Habitat 3d printed house
Habitat for Humanity's First 3D-Printed Home Is the Future of Construction
habitatpgw.org
Founded in 1976, Habitat for Humanity has constructed hundreds of thousands of affordable homes for people who need them. Now, using automated computer technology and a patented concrete mix, Habitat for Humanity recently completed its first 3D-printed house in Williamsburg, Virginia. The house’s new owner, April Stringfield, and her 13-year-old son are excited to move in and make the house a home.
While 3D-printed homes are still relatively rare, the successful completion of the Williamsburg house is a testament to the growing desire to build affordable homes while conserving natural resources like trees.
RELATED: 19 Kit Homes You Can Buy and Build Yourself
It’s a Regular HouseAlthough the walls of the Williamsburg house were printed rather than stick-framed, the home is still just a regular house. In 1,200 square feet of living space, it includes three bedrooms, two full bathrooms, and a covered front porch where Stringfield can enjoy warm summer evenings.
The contractor incorporated traditional siding on the roof gables and used standard bricks on the porch pillars. In addition to the house, Stringfield received a 3D printer that will allow her to print cabinet hardware and light switch covers.
habitatpgw.org
3D Printing Saves on Construction CostsDuring the pandemic, some building material prices doubled or tripled primarily due to supply chain issues, which subsequently drove up homebuilding costs. By using concrete rather than wood, Alquist—the contractor that printed the walls of Stringfield’s new home—saved Habitat an estimated 15 percent per square foot.
While homebuyers do not pay for the labor needed to construct a Habitat home, they do pay for the cost of construction materials. In this way, the money saved on material costs is passed on directly to the buyer.
habitatpgw.org
The Printing Process and Color SelectionIt took just 28 hours to print the concrete walls of Stringfield’s home. Alquist uses a patented concrete mix and impressive-looking extrusion machine to print exterior and interior walls, which are reinforced with steel during the printing process.
Advertisement
Afterward, the exterior walls are sealed with a clear or tinted coating that keeps moisture from transferring through the concrete. Homeowners can choose a standard gray concrete color or select from a range of attractive earth tone hues to give the home a custom look.
RELATED: These Are Some of the Most Architecturally Interesting Solutions to Homelessness
Traditional Construction is Part of the ProcessAfter Alquist finished printing the walls, traditional builders constructed the roof, ran plumbing and wiring, and installed interior flooring and other finishes. Through the Williamsburg chapter of Habitat, contractors, subcontractors, and other volunteers donated their time to complete the remaining parts of the house.
As a Habitat rule, new homeowners must spend some of their own time working on the project, so Stringfield put in 300 hours of sweat equity to make her new home a reality.
While the Williamsburg house is the first 3D-printed home Habitat has completed, it likely won’t be the last. The Habitat buyer program exists to help encourage homeownership for those who need housing but might not be able to purchase a home through conventional means.
Successful Habitat home applicants commit to working on the project or at a Habitat ReStore, and they learn how to budget for mortgage payments and care for their new home. The nationwide nonprofit does not discriminate when selecting homebuyers.
habitatpgw.org
The Future of 3D ConstructionAutomated 3D printing for homes is still in its infancy. However, computer-constructed homes are already being built and sold to the general public, such as this 3D-printed house located in Riverhead, New York. In most communities, however, standard construction is still the name of the game and will likely remain so for the foreseeable future.
Stringfield is thrilled with her new home, and she told CNN how thankful she is to have a home with a backyard where her son can play and her puppy can run.
Advertisement
Live Life in 3D - Habitat for Humanity Peninsula and Greater Williamsburg
Live Life in 3D - Habitat for Humanity Peninsula and Greater Williamsburg Live Life in 3D3D Printed House Project
Alquist, a 3D printing home construction company, and Habitat for Humanity Peninsula and Greater Williamsburg have partnered to build a 3D printed home in Williamsburg. The project represents Habitat for Humanity’s first completed 3D printed home in the country.
