Arduino 3d printer review
The Best Budget 3D Printer You can Buy
There are loads of budget 3D printer options on the market. You can easily find cheap 3D printers, but sourcing one of the best 3D printers under $500 can be a challenge. Enter the Elegoo Neptune 3D printer, a quality device for makers of all skill levels. Learn why this may be the top entry-level 3D printer you can buy in my Elegoo Neptune 3D printer review!
What is the Elegoo Neptune 3D Printer?
From manufacturer Elegoo comes the Neptune 3D printer. It's a Prusa i3 size printer that boasts compatibility with PLA, ABS, and TPU filament. There's a carbine glass build platform and Titan extruder. Whereas many 3D printers come fully assembled, the Elegoo Neptune does require a bit of assembly. However, I was able to get my Elegoo Neptune configured in a jiffy.
Pros:
- Easy to set up
- High-quality print jobs
- Glass print bed
- Compatible with PLA, TPU, ABS
- Titan extruder
- Prusa i3-size
- SD card reader
- Comes with a slew of accessories
- Includes Elegoo Cura
Cons:
- Fiddly screws
- Bed leveling is a pain
Elegoo Neptune 3D Printer Review Verdict
Like the Elegoo Arduino UNO starter kit, I was truly wowed by the Elegoo Neptune. A layer height of 50-300 microns allows for quality as well as speed. Essentially, layer height is the precise height of each layer of plastic in a 3D printed model. You'll find variable speed, smoothness, as well as resolution with different layer heights. Smaller heights range from around 50-100 microns, so its range of 50-300 is quite pleasing, especially for a budget printer.
Upon opening the box, I was greeted with a mostly assembled 3D printer. As a semi-assembled 3D printer, I had everything I needed to put the Elegoo Neptune together. First, you'll need to screw the bed in with four screws, then plug in three plugs. You'll find loads of accessories including a backup nozzle, tweezers, and even a bit of sample filament. You'll definitely want to snag a bit more filament for projects though. Installation took me about 15 minutes, 10 of which were reading through the sparse but completely comprehensive set up pamphlet. There's even a section on leveling your 3D printer, and steps on how to run your first print.
Unfortunately, leveling isn't the most enjoyable experience. How to level a 3D printer depends on what 3D printer you're using. Whereas some mid- to high-end 3D printers use software leveling, or even tout self-leveling, the Elegoo Neptune is a manual leveling get up. Typically, manual leveling a 3D printer requires thumbscrews. The number of screws depends on the printer, with as many as four screws. Sure enough, the Elegoo Neptune features four screws, one in each corner. Under the system menu, there's a leveling setting which checks five different points on the bed. What you'll want to do is place an A4 sheet of paper on the bed, then, test each point. It's best to keep the sheet of paper so that you can slide it out with a minimal amount of resistance. Too tight and no filament will stick to the bed. But too lose means your print job will come out sloppy.
Since leveling requires adjusting four screws, it's a bit of a challenge. With more adjustment points comes near constant fiddling to get your bed correct.
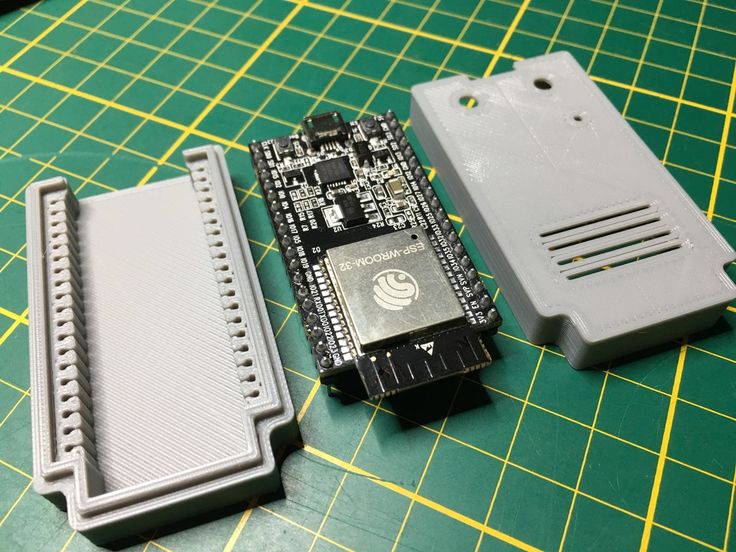
The print resume feature is an excellent inclusion. This way, if you run out of filament while printing, you can merely resume printing once you power back on. I was able to proceed from unboxing a semi-assembled 3D printer to cranking out 3D printed objects in under an hour. I appreciated the USB and SD card connectivity. There's an SD card, complete with flash drive adapter, in the box. Onboard, you'll find software and drivers as well as a test file. Of course, you can always source your own 3D printed projects and send those to your Elegoo Neptune. I preferred merely transferring files to the included SD card and printing from the Neptune.
