Nema 23 3d printer
Nema23 best STL files for 3D printer・Cults
NEMA23 Hand Wheel
Free
Stepper Stand Nema 23
Free
Nema23 end cap housing
Free
Lead CNC Nema 23 Mount
Free
Stepper Cover for Nema23 Motor
Free
NEMA23 extruder with mounting slots
Free
NEMA 17 to 23 adapter
Free
Extruder-X universal -1.75/3mm, direct drive extruder, Nema 17/23
Free
NEMA23 Waterblock
€6.37
NEMA 23 Motor mount
Free
BK12 to NEMA23 Mount
€6. 37
Reinforced PrintNC Nema23 / Nema24 XY motor mount
Free
Smart Lock with Gears
Free
Anycubic Chiron Y Axis Nema 23 Upgrade
€6
WorkHorse Printer - Z-axis Nema 23 Bridge Mount-3030
Free
CNC belt drive plate (Nema 23 inversion for room gain)
Free
Openbuilds Mini Mill Nema23 Motor Mount Cover
Free
Nema 23, D-shaft to 9 mm "Flexible" Coupling
Free
nema 23 coupling
€1
Stepperonline NEMA23 Strain Relief
Free
Kajakens NEMA 23 stepper fan mount (not the round stepper version)
Free
MPCNC F-25mm Nema 23 Upgrade
Free
Stepper Motor Nema 17/23 Mount 2020/3030
Free
Nema 23 Motor Mount
Free
Pilot Printer
Free
Nema23 Stepper Motor Stand Off/ Mount
€1. 19
Convert Nema 23 to 17
Free
NEMA 23 cap for 16mm cable conduit / sleeving
Free
Nema 23 Rear Hole Cover
Free
xtrhdr a geared nema23 extruder for a cupcake
Free
Nema 23 Stepper Motor Lamp
Free
Stepper Motor JK57HS76-2804-14 Mock up model
Free
Do you really need a Nema 23? – gr33nonline
Preamble
Back on the topic of stepper motors again, folks!
Whilst looking a parts for a Kossel, a large Kossel (see Kossel 3D Printer), I came across these aluminium vertices for 2040 aluminium from RobotDigg, see 2040 or 3030 Alu Vertex for Kossel XXL or XXXL. On that product page they recommend using Nema 23, en lieu of Nema 17, stepper motors and, indeed, offer a vertex machined especially to take a Nema 23 stepper motor.
Now, Nema 17 stepper motors are pretty well covered in the RepRap forums, and there are three common favourites. However, the choice is not so clear for Nema 23 stepper motors. I decided to do some research on which Nema 23 stepper motors would be appropriate.
Links
Take a look at the RepRap Wiki page for Nema motors.
From Choosing stepper for a delta:
Using NEMA23 stepper motors for printers
For large machines, there are questions of the interest to use larger size steppers for movement or extruder, say Nema23 sized motors. However, Nema23 steppers are less optimised than Nema17 for micro-steps so there will be loss of precision. In addition, the rotating inertia is larger, so rapid change capacities may be reduced, driving to difficulties at corners. All steppers will have an increase of vibrations at medium step rates. This is called ‘mid-band resonance’. NEMA 23 steppers may be more prone to have this problem, at a lower frequency than NEMA 17 stepper motors.
So, it is preferable to use long NEMA 17 stepper motors than NEMA23. Electrically, larger motors will need more current, whatever their size.
From Collosal Delta:
Nema 17 is most likely more than adequate, depending on your speeds. The bigger challenge is going to be a bowden system that isn’t 6 ft long… Perhaps a counter-weighted bowden floating head.
From Running NEMA 23 motors, again after RobotDigg’s recommendation:
…have been advised (by RobotDigg who make the frame corners) to consider NEMA 23 (76mm). These are rated at 6.7V 2.8A
reply
2.8A is too high for the Duet. However, you can also get Nema 23 motors with 1.5A or 2A rated current, which would be a better match. You will need 24V or 30V power.
and
A larger machine doesn’t necessarily need larger motors, because the effector of a large printer need weigh no more than the effector of a smaller printer.
The belts will weigh more, but you can easily work out the additional torque you need to achieve the desired acceleration, given the additional mass of longer belts.