This partnership between Alquist and Habitat for Humanity Peninsula and Greater Williamsburg is a step forward in addressing the lack of affordable homes in the U.S.
Alquist uses concrete to 3D print its homes, saving up to 15% per square foot in building costs based on preliminary estimates. Concrete also confers additional long-term savings because it better retains temperature, saving on heating and cooling costs. It is resistant to tornado and hurricane damage.
This 3D home will be approximately 1,200-square-feet, with three bedrooms and two full bathrooms. Every new home built by Habitat for Humanity Peninsula and Greater Williamsburg is EarthCraft certified. EarthCraft is a voluntary green building program that serves as a blueprint for healthy, comfortable homes and works to both reduce utility bills and minimize environmental impacts.
Construction of each home built by Habitat for Humanity Peninsula and Greater Williamsburg is a cooperative effort between volunteers, house sponsors, and the buyers of the home. Participating families provide at least 300 hours of work toward building their own and other families’ homes, called sweat equity.
Once completed, this home will be sold to April and her family of two. Although April has worked at a local hotel for almost five years supervising the laundry facilities, her income is still less than 80% of the area median income, which has made it difficult to save enough to become a homeowner.
Once construction is complete, and thanks to Habitat’s homebuyer program, April’s home purchase will result in monthly mortgage payments of no more than 30 percent of her income, including her real estate taxes and homeowner’s insurance.
The U.S. gravely needs homes that are affordable because of the housing shortage caused by the pandemic, climate change, and economic migration. Bidding wars have pushed entire populations out of the housing market. In fact, for every $1,000 increase in the price of a home, 153,967 families are priced out (National Association of Home Builders). Skyrocketing lumber prices (300% since April 2020 – NAHB) have increased the average price of a single-family home by almost $36,000. This puts new houses out of the purchasing range of more than 5.5 million families.
Each Alquist home comes equipped with Virginia Tech’s proprietary Raspberry Pi-based monitoring system, which monitors the indoor environment, provides security and emergency management, optimizes energy consumption, and analyzes occupant comfort and space utilization. Alquist’s future projects include 3D printed homes in rural communities in Arkansas, California, Iowa, North Carolina, North Dakota, Pennsylvania, and others.
We help as many families as we can, but the lack of decent and affordable housing remains a critical problem in our area. By donating, you will provide upfront funding for building materials and services that makes interest-free loans to Habitat partner families possible. Habitat partner families help to build their own homes – alongside volunteers – and pay an affordable mortgage. Your monetary donations enable us to continue building strength, stability and independence for future local families.
Media
Meet April, the 3D Printed Habitat Homebuyer!
Watch Construction Begin on the FIRST 3D Printed Habitat Home on the East Coast!
Watch a Sample Video of the Printer in Action!
DOWNLOAD PACKET
3D House In the News
Virginia family gets keys to Habitat for Humanity’s first 3D-printed home in the US
December 25, 2021
Habitat For Humanity creates its first 3D-printed home
December 27, 2021
How 3D printing can be the solution to the nation’s affordable housing crisis
January 4, 2022
See Inside Habitat for Humanity’s First 3D-Printed Home—and the Future of Construction
January 14, 2022
‘Like a Dream Come True’: Habitat for Humanity Completes First 3D-Printed Home
January 13, 2022
Habitat for Humanity is 3-D-printing houses. The first one is in Virginia
January 7, 2022
Habitat for Humanity Just Unveiled Its First-Ever 3D-Printed Home
January 6, 2022
Habitat for Humanity Debuts First Home Entirely Constructed Via 3D Printer
January 3, 2022
Virginia Family Buys First Habitat for Humanity 3D-Printed Home
December 29, 2021
Habitat for Humanity hands over the keys to their first 3D-printed home
December 28, 2021
Habitat for Humanity sells its first 3D printed home
December 27, 2021
How 3D printing could play a role in housing in the future
December 24, 2021
Searching for affordability, Habitat for Humanity unveils 3D-printed house in Williamsburg
December 22, 2021
Habitat For Humanity and April Springfield Celebrate the Completion of 3D-Printed Home
December 22, 2021
Alquist And Habitat For Humanity Unveil 3d-printed Home In Virginia
December 21, 2021
‘My dream come true:’ James City resident moves into first 3D-printed home in the country
December 21, 2021
First owner-occupied 3D printed home on East Coast
December 21, 2021
Habitat for Humanity unveils 3D-printed home in Williamsburg
December 21, 2021
First 3D-printed, owner-occupied home in US to be unveiled
December 21, 2021
First owner-occupied 3D printed home on East Coast
December 21, 2021
Williamsburg woman moves into 3D printed Habitat for Humanity house, first in U.
