Manufacturing with 3d printing
The evolution of 3D printing in manufacturing
Paul Benning, Chief Technologist at3D Print HP Inc. discusses the current technology trends within the manufacturing industry relating to 3D printing...
Paul Benning, Chief Technologist at 3D Print HP Inc. discusses the current technology trends within the manufacturing industry relating to 3D printing.
What is 3D printing?
3D printing is a manufacturing process that produces objects in accordance to a 3D digital model. By using a 3D printer and adding material layer by layer, such as plastics and metals, complex objects can be produced both rapidly and at low cost, in short runs or as one-of-a-kind parts. HP Multi Jet Fusion 3D technology enables customers to produce complex parts with controllable physical and functional properties at each point and provides speed, quality and strength throughout the manufacturing process for a range of industries and applications.
How has 3D printing evolved over the years?
We’re on the cusp of the 4th Industrial Revolution, where physical and digital technologies will radically alter how companies conceive, design, produce, distribute and repair nearly everything. The increased global demand for sustainable solutions and customised products has resulted in a surge in demand for 3D-printed parts and products. Technological innovations in the field have halved costs while delivering twice the performance. As the 3D printing sector moves beyond prototyping, use of this technology, particularly in supply chains, is becoming increasingly widespread.
In 2018, HP launched Metal Jet technology, the world’s most advanced 3D printing technology for the high-volume manufacturing of production-grade metal parts. It delivers mechanically functional final parts with up to 50x more productivity than other 3D printing methods, and at significantly lower cost compared to other binder jetting systems.
As we see more customers scale for production and further collaboration through a growing ecosystem of partners, the possibilities are growing for a new era of manufacturing.
What are the current trends in 3D printing?
A trend we’ll see is the accelerated impact of digital manufacturing take hold in the form of production applications, particularly across the automotive, industrial and medical sectors. In the auto sector, we’ve seen an increased focus on developing production-grade materials for auto applications as 3D printing gravitates from prototyping to full production of final parts and products. Additionally, as new platforms such as electric vehicles enter mass production, HP Metal Jet is expected to be leveraged for applications such as the light weighting of fully safety-certified metal parts. Industrial 3D manufacturing also enables the automotive industry to produce applications in new ways that were previously impossible, along with the ability to design application-specific parts for individual systems or models.
What innovative technology have you seen being used with 3D printing?
One really powerful example of 3D printing we’ve seen in the last few weeks is how 3D suppliers and digital manufacturers are coming together to help produce vital applications to help fight COVID-19. HP and its global network of partners and customers are printing crucial parts such as ventilator valves, face mask adjusters and hands-free door handles - for local hospitals and healthcare providers around the world.
Beyond how 3D is supporting the current situation at hand, we’ve seen myriad ways that the technology has been used – everything from customised prosthetic limbs, to parts that are used in cars, to invisible braces helping people to achieve their desired smile.
With industries facing increased customer centricity when it comes to the services they provide, how can 3D printing help to drive customer centricity?
One of the major benefits of 3D printing is the ability to customise products and parts fully for the end user. This may be in the form of design preference, or it could serve a more practical purpose such as improving the fit or usability of a product. For example, 3D printing makes it easy to customize prosthetic limbs and shortens the production time from weeks to days, and it can deliver custom-fitted and individualized footwear, including insoles, through innovative 3D scanning, dynamic gait analysis and manufacturing technologies.
How can 3D printing make manufacturing more agile?
By allowing consumers to dictate demand, 3D printing lends itself to increased supply chain mobility, flexibility and adaptability, therefore reducing costs and waste. Companies no longer have to predict consumer demand by gambling on how much of a product they will sell; 3D printing ensures the infinite flexibility as they are able to print what they need.
SEE ALSO:
-
Industry 4.0: managing the Cultural Impact in Manufacturing
-
Oracle: a modern platform for smart connected factories
-
PwC: digital factories shaping the future of manufacturing
-
Read the latest issue of Manufacturing Global here
3D printing also allows manufacturers to prototype more successfully, as they can print a new model/part with every advancement or amendment of the design, through a simple tweak on the software, printed instantly. Thus, saving time and money rather than if they had to produce new moulds each time.
