Recycle pla 3d printer
How To Recycle 3D Printing Filament [Simple And Easy Guide]
Want to learn you can recycle your 3D printing filament and save a lot of money? This simple and easy guide shows you exactly how.
By Justin Evans
It’s often said that 3D printing is an expensive hobby to get into, but the majority of the long-term costs come from buying replacement filament. What if there was a way to decrease these costs and also decrease your environmental impact? Well, guess what? There is, and it’s easier than you might think.
Now, for the time being, there is a decent upfront cost. However, by recycling old filament, you’ll be able to reclaim any materials used in prints that didn’t come out just right. Think about how much filament you’ve wasted since you began. How much money could you have saved?
Table of ContentsShow
Equipment Needed
Before you can begin reclaiming old materials, you first need two pieces of equipment: a shredder and an extruder (this is different from the one on your 3D printer). Essentially, you feed your old print into the shredder, which, as you might expect, shreds it. Then, once you have your shards, these are fed into the extruder, which heats and shapes them into something you can actually use.
So what kind of upfront costs can you expect? Well, a cheap plastic shredder costs around $250 and a basic extruder is around $300. If you’re feeling adventurous, you can even make your own. These DIY solutions cost less but are fairly labor-intensive to create. So, what should you keep in mind before recycling filament?
Rules For Recycling Filament
There are a few golden rules you must follow in order to produce usable filament. First and foremost, make sure you only shred one type of material at a time. Each filament type has diverse characteristics like melting temperature and viscosity. In fact, even combining different brands of the same material can have unexpected results.
By using only one type of filament, you lower the chance of creating unstable materials that fall apart when printing. That’s not all, though: you should also be aware that the recycled filament might have a different diameter. Really, this is all up to which type of extruder you buy.
If you find your new materials to be slightly larger or smaller, you’ll likely need to swap out your printer’s extruder for one that will accept the new filament. It’s crucial that you test each batch for quality though, as outlined in the graphic below.
Finally, in order to prolong the life of your shredder, don’t just throw large objects into it. Try breaking them down first – a hammer usually does the work perfectly. If you find the plastic chunks are still too large, there’s no shame in putting them through a second time.
Conclusion
While it might seem like a lot of work, recycling filament is a far more economical way to print in the long term. This is the main advantage 3D printing has over other kinds of manufacturing; if you mess up during carpentry work, your wood is likely useless. Not so with the filament.
By following our instructions, you can achieve the impossible – creating high-quality models with almost zero waste and minimal impact on the environment. If that’s not a sign that this technology is the way forward, we don’t know what is.
3D Printer Materials Guide
♻️ How can I recycle my 3D printing plastic?
If you’ve been in 3D printing for a while, you’ve certainly gone through all the phases of recycling 3D printing plastic. Over the years, a lot of new projects have appeared that promised to give us the ability to recycle the plastic from our failed prints, media, rafts or purge blocks but, to this day, which of these projects are still standing?
If you want to know the alternatives available in 2020 to recycle the 3D printed plastic, stick around, we’re getting started.
📖 What do you want to read?
What alternatives are there?
There are numerous ways in which we can recycle this plastic, so we are going to explain the main ones and some examples of each one of them so you can delve into the projects that catch your eye.
The two main alternatives we have are: to recycle the plastic from our prints to turn it back into usable material or to use it to make plastic objects using other technologies such as injection molding.
Converting 3D print remainders into new print material
If you want to turn the material left over from your 3D prints back into material you can print on, there are currently three ways to do it: create your own filament, use a special extruder that allows you to print directly using recycled plastic pieces, or buy filament rolls made from recycled material.
Create your own filament
To create your own filament using the remains of other 3D prints there are several machine projects known as filament extruders. Each of these machines works slightly differently, but basically they feed on crushed 3D print debris and melt it down, extruding new filament through a 1.75mm diameter nozzle.
Filastruder
Filastruder is a kit that you can buy for $299 in its most basic version. This product has been releasing new versions and improving for several years, so it is a quite refined equipment and one that can be expected not to give us many problems. If we want to coil this plastic we will also have to buy its filawinder accessory for 169 extra dollars.