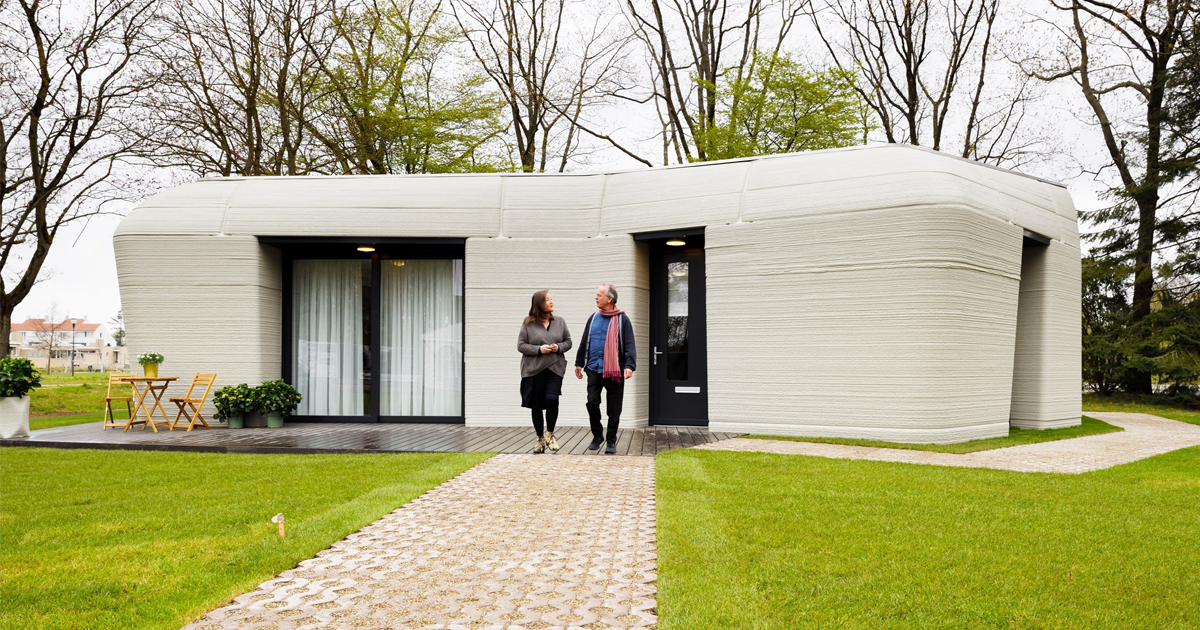
December 21, 2021
Habitat for Humanity Making Progress on Williamsburg Home Built with 3D Printer Technology
September 24, 2021
Habitat For Humanity To Raise Funds For 3D Printed House
September 16, 2021
Habitat for Humanity builds 3D-printed house in Williamsburg
August 31, 2021
Habitat for Humanity Is Now 3D-Printing Houses — and This Family of Two Is Moving Into One (Exclusive)
August 11, 2021
James City County family set to receive first Habitat for Humanity 3D printed home on East Coast
July 26, 2021
Habitat for Humanity is creating a 3D printed home for a family of 3 in Virginia
July 18, 2021
A 3D-Printed Home is Coming to Williamsburg
July 8, 2021
Habitat for Humanity and Alquist partner for the East Coast’s first 3D-printed Habitat home
July 7, 2021
Read an article about the first 3D printed houses?