3D printing also allows for incredible volumes to be produced in a short time frame. HP customer SmileDirectClub uses Mult Jet Fusion 3D printing solutions to produce more than 50,000 personalised moulds each day, and anticipates printing nearly 20 million mouth molds over the next 12 months alone.
In 2018, more than 10 million parts were produced using HP Multi Jet Fusion technology worldwide.
How can 3D printing benefit the manufacturing industry?
3D printing completely reinvents the way things are conceived, designed, produced and distributed, significantly lowering development and production costs, immensely simplifying logistics, and lowering carbon footprint. It holds great potential to revolutionise supply chains, and we are beginning to see an increase in the number of companies who turn to this form of manufacturing in order to stay competitive and create products faster.
3D printing will be the catalyst for significant shifts within the global manufacturing sector, and leaders will be defined by their ability to harness its full disruptive power. In a fully digital future, the production of goods will be driven closer to the consumer, democratizing manufacturing on a worldwide scale and allowing products to be mass-customized.by traditional processes, designers will be free to create entirely new categories of products, as the line between ideas and physical reality erodes. And manufacturers, no longer tethered to overseas factories, will shorten supply chains with a newfound ability to custom-produce anything, anywhere.
What are the challenges of 3D printing?
The most significant hurdle is the change of mindset. It is crucial to think about designing for 3D from the first stages of product development, to think about the wider implications of how development is staged to full scale production, and how supply chains can be further optimized. There are deep, engrained sense of limits and hurdles for those who have worked decades in traditional manufacturing. With 3D manufacturing, there is almost a re-learning process that needs to take place – the vast majority those limits no longer apply. The design possibilities are limitless. And, of course, there are new skills that must be developed to fully leverage these possibilities. For engineers, new elements of the design process will be introduced into their roles where they will need to learn the mechanics of 3D printing to become experts in the processes and best support operational functions during production.
What applications of 3D printing have you seen within the industry?
3D printing is being used in a variety of industries including automotive, manufacturing, healthcare and consumer goods. Alongside the incredible efforts to help support the COVID-19 pandemic, I’ve also seen some fantastic applications in the commercial sector. 3D printing is being used by major car manufacturers to produce gear sticks and safety gloves, fashion designers are producing 3D printed handbags and shoes and companies are printing custom foot insoles with just a scan of a patient’s foot. The possibilities really are endless and I’m looking forward to seeing what comes out of the industry over the next few years.
The work being done by Jaguar Land Rover as they advance EV development, or Vestas VBIC, the largest provider of wind turbines in the world, are significant examples of how 3D printing is enabling industries to move seamlessly from prototyping to production, with incredible flexibility to make improvements in near real time.
For more information on manufacturing topics - please take a look at the latest edition of Manufacturing Global.
Follow us on LinkedIn and Twitter.
3D Printing in Manufacturing - Challenges and Advantages
3D Printing in Production
Low volume manufacturing
Moving across to 3D printing will make it possible for businesses to consider short-run part production, where focused product teams can launch new products more frequently. They will be able to work beyond the realms of their imagination and certainly beyond the restraints that come with traditional methods. It delivers an agile development process for physical parts and has the ability to accelerate the production and the time it takes to get to market.
There is no doubt that 3D printing is way ahead of conventional methods when it comes to manufacturing the first several hundred parts. But is 3D printing also suitable for manufacturing on large scale?
High volume manufacturing
3D printing is a technology that is developing and growing faster than most other technologies due to the way it can influence manufacturing processes and help businesses perform to a higher level. A production line that is set up for 3D printing is easier to alter than that of a production line for traditional manufacturing, making 3D printing a feasible option for many reasons.
The whole production line can be adjusted and adapted with the speed of the printing production line. Therefore, improvements to machinery, adjustments to the print speed or even a change of product can be made almost instantly. When you consider this against older methods, it can take several weeks or months to make the changes and then begin producing again.
