Future uses of 3d printing
What does the future hold for 3D printing?
The ultimate goal of 3D printing is to give us a Star Trek-style replicator, where you can order, for example, a hot drink and the machine will assemble it for you, atom-by-atom, explained Marcel Slot – the coordinator of the EU-funded Diginova project – in a Horizon podcast.
However, don’t throw out your kettle just yet. The project forecasts that we’ll have to wait for a while before we can make a replicator.
In the meantime, though, we’ll be able to embed electronic components into 3D-printed devices, create made-to-measure bones using live cells, and in just two decades we’ll be able to start printing our own homes, Diginova believes.
The project brought together 20 research institutes and companies to compile a roadmap to analyse exactly what the future holds for digital manufacturing.
As well as 3D printing, it also looked at digital 2D printing, printed electronics and smart lighting, and how they could converge in future.
‘If you bring these communities together, you start seeing the enormous advantages of convergence of these fields,’ said Slot.
But how long will it be until we have embedded electronics, made-to-measure replacement bones and 3D-printed houses? We’ve brought together some of the best predictions into an interactive timeline looking at what the future of 3D printing could hold:
10 years
Integrated electronics and personalised drugs
Devices will be printed with integrated electronic chips, enabling manufacturers to radically rethink the design of objects. 3D printing technology will also be used to generate a tailored prescription that includes a specific dose.
In the home, advanced 3D printers that can mix metal and plastic will be as common as microwave ovens, while warships and aircraft hangers will also be equipped with 3D printers.
A 3D printer that can embed 3D electronics. Image courtesy of TNO.
15 plus years
Tissue engineering scaffolds and medical microfactories
Scientists will be able to build scaffolds that are designed to fit specific parts of a damaged bone, for example, providing a framework to help the body heal itself.
Medical microfactories would allow hospitals to print on-site, custom-made medical devices such as dental aligners, medical guides or surgical instruments, and replacement organs.
3D-printed bone scaffolding. Image courtesy of BIO-SCAFFOLDS.
Within 20 years
Mega-scale digital fabrication
Two crane-like arms could support a crossbeam that holds a printing head over a construction site.
The device could then print a building layer-by-layer using jets of concrete. Researchers believe the technology would be able to make a two-storey house in just under a day.
On the moon and in space, 3D printers could be used to create components and even print habitats for astronauts.
3D printers could one day build a house. Image courtesy of Diginova.
Decades into the future
The internet of things
3D printing could mean devices that have tiny batteries and sensors built into them. When this can be done for a reasonable cost, it will enable engineers to create an internet of things, where everyday objects can sense their environment and communicate with each other.
A leaf-shaped sonar cell. Image courtesy of Diginova.
Far future
Nanoscale digital fabrication
One day, 3D printers may be able to construct materials atom-by-atom, for example by using carbon atoms to make a lightweight material that is harder than diamond.
The technology could be used to make things like high-power fuel cells, single-molecule sensors, molecular-scale computer circuits and selectively permeable membranes.
Artist's impression of atoms. Image courtesy of Shutterstock/ U. Shtanzman.
At the moment, the biggest problem is that 3D printing, or additive manufacturing as it’s known in the industry, is slow and expensive, and it is mostly used by big companies to make prototypes.
However, things are poised to change. The technology is becoming much better, and cheaper. And on top of that, researchers are developing ways to combine 3D printing with other techniques so that electronics and fibre optics can be embedded within devices.
‘There is another set of new products to be discovered basically which have these features in them, and which are not around at the moment, of course, because they cannot be made via conventional technologies,’ said Frits Feenstra, coordinator of the EU-funded SASAM project. ‘People are working on that now.’
The SASAM project focussed on working out what standards and regulations are needed to drive the 3D printing industry forward, and Feenstra believes that the 3D printing sector will really take off in one or two years’ time when the basic standards are in place.
In order to work out what kind of research is required to push forward 3D printing, industry and policymakers have come together as part of the Additive Manufacturing Platform to make recommendations. The document, called a Strategic Research Agenda, suggests things like looking for new materials that would be as strong as cast metal when 3D printed, and teaching university students about 3D printing.
10 Predictions on the Future of 3D Printing [Expert Roundup]
21 August 2019
Without a doubt, 2019 is an exciting time for 3D printing. The industry continues to move towards industrialisation, and the technology is increasingly becoming part of the wider manufacturing ecosystem.
But in such a rapidly evolving industry, it can be difficult to keep up with the key trends that are driving the future of 3D printing.
To help you better understand where 3D printing is headed, we’ve sifted through over 30 of our Expert Interviews conducted over the last 12 months and extracted key insights as to what the future holds for this exciting technology.
Contents
1. 3D printing will become a mainstream technology for serial production A 3D-printed stator ring and impeller [Image credit: VELO3D]
“Additive manufacturing is headed for very exciting times because it’s gradually becoming mainstream.”
Andy Kalambi, CEO of Rize
3D printing has long passed the point of being viewed only as a prototyping solution.
Everyday, companies are finding new ways to incorporate the technology into their production, with applications ranging from tooling to spare/replacement parts and some end-use components.
From automotive to consumer goods, companies across industries are becoming aware of the advantages 3D printing offers for production. According to Sculpteo’s 2019 State of 3D Printing report, 51% of companies are actively using 3D printing for production.
There are, of course, the well-publicised cases. For example, large automotive companies like Ford, Volkswagen and BMW are already producing 3D-printed parts for their vehicles. Late last year, BMW announced that it had fitted its one-millionth 3D-printed part for its BMW i8 Roadster.
While the overall volume of parts being printed in these cases is small relative to mass manufacturing volumes, the number, as well as the range of parts produced with 3D printing, are only set to increase.
The next step for both the technology and the industry will be to maintain this momentum and work towards enabling more applications on a larger scale.
“We’re reaching an inflection point and the number of parts that are actually going into production is increasing.
Five years from now, you’ll see a lot of contract manufacturers that have scaled up considerably and have hundreds of these systems on their floor, producing parts with long-term contracts for production.”
Zachary Murphree, VP of Technology Partnerships at VELO3D
A key element that will enable such production volumes is the technology. Over the last few years, new technologies have been brought to market, and a number have already been announced for the years ahead.
For example, on the metal 3D printing side there is huge potential for newer metal binder jetting technologies to carve out a larger share of the traditional metal manufacturing market. Companies like Desktop Metal, 3DEO, ExOne, HP and GE are all working on next-generation metal binder jetting solutions to achieve this.
With lower hardware and material costs than other metal 3D printing technologies, these metal binder jetting machines have the potential to offer higher-volume part production at a cost-competitive price.
Of course, 3D printing will not replace machining, casting or injection moulding. The true goal for the technology is to become a viable production method that can be used on par with other technologies.
As more effort is being put into ensuring greater repeatability and speed with industrial 3D printing, we’re getting ever-closer to reaching this goal.
“One important trend is the development of design software tools for AM. The next step is for them to become fully and seamlessly integrated into popular CAD software products.”
Terry Wohlers, founder and President of Wohlers Associates
Designing for additive manufacturing is a challenging process, not least because it can be counterintuitive for engineers that have been trained to design for traditional manufacturing.
Further complicating this is Computer-Aided Design (CAD) software, much of which until recently hasn’t been optimised for the design requirements of 3D printing.
“Additive manufacturing can do some incredible things in terms of creating complex geometries, but to expect one person or even a team of people to sit down and create those sorts of geometry would create a real bottleneck if it was all being done using conventional tools.”
Ian Campbell, Professor at Loughborough University
For example, it can be difficult to use traditional CAD software to design components made with graded materials, create lattice structures or model porosity.
Combining multiple software packages can alleviate this limitation to a degree. However, switching between different software solutions is a highly inefficient process. In an ideal world, engineers and designers would work in a single design environment without the need to move data from one software product to another.
Fortunately, software companies are beginning to develop integrated design solutions for additive manufacturing.
Companies like Autodesk, Dassault Systèmes and PTC are beginning to explore ways to make it as easy as possible for engineers to optimise their designs for additive manufacturing.