3D printing has been used in construction for several years now. In this article, you will learn about the first real houses printed on 3D printers.
3D printing of houses is still quite new to the layman. While construction 3D printing technologies have been developed for many years, only a few "real" projects have already seen the light of day. We are still far from technology taking over conventional construction methods. But with each new project, she is getting closer to becoming mainstream.
There are many benefits to 3D printing. For example, the cost of a 3D printed house can be much lower. And it will take much less time to build.
In order to draw a line under what has already been achieved in this area and show some interesting projects, we have devoted an article to the "first" and the best. These projects will always remain milestones in the 3D construction printing industry as they set the stage for future advances in the field.
First 3D printed house in Germany
Germany is a country often associated with cutting edge engineering, so let's start our list with Germany's first ever 3D printed house.
The house itself is located in Beckum, a city that is partly located in North Rhine-Westphalia, next to Holland and Belgium. This is the first 3D printed house to be fully certified to official building codes. This project will give way to many other 3D printed construction projects in Germany as well as the rest of Europe.
The project is the result of a collaboration between German construction company Peri and Danish construction 3D printing firm COBOD. Peri is a large corporation that operates not only in Germany, but throughout the EU. Its portfolio includes many products, including scaffolding and formwork solutions that every construction site needs.
Peri followed the construction 3D printing segment for years before acquiring a stake in COBOD in 2018. Now they are pushing the technology together and further. The construction of the house in Beckum began two years after the acquisition of the share.
For 3D printing at home, a BOD2 modular 3D printer from COBOD was used. The printing itself took just over 100 hours.
• Built: (started) September 17, 2020
• Commissioned: summer 2021
• Where: Beckum, North Rhine-Westphalia, Germany
• By: Peri, COBOD
First occupied 3D printed home in the US
Several homes have been printed in the US, but this home is the first officially occupied home, according to CNN. Its creators: the construction company Alquist and the humanitarian organization Habitat for Humanity Peninsula.
From a distance, you might think that this is an ordinary house. However, when approaching it, the layered structure of the concrete walls becomes noticeable. After all, 3D printing creates an object in layers.
Surprisingly, the 111.5 square meter concrete structure of the house (was printed in about 12 hours, significantly faster than traditional construction methods would allow.
The house was reportedly purchased by April Springfield, who lives there with her son and dog She bought the house through Habitat for Humanity's housing program, and given that the nonprofit's goal is to help solve the global housing crisis, it makes sense to use 3D printing to create affordable homes that will make many people's dreams of home ownership come true. 0005
• Built: 2021
• Commissioned: December 22, 2021
• Where: Williamsburg, Virginia, USA
• By: Alquist 3D, Habitat for Humanity Peninsula, Greater Williamsburg
The first five-story 3D printed house
This project, made by the Chinese company WinSun, is a real record holder. It is a 3D printed five-story residential building with a height of 10 meters - the tallest 3D printed building so far.
The house is located in Suzhou Industrial Park in Jiangsu province in eastern China. It stands next to a mansion that was also built by WinSun using a concrete 3D printer.
Looking at the WinSun designs, you can't help but notice that they don't look like they've been 3D printed. Usually 3D printed structures are gray in color, the layer lines are clearly visible. But WinSun adds color and makes walls smoother. Nowhere is it stated how the company achieves the smoothness of the walls, but we assume that the workers smooth them by hand. WinSun projects are not like the ones we're used to.
• Built: Winter 2014
• Commissioned: Not specified
• Where: Suzhou, Jiangsu, China
• By: WinSun
First 3D printed biodegradable house
Can you guess that there is rice in the walls of this house?
Most 3D printed buildings are made from concrete mix. But this project is different from the rest. With the aim of creating housing solutions with little to no environmental impact, Italian company WASP 3D printed Gay's house using soil and agricultural waste.
