3D printer bed insulation
5 Best Ways How to Insulate a 3D Printer Heated Bed – A Guide – 3D Printerly
I was sitting here beside my Ender 3, wondering what the best way to insulate a 3D printer would be. This is especially desired if your 3D prints are taking way too long to heat up, mainly with ABS prints.
Having an insulated bed on your 3D printer is a neat upgrade that has helped out several 3D printer users over the years. Temperature and heating is used all the time with these machines, so this article will look at heated bed insulation and how to install it.
Aluminum insulation mats with foam are a great method to insulate a 3D printer hotbed. They significantly cut heating times, distribute heat more evenly, and keep temperatures more stable which can even reduce warping. Some use cardboard, cork sheets or a basic enclosure to improve insulation.
To install a hotbed insulation square you simple need to attach it to the bottom of your hotbed, making sure it is the correct size for your 3D printer’s bed.
The benefits of having a heated bed are:
- Saves time on heating up your print bed
- More even heat distribution around the bed
- Saves money on having to use more power to heat the bed and keep it hot
- Helps to keep temperatures more stable
- Can reduce warping
Firstly, you need to check how much space you actually have underneath your print bed. Some machines are going to have large gaps which mean you can choose from many options, while others have very little space, so options are limited.
You also don’t want the added insulation to be getting in the way of any parts of your 3D printer, like wires or bearings. Also, since the material will be working with quite high heats, they should have a good amount of heat-resistance to withstand long-term use.
Sticking the insulation material to the bed works in different ways. Some materials have self-adhesives to help stick it down, while others will require a separate adhesive. Good choices in this case are an adhesive spray, or heat-resistance tape.
Materials that 3D printer hobbyists use are:
- FYSETC Self-Adhesive Aluminum Insulation Mat
- Cork Sheets
- Plumber’s Felt
- Cardboard
- Use an Enclosure
Those closed-cell types of foam seem to work really well for most people since they can keep a lot more heat in as compared to something like single-walled cardboard.
1. Self-Adhesive Aluminum Insulation Mat
These lightweight insulation mats work really well to keep your 3D printer beds warm throughout the printing process. Rather than have your print bed overcompensate for a cool room, and require extra heating, we can keep that heat in better.
The Befenybay Self-Adhesive Insulation Mat is a great choice on Amazon, with amazing ratings and it even comes with 2 pieces. They measure up at 220 x 220 x 5mm, or you can get the bigger 300 x 300 x 5mm version if required.
This lightweight foam with aluminum substrate is heat-resistance, durable and has fire prevention properties, allowing it to operate with temperatures from 50-150°C (122-302°F). It’s also waterproof and cold-resistant.
The instructions for this are simple:
- Clean the bottom of your hotbed
- Tear the adhesive backing from the bottom
- Stick onto the bottom of your hotbed
The benefits are also simple:
- Faster warm up
- Keeps temperature stable
- Better prints
- Durable and should remain firmly adhered to your bed
One 3D printer user who had a very slow heating bed of 10-15 minutes for 60°C, used this insulation and managed to cut the timing down to 7-10 minutes. The time saving won’t always be this dramatic, but it should cut down times.
2. Cork Sheets
The good thing about using cork sheets to insulate your 3D printer bed is how dense the internal structure is, being closed-cell as you can tell by the normal make-up of cork.
This is a great material to use for insulating your 3D printer bed, especially if you lack a large amount of space to use for insulation under your bed.
You can find some specially-made Cork Sheets for 3D printers on Amazon with the holes cut out, or you can get a fresh sheet and cut the whole yourself.
Cork is formed with several microscopic bubbles, which works really great as a form of insulation, even used under flooring in many cases.
Some people get cork on a roll after some type of flooring project, you can cut a piece off soak it in hot water, iron it flat, then fit it under your bed.
The better method though, is getting the cork sheets with strong adhesive on one side. One user even added to this by taping aluminum foil to the bottom of the bed with Kaptop tape, then covering the foil with cork.
If you want your bed to heat up faster while pre-heating, you can actually add a sheet of cork or even a cloth to the top of your bed to keep the heat in.
The video below shows the difference in timing to heat a bed up to 120°C before and after insulation with a cork sheet. It took the non-insulated 3D printer bed 18 minutes to heat up, while the insulated bed took just 14 minutes, a difference of 22%.
3. Plumber’s Felt Insulation
This material works really well seeing that it’s used for welding, soldering with an open flame and even brazing. It’s a very high temperature material that you can use to your benefit for 3D printing.