Features:
The Elegoo Neptune arrives with a slew of features.
1. Semi-Assembly Kit
While the Elegoo Neptune doesn't come fully assembled, it's not a complete do-it-yourself job. Instead, it's a semi-assembly kit which is conducive to getting up and running. I was able to cobble my Elegoo Neptune together in under 30 minutes.
2. Titan Extruder
A Titan extruder makes for extremely precise 3D print jobs.
3. Carbide Glass Build Platform
The glass print bed means you'll appreciate superb adhesion and simple removal of prints.
4. Filament Detection and Print Resume
A convenient feature onboard the Elegoo Neptune 3D printer, you'll find a filament detection switch. Further, its print resume capability means if you run out during a print job, it automatically picks up from where it left off upon loading new filament.
Elegoo Neptune 3D printer specs:
- PLA, ABS, TPU compatibility
- Prusa i3 print size 8" x 8" x 8X
- Titan extruder
- Carbine glass build area
- Filament detection switch
- 350W single output switching power supply
- Auto-resume feature
- USB connectivity
- SD card slot
- Heated bed
Cost: $260
Should You Buy the Elegoo Neptune 3D Printer?
If you're in the market for one a budget 3D printer, the Elegoo Neptune is a top choice. With excellent build quality, superb printing, and a slew of features found on higher-end devices, it's a 3D printer sure to wow makers of all skill levels. Beginners should have no issue actually assembling the device.
My only minor complaint is that leveling the Neptune remains a pain. Still, once it's properly leveled, the Neptune provides high-quality prints, and easily clocks in as the best cheap 3D printer you can buy. Quality of printed objects surpasses the Anet A8. In fact, it punches way above its weight class. Lack of features such as software leveling may leave power users wanting, though it's a fantastic printer overall. If you're looking for inspiration, try printing your own Arduino-based coin sorting machine or an Arduino-controlled, 3D printable BB8!
Electroscore:
4.5/5Pros:
- Easy to assemble, modular design
- Comes with filament and tons of accessories
- Affordable, high-quality print jobs
Cons:
- Bed leveling a pain
- Small user base, small community
- Doesn't come assembled
Price: $26,000.
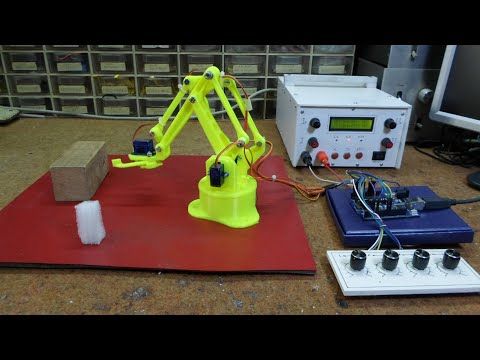
Link: www.amazon.com/product-reviews/B07MWXZGDN
Moe Long is an editor, writer, and tech buff with a particular appreciation for Linux, Raspberry Pis, and retro gaming. Writing online since 2013, Moe has bylines at MakeUseOf, TechBeacon, DZone, SmartHomeBeginner, DEV.to, DVD Netflix, and Electropages. You can read his writings on film and pop culture at Cup of Moe, check out his tech reviews, guides, and tutorials at Tech Up Your Life, and hear his thoughts on movies on the Celluloid Fiends podcast. Aside from writing and editing, Moe has an online course, the Beginner's Guide to Affiliate Blogging From Scratch. When he's not hammering away at his keyboard, he enjoys running, reading, watching cinema, listening to vinyl, and playing with his dog Sebastian.