Felfil Evo
Felfil Evo is a much more expensive but also more premium and open source kit. It is available in 3 different kits, a fully assembled and functional one for 719€, a kit for you to assemble for 599€, and a “barebone” kit that only contains the mechanical components but does not include chassis or electronics for 299€. This last option, in addition to the fact that it is open source, is an excellent choice for the more professional makers looking to create their own filament extruder adapted to the needs of their workshop.
They also have a premium pack with the assembled version that comes with a plastic coiling accessory for 1199€.
Filabot
Filabot is a brand with a line of products designed to create a complete filament coiling and manufacturing system. These equipments, even in their most basic version, are much more expensive than the previous ones, since they are thought for professionals and not for makers. All equipment comes pre-assembled and tested to ensure a quick and smooth start-up without unexpected complications
There are two product ranges, the Filabot ex2 and the Filabot ex6. The first is the simplest and most affordable, starting from $2699 for the extruder and $4559 for the complete kit including the coiler.
The second one is even more professional and starts at 9899 dollars for the extruder or 10899 dollars for the complete combo.
Buy recycled material
If this sounds a bit complicated to you (which it is) but you still want to contribute to the recycling of plastic for 3D printing, then you can buy filament that has been professionally manufactured using recycled material.
Some examples of filaments you can buy made from recycled material are 3RPLAfil or Sakata RE-850.
Directly extrude recycled material
An intermediate solution is to use special extruders that you can attach to your 3D printer to print directly using recycled print pieces, without having to go through extruding a new filament. In this field, Spain is the world leader, as a Spanish extruder is the best and most popular extruder of pellets and recycled plastic: the Mahor-xyz Pellet extruder.
This is actually an extruder-melter kit that is placed in our 3D printer replacing the traditional extruder and hotend. It is one of the best solutions, if not the best, as it allows direct extrusion of virtually any type of material from shredded failed prints or pellets that we buy made from recycled material. The list of materials includes: PLA, ABS, TPU, TPE, EVA, PC… In addition, we can incorporate additives such as carbon fiber, glass fiber or kevlar to improve the properties of the material.
In a future article we will talk at length about this project, as it is a true masterpiece of engineering that will delight the most professional makers in Bitfab.
Making plastic objects
An alternative option to give a second life to the leftovers of our 3D prints is to manufacture objects using techniques such as mold injection. In this respect there is an initiative that stands out: Precious Plastic.
Precious Plastic manufactures everyday objects such as chairs, benches, carabiners, coasters, socket covers or many other things from plastic left over from 3D printing processes.
In addition to these objects, they also sell kits with machinery so that you can recycle them yourself.
If you want to give a second life to the plastic you print but don’t want to use it to print more things, this is the option that suits you best.
Contact Bitfab
Recycling plastic from 3D printing is a very powerful application and Bitfab can also help you with it.
If you need advice on how to recycle your surplus material or you are thinking of starting a project using recycled plastic, do not hesitate to contact us.
3D printing from waste as an alternative to conventional plastic
3D printing from waste
3D technologies and 3D printing do not stand still, but are actively developing and improving. Every company that designs and manufactures 3D printers strives to cover as many areas of 3D technology and 3D printing as possible. The variety of 3D printers and consumables for 3D printing is increasing every day. In addition to really useful products, 3D printers create a large number of unnecessary products. And since most products are printed from plastic or other material that is not recycled, this raises concerns for the environment. Among the developers of new materials for 3D printing there are those who seek to find an alternative to the use of conventional plastic.
Italian designer Marina Kessolini has developed a material called AgriDust. AgriDust is food waste material.
3D printed from waste
The designer mixed together some of the most discarded food waste - coffee grounds, bean pods, peanut shells, tomato, orange and lemon peels. Then, adding a binder food product, which is made from potato starch, I connected everything together using 3D printing.