From NEMA23 steppers seem weak:
I’m using TeaCup firmware with RAMPS 1.4 electronics. It’s a custom design of 3D printer, with a larger print area. It’s essentially a Prusa Mendel iteration 2 in a wooden box frame instead of the triangular frame. The Z and X axis are powered by NEMA23 steppers with TB6560 stepper drivers instead of the NEMA17. Unfortunatly the NEMA23’s seems to be weaker then the NEMA17 and I’m not sure why.
The original RAMPS1.4 elektronics design has two steppers fed by the same stepper drive for the Z as. I changed this to two TB6560 stepper drivers receiving the same CLK, DIR en EN signals so that each NEMA23 has his own dedicated TB6560. The NEMA23’s have their own seperate power supply, an AC to DC convertor with an output of 24V and 10A, this feeds a total of three TB6560’s with one stepper motor each.
![]()
I’ve tried 3A and 2.2A, dont know if they get warm. I’ll test it.
The rest of the TB6560 settings is at stop current 50%, excitation mode 16, and decay setting 100%.
reply
The maximum current you should use on those motors in bipolar series mode is 2.1A. At that current they will get hot. I suggest you use 1.6A or 1.9A. The static voltage drop at 2.1A would be 3.15V, so your 24V supply should be entirely adequate. Are you certain you have them wired correctly, i.e. yellow linked to blue and orange linked to brown? What load are they driving?
From Duet3D – Choosing stepper motors
Nema 23 motors offer higher torque than Nema 17 motors. The Duet WiFi and Duet Ethernet can drive them if you choose them carefully, in particular in respect of rated current. Look for a rated current of around 2.8A. You should use 24V power.
and
- Size: Nema 17 is the most popular size used in 3D printers.
Nema 14 is an alternative in a highly-geared extruder. Use Nema 23 motors if you cannot get sufficient torque from long Nema 17 motors.
From RobotDigg – Reprap Stepper Motor:
Just as the reprap forum has been showed up, Nema14 and Nema17 Stepper are popular as Reprap Stepper Motor in small and medium sizes of 3d printers like Huxley, MendelMax. Nema23 is supplementary to Nema14 and Nema17 Stepper Motors.
We have some comments on the Nema23 stepper motor. Robotdigg do Not Nema23 Stepper is the best choice for Darwin or other reprap strong 3d printers if you use a 2A stepper driver like A4988 driver. At least 24V power supply for a Nema23 stepper and a strong stepper driver up to 3A or 4A are ideal. So if you use 12V and a stepper driver within 2A drive ability, a Nema17 long body stepper motor is recommend or a geared stepper motor is good. A Nema17 60mm stepper motor can have 0.65N.m holding torque. In the other side, a Nema17 60mm stepper motor is much cheaper than a Nema23 stepper or a geared nema17 stepper motor.![]()
For small quantity less than 20pcs, short body Nema17 Stepper Motor 34mm and 40mm long, RobotDigg recommend you source them in your local area. Or buy from our dealers, now we have dealer of 17HS3001-20B Nema17 40mm Stepper in Australia, Brazil, Spain and U.S. 12USD, 14USD is reasonable price from dealers we think, shipping cost, VAT and a piece of profit margin. We will list our dealers out as soon as possible here.
Recently we have some reports on Wiring Questions on our Reprap Stepper Motors. And we have a look on it and find that it is not individual. The questions is that on motor side the color of the lead wires are Red(A+), Yellow(B+), Grey(A-) and Green(B-) in turn. As usual, on the other side the stepper driver B-, B+, A+ and A- but the Mark on A4988 Driver can make you confused. See the following: From the lower 1B, 1A, 2A and 2B. The question is that 1B and 1A is one phase(one coil) and 2A and 2B is the other phase(one coil).
![]()
http://www.pololu.com/catalog/product/1182
A4988 Driver
To solve the wiring question using our stepper motor, you need to exchange the Yellow(the 2nd) and Grey(the 3rd) on the motor side or the other side of the lead wire(Plug to Stepper Driver).RobotDigg welcome your order of our NEMA17 60mm 0.65N.m Stepper Motor and Threaded Rod Nema17 Stepper Motor with strong Tr8*8 Leadscrew.