Follow
Leave your feedback...
Previous Next
Related Articles
Anet A8 Review - Budget ($200 or less!) 3D Printer Kit Review – Maker Hacks
The Anet A8 is a $200 (or less!) 3d printer kit. In this review we answer the question how good could a sub-$200 prusa i3 clone 3d printer kit actually be?
“Review the Anet A8 3D printer kit, 220mm x 220mm for $200 (or less)“, they asked. So I take a look. Prusa-style printer. Lots of social media mentions. Some nice community prints. Meets that magic “3d printer for under $300” checkbox.
Heck yeah, I will review one of those 3d printer kits Mr Gearbest – free 3d printer, even if just for parts? Sign me right up!
Of course, part of me is skeptical. Yeah, lots of people like this guy, but how good could a sub-$200 prusa i3 clone 3d printer kit actually be? Would all the parts be in the package? Would it arrive in good condition? (The 3d printer is after all mostly acrylic …). How well would it actually 3d print?
Only one way to find out! I gladly accepted the challenge and awaited my A8 kit in the mail … Read on to find out what it is like in reality ….
Breaking! Get the A8 for the discount price of $155.
99 at Gearbest for a limited time!
Anet A8 3d printing community support
Before I even received this review printer, I did my research, and of course that means I checked out the Anet 3d printing community online.
I was already familiar with some, and on the strength of that I have cautiously recommended the printer, previously. But there is a huge difference between being aware of a community and a 3d printer and experiencing it for yourself, so I dove in deeper and was extremely pleased with what I found.
The printer has excellent community support, in the form of questions answered, mods provided, and trolls kicked out!
Definitely check out the Facebook group and look around.
Another example of the strength of the community is this printer set up right away in Simplify 3D. Shows how popular it is.
A8 3d printer kit pricing
3D printer kits come in all shapes, sizes, and prices. The latter being super important.
The main appeal of this 3d printer kit, and one of the reasons for its popularity of course, is that it is so affordable. For people dipping their toe into 3d printing, or purchasing for a kid, maker space, etc, budget is a priority. The dollar figure is going to weigh heavily, but you also don’t want to buy a bad cheap 3d printer.
Anet’s recommended retail price for the Anet A8 is around the $200 mark – impressive in itself – but, with regular discounts that appear, you can shave off more dollars bringing it lower. At the time of writing you can buy the Anet A8 at Gearbest for around $155.99! That means even in Canada you can get it for around $200 CAD shipped – that just blows me away.
Yes, you could buy two of these 3d printers for the price of some of its closest “budget” competitors. That’s amazing value, even if you are just looking at the price of parts.
Building the Anet A8 kit
You can read about my unboxing over at 3dpc.tech – a lot of the time between unboxing and printing was stripping the 3d printer frame parts of protective covering.
Grab a beverage and a favourite movie, you are going to be at it for a while.
So. Much. Peeling.
Some pieces had holes that hadn’t been fully cut, but you can resolve that easily if you are careful. That, and the fiddly T-joints were the worst part of the build itself. You need small hands or a lot of dexterity, otherwise it just takes a little while longer, as it did for me 🙂
Tedious, sure, but necessary to bring the pricing down, so can be forgiven. You know what you are getting with a 3d printer kit, it’s never going to be almost plug and play like the Creality CR-10.
The printer comes with tape right on the metal bed, and a sample of PLA, so I did a quick print off the included SD card just to check first layer.
Despite my reservations, and those couple caveats, the build went surprisingly smoothly, and after build it printed several decent prints.