Take Autodesk’s Netfabb as an example. Developed to work with 3D printing STL files, Netfabb can analyse and repair files, generate support structures and lattices and run a simulation for a design of a metal 3D-printed part — all in one package.
Similarly, PTC is offering its Creo 6.0 software to enable design and print preparation in one environment. At the end of 2018, PTC acquired generative design software company, Frustum. The company is now working to add generative design technology, which is often combined with 3D printing, to its CAD platform.
Ultimately, creating integrated 3D printing software solutions will be a crucial piece to the puzzle of taking the technology into the mainstream.
“We’ll see more software tools that help engineers design parts better for a given process. Software-driven build setups like orientation, pre-deformation will be part of that … These developments will help to reduce the number of iterations needed, especially if the goal is printing for production.”
Greg Paulsen, Director of Application Engineering at Xometry
“In terms of skills, in my opinion, innovation is all about people and technologies. There’s no point in pushing for advanced technologies without the people to adopt them.”
Revannth Murugesan, Managing Director at Carbon Performance
Much has been said about the need for more education within the 3D printing industry. Our recent State of the Industry Survey revealed a lack of education as being the biggest challenge faced by service bureaus today.
While adopting 3D printing for prototyping is relatively straightforward, establishing 3D printing for production can be challenging. Not only is investment in hardware required, but companies must also commit the time to develop the expertise needed.
Lack of expertise, in particular, can create a lot of barriers to entry. For one, without proper knowledge about additive manufacturing, companies will likely struggle to develop a business case or use case for 3D printing.
“That workforce element is really critical right now. There are not enough engineers, managers, executives who truly understand the technology well enough to work and develop a strategy to get what they need to get out of it.”
John Barnes, Founder of The Barnes Group Advisors
“The industry is recognising what additive manufacturing can’t do as well as the fact that it can do a lot more than most are using it for today.
”
Harold Sears, Technical Leader of Additive Manufacturing Technologies at Ford
That said, awareness about the capabilities of 3D printing is increasing gradually. A lot of effort is being put into educating the market on how to get started with 3D printing and extract the most value out of it.
At the same time, companies are launching both online and on-site courses, organising user tradeshows and workshops and creating educational content to spread the word about 3D printing.
Consultancy firm, the Barnes Group Advisors, for example, launched an online course with Purdue University earlier this year to provide engineers with the ability to attain relevant knowledge in additive manufacturing.
Only when companies learn about the capabilities and limitations of 3D printing, will they be able to use this knowledge to develop successful applications for the technology.
Take Boyce Technologies as an example. The engineering firm purchased a large-scale 3D printer to create prototypes for communications systems like information kiosks and emergency response systems.
However, the company was willing to experiment with 3D printing to understand its true capabilities.
By learning the ins and out of the technology, Boyce discovered that the same 3D printer used for prototyping could also be used to make certain end-use polymer parts. Since then, the technology has become a key part of Boyce’s business and is used for production applications 90% of the time.
Ultimately, as the understanding of AM grows, its users will be able to identify more industrial applications for the technology, pushing the scope of 3D printing to new horizons.
“In dentistry, you could, in theory, have a great case for converting 80% plus of the means of production to an additive technology.
”
Scott Dunham, Vice President of Research at SmarTech Analysis
3D printing is already playing a huge role in the dental industry, producing crowns, surgical guides and the majority of dental aligner moulds. But the technology has the potential to become a dominant technology in this sector.
A report by SmarTech Analysis indicates that 3D printer sales within the dental industry will exceed sales of machining hardware by 2025, and the technology will become the leading production method for dental restorations and devices worldwide by 2027.
Driving this paradigm shift is the evolution of resin-based 3D printing technologies like SLA, DLP and material jetting. Resin-based 3D printers can produce custom dental devices with excellent surface quality and fine feature detail at a fast speed. The dental industry can benefit from these capabilities, as dentists can provide services faster and cheaper.
“We’re seeing that 3D printing is becoming one of the key tools in areas like dental care and dental restoration.
The digital thread there has been largely developed all the way from intraoral scanning to the workflows and the planning — not just in the lab, but also in the dental clinic. So there you can see a market that is ready for mass adoption.”
Avi Reichental, Founder of XponentialWorks
Furthermore, resin 3D printers are becoming increasingly affordable for dental labs, with a price point of roughly $5,000 on average. These printers are also optimised to work with certified dental printing resins, the number of which has significantly grown over the last few years.
EnvisionTec, one of the largest resin 3D printer manufacturers, offers 13 different types of resin materials optimised for dental applications.
Formlabs, another key player in the resin 3D printing market, offers 5 types of resins, some of which can be used to directly produce dental prosthetics. The company is also said to have increased its market share in the dental 3D printing market more than 20-fold over the last two years.
Additive manufacturing has penetrated a significant number of sectors and industries. However, dental appears as the primary market in which digital manufacturing in the form of 3D printing can be embraced to the fullest.
“Part of the machine learning process is to introduce a high level of repeatability and enable the user to more easily predict how performance is going to function.”
Joshua Martin, CEO of Fortify
Making 3D printing more efficient and productive is an ongoing quest within the industry. One trend enabling this is the development of smarter systems, powered by sensors and machine learning.
3D printer manufacturers are beginning to fit their systems with sensors to enable in-process monitoring. Sensors and cameras placed inside a 3D printer can be used to measure multiple aspects of a build in real-time, helping to document the build process and ensure requirements are met.
For example, with powder bed metal 3D printing, cameras can capture the size and temperature of the melt pool, which directly impacts the microstructure, material properties, surface finish and overall part performance.
Integrating machine learning algorithms with such sensors can help to make 3D printing a much smarter process. Sensors can gather valuable data which then can be fed to a machine learning system.
The system will analyse the data and then provide feedback on how the process can be improved. It can be used to predict the likelihood of defects or build failure, enabling engineers to intervene the process and prevent any defects early on.
Currently, this concept is still in the early stages, with only a few solutions available on the market. VELO3D, a US-based metal 3D printer manufacturer, has developed a system equipped with sensors which can report back on the status of the build. Similarly, 3D printer manufacturer, EOS, offers the EOSTATE monitoring suite, which can capture quality-relevant data in real-time.
MIT startup, Inkbit, is pairing its multi-material inkjet 3D printer with in-built scanners and a machine learning system. The monitoring system scans each layer of the object, while the machine learning system uses that information to predict the warping behaviour of materials and automatically correct any errors in real-time.
“I think that’s the Holy Grail for AM because with in-process control you’re able to almost immediately react on deficiencies within your process.”
Yves Hagedorn, Managing Director at Aconity3D
In the future, we anticipate that all 3D printers will be integrated with smart technologies like sensors and machine learning. These technologies, combined with 3D printing, will significantly increase process repeatability by reducing the risk of build failures.
A more intelligent process will ultimately result in easier quality assurance and open the door for greater productivity with 3D printing on the factory floor.
Service bureaus are a vital segment of the additive manufacturing industry, helping to further the advancement of the technology. Looking to the future, the service bureau segment is poised for continued growth.
This prediction is supported by a number of experts interviewed for our State of the 3D Printing Industry Survey Report and respondents giving a positive outlook for the year ahead.
The growth will largely be driven by the increasing specialisation in certain 3D printing technologies (e.g. metal AM) or industries (e.g. medical).
“The specialists who can cultivate unmatched expertise in a specific area of AM should see a return on that investment in expertise. On the other end, those companies offering an array of printing technologies to make parts for customers, as well as supporting post-processing and design services for each, should also eventually rise to the top.
”
Scott Dunham, Vice President of Research at SmarTech Analysis
Service bureaus will create a lot of opportunities for other industry players to expand into.
“There will be a lot of mergers and acquisitions over the next few years. For some of the larger manufacturers of 3D printing materials, it will be a natural move to have a service bureau attached to their business. There’s a real opportunity for the other manufacturers to do deals or to buy up service bureaus to promote their particular materials.”
Jonathan Warbrick, Business Development Manager at Graphite Additive Manufacturing
We’ve already seen this prediction coming true with recent news of Sandvik, a producer of metal powders for AM, acquiring a stake in 3D printing service provider, Beam-IT.
