Is it possible to 3d print metal
Can 3D Printing Use Metal? (Everything You Need To Know)
Yes, it is possible to 3D print items from metal. There are several manufacturing processes which fall under the heading of metal additive manufacturing, but this article concentrates on those which use layers of metal powder to build up and form complex structures that may be difficult to create with other techniques.
The metal 3D printing process involves sintering or melting metal powders directly, or combining them with a second material to allow delivery through a nozzle. It is used for both rapid prototyping and finished production parts for aerospace, mechanical engineering, tooling and more.
Contents
Click the links below to skip to the section in the guide:
- What metals can be used in 3d printing?
- What metals cannot be 3d printed?
- What processes can be used to 3D print metals?
- Other techniques
- Advantages and disadvantages
- What is the purpose of 3D metal printing?
- Is it expensive?
- Conclusion
A wide range of different metals can be used in powder form to manufacture parts through 3D printing. Titanium, steel, stainless steel, aluminium, copper, cobalt chrome, titanium, tungsten and nickel-based alloys are all available in powdered form for 3D printing, as are precious metals like gold, platinum, palladium and silver.
These different metals offer various properties, making them suitable for a range of applications. For example, stainless steel provides excellent corrosion resistance, making it ideal for printing pipes, valves and steam turbine parts.
Theoretically, any metal can be used for 3D printing if it is available as a suitable powder. However, materials that burn rather than melt at high temperatures cannot be processed safely by sintering or melting, but can be used when extruded through a nozzle for 3D printing. Wood, cloth and paper cannot be 3D printed using these processes.
It is also possible to use sintering (forming inside a mould at high temperature and extremely high pressure) to create solid items from metal powders and, in the case of those metals with very high melting points, sintering is the only reliable method to manufacture items from these materials.
As hinted above, there are several technologies for 3D printing metals. Powder bed fusion techniques, which include Direct Metal Laser Sintering (DMLS), SLM (Selective Laser Melting) and EBM (Electron Beam Melting), are the more widely used techniques for metal additive manufacturing:
Direct Metal Laser Sintering (DMLS)
This commonly used method uses a laser to sinter metal powder layer-by-layer to form an object. The process does not actually melt the metal and is used for prototyping and manufacturing finished parts including medical devices and instruments.
Selective Laser Melting (SLM)
This process involves using a laser to melt the material where required within a layer of powder in an inert gas environment. This proceeds layer by layer for creating objects with similar parameters to those produced with casting. SLM is often used to manufacture parts from aluminium and titanium, including those for the medical, automotive and aerospace industries.
Electron Beam Melting (EBM)
This process is similar to SLM, except an electron beam is used to melt the material rather than a laser. EBM is perceived as being faster and more precise than SLM and is often used to manufacture items from cobalt and titanium. EBM is widely used by the aerospace industry for items including engine components.
There are other techniques that can or have been used for 3D printing metals, although these are not as widely used as DMLS, SLM or EBM:
Laser Metal Deposition (LMD)
LMD is used in the aerospace, automotive and medical industries, creating objects by depositing heated metal on a metallic substrate layer-by-layer. LMD allows different materials to be used to build an object and is faster than other methods
Selective Laser Sintering (SLS)
Similar to DMLS, this process also uses a laser to sinter powdered materials. It has been used to manufacture items from a wide range of materials, including metal. However, these days it is mostly used for sintering plastics, such as polyamide and nylon
Binder Jetting
This process uses a special liquid to bind the powder material and is less expensive than DMLS, SLM or EBM. The accuracy and strength afforded by this process are not perfect and post-processing is often required. Hot isostatic pressing can be used to improve the strength and solidity of the finished object, but this increases the costs. Binder jetting is typically used for the manufacture of large scale and complex prototypes
Metal Injection Moulding
This combination of injection moulding and 3D printing is widely used for making small components in industries including medical and defence. The process works by mixing metal powder with thermoplastic and wax binders. This mix is heated until the binder melts and covers the powder, which is then granulated into pellets. These pellets are heated and injected into a cavity to form the object before the binder material is removed, usually via solvent extraction. The part is then sintered, evaporating any remaining binder and compressing the object into a dense solid. The object can then be finished as required.
