Explain how a 3d printer works
How a 3D Printer Works and What It Is Used for
3D printing, also known as additive manufacturing, is defined as a process in which a digital file is used to create a three-dimensional solid object. In the 3D printing process, sequential layers of material are laid down by the ‘printer’ until object creation is completed. This article covers the working, software, and applications of 3D printing.
Table of Contents
- What Is 3D Printing?
- How Does 3D Printing Work?
- Top 7 3D Printing Software
- 3D Printing Applications
What Is 3D Printing?
3D printing, also known as additive manufacturing, is a process in which a digital file is used to create a three-dimensional solid object. In the 3D printing process, sequential layers of material are laid down by the ‘3D printer’ until object creation is completed.
3D-printed objects are created through an additive process, where the printer places layer after layer of material until the desired thing is ‘printed’. Each layer can be considered a finely sliced cross-section of the printed item. With 3D printing, users can produce complicated shapes without consuming as much material as traditional manufacturing methods require.
The operation style of 3D printing is the opposite of ‘subtractive manufacturing’, where the material is cut out or hollowed using equipment such as a milling machine. Conversely, additive manufacturing does not need a mold or material block to create physical objects. Instead, it stacks layers of material and fuses them together.
3D printing offers swift product creation, low expenses for the initial fixed infrastructure, and the ability to create complicated geometries using several material types, something traditional manufacturing solutions might not be capable of as efficiently.
Timeline of 3D printing
Generally associated with the Do It Yourself (DIY) culture of amateurs and hobbyists, 3D printing has grown to include commercial and industrial applications. For instance, engineers today often use 3D printers for prototyping and creating lightweight geometric objects.
The origins of 3D printing lie in ‘rapid prototyping’. When the base technology was first invented in the 1980s, the term was used to describe it because, at the time, 3D printing was only suitable for creating prototypes rather than production components. In fact, the original intent of its creation was simply to accelerate the development of new products through swift prototyping.
Interestingly, the technology did not garner much interest when it was first introduced. In 1981, Japan’s Hideo Kodama filed the first patent for a machine that leveraged UV light for curing photopolymers. Three years later, French inventors Olivier de Witte, Jean Claude André, and Alain Le Mehaute jointly filed a patent for a similar technology. Both patents were abandoned, with General Electric saying the ‘latter lacked notable business potential’.
It was in 1984 that American inventor Charles Hull filed a patent for an ‘Apparatus for Production of Three-Dimensional Objects by Stereolithography’. He invented the STL file and founded 3D Systems three years later, in 1987.
Within the same decade, significant strides were made in the US 3D printing space, with patents filed for selective laser sintering (SLS) and fused deposition modeling (FDM). Desktop Manufacturing (DTM) Corp. and Stratasys were pioneering companies in the 3D printing space, founded around the same time.
After that, the industry transformed as rapid commercialization took hold of it. The first ‘3D printers’ were large and cost-intensive, with their makers competing to land contracts for industrial prototyping with large-scale automotive, consumer goods, health products, and aerospace manufacturers.
By 1987, 3D Systems had introduced the first commercial-grade SLA printer; in 1992, Stratasys and DTM released the first commercial FDM and SLS printers, respectively. The first metal 3D printer was introduced in 1994 by Electro Optical Systems (EOS), a German enterprise.
By the dawn of the new millennium, companies in the 3D printing space were competing fiercely for profits. Progress in materials science and the lapse of numerous patents increased the affordability of 3D printing.
Soon, thanks to the strides made in the 3D printing space, manufacturing processes were not exclusively owned by enterprises backed by heavy machinery and capital. Today, 3D printing has transformed into a cutting-edge solution for creating many different types of production components.
See More: What Is DevOps? Definition, Goals, Methodology, and Best Practices
How Does 3D Printing Work?
The ISO/ASTM 52900, related to the general principles and terminologies in additive manufacturing, categorizes 3D printing processes into seven distinct groups. Each type of 3D printing works a little differently.
The time taken to print a 3D object depends on the type of printing, the output size, the type of material, the desired quality, and the setup configuration. 3D printing can take anywhere from a few minutes to a few days.
The different types of 3D printing are:
1.
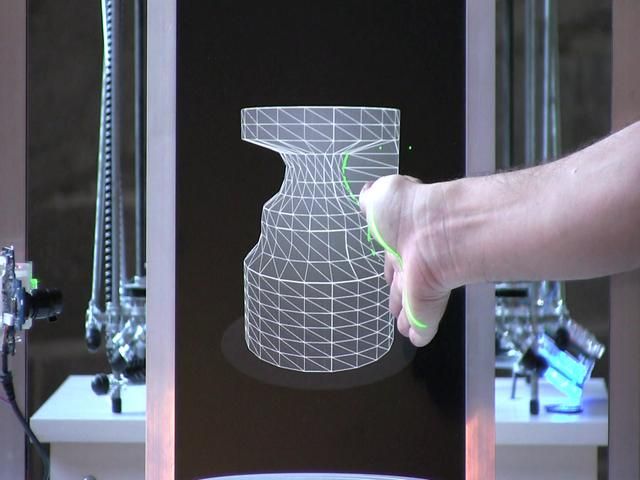
In powder bed fusion (PBF), thermal energy, in the form of an electron beam or laser, selectively fuses specific areas of a powder bed to create layers. These layers are built on one another until a part is made.