Back to Nema23, is using a bigger size stepper motor means more powerful your 3d printer will be?
The answer is absolutely NOT.
RobotDigg find that most of 3d printer makers are trying to buy a longer body stepper motor. But that’s only one side of the solution of higher torque output. The other side is the Stepper Driver. A4988 stepper driver is very popular in 3d printing industry, it’s a good driver which can drive up to 2A. But when you use it to drive a long body stepper motor Nema17 48mm or 60mm Stepper when you give it 12V power supply, you find that you still have the question of low torque output.How to figure it out? Increase the power supply. You may say you have a 12V power system, so increase the set Current, at least equal to the Rated Current of the stepper motor you have in your 3d printer system.
OK, we are a little far. Why a Nema23 Stepper is not that ideal for your 3d printer?
As we know, Nema23 is very popular in CNC machines. We also can see that a CNC machine usually has 24V power supply.
Set the current of the stepper driver the Rated Current of the stepper motor. A stepper motor with rated current 1.5A, if you give only 1A, the holding torque could be half or even lower, especially when increase the speed and heat generation after a long time run.
Is there a Nema23 stepper motor good for 3d printer and can be drived by A4988 stepper driver?
The answer is yes. RobotDigg are glad to show you a Nema23 stepper of this kind in the near future.
Instead of a Nema23, are there a Nema17 Stepper Motor can meet my need?
A Nema17 60mm with Rated Current 1.5A(within 2A, set your A4988 stepper driver at 1.2A or 1.5A won’t hurt the stepper driver. But if you set the stepper driver at 2A, it cann’t run long time, the stepper motor may pause.), a Holding Torque 65N.cm 92oz.in which is really with enough power for your 3d printers.
Other interesting reads
These do not mention which specific Nema 23 stepper motor is used:
- Bigger Delta Rostock ?
- 3D Printers – Big printers, Small printers, Wide printers, Tall printers
- 3DRmega – the BIG RepRap Delta printer
- Delta Bad Boy 3d printer
- Delta design reprap vs industrial
- Delta 3d Printer (mentions 200 oz•in torque)
- Scaling up 3d printer for larger items
- Тема 130: Delta robot nema 23 – totally unreadable, looks like it was translated by a robot
From Page ‘Choosing stepper for a delta’ created in RepRap Wiki, mentions resonance
PRZ,
Yes, you could even say “driver chip” and “driver board”.![]()
Good, I didn’t see the link.No apologies necessary, thank you for your work!
Note that I certainly do not want to complicate the article.
A bit of background on why I mentioned the three items above:
Not knowing better when I built my delta – I had all those issues. I used .9 degree motors and 17 tooth pulleys, and this seriously limited speed, first due to the 8-bit controller and DRV8825 drivers. When I upgraded to a 32 bit controller the motors hit mid-band resonance with what I considered to be reasonable travel speeds. So I agree that Nema 23’s are problematic – but also the combination of my choice in pulleys, controller, and drivers.I had serious mid band resonance issues for the main steppers until I used DSP drivers and tuned them. The arms on my machine can go to very low angles indeed (I’m well aware that this is not ideal) – the required speedup did cause headaches until it was properly accounted for. When the motors reach a certain speed they go no faster now due to the Smoothie config.
This does not affect normal printing, because the cars don’t need to go that fast normally. After increasing the pulleys to 30 teeth I still have 177 steps per mm, with .02 mm repeatability, and then could go faster yet. Although I do not recommend Nema 23, this setup is working fine now.
Mid-band resonance occurs fairly abruptly, and is not eliminated by DSP drivers, only reduced – and the motors run much quieter. Using the settings in the Smoothie config I do not have to worry about the speed/acceleration at all now when accessing any part of the bed, it won’t go into that speed danger zone.
I used these for all 4 motors on my delta, as the maximum print size is (x/y plane) is large, 430mm, and some of it’s parts were designed a bit heavier to allow me to swap out the effector for pick-n-place, laser, drill, etc. I have printed prototypes for someone nearly that large.
Really the motors see hardly any noticeable torque under normal operation compared to what they are rated, it’s when they over-speed into low-torque/resonance zone that is the problem – when fully resonant – boom – they have no torque at all.