WASP developed the sustainable blend in collaboration with Ricehouse, a company that specializes in using natural and agricultural materials such as clay and rice in construction.
The house is named Gaia in honor of the ancient Greek goddess of the earth. In fact, 25% of the mixture contains local soil, 10% hydraulic lime, 25% rice husks and 40% crushed rice straw (a by-product of rice production at harvest).
An innovative solution not only in terms of material, but also in the design of the walls themselves. The specific corrugated structure was used to provide ventilation on warm days as well as insulation on cold periods, virtually eliminating the need for air conditioning.
Gay's house is small - about 20 square meters. The wall printing took only 10 days, while the estimated materials cost is just under $1,000.
• Built: not specified
• Commissioned: October 7, 2018
• Where: Massa Lombarda, Ravenna, Italy
• By: WASP, Ricehouse
AirBnB's first 3D printed house
The perfect weekend getaway.
You can find many different types of accommodation on AirBnB, but what about a 3D printed home?
The so-called Fibonacci house is the first 3D printed house to be offered for booking through AirBnB. Considering that it is located in rural British Columbia, it will be a wonderful place to stay.
Although the Fibonacci house looks small, it has a lot to offer vacationers. About 35 square meters is enough to accommodate up to four people.
The concrete walls of the house were designed and printed by Dutch 3D printing firm Twente. 20 concrete parts were produced offsite in just 11 days. The material was produced by Laticrete. The parts were later transported and assembled at their current location.
• Built: 2020
• Commissioned: Not specified
• Where: Kootenays, British Columbia, Canada
• By: Twente Additive Manufacturing
First 3D printed houseboat
Prvok is not only the first 3D printed house in the Czech Republic, but the world's first floating 3D printed house on a pontoon.
The project was implemented by the start-up company Scoolpt. The concrete structure of the houseboat took only 22 hours to print.
Approximately 43 square meters of living space divided into bathroom, bedroom and living room with kitchen. Weight isn't usually discussed in the context of houses, but given that this one is on water, it's interesting to note that Prvok weighs 43 tons.
The house is equipped with a built-in recirculating shower and tanks for drinking and municipal water and has a service life of at least 100 years.
• Built: June 2020
• Commissioned: August 18, 2020
• Where: Prague, Czech Republic
• By: Scoolpt
Europe's first 3D printed residential house
Not every 3D printed house has visible line layers.
More often than not, 3D printed houses are demos made to show what the technology can do. For most of them there is no information about the actual residents. But in 2017, the couple did move to live in a 3D printed house located in Nantes, France. Thus, the house of "Yanov" became the first of its kind, which was inhabited in Europe.
The house is a project of the University and the Laboratory of Digital Sciences of Nantes. An interesting aspect of the project is the special technique used in its construction by BatiPrint3D. Instead of 3D printing a concrete structure, the robotic arm created wall shells using polyurethane, a material used for insulation. Later, these membranes were filled with concrete.
It took a total of 54 hours to print. It took a little over 4 months to complete the construction. Mainly due to the fact that the rest of the components were created using conventional means. House area - 95 square meters.
• Built: 2017
• Commissioned: March 2018
• Where: Nantes, France
• By: University of Nantes, Nantes Digital Science Lab
India's first 3D printed house
This building was built in a couple of days.
India's first ever 3D printed house was completed back in 2020. The project was carried out by construction startup Tvasta, founded by graduates from the Indian Institute of Technology Madras. In fact, the institute's Chennai campus was chosen as the location of the building.
The significance of this project lies in its possible impact on the solution of the housing crisis worldwide and in India in particular. The ability to build such a house within a few days and at a low cost cannot be underestimated.
House 55.7 sq.m. with a spacious layout, one bedroom, combined kitchen and living room.
The concrete structure of the house was 3D printed off site and the parts were later transported and assembled on campus. The foundation, meanwhile, was built using the conventional method of pouring concrete into the ground.