On the other hand, manufacturing marketplaces like 3D Hubs and Xometry, which offer companies access to a global network of suppliers (for both AM and traditional manufacturing services) on demand, will also see rapid growth.
Manufacturing is hard pressed to provide a more agile response to rapid changes in customer demand, technology and markets. Operating a Manufacturing-As-A-Service (MaaS) business model, online 3D printing platforms are able to offer agility and quicker turnarounds, filling what seems to be a lucrative market gap.
“[MaaS is] a win-win because the shops are getting work without having any need to do marketing for it. We’re getting fulfilment and quality parts made. And finally, the customer has a one-stop location to get their parts ordered over many manufacturing technologies.”
Greg Paulsen, Director of Application Engineering at Xometry
“When it comes to metal 3D printing, we’ve just scratched the surface.”
Scott Dunham, Vice President of Research at SmarTech Analysis
Metal 3D printing remains one of the fastest growing segments in 3D printing. However, the many experts we’ve interviewed agree that, although metal 3D printing market has evolved significantly over the last decade, its real potential has yet to be fully realised.
“When you compare the size of the AM industry with the size of the traditional manufacturing industry, we have a lot of room to grow.”
Zachary Murphree, VP of Technology Partnerships at VELO3D
According to SmarTech’s Scott Dunham, materials will be key to the maturation of metal 3D printing:
“As the industry matures, you would see, of course, much more emphasis on materials, because the utilisation rates of the 3D printers ideally have climbed to support higher volume manufacturing and more regular serial use.”
EOS, a key player in the world of powder bed fusion 3D printing, is heavily focused on developing more materials for metal AM. In May 2019, the company launched four new metal materials, including stainless steel CX, aluminium AlF357 and two grades of titanium.
Another vital requirement for the adoption of metal 3D printing for production is quality assurance.
“Quality control, i.e. understanding the quality requirements and being able to validate your part is really going to make a difference going forward.”
Doug Hedges, President of Sintavia
When a reliable, faster process and a broader material choice come together, “we’ll see adoption steadily improve throughout all industries, not just the early adopters, like aerospace and medical”, believes Dave Conover, ANSYS’ Chief Technologist of Additive Manufacturing.
Indeed, manufacturers in the automotive, industrial goods and energy sectors are beginning to gain confidence in metal 3D printing as a solution. BMW has recently launched its 3D printing production of metal roof brackets, while companies like GE and Conflux Technology are developing next-generation heat exchangers with the technology.
Undoubtedly, there are many opportunities left to be explored with metal 3D printing. To capture those, the industry needs to collaborate more vigorously on developing standards and best practices to ensure repeatable processes and high-quality results.
“The composite space is perhaps the newest segment in 3D printing. There are challenges that come with this, but there are also a lot of opportunities.”
Joshua Martin, CEO of Fortify
The composite market is one of the key emerging opportunities for 3D printing. Composites are lightweight, strong materials, highly sought-after in industries like aerospace, automotive, oil and gas and industrial goods.
A SmarTech Analysis report estimates that composite 3D printing will grow into a nearly $10 billion business within the next decade. Within this timeframe, end-use parts are expected to become the largest revenue opportunity.
The ability to streamline and cut the cost of traditional composite manufacturing will be the key driving factor behind this growth.
“Composite manufacturing is currently very labour, resource and capital intensive, which means that it doesn’t really scale to large volumes. Additionally, there are long design cycles because of inadequate software and inefficient simulation.”
Wiener Mondesir, Co-Founder and Chief Technology Officer at Arevo
The number of companies looking to automate composite manufacturing with 3D printing is growing by leaps and bounds. Currently, Markforged is arguably the biggest player in terms of market presence but other companies like Arevo, Fortify, Impossible Objects and Thermwood are seeing notable growth as well.
Fortify, for example, recently closed a $10 million series A funding round, while technology company, Arevo, announced the successful application of its composite 3D printing technology to manufacture bike frames. Thermwood’s Large Scale Additive Manufacturing technology is also gaining traction in the production of composite tooling for aerospace applications.
Clearly, the potential for the composites 3D printing segment is huge. However, to continue to evolve, companies will need to work on further improving their technologies and expanding the scope of applications suitable for composite 3D printing.
Automation will be the next step in the evolution of additive manufacturing. Achieved through a combination of hardware and software, as well as robotics, sensors and networks, automation will ensure more streamlined processes as part of an end-to-end digital production cycle.
On the hardware side, companies are launching new, integrated production units, which incorporate robotics and smart factory concepts to automate various steps of the manufacturing workflow.
For example, Digital Metal, a manufacturer of binder jetting metal 3D printers, has paired its systems with robots, which handle manual work like removing build boxed and delivering them to a post-processing unit. Jabil is also using robots to automate part handling in secondary AM processes and computer vision to automate inspection processes.
On the software side, workflow automation is gaining traction, as companies realise that achieving serial production with 3D printing will be virtually impossible without an end-to-end management system in place.
Furthermore, the AM post-processing stage, which has typically been a manual process, is becoming more digitised.
“Post-processing automation will become one of the major things to watch out for. This is because the real step change will be in the ability to automate post-production.”
Neil van Es, Founder of Parts on Demand
Several companies, such as Additive Manufacturing Technologies and Post Process Technologies are now overcoming this bottleneck by providing post-processing solutions that speed up the process of support removal and surface finishing – through automated post-processing machines.
Ultimately, adding automation to a 3D printing equation will enable manufacturers to transform 3D printing to a continuous process that will work much better in a volume production setting.
“In the next couple of years we will see a lot more competitive chaos resulting from a fairly crowded field.”
Scott Dunham, Vice President of Research at SmarTech Analysis
With new players entering the industry, there is an increasing level of competition within the AM market. A growing number of startups, as well established companies outside of AM, are entering the 3D printing arena looking to capitalise on the industry’s growth.
AMFG’s Additive Manufacturing Industry Landscape 2019 has identified more than 80 3D printer manufacturers, the majority of which appeared in the last five to ten years.
There’s a huge potential for newcomers to leapfrog more established players.
As Avi Reichental, Founder of advisory firm, XponentialWorks, points out, “[established companies] have a rather unfair disadvantage vis-a-vis new players because they have lots of legacy issues to deal with. Since they’re operating within certain technologies, they’re more likely to implement and introduce linear, incremental improvements. In contrast, a completely new company can solve a similar problem without any of the legacy technology and organisational issues.”
As competition heats up, the industry players will have to refocus and reinvent to survive. We’ve already seen some moves in this direction. For example, Ultimaker has rebranded recently to strengthen its brand as a professional, B2B 3D printing business. 3D Hubs, once a community-based 3D printing marketplace, has recently shifted its focus to the B2B industrial space.
“We live in a period in which you either innovate or evaporate. In other words, you either disrupt or you will be disrupted.
”
Avi Reichental
Clearly, the landscape is becoming more competitive than ever. That said, competition can be a positive sign, pointing to the growth of the industry. Competition can help to push the industry forward, as it forces companies to focus on innovation and development.
However, increasing competition also means that it’s a crucial time for companies to remain innovative to maintain their place in the market.
“I think the additive manufacturing industry will deliver on its promise.”
Simon Fried, Co-Founder of Nano Dimension
The trends discussed above reflect one key idea: 3D printing is reaching maturity. The advancements in the hardware, software, materials and applications suggest that 3D printing will eventually become yet another manufacturing technology.
Naturally, the adoption rate of 3D printing will increase over time, with some segments like dental almost entirely switching to 3D printing. The growing awareness of 3D printing and its benefits will facilitate this growth.
“I really do think you will see the impact of digital manufacturing as a solution for full-scale manufacturing.”
Philip DeSimone, Co-Founder and VP of Business Development at Carbon
In the meantime, the competitive 3D printing landscape will require companies to differentiate themselves from competitors by leveraging their unique expertise and developing a clear value proposition.
Considering the recent progress of the technology and these expert predictions, 3D printing is clearly headed for a bright future of digital, smart manufacturing.