This is a much steeper drop in torque than the RPM/torque curve.
One of those Nema 23 works great for my direct drive 3mm extruder, as their rated output is 11.2 kg/cm. I am running that one at 2A, 26v with a Mk-7 gear bored out to fit, directly from the Smoothie. I don’t measure the output by print speed, I use mm3/second extruded – it will comfortably output 12mm3/second for normal layers, 18 when bridging (ABS).
I wish I’d known then what I know now about what that combination of motors, controller, pulleys, and drivers would do. Would have saved a lot of time and money.
So hopefully you understand a bit where I was coming from in my fuzzy headed post earlier.
Building a Large Kossel Delta Printer – pt. 1: Parts and Planning (Terence)
Motor-wise we chose relatively powerful NEMA 23 stepper motors with 0.9°/step instead of the more commonly used NEMA 17. The 0.9°/step will give us better resolution than the more common 1.
8°/step. We’ll use standard GT2 belts and pulleys which we’ve used in several other machines earlier.
Nema 23 Stepper motor models
From Running NEMA 23 motors
I have just started commissioning my 1600mm tall 600 diameter bed Delta with 0.9 degree NEMA23 motors.
Currently running at 24v and 1.5A set current with these 23HM22-2804S, [www.omc-stepperonline.com]
From Collosal Delta
- Nema 23 motion steppers (Kysan 57BYGh410 rated @ 2A)
From Nema 23 Stepper motor, the Nanotech STS709S1208-B can do 400 0.9° steps (so half stepping not required), but expensive (cost?)
ST5709S1208-B
This was the original standard RepRap stepper motor. It has 400 steps to one revolution (0.9° per step). It actually has 4 coils (which means it can be wired as both a bipolar and unipolar), but we join up the wires to turn it into a bipolar motor.
- Keling KL23H51-24-08B can do 200 1.
8° steps, cheaper
- Motion Control Products FL57STH51-2808A and FL57STH51-3008B, steps unknown
- Lin Engineering 5718X-05S can do 200 1.8° steps
From NEMA23 steppers seem weak
- SY57STH56-3008B Nema 23 Stepper motor
Problems with Nema 23
Resonance
From Page ‘Choosing stepper for a delta’ created in RepRap Wiki, mentions resonance
PRZ,
Yes, you could even say “driver chip” and “driver board”.
Good, I didn’t see the link.No apologies necessary, thank you for your work!
Note that I certainly do not want to complicate the article.
A bit of background on why I mentioned the three items above:
Not knowing better when I built my delta – I had all those issues. I used .9 degree motors and 17 tooth pulleys, and this seriously limited speed, first due to the 8-bit controller and DRV8825 drivers. When I upgraded to a 32 bit controller the motors hit mid-band resonance with what I considered to be reasonable travel speeds.So I agree that Nema 23’s are problematic – but also the combination of my choice in pulleys, controller, and drivers.
I had serious mid band resonance issues for the main steppers until I used DSP drivers and tuned them. The arms on my machine can go to very low angles indeed (I’m well aware that this is not ideal) – the required speedup did cause headaches until it was properly accounted for. When the motors reach a certain speed they go no faster now due to the Smoothie config. This does not affect normal printing, because the cars don’t need to go that fast normally. After increasing the pulleys to 30 teeth I still have 177 steps per mm, with .02 mm repeatability, and then could go faster yet. Although I do not recommend Nema 23, this setup is working fine now.
Mid-band resonance occurs fairly abruptly, and is not eliminated by DSP drivers, only reduced – and the motors run much quieter. Using the settings in the Smoothie config I do not have to worry about the speed/acceleration at all now when accessing any part of the bed, it won’t go into that speed danger zone.
![]()
I used these for all 4 motors on my delta, as the maximum print size is (x/y plane) is large, 430mm, and some of it’s parts were designed a bit heavier to allow me to swap out the effector for pick-n-place, laser, drill, etc. I have printed prototypes for someone nearly that large.
Really the motors see hardly any noticeable torque under normal operation compared to what they are rated, it’s when they over-speed into low-torque/resonance zone that is the problem – when fully resonant – boom – they have no torque at all. This is a much steeper drop in torque than the RPM/torque curve.