It is inevitable that the capabilities that come with 3D printing and the way in which technology is evolving will enable businesses to adopt this new way of producing products or parts and it is likely that this adoption is going to grow well in the future.
What are the advantages of using 3D printing in manufacturing?
1. Reduction in costs
Traditional manufacturing methods are notoriously expensive, whereas the 3D printing process makes the creation of parts products cheaper and more accessible. Unlike traditional manufacturing where many different people may be required to operate a number of machines or a production line is required to piece together the product, 3D printing removes this. Each 3D printer will require an operator to start the machine before it begins an automated process of creating the uploaded design. Therefore, when using 3D printing for manufacturing, the labour costs are significantly lower as there is no need for skilled machinists or operators to form part of the process.
2. Reduction of risks
When businesses have the ability to confirm a design before committing it to production, it can help to remove the risk of errors, wasted materials and money. Creating products with 3D printing can help to increase confidence, especially when you consider that a 3D prototype is easier to redesign and alter than anything that has been created using a traditional method.
When it comes to setup costs, manufacturers won’t have to produce so much of a product in order to justify the setup costs. The traditional methods of production often relies on the efficiencies of mass production and requires a large number of assembly workers, whereas, 3D printing requires the filament material and not a lot more to fulfil an order.
3. Failure is cheaper and faster
3D printers will not need to be retooled between production runs. The speed at which a 3D printer can assemble could be deemed to be slower than that of a traditional assembly line. However, when you factor in machinery problems that can stop production and human error, there is more that can go wrong with traditional manufacturing.
4. Time to market
3D printing makes it possible to develop ideas at a faster pace. In some instances, it could be possible for 3D concepts to be designed and printed on the same day but in terms of large-scale manufacturing, it is certainly faster than conventional methods. This can help companies to reduce manufacturing time from months to days while ensuring that they remain ahead of their competitors.
5. Build and grow
For businesses that adopt 3D manufacturing, it is possible to continue to grow and evolve through the production of items that have been created from their imagination. There are no limits when it comes to 3D manufacturing because things can be created virtually and then printed in a very short time frame. Therefore, for any business, a product can go from an idea, to a concept right through to the finished part.
6. No Limitations in geometries
For many years, standard manufacturing techniques have held back the design of products. However, with many improvements made already and more to come in the future, the 3D manufacturing process can create an endless list of possibilities. Geometries that were once difficult can now be achieved such as holes that change direction or square interior cavities. These kinds of designs have become possible and simpler to construct.
7. Less waste
As this is a relatively new technology that is gaining momentum, the material cost can still remain high. However, the range of materials is growing and this makes it possible for the price to decrease over time. But, in comparison to traditional methods, the overall cost is a lot lower. The manufacturing process can result in a lot of waste, particularly where traditional manufacturing is concerned. However, this is where 3D printing for manufacturing can transform the amount of waste, because of the way in which it uses resources more efficiently.
When it comes to using 3D printing for manufacturing, a 3D printer will only use the material that passes through the extruder of the printer and that is used for the assembly of the product.
In comparison to injection–molds, often there is a requirement to use additional materials to fill the molds. In the majority of mass production needs, 3D printing will deliver a lower amount of waste (for example the support material) than traditional manufacturing.
8. Less storage space
Many industries require businesses to store the parts and products that they need or sell. This means that a significant amount of storage space is required to house goods that can sit on a shelf for months or even years. This costs a lot of money. By using 3D printing for manufacturing, costs can be cut by reducing the amount of storage space that is needed. 3D printing makes it possible for goods to be made as they are sold. This means that there will be no overproduction and reduced storage costs.
3D printing mold making
Desktop 3D printing molding allows engineers and designers to get more functionality out of a 3D printer beyond prototyping. Molding opens up a world of production materials and provides the opportunity to produce small batches and sample test molds before using expensive
tools.