PBF may include sintering or melting processes; however, the primary operation method remains the same. First, a recoating roller or blade places a fine layer of powder on the build platform. Next, the surface of the powder bed is scanned using a heat source. This source selectively increases particle temperature to bind specific areas.
Once the heat source scans a cross-section or layer, the platform descends to let the process be repeated for the next layer. The final output is a volume with fused parts, with the surrounding powder remaining unaffected. The platform then ascends to allow retrieval of the completed build. Powder bed fusion includes several standard printing methods, such as selective laser sintering (SLS) and direct metal laser sintering (DMLS).
SLS is regularly leveraged for manufacturing polymer parts for prototypes and functional components. SLS printing takes place with the powder bed as the sole support structure. The lack of additional support structures allows for the creation of complex geometries. However, produced parts often feature inner porosity and a grainy surface and generally require post-processing.
SLS is similar to selective laser melting (SLM), electron beam powder bed fusion (EBPBF), and direct metal laser sintering (DMLS). However, these processes are used for creating metal parts and rely on a laser for fusing powder particles, one layer at a time.
DMLS increases the temperature of the particles only up to the point of fusion, whereby they combine at a molecular level. On the other hand, SLM completely melts metal particles. Both these techniques are heat-intensive and thus require support structures. Once the process ends, the support structures are removed using CNC machining or manually. Parts are then thermally treated to address residual stresses during post-processing.
These metal 3D printing techniques create components with high-quality physical properties, sometimes even more robust than the base metal used. The surface finish is often excellent as well. In terms of material, these techniques can process metal superalloys and ceramics that can be hard to use in other processes. However, both DMLS and SLM are cost-intensive, and the system’s volume constrains the output size.
2. VAT photopolymerization
VAT photopolymerization can be split into two methodologies: digital light processing (DLP) and stereolithography (SLA). Both these processes create components one layer at a time by using a light source to selectively cure liquid material (usually resin) stored in a vat.
DLP works by ‘flashing’ an image of each complete layer onto the surface of the liquid in the vat. On the other hand, SLA relies on a single-point UV source or laser to cure the liquid. Excess resin has to be cleaned off the output once printing is completed, after which the item must be exposed to light to improve its strength further. Support structures, if any, will need to be removed post-processing, and one can further process the part to create a higher quality finish.
These methods are best-suited for output that requires high-level dimensional accuracy, as they can create intricately detailed items with an excellent finish. DLP and SLA are, therefore, well-suited for the production of prototypes.
However, these methods’ output is often brittle, making them less suited for functional prototypes. These parts’ color and mechanical properties are also likely to degrade in the sun’s UV light, making them unsuitable for outdoor use. Finally, support structures are often required and might leave blemishes, which one can remove through post-processing.
3. Binder jetting
Binder jetting works by depositing a fine layer of powdered material, such as polymer sand, ceramic, or metal, onto the build platform. After this, a print head deposits adhesive drops to bind these particles. The part is hence built layer by layer.
Metal parts must be thermally sintered or infiltrated with a metal that has a low melting point, such as bronze. Parts made of ceramic or full-color polymer can be saturated using a cyanoacrylate adhesive. Post-processing is generally required to finish the output.
Binder jetting has numerous applications, including large-scale ceramic molds, full-color prototypes, and 3D metal printing.
4. Material jetting
Material jetting is conceptually similar to inkjet printing. However, instead of inserting ink on paper, it uses one or more print heads to deposit layers of liquid material. Each layer is cured before the next layer is produced. While material jetting relies on support structures, they can be created using a water-soluble substance that is washable after the building is completed.
This highly precise process is well-suited for creating full-color parts using different material types. However, it is cost-intensive, and the output tends to be brittle and degradable.
5. Fused deposition modeling
In fused deposition modeling (FDM), a heated nozzle is used to feed a filament spool to an extrusion head. The extrusion head increases the temperature of the material, softening it before placing it in predetermined areas to cool. Once a material layer is created, the build platform descends and prepares for the next layer to be placed.
This process, also known as material extrusion, features low lead times and is cost-effective. However, its dimensional accuracy is low, and a smooth finish often requires post-processing. The output is also not well-suited for critical applications as it tends to be anisotropic, i.e., weaker in one direction.