• Built: 2020
• Commissioned: Not specified
• Where: Chennai, India
• By: Tvasta Construction
Africa's first 3D printed house
Back in 2019, in the Moroccan city of Ben Guerir, Spanish firm Be More 3D created Africa's first 3D printed house. The project originated during the team's participation in the Solar Decathlon in Africa. This is an international competition during which teams design and build solar-powered houses.
Be More 3D printed house 32 sq.m. in about 12 hours, took first place and received the title of the most innovative startup.
Be More 3D didn't stop building in Africa and later created the first 3D printed house in Spain and developed its own concrete 3D printer in partnership with several corporations from the automation and materials industries.
• Built: 2019
• Commissioned: Not specified
• Where: Ben Guerir, Morocco
• By: Be More 3D
First 3D printed home for sale in the US
Last on our list is the first 3D printed home for sale in the US.
This house was printed in the same place by SQ4D, a company specializing in the development of robotic building systems. The building was printed with SQ4D's Arcs concrete extrusion system and has a 50-year warranty on the printed structure.
Living area of 130.7 sq.m. with three bedrooms and two bathrooms. There is also a garage for 2 cars.
The house was listed for sale in January 2021 for $299,999. Considering the size of the house and the fact that it is priced 50% below the cost of comparable newly built houses in the same area, the deal is pretty good.
• Built: 2020
• Commissioned: 2021
• Where: Riverhead, New York, USA
• By whom: SQ4D
Translation source: https://m. all3dp.com/2/first-3d-printed-house/
On our website you can choose and order a construction 3D printer for both building construction and small building forms. To do this, go to the catalog of construction 3D printers. "Tsvetnoy Mir" is a reliable supplier of 3D printers with many years of experience, supplying directly from manufacturers and guaranteeing their quality.
Construction 3D printing is waiting for a breakthrough The first construction projects using this technology appeared only in 2014. We are talking, first of all, about the so-called small architectural forms (benches, flower beds, fences). They never even dreamed about building houses. But already in 2015, the Russian startup Apis Cor made a splash - it printed a whole house in the Moscow region. Since then, news about new 3D printed houses has periodically appeared. However, despite the fact that the technology proved to be very promising in terms of the speed of construction of housing and the reduction in the cost of construction, no mass implementation followed.
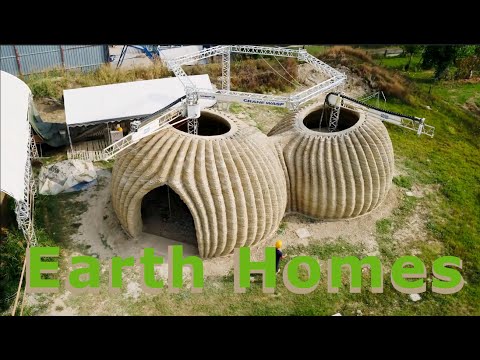
Construction is the world's number one market. And, if many technological innovations are being introduced in the field of high-rise construction, then little has changed in the field of low-rise construction over the past decades. The last 30 years have seen the availability of the Internet, mobile phones, mobile internet, robotics taken to a new level, etc., but when you get to a house construction site, you are unlikely to find many technological innovations. Automation is practically non-existent, and manual labor prevails. 2020 was a test of strength for the whole world, and also led to the highest level of inflation, which, first of all, hit the construction market, there was a dramatic change in prices for metals, cement, wood and much more.
This Internet meme shows what happened to the cost of building materials in just a year. And the process is still going on. At the same time, there is a serious rise in the cost of labor, and there is an acute shortage of it. All this leads to a sharp rise in the cost of building houses. No matter how strange it may sound, statistics show that the growth of automation does not occur when everything is fine, but precisely in crisis situations, during increased competition, reduced demand and the need to urgently look for new technologies to increase production efficiency. So it happened this time, and after some stagnation, construction 3D printing received a new impetus for development.