You can get this High-Temp Felt Plumbers Pad from Amazon for a reasonable price. It’s temperature-resistant to a whopping 1800°F (982°C), tear-resistant, while still being a soft, pliable materials.
4.
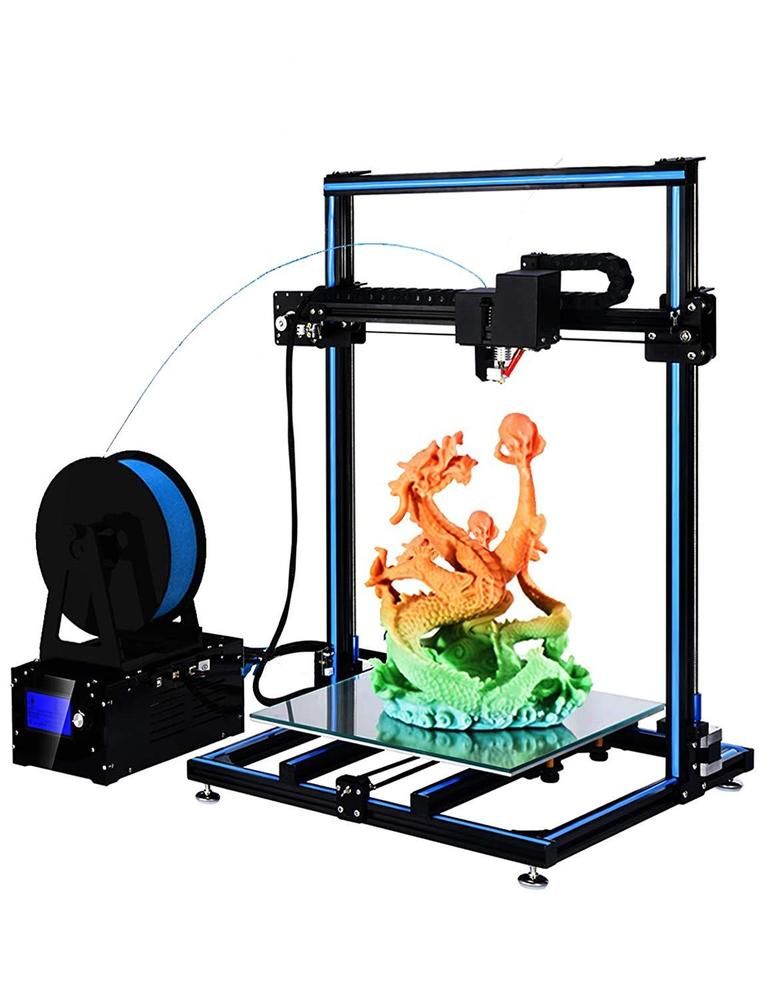
Simple cardboard works surprisingly well for insulating your 3D printer hot bed, specifically double-walled corrugated cardboard wrapped with heat or foil tape. The trapped air bubbles within the cardboard does a good job at retaining heat.
It’s a lot easier to cut to size than other foam and insulation solutions, and the minimum smoke point for cardboard runs at around 392°F+ (200°C+) so the heat from the bed shouldn’t be a bother at all.
You don’t even really have to tape the cardboard down, you can fit a few pieces of cardboard from a box and fit it to the underside of your bed.
Some good heat tape from Amazon is the Equty Baymers Heat-Resistant Tape. It is an easy-peel solution and has a maximum heat-resistance of 482°F (250°C).
5. Use an Enclosure to Keep in the Heat
A solution that not many people actually use on their open-style 3D printers is using a good, airtight enclosure. You don’t realize how much enclosure help to keep in heat until you really start to implement one yourself.
When you use one of the above insulation solutions, along with a good quality enclosure, you can really retain plenty of heat within your 3D printer, saving you time on heating and using less power overall.
The Creality Fireproof & Dustproof Enclosure from Amazon is a great choice to insulate your 3D printer. It’s very highly-rated, with a rating of 4.6/5.0 at time of writing, and does a great job keeping a stable temperature.
The installation is quick and easy, with the ability to fold it for simple storage. You can easily reduce dust build-ups and reduce the overall noise of your 3D printer with this enclosure.
3D Printer Heatbed Insulation: Is It Worth It?
I am constantly talking about heatbed insulation in my reviews, and how a simple and cheap piece of insulating material can have a big impact on power consumption and bed temperature uniformity. I am also posting power draw measurements for the exact same reason.
In this article, I will do a practical test where I test the differences between the heated bed from the Voron Trident 350 with and without insulation. This should give you a better understanding of how this insulation material impacts the way your printer works.