6. Sheet lamination
Sheet lamination can be further classified into two technologies: ultrasonic additive manufacturing (UAM) and laminated object manufacturing (LOM). UAM has a low energy and temperature requirement and works by joining thin metal sheets using ultrasonic welding. It works with several metals, including stainless steel, titanium, and aluminum. On the other hand, LOM places layers of material and adhesive alternatively to create the final output.
7. Direct energy deposition
This technique uses a laser, electric arc, electron beam, or another form of focused thermal energy to fuse powder or wire feedstock as it is placed. The process takes place horizontally to create layers, which are then stacked vertically for part creation. It is suited for different material types, including ceramics, polymers, and metals.
See More: What Is Serverless? Definition, Architecture, Examples, and Applications
Top 7 3D Printing Software
The 3D printing space is heavily software-dependent, with programs required for everything from designing the output and slicing it into G-code to controlling the 3D printer. Let’s check out the top 3D printing software across applications.
1. MatterControl 2.0
This solution by MatterHackers is an all-in-one printer host, slicer, and CAD software for desktops. Users can create new models in the CAD section and slice them. Once the model is ready to print, MatterControl 2.0 can be used to directly monitor and control printing via a USB connection or over a Wi-Fi module.
The software features an intuitive interface and allows users to explore a collection of geometric primitives that users can import into the print. These primitives can be dragged into position on the standard triangle language (STL) file to be printed and designated as support structures.
MatterControl also gives users access to advanced print configurations, making it ideal for end-to-end design, support preparation, slicing, and control. Enterprise users can upgrade to MatterControl Pro for even more valuable features.
2. Tinkercad
This free, browser-based solution allows users to design printable 3D models and provides a starting place for practicing solid modeling. Its easy-to-use block-building feature enables users to form models using basic shapes.
Tinkercad has numerous guides and tutorials to help users create the desired designs, which can then be exported or shared easily. Its library gives users access to millions of files, allowing them to find and modify the required shape. Finally, it features direct integration with third-party printing services.
3. Blender
This free, open-source tool is well-suited for both newbies and advanced users. It is feature-rich and can be used for 3D modeling and sculpting, as well as for animation, rendering, simulation, video editing, and motion tracking. However, it has a steep learning curve.
4. UVTools
This open-source solution is a comprehensive resin printing suite, an excellent file viewer, and optimized for layer repair and manipulation for masked SLA. It is compatible with PrusaSlicer, giving users access to numerous third-party MSLA printer profiles.
Twin-stage motor control (TSMC) is a crucial feature of UVTools, enabling tiered print speeds for different movement parts for each layer. This reduces print time and boosts the likelihood of print success.
Finally, UVTools allows users to create a custom resin layer cure time calibration print for testing new resins and setting the appropriate configuration for different layer heights.
5. WebPrinter
This browser-based solution can be used to preview G-code without having to open the file in a full-capability slicer. Users simply need to upload the G-code file, and WebPrinter will show the tool pathing that the file will transmit to the 3D printer. It is a fast and simple method to view a potential 3D print output.
6. Ultimaker Cura
This open-source slicer is compatible with most modern 3D printers. Cura is well-suited for beginners as it is easy to use, swift, and intuitive. On the other hand, advanced users can leverage it to access 200 settings for refining prints.
7. Simplify3D
Simplify3D is a powerful slicing tool for enhancing 3D print quality. It slices CAD into layers, corrects model issues, and showcases a user preview of the final output. Its premium features are handy for enterprise heavy-use 3D printers.
See More: What Are Microservices? Definition, Examples, Architecture, and Best Practices for 2022
3D Printing Applications
Although 3D printing is not a recent invention, it has gained immense popularity in recent times across industries due to its newfound simplicity, efficiency, and cost-effectiveness.
The top applications of 3D printing are:
1. Construction
Construction is one of the significant applications of 3D printing. Concrete 3D printing has been explored since the 1990s as researchers sought a faster and cheaper way to construct structures. Specific applications of 3D printing in construction include additive welding, powder bonding (reactive bond, polymer bond, sintering), and extrusion (foam, wax, cement/concrete, polymers).
Today, large-scale 3D printers designed to print concrete are used to pour foundations and erect site walls. They are also capable of printing modular concrete sections for onsite assembly. These solutions allow for higher accuracy, more complexity, faster construction, and improved functional integration while lowering labor costs and minimizing waste.
In 2016, the first pedestrian bridge (12 meters long, 1.75 meters wide) was 3D printed in Spain using micro-reinforced concrete. A year later, the first fully 3D-printed residence was built in Russia. 600 wall elements were 3D-printed and assembled, after which, the roof and interiors were created for a total area of nearly 300 sq meters.
3D printing is also helpful in producing architectural-scale models. It is even being explored as a solution for constructing extraterrestrial habitats on the Moon or Mars, should the need ever arise.
2. Prototyping and manufacturing
In the case of traditional injection-molded prototyping, it can take weeks to produce a single mold that would cost up to hundreds of thousands of dollars. As established earlier in the article, the original purpose of 3D printing was faster and more efficient prototyping.