3D printing from waste
The new material is environmentally friendly and designed for printing non-edible products. It could be a much needed and safe replacement for the conventional plastic used in most 3D printers today.
3D printing from waste
AgriDust can fully replace conventional plastic in printing products with a short lifespan, such as packaging or plant pots, for printing industrial prototypes and objects that serve only for the initial stage of research. After the printed product has served its time or simply becomes unnecessary, it can go to compost.
3D printing from waste
in some areas, this is simply not possible. The new AgriDust threads will make it possible to significantly reduce the amount of conventional plastic used and reduce the cost of its disposal or disposal. The use of AgriDust thread is not the only possible alternative to conventional plastic. 3Dom has developed 2 materials that can become an alternative to conventional plastic. 3Dom has developed the c2renew biocomposite material from recycled coffee grounds.
3D Printing from Waste
c2renew is completely different from other materials, thanks to its rich brown tint and natural grain, it is perfect for creating various tools, figures or decorative details.
The new thread is a mixture of coffee and polylactide. It comes in two sizes: 1.75mm and 2.85mm and can be used in any 3D printer that prints PLA plastic. After creating eco-friendly 3D printing filament from recycled coffee grounds, the company's developers turned to beer waste.
The company's new slogan: "If good people drink beer, why shouldn't they use it for construction?" The new composite threads are made from waste products from the brewing process.
The new material, dubbed "Buzzed", is a high quality material that can also be used on most PLA 3D printers.
3Dom is not going to stop there and plans to release more bio-filaments made from waste in the future.
3D Printing from Waste
Back to Home
4 Ways to Recycle Your Failed 3D Prints
You have purchased one of the best 3D printers around. You've learned how to do this with our beginner's guide to 3D printing. You may even have designed your own 3D models with OpenSCAD. You are no longer a 3D printing beginner.
But no matter how good you are at 3D printing, you will end up with unwanted or unsuccessful prints. Maybe you have experimented with a new thread. Perhaps you were still calibrating your machine, or an accidental push messed up the last batch. Whatever the reason, bad prints happen.
Today I'm going to show you some of the coolest things you can do with all those broken parts.
1. Create something cool
One of the easiest ways to recycle prints is to combine two or more prints into something new and unique. Consider combining something like a bust of Yoda or a low poly Darth Vader into a new unique figure. The best part is that you only need simple materials like glue or tape.
This project depends entirely on what you have. If you're only designing and printing prototype parts, this can be tricky, but if you're printing the best 3D prints for desktop fantasy RPGs then you already have everything you need!
If you don't have the parts you need but still want to make something cool, check out this video on the Make Anything YouTube channel.
As shown, you can smash, melt and turn a few bad prints into a new and unique item. You can even achieve a multi-colored design by combining prints of different colors - or stick to one solid color - the choice is yours!
2. DIY Thread Recycling Machine
Did you know that it is possible to recycle 100 percent of your failed prints? I'm not talking about your local recycling facilities, I'm talking about recycling your parts into brand new filament, ready to be printed again.
Using a machine that looks more like a manufacturing process than a DIY project, this "weak" recycling workflow is called the Filament Extruder.
Thread extrusion almost always consists of three steps:
- Break up old parts
- Melt and extrude thread
- Glow coil for new coil
First, each bad print is broken into very small pieces. This makes melting easier. Once melted, the liquid plastic is passed through a small hole and then cooled before being wound onto a plastic spool. This is a very cool process that is actually a form of injection molding.
As YouTuber Hugh Lyman shows in this video, this is a tough project, but don't let that stop you from saving the planet!
Equipment such as Filabot is available for purchase but very expensive. If you want to learn more about this project, check out the many extruders you can print yourself! Popular models include Lyman/Mulier or Yalfe.
3.