More Expert Roundups:
10 of the Biggest Challenges in Scaling Additive Manufacturing for Production [Expert Roundup]
Expert Roundup: 20 Experts Share Their 3D Printing Predictions for 2020
additive manufacturing experts forecast / Habr
What is the future of 3D printing? In 2022, the 3D printing industry will celebrate its first decade as an additive manufacturing tool. We look forward to the second and asked 3D printing experts to share their predictions for the development of additive technologies.
Which 3D printing materials will be the most in demand in the future?
What 3D printing materials will thrive in the next decade? Will we see new materials for 3D printing resulting from the discovery of new alloys using artificial intelligence-based computational processes, where the end user can specify the desired characteristics? What about the widespread use of metamaterials - materials with properties that do not occur in nature? How will the issue of sustainability, the growth of production of bio-based polymers or the recycling of waste plastics and metals, the return of resources to a closed economy be considered?
Is there too much hope for 3D printing? Like any cutting edge technology, 3D printing has gone through its fair share of futuristic hype. The hype and fashion trends can be useful tools for attracting funding, but excessive expectations can be detrimental in the long run. Marketers can use fashion trends or provide beautiful concepts, but it's important to understand the end goal you're aiming for.
Can 3D Printing Companies Expect Increased Government Control? Some inventions extend security concerns beyond defense to other verticals such as energy, aerospace, or broader technology markets.
Concerns about the semiconductor market, exemplified by the conflict between China and Taiwan's TSMC, the European chip law announced in Davos, or Intel's $20 billion investment in a "Silicon Center" could herald a new era of protectionism. Export controls and ITAR restrictions are unlikely to be lifted as tensions escalate between Russia and NATO over the conflict in Ukraine. How will the tax on digital goods work and will the current moratorium on customs duties on electronic goods be extended - if it is lifted, how will the market react to smart factories and collaborative business models?
Rising transport costs and confusing supply chains leading to a logistical crisis have contributed to the revaluation of production sites. Does additive manufacturing play a role in reorientation projects by returning production to consuming countries, and will this take the form of the long-advertised distributed production – or will production most likely be relocated but remain concentrated due to economies of scale?
Back to the 3D printing industry and how the brand landscape will change in the next decade. Consolidation in the 3D printing sector is on the horizon, fueled by IPOs and SPAC's insane capital injections into the sector. How will this R&D money be used to bring innovation and new 3D printing technology to market, given the short timeframe investors are looking for?
Business leaders must demonstrate quarterly improvement in performance, and the acquisition of innovative equipment plays an important role in profit growth. The 3D printing industry will release an update on 3D printing patents soon.
How can the additive manufacturing market be valued at $12 billion when SPAC activity has exceeded $11 billion over the past 12 months? Is the market capitalization of one company using additive manufacturing three times the value of the 3D printing industry? (Align Technology, NASDAQ: ALGN, market cap: $37. 4 billion vs. 3D Systems, NYSE: DDD, market cap: $2.2 billion).
Market through end users can do some of the work. Demand helps find the most winning technology platforms from a sea of options. As demand for additive manufacturing rises, the growing market can help grow all firms, both new and established, who will have access to a larger pie.
It may seem strange to refer to history in an article about the future, but the mistakes of the past can be instructive and can help chart a safer course of development. 1922 is often referred to as the birth of modernism: workers returning from global conflicts, the great migration underway, workers moving into newly mechanized factories. Artists under the banner of Futurism, led by Marinetti, celebrated the movement and the rapid development of technology, while the Dadaists and the film Modern Times, starring Charlie Chaplin, later opposed it. Wolfe, Elliot, and Joyce took their thinking to a clean slate, experimenting during the Harlem Renaissance, when modernism flourished in literature, music, and other arts, not just in the US, but around the world. Can new design tools and technologies provide a modern renaissance and the realization of creative impulses? How will broader societal trends and macroeconomic forces interact?
Aldous Huxley's novel "Brave New World" not only reflects the social characteristics of that time, but also illustrates the ideas about the application of new technologies. The author expresses the anxieties of that time along with the dangers of scientific futurism. A clumsy selection of elements to draw parallels with the current decade is pleasant entertainment, but it would be a mistake to ignore the malign forces of frenzied speculation, overproduction, and inadequate or absent controls that plunged the subsequent period into a great depression. We will return to this topic later, after additive manufacturing experts present their view of the broader technology landscape that will shape the coming decade. Will NFT-enabled STLs be readily available in the metaverse, and will engineers work on them in augmented reality?
Meltio aerospace disc in 316L.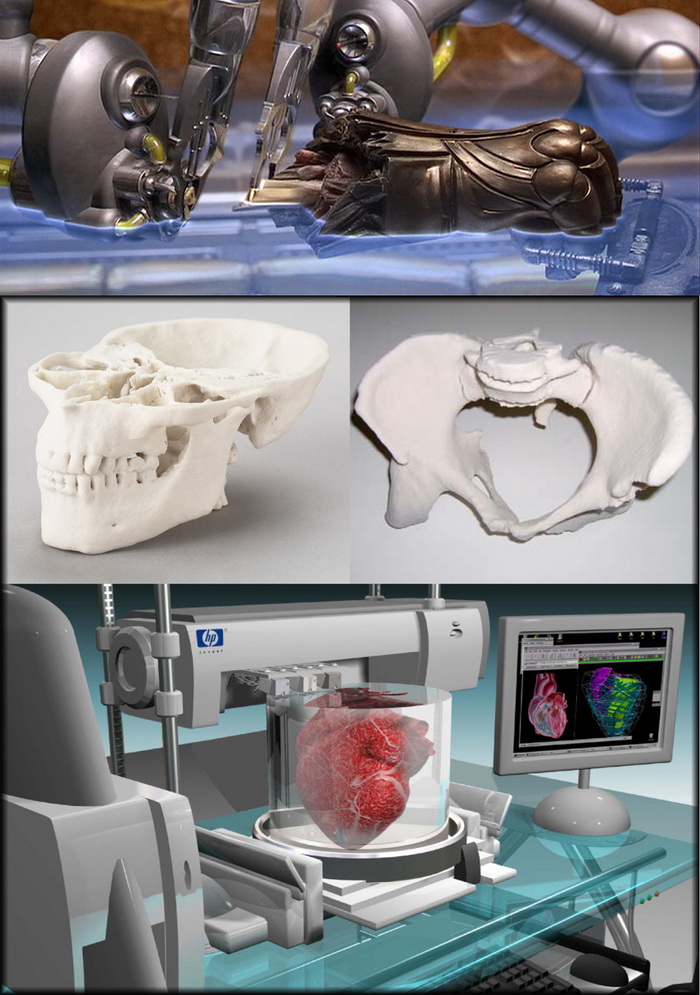
Arno G. Held, Managing Partner, AT Ventures
Over the next 10 years, additive manufacturing is set to take its place as the manufacturing technology that will support the transition to a sustainable and resource efficient civilization. The biggest potential applications are in the design and manufacture of lightweight structural components or electric motors. To do this, industry players must understand the need to work together and overcome the challenges of quality control, cross-platform repeatability, and material recycling together.
Dr. Jeffrey Graves, President & CEO, 3D Systems
I expect mass customization to be a trend not just in 2022 but in the next decade. Many organizations are looking to take advantage of the possibilities of additive manufacturing to produce large numbers of individual parts, but it seems to me that many firms have not yet figured out how to integrate AT (Additive Manufacturing) into their workflows. We are seeing a growing adoption of additive technologies, alongside traditional manufacturing methods. I think we will soon see manufacturers large and small using AT for mass personalization.
I believe machine learning will play a critical role in facilitating the integration of AT into existing workflows. Additive manufacturing has the potential to offer design flexibility, fast time to market, and efficient supply chains. In order for companies to maintain their competitive position, they need a sound production strategy that allows them to effectively and efficiently integrate AT into the overall production process. As more companies adopt smart manufacturing solutions, I expect they will see how machine learning can enable autonomous manufacturing, which will help increase productivity and increase the ability to inject scalability and agility into processes.