3D printing technology minimizes lead times in manufacturing, enabling prototyping to be completed within a few hours and at a small percentage of traditional costs. This makes it especially ideal for projects where users must upgrade the design with every iteration.
3D printing is also suitable for manufacturing products that do not need to be mass-produced or are usually customized. SLS and DMLS are used in the rapid manufacturing of final products, not just prototypes.
3. Healthcare
In healthcare, 3D printing creates prototypes for new product development in the medical and dental fields. In dentistry, 3D printing is also helpful in creating patterns for casting metal dental crowns and manufacturing tools for creating dental aligners.
The solution is also helpful for directly manufacturing knee and hip implants and other stock items and creating patient-specific items such as personalized prosthetics, hearing aids, and orthotic insoles. The possibility of 3D-printed surgical guides for particular operations and 3D-printed bone, skin, tissue, organs, and pharmaceuticals is being explored.
4. Aerospace
In aerospace, 3D printing is used for prototyping and product development. The solution is also critically helpful in aircraft development, as it helps researchers keep up with the strenuous requirements of R&D without compromising on the high industry standards. Certain non-critical or older aircraft components are 3D-printed for the flight!
5. Automotive
Automotive enterprises, especially those specializing in racing automobiles, such as those used in F1, leverage 3D printing for prototyping and manufacturing specific components. Organizations in this space are also exploring the possibility of using 3D printing to fulfill aftermarket demand by producing spare parts as customers require rather than stocking them up.
See More: What Is an API (Application Programming Interface)? Meaning, Working, Types, Protocols, and Examples
Takeaway
The term ‘3D printing’ encompasses numerous technologies and processes that collectively offer a wide range of capabilities for producing components using various materials. The key similarity across 3D printing types is the additive layer-by-layer production process where no subtractive methodology, molding, or casting is required. Applications of 3D printing are rapidly emerging across industry verticals as the solution becomes more effective and affordable and penetrates deeply and widely across sectors.
Did this article help you gain a comprehensive understanding of 3D printing? Share your views with us on Facebook, Twitter, or LinkedIn!
MORE ON DEVOPS- What Is Agile Software Development? Life Cycle, Methodology, and Examples
- Terraform vs. Ansible: Understanding the Key Differences
- Software Developer vs. Software Engineer: Top 10 Differences
- What Is OOP (Object Oriented Programming)? Meaning, Concepts, and Benefits
- What Is Version Control? Meaning, Tools, and Advantages
How do 3D printers work?
by Chris Woodford. Last updated: April 24, 2021.
Even the best artists struggle to show us what real-world objects look like in all their three-dimensional (3D) glory. Most of the time that doesn't matter—looking at a photo or sketch gives us a good-enough idea. But if you're in the business of developing new products and you need to show them off to clients or customers, nothing beats having a prototype: a model you can touch, hold, and feel. Only trouble is, models take ages to make by hand and machines that can make "rapid prototypes" cost a fortune (up to a half million dollars). Hurrah, then for 3D printers, which work a bit like inkjets and build up 3D models layer by layer at up to 10 times the speed and a fifth the cost. How exactly do they work? Let's take a closer look!
Photo: 3D printing in action: this is the printhead of an Invent3D printer, slowly building up an object, layer by layer, by squirting molten blue plastic out of its precisely moving nozzle. Photo by Cpl. Justin Updegraff courtesy of US Marine Corps.
Contents
- From hand-made prototypes to rapid prototyping
- How does a 3D printer work?
- Q: What kind of "ink" does a 3D printer use? A: ABS plastic!
- Advantages and disadvantages
- Applications
- Medicine
- Aerospace and defense
- Visualization
- Personalized products
- The future of 3D printing
- Find out more
From hand-made prototypes to rapid prototyping
Photo: A high-quality rapid prototype of a space plane made in wax from a CAD drawing by NASA. Photo courtesy of NASA Langley Research Center (NASA-LaRC).
Before there were such things as computer-aided design (CAD) and lasers, models and prototypes were laboriously carved from wood or stuck together from little pieces of card or plastic. They could take days or even weeks to make and typically cost a fortune. Getting changes or alterations made was difficult and time-consuming, especially if an outside model-making company was being used, and that could discourage designers from making improvements or taking last-minute comments onboard: "It's too late!"
With the arrival of better technology, an idea called rapid prototyping (RP) grew up during the 1980s as a solution to this problem: it means developing models and prototypes by more automated methods, usually in hours or days rather than the weeks that traditional prototyping used to take. 3D printing is a logical extension of this idea in which product designers make their own rapid prototypes, in hours, using sophisticated machines similar to inkjet printers.
How does a 3D printer work?