Of course, this is not my first 3d printer kit by any means, but I only followed the YouTube instructions, I was under-caffeinated, and as you can see from the pictures I am not the tidiest printer builder in the world, and I managed to build with only a couple of minor issues over a weekend on and off. In my defence, I didn’t do the cable management in case I had wired something up wrong, I am not leaving it like that 😉
Example Anet A8 3d prints
How well does it print?
Baymax, Anet A8 example print Custom 3d maze Benchy the Benchmark Tug Boat Custom Robot ChassisConsidering I did zero tuning, it prints very well for a sub $200 printer. For these 3d prints I just printed off the example Baymax gcode from the provided SD card files, then continued with the default Simplify 3D profile.
For the latest prints I increased extrusion slightly, and I need to tighten my belts. That’s it.
I am not entirely happy with essentially bare wiring connections, especially coming from the power supply. The main board is exposed. All of this rules it out from classroom use unless you can build safety casing for the board and PSU.
Now this is “out of the box”, as it were. The community has a lot of crowd-sourced options for improvements, mods, upgrades, tweaks, and maintenance tips, just like all the upgrades I ran through with the Wanhao Di3 that made that printer superb. If I get time I will try some, priorities being nylock nuts on the bed, better belt tensioning, and maybe some bracing.
Right now the only upgrade I did was added a 3Dpc.tech branded Fleks3d plate (the bed size is actually a bit larger than my Fleks3d, but I have other printers so I am not worried about losing some mm, YMMV). I am seriously considering the Mk8 Micro Swiss upgrade for ability to print, well, anything pretty much.
After loading the example filament then loading up some purchased filament I slowly got used to using buttons and hitting right instead of the middle button rather than the familiar dial I am used to. If you don’t already have that motor memory then it will be no big deal 🙂
Anet A8 Review Summary
So all of this in mind, what is the outcome? First, let’s summarize …
Low points:
- Removing all the protective adhesive paper is a pain.
- Fiddly T-joints.
- Bare PSU wiring, mainboard, and general cable management.
- Own-brand mainboard and closed-source firmware.
- Menu system takes some getting used to.
High points:
- AMAZING value.
- Prints great, as well out of the box as any Prusa clone I have seen, and better than some well-respected options.
- 220 x 200mm heated bed is a great size for beginners and most general-purpose 3d printing.
- Mk8 extruder and hot end means you have easy maintenance and nozzle supply.
- Design means it’s easy to fix, replace, upgrade.
- LCD screen and menu control – I have used printers 3x the price that don’t have screens or SD printing ability!
Conclusion?
Absolutely recommended! Be careful assembling, especially around the acrylic and the wiring, and you will have an excellent budget printer!
PS!
Breaking! Get the A8 for the discount price of $155.99 at Gearbest for a limited time!
Category: Reviews and Buying GuidesTag: 3d printers, 3d printing, a8, anet, budget, kit, prusa
Cheap Arduino 3D Printer||Arduino-diy.com
This article describes the construction of a 3D printer that costs around $60-70 (probably the cheapest concept in the world).
This 3D printer works with the cheapest motors on the market - 28Byj-48, Electronics - Ramps 1.4 controlled by Arduino.
The author of the project is a 16-year-old guy from Germany.
3D printer specifications:
Working space: 10x10x10 cm;
Speed: 20 mm/s;
Resolution (accuracy): 0.2 mm.
P.S. Under each section, in accordance with the table of contents of the article, photos are posted as a visual instruction
Mechanical part
MDF boards:
-1x 30x34 cm (Base).
-2x 6x4 cm.
-1x 34x6 cm.
-1x 15x4 cm.
- 2 GT2 pulleys + 1 m GT2 timing belt.
-10 bearings 624.
-1 pulley Mk8 for drive.
-1 PTFE tube.
Smooth rods for guides with a diameter of 8 mm:
- 2, 22 cm long.
- 4 x 17.5 cm long.