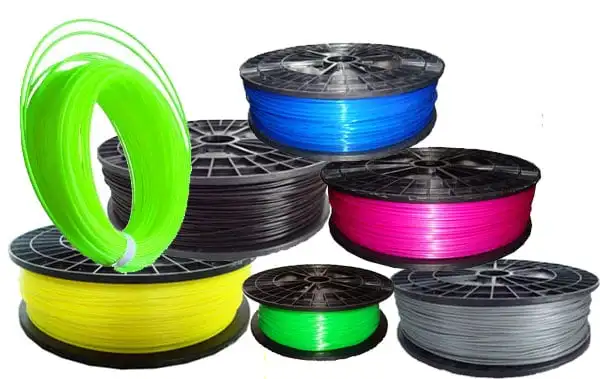
This processing method only applies to acrylonitrile butadiene styrene (ABS). Since ABS is oil based, it can be melted with acidic liquids. By combining a small piece of ABS with acetone, three different liquids can be made, all with slightly different uses.
ABS juice: is used to help parts stick to the bed.
ABS Adhesive: Used to glue or weld two pieces together.
ABS Slurry: is used to fill any small holes between parts - the filler of the 3D printing world.
By sacrificing some bad prints, you can improve the quality of the good ones!
Hoffman Engineering's YouTube channel shows us how to do it:
Be careful! Even when combined with ABS, acetone is still a solvent that can injure you if used incorrectly. Although acetone is very mild, it can still cause skin irritation. Always follow the manufacturer's recommendations.
4.
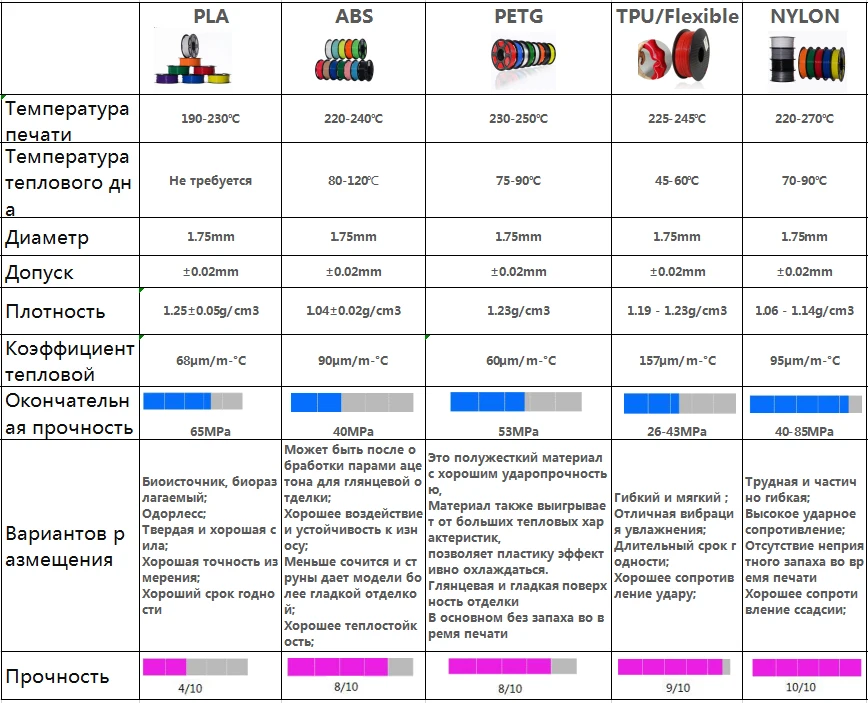
Our ultimate recycling technology is exactly what you need: recycling!
In theory, most 3D printed parts can be recycled, but you will struggle to do so. It also depends a lot on what material you are printing on. Once again, ABS is the big offender here. ABS can produce some very nasty chemicals and fumes, which is why it almost always ends up in a landfill.
If you're not interested in recycling, then this short video from YouTuber Amanda Anez explains why it's so beneficial:
The environmentally friendly PLA material is often advertised as biodegradable, but it has a catch! PLA can take hundreds of years to decompose if conditions are not ideal. While PLA does not release any harmful substances when it decomposes, many recycling service providers may refuse to accept it as it can be difficult to deal with other plastics.
One of the easiest solutions you can do is to compost it in a factory or at home. Composting simply speeds up the natural decomposition process.