Artwork: One of the world's first three-dimensional FDM printers, developed by S. Scott Crump in the 1980s. In this design, the model (pink, 40) is printed on a baseplate (dark blue, 10) that moves in the horizontal (X–Y) directions, while the print head and nozzle (2 and 4, orange) move in the vertical (Z) direction. The raw material for printing comes from a plastic rod (yellow, 46), melted by the print head. The heating process is carefully regulated by a thermocouple (electrical heat sensor) connected to a temperature controller (purple, 86). The rod is extruded using compressed air from the large tank and compressor on the right (green, 60/62). Things have changed a bit since then, but the basic principle (of building up an object by melting and depositing plastic under three-dimensional control) remains the same. Artwork from US Patent 5,121,329: Apparatus and method for creating three-dimensional objects by S. Scott Crump, Stratasys Ltd, June 9, 1992, courtesy of US Patent and Trademark Office.
Imagine building a conventional wooden prototype of a car. You'd start off with a block of solid wood and carve inward, like a sculptor, gradually revealing the object "hidden" inside. Or if you wanted to make an architect's model of a house, you'd construct it like a real, prefabricated house, probably by cutting miniature replicas of the walls out of card and gluing them together. Now a laser could easily carve wood into shape and it's not beyond the realms of possibility to train a robot to stick cardboard together—but 3D printers don't work in either of these ways!
A typical 3D printer is very much like an inkjet printer operated from a computer. It builds up a 3D model one layer at a time, from the bottom upward, by repeatedly printing over the same area in a method known as fused depositional modeling (FDM). Working entirely automatically, the printer creates a model over a period of hours by turning a 3D CAD drawing into lots of two-dimensional, cross-sectional layers—effectively separate 2D prints that sit one on top of another, but without the paper in between. Instead of using ink, which would never build up to much volume, the printer deposits layers of molten plastic or powder and fuses them together (and to the existing structure) with adhesive or ultraviolet light.
Q: What kind of "ink" does a 3D printer use? A: Plastic!
Where an inkjet printer sprays liquid ink and a laser printer uses solid powder, a 3D printer uses neither: you can't build a 3D model by piling up colored water or black dust! What you can model with is plastic. A 3D printer essentially works by extruding molten plastic through a tiny nozzle that it moves around precisely under computer control. It prints one layer, waits for it to dry, and then prints the next layer on top. Depending on the quality of the printer, what you get is either a stunning looking 3D model or a lot of 2D lines of plastic sitting crudely on top of one another—like badly piped cake icing! The plastic from which models are printed is obviously hugely important.
Photo: A Lulzbot 3D printer. You can see the little reel of raw, red plastic (the "filament") that feeds into the print head from the top. Photo by Stephane Belcher courtesy of US Navy.
When we talk about plastic, we generally mean "plastics": if you're a diligent recycler, you'll know there are many types of plastic, all of which are different, both chemically (in their molecular makeup) and physically (in the way they behave toward heat, light, and so on). It's hardly surprising that 3D printers use thermoplastics (plastics that melt when you heat them and turn solid when you cool them back down), and typically either ABS (acrylonitrile butadiene styrene), PLA (polylactic acid), or PETG (polyethylene gerephthalate glycol).
Perhaps most familiar as the material from which LEGO® bricks are made, ABS is also widely used in car interiors (sometimes in outside parts such as hubcaps too), for making the insides of refrigerators, and in plastic computer parts (it's quite likely the mouse and keyboard you're using right now are made from ABS plastic). So why is this material used for 3D printing? It's really a composite of a hard, tough plastic (acrylonitrile) with a synthetic rubber (butadiene styrene). It's perfect for 3D printing because it's a solid at room temperatures and melts at a little over 100°C (220°F), which is cool enough to melt inside the printer without too much heat and hot enough that models printed from it won't melt if they're left in the Sun. Once set, it can be sanded smooth or painted; another useful property of ABS is that it's a whiteish-yellow color in its raw form, but pigments (the color chemicals in paint) can be added to make it virtually any color at all. According to the type of printer you're using, you feed it the plastic either in the form of small pellets or filaments (like plastic strings).
PLA is easier to use than ABS and a little more environmentally friendly, though it's softer and less durable. PETG is a halfway house, closer to the strength of ABS, easy to shape, and relatively easy to recycle.
You don't necessarily need to print in 3D with plastic: in theory, you can print objects using any molten material that hardens and sets reasonably quickly. In July 2011, researchers at England's Exeter University unveiled a prototype food printer that could print 3D objects using molten chocolate!
Advantages and disadvantages
Photo: A B9Creator™—a typical low-cost, DIY 3D printer. It was originally available in kit form, priced at $2495; now it comes ready-assembled in three different versions priced from $6000–12000. Photo by courtesy of Windell H. Oskay, www.evilmadscientist.com, published on Flickr in 2012 under a Creative Commons Licence.