Local hardware store:
- 1 shaft with M5 thread, which you will cut into 2 pieces.
-2 M5 hex nuts.
- 8 screws M3x16 mm.
-6 screws M3x 25 mm.
-4 screws x M4x45 mm.
-2 screws M4x60 mm.
-4 screws M4x20 mm.
-20 M4 hex nuts.
-10 M3 hex nuts.
-12 small screws.
Electronics
-1 Arduino Mega 2560 board + Ramps 1.4 + 4 A4988 stepper motor drivers.
-4 stepper motors 28byj-48.
-3 optical limit switches.
-1 Nema 17 stepper motor (we also order from Ali or Ebay. Such drives cost about 10 dollars).
Extruder tip:
-1 E3D-V5 Aliexpress extruder
or more expensive but with cooling
-1 E3D-V6 Aliexpress extruder.
Knots to be printed on a 3D printer
Download the latest versions of 3D models of units to be printed from the link: Thingiverse
.
2 "Z-Motor" parts
2 "Y-End" parts
2 "X-End" parts
1 "X-Carriage" part
1 "Motor" part
1 "Hotend" part
1 piece "Hotend Clamp"
Download mechanism for extruder here: Thingiverse.
28BYJ-48 Stepper Motor Modification
In order to convert the 28BYJ-48 stepper motor from unipolar to bipolar, you need to open the plastic cover.
Then remove the red cable and open the contact track from it as shown in the figure.
Now at the other end is the output that you will connect to the Ramps, arrange the pins as follows:
blue--yellow--orange--pink
With this little modification, you can connect these motors directly to the pins provided on the Arduino Ramps 1.4 shield
Y Axis
First you need to glue two wooden boards together.
Then place the printed parts "Motor", "Z-Motor" on the wooden boards.
Then fix the printed parts with the screws.
Next step: fit the motors into the slots and then the LM8UU bearings.
Install the pulley on the motor and the 624zz bearings next to it.
Use plastic ties to secure LM8UU bearings.
Next - install two guide rails 17.5 cm long with a diameter of 8 mm.
Finally, pull the belt through the "Y-ends" and install the limit switch.
X-Axis
For X-Axis you need:
Install two M4x45mm bolts in the "X-End".
Connect the motor as shown in the illustrations.
Tension the belt and install the limit switch.
Mount the extruder with two screws M3x25 and tighten with nuts.
Z Axis
In order to assemble the Z axis, you need:
Install LM8UU bearings in "X-Carriage" + "X-Ends".
Post install "X-Ends" + "X-carriage" on rails 17.5 cm (X-Axis) and 21cm (Z-Axis).
After that it is necessary to connect the threaded shaft with the motor
Printing table
We drill four holes with a diameter of 3 mm in a wooden plate 20x13 cm.
After that we tighten 4 bolts M3x25.
We assemble the entire 3D printer
We assemble it in accordance with the figures below. There is no point in giving additional explanations. The main thing is that the previous steps are correctly implemented. In this case, there should be no problems.
We connect electronics to the 3D printer
We connect electronics (including Arduino) in accordance with the figure below.
Software for Arduino
You can download the Arduino IDE configuration file from www.repetier.com.
This should be enough. You can carry out direct adjustment for your received design, dimensions, etc.
Photo of the printing process and results
After some calibration, good cube samples were printed with dimensions of 1x1x1 cm. As a result, there is a significant displacement of the layers.
So I recommend setting the A4988 to 1/16 microstepping and adjusting the current to the minimum value.
You can also play around with the Arduino firmware to get better results.
Leave your comments, questions and share your personal experience below. In the discussion, new ideas and projects are often born!
Why the first 3D printer is worth assembling yourself / Sudo Null IT News
- 0207
- It's faster than waiting from China Anet A8 for $109
- This is better (with non-crooked hands)
And finally, sooner or later you will face the need to repair / modify the printer and you will still have to master the practical skills of these devices.
And at the most inopportune moment.