This booklet covers the following three mold making strategies: injection molding, high temperature molding and injection molded elastomers. Typically, molds are made from Formlabs clear resin, which is preferred for its transparency, although any standard resin can be used, and high temperature resin is ideal for processes with high temperature requirements. It should be noted that these processes are best suited for stereolithographic 3D printing (SLA) because the printed parts are isotropic and waterproof.
Prototyping and small-scale production with 3D printing tools
Process | Equipment | Run time | Material cost (for example: 300 ml/cm3) |
Do-it-yourself mold making and parts making | Mold 2 and injection molding machine | 5 to 24 hours (form print time) | Approximately $50 for High Temperature Resin |
Outsourced SLA Form | injection molding machine | 3-5 days | Approximately $700 for back office printing on industrial SLAs |
Outsourced metal mold | injection molding machine | 1-2 weeks | Approximately US$6,400 for office desk, aluminum finish |
Outsourced mold Creation and production | no - full outsourcing | 1-3 weeks | $4,000 to $15,000 depending on volume and materials |
Silicone molding and some desktop molds are available using Formlabs Standard Resins High Temp, which has the highest HDT at 0. 45 MPa for any 3D printed materials currently on the market and allows print parts that can be used for high temperature forming such as thermoforming and injection molding of materials with higher melt temperatures
Injection molding
High-resolution SLA 3D printing on the Form 2 can be used to quickly prototype inexpensive injection molds that can be used to make real parts from a wide variety of
thermoplastic materials. Injection molds can be used to test mold designs prior to metal tooling or to produce low-volume parts
3D Printed Injection Molding covers injection molding using Formlabs clear resin printed molds. Following the release of Formlabs High Temperature Resin, designed to achieve higher heat resistance and stiffness, the booklet has been updated to describe the benefits of High Temperature Resin plates that are less likely to break due to thermal shock or temperature-related deformation
USB Device Enclosure Mold, 3D Printed on Form 2 High Temperature Resin
This mold contains a core, a cavity, and two "gates" leading to the two halves of the enclosure. High temperature resin molds can be used to mold a wide range of thermoplastics without thermal stress or temperature-related deformation
Formlabs High Temperature Resin can be used to injection mold a wide range of plastics.
3D printed mold tools reproduce the exact quality of the SLA print finish on the Form 2. Forms can be printed at 100 microns for faster prototyping or the recommended 50 microns for fine detail and smoothness
electronics molded in HDPE with a High Temp tool.
This shape of the USB case has been adjusted over three iterations to remove cavities, entrapped air, and partial shrinkage. Total cost of materials for prototyping this high temperature resin mold tool: $25
Thermoforms
Form 2 3D printed thermoformed dies are a fast and efficient way to create high quality vacuum formed parts for low volume production. Printed thermoformed dies can be used to make packaging prototypes, clean orthodontic retainers, and food-safe molds for chocolate confectionery.
Thermoforming dies experience less pressure than injection molds, but still reach high surface temperatures.
High temperature polymer resists deformation and surface degradation from the combined heat and pressure of thermoforming for most plastics. Standard resins may also be suitable for thermoforming with some low temperature plastics such as vinyl.
APPLICATION EXAMPLE
Formech thermoformed prototype packaging.
Thermoforming a thin sheet of polycarbonate over a high temperature polymer matrix produces a transparent detail by matching the geometry and detail of the matrix. Thermoformed packaging can be easily prototyped and incorporated into the design process along with 3D printed product prototypes, and all this is achievable on the Form 2. The printed matrix was used without additional processing and the need for UV curing. Texture is recommended in thermoforming design to prevent air trapping under the sheet - layer lines on the printed thermoforming die can be helpful in this regard.
TEMPERATURE CONTROL
High Temperature Polymer Cycle Thermoforming
The surface temperature of the die reaches 130°C. The high temperature resin is highly resistant to deflection, whereas with standard resins you must allow the print matrix to cool between cycles, otherwise warping and degradation may occur.
If temperature rise becomes a limiting factor in molding efficiency, cooling channels are an effective way to remove heat from the print. When used in conjunction with an automated thermoforming machine, the water-cooled die can produce more parts with shorter cycle times.