Test Printer and Testing Methodology
For this test, I used the FYSETC Voron Trident 350 printer I recently reviewed. I think this is a good candidate for the test because it has a large print surface, it also has a thick magnetic sticker applied with a PEI flex plate and the thick aluminum bed has some thermal mass.
The thermal measurements were made with the FLIR Camera installed on the CAT S62 Pro and for measuring the temperature inside the chamber, I used a simple thermal probe that came with my multimeter.
The probe was located just over the top of the Afterburner extruder with direct visibility to the bed. Also note that my Voron Trident 350 is not completely enclosed. I didn’t print the air filter duct which sits at the top of the machine.
To measure the power consumption, I used a Blitzwolf smart power socket which indicates the power draw in real-time and also measures the power draw for a single day.
All the measurements were done at a 22C environment temperature.
I used this 400x400mm heatbed insulation material which I cut to size, and partially sculpted so it fits around the aluminum extrusions for the bed. Not my best work, but it’s good enough.
Print Surface Temperature without insulation
60% power
Heating the bed to 100C takes 12 minutes with 414W of power drawn from the wall. The surface of the bed only reaches 84C at the highest point even though the thermistor reports 100C and the heat distribution is not good with temperature differences up to 12C.
After 30 minutes, the print surface reaches 91C which is still 9 degrees lower compared to the set temperature. You can also see that the temperature distribution across the print bed is not as expected, even after waiting for 30 minutes.
100% power
Heating the bed to 100C takes 3 minutes and 15 seconds while drawing 630W of power from the wall. The surface of the bed only reaches 71C at the highest point even though the thermistor reports 100C and the heat distribution is not good with temperature differences of about 16C.
After 30 minutes, the print surface reaches 93C which is 7 degrees lower compared to the set temperature. You can also see that the temperature distribution across the print bed is not as expected, even after waiting for 30 minutes, but pretty close to ideal.
Print Surface Temperature with insulation
60% power
After insulating the bed, I set the power to 60% and started the heating test again.
Heating the bed to 100C takes 9 minutes and 20 seconds with 435W of power drawn from the wall. The surface of the bed only reaches 82C at the highest point even though the thermistor reports 100C and the heat distribution is not good with temperature differences up to 12C.
After 30 minutes, the print surface reaches 91C which is 9 degrees lower compared to the set temperature. You can also see that the temperature distribution across the print bed is not as expected, even after waiting for 30 minutes.
100% power
Heating the bed to 100C takes 4 minutes and 45 seconds with 630W of power drawn from the wall. The surface of the bed only reaches 73C at the highest point even though the thermistor reports 100C and the heat distribution is not good with temperature differences up to 17C.
After 30 minutes, the print surface reaches 91C which is 9 degrees lower compared to the set temperature. You can also see that the temperature distribution across the print bed is not as expected, even after waiting for 30 minutes.
Power Consumption after 1 hour ABS print
To get an accurate reading of the power draw during operation, I sliced a 200% calibration cube with settings that take 1 hour, which was printed in ABS with 250C for the hotend and 100C for the heatbed. The same G-Code was used for both tests.
Without insulation
Before the bed was insulated, the power draw ranges from 210W to 275W. After a 1 hour print, the printer used 0.24 KWh. This means that a 24-hour print will use about 5.76 KWh.
With insulation
After the bed has been insulated, the power draw during printing ranges from 161W to 280W. After 1 hour of printing, the printer used 0.15 KWh. This means that a 24-hour print will use about 3.6 KWh.
Changes in the Bed Mesh Variance
Without insulation
Before installing the bed insulation material, the Bed Mesh Variance was at 0.288mm.
With insulation
After installing the bed insulation material, the Bed Mesh Variance was at 0.330mm.
As you can see, there is a change in the bed mesh, but for me it is insignificant and it’s easy to compensate for that during printing. We also need to remember that we are dealing with a 3D printer, not with a super high-precision machine.
Enclosure temperature
Without insulation
The enclosure temperature after the 30 minutes heating time reached 45C.
With insulation
The enclosure temperature after the 30 minutes heating time reached 48C.
As a bonus shot, I also took a picture during the 1 hour ABS print to showcase how the hot air rises and is trapped in the printing area. So there is no reason to be concerned about the temperature inside the printer, for the Voron Trident.
This might be an issue for a Voron 2.4 which has the bed fixed on the bottom of the enclosure where the air will be cooler. The enclosure temperature will also be different according to the fan speed set on the exhaust.