And given that there were New Year holidays ahead and a long quarantine winter evenings,
I bought all the necessary components in two days in three local stores, which cost the same $ 109.
And only thanks to the "Martian rule" the total amount increased by only three evergreens.
But contrary to the well-known tape from the film, I used blue (and how could I do without it) electrical tape and plastic ties.
In general, if you are only thinking of assembling a 3D printer - welcome under cat,
where will be my thoughts on the design and assembly of some nodes.
For there are so many detailed assembly instructions on the Internet.
So, let's start with the Martian rule - after purchasing all the necessary components, consider that you are on the red planet, and the next rocket from Earth will be in half a year.
Thanks to this, I avoided an increase in the cost of the device by at least one and a half times and still improved the quality of the mechanical part.
The only thing you can afford is to go to neighboring manufactured goods or unscrew a spare part from your favorite rover is large.
Next, we will talk about assembling a Prusa-compatible Graber I3 printer, but it also applies to any device based on the RAMPS 1.4 + Arduino Mega 2560 control board. his hand and began to shake.
Correct! Without proper mechanical strength, you will either have to set the level of the printer table every time, or screw it with screws to the kitchen worktop.
From this point of view, the presence of a high box at the base adds rigidity compared to the original grabber or Annushka.
But the second time from the start I would have already assembled RepRap Mendel
Yes, the body is made of plywood, as I will have to paint, peel and drill during assembly, the main thing is not to loosen the seats giving room for backlash.
It is better to paint with acrylic varnishes - they do not stink, unless their version is sprayed.
And of course, plywood is preferable to metal in terms of acoustic comfort.
The only disadvantage of the selected ATX version of the case is the inconvenient vertical position of the screen compared to the original Graber version:
Pluses - better durability, you don't have to bother with laying wires and fixing the control board, the use of cheap ATX power supplies.
So we come to the second cornerstone issue - NUTRITION.
Our 12 volt unit should provide 20A.
Remember how you chose a PSU for your gaming/school/work PC?
By weight!
I will say right away that if you buy a new power supply from a store, it is no lighter than 1 kilo and the declared power is from 400W.
If used - look at the current and before use you should remove the cover and blow out all the dust with a compressor - at a tire fitting you will blow it out for three rubles along with cockroaches.
Go ahead, computer scientists / 3D-shniks are cool guys, but sometimes they forget Ohm's law by connecting power to the RAMPS with one, Carl wire AWG-20 (section ~ 0. 5mm sq.)
I did the right thing and made a mistake!!!
On a hot table with a power of 120W, a current of 10A simply melted the power connector
I had to dismantle it and solder the wires.
Yes, about soldering irons - the power of 60W is decidedly small: neither the old-fashioned one with a copper (thick) tip, nor the modern one with a thermostat could melt the solder in the process of soldering an acoustic wire with a cross section of 1.5 squares to a hot table.
I had to unearth an ax from the pantry:
But it will not be a crime to use a wire of 1 square and solder not 3, but 2 twisted AWG-20 wires from the power supply, then 60W is enough.
Continuing the topic of Ohm's law - You have already purchased "cheap" NEMA-17 stepper motors, it's time to look at the current consumption of the windings.
Standard model 1.66 (1.7) A, reinforced - 2 (2.1) A, "quiet / cheap" - 1.33 A, I have the last one.
The current produced by a conventional driver 4988 is up to 2Amps (even the dock does not speak to the winding or in general.
Everything seems OK, but there are two motors and RAMPS on the Z axis, and other control boards obviously contain two connectors for their parallel connection.
No, it's not scary if the R100 resistors are charred at the maximum current (there are boards with R50 for half the current).
And not even that the engines do not receive enough power (I have 0.75A everywhere except for the Z axis)
It's just that with this inclusion, the characteristics of the engines must match ABSOLUTELY, otherwise a wedge / skipping steps is possible in certain modes.
The REPETIER firmware did not cope with this at all, MARLIN got lost once at the stage of moving the extruder from the parking position at the beginning of printing.
Neither shuffling the motors nor the drivers helped.