Conformal water channels visible in the thermoforming high temperature die.
Thermoforming die surface temperature
Conformal cooling channels are easy to implement when designing for SLA 3D printing and print successfully without any internal supports to interfere with flow. After printing, the channels are flushed with uncured resin using isopropyl alcohol. The mold is connected to a pump and a source of cold water.
Integrated water cooling as a strategy can also be applied to standard and rigid polymer parts to reduce heat dissipation when used in higher temperature environments.
Elastomer casting
Precision molds for most flexible elastomers such as silicone and urethane rubber can be printed on the Form 2 using standard resin. The transparency of Clear Resin allows the material to be observed during the pouring or injection process. Flexible materials can be easily removed from rigid SLA printing plates, and applications from model production to functional molding can be obtained. Silicone molding can also be used to quickly replicate master prints, greatly reducing production time when multiple rigid parts and objects are needed.
APPLICATION EXAMPLE
Forms printed on Form 2 are used to create composite parts with advanced built-in features. Assembly subcomponents such as electronic, metal and SLA printed elements can be embedded and sealed in soft surface molds.
RightHand Robotics used the Form 2 to create the production blocks of their robotic gripper using urethane molding. The forms were printed in clear resin, with black resin inserts forming the internal structure.
The Form 2 printer allowed RightHand Robotics to move from prototypes to small-scale production without the need for expensive tooling. The rapid transition from original printed prototypes to production materials that have longer flex cycle life was done with 3D printed plates on the same Form 2 hardware they used for initial prototyping.
The first layer applied from RightHand Robotics' multi-stage process includes urethane compounds that can withstand multiple flex cycles while still providing the high elasticity needed to securely return the gripper to its open state.
The outer layer provides improved tactile grip and control, as well as sealing the sensor electronics with softer, lower durometer rubber.
SLA 3D printed parts can also be encapsulated inside molds to provide a rigid structure for flexible materials. The overlay can be mechanically bonded to the insert by adding holes, recesses, and columns to the printed parts, which enhances assembly and reduces the need for chemical adhesive.
Conclusion
Form 2 molding is a powerful strategy for the production of parts in small batches, as well as production from commonly used plastic and elastomer materials. 3D printing tools allow engineers and designers to easily prototype parts that look and function exactly like the final product, with geometries and material configurations that are quite complex, using 3D printing, such as in the case of encapsulated electronics and thin packaging. For high temperature forming, high temperature polymer offers superior thermal properties at a lower cost and with shorter lead times than process outsourcing 9This unique modern fixtures like a 3D printer.
Professional 3D printing services for the creation of any products are offered by the Technoplast manufacturing company.
Scope of application of three-dimensional printing
Modern technologies allow the use of this technique in almost all areas of modern life without exception. Therefore, orders for the manufacture of products using 3D printing come from various areas of production. In particular, 3D printing is used for:
- Creation of prototypes - experimental, trial, samples of new products being developed.
- Manufacture of souvenirs, elements of original decor.
- Production of medical equipment and even individual organs of the human body.
- Create tutorials and tutorials
Book a product consultation
Submit a request
Use a 3D printer in a foundry
3D printing can also be used to create any injection mold. Unlike standard technology, when the shape of the finished master model is additionally painstakingly corrected by the master to the parameters specified by the program using milling finishing or manual grinding, this method is much more profitable, both in terms of time and labor. When manufacturing a mold by printing on a printer, in a few hours the desired product is completely ready, 100% corresponding to the parameters of a digital model created using 3D modeling.
By choosing a 3D printing technique to create molds, the customer benefits from the following:
- Saves time and money. In addition to the fact that the forms are prepared much faster than with the standard method, the cost of their production is also more affordable.
- Has the ability to order molds of any shape and size. The printer can reproduce in reality an object of any degree of complexity.
Also, forms created in this way are much easier to improve and correct, if necessary,
Technologies and materials of modern 3D printing
There are several types of 3D printing.