Conclusions
After doing these tests, I’ve reached the following conclusions:
- For this specific case, the Voron Trident 350 only benefits from having a bed insulation material installed when it comes to power efficiency.
Other printers with thinner heated beds benefit more from this.
- The temperature on the print surface is mostly the same, with or without the bed insulation material, and should be compensated by adjusting the slicer settings. Of course, this applies if you have a magnetic sticker applied to the aluminum bed. If you have magnets embedded, then this is probably not needed.
- Enclosure temperature does not change significantly and you can get 45-50C when printing ABS without any issues. Higher temperatures could be reached if more insulation is applied for the sides of the printer, but I don’t think that’s needed, especially for ABS.
- Bed Mesh Variance changes a bit after installing the bed insulation material, but the change is not significant in my opinion and the printer can compensate for that. This might be different for other people depending on the quality of their aluminum bed.
- Using 100% power doesn’t actually help because the aluminum bed cannot absorb the heat efficiently.
The heater will reach the set temperature and will stop heating even though the aluminum bed didn’t reach it, making the heating process take longer. It usually takes about 10 minutes for the aluminum bed to reach a temperature close to the one set in the printer settings.
In my opinion, installing a bed insulation material is well worth the effort for any kind of printer. The power draw will be lower saving you money over time which would be otherwise spent on paying for electricity.
But what do you think? Feel free to join the discussion about this topic on the 3DPrintBeginner Forum.
Liked it?Consider supporting 3DPrintBeginner if this content helped. You can also join Patreon for exclusive perks! |
Sunhokey Prusa i4 - we replace the bed heater
As it turned out during work with the Sunhokey Prusa i4 printer, the bed heater is clearly weak. Not only did it initially heat up to a maximum of 90 ° C, which was later corrected by adjusting the PID controller parameters, but also the heating takes too long - about 10 minutes. Such an outrage could not go on forever, and one day my patience snapped. So it was decided - a more powerful heater is needed.
Fortunately, I was not the only sufferer and here is an excellent description of the process of replacing the heater with a diagram and video.
I will just tell and show how I did it and why everything is done this way and not otherwise.
The main idea of this upgrade is not only to increase the power of the heater, but also to use a 220 volt AC heater as a replacement, instead of the traditional 24 volt heater powered by the power supply.
The regular heater, despite its relatively low power, consumed quite a lot of current due to the low supply voltage, which required a powerful power supply and led to additional heating of the power supply and, as a result, the space inside the case. Increasing the heater power without changing the supply voltage would require replacing the power supply with a more powerful one, which is irrational both in terms of dimensions and financially.
The use of a 220 volt heater made it possible to unload the power supply and reduce the current and, as a result, the thickness of the wires for powering the table and the temperature inside the case.
I saw fears on the net about the use of high voltage, which can be life-threatening in the event of a breakdown of the heater on the device case, but I consider these fears far-fetched. Personally, I have a normal network at home with a machine and grounding in each outlet. The power supply and the printer case are connected to a protective conductor and I do not see any problems even in the event of a breakdown on the case. If you have shitty wiring and no protection, then I can only say that it is worth doing this in the first place, regardless of the presence of a 3d printer.
Keenovo Silicone Heater 500W@220V was used as a heater.
Adhesive base on the bottom, covered with a protective film.
The ends of the wires are not tinned and not crimped, so I crimped them with ferrules.
So, unscrew the table. In my case, there is a scratched and torn insulation, crookedly glued with Kapton tape.
Tear off the tape and remove the insulation. We have a view of the heater. In the middle, under a layer of adhesive tape, there is a temperature sensor that hangs in a bubble between the adhesive tape and the table surface. In general, some kind of pornography. I think there can be no question of any accuracy of heating the table.
With a titanic effort, we begin to tear off the old heater. The process is simple, but peeling off is rather difficult - after all, it is glued over the entire surface. After tearing off the heater looks something like this and I think it can be safely thrown away.
Then we take alcohol (the instructions for the heater indicate that acetone cannot be used) and wipe the table, getting rid of the glue residue.
After the table has been cleaned, start sticking the heater. The process is simple, but you need to do it carefully. It is somewhat reminiscent of sticking a protective film on a phone, but more roughly. Actually, we tear off the protective paper on one side, apply the heater to the table, level it and start pulling the paper from the bottom, ironing the heater to avoid the appearance of air bubbles.
After gluing the table and heater look like this
In the original video, the heater was glued back to front, and the wires were bent and laid along the table. I did not understand the meaning of this action and somehow did not dare to bend the wires, so I glued it differently.