We will see how additive manufacturing can help achieve significant breakthroughs in medicine. AT has already shown excellent results in this industry. Additive technologies have helped provide patient-specific healthcare with unique solutions for surgical planning and medical device design. I am very excited about the next frontier in healthcare, where bioprinting plays an important role. Over the past year, the number of participants in this industry has increased dramatically, whether they are research organizations or private and public companies. We have seen the scope of research expand to include new printing technologies and new materials to help drug discovery, tissue creation and, hopefully, human organ donation in the near future. I believe that we are on the cusp of amazing developments in this field and look forward to discoveries in this industry.
Avi Reichenthal, co-founder and CEO of Nexa3D
AT will play a key role in reversing global warming through weight reduction, reduced carbon footprint, localized manufacturing, lower energy consumption and reduced waste, and shift to plant-based materials origin.
Over the next decade, AT will become a cost effective and practical tool spanning the entire product lifecycle from concept models to aftermarket parts and everything in between, including the holy grail: mass production.
AT will reach a new level, becoming an effective tool for the manufacture of aircraft, trains, cars and houses, as well as for the creation of atomic structures.
We will get closer to the emergence of the “replicator”, especially in the field of bioprinting.
Christine Mulcherin, General Manager of Powder Products, Nexa3D and President of Women in 3D Printing
Sustainability and the Circular Economy have been hot topics in 2021 and I expect interest will only increase over the course of the decade. Additive manufacturing contributes to the development of the circular economy. In addition to the growing pressure on the environment, the efficient recycling of materials, both plastic and metal, is critical to reducing the cost of commercial-scale printing. The high cost of 3D printing raw materials is arguably one of the biggest obstacles to making AT a true mainstream manufacturing method. And until we can effectively and efficiently reduce or almost eliminate material waste and therefore reduce these costs, actual large-scale printing is likely to remain prohibitively expensive.
Didier Deltorte, President, HP Personalization & 3D Printing
Consumer behavior is undergoing a historic shift. Personalization and stability are becoming benchmarks for brands seeking to stand out in increasingly competitive markets. Traditional product design, manufacturing, and long supply chains do not fit well with these trends. In the coming years, as we continue to improve additive manufacturing solutions, more brands, both small and large, will implement new automated, data-driven, high-performance innovations that are ubiquitous with complex design, ordering, and ordering systems. and logistics. All this allows us to turn both mass personalization and classic production into a scalable reality.
Chris Connery, VP Global Research, CONTEXT
Supply trends have shown time and time again that the industrial 3D printing market is growing with every innovation. Innovation can be realized through a new approach to existing technologies, expansion of the product portfolio by existing players, and by complementing existing technologies or introducing completely new developments to the market. Developments in new categories from both established players and well-funded startups.
End markets are always looking to explore technological advances, trying to find the “silver bullet” technology that will give them a competitive edge. It is expected that just as Carbon's vat polymerization technology or Markforged's material extrusion technology has driven market growth, other vendors are expected to find new enhancements to 7-core AM technologies. Just as we are now seeing Stratasys expand its polymer portfolio to include powder coating, we can expect other manufacturers to independently develop or acquire new technologies and actively bring them to market.
Brian Thompson, Vice President, CAD Division and General Manager, PTC
In the next decade, we expect digital technology to come into full force and become the backbone of smart factories, and additive manufacturing to play a major role in the transformation of integrated industrial manufacturing.
As AT standards continue to evolve and more materials, processes and parts are certified and qualified, more industries will move to end-use mass production. We will see multi-batch printing and consolidation become more ubiquitous.
From a technological standpoint, we also expect big breakthroughs in bioprinting and regenerative medicine, whether it's the creation of complex tissues or the development of drugs.
Cathy Bui, Head of Product Development, Business Engineering, Formlabs
The past two years have shown us just how fragile and important supply chains can be. AT/3DP technology has already helped support and strengthen supply chains, but the next decade will see an even greater role for AT/3DP in supporting traditional manufacturing technologies. In particular, we will see more companies using 3D printing to create consumer-facing parts, make custom manufacturing fixtures, and enable decentralized manufacturing. AT/3DP will never completely replace traditional mass production, but in the next decade we will see this technology take on more and more processes that used to be done by traditional methods.
Stephan Kuhr, Founder & CEO, 3YOURMIND
When it comes to manufacturing in 10 years, I envision new collaborative business models powered by digital platforms and technologies around the world. AT/3D will be implemented by all manufacturers not only for prototyping, but, first of all, for mass production. Barriers related to AT knowledge, quality certification, data collection will be removed. These new Industry 5.0 factories will be sustainable, interconnected and digital. Through this, I hope, creativity will become limitless; the production of new forms (additive, hybrid, etc.) will be fully integrated with artificial intelligence, robotics, and digital twins will push us to open the boundaries of IoT. Ultimately, this will show everyone that there are no boundaries! I can't wait to see this!
Frank Roberts, President, 6K Additive
Technology across the AT supply chain, from materials to machinery to post-processing and software, will greatly add value to organizations, and more will open as we transition to such manufacturing. areas of application.
In terms of materials, we are seeing an ever-expanding range of high-performance metal materials that will allow rockets to fly faster and operate at extreme temperatures that can be used in medicine, which will greatly improve patient care, and allow doctors to perform operations using implants made from exotic materials. Materials from high-entropy alloys will appear, which are in their infancy today. And although new materials will appear, the commitment of manufacturers and consumers of materials to the principles of sustainable development will be no less important than quality and cost factors.
Kai Führer, CEO, enter2net.com
In the future, additive manufacturing will take up an increasing share of the total. A new driving force is the stabilization of supply chains through local and decentralized production. On the way to a sustainable and cost-effective introduction into the manufacturing industry, 3D printing will lose its special status as a new technology "where everything is different" and will be fully integrated into the economic chain, using the concepts of automation and industrial IoT. This assumes that the main issues regarding the cost and qualification of materials, the speed and quality of printing, as well as the integration of AT processes into standard software will be solved, I firmly believe in this.
Joseph Crabtree, CEO and founder of AT&T
As we look forward to the next decade, we look forward to a period of consolidation in the AT industry. Several "traditional" manufacturing companies will start to "play" in the field of AT, and there will be an increase in activity in the field of mergers and acquisitions. We expect the reset of the bloated markets of the last 2 years to lead to consolidation of companies, and only those with viable long-term businesses that are resilient to profitable growth will be able to ride the wave. This will contribute to the eventual growth and expansion of the AT industry and lead to 3D printing becoming "just another manufacturing technology." This will be the final acceptance that we have all been looking for.
Dr. Robert Gmeiner, Cubicure CEO & CTO
The current decade is likely to see a shift away from technology strategies towards an intense focus on measurable value added based on realistic production scenarios.
Vertical markets will be the first to show sustainable examples of AT success. While the mergers will continue, both technologically and in terms of companies, the AT industry is on the rise.
In the past, attention in the field of polymer AT has focused on FDM and powder-based printing processes. However, the largest turnover in the industrial production of AT has always been associated with resin-based 3D printing. The next decade will further reflect this economic fact: Light-curing materials are rapidly becoming polymers that meet the high specifications of many industries. Customized mass production will continue to play an increasing role in patient and consumer related products. At the same time, full-scale additive manufacturing of small and complex parts will see huge growth in industries such as electronics and connectors.
Flexibility and risk reduction are important to all industries now and will continue to be so in the future.
Deho Hong, Product Manager, nTopology
Over the next decade, mass customization will become the standard in many more areas than today (such as medical devices and high-end sports equipment). As the cost of materials and production of ATs continues to decline, we are likely to see some change in supply chains as locally printed parts become more profitable than those sourced from global manufacturing centers. We will also witness an expansion of the range of materials for AT with the advent of new alloys, polymers and hybrid metamaterials. Advances in additive manufacturing will enable printing with little or no human intervention, and many printers will provide high-tech fabrication, allowing parts to be created from all sides, not just z-layer growth.
Gil Lavie, Founder & CEO, 3D Alliances
I see two trends in the next decade. The first is accelerating research and development on new AT capabilities, leading to exciting technologies that will provide higher productivity, special materials for specific applications, higher accuracy and repeatability, in other words, better compatibility with real production needs.