Makers of 3D printers claim they are up to 10 times faster than other methods and 5 times cheaper, so they offer big advantages for people who need rapid prototypes in hours rather than days. Although high-end 3D printers they are still expensive (typically about $25,000–$50,000), they're a fraction the cost of more sophisticated RP machines (which come in at $100,000–$500,000), and vastly cheaper machines are also available (you can buy a Tronxy 3D printer kit for around $100–200). They're also reasonably small, safe, easy-to-use, and reliable (features that have made them increasingly popular in places such as design/engineering schools).
On the downside, the finish of the models they produce is usually inferior to those produced with higher-end RP machines. The choice of materials is often limited to just one or two, the colors may be crude, and the texture may not reflect the intended finish of the product very well. Generally, then, 3D-printed models may be better for rough, early visualizations of new products; more sophisticated RP machines can be used later in the process when designs are closer to finalization and things like accurate surface texture are more important.
Applications
What can you use a 3D printer for? It's a bit like asking "How many ways can you use a photocopier?" In theory, the only limit is your imagination. In practice, the limits are the accuracy of the model from which you print, the precision of your printer, and the materials you print with. Modern 3D printing was invented about 25 years ago, but it's only really started to take off in the last decade. Much of the technology is still relatively new; even so, the range of uses for 3D printing is pretty astonishing.
Medicine
Photo: 3D-printed plastic hearts make it possible for surgeons to practise operations with no risk. Model by Dr. Matthew Bramlet. Public domain photo published on Flickr courtesy of US NIH Image Gallery and 3D Print Exchange.
Life's a one-way journey; fallible, aging humans with creasing, crumbling bodies naturally see great promise in a technology that has the potential to create replacement body parts and tissue. That's why doctors were among the earliest people to explore 3D printing. Already, we've seen 3D printed ears (from Indian company Novabeans), arms and legs (from Limbitless Solutions, Biomechanical Robotics Group, and Bespoke), and muscles (from Cornell University). 3D printers have also been used to produce artificial tissue (Organovo), cells (Samsara Sciences), and skin (in a partnership between cosmetics giant L'Oreal and Organovo). Although we're some way away from having complete 3D printed replacement organs (such as hearts and livers), things are rapidly moving in that direction. One project, known as the Body on a Chip, run by the Wake Forest Institute for Regenerative Medicine in North Carolina, prints miniature human hearts, lungs, and blood vessels, places them on a microchip, and tests them out with a kind of artificial blood.
Apart from replacement body parts, 3D printing is increasingly being used for medical education and training. At Nicklaus Children's Hospital in Miami, Florida, surgeons practise surgery on 3D-printed replicas of children's hearts. Elsewhere, the same technique is used to rehearse brain surgery.
Aerospace and defense
Designing and testing airplanes is a complex and expensive business: a Boeing Dreamliner has about 2.3 million components inside it! Although computer models can be used to test quite a few aspects of how planes behave, accurate prototypes still need to be made for things like wind-tunnel testing. And 3D printing is a simple and effective way to do that. While commercial airplanes are built in quantity, military planes are more likely to be highly customized—and 3D printing makes it possible to design, test, and manufacture low-volume or one-off parts both quickly and cost-effectively.
Photo: The US Navy has been testing 3D printers on ships since one was installed on USS Essex in 2014. In theory, an onboard printer makes a ship more self-reliant, with less need to carry spare parts and materials, especially during wartime. This is a 3D-printed undersea wireless charger, typical of the objects that might be printed during a mission at sea. Photo by Devin Pisner courtesy of US Navy.
Spacecraft are even more complex than airplanes and have the added drawback that they are "manufactured" in tiny quantities—sometimes only one is ever made. Instead of going to all the expense of making unique tools and manufacturing equipment, it can make much more sense to 3D print one-off components instead. But why even make space parts on Earth? Shipping complex and heavy structures into space is difficult, expensive, and time-consuming; the ability to manufacture things on the Moon, or on other planets, could prove invaluable. It's easy to imagine astronauts (or even robots) using 3D printers to produce whatever objects they need (including spare parts), far from Earth, whenever they need them. But even conventional, Earth-spawned space projects can benefit from the speed, simplicity, and low-cost of 3D printing. The latest, human-supporting NASA Rover uses 3D-printed parts produced with help from Stratasys.
Photo: Spares and repairs are no problem. Closeup view of a Lulzbot Taz 6 3D printer being used to make spare parts onboard a US naval ship. Photo by Christopher A. Veloicaza courtesy of US Navy.
Visualization
Making prototypes of airplanes or space rockets is an example of a much broader use for 3D printing: visualizing how new designs will look in three dimensions. We can use things like virtual reality for that, of course, but people often prefer things they can see and touch. Increasingly, 3D printers are being used for rapid, accurate architectural modeling. Although we can't (yet) 3D print in materials such as brick and concrete, there's a wide range of plastics available and they can be painted to look like realistic building finishes. In the same way, 3D printing is also now widely used for prototyping and testing industrial and consumer products. Since many everyday things are molded from plastic, a 3D printed model can look very similar to the finished product—perfect for focus-group testing or market research.