There are a number of benefits and drawbacks associated with 3D metal printing, as follows:
Advantages
- Easy to manufacture items with complex shapes faster than traditional manufacturing methods
- Cheaper than many conventional manufacturing methods for some parts
- Capable of producing precise and highly detailed objects
- Because details can be included at time of assembly, it can save time and money compared to more traditional methods of manufacture
- Complicated forms can be created to create lighter objects without sacrificing strength, making 3D metal printing ideal for automotive, aerospace and space applications
- Very little material wastage
- Multiple parts of a complicated assembly can be combined into a single component, reducing part count and assembly costs
Disadvantages
- Slow to produce parts designed for traditional manufacturing, making high volume production uncompetitive on cost alone
- Powdered metal materials are more expensive than non-powdered metals (e.
g. billet or bar)
- Metal 3D printers can be expensive
- Surface finishing and post-processing of 3D printed parts may be required
- Offers lower precision and tolerance than specialised CNC machining
- Heat treatment may be needed to reduce inner stresses in a 3D printed item, or achieve maximum strength in the metal
- Design of 3D metal parts can be complex and require the services of professional CAD engineers
- The size of parts is limited by the build volume of the 3D printer
The advantages and disadvantages of the process provide an insight into the purpose of 3D printing in metal, showing that it is well suited to manufacturing relatively small, complex parts, including prototypes. It can also facilitate tooling for conventional manufacturing technologies, lowering costs and reducing lead times.
By combining the flexibility of 3D printing with the mechanical properties of metal, this technology has found uses across industry, from inserts with cooling channels through lightweight structures for the aerospace industry, to complex parts to be used in highly demanding environments. Typical uses include fully functional prototyping, creating production tools, tooling for moulds or inserts, housings, ductwork, heat exchangers and heatsinks.
Of course, different metals lend themselves to the printing of different objects, for example:
- Stainless Steel: Perfect for objects that will come into contact with corrosive liquids, water or steam, due to the superb corrosion resistance
- Bronze: Pump impellors and marine propellers, fixtures and more decorative items, such as vases
- Gold: Can be used to print jewellery
- Nickel: Can be used to print turbine engine parts or even coins
- Aluminum: Ideal for metal objects, especially where lightweighting is required, such as with airframe parts
- Titanium: Capable of producing very strong, accurate parts such as medical implants (e.g. hip joints) and other solid fixtures and objects
Different 3D printing techniques use different solutions for industry with different materials and complexity, meaning that the cost of 3D printing in metal can vary substantially. However, most of the cost comes from the 3D printing machines, which can be a large proportion of overall costs for a production run, alongside labour, materials, preparation and post-processing. The requirement for high-quality powdered materials also adds to the cost of 3D metal printing as they are more expensive than non-powdered metals in the same quantities.
As mentioned, printer prices can be high, with costs of several or even hundreds of thousands of pounds, although these prices are comparable to a high quality CNC machine tool of a similar size. As technology and the market size improves, it is expected that the price of 3D printing machines will decrease.
As well as the cost of materials and the printer, there are design costs for the objects to be created. This can involve the need to buy specialist software or hire the services of CAD engineers with specialist knowledge of 3D printing. There are, of course, other labour costs for the operation and maintenance of the machines.
Finally, there are costs associated with post processing of printed parts. This can include cleaning, heat treatment, the removal of support structures and applying coatings to the surface.
3D printing with metal, or additive manufacturing, allows for parts to be made with almost the same strength as regular metal objects.
While it can be expensive and is not well-suited to replacing conventional manufacturing for high volume production of standard items, it is ideal for making smaller, complex items. 3D printing with metals also assists with lightweighting for parts used in industries including aerospace and automotive.
Related Frequently Asked Questions (FAQs)
New filament means you can print metal on any 3D printer
0Shares
You might want to sit down, because this one is exciting. The Virtual Foundry has just launched Filamet™, a new metal infused filament that makes any FDM 3D Printer, a 3D Metal Printer!
Yes, really…
We just got used to the fact that only high-end printers could manage metal and most mortal makers would have to make do with simple plastics. That just changed, you can now print Copper and Bronze on any 3d Printer.
This new filament from the Wisconsin-based company could literally be a game changer, disrupting the current course of 3D Printed Metal. They’ve launched with copper and bronze, but you can expect to see more metals in the near future.
More than just metal.
The Virtual Foundry’s patented process works not only with metal,but they will follow up with 3d printable Glass and Ceramic products over the next 6 months. So maybe you don’t have to upgrade your 3D printer after all and even the most basic desktop unit could become a complete manufacturing facility thanks to this quantum leap in material science.