2021 has been a big year for many companies that have raised funds/decided to go public with some of the capital focused on developing new products.
The second trend is the introduction of AT for new applications in non-standard industries such as construction, food, fashion, space and others.
Oliver Smith, Founder, Principal Consultant, Rethink Additive
If the 2010s was the decade of 3D printing coming of age, the 2020s will be the decade of its going public. Over the past 24 months, the industry has been flooded with capital, which has led to a sharp acceleration in the development of new platforms, as well as spurring M&A activity, and there is no sign of a downturn in this trend. I could argue that the renewed investment interest in the technology has been driven by a significant amount of positive press coverage demonstrating how 3D printing can address critical parts shortages and supply chain disruption, but unlike the wave of investment hype 10 years ago, this the second wave is stable, because many 3D printing technologies can be incorporated into manufacturing processes or used to support manufacturing. The next ten years will be an interesting time for technology vendors and investors, as a wave of public offerings lies ahead (several successful private vendors such as Formlabs have already publicly indicated their interest in an IPO), as well as consolidation among new and old vendors through mergers and acquisitions .
Another trend we expect to see in Rethink, due to AT's increased prominence as a result of the pandemic supply disruption, is explosive growth this year and over the decade driven by financial investment in technology providers. 3D printing has again become one of the most mentioned technologies in conversations about the development of the market and the factories of the future. This led to a wave of acquisitions, investments and IPOs. With this influx of capital, we are already seeing accelerated time-to-market for new technologies and platforms, as well as M&A among legacy vendors. With several more successful AT vendors publicly stating their intention to go public, whether through traditional public offerings or SPACs, the M&A and IPO trend should be expected to continue into 2023 and beyond, with not all of them being sustainable.
Mohsen Seifi, Director of Global Additive Manufacturing Programs, Martin White, Head of Additive Manufacturing Programs - European Region, UK, Alexander Liu, Head of Additive Manufacturing Programs - Asia Region, Singapore, and Terry Wahlers, Head of Advisory Services and Market Analysis, ASTM International Center of Excellence for Additive Manufacturing.
Over the next decade, we predict AT will play a vital role in the pursuit of sustainability by supporting the global shift towards cleaner production methods. This trend will help support the economic and environmental goals set by governments around the world. AT methods will continue to be driven by market demand, such as zero-carbon solutions, especially in transport and heavy industry.
In applications, demand will continue to grow for large parts such as titanium blanks in the aerospace industry and large molds that compete with alternative AT methods (powder melting or metal spraying). This will expand the supply chain, reduce the development time for new platforms, and ultimately help reduce the final cost.
Dr. Johannes Homa, CEO of Lithoz
Additive manufacturing is an increasingly common technology. We see companies successfully incorporating this powerful technology into their workflow, complementing existing production methods. We will soon see the creation of geographically independent, yet globally and digitally connected manufacturing sites that can reach simultaneous mass production through the digital capabilities of 3D printing.
In addition, more attention will be paid to quality and reliability in serial production. As more and more companies enter mass production, there will be a need for a higher level of quality and confidence in the efficiency and capabilities of the additive manufacturing process. Therefore, companies in this industry will prioritize making each step as reliable as possible. Finally, as a consequence of the previous point, the level of automation will increase in the industry, eliminating the human factor and making the whole process more efficient and simple for both manufacturers and customers.
Roger Useda, CIM-UPC Director of Technology Transfer and co-founder of BCN3D
I firmly believe that we will finally see mass production using AT technology, and not only for piece or expensive products, but also for series production . To do this, we still have to solve some problems, such as the quality of the primary products and the price of the final part.
Henrique Wonneberger, COO and co-founder, Replique
Applications for AT materials are already on the rise as metallic and high temperature polymers for FDM printing are being developed. Improvements in AT have already led to a shift from prototyping to mainstream manufacturing, but we expect AT to be used in the coming years not only as a replacement for traditional manufacturing, but as a completely new approach to creating a production chain. AT will be integrated into a comprehensive and reliable platform, where the individual steps of 3D printing will be combined into one process, from ordering a part to its delivery to the customer. Advances in AT software have improved quality control and can now predict warp and thermal stress before a part is made, minimizing printing defects and wasted materials. 3D modeling can be used to get the most out of materials, allowing designers to create shapes that would not be possible without 3D printing, develop new products that optimize topology and reduce weight.
Rush Laselle, Senior Director, Additive Manufacturing, Jabil
The next decade in manufacturing will bring major transformations in the digital technologies and applications being implemented in the world's factories. The advent of a more comprehensive digital ecosystem will kick-start the entire additive manufacturing industry, making small-scale manufacturing, including batch sizes of one, truly cost-effective, for more consumer-oriented products. As a result, the democratization of production and localization is expected, which will allow better customer service.
Louis Folgar, EVP Americas, ATT Inc.
The range of resin materials available for 3D printing will be unlimited. Part quality and productivity will increase proportionally. With lessons learned from supply disruptions, 3DP end-use parts will become the only viable choice for many OEMs from the automotive to medical industries. 3DP manufacturers will offer fully automated, end-to-end systems and technology solutions that keep the digital link from design to post-production and control of any 3D printed part.
Philemon Schoffer, co-founder and CEO of Hubs
New types of materials and composites, lower prices and improved post-processing options will make it more viable to integrate 3D printing into production cycles. As technology advances, 3D printing technology is becoming a more competitive alternative to injection molding for low-volume plastic parts.
Even more exciting, modern composite materials, combined with the ability to produce complex geometries, will open up new manufacturing possibilities that could not be realized with traditional technologies (it's already happening!).
Kwang-Ming Lee, Vice President of Carima
AT/3DP technology applications and market size have expanded significantly, but the application of AT/3DP to the production of finished parts in mechanical engineering has not yet reached full maturity.
In other words, in addition to being used for 3D prototyping, education and research and development, many industrial companies are working to use this technology as an alternative to traditional manufacturing methods such as milling and injection molding, but the point is that 3D printing production speed is still a sticking point compared to these methods.
To compete with traditional manufacturing methods, differentiated 3D printing technology needs to be developed and should be pursued in the near future and the AT/3DP market is likely to remain unchanged for the next decade.
To prepare for this development, almost all 3D printer manufacturers are investing a lot of time and money in developing the fastest 3D printing technology, but it is still difficult to achieve both high accuracy and repeatability.
The fact is that we, Carima, as one of the global manufacturers of 3D printers, have developed C-CAT (Carima Continuous Additive Technology), which is the world's fastest 3D printing technology, increasing productivity by at least 20 times compared to existing DLP technology. We successfully demonstrated it at Formnext 2021 and intend to upgrade it and bring new 3D printers with this technology to the market in the next 1-2 years.
C-CAT is the fastest 3D printing technology that allows DLP 3D printers to print 1 cm per minute (60 cm per hour) with high precision and repeatability. Our development team has been able to minimize model output problems at this speed, as well as significantly reduce power consumption. Thanks to this, more stable continuous additive manufacturing is possible with C-CAT.
As I mentioned earlier, improving the 3DP workflow and more robust implementation of the technology is absolutely essential to supply some of the existing plastic or rubber parts industries. We plan to lead the era of mass personalization of end products by accelerating the development of a new 3D printer capable of producing various components in industries such as eyewear, footwear, consumer goods, and automotive interior and exterior parts at a print speed of several tens of centimeters per hour.
Carima at Formnext 2021. Photo by Michael PetchAmir Veresh, Founder, eConsulting Ltd.
I am confident that in the second half of the next decade, additive manufacturing will become an important, legitimate (regulated and standards-based) and mainstream manufacturing method. It will improve the way products are produced, as in many cases it will complement traditional methods of production, and for other products it will become the main technology and method of production. Replacing traditional mass production with additive mass production requires an appropriate justification, which may be due to cost, environmental considerations, supply chain, improved functionality, etc. (no need to prioritize between these justifications). It will take time for equipment manufacturers to develop their products in a way that justifies the transition from traditional to additive manufacturing. This will happen as technology improves and education in design for additive manufacturing develops. Many endeavors will fail because of weak justification, but over time more and more applications will benefit from the use of AT.
