenches of hackers and hobbyists the world over. It is difficult to predict whether the same price-cutting race will start for high-temperature 3D printers, but the first steps to democratize the technology have already been made.
Engineering difficulties
Simply put, a machine that supports these so-called. "engineering plastics", you need to be a hybrid of a 3D printer and a stove. This, of course, is the main problem. The printer itself - of the type and quality we are accustomed to seeing on our desks - will not survive in such conditions. In order for a consumer printer to produce PEI and PEEK plastic parts, it needs to be seriously redesigned. This is exactly what NASA did with the LulzBot TAZ 4 in 2016.
LulzBot TAZ 4 redesigned to support high temperature printing
The first step was to design an insulated housing to fit the TAZ 4 and install a set of 35W infrared lamps for heating. Under such conditions, the printer's electronics, of course, would overheat - so it had to be taken outside.
Stepper motors would also overheat. But instead of taking them out, the team at the Langley Research Center decided to build cooling shrouds on each of the motors through which the compressed air must circulate.
Like many desktop 3D printers, the TAZ 4 uses several printed components. Since they are ABS, they would quickly break down in a chamber designed to support PEEK. They were printed from PC, but even this material was not resistant enough for permanent use. In classic RepRap tradition, the team printed the last, third set of components on their most modified printer, in PEI plastic, commercially named Ultem.
Surprisingly, the team had no trouble changing the printer's nozzle to one that could extrude plastic at 400°C. The popular E3D-v6 extruder costs less than $100 and has been shown to be able to maintain this temperature. True, the team had to replace the thermistor with a better one, as well as edit the Marlin firmware so that it allowed it to reach high temperatures. For conventional printers, too high a temperature should cause an emergency shutdown.
Printing results from Ultem 1010 plastic on a redesigned LulzBot TAZ 4.
In the end, the NASA report indicated that the LulzBot TAZ 4 redesign was a complete success. They noted that an attempt to print PEI with infrared lamps turned off ended in failure - delamination and distortion of the model, which was to be expected. They did not specify the cost of the conversion, but given that at that time the TAZ 4 cost $2200, the entire project could cost 10 times cheaper than similar commercial proposals.
Starting from zero
A NASA experiment has shown that an existing desktop 3D printer can be converted to print with high-temperature engineering plastics, and quite inexpensively. But hardly anyone believes that this approach is the ideal solution. There are too many repetitive operations involved here, and NASA engineers had to abandon some of the decisions made by the LulzBot developers. Still, the experiment provided a valuable baseline for other projects built from scratch.
In September 2020, a team from Michigan Technological University demonstrated the Cerberus, an open-source, high-temperature 3D printer capable of creating items from PEI and PEKK, that costs as little as $1,000 to build. Without trying to adapt existing designs, the team started development from scratch, aiming for high temperature printing. All electronics are housed separately from the sealed chamber, which uses a kilowatt heating element to quickly raise the temperature in the chamber to operating temperature.
All stepper motors are also outside the chamber. Because of this, the kinematics become more complex than in desktop 3D printers, but Cerberus no longer requires a special motor cooling system.
Building a Cerberus is quite affordable for the aspiring hobbyist. It has a simplified circuit, ready-made control electronics based on the Arduino Mega 2560 and RAMPS 1.4, and the same E3D-v6 extruder as the TAZ 4. In addition, the team posted clear and detailed instructions for assembling the printer - this is not in the NASA report. meet.
Expanding possibilities
Whether it's NASA's redesign of the TAZ 4, or the new Cerberus-type circuits, it's clear that the technical capabilities of PEI and PEEK printing in the home workshop are already available for those who really need them. So far, it's not as easy as buying a $200 3D printer on Amazon, but if there is demand, cheaper machines based on the same principles will appear on the market. The situation is not much different from the current wave of affordable laser cutters hitting the markets in the past few years.
Fans from all over the world print PPE
Is there a demand for such machines? A year ago, the answer might have been different from today. But in the fight against the coronavirus pandemic, there is a new demand for the rapid production of personal protective equipment (PPE) that no one could have foreseen.
print PPE that can be sterilized at high temperatures. The team believes that masks printed from PEKK can be reused rather than thrown away.
Components that can be printed and re-sterilized will obviously have other potential medical applications. A portable, low-cost machine capable of producing such components has the potential to save lives in places on the planet where supplies and equipment cannot be quickly accessed.
Critics of 3D printing have often said that the main disadvantage of these machines is that the reliability of the items they make rarely allows them to be used for anything other than rough prototyping.