The Z axis with two motors is saved only by their serial connection:
And oh, miracle, everything worked not on 2 amperes, but on the same 0. 75 as the rest of the axes!
Someone may reproach me for the insufficient accuracy of the assembly of the axles, and as a result, the large required force on the Z-shafts.
I will answer - with the printer turned off, turn the right / left shaft by hand - what will happen to the free one?
That's right, for most it will remain motionless, but for me, when connected in parallel due to self-induction, the second shaft also spun.
Yes, about the shafts - usually, the Graber is designed for Hozmag threaded studs m5 with a pitch of 0.8mm.
They should be lubricated with any paste-like grease for bearings - CV joint, "blue" for needle bearings, graphite and hot grease!
In general, you are on your way to your grandfather's garage / car market, or even better, take lubricant from moon rover bike chain.
Of course, you can also buy the glamorous white Molycote-DX, but this is a matter of taste.
Yes, here the "Martian rule" saved me for the first time - I screwed up the sockets of the nuts of the left carriage of the Z axis Almost ran to buy 3D plastic X/Z carriages and "regular" trapezoidal studs/nuts But no, it turned out that you can throw away the extra / incorrect pads, and nuts on m6 are perfectly clamped between the elements of the plywood carriage: By the way, there were no stainless steel studs in the local hardware store - I took ordinary, galvanized ones. Filed off the threads a bit so they fit into 5mm sockets and bingo! The advantages of such tuning are a normally considered thread pitch of 1mm and the fact that not a threaded part, but a cylindrical part is clamped into the stepper sleeve! Yes, I recommend reaming the mounting holes of the Z-axis motors with a 5-bit drill before assembling - the distance between the guide and the threaded stud varies slightly in mounting and carriages! As a result, this leads to the fact that when moving along the Z axis, the upper ends of the pins move in a circular orbit, and the extruder shakes. In general, you need to select the position of the motors so that the pins remain on the same axis when the axes rotate (via the printer menu). In addition, many mounting holes were reamed, because the sockets in the plywood of my version of the printer are cut out for the M5 nut. Don't forget to press down on the plank when drilling from the back side, otherwise chipping of the plywood can be catastrophic. In a word, the base of the body is assembled on five-millimeter bolts!!! Yeah, and the notorious left carriage is generally assembled on screeds: The fact is that with 6mm studs and 4 fastening screws, a touch was found on their threaded parts. I didn't use 3mm screws and hope for half a millimeter, but used zip ties. This is a truly unique fastener that has replaced the wire used in the past. The only thing that screeds cannot withstand is water hammer in the country water supply. So if you're going to Mars, grab more zip ties! Now let's move on to the control board itself, or rather to the stepper motor drivers and their settings. Let's talk more specifically about the fight against noise. Someone puts expensive TMC2100 drivers in "silent" mode (by the way, you need only two of them - on the X and Y axes) But it's really all about psychoacoustics: And now let's calculate - with a microstep of 1/16, a carriage speed of 60 mm / s and a 20-tooth gear with a 2 mm belt pitch, we get a frequency of 4800 Hz !!! OMG! This is the same peak frequency of perception! Is it possible to double the microstepping (and at the same time the current in order to avoid skipping steps) by installing a DRV8825? thereby shifting the frequency range upwards. And you can show the noise of the middle finger Of course, you can completely remove the microsteps, and stop at the positioning accuracy of the X, Y axes of 0.2 mm. For most tasks, this is enough, the printer will start to "bass" at 300Hz. But it's all about individual preference and sound perception - experiment with a smaller microstep divider and find your comfortable frequency! Where the DRV8825 really comes in handy at 1/32 micro pitch is the standard MK8 extruder! If we calculate that with a 1.75mm filament and an 11mm toothed roller, on a standard 0.4mm nozzle and a 16 divider, we get a 0.2mm column of plastic per step!!! This replacement is justified only after adjusting the pressing force, extruder temperature, plastic type and stepper motor current! If you cannot ensure that the feed system operates normally without clicking and with