Additive manufacturing will be able to use more of the standard industrial materials currently in use. It is possible that some materials developed for additive manufacturing will be approved for use in the manufacture of products.
Additive technologies will enable distributed manufacturing, thereby optimizing supply chains and reducing costs, increasing customer appeal and supporting the well-being of our planet.
Based on current trends, I expect a breakthrough in the mainstream segment to come from the identification of more products with low production volume and a large number of components, which will gradually replace existing (not adapted) mass-produced products. This is an exponential process that will accelerate significantly over time. Additive technologies should solve the problem of storage of spare parts by introducing a comprehensive solution of digital inventories, backed up by distributed local digital production.
Additive manufacturing will become an integral part of the advanced PLM complex, which will be deeply focused on IoT and the fourth industrial revolution.
Jordi Driman, 3D Applications Specialist, Mimaki Europe
I predict that full-color 3D printing will be in demand in the next decade by SMEs as printers like our 3DUJ-2207 become more cost effective and convenient for office space.
Automation is another exciting technology that I think is becoming commonplace throughout the printing sector as hopes for faster delivery times grow and with it the need for 24/7 operation.
Dr. Alvaro Goyanes Goyanes, co-founder and CEO of FabRx
In the next decade, 3D printing will be widely used in hospitals and pharmacies, for the preparation of complex drugs, and for clinical and preclinical research. One of the sources of income for large pharmaceutical companies will be the sale of drug cartridges for the preparation of individual drugs next to patients. This will increase the personalization of drugs, increasing their tolerability and effectiveness, and reducing side effects.
Andreas Langfeld, President EMEA, Stratasys
AT will find its place as a unique and unique manufacturing technology. There will be a general understanding that certain parts must be produced additively due to lot size, the need for customization, the need for on-site production on demand. This standardization of AT as the manufacturing method of choice is seen today in the mobile, aerospace, dental and medical sectors, but it will spread to other verticals and become the new normal for some component manufacturing.
André Wegner, CEO, Authentise
New technologies. One thing is clear - the evolution of digital technologies will not stop. We will see not only continuous, incremental improvements to existing technology platforms, but entirely new platforms and technology suites.
Concept based design. Partly to ensure the rapid deployment of new technology platforms and to increase the speed of bringing new ideas to market, we will increasingly rely less on CAD and other design tools to communicate our ideas. Instead, we will focus on semantics that can convey our true intent. This design, in turn, will be used by a variety of software tools, including generative designers, to determine the final shape, influenced by other parameters such as available equipment and materials.
Artificial intelligence in AT. Transposed design means that the results of the last stage of the process (for example, measurements during testing) can influence new versions of designs or change parameters. We get a full-fledged technological complex for the entire production cycle, and not just limit the production technology to specific machines.
Martin Hermatschweiler, CEO of Nanoscribe
People tend to overestimate what they can achieve in 1 year and underestimate what can be achieved in 10 years. 3D microfabrication will be the driving force behind innovation. Size matters - especially on a small scale. And the material matters too. We will see many applications develop, from basic to applied research, until eventually reaching industrial maturity with a steep evolution in technology readiness level (TRL). In particular, startups will identify niches early and develop them. A huge range of materials will emerge and reach industrial levels, whether they be biomaterials such as biocoatings and biodegradable materials or technical materials beyond high-performance polymers, including glass and ceramics.
Multi-material 3D printing concepts will also become industrially applicable. The computational design capabilities and ease of use of two-photon polymerization will shorten the development cycle from sketch to ready-to-use product from years to weeks.
Xavier Martinez Faneca, CEO, BCN3D
Consolidation will play a key role in the coming years. In the coming decade, the 3D printing industry will certainly undergo a complete transformation. Technology will evolve towards high performance solutions, leading to greater autonomy in the hands of end customers. I expect that during this 10 year period AT will be able to truly deliver on the promises that have been made in recent years and become a mainstream manufacturing method.
John Barnes, Managing Director, and Laura Ely, Program Director, The Barnes Group Advisors
AT will become less unusual, perhaps even boring. Boredom is good for batch production, and batch production is good for AT. We will be happy, free, less confused and alone - all at the same time.
Equipment. More diversification as the industry learns about 3D printing and its techniques.
Materials. Here we see two directions: 1) a deeper understanding of how the material functions in various processes, and 2) the emergence of more advanced polymers that will push the boundaries of performance. (We are seeing a move to higher cost materials, as is the case with metal ATs.)
Digital technologies. Improved software is on the horizon, it will be integrated into the AT workflow and become smarter, perhaps even artificially intelligent. Machine learning will become a standard tool for the industry.
People. As more people learn AT and understand its importance, the gap in practical experience will be minimized, the existing workforce will continue to learn and be supplemented by new graduates of vocational schools and colleges for whom AT is already a tool in the arsenal .
David Iacovelli, Regional Director EMEA, EOS
AT has clear advantages over other production methods in terms of stability. We will see how AT will compete and replace technologies that are widely used today. Additive manufacturing will become the dominant mass production technology. The full automation and digital workflow that is possible with polymer additive manufacturing will replace mass production technologies that require high precision and productivity, while reducing costs. We have our own Fine Detail Resolution technology. But this also applies to other technologies such as Laser ProFusion. They will bring the industry closer to tool-free injection molding.
The second innovation we anticipate is the industry's shift to digital storage and on-demand production of needed parts. This will enable companies to significantly reduce aftermarket costs and create new businesses focused on providing locally produced parts and services for a variety of consumer and industrial products.
We believe that in the next decade we can expect further market consolidation and the emergence of several major players. In addition, interoperability will be improved, which will lead to increased competition in the market, as it will be much easier for manufacturers to switch from one technology to another and mix competitive technologies depending on their needs.
Nora Toure, Founder of Women in 3D Printing
I wish this was a prediction for 2022, but it will probably take more than a year. However, I hope we will see a trend towards diversity, with people of different races and nationalities represented in key positions and at all levels of any organization.
In terms of technology, continuous improvement in the production of products and materials in general is to be expected. I wouldn't be surprised if AT doesn't look exactly the same in the next decade as it does today.
Sylvia Monsheimer, Head of New 3D Printing Technologies Evonik
I don't think we're going to see a "big bang" in 3D printing in the next decade. I rather expect to see specific approaches to mass production that will lead to huge success in the industry. Successful mass production using AT will require such specialization in terms of process parameters, equipment and material that allows 3D printing to surpass conventional production. I look forward to seeing new technologies! Now so many specialists are working to overcome the existing difficulties. This will be an exciting decade.
Fedor Antonov, CEO Anisoprint
The main technological trends will be further development and improvement, as well as an increase in preparedness and adoption of technologies - those technologies that have attracted market attention and have already been developed. I don't see any significant new technologies emerging in the next few years, and most likely it will be about the consolidation, maturation, improvement and market entry of existing technologies. New technologies will find a new niche. We are talking about the stable growth of the market and the destruction of the usual technological processes. Each group of companies and equipment will focus on a specific niche where it performs best. In the future, 3D printing technologies will be more specialized: even more tailored to specific industries and problems in various niches.
The next decade will bring the prospect of 3D printing to new emerging markets such as commercial space, drones and aircraft, robotics, urban transportation and many others that will grow rapidly. They will be the main stimulus for the growth of technologies such as 3D printing. This is where new players will be able to defeat the old ones - due to greater flexibility through the use of 3D printing. Applying new technologies that are more stable and allow better, lighter parts to be made to order will help solve supply chain problems.
There is interaction between new and emerging markets such as 3D printing and the new technology markets I just mentioned. These segments are still growing at a very impressive rate of 20 to 30 percent and will collectively reach a trillion dollars in the next decade. Obviously, the 3D printing market will continue to grow at the same rate and we will have a significant share of this market.
Dr. Ingo Ederer, CEO Voxeljet
The past year has been marked by acquisitions and consolidations as the industry is extremely fragmented. We believe this trend will continue in the next couple of years. Despite the fact that additive manufacturing has been around for about half a century, we are currently seeing an incredible rate of development of the technology and the ecosystem around it.