How does it work? It’s basically a highly infused plastic, just enough plastic to get it through your current printer. Currently this is a mere 11.5%, an amount considered below the theoretical limit only a year ago. The 88.5% of mass that remains is high purity metal powder. The prints can then be simply polished, or more interestingly be post-processed to remove the small amount of plastic. The resulting product is 99+% pure metal, which is as close to pure as many of us will ever need. The Virtual Foundry says they continue to improve the process and expect future versions to be closer to only 8% plastic.
This project surfaced on Kickstarter last year, where it raised 135% of the target funding. The Virtual Foundry, though, has been on a mission to bring metal production to our desktops since before 3D printing was even an option. It worked with cold-casting and electro forming in the old days, but now technology has caught up and 3D printing looks to have given them the answer.
We haven’t got our hands on the finished product just yet. But the big launch at the Hubble Auditorium at Lockheed-Martin suggests that the team has really cracked the code.
“Printer manufacturers have struggled for years to bring metal printing down into the price range of the average individual or small business,” said Bradley Woods, the man behind this technical breakthrough. “Filamet™ takes the opposite strategy. Rather than bring the high-end down, it simply expands the capabilities of current 3D printers.”
“We expect materials to account for a large portion of near-term product innovation in the 3D printing market. Our company offers an immediate solution to producing real and useful metal prints on the desktop 3D printer that you already own.”
Professionalise your home printerThis filament could turn your desktop printer into a rival for the serious commercial machines and could even prove to be better. That’s because metal printers are notoriously slow and a large printer can actually take 48 hours to produce a single print.
So while the end result might be spectacular, it simply might not suit your workflow even if you could afford to have one in your home workshop.
Consumer printers are designed with the average user in mind, so they offer a realistic compromise of price, resolution and speed. With the addition of this metallic filament, then your home 3D printer could become a real manufacturing weapon. We can suddenly make copper and bronze statues and parts without access to a kiln and that could be a maker’s revolution on its own.
Prints can take less than five hours with a consumer printer and this new material is even big news for big business.
Companies are into this too
The technology has attracted big names like Calvin Klein and a company that wants to license the technology to fabricate consumable parts for its facility that 3D prints Uranium fuel cells for nuclear reactors. The technology works with any 3D printer,which means that even commercial companies with several printer scan now opt to use their simpler units for faster, cheaper production.
This opens up so many new avenues and the science itself could be a launchpad for other companies to create their own innovations. We’ve often said that the biggest step forward will come from the materials, but even we didn’t see a company turning today’s printers into complete metal, glass and ceramic production facilities.
We can’t wait to see the products in action and to test this filament for ourselves. If it turns out to be half as good as the claims then it has the capacity to change everything.
http://www.theVirtualFoundry.com & [email protected]
More images at http://www.thevirtualfoundry.com/showcase/
Tags fdmfff Filamet metallic
Nick Hall
Nick is a freelance journalist who has covered the cut and thrust of Formula One and the technical side of the supercar industry for the likes of The Sunday Times, Automobile and Penthouse on these shores, Tatler and The National in Dubai. After finally driving an F1 car there was nowhere left to go, so now he is here!
How metal 3D printers work. Overview of SLM and DMLS technologies. additive manufacturing. 3D metal printing.
Metal 3D printing. Additive technologies.
SLM or DMLS: what's the difference?
Hello everyone, Friends! 3DTool is with you!
BLT metal 3D printer catalog
Selective laser melting ( SLM ) and direct metal laser sintering ( DMLS ) are two additive manufacturing processes that belong to the family of 3D printing using the powder layer method. The two technologies have much in common: they both use a laser to selectively melt (or melt) metal powder particles, bonding them together and creating a pattern layer by layer. In addition, the materials used in both processes are metals in granular form.
The differences between SLM and DMLS come down to the basics of the particle bonding process: SLM uses metal powders with a single melting point and completely melts the particles, while in DMLS the powder consists of materials with variable melting points. nine0014
Specifically:
SLM produces single metal parts while DMLS produces metal alloy parts.
Both SLM and DMLS technologies are used in industry to create final engineering products. In this article, we will use the term "metal 3D printing" to summarize the 2 technologies. We will also describe the main mechanisms of the manufacturing process that are necessary for engineers to understand the advantages and disadvantages of these technologies. nine0002 There are other manufacturing processes for producing dense metal parts, such as electron beam melting (EBM) and ultrasonic additive manufacturing (UAM). Their availability and distribution is rather limited, so they will not be presented in this article.