One of those Nema 23 works great for my direct drive 3mm extruder, as their rated output is 11.2 kg/cm. I am running that one at 2A, 26v with a Mk-7 gear bored out to fit, directly from the Smoothie. I don’t measure the output by print speed, I use mm3/second extruded – it will comfortably output 12mm3/second for normal layers, 18 when bridging (ABS).
I wish I’d known then what I know now about what that combination of motors, controller, pulleys, and drivers would do.
Would have saved a lot of time and money.
So hopefully you understand a bit where I was coming from in my fuzzy headed post earlier.
From Running NEMA 23 motors
David, I feel 3V is a very thin margin, I will be afraid of voltage spikes due to return current generated by decelerating stepper, especially if you use higher inductance steppers and/or high mobile mass. In addition, if using Nema 23 you get mid-band resonances, that may also creates spikes. 0.9° stepper will also increase return current for a given inertia.
Nearing the max voltage may need high capacitors.I have no usable scope, so I cannot check deceleration spikes but I found these links :
- [electronics.stackexchange.com] stepper-motor-causes-massive-spikes-in-power-supply-when-decelerating
- [forum.pololu.com] stepper-motor-deceleration-causing-large-voltage-spikes
- [www.phidgets.com] Using_Steppers_in_High-Energy_Applications
Also, Paul Wanamaker built a large machine and faced miscellaneous problems with large steppers.
You may find posts from him on the forum.
Back EMF
From Running NEMA 23 motors
You may have a good point. A decelerating stepper motor feeds power back into the supply, which is likely to increase the supply voltage depending on the load on the supply (which may or may not include other stepper motors, extruder heaters, bed heaters, and fans) and the total amount of capacitance across the supply. I guess one of the worst cases will be on a delta when commanding the head down to the bed at full speed with high acceleration. I’ll do some measurements when I have time.
and
David, if I well remember, your machine use low acceleration (2000) and have a relatively light effector. However, you use 0.9 stepper. This is not very demanding compared to some others machines.
My D-Box with similar steppers as yours is using acceleration 6000 (and was tested at 8000) with an effector weighting slightly above 200g.It works well, but I am only in 24V.
So, For tests, I think you may increase acceleration and may be add weight on your effector.
And that will be still much lighter than AussiPhil and Motley will have.Also, most of us are using LED power supply. I think we can reasonnably assume they are not designed for hard power transient.
I have seen in one of the listed link that some people are using active dump circuits. Interesting, but complex.
Very big printers face same problems as CNC and that is more difficult to handle than simple printers.
and
It occurs to me that on a printer with the heated bed driven from the same power rail as the stepper drivers, an effective way of dumping the excess energy would be to turn on the bed heater during hard deceleration.
David Crocker also makes points about Nema 23 and Back EMF in More upgrades to the large Delta 3D printer:
24V power
In my last post I described how I upgraded to 0.
9 degree/step motors to improve the resolution of the printer. I hadn’t allowed for the higher back EMF of these motors when running at the speeds (up to 333mm/sec) that I used with the original motors, so I had to reduce the maximum speed to 150mm/sec. The obvious solution was to change from 12V to 24V power.
Like this:
Like Loading...
Free STL file of Nema 23 Motor Mount・3D printing template to download・Cults
20 mm x 40 mm MGN12 Linear rail stop mount alignment tool
Free
SolidCore CoreXY 3D Printer
Free
Workhorse 3D Printer
Free
nine0003 12mm Lead Screw Nut Mount - WorkHorse 3D PrinterFree
Nema 17 Z Axis Motor Mount
Free
SolidCore Z-Axis Bracket Bed Mount
Free
SolidCore CoreXY Carriage
Free
Pilot Printer
Free
nine0005The best files for 3D printers in the Tools category
COVID 19 - DENTAL ASPIRATOR - VACUUM
2,80 €
Spare key Midi usb controller Korg NanoKey2
0,85 €
60 NeoPixel Ring Camera Mount
Free
Filament Dehydrator Tray Extensions
Free
Wedo 2.