Personalized products
From plastic toothbrushes to candy wrappers, modern life is here-today, gone-tomorrow—convenient, inexpensive, and disposable. Not everyone appreciates off-the-shelf mass production, however, which is why expensive "designer labels" are so popular. In the future, more of us are going to be able to enjoy the benefits of affordable, highly personalized products custom-made to our exact specification. Jewelry and fashion accessories are already being 3D printed. Just as the Etsy website created a worldwide community of artisan crafters , so Zazzy has now replicated that using 3D printing technology. Thanks to simple online services like Shapeways, anyone can make their own 3D printed nick-nacks, either for themselves or to sell to other people without the expense and hassle of using their own 3D printer (even Staples is now offering 3D printing services in some of its stores).
"Customized products" aren't simply things we buy and use: the food we eat can fall into that category too. Cooking takes time, skill, and patience, because preparing a mouthwatering meal goes far beyond mixing ingredients and heating them on a stove. Since most food can be extruded (squeezed through nozzles), it can (theoretically) also be 3D printed. A few years ago, Evil Mad Scientist Laboratories playfully printed some weird objects out of sugar. In 2013, New York Times columnist A.J. Jacobs challenged himself to print an entire meal—including the plate and cutlery. In the process, he chanced upon the work of Cornell University's Hod Lipson, who believes meals may one day be personally, 3D printed to match your body's exact nutritional needs. Which brings us neatly to the future...
Photo: In theory, you can make 3D prints from any raw material you can feed into your printer. Here are some fantastic 3D objects printed with granulated sugar by a "CandyFab 4000" (a hacked old HP plotter) by the always entertaining folk at Evil Mad Scientist Laboratories. Photo by courtesy of Windell H. Oskay, www.evilmadscientist.com, published on Flickr in 2007 under a Creative Commons Licence.
The future of 3D printing
Many people believe 3D printing will herald not merely a tidal wave of brash, plastic gimmicks but a revolution in manufacturing industry and the world economy that it drives. Although 3D printing will certainly make it possible for us to make our own things, there's a limit to what you can achieve by yourself with a cheap printer and a tube of plastic. The real economic benefits are likely to arrive when 3D printing is universally adopted by big companies as a central pillar of manufacturing industry. First, that will enable manufacturers to offer much more customization of existing products, so the affordability of off-the-shelf mass-production will be combined with the attractiveness of one-off, bespoke artisan craft. Second, 3D printing is essentially a robotic technology, so it will lower the cost of manufacturing to the point where it will, once again, be cost-effective to manufacture items in North America and Europe that are currently being cheaply assembled (by poorly paid humans) in such places as China and India. Finally, 3D printing will increase productivity (since fewer people will be needed to make the same things), lowering production costs overall, which should lead to lower prices and greater demand—and that's always a good thing, for consumers, for manufacturers, and the economy.
Photo: Two views of the printhead (sometimes called the "tool head") of a 3D printer. Photo by Ashley McLaughlin courtesy of US Marine Corps.
How a 3D printer works, what can be printed on a 3D printer
The 3D printer is a technology that allows you to create real objects from a digital model. It all started in the 80s under the name "rapid prototyping", which was the goal of the technology: to create a prototype faster and cheaper. A lot has changed since then, and today 3D printers allow you to create anything you can imagine.
Contents:
- What is 3D printing?
- How does a 3D printer work?
- What can be printed?
The 3D printer allows you to create objects that are almost identical to their virtual models. That is why the scope of these technologies is so wide.
What is 3D printing?
3D printing is an additive manufacturing process because, unlike traditional subtractive manufacturing, 3D printing does not remove material, but adds it, layer by layer—that is, it builds or grows.
- In the first step of printing, the data from the drawing or 3D model is read by the printer.
- Next is the sequential overlay of layers.
- These layers, consisting of sheet material, liquid or powder, are joined together to form the final shape.
With limited production of parts, 3D printing will be faster and cheaper. The world of 3D printing does not stand still and therefore there are more and more different technologies competing with each other on the market. The difference lies in the printing process itself. Some technologies create layers by softening or melting the material, then they provide layer-by-layer application of this same material. Other technologies involve the use of liquid materials, which acquire a solid form in the process under the influence of various factors.
In order to print something , you first need a 3D model of the object, which you can create in a 3D modeling program (CAD - Computer Aided Design), or use a 3D scanner to scan the object you want print. There are also easier options, such as looking for models on the internet that have been created and made available to other people.
Once your design is ready, all you need to do is import it into the Slicer, a program that converts the model into codes and instructions for a 3D printer, most of the programs are open source and free. The slicer will convert your project into a gcode file ready to be printed as a physical object. Simply save the file to the included SD card and insert it into your 3D printer and hit print.