How 3D printing with SLM or DMLS metal works.
How does metal 3D printing work? The basic manufacturing process for SLM and DMLS is very similar.
1. The printing chamber is first filled with an inert gas (such as argon) to minimize the oxidation of the metal powder. It then heats up to the optimum operating temperature. nine0002 2. A layer of powder is spread over the platform, a powerful laser makes passes along a predetermined path in the program, fusing the metal particles together and creating the next layer.
3. When the sintering process is completed, the platform moves down 1 layer. Next, another thin layer of metal powder is applied. The process is repeated until the entire model is printed.
When the printing process is completed, the metal powder already has strong bonds in the structure. Unlike the SLS process, parts are attached to the platform via support structures. The support in metal 3D printing is created from the same material as the base part. This condition is necessary to reduce deformations that may occur due to high processing temperatures. nine0002 When the 3D printer's chamber cools down to room temperature, excess powder is removed manually, such as with a brush. The parts are then typically heat treated while they are still attached to the platform. This is done to relieve any residual stresses. They can then be further processed. The removal of the part from the platform occurs by means of sawing.
Scheme of operation of a 3D printer for metal.
In SLM and DMLS, almost all process parameters are set by the manufacturer. The layer height used in metal 3D printing varies from 20 to 50 microns and depends on the properties of the metal powder (flow, particle size distribution, shape, etc.). nine0002 The basic size of the print area on metal 3D printers is 200 x 150 x 150 mm, but there are also larger sizes of the working area. Printing accuracy is from 50 - 100 microns. As of 2020, metal 3D printers start at $150,000. For example, our company offers 3D metal printers from BLT.
metal 3D printers can be used for small batch production, but the 3D printing capabilities of such systems are more like those of mass production on FDM or SLA machines. nine0002 The metal powder in SLM and DMLS is recyclable: typically less than 5% is consumed. After each impression, the unused powder is collected and sieved, and then topped up with fresh material to the level required for the next production.
Waste in metal printing, are supports (support structures, without which it will not be possible to achieve a successful result). With too much support on the manufactured parts, the cost of the entire production will increase accordingly. nine0002
Adhesion between coats.
3D metal printing on BLT 3D printers
SLM and DMLS metal parts have almost isotropic mechanical and thermal properties. They are hard and have very little internal porosity (less than 0.2% in 3D printed condition and virtually non-existent after processing).
Metal printed parts have higher strength and hardness and are often more flexible than traditionally made parts. However, such metal becomes “tired” faster. nine0014
3D model support structure and part orientation on the work platform.
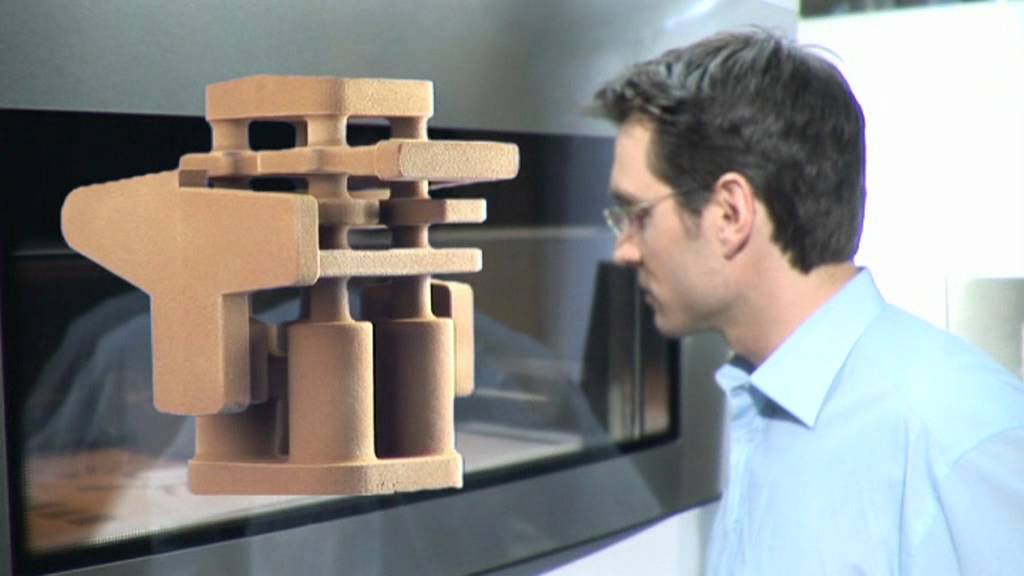
Support structures are always required when printing with metal, due to the very high processing temperatures. They are usually built using a lattice pattern.