Particularly in times of pandemic and climate change, additive manufacturing can position itself as a technology capable of solving problems in an extremely efficient manner. In terms of complementing existing manufacturing processes, to meet fluctuating excess demand, manufacturing locally, and in terms of lightweight construction and resource efficiency. However, there is still a lack of automation and wider application possibilities due to the lack of new materials and process standardization. These elements will be the focus of the industry over the next decade and will be needed to turn AT into a viable mass production technology.
With the expansion of the use of AT, the demand for skilled workers and AT education will also grow, while we are already seeing the first AT-oriented courses in schools and universities, the whole engineering mentality will shift towards more efficient use of resources and stable design. This will include the development of improved software solutions.
James DeMuth, founder and CEO of Seurat
The cost of LPBF (Powder Bed Laser Fusion) products will be significantly reduced and will compete with casting and milling in small to medium volumes while maintaining the high quality and benefits of AT that we are all used to today (and even more) . Mass production of AT parts will become commonplace.
Dr. Joshua Pierce, John M. Thompson Department of Information Technology and Innovation, Western University, Canada
Many predictions that a 3D printer will be in every home have not yet come true, but the steady and smooth growth of distributed production using 3D printers in the home is undeniable. 3D printing filament is now classified as "Amazon Basic" along with batteries and paper. The technology that I believe will tip the scales of distributed manufacturing in the next decade is distributed processing and additive manufacturing (or DRAM for short). Several open source technologies have already been created, from filament-producing recycling robots to “direct waste” 3D printers that allow us to use 3D printing at home to recycle plastic waste into valuable items. DRAM saves people real money. This technology allows consumers to make custom products at less than US sales tax (6%) - from skateboards and toys to syringe pumps and arthritis treatments. As more companies take advantage of the economic advantage and make more DRAM technologies available to their customers, DRAM should be expected to follow the growth curve of consumer 3D printing.
Alessio Lorusso, CEO, Roboze
The impact that additive technologies will have on the future is the most exciting and, at the same time, fantastic idea. I believe that the most important and overarching theme in which AT will continue to show breakthrough results is the response to the strategies for the environmental sustainability of our planet. The possibilities are endless. Creating local production on demand, reducing transport emissions and combating production waste is just the beginning. We at Roboze look forward to supporting the innovators who will change our future for the better.
The Roboze ARGO 1000. Photo by Michael Petch.
Ankush Venkatesh, intra-entrepreneur, additive manufacturing, Glidewell Dental
In the coming decade, AT will mature in its role in the digital manufacturing constellation. This will enable new innovative business models to take advantage of a suite of digital solutions. These solutions will be based on software platforms that will be modular, interoperable and highly complex. In part, this may lead to the emergence of many hyper-specialized service providers, but it will also force incumbents to focus on the development of "hot", complex offers. We have already seen this in the personal computer industry (1980s - 2000s), as well as in the smartphone industry (2000s - present).
This decade will also see a major shift in boundaries. We're thinking edge computing or point-of-use manufacturing. All of this has been made possible by significant advances in technological capabilities, coupled with increased access to them. Given the constant growth of these factors, I sincerely believe that it is in this decade that distributed production can truly be realized. Advanced technology will soon become the norm. The FDA (Food and Drug Administration, USA) recently released a discussion paper asking industry participants to contribute to the development of policy and regulation for 3D printed healthcare solutions.
Data will play a critical role in getting the most out of additive manufacturing. Information about process control, supply/demand trends, supply chain agility and carbon emissions will increasingly flow into systems capable of processing this volume of data and generating actionable insights.
what lies ahead for 3D printing
The prospects for 3D printing
Even now, the prospects for 3D printing are extremely promising. Scientists are actively developing existing 3D printing techniques, developing new technologies and types of materials, and finding new areas of application. Many call 3D printing the technology of the future, and for good reason. The technique is able to completely turn the usual way of life, changing the way most things are produced. In fact, a 3D printer is a real multifunctional factory, small and compact. Due to this, the future of 3D printing can definitely be called successful.
3D printers can significantly reduce production costs, thereby reducing the cost of products. Judging by the growing trend towards the popularization of 3D technologies, raw materials for 3D printing will become the main commodity unit in the future. In general, the prospects for 3D printing are defined for many areas. And now we will try to reveal them as much as possible.
The future of 3D printing
If you try to imagine the future of 3D printing, the imagination paints a rather interesting picture. Given the great interest of scientists in the 3D bioprinting technique, which is one of the most promising 3D printing technologies, the production of artificial organs on a 3D printer is not far off. It is also safe to say that the future of 3D printing will bring us dramatic changes in areas such as:
- Construction. 3D printing of houses, or contour construction, attracts many with its futurism and simplicity. The first steps in this direction have already been taken. The pioneers in 3D printing of houses were the Chinese, followed by the government of Dubai who discovered contour building. The first 3D printed office building has already been built in this city of the future, and an entire block is planned to be printed in the near future. And just recently, the first printed house in Europe was created on a 3D printer;
- Electronics.
When listing the prospects for 3D printing, this point should be given special attention. Scientists believe 3D printing of electronics is the future of digital device manufacturing, and with good reason. Graphene properties and its application in additive manufacturing are currently being actively researched. A huge breakthrough in this area is the creation of a graphene battery with an unlimited service life on a 3D printer;
- Automotive and aerospace industry. The future of 3D printing is largely based on its ability to reproduce almost any element of varying complexity. In this regard, 3D printing is already widely used in the development of aircraft, machines and satellites. The ISS even has its own 3D printer, not to mention a number of successful 3D printing of cars.
- Pharmaceutical industry. Yes, yes, you can imagine. The future of 3D printing is in the manufacture of tablets and other medicines. This is confirmed by epilepsy pills legalized in the USA, made according to a special technique.
The essence of this perspective of 3D printing is the gradual release of active substances, so that instead of many tablets, you can drink just one.
- Food industry. 3D food printers are gradually gaining space in cafes and restaurants. While this is probably one of the most raw 3D printing technologies out there, it has potential. Food 3D printers are especially interesting for the possibility of making food for astronauts, as well as the freedom to display culinary talent. This is confirmed by the amazing 3D-printed desserts of our compatriot.
Other questions and answers about 3D printers and 3D printing:
- Finance Which 3D printer manufacturers are the best?
- Finance Which 3D printer is better to buy?
The future of 3D printers
Now let's try to imagine the future of 3D printers. There are several important points to be noted here. Below we list the most likely scenarios for the future of 3D printers.
- Improving the reliability and quality of instruments. Surely, many users are looking forward to this, because most of the existing models of 3D printers cannot boast of uninterrupted operation and the absence of printing errors;
- Large-scale distribution. It is certain that the future of 3D printers will please us with their popularization. Even now, one can observe a growing trend towards the use of 3D printing in almost all areas of industry. In parallel with the fact that more and more users learn about the possibilities of technology, the demand for desktop 3D printers is also growing;
- Availability. In continuation of the previous paragraph, it is worth noting that the growing demand for 3D printers will lead to lower prices for these devices. The use of 3D printing for domestic purposes is gaining momentum, which brings new equipment manufacturers to the market. Naturally, such a step will entail a reduction in the cost of devices;
- Enlargement of the construction area.
3D printing of large-sized objects has long occupied the minds of developers. Of course, this applies to industrial 3D printers, because the functionality of 3D printing at this scale will allow you to create full-fledged components, for example, cars and aircraft;
- Expanding the range of available materials. The future of 3D printers depends a lot on 3D printing materials, because more means more possibilities. The development of special equipment and related materials is being carried out by many companies, and news about the release of new polymers is constantly appearing.
3D technologies of the future
Summing up, it remains to consider only 3D technologies of the future. These include various futuristic scenarios that, to one degree or another, are already beginning to develop today. These include the technique of virtual reality, 3D scanning to create the perfect clothes and shoes, 3D printed makeup, and more. In a way, 3D technologies of the future also include bioprinting.