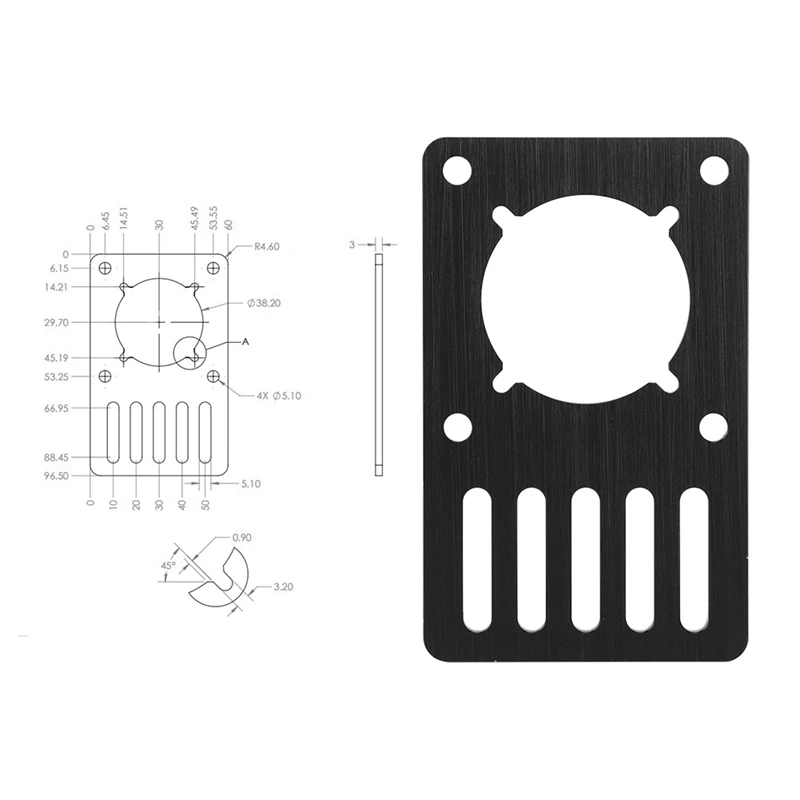
5 €
Paper Towel Face Mask
Free
Low and High Jar I BM003
Free
Toothless Herb Grinder 2.0 By 420ThreeD
Free
Bestsellers in the Tools category nine0037
Armadillo - flexible wire conduit
1.66 €
Display holder FLSUN v400
€9.99 -fifty% 4.99 €
Quick Print Paint Bottle Rack (6 sizes)
2.82 €
SUPERBOX
1,50 €
ENDER 3 S1, S1 PRO, SPRITE, V3 AIR DUCT FAN 5015, ACCELEROMETER, LED strip
€2. -twenty% 2.14 € 68
Case for Chill Buddy lighter
0,93 €
nine0003 Phone holder2.42 €
Ender 3 S1 BEST cable guide - vertical
2,50 €
'ELEGANCE' Bambu lab set and general 3d printers
5 €
ARTEMIS -> Shop for Alligator 2 || 6.5" arrows || Repeating crossbow
6.25 €
nine0003 Ratchet holders - magnetic - holders for tool box organization2,65 €
ENDER 3 S1/S1 PRO REEL HOLDER AND DEPORTED REEL
2,12 €
Ender 3, 3 V2, 3 pro, 3 max, dual 40mm axial fan hot end duct / fang.
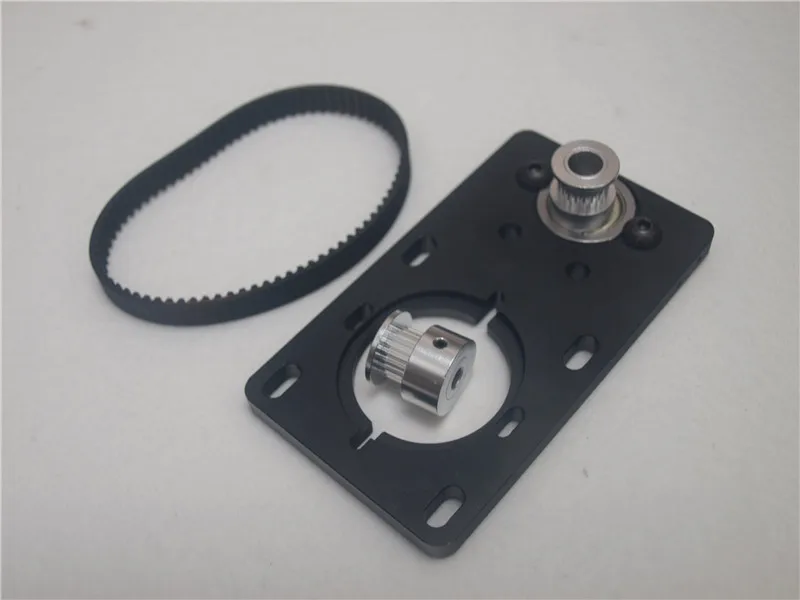
1.55 €
PRECISION CALIPER 3D PRINT DIY
3,12 €
PET-Machine, make your own plastic bottle filament at home!