Supports in metal 3D printing perform 3 functions:
• They form the basis for creating the first layer of the part.
• They secure the part to the platform and prevent it from deforming.
• They act as a heat sink, removing heat from the model. nine0014
Parts are often oriented at an angle. However, this will increase the amount of support required, the printing time, and ultimately the overall cost.
Deformation can also be minimized with laser sintering templates. This strategy prevents the accumulation of residual stresses in any particular direction and adds a characteristic surface texture to the part.
Since the cost of metal printing is very high, software simulations are often used to predict how a part will behave during processing. These topology optimization algorithms are otherwise used not only to increase mechanical performance and create lightweight parts, but also to minimize the need for supports and the likelihood of part distortion. nine0014
Hollow sections and lightweight structures.
An example of printing on a BLT 3D printer
Unlike polymer powder melt processes such as SLS, large hollow sections are not typically used in metal printing as the support would be very difficult to remove, if at all possible.
For internal channels larger than Ø 8 mm, it is recommended to use diamond or teardrop cross-sections instead of round ones, as they do not require support. More detailed recommendations on the design of SLM and DMLS can be found in other articles on this topic. nine0014
As an alternative to hollow sections, parts can be made with sheath and cores, which in turn are machined using different laser power and pass speeds, resulting in different material properties. The use of sheath and cores is very useful when producing parts with a large solid section, as it greatly reduces printing time and reduces the chance of warping.
The use of a lattice structure is a common strategy in metal 3D printing to reduce part weight. Topology optimization algorithms can also help design organic lightweight shapes. nine0014
Consumables for 3D metal printing.
SLM and DMLS technologies can produce parts from a wide range of metals and metal alloys, including aluminum, stainless steel, titanium, cobalt, chromium and inconel. These materials meet the needs of most industrial applications, from aerospace to medical applications. Precious metals such as gold, platinum, palladium and silver can also be processed, but their use is of a minor nature and is mainly limited to jewelry making. nine0014
The cost of metal powder is very high. For example, a kilogram of 316 stainless steel powder costs approximately $350-$450. For this reason, minimizing part volume and the need for supports is key to maintaining optimal manufacturing cost.
The main advantage of metal 3D printing is its compatibility with high-strength materials such as nickel or cobalt-chromium superalloys, which are very difficult to machine with traditional methods. Significant cost and time savings can be achieved by using metal 3D printing to create a near-clean shape part. Subsequently, such a part can be processed to a very high surface quality. nine0002
Metal post-processing.
Various post methods. treatments are used to improve the mechanical properties, accuracy and appearance of metal printed products.
Mandatory post-processing steps include the removal of loose powder and support structures, while heat treatment (heat annealing) is typically used to relieve residual stresses and improve the mechanical properties of the part.
CNC machining can be used for critical features (such as holes or threads). Sandblasting, plating, polishing, and micro-machining can improve the surface quality and fatigue strength of a metal printed part. nine0014
Advantages and disadvantages of metal 3D printing.
Pros:
1. Metal 3D printing can be used to produce complex custom parts, with geometries that traditional manufacturing methods cannot provide.
2. Metal 3D printed parts can be optimized to increase their performance with minimal weight.
3. Metal 3D printed parts have excellent physical properties, metal 3D printers can print a wide range of metals and alloys. Includes difficult-to-machine materials and metallic superalloys. nine0014
Cons:
1. Manufacturing costs associated with metal 3D printing are high. The cost of consumables is from $ 500 per 1 kg.
2. The size of the working area in metal 3D printers is limited.
Conclusions.
• Metal 3D printing is most suitable for complex, one-piece parts that are difficult or very expensive to manufacture using traditional methods, such as CNC.
• Reducing the need for building supports, will significantly reduce the cost of printing with metal. nine0002 • 3D printed metal parts have excellent mechanical properties and can be made from a wide range of engineering materials, including superalloys.
And that's all we have! We hope the article was useful to you.