FDM technology
The method involves the creation of a 3D object by layering a material, thermoplastic, melted in the print head of the printer used for printing. The method is characterized by relatively low cost, a wide choice of materials (ABS plastic, nylon, polycarbonate, polyethylene, etc. can be used), as well as high printing speed.
The disadvantages of the technique include the need to use props when creating parts with overhanging elements, as well as post-processing of the finished product, the impossibility of manufacturing large solid objects.
FDM technology is mainly used for prototyping parts and medium-sized objects.
SLS technology
The object is formed by layer-by-layer application of the powder sinter product. Nylon, resins, ceramics, glass, etc. can be used as the printing material. The product created in this way is highly durable, does not need a manufacturing process to use support. But this technique is more expensive than the above. In addition, the product that came out of the 3D printer has a rough surface and needs additional polishing.
The method is used most often for the manufacture of complex parts for mechanical engineering, as well as the production of small series of products for various industries.
SLA or photopolymer technology
Made from photopolymer that cures when exposed to ultraviolet light. The result is an impeccable quality part with high detail and a smooth surface (no need for additional grinding). The disadvantages of the technique include the high cost of materials and their limited choice, slow printing speed.
Stages of manufacturing products by printing on a three-dimensional printer
- Provision by the client of a 3D model created using a 3D scanner or 3D modeling process. If you do not have a digitized version of the future product for printing, our employees will produce it themselves, based on the drawings, photographs or detailed description provided by you.
- Choice of 3D printing technology and material from which the object will be made.
- Drawing up an estimate of the order and its coordination with the customer.
- Printing a product - depending on the complexity, the process takes from half an hour to several days.
- Post-processing of the product that came out of the 3D printer (if necessary): the procedure includes grinding, painting, removing supports.
Book a product consultation
Send a request
Why choose 3D printing
Object crafting speed
3D printing allows you to create products in the shortest possible time - from 30 minutes to several days. When choosing the injection molding method, only preparatory work takes up to several months.
Choice of technology and material
In addition to choosing the right technology (FDM, SLA, etc.), the customer can also order a specific material. Most 3D printers print from plastic, but many modern models also work with wax, clay, wood, rubber, and other materials.
Creation of objects of any level of complexity
With the help of 3D printing, you can easily bring to life any, even the most complex and detailed object. By means of a 3D printer, they even now create prostheses and individual internal organs for patients.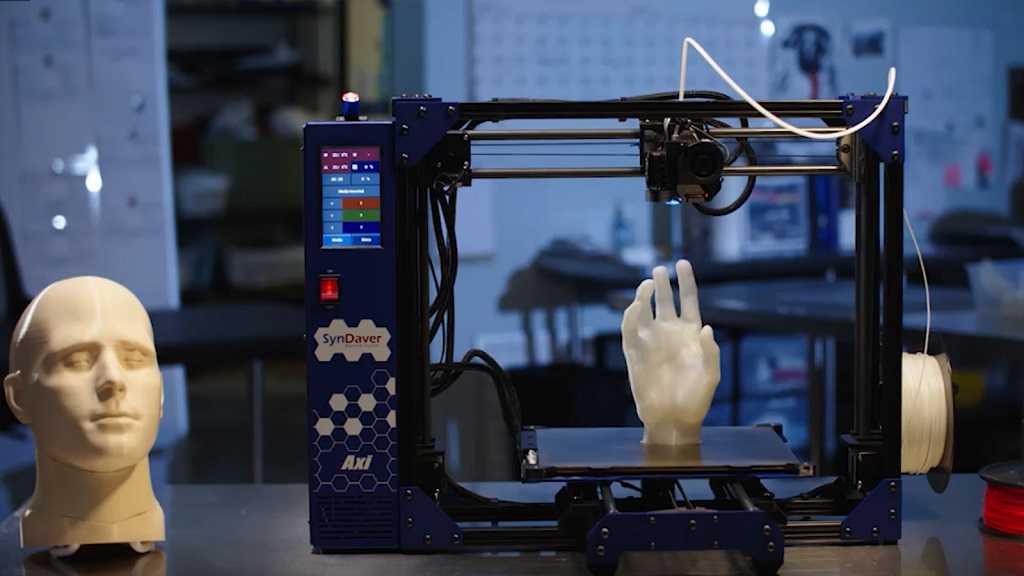
Simplicity and accessibility
3D printing does not require any special tools or equipment other than a 3D printer and a prepared digital model in STL format. Whereas with the injection molding technique, it is necessary to have a pre-prepared mold, injection molding machine, etc.Place an order for the manufacture of products by 3D printing in Technoplast!