less than half the nominal current on the stepper, this path is not suitable. Then you should either print a gear feed system or buy a "Titan", which will contradict the "Martian Rule". Has the quality improved from such tuning? At least the supports began to separate without excessive effort, which is already an indicator. To print gears and other parts of the RepRap system (partially self-reproducing printer), a certain print quality is required. But having reached it, the need for the above paragraph disappears. OK, the second most important part after assembly/adjustment of the X/Z axis is the print table!!! Here I am not against plywood, but not for it either! Maybe the proximity of the heating element, even if it was covered with thermal insulation, was influenced by the fact that I did not paint the plywood base with silver, or maybe three bearings instead of four. In general, the level of the table walked constantly, unpredictably and by 0. And if it weren't for the "Martian Rule", an auto level would have been bought. In a word, armed with a grinder, I built a table for 4 bearings from an aluminum-polyethylene-aluminum sandwich: Now the table walks no more than 0.05 mm (I checked it with probes to adjust the valves) and I don’t even correct it for the layer 0.20/0.30 mm. Yes, the springs are mega-rigid, I took brass adjusting screws from the same table as the upper support / spring guides. And the glass of the table, it is 4 mm, because this is its main rigid element (the 1.5 mm textolite of the heater "walks" and bends as it wants). Clamps should preferably be placed as close as possible to the corners, but this interferes with the control/adjustment of the gap! And yes, my axles turned out to be longer, I didn’t cut them, but fixed them with ties - it’s more reliable! Print area is 190x180x180 (XYZ). Of course, you can radically redo everything (make the table lower, change the fastening of the belt on it, otherwise position the extruder), but for now it suits me. And a few words about firmware - I counted 8 different names, but I tried only three: At first I grabbed the second version of Marlin, hoping to switch from Arduino Mega to Due, which has been gathering dust in the box for a long time, but the firmware is heavy both during compilation and for the 8-bit Atmega2560. Then stuck with engines in Repetir. Teacup considered between glasses of tea - not ours how to quickly launch the 2004 screen - gave up this idea. Well, I returned to Marlin version 1.1.9, downloading separately examples of firmware from github. I came up with a fresh version from Aliexpress's Prusa_i3_MKS_Gen_2Z_V1.2, set only my table sizes, steps and inverted the Y direction. That's basically all my notes/remarks. Yes, the choice of filament should also be taken responsibly. Don't print out of shit Liberator! Of course, you've probably already bought a roll of ABS along with the rest of the accessories, but it's better to save it for later, and take PETj, coPET or PLA first. I bought coPET right away. The fact is that these plastics are not as demanding in terms of parameters and printing conditions as ABS. Someone even prints with them on printers without heated bed! ABS is good only for the price, but if you print in a living room not under an exhaust hood, the aroma will still be the same. Yes, and they talk about the dangers to health from its fumes, and heating the table to the desired 100-110 degrees Celsius requires titanic patience. By the way, I got the "Zaporozhets" right, up to a hundred So, having printed a skein of filament, I almost ordered a second one, but I found ABS + half the price! On it, the part behaves differently (compared to conventional ABS), the temperature of the table is 90-100 degrees Celsius, and even the first model was still printed, albeit with a tear off of the edges. After that, a hood with a carbon filter was built, a new coil holder and blowing the RAMPS power transistors. And even the edges of the parts began to stick better. It would seem that ABS + is an absolute plus, but no! On the third model, the edges of the part rose along with the 4mm glass, which predictably burst in the middle!!! Maybe the fault was a glass defect, but somehow I didn’t want to check it. Therefore, my choice is PET-plastics (PETj, coPET and others like them) - the table can not be heated at all (when using a regular PVP-based glue stick). I heat it for the first layer to 75 degrees Celsius, then - 70 in order to avoid peeling high parts.
jumper by moving to a 1/4 microstep.
2 mm!
accelerates heats for 10 minutes, up to 120 - nothing.
Learn more