Catalog of 3D printers for metal BLT
You can purchase metal 3d printers, as well as any other 3d printers and CNC machines, by contacting us:
• By email: [email protected]
• By phone: 8(800)775-86-69
• Or on our website: http://3dtool.ru
Also, don't forget to subscribe to our YouTube channel:
Subscribe to our groups in social networks:
In contact with
Precision 3D metal printing on order in Sprint 3D
Metal 3D printing - additive manufacturing of metal products, which is rightfully one of the most promising and rapidly developing areas in 3D printing as such. The technology itself originates from the conventional sintering of materials used in powder metallurgy. But now it has become more perfect, accurate and fast. And today SPRINT3D offers you metal printing on 3 D printer on really favorable terms. But first, a little information about the production process itself and its capabilities.
Selective Laser Fusion Technology
SLM or Selective Fusion Technology is a type of direct metal printing that achieves a density of 99.5%. The difference is especially noticeable when compared with models obtained by conventional casting. This indicator is achieved thanks to the introduction of the latest technologies in the hardware part:
- The use of special rollers for compacting powders and, as a result, the possibility of using powders with a particle size of 5 µm.
- Bulk density increase to help compact end products.
- Creates a rarefied atmosphere of inert gases, which ensures maximum purity of the material, no oxidation, and eliminates the risk of introducing third-party chemical compounds into the composition.
But most importantly, the modern 3 D Metal Printer makes it easy to customize the configuration for printing with a specific metal powder. Thus, even with inexpensive material, you can get a first-class result. But only if you use high-quality modern equipment. And here we are ready to surprise you too!
Metal 3D printing B SPRINT 3D
3D printing with own 3D printers
The largest working area is 280x280x350 mm
layer thickness up to 15 microns3D with various types of metals
Delivery throughout Russia and CIS countries
installation for 3 9020 which we use
Production quality is a key requirement that we set ourselves. Therefore, in our work we use only professional equipment with wide possibilities for metal printing. Let's take a closer look at each of the production units. nine0014
Production unit SLM 280HL
SLM 280HL is a development of the German company SLM Solutions GmbH, which uses the technology of layer-by-layer laser melting of powder metal materials. The installation is equipped with a large working chamber and allows you to create 3D objects with dimensions of 280x280x350 mm. Among the main advantages of printing with this installation are:
- Small minimum thickness of the applied layer - 20 microns.
- Filling the working chamber with inert gas, which allows you to work with various reactive metals.
- Print speed up to 35 cm/hour.
- Building layer thickness – 30 and 50 µm.
- Power - 400 W.
A special highlight is the patented powder feed system, which delivers significantly faster print speeds than most production machines in the same price range. We use the following materials in production:
- Stainless steel (domestic 07X18H12M2 (Polema), 12X18H10T and imported 316L).
- Tool steel (imported 1.2709).
- Heat-resistant alloys 08KhN53BMTYu (similar to Inconel 718, produced by Polem) and EP 741 (produced by VILS).
- Cobalt Chrome (COCR)
The SLM 280HL 3D printer can be used to create all kinds of metal components, prototypes and end products. If necessary, we can provide small-scale production. nine0014
ProX 100 production unit
ProX 100 is a compact unit for 3 D metal printing, developed by the American company 3D Systems. It uses direct laser sintering technology, which ensures high speed and precision of production. Among the main characteristics it is worth highlighting:
- The size of the working chamber is 100x100x80 mm.
- Building layer thickness – 20 and 30 µm. nine0219
- Power - 50 W.
ProX 100 allows you to create prototypes that can not be developed by standard methods, provides short lead times, guarantees the absence of material porosity and high part density. In addition, we note the standardized quality of all products, regardless of their structure. At the moment, the model is actively used in dentistry when creating high-precision prostheses, but it has found wide application in other industries:
- Manufacture of engines and their individual parts.
- Development of medical equipment.
- Printing jewelry and even contemporary art.
In printing, we use an alloy of cobalt-chromium KX28M6 (manufactured by Polem), originally developed for additive technologies when creating endoprostheses.
Metal 3D printing - current application
Many experts argue that 3D printing as such has not yet fully revealed its potential. For example, Elon Musk plans to use technology in the colonization of Mars to build administrative and residential buildings, equipment and technology right on the spot. And this is quite real, because 3D metal printing technology is already actively used in various industries:
- The high precision of production and relatively affordable price have made 3D printing very relevant in this industry.
Learn more