The whole process can take several hours and sometimes several days. It all depends on the size, material and complexity of the model. Some 3D printers use two different materials. One of them is part of the model itself, the other acts as a prop that supports parts of the model hanging in the air. The second material is subsequently removed.
How does a 3D printer work?
Although there are several 3D printing technologies, most create an object by building up many successive thin layers of material. Typically desktop 3D printers use plastic filaments (1) which are fed into the printer by the feeder (2) . The filament melts in the print head (3) which extrudes the material onto the platform (4) creating the object layer by layer. Once the printer starts printing, all you have to do is wait - it's easy.
Of course, as you become an advanced user, playing with the settings and tweaking your printer can lead to even better results.
What can be 3D printed?
The possibilities of 3D printers are endless and they are now becoming a common tool in fields such as engineering, industrial design, manufacturing and architecture. Here are some typical usage examples:
Custom Models
Create custom products that perfectly match your needs in terms of size and shape. Do something that would be impossible with any other technology.
Rapid Prototyping
3D printing allows you to quickly create a model or prototype, helping engineers, designers and companies get feedback on their projects in a short time.
Complex geometry
Models that are hard to imagine can be easily created with a 3D printer. These models are good for teaching others about complex geometry in a fun and useful way.
Cost reduction
The cost of 3D printing end-use parts and prototypes is low due to the materials and technology used. Reduced production time and material consumption as you can print models multiple times using only the material you need.
How to choose and buy a 3D printer? →
What is 3D printing and how it can be used! Interesting!
What is 3D printing
3D printing technology was patented in the 80s of the last century, but gained popularity relatively recently. New, promising techniques have been developed and the possibilities of 3D technologies have reached a completely new level. However, to this day, the technique is not known in all circles, and not everyone is aware of what 3D printing is. In today's article, we will try to explain in detail and in an accessible way what 3D printing is and where it is used.
In short, 3D printing is a technique for manufacturing three-dimensional products based on digital models. Regardless of the specific technology, the essence of the process is the gradual layer-by-layer reproduction of objects.
This process uses a special device - a 3D printer, which prints certain types of materials. More details about it are written here. Other names for the technology are rapid prototyping or additive manufacturing. Often the phrase "additive technologies" is used in the meaning of "3D technologies".
3D printing steps
To make it clearer what 3D printing is, let's take a look at the reproduction process step by step. Below are the specific stages of 3D printing. How it works:
- 3D modeling of the required object is performed according to certain rules;
- The file with the digital model is loaded into the slicer program, which generates the control code for the 3D printer;
- Sets required 3D printing options;
- The code is written to a removable memory that connects to the 3D printer;
- 3D model reproduced.
Objects are rendered gradually. According to the required shape, the selected material is applied layer by layer, forming the finished product. It is worth noting that the possibilities of 3D printing are almost limitless, that is, anything can be made. In some technologies, very thin overhanging elements are provided with supports, thanks to which they can be avoided from sagging.
Naturally, this is a very simplified description of the stages of 3D printing, but they give a very clear idea of the essence of the technique.
Other questions and answers about 3D printers and 3D printing:
- Basics What is 3D scanning?
- Basics What is a 3D model?
3D Printing Technologies
Different 3D printing technologies are used to reproduce different objects. They differ both in the consumables used, and in the speed and accuracy of printing. Here are the main 3D printing technologies:
- Fused deposition modeling (FDM) .
One of the most common 3D printing technologies, used in most desktop 3D printers, and represents an ideal price / quality ratio. Printing occurs by layer-by-layer supply of a thread of molten plastic;
- Laser stereolithography (SLA) . The formation of the object occurs due to the layer-by-layer illumination of a liquid photopolymer resin by a laser, which hardens under the influence of radiation. One of the variations of this technology is DLP 3D printing. It uses a special projector instead of a laser. Both 3D printing methods are used to create objects with a high degree of detail. In the case of DLP printing, speed is also an added advantage;
- Selective laser sintering (SLS) . Reproduction is performed by layer-by-layer melting of a special powder under the action of laser radiation. This 3D printing method is widely used in the industry for the manufacture of durable metal elements
3D Printing Applications
As you may have guessed by now, 3D printing is extremely versatile. The second name of the technology - rapid prototyping - speaks for itself. In the manufacture of prototypes and models of models, 3D printing can be simply indispensable. It is also a very cost-effective solution for small-scale production. In the aerospace and automotive industries, 3D technologies are already being used with might and main due to the high profitability and speed of manufacturing components. Culinary professionals are working on the development of 3D food printers, and in medicine, 3D printing has become something of a technology of the future. With the help of 3D bioprinting, it is planned to produce bones, organs and living tissues, but for now, implants and full-fledged medicines are printed on 3D printers. Desktop 3D printers can be used for domestic purposes: for repairs, making various household items, and so on. And designers, fashion designers, sculptors and artists appreciate the possibilities of 3D printing and 3D modeling as an unusual way to realize their talent.