Preparing to write an article, I turned to the founder of Arkon - Boris Kozlov cu. Arkon was established in 2020 and is engaged in the production of construction 3D printers, both a workshop type for creating prefabs (prefabricated houses) and a portal one capable of printing a two-story house. I asked Boris the key, in my opinion, question:
- Construction 3D printing appeared in 2014, but no mass introduction of this technology followed in 7-8 years. Why do you think this happened, and why is there a surge of new projects right now?
- It seems to me that the reason is the snowball effect.
The technology had to mature, grow from a hypothesis to a pilot implementation, and finally to commercialization and scaling (what is happening now). In addition, it should be borne in mind that construction is one of the most conservative industries, where, unlike even aviation and the automotive industry, there is still an extremely low introduction of digital solutions and automation in the field of the production process itself - the construction itself. The issue of regulation and certification also plays an important role - this process is long and creates an additional lag.
In 2014-2016 the first samples of building 3D printers and prototypes of printed buildings appeared. The concepts of various form factors of construction 3D printers and types of printing materials were tested.
In 2017-2018 in the world, the first notable investments were made in a number of construction 3D printing start-ups. Further, by 2020, these investments "rolled" in the form of reaching a certain level of technology maturity - the first commercial products (3D printers and houses) appeared.
![]()
Finally, in 2020-2022 it became clear that the hypotheses of the effectiveness of construction 3D printing were justified (cheaper, faster, more environmentally friendly), and large investments began in the industry. A striking example is the investment of GE (the French division of General Electric) in the Danish COBOD or the achievement of a capitalization of $ 2 billion by the American company ICON.
In 2022-2023 over 1,000 buildings will be printed worldwide already, scaling from single buildings/pilot projects to entire villages and major infrastructure/reinforced concrete implementations. In addition, in a number of countries, by now, a regulatory framework has been created or is being actively created for the introduction of additive technologies in the construction industry.
Thus, I believe that the specified time period is a fairly natural cycle of technology development, which is likely to experience exponential growth in the next decade.
![]()
According to ResearchAndMarket report, the global construction 3D printing market is valued at US$354.3 million in 2022 and is projected to reach US$11068.1 million by 2027, growing by 99.04%.
Various market processes affect the prices and behavior of participants in the global 3D construction printing market. They create price signals that are the result of changes in the demand and supply curves for a product or service. They can be associated with both macroeconomic and microeconomic factors. Even human emotions can also drive decisions, influence the market, and create price signals.
Now let's take a quick look at what is the construction 3D printer. Without delving too deeply into the technology, we can say that construction 3D printers are very similar to classic FDM/FFF printers that print with plastic, but instead of plastic, the material here is a cement mixture, which is fed directly into the nozzle and forms an object by layer-by-layer overlay. Printers are also portal, on the basis of a flying boom, with a robotic arm.
Pictured left is a construction printer based on a boom. The figure on the right is a gantry construction 3D printer
In the figure above, a construction 3D printer in the form of a robot arm installed on a mobile platform.
Everything changed completely when, in the summer of 2021, the American company ICON, which was trying to introduce 3D printing into the construction of various auxiliary facilities, signed a contract with one of the largest American developers, Lennar, to build a village of 100 houses in Texas and immediately became a unicorn , having received 200 million dollars of investments from several investment funds.
Pictured is a 3D printed house in Austin, Texas. A 3D printed house in Austin, Texas. At the same time, the Danish company COBOD, created by the world's largest construction formwork company PERRI, began selling its gantry 3D construction printers and participating in construction projects around the world. In the photo below, a modern two-story house built in Germany and a school building in Malawi, built in record time with a minimal budget.
There is little that unites developed, developing and poor countries, everywhere their problems and tasks, but the lack of affordable housing is a global agenda . If in poor countries there is an acute problem with the increase in the number of homeless people due to a lack of housing, as such, then in developing countries it is necessary to dramatically accelerate the number of new housing being built to meet the needs of a growing population. In developed countries, the problem is primarily in the cost of housing, which has risen in price to such an extent that it has become practically inaccessible to young people. And with the simultaneous increase in life expectancy in these countries, this problem is only getting worse.