Unfortunately, I don’t have Kapton tape yet (the Chinese let me down and the adhesive tape has been coming to me for 2 months and apparently won’t reach it) to glue the insulation from below, so for now I will use it like that. This is not very good, but I don’t have a choice yet, and the power reserve of the heater allows me not to worry too much about heat losses. But in the plans, of course, to insulate the table from below, for which an additional heater Heating Bed Block Insulation Cotton was also purchased.
Unfortunately, as it turned out, the printer is equipped with an SSR relay, although for 220 volts, but constant current , which I somehow did not pay attention to and kind of burned it safely. At least it doesn't work and the heater is always on. In connection with this misunderstanding, the relay was replaced with the Chinese SSR-25DA, which so far takes care of it normally - at least the heater heats up as it should, and the relay itself is cold.
It was worth it! Heating occurs at a rate of 1-2°C per second, which is very fast. In fact, the table heats up to 110°C in less than a minute. I think after adjusting the PID coefficients everything will be even better. Now, with the coefficients from the old table, there are strong temperature fluctuations during heating, which gradually fade.
I strongly recommend that all owners do this operation and stop wasting time endlessly waiting for the table to heat up.
- https://www.thingiverse.
com/thing: 1755959
5 COOL THINGS ON STEEL ANET A8 - voltNik
Upgraded, assembled and tuned Anet A8
Steel frame for Anet A8 updated mega popular model.
You all probably know the Anet A8 printer, at one time it broke the price bar down and sold tens of thousands of copies. The printer, in fact, had only one significant drawback - it was a flimsy acrylic frame, which did not provide structural rigidity and print quality was average. But today I will show you the upgraded steel Anet A8. There is no acrylic here, absolutely all body parts are made of steel, the printer can even be safely carried right behind the frame. Cases for these printers are manufactured by the Russian company 3DIY. Therefore, if you have an acrylic Anet A8, then you can rebuild it on steel and get rid of the flimsy acrylic construction. Steel will increase rigidity, enable high speed printing, and greatly improve print quality. I printed a calibration cube, printing layers of 0. 1 millimeters. Well, I think you can see for yourself, almost perfect layers of plastic laying. No wobble and minimal waviness on the layers. The print is very high quality. If you are interested, the link to such a frame is in the description of this video. Well, let's print already:
- Vase: I liked this model in the form of two fish and decided to print it. Height 15 centimeters, but I think you understand. The beauty of 3D printing is that you choose the right size by scaling the model in the slicer. Of course, the plastic laying is not airtight, I have known this for a long time - the vase will let water through. Therefore, it is applicable for decor and decoration, well, as an option.
- Crystal: A simple and interesting lamp, it was printed without filling with walls in one layer along the contour to let in more light. Inside there is free space to install the LED and then you get a small night light, or a lamp on the table.
The model, of course, can be increased, then it will be possible to put more LEDs or even a light bulb.
- Fish Skeleton: This model is printed assembled. Those. all moving parts are already closed and there is no need to dock anything. The skeleton turns out to be mobile and not collapsible. It has always amazed me that a 3D printer can immediately print closed movable joints and even movable mechanisms inside a closed case.
- Voronoi Tower: This model is built with a Voronoi surface partition, forming a set of convex polygons like a geometric web. This pattern is used in architecture and design. Well, it occurs regularly in nature. The tower is not large and shows the printer's capabilities when printing complex geometry.
- Dragon lamp: Another interesting model of a lamp with a dragon sitting on it. It is also hollow inside so that you can place the lamp and set it as a decoration on your desktop behind the computer or near the bed.
To make such a lamp, I used an unnecessary USB cable, and simply soldered a 150 ohm resistor with a small LED for plus and minus. It turned out simple and works when connected to the USB port of the computer.
Well, let's talk a little about the printer itself, there is a Direct extruder installed. Cooling is one-sided, with the help of a powerful radial snail fan, but of course it is possible to print both-sided and circular airflow. Hot table covered with glass, there is insulation underneath. The holder for plastic spools is very conveniently made, it is wide and located behind the printer, it will be possible to fit several spools at once and choose among them the type of plastic and color you need. The printer is built on the Arduino Mega platform with a RAMPS 1.4 shield module. Absolutely everything in it is maintainable and interchangeable, there are no unique details.
Modified steel Anet A8 provided for review by 3DIY, they also have steel frames for sale for upgrading Prusa I3, Anet A6, Anet A8 printers and the Bizon version with a larger print area.