15 €
Cut-Man - PET bottle cutter with handle!
€3.49
Do you want to support Cults?
Do you like Cults and want to help us continue our journey on our own ? Please note that we are a small team of 3 people, so supporting us in maintaining activities and creating future developments is very easy. Here are 4 solutions available to everyone:
-
AD: Disable your AdBlock banner blocker and click on our banner ads.
-
AFFILIATION: Shop online with our affiliate links here Amazon.
nine0006
-
DONATIONS: If you want, you can donate via PayPal here.
-
* INVITE FRIENDS: * Invite your friends, discover the platform and great 3D files shared by the community!
stepper motor selection, which is better
With the advent of 3D printers, people's lives have become much easier. Devices are successfully used in many areas - dentistry, industry, jewelry and medicine. Now a 3D printer is not a luxury item, but a design that is quite affordable. But still there are those who decide to independently manufacture printing presses. Next, let's talk about how to choose a stepper motor for a future 3D printer and what features should be taken into account. nine0006
3D printer motor
In the design of a 3D printer, the main function for the movement of the extruder along the axes is performed by stepper motors. They have low weight and high torque.
A stepper motor is a motor without a commutator, whose rotation is not smooth, but discrete (in steps).
By setting the speed and duration of the pulses, you can make the device rotate in a certain direction. In this case, it is possible to adjust the direction of rotation and the number of revolutions of the rotor. nine0006
If we talk about the design of such devices, then there are three main types:
- Motors with variable magnetic resistance - have several poles on the stator and a rotor made of soft material, and 3 windings independent of each other. This type is practically not used.
- Permanent reluctance motors - Includes stator and magnetized rotor. Such motors have 24 to 48 steps per revolution. nine0163
- Devices combining variable and constant magnetic resistance (hybrids) - combination of the best properties of an AC and a constant rotating motor. The number of steps is from 100 to 400.
The hybrid engine is the most common design, which, in turn, is divided into unipolar and bipolar types.
![]()
Which stepper motors to choose for a 3D printer: the best options
When buying a rotator for a 3D printer, you should pay attention to the following parameters:
- rotating structure size;
- holding torque - 2.5-4 kg/cm;
- rated current - optimal version for 1.7 A;
- Shaft - Diameter must match the design of the printer.
The most common motors that are installed on the design of the printing device are bipolar with four leads. Such structures in the event of a breakdown are easy to find and replace.
NEMA marked rotary motors are installed in 3D printers. nine0006
NEMA is a National Electrical Manufacturers Association that standardizes rotating devices in terms of flange size and fit. This standard allows different manufacturers to produce engines according to certain parameters, depending on the marking.
Most popular models in the NEMA series:
- NEMA 17 with 42*42mm flange;
- NEMA 23 with 57*57mm flange;
- NEMA 34 size 86*86mm.
nine0163
Stepper motor drivers for 3D printer
To control motors in 3D devices, drivers installed in the board slot were developed.
There are several types of drivers:
- Constant voltage - such drivers are inefficient and are used in a product with low speeds.
- Two-level - These controllers support stepping and half-stepping modes. They reduce engine heat and are efficient in operation. nine0163
- PWM drivers are the most popular on the market. They are highly intelligent and have many additional features.
Also, when choosing a driver, you should pay attention to the following parameters:
- current strength;
- supply voltage;
- availability of optoisolated inputs;
- availability of resonance suppression mechanisms;
- availability of protocols required for engine operation;
- surge protection; nine0163
- micro stepping;
- driver quality.
Learn more