At the same time, the trend towards “green agenda ”, CO2 emission reduction, building with more environmentally friendly materials, etc. is developing. But, unfortunately, so far the construction industry is the absolute leader in CO2 emissions, as well as in the amount of garbage that each construction site leaves behind. This is not to say that construction 3D printing solves all these problems, but at least it is moving in the right direction. Let's look at this with a few illustrative examples.
Today, when we talk about 3D printing houses, we are talking about printing walls. Everything else (foundation, windows, doors, ceilings and roof) is done in the traditional way. 3D printed walls are built as fixed formwork, which significantly saves the amount of cement used , which in turn reduces construction costs and reduces the environmental impact of cement production. In addition, with this method of construction, no additional waste is produced, the strength of the structure does not suffer. It can be reinforced, as shown in the photo on the left, and engineering communications can be immediately laid, as shown in the photo on the right, which also affects the final speed of the construction of the object. At the same time, the total weight of the structure is reduced, the remaining cavities can be filled with lightweight foam concrete, insulation, straw or any other available material. Such a lightweight design can use a lighter foundation. The construction method itself is more economical in terms of material, and therefore environmentally friendly.
eco-concrete with the addition of polymers is currently being actively developed, the production of which reduces CO2 emissions from 30% to 100%. The Apis Cor company mentioned at the beginning of the article, which built a house in the suburbs in 2015, is now based in hot Florida, plans to start using this material in its projects.
Another startup from Russia, Mighty Buildings, headquartered in California, initially relied on a polymer with the addition of mineral chips. And while the company doesn't build entire homes, it only makes wall panels, it has won numerous design awards, as well as a $400 million valuation in several investment rounds.
As a result, with a rough calculation, we can say that the total savings on the construction of walls can reach 30%, and the total cost of the house can be reduced by 10%. This is true for houses designed for conventional construction. And if you initially design with 3D printing, you can improve this ratio by optimizing the laying of communications, the ability to immediately print interior walls, bookmark niches for bathrooms, fireplaces, built-in wardrobes and kitchens, as was done in the house built by COBOD in Germany.
"There are spots on the sun." Despite all the advantages of construction 3D printing, has several significant disadvantages . The main one is layering, which cannot be avoided at the current level of technology development.
The photo above shows the layering of the 3D printed walls.
This task can be worked in several directions:
-
Ribbed walls can be plastered, painted and played with as a design element.
That's how ICON does it in the US, for example their latest project House Zero is done that way and has won a number of design awards.
-
Use special "shutters" on the print head that allow smooth layers, as COBOD and other manufacturers do. The photo below shows that this does not ensure the complete absence of layering.
-
Fully sand the surface to obtain the usual smooth wall for plastering, painting, wallpapering or other finishing. It is possible, but it will require huge labor costs, which can reduce the overall efficiency of using 3D printing.
Pictured above is a 3D printed wall sanded smooth.
The second problem is the required temperature. Ideally, printing should take place at temperatures between +5C° and +30C°. Humidity is also important. Using additives, you can push these boundaries, but not indefinitely. At strong sub-zero temperatures, printing will be possible in the field only if the construction site is covered with a dome and the required temperature is reached inside with the help of heat guns. In conditions of intense heat, it is preferable to print at night. Another solution could be to print the wall panels in the shop and assemble them on site. Of course, each of these decisions will have a negative impact on the economic efficiency of the project.
Building 3D printing can be useful not only for the construction of houses . With its help, you can solve many other problems, and there its disadvantages will not matter. For example, the American concern GE uses COBOD printers to build towers for wind turbines in the shop. Ribbed surface and temperature restrictions in this case do not play any role. Construction takes place in the shop, after which the object is transported to the installation site.
3D printed wind tower. 3D printed wind tower. Construction 3D printing, or, as it is also called, additive construction, has just appeared, and I want to believe in its bright future. There are many prerequisites for this, but a lot still needs to be done for success.
Learn more