Affordable prices for services
It is profitable to place an order for the manufacture of any product using the 3D printing method with us. After all, you communicate directly with the manufacturer and do not overpay for the services of third-party intermediaries, and we also provide individual discounts and can consider the possibility of payment by installments. Contact us!
Turnkey work
We provide not only services for printing products on 3D printers, but, if necessary, our company's employees can independently draw a digital version of the part for its further manufacture - you can order 3D modeling and scanning of an object from us with subsequent refinement.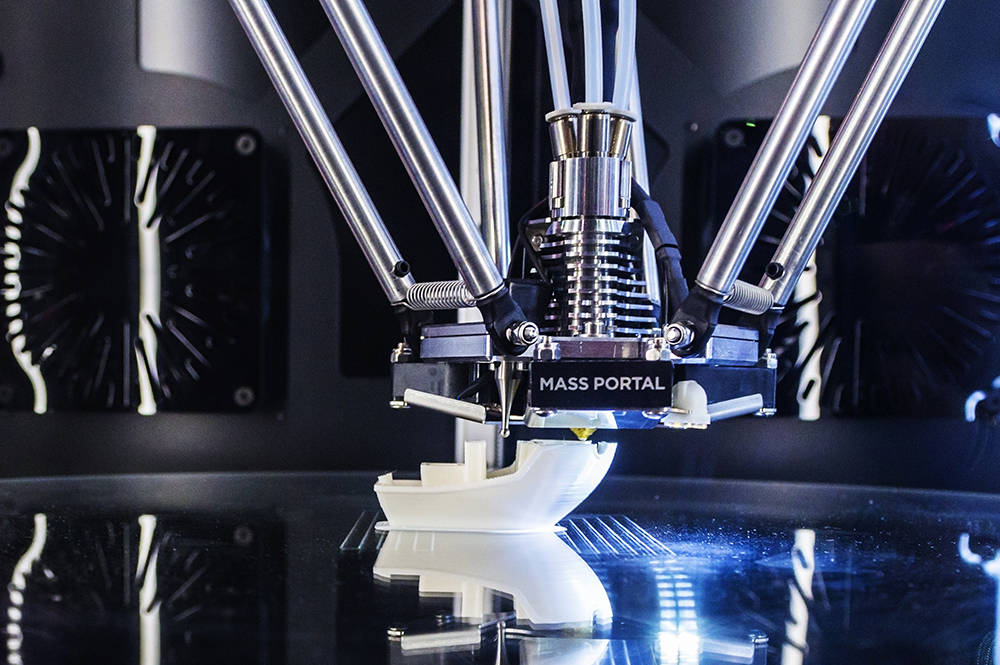
Assistance in filling out an application
We provide professional advice, answer all your questions, help with the selection of suitable materials and technologies that will ensure the creation of high-quality products that meet all your needs.
High quality
We employ experienced employees who know absolutely everything about 3D printing and are able to perfectly apply their knowledge in practice, and the use of modern equipment and quality materials ensures that the products that you receive from us within the agreed time will be of high quality, durable and in accuracy that meets all your expectations.
Any number of
We accept orders for the production of three-dimensional printing both for single items and for mass production - we produce batches of goods up to 1000 pieces.Q&A
How much does 3D printing cost you?
The total cost of 3D printing depends on many factors, including the printing method and material, the complexity of the product being created, the number of applied layers, infill density, and the need for post-processing of the finished product.